Проблемы машиностроения и надежности машин, 2021, № 3, стр. 95-100
Опыт обкатки тракторного дизеля и редуктора буровой установки с порошком наноструктурного бемита
А. В. Федотов 1, *, А. А. Гвоздев 2, А. В. Дунаев 1, Н. Н. Сергеев 3, О. В. Бармина 4
1 Федеральный агроинженерный центр ВИМ
Москва, Россия
2 Ивановская государственная сельскохозяйственная академия имени Д.К. Беляева
Иваново, Россия
3 Рязанское отделение Федерального агроинженерного центра ВИМ
Рязань, Россия
4 Институт машиноведения им. А.А. Благонравова РАН
Москва, Россия
* E-mail: fedotov48@list.ru
Поступила в редакцию 09.11.2020
После доработки 21.01.2021
Принята к публикации 24.02.2021
Аннотация
Исследованы добавки к смазочным маслам на основе наноструктурного бемита для обкатки дизеля Д-243 и редуктора буровой установки. Показано, что ввод в моторное масло М-10Г2к порошка бемита и поверхностно активного вещества до двух раз ускоряет и повышает качество приработки дизеля, обеспечивая быстрое достижение паспортных значений мощности и расхода топлива. Композиция, содержащая порошки каолина, талька, бемита и поверхностно активного вещества сокращает продолжительность обкатки редуктора буровой установки в 2.5 раза. Проведен анализ процессов, происходящих при обкатке двигателя и редуктора с разработанными добавками. Предположено, что эффективность обкатки зависит не только от физико-химических свойств компонентов добавки, но и от соотношения размера частиц компонентов и шероховатости поверхности притираемых деталей.
Постановка проблемы. Завершающей операцией в капитальном ремонте агрегатов сложных по конструкции технических объектов является обкатка, которая позволяет проверить их исправность и качество ремонта агрегатов. Происходящая при обкатке приработка обеспечивает притирку сопряжений трения, подготовку их к восприятию эксплуатационных нагрузок, предотвращает повышенное изнашивание в эксплуатации, увеличивает послеремонтный срок службы агрегатов.
Одними из сложных и ответственных агрегатов, кроме ДВС, являются агрегаты трансмиссии: ведущие мосты, коробки передач, промышленные редукторы. В соответствии с нормативно-технической документацией заводы и ремонтные предприятия обязаны подвергать эти агрегаты обкатке с приработкой и приемо-сдаточным испытаниям. Однако обычно приработку проводят только при обкатке за 0.5–1.5 ч, в результате чего основная часть приработки переносится на начальную эксплуатацию. Вынужденная работа узлов и агрегатов на эксплуатационных нагрузках с не полностью приработанными деталями может приводить к их повышенному износу, возможно образование схватывания и задира поверхностей, а в итоге – снижение межремонтного ресурса.
По этой теме во многих странах проведены разнообразные исследования режимов обкатки и испытаний, процессов, происходящих на поверхностях трения при разных этапах приработки, способов управления этими процессами, а особенно много исследований по применяемым приработочным, притирочным материалам, а также по приработочным маслам [1–4]. Основная масса исследований проведена для обкатки ДВС, а для остальных узлов и агрегатов таких исследований меньше [5, 6]. Но во всех исследованиях ставилась задача интенсификации механических, физических и химических процессов на поверхностях трения с минимумом приработочного износа.
Для ускорения процесса приработки применяют специальные обкаточные масла или вводят в товарные масла различные по механизму действия триботехнические составы (добавки). По нашему мнению, для обкатки двигателей и узлов трансмиссии можно применять наноструктурный оксигидроксид алюминия (бемит). Подобно каолину, который применяется для обкатки, бемит, являясь мягким абразивом (твердость по шкале Мооса около 3.5), может быть перспективным материалом.
Цель исследований – оценка эффективности применения наноструктурного бемита и других веществ для обкатки двигателей и агрегатов трансмиссии.
Материалы и методы исследования. В работе использовали порошок наноструктурного бемита, полученный методом гидротермального синтеза из промышленных порошков алюминия марки АД-4 [7]. Отличительной особенностью бемита, полученного таким методом, является высокая степень его однородности, стабильность состава и структуры разных партий. Использованный порошок имеет следующие характеристики: 1) твердость по минералогической шкале 3.5; 2) потери при прокаливании 15%; 3) плотность, кажущаяся 3.07 г/см3; 4) размер кристаллов 70 нм; 5) удельная поверхность 70 м2/г.
Для приготовления трибосостава для обкатки двигателя порошок бемита растирали в олеиновой кислоте, перемешивали с минеральным маслом, суспензию обрабатывали ультразвуком и вводили в картер дизеля Д-243, содержащий 15 л моторного масла М-10Г2к, из расчета содержания порошка бемита и поверхностно активного вещества (ПАВ) в картерном масле по 0.76 мас.%.
Обкатку дизеля без/с трибосоставом проводили одинаково по стандартной технологии на модернизированном обкаточно-тормозном стенде КИ-3540-ГОСНИТИ. К каждой обкатке дизель собирали с новыми деталями цилиндропоршневой группы, новыми втулками верхней головки и вкладышами шатуна.
Шероховатость поверхностей вкладышей подшипников дизеля и поршневых колец проверяли до и после приработки профилометром “Surtronic-ЗР” фирмы “Тейлор–Гобсон” (Англия). Износ сопряжений двигателя на различных стадиях приработки оценивали по массовой доле механических примесей в моторном масле, пробы которого по 300 г брали через 3 мин после начала холодной приработки, после холодной приработки, после горячей приработки и после испытания на износостойкость. Система сбора информации позволяла регистрировать во времени компрессию, характер изменения частоты вращения вала двигателя, момент на валу, давление масла в системе смазки, температуру масла и воды, расход картерных газов и топлива.
Для приготовления трибосостава для приработки сопряжений трения редуктора буровой установки, устанавливаемой на шасси автомобиля ГАЗ, дополнительно к наноструктурному бемиту использовали каолин Просяновского месторождения по ТУ 421-533-2001, тальк Шабровского месторождения марки ТМК-28 и олеат меди (готовили смешиванием олеиновой кислоты и хлорокиси меди). Компоненты сушили, готовили смесь, которую измельчали два часа в шаровой мельнице. Далее порошок перемешивали в смесителе Вернера с минеральным дизельным отработанным маслом, принятым как базовое масло (БМ), и обрабатывали ультразвуком при частоте 35 кГц в течение 20–25 мин до образования гомогенной суспензии добавки. По стандартной технологии обкатки в редуктор заливали 10 л трансмиссионного масла ТМ-3.
Редуктор с трибосоставом перед обкаткой вводили в картер редуктора с 10 л минирального дизельного отработанного масла из расчета содержания каолина, талька, бемита и ПАВ в приработочном масле редуктора в пределах, мас.%: 0.3–0.6; 0.2–0.4; 0.1–0.3, 0.06–0.08 соответственно, после чего производили обкатку редуктора по стандартной технологии.
Привод обкатываемого редуктора буровой установки осуществляли асинхронным электродвигателем мощностью 7.5 кВт с частотой вращения 750 мин–1. Во всех случаях окончание приработки определяли по снижению шума зубчатых передач и качеству сформированного контакта зубьев осмотром при вскрытии боковых крышек редуктора.
Для сравнительных исследований испытывали несколько новых составов: реметаллизант “Ресурс” (РМ) и геомодификатор трения “Форсан” (ГМТ), рекомендуемых производителями и для обкатки агрегатов.
Лабораторные испытания перечисленных составов проводили на машине трения 2070 СМТ-1 по схеме “ролик–самоустанавливающаяся колодка”. Их материалы, соответственно, сталь 40Х и сталь 45 с твердостью 50–55 HRC, шлифованные до Ra = = 0.32–0.63 мкм. Режим испытаний: частота вращения ролика 400 мин–1, в первые пятнадцать минут испытаний нагружение возрастало ступенчато с интервалом по пять минут: 1000 Н, 1250 Н, 1500 Н с ростом момента трения; во вторые пятнадцать минут нагрузка оставалась постоянной 1500 Н и шла стабилизация момента трения. Нижняя часть ролика на 1/3 была погружена в смазочную композицию. В ходе испытаний велась запись момента трения и измерялась температура масла. Продолжительность испытания каждого состава составляла 30 мин (адаптировано к техническим требованиям на обкатку агрегатов трансмиссии) с трехкратной повторностью опытов.
Результаты исследований и обсуждение. Испытания дизеля Д-243 показали, что добавка бемита способствовала ускорению приработки сопряжений “гильза–кольцо” (рис. 1) [8]. Так компрессия стабилизировалась через тридцать минут при 3.0 МПа, а без добавки – только на 80-й минуте.
Рис. 1.
Динамика компрессии при приработке дизеля [8]: 1 – с добавкой бемита; 2 – без добавки бемита.
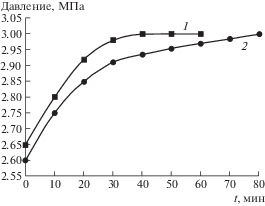
Через шестьдесят минут приработки износ первого компрессионного кольца с использованием бемита был меньше в два раза, расход картерных газов меньше в 1.6 раза, а температура масла ниже на 15–20°С. Максимальная эффективная мощность дизеля, приработанного в течение 90 мин на масле с бемитом, составила 52.5 кВт, удельный расход топлива – 257 г/л.с.ч., что близко к показателям дизеля после 50–100 ч работы. А при обкатке на товарном масле в течение тех же 90 мин наибольшая эффективная мощность была около 45 кВт, а расход топлива около 270 г/л.с.ч. После 120 мин работы дизеля износ первого компрессионного кольца оказался меньше в 2.5 раза, расход картерных газов на 12.7%, а масла на 27%.
При этом шероховатость шатунных и коренных вкладышей в приработке с бемитом, из-за их мягкости, увеличилась, а поршневых колец – уменьшилась (рис. 2). Обе шероховатости после приработки без добавки больше чем с добавкой: у шатунных вкладышей с типовой приработки – 1.87 мкм, а с добавкой – 1.35 мкм (т.е. в 1.38 раза меньше), у поршневых колец, соответственно 0.84 и 0.51 мкм (т.е. в 1.7 раза меньше).
Рис. 2.
Изменение шероховатости поверхностей деталей при разных приемах приработки: 1 – до приработки; 2 – после приработки без добавки; 3 – после приработки с добавкой бемита.
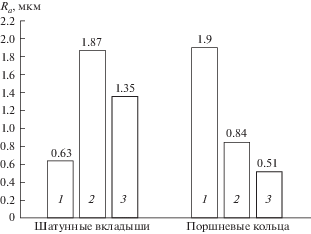
Изменение шероховатости при приработке шатунных вкладышей и поршневых колец происходит по-разному, т.к. приработка не просто обеспечивает уменьшение шероховатости, но и обеспечивает в конкретных сопряжениях ее оптимальное значение [7, 8]. Происходит переформирование поверхностей и изменение их физико-механических свойств до равновесных значений. Ее достижение приводит к снижению скорости изнашивания, коэффициента трения и тепловыделения.
В целом ввод бемита в моторное масло дизеля Д-243 уменьшил время его полной приработки, повысил износостойкость сопряжений на 22%, уменьшил приработочный износ на 5.8%, износ первого компрессионного кольца в 2.5 раза, расход картерных газов на 12.7%.
Следует отметить, что для официальных рекомендаций по применению наноструктурного бемита AlO(OH) производства ГОСНИТИ для обкатки тракторных, особенно импортных, дизелей в ремонтном производстве все же требуются дополнительные сравнительные испытания с существующими обкаточными материалами.
Принимая во внимание положения трибологии, роль бемита в трибосреде со стандартными смазками можно свести к следующему: 1) абразивное изнашивание и подшлифовка зон повышенной шероховатости сопряжений трения, повышение чистоты поверхностей, снижение механической составляющей коэффициента трения; 2) очистка поверхностей трения от наслоений, оксидных пленок и дефектных структур, что обеспечивает доступ веществ трибосреды к ювенильным поверхностям металлов и ускоряет образование антифрикционных покрытий; 3) некоторая последующая адсорбция на поверхностях частиц бемита смолистых веществ, что создает частицы, разделяющие детали (“третьи тела” в трибопаре), уменьшающие коэффициент трения.
Разработанная добавка кроме мягкого абразивного трения осуществляет адсорбционное снижение прочности и пластифицирование трущихся поверхностей воздействием ПАВ (эффект академика П.А. Ребиндера).
Результаты испытаний показали, что применение наноструктурного бемита в обкаточном составе для приработки двигателей повышает нагрузочную способность пары трения на 16–17%, снижает коэффициент трения на 10–30%, а теплонапряженность узлов трения на 6–15%. Разработаны и рекомендации по обкатке ДВС с использованием наноструктурного бемита.
Притирочная добавка на основе наноструктурного бемита хорошо зарекомендовала себя в условиях приработки деталей ДВС с твердостью 52–56 HRC и 10–11 классом чистоты. Зубья зубчатых колес в трансмиссиях (стали типа 18ХГТ) и подшипники качения (стали типа ШХ-15) имеют твердость 179–207 МПа или 61–63 HRC при классе чистоты 7–8 с шероховатостью Rz 3.2–6.0 мкм. Нанодисперсность частиц бемита (размер кристаллов менее 100 нм, агрегатов менее 1 мкм) приводит к их вдавливанию в глубокие впадины шероховатостей грубых поверхностей зубьев зубчатых колес и, видимо, поэтому абразивность порошка бемита в агрегатах трансмиссий оказалась слабой. Кроме того, в условиях трения и повышенной температуры в точках контакта бемит может разлагаться с выделением воды и образованием безводных форм оксидов алюминия. При этом происходит самоизмельчение исходных кристаллов и агрегатов, что еще больше уменьшает их размер [9]. Температура, соответствующая образованию частиц минимального размера, составляет около 500°С.
Исходя из этого для приработки агрегатов трансмиссии была разработана добавка, содержащая наноструктурный бемит, ПАВ, тальк и каолин. В ходе предварительных исследований была найдена область оптимальных количеств ингредиентов комплексной добавки, при этом функциями отклика в испытаниях служили: скорость снижения (стабилизации) момента трения, температуры, площадь приработанной поверхности (доля в геометрической площади контакта) в равных условиях испытаний по нагрузке, скорости скольжения и времени испытаний.
Результаты испытания экспериментального состава в сравнении с результатами испытаний известных притирочных составов показали ускорение приработки, снижение температуры смазки, увеличение площади приработанной поверхности деталей (табл. 1).
Таблица 1.
Показатели процесса приработки исследуемых образцов
Смазочный состав | Момент трения, в начале/в конце Мтр. нач/Мтр. кон | Скорость изменения момента трения, Н см/мин | Температура в конце опыта, °С | Площадь приработанной поверхности, % |
---|---|---|---|---|
БМ | 230/215 | 1.00 | 74.5 | 30–35 |
БМ+РМ | 195/175 | 1.33 | 72.8 | 40–45 |
БМ+ГМТ | 225/190 | 2.33 | 64.2 | 65–70 |
БМ+ЭК | 245/195 | 3.33 | 61.4 | 75–80 |
Производственные испытания разработанной приработочной добавки провели на редукторе мобильной буровой установки. Его конструктивной особенностью является наличие высокотвердых зубчатых колес, опорных подшипников, отсутствие цветных металлов и мягких сплавов. Введение в композицию повышенного количества (до 2-х раз в сравнении с добавкой для обкатки ДВС) абразивов умеренной твердости (каолин, тальк, бемит) и ПАВ, обладающего дезагрегирующими свойствами, повышающего седиментационную устойчивость композиции и обеспечивающего эффект П.А. Ребиндера привело к ускорению приработки.
Получено сокращение длительности обкатки редуктора в 2.5 раза по сравнению с обкаткой на штатном трансмиссионном масле ТМ-3. Добавка позволяет эффективно приработать детали, сформировать полное пятно контакта в зацеплении зубьев зубчатых колес, шлицевых валов и подшипников. А после слива обкаточного масла и заправки штатного заметно снизился шум, нагрев корпуса, что предполагает повышенный ресурс редуктора.
Положительный эффект добавок каолина и талька видимо обусловлен также соответствующими для приработки зубчатых колес их физико-механическими свойства и размерами частиц (единицы мкм), сопоставимыми с размерами неровностей поверхностей деталей редуктора. Они термически более стабильны и не разлагаются при температурах 400–500°С, как бемит с образованием более мелких частиц. Частицы талька и каолина истирают микронеровности трущихся поверхностей, увеличивая площадь опорной поверхности контакта, снижая удельные нагрузки и препятствуя тем самым появлению задиров. Попадая между трущимися деталями, нивелируя поверхности, они могут адсорбировать смолистые и окисленные продукты среды. Каолин с более крупными частицами активно участвует в абразивной притирке поверхностей зубьев зубчатых колес, открывает ювенильные их поверхности и способствует более активному действию ПАВ по эффекту академика П.А. Ребиндера. Тальк, как пластичный, дисперсный порошок, служит промежуточным материалом между частицами каолина и вместе с бемитом способствует более равномерному распределению частиц каолина в притирочной композиции и в приработочном масле.
Заключение. Ввод в масла бемита до 2-х раз ускоряет и повышает качество приработки ДВС, обеспечивает быстрое достижение паспортных значений мощности и расхода топлива. Разработанная приработочная композиция для обкатки редукторов, содержащая каолин, тальк, бемит и ПАВ обеспечивает сокращение длительности их обкатки в 2.5 раза. Эффективность приработки зависит не только от физико-механических свойств компонентов добавки, но и от соотношения размера частиц компонентов и шероховатости поверхности прирабатываемых деталей.
Список литературы
Долгополов К.Н., Потеха В.Л., Любимов Д.Н. Трибология геомодифицированных смазочных материалов: Монография. Гродно: ГГАУ. 2013. 430 с.
Дунаев А.В., Лялякин В.П., Соловьев Р.Ю. Технологические рекомендации по повышению ресурса агрегатов тракторов ремонтно-восстановительными добавками к смазочным маслам. М.: ФГБНУ “Росинформагротех”, 2013. 96 с.
Лазарев С.Ю. О концептуальных вопросах исследований в области трибологии природных минеральных материалов // М.: Труды ГОСНИТИ, 2016. Т. 124. Ч. 2. С. 47.
Лялякин В.П., Соловьев Р.Ю., Ольховацкий А.К., Гительман Д.А. Повышение послеремонтной безотказности отремонтированных ДВС и трансмиссий применением наноматериалов // М.: Труды ГОСНИТИ, 2013. Т. 113. С. 90.
Белый И.Ф., Меркулов А.Ф., Белый В.И., Голубев И.Г. Эффективное использование антифрикционных добавок к трансмиссионным и моторным маслам. М.: ФГНУ “Росинформагротех”, 2011. 52 с.
Чечет В.А. Избирательный способ ремонта агрегатов машин // М.: Труды ГОСНИТИ, 2011. Т. 107. Ч. 2. С. 3.
Берш А.В., Иванов Ю.Л., Мазалов Ю.А., Глухов А.В., Трубачев О.А. Способ получения гидроксидов или оксидов алюминия и водорода. Патент 2278077. 2006.
Мазалов Ю.А., Соловьев Р.Ю., Сергеев Н.Н., Федотов А.В., Дунаев А.В., Витязь П.А., Судник Л.В. Исследование триботехнических свойств наноструктурного бемита // Трение и износ, 2015. Т. 36. № 6. С. 627.
Bersh A.V., Mazalov D.Yu., Solov’ev R.Yu., Sudnik L.V., Fedotov A.V. Nanostructured Disaggregated Aluminum Hydroxide and Oxide Powders // Refractories and Industrial Ceramics. 2016. V. 57. P. 364.
Дополнительные материалы отсутствуют.
Инструменты
Проблемы машиностроения и надежности машин