Проблемы машиностроения и надежности машин, 2021, № 1, стр. 57-63
Сравнительные характеристики износостойкости газодинамических покрытий, полученных с использованием электроэрозионных карбидов
Е. В. Агеев 1, *, С. Б. Беневоленский 2, **, М. Ю. Карелина 3, ***, А. Н. Новиков 4, ****
1 Юго-Западный государственный университет
Курск, Россия
2 Научно-исследовательский институт – Республиканский исследовательский
научно-консультационный центр экспертизы
Москва, Россия
3 Московский автомобильно-дорожный государственный технический университет (МАДИ)
Москва, Россия
4 Орловский государственный университет имени И.С. Тургенева
Орел, Россия
* E-mail: ageev_ev@mail.ru
** E-mail: sbb13@mail.ru
*** E-mail: karelinamu@mail.ru
**** E-mail: srmostu@mail.ru
Поступила в редакцию 06.07.2020
Принята к публикации 22.10.2020
Аннотация
В статье представлены результаты изучения характеристик износостойкости газодинамических покрытий, полученных с использованием электроэрозионных карбидов, изготовленных методом электроэрозионного диспергирования из отходов твердых сплавов ВК8 в дистиллированной воде и керосине осветительном. В качестве диспергируемого материала и в качестве электродов использовались изношенные пластины режущего инструмента из спеченных твердых сплавов марки ВК8. Изготовление образцов с покрытиями из порошков ВК8 на поверхности металлических изделий проведено на специализированной установке для сверхскоростного газодинамического формирования. Полученные результаты показали, что наилучшей износостойкостью обладают покрытия, полученные с использованием электроэрозионных карбидов, изготовленных методом электроэрозионного диспергирования из отходов твердых сплавов ВК8 в керосине осветительном, поскольку содержат значительно большее количество свободного углерода.
Проблема износостойкости деталей и узлов машин является одной из ведущих в технологии машиностроения. Важнейшим фактором, определяющим длительность работы различных деталей, являются физико-механические свойства их поверхности. Разработка и совершенствование методов модификации поверхности является ведущим направлением повышения качества деталей машин [1–4]. Значительный эффект в решении проблемы модификации рабочей поверхности металлических изделий дает применение технологий для осаждения слоев из твердых, жаро- и коррозионностойких материалов [5, 6]. При этом одной из новых технологий, обеспечивающей возможность модификации поверхностей конструкционных материалов, нанесения на них покрытий с защитными и другими функциями, является сверхскоростное газодинамическое формирование – одна из разновидностей газотермического напыления промышленных покрытий. Анализ показывает, что при использовании технологии сверхскоростного газодинамического формирования реально в течение длительного периода поддерживать технологическое оборудование в работоспособном состоянии без замены новым. В настоящее время значительный интерес вызывают защитные композиционные покрытия на основе карбида вольфрама, обладающие хорошими физико-механическими и химическими показателями (высокой твердостью, стойкостью к износу и воздействию агрессивной среды, низкой тепло- и электропроводностью и т.д.) [7–10].
Детали из твердых сплавов на основе карбида вольфрама в современной технике находят широкое применение. В связи с высокой стоимостью и дефицитом исходного сырья важными вопросами являются экономия вольфрама в процессе нанесения. Одним из перспективных методов получения покрытия практически из любого токопроводящего материала, в том числе и твердого сплава, отличающегося относительно невысокими энергетическими затратами и экологической чистотой процесса, является метод электроэрозионного диспергирования (ЭЭД) [11–13].
В настоящее время в современной научно-технической литературе отсутствует полноценная информация по использованию карбидов вольфрама, полученных из отходов твердых сплавов электрической эрозией, при газодинамическом формировании покрытий и влиянии их на износостойкость.
Целью настоящей статьи являлось изучение характеристик износостойкости газодинамических покрытий, полученных с использованием электроэрозионных карбидов, изготовленных методом электроэрозионного диспергирования из отходов твердых сплавов ВК8 в воде дистиллированной и керосине осветительном.
Материалы, методика экспериментов и используемые инструменты. В качестве исходного (диспергируемого) материала и в качестве электродов использовались изношенные пластины режущего инструмента из спеченных твердых сплавов марки ВК8. Рабочей жидкостью были выбраны вода дистиллированная (ГОСТ 6709–72) и керосин осветительный (ТУ 38.401-58-10–01), как жидкости, имеющие наиболее простой химический состав, достаточно высокую охлаждающую способность, а также относительно низкую стоимость.
Изготовление образцов с покрытиями из порошков ВК8 на поверхности металлических изделий проведено на специализированной установке для сверхскоростного газодинамического формирования в соответствии с ГОСТом 9.302-88 (Покрытия металлические и неметаллические неорганические), 28076-89 (Газотермическое напыление. Термины и определения), 28844-90 (Покрытия газотермические упрочняющие и восстанавливающие), 12.3.008-75 (Система стандартов безопасности труда. Производство покрытий металлических и неметаллических неорганических. Общие требования безопасности), 27953-88 (Детонационные покрытия. Общие требования). Подложка – сталь 12Х18Н10Т.
Технологический процесс сверхскоростного газодинамического формирования покрытий состоит из следующих операций: подготовка поверхности деталей перед нанесением покрытий; подготовка порошка; нанесение покрытий; контроль качества покрытий; механическая обработка; контроль качества покрытий после механической обработки.
Образцы металлических изделий подвергали струйно-абразивной обработке сухими, не загрязненными маслом, остогранными абразивами с размером зерна 1 мм в установке для пневмоструйной обработки Euroblast (фирма Guyson, Великобритания). После струйно-абразивной обработки поверхность деталей обдували сжатым воздухом для удаления остаточных загрязнений. Промежуток времени после подготовки поверхности основного металла до нанесения покрытия не превышал 0.5 ч. Порошок проходил входной контроль на соответствие паспортных данных по гранулометрическому составу, физико-химическим свойствам и условиям хранения. Отслоения (вздутия), следы местной коррозии и другие дефекты покрытия устранялись обработкой дефектного участка и повторным нанесением на него покрытия.
Нанесение покрытий осуществляли на следующих параметрах: длина ствола 300 мм; диаметр ствола 18 мм; расстояние до образца 55 мм; расход газов (м3/ч): О2 – 3.3, воздух – 1.56; С3Н8 – 0.66; расход порошка – 1500 г/ч.
Исследование износостойкости экспериментальных образцов проводили методами трибометрии с помощью автоматизированной машины трения (Tribometer, CSM Instruments, Швейцария), управляемой компьютером, по стандартной схеме испытания “шарик–диск”.
Образец устанавливали в держателе, перпендикулярно плоскости образца закрепляли стержень, на конце которого находился шарик диаметром 6 мм из оксида алюминия. С помощью регулировки датчика перемещения выбирали радиус кривизны износа, еще один датчик компенсировал силу трения и позволял установить значение коэффициента трения в определенный момент времени.
Объем удаленного материала покрытия определяли по сечению дорожки износа на поверхности образца с помощью автоматизированного прецизионного контактного профилометра Surtronic 25 производства фирмы Taylor Hobson.
Полученные результаты и их обсуждение. Обобщенные данные по результатам исследования полученных порошков представлены в табл. 1 и на рис. 1.
Таблица 1.
Результаты рентгеноспектрального микроанализа порошков, полученных в воде и керосине
Порошок | Элемент, % | |||||||
---|---|---|---|---|---|---|---|---|
С | O | S | Cl | Ti | Fe | Co | W | |
ВК8 в воде | 3.75 | 7.74 | 0.33 | 0.16 | 0.36 | 2.17 | 9.78 | 75.71 |
ВК8 в керосине | 40.91 | 2.77 | 0.33 | – | 0.59 | 0.72 | 4.03 | 50.64 |
Рис. 1.
Микроструктура и морфология порошков, полученных методом ЭДД: (а) – ВК8 в воде; (б) – ВК8 в керосине.
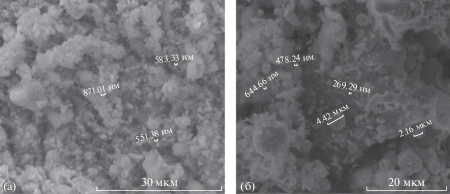
Изучение морфологии и рентгеноспектральный микроанализ порошков, полученных из отходов твердого сплава ВК8 в воде дистиллированной и керосине, выполнялся на растровом электронном микроскопе Quanta200 3D при ускоряющем напряжение 20 кВ.
В порошках, полученных в воде дистиллированной, присутствует значительная часть кислорода, а в порошках, полученных в керосине осветительном, углерода. Все остальные элементы распределены по объему частиц относительно равномерно. Показано, что основными элементами в твердых сплавах из порошков, полученных электроэрозионным диспергированием, как в керосине осветительном, так и в воде дистиллированной, являются W и Со.
Форма частиц полученного порошка в основном сферическая и эллиптическая, а их размер лежит в интервале от 100 нм до 200 мкм, однако исследования морфологии порошков методом сканирующей электронной микроскопии позволяют утверждать, что частицы величиной более 30 мкм – агломераты. Преобладающий размер частиц 500 нм–10 мкм.
Результаты исследования на растровом электронном микроскопе Quanta200 3D микроструктуры и элементного состава газодинамических покрытий на основе порошков, полученных из отходов твердого сплава ВК8 в воде дистиллированной и керосине осветительном, приведены на рис. 2 и в табл. 2.
Таблица 2.
Результаты рентгеноспектрального микроанализа полученных покрытий
Покрытие | Элемент, % | |||||||||
---|---|---|---|---|---|---|---|---|---|---|
С | O | Al | S | Ca | Ti | Cr | Fe | Co | W | |
ВК8 в воде | 3.83 | 10.33 | 0.58 | 0.10 | 0.39 | 0.89 | 0.22 | 40.33 | 5.09 | 38.23 |
ВК8 в керосине | 10.13 | 3.63 | – | 0.27 | – | 1.60 | – | 1.71 | 5.56 | 76.61 |
Исследование микроструктуры поперечного шлифа образцов показало, что получены покрытия толщиной 15–30 мкм без видимых дефектов на границе “покрытие/подложка”. Покрытия имеют смешанную структуру с хорошо проплавленными частицами порошка.
Небольшая толщина покрытий обусловлена малым размером частиц полученных порошков. В процессе нанесения покрытий порошки нагреваются в газовой струе и подаются вместе с ней на подложку. Если порошки имеют малый размер (до 5 мкм), то происходит их перегрев, и они не долетают до подложки. Ранее было установлено, что полученные порошки имеют большое процентное содержание фракции размером до 5 мкм.
Отмечено, что в покрытиях, полученных с использованием электроэрозионных карбидов, изготовленных методом электроэрозионного диспергирования из отходов твердых сплавов ВК8 в воде дистиллированной и керосине осветительном, основными элементами являются W, Co, а также углерод и кислород.
Результаты исследования износостойкости экспериментальных образцов приведены в табл. 3.
Таблица 3.
Трибологические характеристики газодинамических покрытий
Образец | Фактор износа статистического партнера (шарик Al2O3 ∅6 мм), мм3 Н–1 м–1 | Фактор износа образца, мм3 Н–1 м–1 |
---|---|---|
ВК8 в воде | 5.036 | 3.341 |
ВК8 в керосине | 5.896 | 2.150 |
Экспериментально установлено, что фактор износа статистического партнера при испытании образца с покрытием, полученным с использованием электроэрозионных карбидов, изготовленных методом электроэрозионного диспергирования из отходов твердых сплавов ВК8 в керосине осветительном, выше, чем фактор износа статистического партнера при испытании образца с покрытием, полученным с использованием электроэрозионных карбидов, изготовленных методом электроэрозионного диспергирования из отходов твердых сплавов ВК8 в воде дистиллированной. Фактор износа образца при испытании образца с покрытием, полученным с использованием электроэрозионных карбидов, изготовленных методом электроэрозионного диспергирования из отходов твердых сплавов ВК8 в керосине осветительном, ниже, чем фактор износа статистического партнера при испытании образца с покрытием, полученным с использованием электроэрозионных карбидов, изготовленных методом электроэрозионного диспергирования из отходов твердых сплавов ВК8 в воде дистиллированной.
Это подтверждается изучением дорожки износа на поверхности покрытий после испытаний на растровом электронном микроскопе Quanta200 3D (рис. 3).
Рис. 3.
Дорожки износа на поверхности покрытий после испытаний: (а) – ВК8 в воде; (б) – ВК8 в керосине.
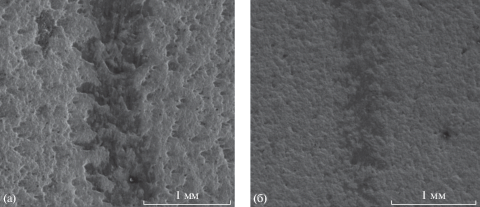
Выводы. 1. Проведенные исследования показали, что: 1) в порошках, полученных в воде дистиллированной, присутствует большая часть кислорода, а в порошках, полученных в керосине осветительном – углерода. Все остальные элементы распределены по объему частиц относительно равномерно. Показано, что основными элементами в твердых сплавах из порошков, полученных электроэрозионным диспергированием, как в керосине осветительном, так и в воде дистиллированной, являются W и Со; 2) форма частиц полученного порошка в основном сферическая и эллиптическая, размер этих частиц лежит в интервале 100 нм–200 мкм, однако исследования морфологии порошков методом сканирующей электронной микроскопии позволяют утверждать, что частицы величиной более 30 мкм – агломераты. Преобладающий размер частиц 500 нм–10 мкм.
2. Изготовленные экспериментальные образцы металлических изделий с рабочей поверхностью, модифицированной защитными износостойкими порошковыми покрытиями, обладают следующими характеристиками: 1) сформированной толщиной покрытия 15–30 мкм без видимых дефектов на границе “покрытие–подложка”; 2) основные элементы в составе покрытий вольфрам и кобальт, а также углерод и кислород; 3) наилучшей износостойкостью обладают покрытия, полученные с использованием электроэрозионных карбидов, изготовленных методом электроэрозионного диспергирования из отходов твердых сплавов ВК8 в керосине осветительном, поскольку содержат значительно большее количество свободного углерода в отличие от покрытий, полученных с использованием электроэрозионных карбидов, изготовленных методом электроэрозионного диспергирования из отходов твердых сплавов ВК8 в дистиллированной воде.
Список литературы
Погребняк А.Д. Импульсно-плазменная модификация свойств поверхности и нанесение покрытий / Под ред. А.Д. Погребняк, Ю.Н. Тюрин // Успехи физики металлов, 2003. Т. 4. № 1. С. 1.
Погодаев Л.И., Кузьмин В.Н., Третьяков Д.В. Влияние металлоплакирующих добавок к пластичным смазкам на работоспособность трибосопряжений // Проблемы машиностроения и надежности машин. 2003. № 1. С. 54.
Беневоленский С.Б., Лисов А.А. Алгоритм идентификации процессов деградации физических свойств технических объектов // Измерительная техника, 2005. № 1. С. 16.
Кравченко И.Н., Карелина М.Ю., Зубрилина Е.М., Коломейченко А.А. Ресурсосберегающие технологии получения функциональных наноструктурированных покрытий высокоскоростными методами нанесения // Вестник Донского государственного технического университета. 2015. Т. 3. № 15 (82). С. 19.
Лесневский Л.Н., Лежнев Л.Ю., Ляховецкий М.А., Трошин А.Е., Ушаков А.М. Износостойкость композитных плазменных покрытий с графитом // Ж. Проблемы машиностроения и надежности машин. 2017. № 1. С. 31.
Буяновский И.А., Левченко В.А., Большаков А.Н., Самусенко В.Д. Молибденсодержащее углеродное покрытие триботехнологического назначения и антифрикционные свойства масел при граничной смазке // Ж. Проблемы машиностроения и надежности машин, 2019. № 1. С. 86.
Choi W.B. Stress-Strain of Thermal Spray Coatings / W.B. Choi // J. Therm. Spray Technol. 2008. V. 18. № 1. P. 58.
Stokes J. The Theory and Application of the HVOF Thermal Spray Process // J. Stokes. Dublin: Dublin City University, 2005. 204 p.
Tani K. Status of Thermal Spray Technology in Japan / K. Tani, H. Nakahira // J. Therm. Spray Technol. 1992. V. 333. № 1. P. 133.
Murthy J.K.N. Abrasive wear behaviour of WC-CoCr and Cr3C2-20(NiCr) deposited by HVOF and detonation spray processes / J.K.N. Murthy, B. Venkataraman // Surf. Coat. Technol. 2006. V. 200. P. 2642.
Wanstrand O. Mechanical and tribological evaluation of PVD WC/C coatings / O. Wanstrand, M. Larsson, P. Hedenqvist // Surf. Coat. Technol. 1999. V. 111. P. 247.
Ageev E.V., Ageeva E.V., Latypov R.A. Investigation into the properties of electroerosive powders and hard alloy fabricated from them by isostatic pressing and sintering // Russian Journal of Non-Ferrous Metals. 2015. V. 56. № 1. P. 52.
Ageev E.V., Ugrimov A.S., Latypov R.A. Metallurgical features of the manufacture of hard-alloy powders by electroerosive dispersion of a T15K6 alloy in butanol // Russian metallurgy (Metally). 2016. № 12. P. 1155.
Дополнительные материалы отсутствуют.
Инструменты
Проблемы машиностроения и надежности машин