Проблемы машиностроения и надежности машин, 2021, № 4, стр. 88-95
Анализ работы торсионного вала, установленного в двс и в повышающем обороты редукторе на входе в гидротрансформатор механизма передач и поворота легкой гусеничной машины, и повышение его надежности
Ю. И. Крыхтин 1, В. И. Карлов 1, *
1 Волгоградский государственный технический университет
Волгоград, Россия
* E-mail: au@vstu.ru
Поступила в редакцию 15.08.2020
После доработки 31.03.2021
Принята к публикации 26.04.2021
Аннотация
Проведен анализ причин поломки торсионного вала, установленного в двигателе внутреннего сгорания и в повышающем обороты редукторе на входе в гидротрансформатор механизма передач и поворота легкой гусеничной машины с большой удельной мощностью (более 30 л.с./Тс). Из-за большой цикличности работы торсионного вала, возможного крутильного удара и для снижения уровня крутильных колебаний торсионного вала предложено устанавливать пружинно-фрикционный демпфер крутильных колебаний торсионного вала, работающий в масле, в ограниченном объеме на выходном фланце двигателя внутреннего сгорания. Результаты исследований можно использовать при создании новых гидромеханических трансмиссий для легких гусеничных машин с большой удельной мощностью.
Рассматривается работа моторно-трансмиссионной установки (МТУ) без демпфера и с демпфером крутильных колебаний гусеничной машины (ГМ) массой 13–18 т, включающей в себя дизельный оппозитный шестицилиндровый без маховика двигатель внутреннего сгорания (ДВС) и гидромеханическую трансмиссию (ГМТ) с дифференциальным гидрообъемным механизмом поворота [1–3]. Связь двигателя с трансмиссией без демпфера осуществляется через торсионный вал диаметром 35 мм.
На рис. 1 показана кинематическая схема ГМТ легкой ГМ с торсионным валом между ДВС и повышающим обороты редуктором к гидротрансорматору (ГТ) механизма передач и поворота (МПП).
Рис. 1.
Кинематическая схема ГМТ легкой ГМ: 1, 16 – водометные движители; 2, 15 – фрикционные муфты водометных движителей; 3, 14 – высокооборотные вентиляторы системы охлаждения; 4 – гидромуфта; 5 – МПП; 6 – фрикционная муфта коробки передач (КП); 7 – блок маслонасосов; 8 – двигатель; 9 – выходной фланец ДВС, на котором далее устанавливается гаситель крутильных колебаний; 10 – реверс КП; 11 – вал промежуточный; 12 – тормоз-синхронизатор; 13 – фрикционная муфта отключения гидропередачи механизма поворота (МП); 17, 26 – бортовые передачи; 18, 24 – тормоза остановочные; 19 – гидропередача МП; 20 – вал торсионный; 21 – ГТ; 22 – редуктор, повышающий обороты на входе в ГТ; 23 – вал грузовой; 25 – вал выходной.
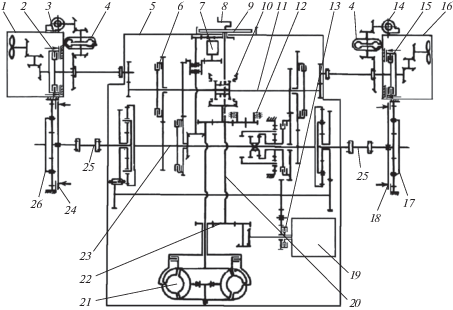
При компоновке МТУ легкой ГМ возникает необходимость удаления ГТ от ДВС на значительное расстояние. Связь ДВС с повышающим обороты редуктором на входе в ГТ при этом осуществляется через стальной торсионный вал со шлицевыми концами.
При эксплуатации изделий с ГМТ с 2-х дисковым блокировочным фрикционом после пробегов различной протяженности (даже небольшой) наблюдались случаи поломки торсионного вала. Поломка стального торсионного вала показана на рис. 2.
Торсионный вал был изготовлен из стали 45ХН2МФА с твердостью HB = 477, с троосто-мартенситной структурой. По внешнему виду излом – срез на кручение, о чем свидетельствует гладкая поверхность излома.
На вышедших из строя торсионных валах цилиндрическая часть вала диаметром 35 мм имеет цвета побежалости от излома – серый, соответствующий приблизительно 350°С, с переходом к васильковому (приблизительно 320°С), фиолетовому (приблизительно 280°С) и соломенному (приблизительно 220°С) ближе к галтели. Галтель радиусом 50 мм и шлицы диаметром 45 мм – светлые, без цветов побежалости. Излом находится на расстоянии 50 мм от торца шлиц, почти на оси вала.
Характер излома – усталостный, происходит в результате растяжений и одностороннего изгиба расчетным номинальным напряжением и при слабом локальном концентраторе.
Попытка заменить стальной торсионный вал на титановый не увенчалась успехом. На рис. 3 показана поломка экспериментального торсионного вала из титанового сплава ВТЗ-1 с микроструктурой, соответствующей 3–4 балла десятибалльной шкалы микроструктур титановых сплавов.
Внешним осмотром установлено, что поломка этой детали произошла со скручиванием, о чем свидетельствует деформация структуры излома.
Постановка задачи. Создание надежных ГМТ с торсионным валом, установленным в ДВС и в повышающем обороты редукторе на входе в ГТ МПП для моторно-трансмиссионных установок с оппозитным дизельным ДВС без маховика легких ГМ с большой удельной мощностью, является актуальным вопросом.
Цель настоящей статьи – анализ работы торсионного вала, установленного в ДВС и в повышающем обороты редукторе на входе в ГТ МПП легкой ГМ с большой удельной мощностью, и повышение его надежности.
Новизна исследования – установка на выходной фланец ДВС (без маховика) в ограниченном по длине габарите пружинно-фрикционного демпфера крутильных колебаний, работающего в масле, что повышает надежность работы торсионного вала.
Анализ результатов. Характерные пятна на рис. 2 указывают на усталостные разрушения, так как из-за высокой цикличности работы вала не обеспечивается усталостная прочность, и получаются высокие касательные напряжения при кручении – ${{\tau }_{{ - 1}}}$. Для торсионного вала из стали 45ХН2МФА, используемого в ГМ массой 13–18 т, расчетные касательные напряжения составляют ${{\tau }_{{ - 1}}} = 3250$ кГс/см2. Количество циклов N работы торсионного вала определяется по выражению: $N = tnm$, где t – время работы, мин, n – номинальные обороты ДВС, об./мин, m – количество вспышек в цилиндрах за оборот ДВС. При количестве циклов $N \approx 1{\text{--}}2$ миллиона допускаемые напряжения ${\text{[}}{{{{\sigma }}}_{{ - 1}}}{\text{]}}$ для сталей существенно уменьшаются от ${\text{[}}{{{{\sigma }}}_{{ - 1}}}{\text{]}}$ = 14500 кГс/см2 до ${{{\text{[}}{{{{\sigma }}}_{{ - 1}}}{\text{]}}}_{{{\text{min}}}}}$ и соответственно уменьшаются допускаемые касательные напряжения ${\text{[}}{{{{\tau }}}_{{ - 1}}}{\text{]}}$ = ${\text{0}}{\text{.22[}}{{{{\sigma }}}_{{ - 1}}}{\text{]}}$ от ${\text{[}}{{{{\tau }}}_{{ - 1}}}{\text{]}} = 3190$ кГс/см2 до ${{[{{\tau }_{{ - 1}}}]}_{{\min }}}$.
При проверке на крутильный удар, $\frac{{J\omega _{0}^{2}}}{2} = \frac{{c\Delta {{\varphi }^{2}}}}{2}$, $\Delta \varphi = {{\omega }_{0}}\sqrt {\frac{J}{c}} $, где J – момент инерции ведущих частей; ${{\omega }_{0}}$ – угловая скорость; с – податливость торсионного вала; $\Delta \varphi $ – угол поворота торсионного вала.
При крутильном ударе от скручивания момент на торсионном валу определяется по формуле: $М = с\Delta \varphi $ = $2210{{\omega }_{0}}\sqrt {сJ} {\text{,}}$ кГс·м. При этом касательные напряжения от крутильного удара: $\tau = M{\text{/}}W$ = 41 000 кГс/см2, где W – момент сопротивления торсионного вала.
Для устранения таких напряжений рекомендуется убрать один из 2-х дисков трения блокировочного фрикциона ГТ и установить упруго-фрикционный демпфер, например, на противоположный конец ДВС установить демпфер сухого трения с буксующим диском или на выходном фланце ДВС установить в ограниченном по длине габарите пружинно-фрикционный демпфер крутильных колебаний, работающий в масле.
При кратковременном (0.2–0.3 с) импульсном воздействии 40–45 Тс от тепловой ударной установки на движущуюся ГМ усилие передается через корпус машины, гусеничный движитель, грунт, трансмиссию на базовый ДВС машины через включенный блокировочный фрикцион гидротрансформатора, имеющий коэффициент запаса по условиям работы моторно-трансмиссионной установки, и торсионный вал.
Уравнение движения центра тяжести быстроходной ГМ на подъеме при этом имеет вид: $P - R - {{R}_{I}} - G\sin \alpha - m\ddot {x} - {{P}_{a}}$ = 0, где P – сила тяги; R – сила сопротивления движению машины; RI – сила импульсного воздействия; G – вес машины; α – угол наклона местности; m – масса машины; $\ddot {x}$ – ускорение движения машины; Pa – сопротивление воздуха.
При импульсном воздействии диски трения включенного блокировочного фрикциона подвергаются пробуксовке, что отражается на их износе и изменении геометрических характеристик, а также на работе торсионного вала.
Расчет крутильных колебаний торсионного вала выполнен для варианта работы с незаблокированным ГТ [4, 5]. Опыт расчетного исследования аналогичных установок свидетельствует, что наиболее нагруженными элементами МТУ являются элементы силовой цепи ДВС–ГТ, причем нагруженность их полностью определяется вариантом работы с незаблокированным ГТ. Динамическая нагруженность от крутильных колебаний, возбуждаемых ДВС, элементов турбинной части МТУ даже при работе с заблокированным ГТ существенно ниже.
На рис. 4 представлены результаты расчета вынужденных крутильных колебаний в виде расчетной кривой амплитуд динамических нагрузок (MT) в торсионном вале от вынужденных крутильных колебаний в зависимости от оборотов ДВС.
Рис. 4.
Расчетные динамические нагрузки от вынужденных крутильных колебаний без демпфера во входном торсионном вале: 1 – ГТ не заблокирован; 2 – ГТ заблокирован, пятая передача; 3 – ГТ заблокирован, первая передача.
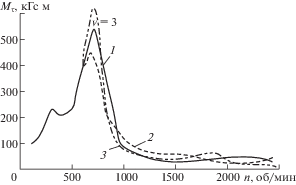
Максимальный уровень расчетных динамических нагрузок в торсионном вале между ДВС и трансмиссией MT = 560 кГс м имеет место на резонансе “главной” гармоники ${v}$ = 3 (${v}$ – порядок гармонической составляющей возмущающих моментов на кривошипно-шатунных массах коленчатого вала без маховика оппозитного дизельного ДВС) при n = 740 об./мин коленчатого вала. Этот уровень нагрузок может представлять опасность для входных элементов трансмиссии – зубчатых шестерен согласующего редуктора, шлицевых соединений и торсионного вала. В связи с этим длительная работа в диапазоне частот вращения коленчатого вала n < 1000 об./мин должна быть исключена. Регулировку ДВС необходимо выполнить таким образом, чтобы минимальная частота вращения на холостом ходу была не менее 1100 об./мин. Эта рекомендация дана по результатам тензометрирования ДВС в стендовой установке.
В легкой ГМ массой 13–18 т обеспечивается необходимое значение суммарной податливости элементов соединения ДВС с трансмиссией, при которой главные резонансные колебания выводятся в нерабочую, проходную зону частот вращения коленчатого вала n < 800 об./мин.
При этом уровень динамической нагруженности торсионного вала в зоне частот вращения n > 1100 об./мин становится незначительным. Максимальный уровень расчетных динамических нагрузок в диапазоне частот вращения коленчатого вала 1300 < n < 2500 об./мин не превосходит 50 кГсм.
Уровень расчетных динамических нагрузок в коленчатом вале ДВС во всем диапазоне частот вращения находится в допустимых пределах. Полученные результаты расчетного динамического анализа трансмиссии используются при расчете долговечности элементов трансмиссии [6–8].
Разработка пружинно-фрикционного демпфера крутильных колебаний, работающего в масле. Для быстроходных легких транспортных ГМ предлагается использовать силовой блок, состоящий из оппозитного дизельного ДВС (без маховика) и ГМТ, в котором установлен на свободном конце коленвала ДВС демпфер крутильных колебаний пружинно-фрикционного типа, работающий в масле. Выходной элемент демпфера связан с торсионным валом диаметром 35 мм длиной 430 мм, второй конец которого связан с повышающим обороты редуктором на входе в ГТ с блокировочным фрикционом.
На рис. 5 показан демпфер крутильных колебаний пружинно-фрикционного типа, работающий в масле. Демпфер – гаситель колебаний, состоит из упругого элемента – 20 пружин, расположенных по двум окружностям, для снижения жесткости трансмиссии и устранения возможности появления высокочастотного резонанса и фрикционного устройства с тарельчатыми пружинами для поглощения энергии низкочастотных резонансных колебаний. На поверхностях трения A и B ведомого диска позиция 3 рекомендуется наносить пористое фрикционное плазменное покрытие для повышения коэффициента трения и износостойкости [9, 10].
Рис. 5.
Пружинно-фрикционный демпфер крутильных колебаний – продольный разрез: 1 – болт; 2 – пружина; 3 – диск ведомый; 4, 17 – подшипники; 5 – винт для фиксации опоры от проворота; 6 – опора; 7 – заклепка; 8 – пружина тарельчатая (две подряд); 9 – заклепка; 10 – шайба регулировочная; 11 – диск с маховой массой; 12 – проставка МПП; 13 – диск ведущий; 14 – шайба; 15 – вал торсионный; 16 – кольцо стопорное; 18, 19 – шестерни привода маслонасоса системы гидроуправления; A, B – поверхности трения; D – диаметр посадочный поверхности картера МПП на ДВС.
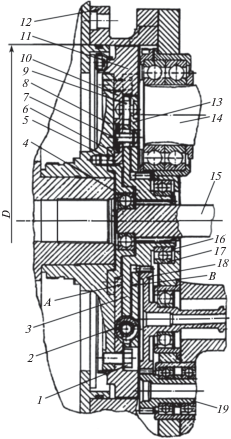
На рис. 6 показана расчетная схема для определения собственной частоты крутильных колебаний торсионного вала.
Рис. 6.
Расчетная схема для определения собственной частоты крутильных колебаний торсионного вала: 1 – ДВС (момент инерции j1 = 1.648 кг·м2); 2 – вал торсионный (длина L = 430 мм); 3 – насосное колесо ГТ (момент инерции j2 = 1.275 кг·м2).
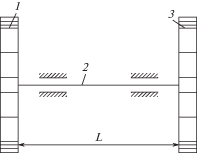
Предлагается методика расчета пружинно-фрикционного демпфера крутильных колебаний, работающего в масле:
1. Определение предельного момента ${{M}_{{up}}}$, скручивающего гаситель до упоров при двухрядном расположении цилиндрических пружин на концентрических окружностях с радиусами ${{R}_{{{\text{sr}}}}}$ ${{M}_{{{\text{up}}}}}$ = ${{P}_{2}}{{N}_{1}}{{R}_{{{\text{sr1}}}}}$ + $P_{2}^{'}{{N}_{2}}{{R}_{{{\text{sr2}}}}}$ = 222 кГс м, где ${{P}_{2}}$ – усилие одной пружины; ${{N}_{1}}$ – число пружин; ${{R}_{{{\text{sr1}}}}}$ – радиус расположения пружин, установленных в первом ряду. Параметры $P_{2}^{'}$, ${{N}_{2}}$, ${{R}_{{{\text{sr2}}}}}$ – те же самые параметры для пружин во втором ряду, $P_{2}^{'} = {{P}_{2}}\frac{{{{R}_{{{\text{sr2}}}}}}}{{{{R}_{{{\text{sr1}}}}}}}$. Должно быть ${{M}_{{{\text{up}}}}} > {{M}_{{d{v}\max }}}$, где ${{M}_{{d{v}\max }}}$ – максимальный момент на коленчатом валу ДВС.
2. Определение резонансных оборотов, при которых возникают крутильные колебания в связи с изменениями жесткости системы. Собственная частота крутильных колебаний для 2-х массовой системы определяется по формуле: ${{\omega }} = {{{\text{(}}{{c}_{k}}{\text{(}}{{j}_{1}} + {{j}_{2}}{\text{)/(}}{{j}_{1}}{{j}_{2}}{\text{))}}}^{{0.5}}}$, где ck – крутильная жесткость системы без учета жесткости торсионного вала; ${{c}_{k}} = {{R}_{{{\text{sr1}}}}}{{M}_{{{\text{up}}}}}{\text{/}}{{S}_{2}}$, где S2 – рабочая деформация пружины. Резонансное число оборотов: ${{n}_{{d{v}}}} = n{\text{/}}a = 651$ мин–1, где а – число вспышек за один оборот коленчатого вала ДВС, $n = 30{{\omega /\pi }}$.
3. Определение резонансных оборотов системы с учетом жесткости пружин и торсионного вала: $c_{k}^{'} = {{\left( {c_{k}^{{ - 1}} + c_{{k{\text{val}}}}^{{ - 1}}} \right)}^{{ - 1}}}$, где ${{c}_{{k{\text{val}}}}}$ – жесткость торсионного вала; $c_{{k{\text{val}}}}^{{}} = GJ{\text{/}}L$, где G – модуль упругости материала; J, L – соответственно момент инерции и длина торсионного вала. Резонансные обороты ДВС: $n_{{d{v}}}^{'} = {{n}_{{d{v}}}}{{{\text{(}}c_{k}^{'}{\text{/}}{{c}_{k}}{\text{)}}}^{{0.5}}}$ = 557 мин–1.
4. Расчет параметров поглотителя энергии низкочастотных резонансных колебаний. Оптимальное значение момента трения фрикционного устройства ${{M}_{{{\text{fr}}{\kern 1pt} {\text{opt}}}}}$ = = $\sqrt 2 {{J}_{{{\text{gt}}}}}{{{{\omega }}}^{2}}\varphi {}_{0}/{{\pi }}$ = 20.21 кГс·м, где ω – угловая частота вращения коленчатого вала ДВС при околорезонансных оборотах; $\omega = \pi n_{{d{v}}}^{'}{\text{/}}30$, ${{J}_{{{\text{gt}}}}}$ – момент инерции насосного колеса ГТ относительно оси вращения; ${{\varphi }_{0}} = {{\varphi }_{{{\text{fr}}}}} + {{\varphi }_{{{\text{val}}}}}$ – амплитуда колебаний угла поворота того сечения вала, с которым связан поглотитель энергии; ${{\varphi }_{{{\text{fr}}}}}$ – угол проворота элементов фрикционного устройства, ${{\varphi }_{{{\text{val}}}}}$ – угол закрутки торсионного вала. По рекомендации И.А. Биргера и Я.Г. Пановко $\varphi \approx 0.035{\text{--}}0.07$ рад, ${{M}_{{{\text{fr}}}}} \approx (0.15{\text{--}}0.25){{M}_{{d{v}}}}$ [5].
5. Определение момента трения фрикциона, заложенного в конструкции. ${{M}_{{{\text{fr}}}}} = 0.5{{P}_{{{\text{ts}}}}}\mu z{{R}_{{{\text{sr}}}}}Km$ = 14.48 кГс·м, где ${{P}_{{{\text{ts}}}}}$ – усилие одной тарельчатой пружины; μ – коэффициент трения сталь по стали в масле; z – число пар поверхностей трения; ${{R}_{{{\text{sr}}}}}$ – средний радиус поверхности трения; K – количество пакетов тарельчатых пружин; m – число пружин в пакете.
Рассчитанный по методике демпфер за счет пружин снижает резонансные обороты с 970 до 557 об./мин вследствие уменьшения частоты собственных колебаний системы и предохраняет систему “ДВС–насосное колесо ГТ” от резонанса на низких частотах при ${{n}_{{d{v}}}}$ = 557 об./мин за счет фрикционного устройства.
По результатам проведенного расчета рекомендуемая схема установки выбранной тарельчатой пружины в демпфере для обеспечения необходимого момента трения и его повышения при наличии места для компоновки демпфера показана на рис. 7. Пружины должны быть установлены по схеме конус в конус.
Эксплуатационные испытания на машинах пружинно-фрикционного демпфера крутильных колебаний. ГТ в МПП при испытаниях устанавливался с однодисковым блокировочным фрикционом. На быстроходной ГМ массой 13.2 т демпфер крутильных колебаний испытывался в пробеге 4000 км без замечаний, обеспечивал нормальную работу силового блока. На быстроходной ГМ массой 18 т демпфер испытывался в пробеге 1900 км без замечаний, силовой блок нормально работал. Поломок торсионного вала при испытаниях не было.
Вывод. Результаты анализа работы торсионного вала, установленного в ДВС и в повышающем обороты редукторе на входе в ГТ МПП, и рекомендации по уменьшению числа фрикционных дисков в блокировочном фрикционе ГТ с двух до одного и установки пружинно-фрикционного демпфера крутильных колебаний для повышения надежности работы торсионного вала можно использовать при создании новых ГМТ легких ГМ с большой удельной мощностью.
Список литературы
Труханов В.М., Зубков В.Ф., Крыхтин Ю.И., Желтобрюхов В.Ф. Трансмиссии гусеничных и колесных машин. М.: Машиностроение, 2001. 736 с.
Львовский К.Я., Черпак Ф.А., Серебряков И.Н., Щельцин Н.А. Трансмиссии тракторов. М.: Машиностроение, 1970. 280 с.
Шарипов В.М. Конструирование и расчет тракторов. М.: Машиностроение, 2004. 590 с.
Сцепления транспортных и тяговых машин / Под ред. Ф.Р. Геккера, В.М. Шарипова, Г.М. Щеренкова. М.: Машиностроение, 1989. 340 с.
Прочность. Устойчивость. Колебания. Справочник / Под общей редакцией И.А. Биргера и Я.Г. Пановко. Т. 3. М.: Машиностроение, 1968. 338 с.
Светлицкий В.А., Нарайкин О.С. Упругие элементы машин. М.: Машиностроение, 1989. 261 с.
Маслов Г.С. Расчеты колебаний. М.: Машиностроение, 1968. 271 с.
Ивович В.А., Онищенко В.Я. Защита от вибрации в машиностроении. М.: Машиностроение, 1990. 272 с.
Крыхтин Ю.И., Карлов В.И. Физические основы разработки заготовок дисков трения с молибденовым покрытием для повышения надежности работы в масле в узлах трансмиссий транспортных машин // Вестник машиностроения. 2016. № 12. С. 70.
Крыхтин Ю.И., Карлов В.И. Физические основы разработки дисков трения с бронзовым покрытием для транспортных машин // Вестник машиностроения. 2018. № 6. С. 42.
Дополнительные материалы отсутствуют.
Инструменты
Проблемы машиностроения и надежности машин