Проблемы машиностроения и надежности машин, 2021, № 3, стр. 31-39
Влияние параметров газотермического напыления на прочность сцепления функциональных стойких покрытий
А. А. Ковалев 1, *, А. С. Краско 1, **
1 Московский государственный технический университет имени Н.Э. Баумана
Москва, Россия
* E-mail: kovalevarta@gmail.com
** E-mail: krasko_as@mail.ru
Поступила в редакцию 07.12.2020
Принята к публикации 24.02.2021
Аннотация
В статье рассматриваются влияния основных параметров газотермического напыления на прочность сцепления покрытия с поверхностью основы. На этапах нагрева, ускорения, переноса и контакта частиц раскрываются взаимосвязи параметров процесса напыления и факторов, определяющих прочность сцепления напыляемого материала с поверхностью основы. Формализованы зависимости прочности сцепления от технологических параметров и режимов напыления на операциях нанесения и механической обработки функциональных стойких покрытий.
В настоящее время возрастает актуальность проблемы обеспечения заданных эксплуатационных свойств изделий современного машиностроения, работающих в условиях многофакторных воздействий. В процессе эксплуатации такие изделия подвержены значительным тепловым и силовым факторам, а также интенсивному изнашиванию. Рассматривая условия работы ответственных изделий авиа- и двигателестроения (сопла, лопатки, валы, корпуса камер сгорания, детали гидравлики и газотурбинных двигателей), нефтегазовой промышленности (детали установок погружных электроцентробежных насосов, детали различных уплотнений, запорной арматуры) можно выделить основные виды изнашивания их поверхностей: абразивное, гидроабразивное, гидроэрозионное, коррозионное и усталостное изнашивание.
Повышение требований к износостойкости рассматриваемых изделий приводит к усложнению их конструкции и применению труднообрабатываемых материалов высокой стоимости. С целью сокращения производственных затрат целесообразно применение ресурсосберегающих технологий, базирующихся на рациональном использовании и наилучшем сочетании ресурсов производства.
К таким технологиям относится нанесение функциональных покрытий для обеспечения заданных показателей качества поверхностей деталей. Наиболее перспективным методом нанесения функциональных стойких покрытий в условиях современного мелкосерийного производства является газотермическое напыление и, в особенности, его разновидность, плазменное напыление [1, 2]. Однако получение заданных эксплуатационных свойств рассматриваемых деталей усложняется отсутствием обобщенных достоверных данных по нанесению стойких покрытий и недостатком времени на отработку технологии в условиях мелкосерийного производства.
Стабильности получаемых эксплуатационных свойств можно достигнуть за счет направленного формирования показателей качества изделий в процессе их изготовления [3–5]. На основании анализа работ [6–22] в случае применения газотермических покрытий одним из определяющих и комплексных показателей качества предлагается рассмотреть прочность сцепления покрытия с основой σs. Поэтому задача исследования влияния параметров газотермического напыления на прочность сцепления функциональных стойких покрытий является актуальной.
На основании работ [3–5] сформулируем определение термина “направленное формирование эксплуатационных свойств изделий” – стратегия разработки технологического процесса (операции), направленная на достижение заданных свойств изделий с максимальной производительностью и минимальными затратами, посредством учета взаимосвязей формируемых показателей качества с параметрами процесса обработки.
Формирование множества значений показателей качества на j-й операции (этапе) технологического процесса, согласно теории наследственности, представляют уравнением [3]
(1)
${{\left\{ {{{P}_{i}}} \right\}}_{j}} = {{\left\{ {{{S}_{i}}} \right\}}_{j}}{{\left\{ {{{P}_{i}}} \right\}}_{{j - 1}}} + \sum\limits_l {{{{\left\{ {{{k}_{{il}}}} \right\}}}_{j}}{{{\left\{ {{{P}_{u}}} \right\}}}_{l}},} $Основной задачей при исследовании закономерностей направленного формирования показателей качества является определение коэффициентов трансформации, которые позволяют установить значение изменений свойств изделий в ходе технологического процесса.
Коэффициент трансформации зависит от технологических режимов, условий реализации метода воздействия (обработки) и случайных воздействий
(2)
${{\left( {{{S}_{i}}} \right)}_{j}} = f\left[ {{{{\left\{ {{{Z}_{i}}} \right\}}}_{j}},{{{\left\{ {{{K}_{2}}} \right\}}}_{j}},{{{\left\{ {{{K}_{3}}} \right\}}}_{j}}} \right],$Для вновь создаваемого показателя качества зависимость (1) с учетом (2) следует записывать в функциональном виде
(3)
$\begin{gathered} {{\left( {{{P}_{i}}} \right)}_{j}} = f\left[ {{{{\left( {{{P}_{i}}} \right)}}_{{j--1}}},{{{\left\{ {{{P}_{u}}} \right\}}}_{l}},{{{\left\{ Z \right\}}}_{j}},{{{\left\{ {{{K}_{2}}} \right\}}}_{j}},{{{\left\{ {{{K}_{3}}} \right\}}}_{j}}} \right], \\ i = 1,...,n,\quad u = 1,...,\left( {n - 1} \right),\quad 1 \leqslant l \leqslant \left( {j--1} \right), \\ \end{gathered} $Для реализации стратегии направленного формирования показателей качества изделия необходимо определить, какие технологические параметры и режимы {Z}j являются основными факторами и должны учитываться одновременно в зависимостях (1) и (2) или только в (3).
Адгезия покрытия с основой или когезия слоя покрытия с промежуточными слоями определяются механической и химической связями, которые зависят от температуры Θc, давления pc, времени контакта τc частиц с поверхностью напыления, а также показателями качества поверхности основы Pb [8, 15, 19, 20]. Помимо этого, указанные параметры влияют на остаточные напряжения, возникающие в покрытии σr.c [8]. Таким образом, прочность сцепления можно представить соотношением
Температура контакта частиц с поверхностью напыления зависит от этапов нагрева, ускорения и переноса частиц (рис. 1) и ее можно представить выражением
Рис. 1.
Изменение температуры (Θp) и скорости (vp) частиц напыляемого материала от времени (τ): 1 – зона нагрева, диспергирования и ускорения частиц напыляемого материла (распылитель); 2 – активный участок струи; 3 – основной участок струи; 4 – формируемое газотермическое покрытие; 5 – поверхность основы; a – кривые роста температуры и скорости частиц при осевой подаче распыляемого материала; b – кривые роста температуры и скорости частиц при радиальной подаче распыляемого материала за срезом сопла.
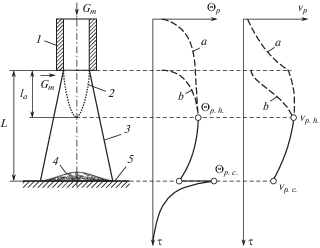
Анализ процесса газотермического напыления в работах [7–12, 17, 18] позволяет сделать вывод о том, что температура Θp.h зависит от интенсивности нагрева и времени нахождения частиц в зоне нагрева, а также от эффективного коэффициента полезного действия (КПД) нагрева частиц
На основании анализа параметров процесса напыления в работах [7–9, 11, 22], разность температуры частиц на выходе из зоны нагрева и температуры частиц в момент контакта с поверхностью напыления (ΔΘp.f) зависит от интенсивности и времени охлаждения частиц, находящейся в основном участке струи
С учетом взаимосвязей параметров процесса напыления, рассмотренных в работах [9, 14, 17], температура, возникающая на контакте и вызванная переходом кинетической энергии частицы в тепловую (Θe) зависит от
Давление на контакте частицы с поверхностью напыления pc состоит из двух составляющих, ударного и напорного давления [8, 15]
Представив связь рассмотренных факторов в виде схемы (рис. 2), можно выделить наиболее важные факторы, влияющие на температуру и давление на контакте частиц с поверхностью напыления. Схема разбита на четыре блока. В первые три блока объединены управляемые параметры процесса напыления покрытия, в четвертом блоке – управляющие параметры. Блок 1 – технологические параметры зоны нагрева, диспергирования и ускорения частиц напыляемого материала. Блок 2 – технологические параметры зоны переноса частиц до поверхности напыления (струя). Блок 3 – параметры зоны контакта частиц с поверхностью основы. Блок 4 – технологические параметры и режимы газотермического напыления покрытия.
Рис. 2.
Схема влияния технологических параметров и режимов газотермического напыления на прочность сцепления покрытия с поверхностью основы: 1 – параметры зоны нагрева, диспергирования и ускорения частиц напыляемого материала; 2 – параметры зоны переноса частиц до поверхности напыления (струя); 3 – параметры зоны контакта частиц с поверхностью основы; 4 – управляющие параметры напыления покрытия.
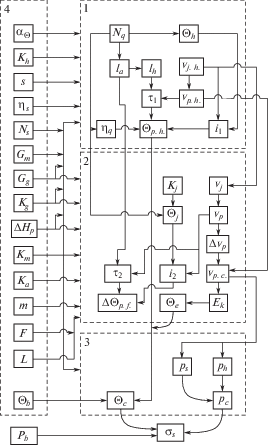
Исключив промежуточные зависимости, получим, что на температуру и давление контакта частиц с поверхностью напыления оказывают прямое воздействие следующие технологические параметры и режимы:
Рассмотренные основные параметры и режимы напыления можно объединить в пять групп:
1. Параметры поверхности напыления, Θb;
2. Параметры напыляемого материала:
2.1. Размерно-массовые параметры напыляемого материала: s, F, m;
2.2. Химический состав и теплофизические свойства материала напыляемых частиц (Km): ΔHp, μ, ρ, ${{{v}}_{s}}$, ρp;
3. Конструктивные параметры зоны нагрева и сопла:
3.1. Тип и характеристики зоны нагрева (Kh): Nq, ηs;
3.2. Конструктивные параметры зоны ускорения (Kn): d, l, Pn;
4. Параметры горючего газа, струи и атмосферы: Kj, Ka, Kg, αΘ;
5. Технологические режимы напыления: Ns, Gg, Gm, L.
Время контакта частицы с поверхностью напыления τc составляет порядка 10–5–10–9 с [7, 8]. Это означает, что τc можно принять как константу и считать, что контакт происходит мгновенно.
Под характерным размером частицы s примем наименьший линейный размер, на который необходимо прогреть частицу. Для частиц различных видов характерные размеры показаны на рис. 3.
В качестве напыляемого материала применяются порошки в виде частиц сферической формы, а также прутки и стержни, диспергируемые в процессе напыления в виде частиц (рис. 3а), при этом s = D/2, где D – диаметр частицы. При напылении тугоплавких материалов используются плакированные порошки в виде частиц, состоящих из “ядра” тугоплавкого материала 1 и “оболочки” легкоплавкого материала 2 (рис. 3б), а также порошки, состоящие из частиц в виде пластинок (рис. 3в). В случае плакированных частиц s = (D – d)/2, где d – диаметр ядра частицы, и для частиц в виде пластинок s = H/2, где H – толщина пластинки.
Операции изготовления деталей с газотермическими покрытиями можно разделить на три этапа: 1) подготовка поверхности основы под напыление (очистка и активация); 2) напыление покрытия; 3) обработка покрытия (изменение свойств, в частности, термообработка, механическая обработка, пропитка, для получения заданных показателей качества поверхности покрытия).
Исходя из проведенного исследования запишем технологические параметры и режимы этапа напыления покрытия {Z}2, влияющие на прочность сцепления σs
(4)
${{\left\{ Z \right\}}_{2}} = {{\left\{ {{{N}_{s}},{{K}_{h}},{{K}_{n}},{{K}_{a}},{{K}_{g}},{{G}_{g}},{{K}_{m}},{{G}_{m}},s,L,{{\Theta }_{b}}} \right\}}_{2}}.$Параметры, приведенные в (4), следует уточнять для конкретных способов газотермического напыления (плазменного, детонационного, газопламенного напыления и электродуговой металлизации). В настоящее время наиболее перспективными способами газотермического напыления являются разновидности плазменного напыления, в частности, на воздухе (APS), в условиях динамического вакуума (VPS) и низкого давления (LPPS), сверхзвуковое (SST) и микроплазменное (MPS), позволяющие наносить функциональные стойкие покрытия из широкой номенклатуры материалов, в том числе наноструктурированных [1, 7, 16, 26, 27]. В этой связи, уточним параметры и режимы, указанные в зависимости (4), для плазменного напыления.
Источником нагрева напыляемого материала является плазменная струя, получаемая при прохождении плазмообразующего газа (аргона, водорода, гелия, азота или их смеси, воздуха) через электрическую дугу [12]. Тепловая мощность источника нагрева (дуги) Nq определяется мощностью, подводимой к плазмотрону Ns и коэффициентом его полезного действия, ηs = 0.4–0.75 [12]. Подводимая мощность определяется силой тока I и напряжением U. Напряжение дуги Ud существенно зависит от длины дуги ld, которая в свою очередь определяется конструктивными параметрами плазмотрона – длиной lс и диаметром dс канала [23].
При плазменном напылении применяются сменные сопла-аноды, которые характеризуются размерами профиля продольного сечения Pn, диметром d и длиной сопла l [9].
При плазменном напылении наиболее часто применяются материалы в виде порошков, состоящих из частиц сферической формы, поэтому, в качестве размерного параметра выделим диаметр частиц D.
Таким образом, уточним зависимость (4) для плазменного напыления
С учетом взаимосвязей параметров плазменного напыления, конструктивных параметров плазмотронов и показателей качества формируемых покрытий, изложенных в экспериментальных исследованиях и имитационном моделировании процесса плазменного напыления [12, 14, 24, 25], выберем основные технологические параметры и режимы в наибольшей степени влияющие на формируемый показатель прочности сцепления
(5)
${{\left\{ Z \right\}}_{2}} = {{\left\{ {I,U,{{P}_{n}},d,{{K}_{a}},{{K}_{g}},{{G}_{g}},{{K}_{m}},{{G}_{m}},D,L,{{\Theta }_{b}}} \right\}}_{2}}.$На основании анализа работ [10–12, 15] выделим основные показатели качества поверхности основы
где Ra – среднее арифметическое отклонение профиля поверхности, мкм; S – степень очистки поверхности от загрязнений (по ISO 8501); σr.b – остаточные напряжения первого рода в поверхностном слое основы, МПа.На этапе напыления покрытия формируется показатель прочности сцепления, поэтому с учетом (5), (6) запишем зависимость (3) для операции плазменного напыления
(7)
${{\left( {{{\sigma }_{s}}\left( {{{\sigma }_{a}},{{\sigma }_{r}},{{\sigma }_{k}}} \right)} \right)}_{2}} = f\left\{ {{{{\left( {Ra,S,{{\sigma }_{{r.b}}}} \right)}}_{1}},{{{\left( Z \right)}}_{2}},} \right.\left. {{{{\left( {{{K}_{2}}} \right)}}_{2}},{{{\left( {{{K}_{3}}} \right)}}_{2}}} \right\}.$На третьем этапе показатель прочности сцепления изменяется вследствие влияния технологических параметров и режимов обработки покрытия, а также показателей качества, сформированных на предыдущих операциях (этапе) технологического процесса. Таким образом, зависимость (1) запишем в виде
(8)
${{\left( {{{\sigma }_{s}}\left( {{{\sigma }_{a}},{{\sigma }_{r}},{{\sigma }_{k}}} \right)} \right)}_{3}} = \left\{ \begin{gathered} {{\left[ {{{\sigma }_{a}}} \right]}_{3}} = {{\left[ {{{S}_{{{{\sigma }_{a}}}}}} \right]}_{3}} \cdot {{\left[ {{{\sigma }_{a}}} \right]}_{2}} + {{k}_{{l6h7}}}{{\left[ P \right]}_{2}} + {{k}_{{o6h7}}}{{\left[ {{{T}_{d}}} \right]}_{2}}, \hfill \\ {{\left[ {{{\sigma }_{r}}} \right]}_{3}} = {{\left[ {{{S}_{{{{\sigma }_{r}}}}}} \right]}_{3}} \cdot {{\left[ {{{\sigma }_{r}}} \right]}_{2}} + {{k}_{{f5i7}}}{{\left[ h \right]}_{2}} + {{k}_{{l6i7}}}{{\left[ P \right]}_{2}}, \hfill \\ {{\left[ {{{\sigma }_{k}}} \right]}_{3}} = {{\left[ {{{S}_{{{{\sigma }_{k}}}}}} \right]}_{3}} \cdot {{\left[ {{{\sigma }_{k}}} \right]}_{2}} + {{k}_{{l6n7}}}{{\left[ P \right]}_{2}} + {{k}_{{m6n7}}}{{\left[ {{{Н}_{\mu }}} \right]}_{2}}, \hfill \\ \end{gathered} \right.$Полученные формализованные зависимости (7), (8) показателя прочности сцепления от технологических параметров и режимов операций подготовки, напыления и обработки газотермических покрытий дают возможность реализовать направленное формирование показателей качества деталей в процессе их изготовления.
Это позволит повысить стабильность формирования эксплуатационных свойств деталей с функциональными стойкими покрытиями в условиях мелкосерийного производства при частой смене обрабатываемых изделий, напыляемых материалов и недостаточном времени на отработку технологии.
Список литературы
Коробов Ю.С. Международная конференция-выставка по термическому напылению ITSC 2010: Обзор и анализ // Материалы международного научно-практического семинара (28‒29 октября 2010 г.). Термическое напыление. Современное состояние. 2010. С. 4.
Албагачиев А.Ю., Ставровский М.Е., Сидоров М.И. Типологические противоизносные покрытия // Проблемы машиностроения и надежности машин. 2020. № 1. С. 73.
Васильев А.С. и др. Направленное формирование свойств изделий машиностроения / Под ред. А.И. Кондакова М.: Машиностроение, 2005. 352 с.
Дальский А.М., Базров Б.М., Васильев А.С. и др. Технологическая наследственность в машиностроительном производстве / Под ред. А.М. Дальского. М.: Изд-во МАИ, 2000. 364 с.
Ящерицын П.И., Рыжов Э.В., Аверченков В.И. Технологическая наследственность в машиностроении. Минск: “Наука и техника”, 1977. 256 с.
Воронин Н.А. Эффективная и истинная адгезионная прочность тонких защитных покрытий // Проблемы машиностроения и надежности машин. 2019. № 4. С. 45.
Калита В.И., Комлев Д.И. Плазменные покрытия с нанокристаллической и аморфной структурой. М.: “Лидер М”, 2008. 388 с.
Кудинов В.В., Бобров Г.В. Нанесение покрытий напылением. Теория, технология и оборудование. Учебник для вузов. М.: Металлургия, 1992. 432 с.
Хасуи А., Моригаки О. Наплавка и напыление. М.: Машиностроение, 1985. 240 с.
Пузряков А.Ф. Теоретические основы технологии плазменного напыления: Учеб. пособие по курсу “Технология конструкционных материалов”. 2-е изд. М.: Изд-во МГТУ им. Н.Э. Баумана, 2008. 360 с.
Балдаев Л.Х., Борисов В.Н., Вахалин В.А. и др. Газотермическое напыление: учеб. пособие / Под ред. Л.Х. Балдаева М.: Маркет ДС, 2007. 344 с.
Ильюшенко А.Ф., Шевцов А.И., Оковитый В.А. и др. Процессы формирования газотермических покрытий и их моделирование. Минск: Беларус. навука, 2011. 356 с.
Ярославцев В.М. Обработка газотермических покрытий резанием: учеб. пособие. М.: Изд-во МГТУ им. Н.Э. Баумана, 2013. 89 с.
Кузьмин В.И., Голубев М.П., Тырышкин П.А., Долматов А.В. Визуализация газодинамической структуры плазменных потоков напылительного плазмотрона “ПНК-50” теневым методом // Вестник Югорского государственного университета. 2018. № 4 (51). С. 61.
Tillmann W., Hagen L., Schaak C., Liß J., Schaper M., Hoyer K.-P., Aydinöz M.E., Garthe K.-U. Adhesion of HVOF-sprayed WC-Co coatings on 316L substrates processed by SLM // J. of thermal spray technology. 2020. № 29. P. 1396.
Ashok Meghwal, Ameey Anupam, Murty B.S., Christopher C. Berndt, Ravi Sankar Kottada, Andrew Siao Ming Ang. Thermal spray high-entropy alloy coatings: a review // J. of thermal spray technology. 2020. № 29. P. 857.
Mauer G., Vaßen R., Stöver D. Plasma and particle temperature measurements in thermal spray: approaches and applications // J. of thermal spray technology. 2011. № 3 (20). P. 391.
Jing Xue, Min Huang. Optimization of plasma spray process VIA orthogonal test design method, SVM, and improved PSO // International journal of materials, mechanics and manufacturing. 2017. № 3 (5). P. 153.
Lyphout C., Nylen P., Östergren L.G. Adhesion strength of HVOF sprayed IN718 coatings // J. of thermal spray technology. 2012. № 21. P. 86.
Yongjing Cui, Mengqiu Guo, Changliang Wang & Zhihui Tang. Adhesion enhancement of a metallic al coating fabricated by detonation gun spray on a modified polymer matrix composite // J. of thermal spray technology. 2019. № 28. P. 1730.
Vignesh S., Shanmugam K., Balasubramanian V., Sridhar K. Identifying the optimal HVOF spray parameters to attain minimum porosity and maximum hardness in iron based amorphous metallic coatings // Defence Technology. 2017. № 13. P. 101.
Pulido-Gonzalez N., Garcia-Rodriguez S., Campo M., Rams J., Torres B. Application of DOE and ANOVA in optimization of HVOF spraying parameters in the development of new Ti coatings // J. of thermal spray technology. 2020. № 29. P. 384.
Клименко Г.К., Ляпин А.А. Генераторы плазмы: метод. указания к выполнению курсового проекта. М.: Изд-во МГТУ им. Н.Э. Баумана, 2010. 62 с.
Ramachandran C.S., Balasubramanian V., Ananthapadmanabhan P.V. Multiobjective optimization of atmospheric plasma spray process parameters to deposit yttria-stabilized zirconia coatings using response surface methodology // J. of thermal spray technology. 2011. № 20. P. 590.
Nylé P., Hansbo A., Friis M., Pejryd L. Investigation of particle in-flight characteristics during atmospheric plasma spraying of yttria stabilized ZrO2: Part 2. Modeling // J. of thermal spray technology. 2001. № 10. P. 359.
Оковитый В.А., Пантелеенко Ф.И., Оковитый В.В., Асташинский В.М. Плазмотрон для нанесения покрытий // Наука и техника. 2019. № 18 (1). С. 5.
Кравченко И.Н., Карелина М.Ю., Зубрилина Е.М., Коломейченко А.А. Ресурсосберегающие технологии получения функциональных наноструктурированных покрытий высокоскоростными методами нанесения // Вестник Донского государственного технического университета. 2015. № 3 (82). С. 19.
Дополнительные материалы отсутствуют.
Инструменты
Проблемы машиностроения и надежности машин