Проблемы машиностроения и надежности машин, 2021, № 3, стр. 40-46
К вопросу раннего обнаружения трещин в рабочих колесах гидроагрегатов
Е. В. Георгиевская *
Центр конструкторско-технологических инноваций
Санкт-Петербург, Россия
* E-mail: sciencedir@cdti.ru
Поступила в редакцию 14.12.2020
Принята к публикации 24.02.2021
Аннотация
Появление и развитие усталостных трещин в лопастях рабочих колес гидроагрегатов является одной из главных причин, ограничивающих их ресурс. Практика эксплуатации показывает, что используемые в настоящее время системы диагностики гидроагрегатов не позволяют своевременно идентифицировать трещины на работающем оборудовании. На основании результатов проведенного численного эксперимента показано, что высокая жесткость и наличие специфических форм собственных колебаний конструкции не позволяют связать динамические напряжения в лопастях, ответственные за появление трещин, с контролируемыми системой диагностики параметрами. Решить проблему помогут аналитические походы на базе расчетной оценки усталостной прочности и методов механики разрушений.
Настоящая статья подготовлена по материалам доклада “Влияние трещин на динамические параметры и срок службы гидроагрегатов”, представленного на международной конференции “Живучесть и конструкционное материаловедение” ЖивКоМ-2020, г. Москва, 27–29 октября 2020 г.
В соответствии с ГОСТ Р 55890-2013 [1] в целях обеспечения надежности и устойчивости Единой энергетической системы России и технологически изолированных территориальных электроэнергетических систем должно осуществляться непрерывное регулирование электроэнергетического режима как по частоте, так и по перетокам активной мощности. Основной вклад в регулирующую мощность вносят гидроэлектростанции (ГЭС), что объясняется следующими основными причинами: 1) высокая маневренность гидроагрегатов (ГА) по сравнению с энергоблоками тепловых (ТЭС) и атомных электростанций (АЭС): пуск ГА или изменение его мощности осуществляется всего в течение нескольких десятков секунд; 2) изменение мощности ГА не связано с необходимостью дополнительных ограничений по режиму работы технологической части ГЭС; 3) незначительное (по сравнению с ТЭС и АЭС) снижение экономичности ГЭС при работе в переменных режимах.
В большинстве случаев на гидростанциях применяется система группового регулирования активной мощности (ГРАМ), которая осуществляет регулирование активной мощности ГЭС путем распределения между агрегатами суммарной заданной мощности ГЭС по определенному критерию. Для гидроагрегата участие в системе регулирования означает расширение его рабочего диапазона, частую смену режимов, длительную работу на малых и средних частичных мощностях, большое количество пусков и остановов [2, 3], что в конечном итоге выливается в преждевременное образование усталостных трещин и исчерпание его ресурса ранее предусмотренных проектными показателями сроков.
Объект исследования. В настоящей статье основное внимание уделено высоконапорным мощным гидроагрегатам, которые обычно оснащаются турбинами радиально-осевого (РО) типа и отличаются высокой эксплуатационной надежностью и кавитационной стойкостью. В России самые мощные РО-турбины установлены на Саяно-Шушенской и Красноярской ГЭС на реке Енисей, Братской, Усть-Илимской и Богучанской ГЭС на Ангаре, Бурейской ГЭС на реке Бурее.
Рабочее колесо (РК) гидроагрегата является одним из его главных ресурсоопределяющих элементов. Замена РК – это дорогостоящий и длительный процесс, сопровождающийся полной разборкой ГА, долговременным простоем в ремонте, а зачастую и вынужденной заменой других элементов агрегата. Стоимость, продолжительность и качество ремонта РК по устранению возникающих в процессе работы трещин в лопастной системе напрямую зависит от их размеров, поэтому раннее обнаружение таких трещин является практически важной для ГЭС задачей, особенно в условиях частого изменения режимных факторов.
Рабочее колесо турбины РО-типа обычно состоит из 11–19 лопастей, жестко закрепленных между нижним массивным ободом и ступицей. Такая лопастная решетка обеспечивает высокую жесткость конструкции РК, но в силу геометрических особенностей обуславливает высокий уровень концентрации напряжений в зонах сопряжения лопасти со ступицей или ободом, особенно вблизи выходной (более тонкой) кромки [4, 5]. В этих же зонах могут возникать значительные остаточные напряжения (более 100 МПа), обусловленные особенностями технологии приварки лопастей.
Причины трещинообразования. При работе гидроагрегатов РО-типа на больших мощностях, вблизи проектных значений номинальной мощности, максимальные статические напряжения в лопастной системе обычно составляют не более 20–30% от предела текучести материала лопасти, а амплитуда динамической составляющей не превышает 10% от статической. При таком режиме работы зарождение усталостных трещин в лопастях РК маловероятно, даже с учетом высокой концентрации напряжений, сверхдлительной (более 50 лет) эксплуатации ГА и наличия больших остаточных сварочных напряжений. Однако на режимах малой или средней частичной мощности, а также при смене режимов работа гидроагрегата сопровождается значительными гидродинамическими нагрузками, вызванными нестабильностью потока и формированием масштабных вихревых структур, влияющих на все компоненты агрегата и способствующих ускоренному трещинообразованию в лопастной системе [6–9].
Как показывает многолетняя практика, в РО-турбинах наиболее часто встречаются трещины усталостного происхождения, распространяющиеся вдоль линии приварки лопасти к ступице или ободу от выходной кромки к входной. Обычно их находят только при осмотрах агрегатов в периоды плановых ремонтов [8, 10–12]. Часто на момент обнаружения такие трещины достигают длины более 300 мм, могут быть сквозными, с большим раскрытием. Известны даже случаи полного разрыва лопасти [13]. Восстановительный ремонт лопастей с глубокими протяженными трещинами занимает много времени и требует существенных финансовых затрат. Кроме того, он может способствовать искажению геометрии лопасти, созданию поля высоких остаточных напряжений в зоне заварок и другим негативным последствиям.
Возможности вибродиагностики для идентификации трещин. Крупные гидроагрегаты оснащаются стационарными системами мониторинга и диагностики [14, 15], анализирующими информацию от множества датчиков, в том числе вибрационных, устанавливаемых на неподвижные и вращающиеся компоненты агрегата. Целью таких систем является поиск неисправностей, основанный на сравнении результатов непрерывного мониторинга ряда характеристик агрегата с допускаемыми значениями. Кроме того, регулярно проводятся дополнительные вибрационные испытания агрегата с помощью переносных систем. Хотя современные системы мониторинга/диагностики ГА весьма эффективны для поиска ряда неисправностей оборудования, в отношении ранней идентификации трещин на рабочих колесах они оказываются практически бессильными. Развитие усталостных трещин в лопастной системе обычно происходит медленно, трещины растут годами и часто остаются невидимыми для систем вибродиагностики [16] вплоть до осушения проточного тракта и проведения контроля состояния металла РК в периоды капитальных ремонтов.
Неэффективность вибродиагностических систем для ранней идентификации трещин в рабочих колесах РО-турбин можно объяснить конструктивными особенностями гидроагрегатов, обуславливающими высокую жесткость конструкции, а также отсутствием корреляции между появлением и развитием усталостных трещин в лопастях РК и контролируемыми в процессе работы вибрационными параметрами ГА.
Зарождение и развитие трещин происходит под действием переменных динамических нагрузок, вызванных эксплуатацией агрегата во всем режимном диапазоне. Статическая составляющая нагрузки и уровень остаточных напряжений влияют на время зарождения трещины и живучесть конструкции. На рис. 1 приведено сравнение данных обработки результатов натурного тензометрирования и вибромониторинга для трех крупных гидроагрегатов российских ГЭС (ГА-1, ГА-2 и ГА-3 с одинаковой номинальной мощностью 240 МВт и близкими напорами) по данным, представленным в [17, 18]. Тензометрирование выполнялось в период 2011–2015 гг. специалистами отдела гидроэнергетики и гидроэнергетического оборудования ОАО “НПО ЦКТИ”. Тензометрические датчики были установлены в непосредственной близости от зоны сопряжения выходной кромки лопасти со ступицей рабочего колеса, соответствующей зоне максимальных статических напряжений на номинальной мощности и максимальных динамических напряжений на большинстве эксплуатационных режимов работы. Методика проведения натурных испытаний подробно описана в [17].
Рис. 1.
Сопоставление результатов вибродиагностики и натурного тензометрирования: (а) – ГА-1; (б) – ГА-2; (в) – ГА-3.
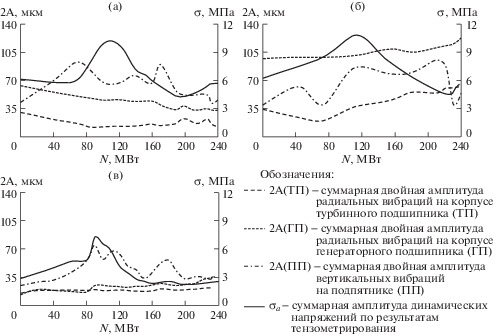
Взаимосвязь между суммарными измеряемыми вибрациями и величиной возникающих динамических напряжений (рис. 1), ответственных за появление и развитие трещин в лопастной системе, не просматривается ни на качественном уровне, ни в количественном выражении. Разложение суммарного измеренного сигнала на частотные составляющие также не выявило каких-либо корреляционных зависимостей [18]. Правомерность этих выводов подтверждена на основе численного эксперимента на примере двухопорного мощного гидроагрегата.
Описание расчетной модели. Для проведения численного эксперимента была построена расчетная конечно-элементная модель вращающейся части агрегата, состоящая из турбинного вала, жестко соединенного с рабочим колесом, и генераторного вала с насаженным на него ротором гидрогенератора. Крепление вала в радиальном направлении осуществляется в средней по высоте плоскости генераторного и турбинного подшипников, в вертикальном (осевом) направлении – в плоскости опирания ГА на строительные конструкции.
При разработке этой модели для повышения наглядности результатов были приняты упрощения, не оказывающие существенного влияния на исследование взаимосвязи между контролируемыми вибрационными параметрами и динамическими характеристиками агрегата: 1) элементы РК моделируются конечными элементами оболочечного типа с сохранением кривизны и толщины в каждой точке лопасти, но без учета фактических радиусов галтелей в зоне приварки лопастей; 2) ротор генератора моделируется в упрощенном виде как набор кольцевых объемов, имитирующих втулку, систему спиц, обод и полюса. При разбиении на конечные элементы задаются эквивалентные параметры плотности и упругости материала, отражающие массогабаритные и жесткостные характеристики натурного генератора. Это позволяет сохранить основные частотные характеристики, но исключить локальные эффекты, обусловленные особенностями конструкции ротора генератора; 3) конструкционные натяги и затяг шпилек не учитываются, предполагается обеспечение плотной посадки сопрягаемых элементов и нераскрытие фланцевых соединений во всем режимном диапазоне; 4) направляющие подшипники и подпятник моделируются линейными конечными элементами пружинного типа с заданием эквивалентных жесткостей, имитирующих жесткость каждого из опорных элементов; 5) остаточные напряжения в зоне приварки лопастей к ступице или ободу не учитывались, поскольку локальное напряженное состояние в этой зоне не оказывает существенного влияния на частоты и формы собственных колебаний вращающейся части ГА, а определяет преимущественно время зарождения и скорость роста трещины, при этом появление трещины приводит к перераспределению остаточных напряжений; 6) сквозные трещины в РК моделируются в виде разрывов по линии сопряжения лопасти со ступицей, начинающихся со стороны выходной кромки; длина разрыва увеличивается поэтапно по мере роста трещины и отражает интегральное влияние всех факторов, определяющих развитие трещины; при этом время достижения трещиной определенной длины не имеет принципиального значения в целях данного исследования.
На первом шаге исследований определялся спектр собственных частот и формы собственных колебаний, а также исследовались взаимосвязи между деформациями в лопастной системе рабочего колеса и перемещениями вала в местах фактической установки датчиков вибраций на натурном гидроагрегате в бездефектной конструкции рабочего колеса (при отсутствии трещин в лопастной системе). На втором шаге численного эксперимента изучалось влияние наличия и длины трещин в лопастях на собственные частоты модели. При этом рассматривались два сценария трещинообразования: 1) зарождение и рост единичной трещины (только в одной лопасти); 2) массовое растрескивание – одновременное зарождение и синхронный рост одинаковых по длине трещин на всех лопастях.
Результаты расчетов. Были определены первые 50 частот и соответствующие формы собственных колебаний в диапазоне 0÷120 Гц. Все формы собственных колебаний можно разделить на три группы (рис. 2), отражающие различные варианты взаимосвязи деформации рабочего колеса с радиальными перемещениями вала в точках установки датчиков на натурном гидроагрегате при проведении вибродиагностики ГА: 1) изгибные колебания агрегата в целом, когда деформации рабочего колеса сопровождаются радиальными перемещениями вала; такие деформации могут быть идентифицированы по результатам анализа биений вала вблизи направляющих подшипников; 2) крутильные колебания вращающейся части агрегата, когда при закрутке РК отсутствуют перемещения вала в радиальном направлении; закрутка вала обычно не входит в перечень регистрируемых вибрационных параметров, поэтому такие колебания не идентифицируются системой вибромониторинга или вибродиагностики; 3) изгибные колебания рабочего колеса, не сопровождающиеся изгибом вала агрегата; вибрационное перемещение вала в радиальном направлении отсутствует, несмотря на наличие деформации элементов РК. Система вибродиагностики не регистрирует данный вид колебаний.
Рис. 2.
Основные типы форм собственных колебаний для бездефектной конструкции: (а) – совместные изгибные колебания рабочего колеса и вала; (б) – крутильные колебания рабочего колеса; (в) – изгибные колебания рабочего колеса без деформации вала.
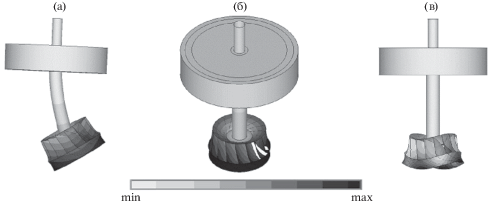
Таким образом, идентифицировать крутильные формы колебаний и формы, связанные с изгибом РК без изгиба вала, с помощью средств вибромониторинга не представляется возможным. В случае возбуждения таких форм колебаний при работе ГА, а также любых смешанных форм, в которых есть указанные выше составляющие, невозможно связать фактический уровень динамических напряжений в лопастной системе РК с измеряемыми системой мониторинга вибропараметрами.
Развитие трещин в лопастях РК приводит к снижению собственных частот вращающейся части ГА и, соответственно, к изменению реакции на опорных узлах. Результаты расчета для первых десяти собственных частот в бездефектной конструкции и при наличии одиночной и множественных трещин (во всех лопастях) приведены в табл. 1. Длина трещин одинакова для всех лопастей и составляет 10% от общей длины линии сопряжения лопасти со ступицей РК. Сдвиг частоты определялся по отношению к частоте в бездефектной конструкции.
Таблица 1.
Собственные частоты ГА при отсутствии и наличии трещин в лопастях
№ моды | Без трещин | Трещина на одной лопасти | Трещины во всех лопастях | ||||
---|---|---|---|---|---|---|---|
частота, Гц | частота, Гц | сдвиг частоты | частота, Гц | сдвиг частоты | |||
абсолютный, Гц | относительный, % | абсолютный, Гц | относительный, % | ||||
1 | 6.48 | 6.48 | 0.0 | 0.0 | 6.48 | 0.0 | 0.0 |
2 | 7.59 | 7.59 | 0.0 | 0.0 | 7.59 | 0.0 | 0.01 |
3 | 7.84 | 7.84 | 0.0 | 0.0 | 7.84 | 0.0 | 0.01 |
4 | 12.31 | 12.30 | 0.01 | 0.06 | 12.24 | 0.07 | 0.58 |
5 | 12.32 | 12.32 | 0.0 | 0.0 | 12.25 | 0.07 | 0.58 |
6 | 14.72 | 14.72 | 0.0 | 0.0 | 14.72 | 0.0 | 0.0 |
7 | 16.66 | 16.64 | 0.01 | 0.08 | 16.41 | 0.25 | 1.51 |
8 | 25.48 | 25.47 | 0.01 | 0.03 | 25.34 | 0.14 | 0.55 |
9 | 25.50 | 25.49 | 0.01 | 0.04 | 25.35 | 0.14 | 0.55 |
10 | 28.76 | 28.61 | 0.15 | 0.52 | 27.23 | 1.53 | 5.35 |
Расчеты показали, что в регистрируемом при проведении вибромониторинга диапазоне изменения собственных частот при наличии протяженной единичной сквозной трещины составляют не более 0.15 Гц или ~0.5%, что на практике не позволяет их идентифицировать на работающем оборудовании. При массовом растрескивании соответствующее изменение может достигнуть ~1.5 Гц или ~5%, но одновременное развитие трещин на всех лопастях маловероятно. Изменения режимов работы ГА, связанные с колебаниями мощности и напора, сезонными изменениями водного режима, трансформацией жесткостных характеристик подшипников в процессе длительной эксплуатации также приводят к изменению частотного спектра агрегата, что дополнительно затрудняет выделение частотного сдвига, обусловленного развитием трещин в лопастной системе РК.
Представленные результаты численного моделирования показывают, что решение проблемы идентификации трещин в рабочих колесах РО-гидротурбин на ранней стадии развития только за счет усовершенствования существующих систем вибродиагностики вряд ли приведет к желаемому результату. Фокус исследования по данной тематике имеет смысл перенести на опробованные аналитические методы на базе расчетной оценки усталостной прочности и подходов механики разрушений [19, 20].
Заключение. Представленные в статье результаты показывают, что наличие специфических форм собственных колебаний гидроагрегата и высокая жесткость конструкции рабочих колес радиально-осевых гидротурбин не позволяют своевременно идентифицировать развивающиеся усталостные трещины в лопастях с использованием современных систем вибродиагностики на работающем оборудовании. Решить эту проблему можно с помощью походов, реализующих аналитические методы оценки времени зарождения и скорости роста усталостных трещин.
Список литературы
ГОСТ Р 55890-2013 Единая энергетическая система и изолированно работающие энергосистемы. Оперативно-диспетчерское управление. Регулирование частоты и перетоков активной мощности. Нормы и требования.
Trivedi C., Gandhi B., Michel C.J. Effect of transients on Francis turbine runner life: a review // J. of Hydraulic Research, 2013. V. 51 (2). P. 112. https://doi.org/10.1080/00221686.2012.732971
Monette C., Marmont H., Chamberland-Lauzon J., Skagerstrand A., Coutu A., Carlevi J. Cost of enlarged operating zone for an existing Francis runner. IOP Conf. Series: Earth and Environmental Science. 2016. V. 49. P. 072018. https://doi.org/10.1088/1755-1315/49/7/072018
Flores M., Urquiza G., Rodríguez J.M. A Fatigue Analysis of a Hydraulic Francis Turbine Runner // World Journal of Mechanics. 2012. № 2. P. 28. https://doi.org/10.4236/wjm.2012.21004
Huang X., Oram C., Sick M. Static and dynamic stress analyses of the prototype high head Francis runner based on site measurement // IOP Conf. Series: Earth and Environmental Science. 2014. V. 22 (10). № 3. P. 32052. https://doi.org/10.1088/1755-1315/22/3/032052
Favrel A., Gomes Pereira Junior J., Müller A., Landry C., Yamamoto K., & Avellan F. Swirl number based transposition of flow-induced mechanical stresses from reduced scale to full-size Francis turbine runners // J. of Fluids and Structures. 2020. № 94. P. 102956. https://doi.org/10.1016/j.jfluidstructs.2020.102956
Unterluggauer J., Doujak E., Bauer C. Fatigue analysis of a prototype Francis turbine based on strain gauge measurements // Wasser Wirtschaft, 2019. V. 09 (S1). P. 66. https://doi.org/10.1007/s35147-019-0238-92
Liu X., Luo Y., Wang Z. A review on fatigue damage mechanism in hydroturbines. Renewable and Sustainable. Energy Reviews, 2016. V. 54. P. 1. https://doi.org/10.1016/j.rser.2015.09.025
Seidel U., Mende C., Hübner B., Weber W., Otto A. Dynamic loads in Francis runners and their impact on fatigue life. IOP Conf. Series: Earth and Environmental Science. 2014. V. 22 (9). № 3. P. 32054. https://doi.org/10.1088/1755-1315/22/3/032054
Nennemann B., Monette C., Chamberland-Lauzon J. Hydrodynamic damping and stiffness prediction in Francis turbine runners using CFD. IOP Conf. Series: Earth and Environmental Science. 2016. V. 49 (7). P. 072006. https://doi.org/10.1088/1755-1315/49/7/072006
Boukani H. Habibzadeh, Viens M., Tahan S.A., Gagnon M. On the performance of nondestructive testing methods in the hydroelectric turbine industry. IOP Conf. Series: Earth and Environmental Science. 2014. V. 22. № 1. P. 12018.
Balauntescu I., Panaitescu V. Low Frequency Pressure Pulsations at High Load in a Francis Turbine. U.P.B. Sci. Bull. 2016. Series D. V. 78(4). Iss. 4.
Frunzăverdel D., Muntean S., Mărginean G., Câmpiani V., Marşavina L., Terzi R., Şerban V. Failure analysis of a Francis turbine runner. IOP Conf. Series: Earth and Environmental Science 2010. V. 12. P. 012115. https://doi.org/10.1088/1755-1315/12/1/012115
Стационарная система виброконтроля, мониторинга и диагностики гидроагрегатов АЛМАЗ-7010-ГЭС. http://www.diamech.ru/almaz_ges.html
Selak L., Butala P., Sluga A. Condition monitoring and fault diagnostics for hydropower plants. Computers in Industry. 2014. https://doi.org/10.1016/j.compind.2014.02.006
Zhang M., Valentin D., Valero C., Egusquiza M., Zhao W. Numerical Study on the Dynamic Behavior of a Francis Turbine Runner Model with a Crack // Energies. 2018. V. 11. P. 1630. https://doi.org/10.3390/en11071630
Панов К.А. Прочностные испытания лопастей радиально-осевых турбин Усть-Илимской ГЭС // Гидравлические машины, гидропневмоприводы и гидропневмоавтоматика. Современное состояние и перспективы развития. Научные труды Международной научно-технической конференции. Санкт-Петербург, 2016. С. 86.
Георгиевская Е.В. О связи вибраций и динамических напряжений в лопастной системе гидротурбин // Известия ВНИИГ им. Б.Е. Веденеева. 2017. Т. 283. С. 54.
Georgievskaia E. Hydraulic turbines lifetime in terms of fracture mechanics // Engineering Failure Analysis. 2019. V. 105. P. 1296.
Åsnes A., Willersrud A., Kretz F., Imsland L. Predictive maintenance and life cycle estimation for hydro power plants with real-time analytics. Conference: Hydro Gdansk, Poland, 2018. https://www.researchgate.net/publication/328879561
Дополнительные материалы отсутствуют.
Инструменты
Проблемы машиностроения и надежности машин