Проблемы машиностроения и надежности машин, 2021, № 3, стр. 3-10
Влияние конструкции сопловой системы аппаратов электродуговой металлизации на условия распыления проволочных материалов
В. М. Гусев 1, О. Ю. Елагина 1, Н. С. Нестеренко 1, *, А. Г. Буклаков 1
1 Российский государственный университет нефти и газа
Москва, Россия
* E-mail: nesterenko.n@gubkin.ru
Поступила в редакцию 27.10.2020
После доработки 17.02.2021
Принята к публикации 24.02.2021
Аннотация
В статье рассмотрено конструктивное влияние соплового вооружения металлизаторов (сопло трубка, сопло диафрагма) на геометрию и физические особенности потока транспортного газа при давлении системы 0.4 и 0.5 МПа, что влияет на механику перемещения и диспергирования напыляемого материала. В статье представлен начальный этап оценки влияния технологических параметров режима электродуговой метализации на воздействие транспортируемого распыляемого материала, дробление, испарение, геометрию, как прогнозируемую результирующую процесса.
Процесс электродуговой металлизации (ЭДМ) заключается в распылении потоком сжатого воздуха двух электропроводных проволок, между которыми горит электрическая дуга. Под действием струи транспортирующего газа расплавленный металл эвакуируется с электродов, дробится на мелкие капли и переносится на обрабатываемую поверхность. В зависимости от скорости истечения газа и его плотности изменяется динамическое давление на эвакуируемый материал. Это приводит к изменению условий его диспергирования и переноса к поверхности изделия, что в свою очередь определяет такие характеристики качества газотермического покрытия как адгезионная прочность и пористость покрытия. Как показано в работах [1–3] изменение динамического давления на различном расстоянии от сопла металлизатора характеризуется нелинейной зависимостью.
Целью настоящей статьи являлось исследование влияния конструкции сопла металлизатора на изменение динамического давления и диспергирование распыляемого материала при ЭДМ.
Расчетный анализ влияния параметров потока газа на диспергирование капли для различных сопловых устройств металлизаторов. Электродуговые металлизаторы работают при подаче воздуха на входе в сопловое устройство под давлением Р1 в пределах 0.4‒0.7 МПа, что соответствует критическому режиму его истечения при выходе из сопла. Его давление на срезе сопла Р2 устанавливается выше давления наружной среды и зависит исключительно от показателя адиабаты воздуха, который для двухатомных газов равен 0.528 [5].
На степень расширения воздуха и величину давления на срезе сопла Р2 влияет конструкция сопла металлизатора. Наиболее широко распространены два вида сопловых устройств электродуговых металлизаторов: сопло-трубка и сопло-диафрагма с острой кромкой (рис. 1).
Рис. 1.
Конфигурация соплового вооружения электродуговых металлизаторов (1): (а) – сопло-диафрагма; (б) – сопло-трубка.
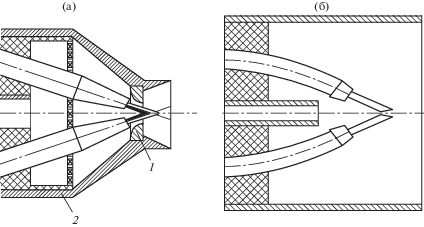
Каждый вариант имеет свои положительные и отрицательные свойства.
При работе конструкции с соплом-диафрагмой воздух из магистрали поступает в колпак 2. При этом в результате первого расширения давление Р2 уменьшается в 0.528 раза по отношению к давлению на входе в сопло Р1. Повторное уменьшение давления происходит при прохождении потока через диафрагму. В результате двойного разряжения давление на выходе из сопла-диафрагмы составляет
При использовании сопла-трубки снижение давления Р1 и плотности газа происходит только один раз. Поэтому давление Р2 в сопле-трубке значительно выше, чем при сопле-диафрагме и составляет
Давление Р2 определяет условия формирования капли электродного металла на торце проволок при их плавлении. Изменение геометрических размеров капли в газовом потоке происходит под действием сил, возникающих в результате динамического давления газа [3, 4]
где: Сх – коэффициент формы тела, принятый для тел шарообразной или цилиндрической формы равным Сx = 0.4 [6–8]; W – скорость потока газа, м/с; ρ – плотность набегающего потока, кг/м3.Распад исходной капли характеризуется критерием Вебера (We) и зависит от отношения динамического давления к давлению сил поверхностного натяжения [6, 7]
(4)
$We = \frac{{{{P}_{{\text{д}}}}}}{{{{Р}_{{\text{ж}}}}}} = \frac{{{{Р}_{{\text{д}}}}{{d}_{{\text{к}}}}}}{{4\sigma }},$Коэффициенты поверхностного натяжения расплавленных металлов находятся в интервале 0.73–1.73 Дж/м2 и составляют для Al 0.914–0.924 Дж/м2; Zn 0.730–0.814 Дж/м2; Fe 1.720–1.730 Дж/м2.
По данным работы [1] исходный размер капли электродного металла, формируемой на торце электрода составляет для алюминия порядка 1 мг, что соответствует эквивалентному диаметру 1.0–0.9 мм. Исходя из этого максимального размера исходной капли электродного металла был выполнен расчет изменения числа Вебера в зависимости от динамического давления по формулам (2)–(4). Диапазоны значений критерия Вебера, определенные для разных металлов показаны на рис. 2.
Рис. 2.
Изменение критерия Вебера в зависимости от динамического давления для разных металлов при исходном диаметре капли на торце электрода 1.0 мм.
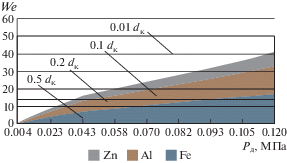
В зависимости от значения числа Вебера исходная капля расплавленного металла подвергается дроблению.
Режимы дробления и данные по изменению размеров капли в зависимости от числа Вебера, обобщенные по данным разных источников [5, 6, 8] применительно к плазменно-дуговому напылению, показаны в табл. 1.
Таблица 1.
Сводная информация для процесса диспергирования капли напыляемых материалов методом ЭДМ
Критерий Вебера | Фактический размер капли | Критерий Вебера | Фактический размер капли |
---|---|---|---|
We < 8 | dф = dк | 20 ≤ We < 50 | ${{d}_{{\text{ф}}}} = \frac{{{{d}_{{\text{к}}}}}}{{100}}$ |
8 ≤ We < 10 | ${{d}_{{\text{ф}}}} = \frac{{{{d}_{{\text{к}}}}}}{2}$ | 50 ≤ We < 100 | ${{d}_{{\text{ф}}}} = \frac{{{{d}_{{\text{к}}}}}}{{200}}$ |
10 ≤ We < 14 | ${{d}_{{\text{ф}}}} = \frac{{{{d}_{{\text{к}}}}}}{{3{\kern 1pt} - {\kern 1pt} 5}}$ | 100 ≤ We < 350 | ${{d}_{{\text{ф}}}} = \frac{{{{d}_{{\text{к}}}}}}{{700}}$ |
14 ≤ We < 20 | ${{d}_{{\text{ф}}}} = \frac{{{{d}_{{\text{к}}}}}}{{10}}$ | – | – |
Экспериментальные исследования по определению динамического давления. С целью определения динамического давления струи воздуха, выходящего из сопловых устройств металлизатора рассматриваемых конструкций, были проведены экспериментальные исследования на модельных образцах. Экспериментальная установка, представленная на рис. 3, включала в себя модель распылительной системы, выполненные с помощью 3Д-печати, устройство для замеров давления в разных положениях и сопловые устройства.
Сопло-диафрагма имело внутренний диаметр 6 мм и длину 70 мм. Сопло-трубка для обеспечения аналогичного проходного сечения для воздуха имеет внутренний диаметр 8 мм. Испытания проводились при исходном давлении воздуха 0.4 МПа и 0.5 МПа.
Для замера динамического давления использовалась заборная трубка с внутренним диаметром 0.75 мм, к которой при помощи шлангов присоединялся манометр KFM с точностью 0.1 кг/см2 и вакуумметр МЗМ с точностью 0.25 кгс/см2. Заборная трубка была установлена на суппортную группу станка, осуществляющую продольное и поперечное контролируемое перемещение. Такая установка позволяет измерять динамическое давление на различном расстоянии от среза проволок в двух направлениях – по оси потока и в радиальном направлении под углом к плоскости подачи проволок.
Результаты измерения динамического давления по оси истечения воздуха на разных расстояниях от стыка проволок для варианта распылительной системы сопло-диафрагма представлены на рис. 4.
Рис. 4.
Распределение динамического давления вдоль оси потока транспортирующего газа (ТГ) по оси потока для сопла-диафрагмы при давлении: 1 – Р1 = 0.4 МПа; 2 – Р1 = 0.5 МПа.
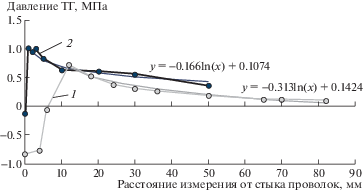
Как видно из результатов экспериментов, непосредственно у стыка проволок имеется зона разряжения. Затем происходит резкий рост динамического давления до максимального значения. Расстояние от стыка проволок до точки, в которой регистрируется максимальное значение динамического давления в зависимости от исходного давления Р1 составляет для 0.4 МПа 12 мм, а для 0.5 МПа 1 мм. Используя линейную аппроксимацию для определения протяженности зоны разряжения в исследованном диапазоне давлений, получаем следующую зависимость для расчета требуемого расстояния от сопла, на котором необходимо располагать срез проволок для получения максимального динамического давления L
Исходя из допущения о наличии линейной зависимости между изменением статического давления Р2 и динамического давления на основе полученных экспериментальных данных зависимость (5) можно представить в виде
где n, m – коэффициенты пропорциональности, определяемые экспериментально.Для расчета значений коэффициентов пропорциональности n и m была выполнена обработка полученных зависимостей, характеризующих положение линий тренда (табл. 2).
Таблица 2.
Результаты расчета коэффициентов пропорциональности для сопла-диафрагмы
Давление на входе и выходе из сопла-диафрагмы | Экспериментальные данные | ||
---|---|---|---|
Давление Р1, МПа | Давление Р2, МПа | Рmax | а |
0.5 | 0.138 | 0.1074 | 0.0166 |
0.4 | 0.111 | 0.0525 | 0.0313 |
Линейная аппроксимация | $2.0341{{Р}_{2}} - 0.173$ | $0.0917 - 0.544{{Р}_{2}}$ |
Подставляя коэффициенты пропорциональности в формулу (6) было получено уравнение для расчета динамического давления при использовании сопла-диафрагмы
(7)
${{Р}_{{\text{д}}}} = \left( {2.0341{{Р}_{2}} - 0.173} \right) - \left( {0.0917 - 0.544{{Р}_{2}}} \right)\ln \left( х \right).$Полученная зависимость характеризует распределение динамического давления в интервале [х0 = L; xi > L] по дистанции распыления по оси потока транспортирующего газа. Результаты замеров динамического давления с использованием модельного сопла-трубки представлены на рис. 5.
Рис. 5.
Распределение динамического давления вдоль оси потока транспортирующего газа при радиальном перемещении под углом относительно плоскости проволок для сопла-трубки: 1 – Р1 = 0.5 МПа; 2 – Р1 = 0.4 МПа.
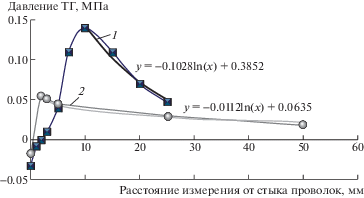
Обработка данных трендов экспериментальных данных, полученных на сопле-трубке, была выполнена аналогично данным по соплу-диафрагме (табл. 3).
Таблица 3.
Результаты расчета коэффициентов пропорциональности для сопла-трубки
Давление на входе и выходе из сопла-трубки | Экспериментальные данные | ||
---|---|---|---|
Давление Р1, МПа | Давление Р2, МПа | Рmax | а |
0.5 | 0.138 | 0.38520 | 0.1028 |
0.4 | 0.111 | 0.06352 | 0.0112 |
Линейная аппроксимация | $11.914{{Р}_{2}} - 1.259$ | $3.393{{Р}_{2}} - 0.365$ |
В результате получена следующая зависимость для расчета изменения динамического давления для сопла-трубки для интервала значений [х0= L; xi > L] по дистанции распыления по оси потока транспортирующего газа
(8)
${{Р}_{{\text{д}}}} = \left( {11.914{{Р}_{2}} - 1.259} \right) - \left( {3.393{{Р}_{2}} - 0.365} \right)\ln \left( х \right).$По полученным максимальным значениям динамического давления были определены значения критерия Вебера и фактический диаметр для капель с исходным диаметром 1.0 мм (табл. 4).
Таблица 4.
Значения критерия Вебера и фактического диаметра капли при металлизации с использованием различных типов сопловых устройств
Тип сопла | Сопло-диафрагма | Сопло-трубка | |||
---|---|---|---|---|---|
Р1, МПа | 0.5 | 0.4 | 0.5 | 0.4 | |
Рд max, МПа | 0.11 | 0.05 | 0.39 | 0.06 | |
We для металлов | Al | 30 | 16 | 41 | 16 |
Zn | 35 | 19 | 48 | 19 | |
Fe | 16 | 9 | 22 | 9 | |
Фактический диаметр, мкм | Al | 45 | 150 | 27 | 150 |
Zn | 34 | 110 | 21 | 110 | |
Fe | 150 | 500 | 88 | 500 |
Анализ полученных данных показал, что в результате дробления для алюминия и цинка размер капель будет уменьшаться до диапазона 1–100 мкм, а для Fe – до 500–100 мкм.
Для экспериментальной проверки фактических размеров частиц жидкого металла, получаемых при металлизации, было выполнено распыление алюминиевой проволоки диаметром 2.2 мм при давлении 0.5 МПа при силе тока 100–110 А, напряжении 26 В. Распыление проводилось с использованием двух типов сопловых устройств, с устройством “сбора” факела распыления и концентрации на подложку из оцинкованной стали, изогнутой параболой, с вершиной в точке пересечения с осью движения ТГ. Полученные частицы были рассеяны на комплекте сит. Фракционный состав представлен на рис. 6.
Рис. 6.
Фракционный состав частиц алюминия, полученных при металлизации с использованием сопловых устройств разного типа: 1 – сопло-трубка; 2 – сопло-диафрагма.
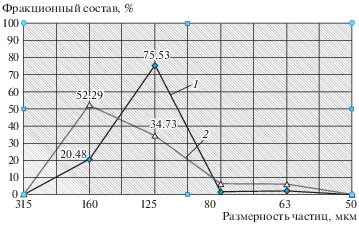
Как видно из полученных данных сопло-трубка обеспечивает более мелкодисперсный состав напыленного металла, чем сопло-диафрагма. Однако, полученный размер частиц не соответствует значениям, полученным в результате расчета критерия Вебера. Это указывает на необходимость корректировки диапазонов дробления исходных частиц металла при их распылении методом электродуговой металлизации. В диапазоне значений критерия Вебера 20–50 дробление капли происходит на 5–10 частей соответственно.
На основе полученных данных можно сделать следующие выводы: 1. Анализ представленных результатов свидетельствует о необходимости учета распределения динамического давления для размещения среза проволок с целью получения более мелкодисперсного покрытия. 2. Полученные эмпирические зависимости для расчета динамического давления и расстояния от сопла до стыка проволок позволяют определять указанные параметры и оценивать ожидаемую дисперсность частиц напыляемого металла в диапазоне давлений от 0.4 МПа до 0.5 МПа. 3. При этом следует отметить необходимость корректировки интенсивности дробления исходной капли жидкого металла в зависимости от критерия Вебера применительно к электродуговой металлизации в сторону меньших значений.
Список литературы
Газотермическое напыление: учебн. пособие / под ред. Л.Х. Балдаева. М.: Маркет ДС, 2007. 344 с.
Мордасов Д.М., Мордасов М.М. Особенности аэродинамических характеристик акустически модулированной струи газа // Ж. технической физики. 2017. Т. 87. № 3. С. 468.
Elagina O.Yu., Gusev V.M., Buklakov A.G., Nesterenko N.S., Tomskii K.O. Deposition of Pseudo Alloy Coatings by Electric Arc Metallization // Inorganic Materials: Applied Research. 2020. V. 11. № 3. P. 641.
Абрамович Г.Н. Прикладная газовая динамика. Учебн. пособие для вузов. М.: Наука, 1991. 600 с.
Кудинов В.В., Бобров Г.В. Нанесение покрытий напылением. Теория, технология и оборудование. Учебник для вузов. М.: Металлургия, 1992. 432 с.
Волынский М.С. Необыкновенная жизнь обыкновенной капли. М.: Знание, 1986. 144 с.
Пажи Д.Г., Галустов В.С. Основы техники распыливания жидкостей. М.: Химия, 1984.
Бойко В.М., Поплавский С.В. Экспериментальное исследование двух типов срывного разрушения капли в потоке за ударной волной // Физика горения и взрыва, 2012. Т. 48. № 4. С. 440.
Дополнительные материалы отсутствуют.
Инструменты
Проблемы машиностроения и надежности машин