Проблемы машиностроения и надежности машин, 2021, № 3, стр. 101-106
Абразивостойкость композитов на эпоксидной основе с наполнителями из составляющих шлама от заточки металлорежущего инструмента
А. М. Михальченков 1, И. В. Козарез 1, С. А. Феськов 1, И. Н. Кравченко 2, *, Ю. А. Кузнецов 3, А. Д. Быкова 4
1 Брянский государственный аграрный университет
Брянская обл., Выгоничский р-н, с. Кокино, Россия
2 Институт машиноведения им. А.А. Благонравова РАН
Москва, Россия
3 Орловский государственный аграрный университет им. Н.В. Парахина
Орел, Россия
4 Институт проблем машиноведения РАН
Санкт Петербург, Россия
* E-mail: kravchenko-in71@yandex.ru
Поступила в редакцию 07.12.2020
После доработки 21.01.2021
Принята к публикации 24.02.2021
Аннотация
Изменение абразивостойкости при испытании композитов с эпоксидной матрицей, наполненных составляющими шлама от заточки режущего инструмента, имеет одинаковый характер для всех составов и отражает процесс самоорганизации изнашивания. Максимальную стойкость к абразивному изнашиванию имеет композит с наполнителем из абразивных частиц заточных кругов.
В исследованиях [1, 2] показана возможность применения в качестве антиабразивных покрытий дисперсных композитов с эпоксидной матрицей. Увеличение стойкости к абразивному изнашиванию в этом случае достигается введением в клееполимерную основу дисперсной абразивостойкой компоненты, состоящей из фракций природного песка [3]. Определенные возможности в этом плане заложены в эпоксидных композитах с наполнителями из составляющих шлама от заточки металлообрабатывающего инструмента. Примером могут служить исследования, в которых получены положительные результаты при применении шлифовальных металлоабразивных отходов подшипникового производства в качестве компонентов порошковых материалов для формирования покрытий повышенной износостойкости, которые могут быть альтернативой монолитной износостойкой керамике [4–9]. В качестве антиабразивных керамических материалов или покрытий на их основе могут выступать материалы, включающие керамическую основу с высоким содержанием компонентов слоистой структуры, к таким материалам также можно отнести армированные материалы [10–12].
Необходимо отметить, что полимерные композиты с наполнителями из абразивных компонентов, природного или искусственного происхождения, имеют широкие перспективы при использовании их в машиностроении и других отраслях промышленности как износостойких материалов для предупреждения, торможения и устранения износов рабочих поверхностей [13]. Кроме этого они могут выполнять функции покрытий, способствующих повышению ресурса деталей. Весьма важно и то, что нанесение покрытий из таких материалов проходит в жидкой фазе и позволяет устранять дефекты любой формы на поверхности с различной геометрией [14]. Однако малочисленность информации о сопротивляемости изнашиванию композитов на основе эпоксидной смолы с наполнителями из компонентов шлама от заточки режущего инструмента при перемещении в незакрепленном абразиве не дает оснований в полной мере оценить их значимость как противоабразивных покрытий.
Поэтому необходимо провести серию экспериментов, направленных на выявление абразивостойкости (c) эпоксидных композитов с наполнителями из составляющих шлама от заточки металлорежущего инструмента.
Материалы и методика исследований. В качестве матрицы композита использовался клеевой, самотвердеющий состав со следующими компонентами: эпоксидная смола ЭД-20 (100 частей) и полиэтиленполиамин (отвердитель, 7 частей) [15]. Испытывались композиционные материалы с матрицей из вышеуказанного эпоксидного состава и наполнителями из: шлама отходов заточного производства; магнитно-отсепарированных частиц твердых сплавов и быстрорежущих сталей; абразивных составляющих заточных кругов. Изучаемые композиты представляли собой совокупность компонентов из эпоксидного клеевого состава – 30 мас.ч. и дисперсно-армирующих наполнителей – 70 мас.ч. [16].
Абразивной средой служил состав из кварцевого песка с размерами частиц около 0.20 мм (70%) и 30% гранитной крошки с размерами фракций 9.2 мм. Выбор подобного состава базировался на том, что большинство разрабатываемых грунтов имеют гравиевидные включения. Наличие гранитной крошки в абразивной массе будет способствовать ускорению времени испытаний.
Эксперименты проводились на установке, разработанной в Брянском ГАУ, которая позволяет проводить изучение нескольких составов одновременно при соблюдении идентичности испытаний для всех изучаемых материалов в любой момент времени, что особенно важно при исследовании веществ одной природы, но разных составов [17]. Перемещение образцам задается вращением шпинделя фрезерного станка со скоростью n = 800 мин–1 [18]. При этом контроль износа осуществлялся известным методом “лунок”.
Устройство (рис. 1а) работает следующим образом. Опытные образцы 1 устанавливаются на оправку 2, имеющую упор 3 и фиксируются зажимной гайкой 4. Испытуемые образцы устанавливаются через определенные промежутки с помощью промежуточных втулок 5 меньшего диаметра. В емкости 6, установленной на столе станка 7, находится абразив 8. Исследуемые материалы погружаются в абразив на такую глубину, чтобы промежуточные втулки 5 его не касались и приводятся во вращение с одновременным перемещением абразива, находящимся в емкости, в продольном направлении.
Рис. 1.
Схема проведения испытаний: (а) – схема установки; (б) – натурная установка (съемка в период проведения испытаний).
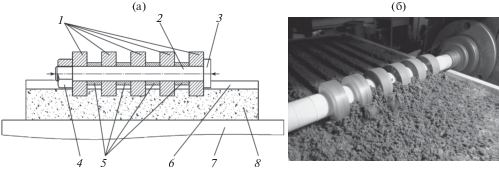
Для исключения повторного перемещения образцов по тому же следу, и для обеспечения перемешивания истирающей массы, емкость с абразивом периодически смещается в поперечном направлении.
Всего испытывалось шесть образцов с наполнителями из составляющих шлама заточного производства (Э + Ш), магнитно-отсепарированных частиц материалов инструментов, изготовленных из быстрорежущих сталей и твердых сплавов (Э + Тв) и абразивных составляющих заточных кругов (Э + А) (где Э – эпоксидная матрица). Лабораторные испытания в реальном времени показаны на рис. 1б.
Диаметры наружный и внутренний и ширина контактирующей поверхности образцов – 80 мм, 22 мм, 20 мм соответственно; длина, ширина и глубина емкости 700 мм, 450 мм, 90 мм соответственно.
Результаты экспериментов. Экспериментами установлено, что характер изменения стойкости к абразивному изнашиванию композитов с эпоксидной основой наполненных составляющими шлама от заточки режущего инструмента одинаков для всех составов (рис. 2), независимо от природы наполнителя. На графиках прослеживаются два типичных, ярко выраженных участка (обозначены цифрами, расположенными внутри окружности). Это обусловлено явлением самоорганизации процесса износа [19].
Рис. 2.
Изменение износостойкости во времени испытаний: (а) – (Э + А); (б) – (Э + Тв); (в) – (Э + Ш) (цифрами в окружностях показаны характерные участки).
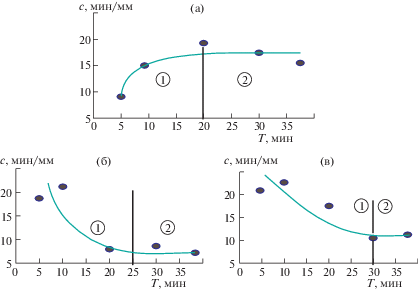
Первый участок характеризует процесс адаптации (приработки) материала к абразивной среде. Второй – изнашивание при фактически полной совместимости абразивной среды и поверхности испытуемого композита.
В реальных условиях, применительно к конкретным изделиям принято считать с величиной постоянной и явление самоорганизации изнашивания в большинстве случаев не рассматривается. Однако в последнее время на этот фактор стали обращать серьезное внимание т.к. в условиях интенсивного абразивного изнашивания нередко имеют место случаи, когда значение износа в момент приработки бывает столь велико, что изделия снимаются с дальнейшей эксплуатации вследствие невозможности выполнения ими заданных функций.
Стабилизация процесса изнашивания для композита, наполненного частицами абразива от частиц заточного круга, сопровождается ростом износостойкости в период приработки (рис. 2а). При наличии в эпоксидной матрице дисперсных наполнителей в виде фракций от заточки инструментов (рис. 2б) и шлама (рис. 2в) имеет место снижение стойкости к абразивному изнашиванию на первом участке с последующим выходом на постоянное значение c.
Разница в протекании процессов самоорганизации изнашивания для изучаемых композитов кроется в том, что степень оседания минеральных частиц наполнителя, состоящего из фракций заточного круга (в данном случае карборунда) выше аналогичного показателя для металлических компонентов. В связи с этим, количество фракций наполнителя из абразивостойких составляющих в поверхностных слоях несколько меньше чем количество металлических частиц и частиц шлама, что и приводит к более высокой c композитов с этими наполнителями в период адаптации процесса износа (рис. 2б, в, область 1).
Рассмотрим причины повышенной износостойкости для композита с наполнителем из абразивных частиц заточных кругов в установившемся режиме испытаний (рис. 2а). В процессе заточки инструмента, в силу высокой теплостойкости абразивных фракций при удалении из круга при заточке, они не претерпевают существенных изменений своих свойств, прежде всего твердости [20]. Это подтверждается использованием кругов с карборундовыми фракциями (SiC) теплостойкость, которых составляет около 1800°C. При этом мгновенная контактная температура при заточке не превышает 1200°С. Микротвердость частиц SiC достигает до 2600 МПа (9 единиц по Моосу или 1300 HRC). Кроме этого, сравнительно высокие адгезионные свойства абразивных частиц к различного рода связующим вызывают существенные затруднения при их удалении с поверхности при проведении испытаний на изнашивание. Указанные факторы обеспечивают достаточно высокую износостойкость материалов, составляющую порядка 17.5 мин/мм (рис. 2а).
В свою очередь, не высокая c при установившемся режиме испытаний композитов с наполнителями из металлических частиц от заточки инструментов (рис. 2б) объясняется потерей ими механических свойств, прежде всего твердости, вследствие влияния высоких контактных температур, которая способствует выгоранию легирующих элементов и пережогу железоуглеродистых составляющих. Данное обстоятельство подтверждается тем, что теплостойкость твердых сплавов находится в пределах 800–850°С, а быстрорежущих сталей около 600°С, тогда как мгновенная контактная температура при заточке, как уже отмечалось, составляет около 1200°С. Немаловажное значение имеет и относительно не высокая адгезионная способность этого материала.
Испытания композита с наполнителем из шлама показало некоторое повышение стойкости к абразивному изнашиванию по сравнению с износостойкостью материала, наполненного металлическими частицами от заточки инструментов, что связано с присутствием в наполнителе частиц составляющих заточных кругов.
Для большей наглядности итоговые данные по абразивной износостойкости композитов на эпоксидной основе с наполнителями из составляющих шлама от заточки металлорежущего инструмента представлены на рис. 3.
Наибольшая износостойкость присуща композитам дисперснонаполненным частицами отходов от абразивных кругов после проведения работ по заточке инструмента из быстрорежущей стали и твердых сплавов, которая составляет 17.5 мин/мм. Наименьшей стойкостью к абразивному изнашиванию (7.5 мин/мм) обладают композиционные материалы, у которых в качестве наполнителей используются металлические фракции от заточки инструментов.
Выводы. 1. Характер изменения стойкости к абразивному изнашиванию во времени испытаний (T) композитов с эпоксидной основой, наполненных составляющими шлама от заточки режущего инструмента одинаков для всех составов, независимо от природы наполнителя, и имеет два типичных участка, отражающих процесс самоорганизации износа. 2. Максимальная износостойкость (17.5 мин/мм) присуща композиту с наполнителем из абразивных частиц заточных кругов вследствие высокой теплостойкости и твердости карборунда. 3. Не высокая стойкость к абразивному изнашиванию (7.5 мин/мм) у композитов с наполнителями из металлических частиц от заточки инструментов связана с потерей твердости из-за выгорания легирующих элементов и пережога металлический фракций. 4. Присутствие в композите наполнителя из шлама и металлических частиц в некоторой степени проводит к увеличению абразивостойкости (11.5 мин/мм) из-за присутствия в наполнителе фракций компонентов заточных кругов.
Список литературы
Филин Ю.И. Эпоксидный композит для повышения ресурса термоупрочненных лемехов // Сельский механизатор. 2017. № 5. С. 36.
Mostovoi A.S., Kurbatova E.A. Controlling the properties of epoxy composites filled with brick dust // Russian Journal of Applied Chemistry. 2017. V. 90. № 2. P. 267.
Mikhalchenkov A.M., Torikov V.E., Filin Y.I. The influence of the concentration of components of an epoxy–sandy composite on its abrasive-wear resistance // Polymer Science. Series D. 2018. V. 11. № 1. P. 47.
Latypov R.A., Latypova G.R., Ageev E.V., Altukhov A.Y., Ageeva E.V. Properties of the coatings fabricated by plasma-jet hard-facing by dispersed mechanical engineering wastes // Russian metallurgy (Metally). 2018. V. 2018. № 6. P. 573.
Latypov R.A., Ageev E.V., Altukhov A.Y., Ageeva E.V. Effect of temperature on the porosity of the additive products made of the dispersed wastes of cobalt–chromium alloys // Russian metallurgy (Metally). 2019. V. 2019. № 12. P. 1300.
Perevislov S.N., Markov M.A., Motailo E.S., Vikhman S.V., Titov D.D. Physical and mechanical properties of composite materials in the MoSi2-SiC-TiB2 system // IOP Conference Series: Materials Science and Engineering. 2020. V. 848–012067. P. 1.
Perevislov S.N., Lysenkov A.S., Titov D.D., Omkovich M.V., Nesmelov D.D., Markov M.A. Materials based on boron carbide obtained by reaction sintering // IOP Conference Series: Materials Science and Engineering. 2019. V. 525. № 1. Iss. 1. P. 012074.
Perevislov S.N., Lysenkov A.S., Titov D.D., Kim K.A., Tomkovich M.V., Nesmelov D.D., Markov M.A. Liquid-sintered SiC based materials with additive low oxide oxides // IOP Conference Series: Materials Science and Engineering. 2019. V. 525. № 1. Iss. 1. P. 012073.
Марков М.А. Комбинированные технологии получения функциональных покрытий для изделий авиационной и морской техники. Актуальные проблемы прочности. Монография / Под редакцией В.В. Рубаника. Молодечно. 2020. С. 34.
Frolova M.G., Lysenkov A.S., Titov D.D., Istomina E.I., Perevislov S.N. Properties of composites SiC/SiCf obtained by hot pressing of SHS of silicon carbide powder // IOP Conference Series: Materials Science and Engineering. – IOP Publishing, 2020. V. 848. № 1. P. 012113.
Perevislov S.N., Afanas’eva L.E., Baklanov N.I. Mechanical properties of sic-fiber-reinforced reaction-bonded silicon carbide // Inorganic materials. 2020. V. 56. № 4. P. 425.
Frolova M.G., Kargin Y.F., Lysenkov A.S., Perevislov S.N., Titov D.D. et al. SiC-Fiber Reinforced Silicon Carbide-Based Ceramic Composite // Inorganic Materials. 2020. V. 56. № 9. P. 987.
Михальченков А.М., Гуцан А.А., Феськов С.А., Козарез М.В., Дьяченко А.В. Износостойкий плужный лемех. РФ Патент 2695867, 2019.
Бирюлина Я.Ю. Устранение сквозных износов лап культиваторов “моррис” клееполимерными композитами // Труды ГОСНИТИ. 2015. Т. 119. С. 264.
Mikhalchenkov A.M., Kozarez I.V., Tyureva A.A., Kuzmin V.N. Procedure for comparative accelerated testing of materials for resistance to abrasive wear as they move in a loose abrasive environment // Polymer Science. Series D. 2018. V. 11. № 1. P. 110.
Mikhalchenkov A.M., Mikhalchenkova M.A., Feskov S.A., Kononenko A.S. Effect of concentration and dispersion of filler fractions on adhesive strength and abrasion resistance of an epoxy and sand composite // MATEC Web of Conferences. 298. P. 1.
Михальченков А.М., Ториков В.Е., Дьяченко А.В., Анищенко А.В. Методика определения абразивной износостойкости материалов с различными свойствами. Все материалы. Энциклопедический справочник. 2018. № 4. С. 40.
Михальченков А.М., Бирюлина Я.Ю., Михальченкова М.А. Интенсивность изнашивания покрытия из шламо-эпоксидной абразивостойкой композиции от скорости его перемещения // Материаловедение. 2016. № 8. С. 36.
Zelinskyi V.V., Borisova E.A. About the quantum-mechanical nature of wear on magnetized cutting and deforming tools. Proceedings of 2015 International Conference on Mechanical Engineering, Automation and Control Systems, MEACS. 2015. P. 7414978.
Зубарев Ю.М., Юрьев В.Г. Абразивные инструменты. Разработка операций шлифования. Санкт-Петербург: Лань, 2018. 360 с.
Дополнительные материалы отсутствуют.
Инструменты
Проблемы машиностроения и надежности машин