Проблемы машиностроения и надежности машин, 2021, № 4, стр. 81-87
Управление сборкой изделий на основе данных о параметрах составляющих деталей и сборочных единиц
А. В. Медведев 1, *, И. Ю. Зараменский 1, Е. М. Халатов 1
1 Конструкторское бюро “Арматура” –
филиал АО “Государственный космический научно-производственный центр
имени М.В. Хруничева”
Ковров, Владимирская обл., Россия
* E-mail: mavrich@mail.ru
Поступила в редакцию 07.11.2020
После доработки 29.03.2021
Принята к публикации 26.04.2021
Аннотация
На примере электрогидравлического сервопривода показано, как данные о численных значениях параметров составляющих деталей и сборочных единиц, поступающих на участок сборки, позволяют управлять ходом сборки, качественно преобразовать процесс сборки и улучшить характеристики готовых изделий. Описанный подход к организации сборки можно применить для любых изделий, как с целью обеспечения сборки годных изделий при изготовлении составляющих деталей с заведомо расширенными полями допусков на значения параметров, так и с целью улучшения характеристик и снижения трудоемкости регулировок изделий.
Процессы сборки подавляющего большинства изделий: механических, оптических, электротехнических, построены с применением допускового контроля качества. В технической документации на такие изделия заданы диапазоны значений (поля допусков) параметров составляющих деталей и сборочных единиц (ДСЕ), при которых с достаточной вероятностью обеспечивается сборка годного изделия – изделия, численные значения характеристик которого также лежат в заданных диапазонах. Если перед вовлечением в сборку и измеряют значения параметров ДСЕ, то только чтобы убедиться, что они лежат в заданных диапазонах, ДСЕ распределяют по сборочным комплектам случайным образом, без учета измеренных значений их параметров. В силу этого дальнейший процесс сборки приобретает элементы случайности: значения характеристик готовых изделий – случайные величины в пределах полей допусков, становятся известны только по окончании сборки. Последнее справедливо и для селективной сборки изделий методом групповой взаимозаменяемости, когда селективные группы деталей определены по значениям их параметров так, чтобы обеспечить сборку годного изделия без улучшения характеристик в пределах поля допуска. В то же время известны случаи, когда сборка сложных прецизионных изделий требует направленного подбора ДСЕ исходя из измеренных значений их параметров [1–3]. За счет такого подбора достигается улучшение характеристик изделий. Более того, данные об измеренных значениях параметров ДСЕ можно использовать для прогноза характеристик будущих изделий, для подбора оптимальных параметров регулировок изделий до начала сборки [4, 5]. В целом, данные об измеренных значениях параметров ДСЕ, поступающих на участок сборки, дают возможность активно воздействовать на процесс, управлять сборкой. При этом в роли объекта управления выступает процесс сборки одного или партии изделий, результатом управления являются значения характеристик готовых изделий, сигналом управления – подобранные сочетания ДСЕ в сборочных комплектах и подобранные параметры регулировок. Такой подход к организации сборки является развитием селективной сборки, причем при решении задачи обеспечения сборки годных изделий и улучшения их характеристик он потенциально более эффективен, чем метод групповой взаимозаменяемости [6, 7]. Несмотря на это, в силу сложности реализации, примеры практического внедрения такого подхода к организации сборки сложных прецизионных изделий редки, а результаты не достаточно описаны. В представленных результатах внедрения управления сборкой для изготовления такого сложного прецизионного изделия как электрогидравлический сервопривод (ЭГС) показано, как управление сборкой влияет на процесс сборки и характеристики готовых изделий.
Конструкция ЭГС показана на рис. 1. ЭГС представляет собой электро-гидромеханическое силовое исполнительное устройство, предназначенное для перемещения инерционного объекта на расстояние, пропорциональное входному электрическому сигналу, с требуемой динамической и статической точностью при воздействии различных нагрузок.
Рис. 1.
Конструкция ЭГС: 1 – гидроцилиндр с блоком гидрозамков; 2 – гидродемпфер; 3 – корпус; 4 – электрогидравлический усилитель; 5 – механизм обратной связи; 6 – блок фильтров; 7 – хвостовик.
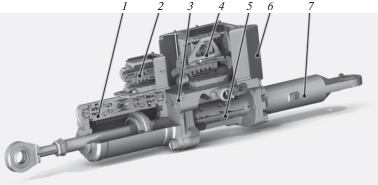
К ЭГС предъявляются высокие требования. Сложность сборки рассматриваемого изделия обусловлена тем, что характеристики изделия взаимосвязаны и нелинейно зависят от параметров составляющих ДСЕ. Изготовление ДСЕ с малым разбросом параметров технически сложно. Как результат – неблагоприятное сочетание параметров ДСЕ может приводить к сборке привода, характеристики которого не будут удовлетворять всем требованиям технической документации на изделие. Блок-схема процесса сборки ЭГС без учета параметров составляющих ДСЕ показана на рис. 2а. Помимо поэтапной установки отдельных ДСЕ сборка ЭГС включает в себя выполнение регулировок: сначала первого каскада электрогидравлического усилителя, затем – второго каскада, разомкнутого привода и привода замкнутого обратной связью. Результаты каждой регулировки контролируются по результатам испытаний. В ходе сборки ЭГС необходимо обеспечить выполнение требований к четырнадцати взаимосвязанным характеристикам отдельных сборок и изделия в целом (девять из них – характеристики готового изделия).
Рис. 2.
Блок-схема сборки ЭГС: (а) – без учета измеренных значений параметров составляющих
ДСЕ; (б) – при управлении процессом с учетом данных об измеренных значениях параметров
составляющих ДСЕ; – условный номер цикла итераций при выполнении регулировок.
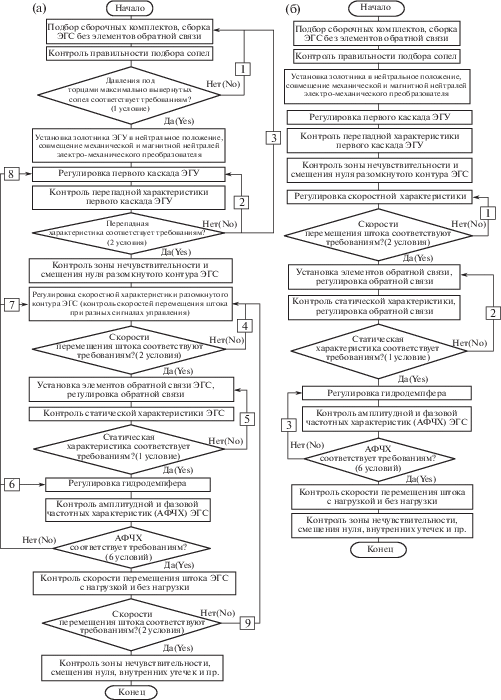
Конструкция ЭГС имеет четыре места регулировки, однако данные регулировки позволяют лишь частично компенсировать отклонения параметров ДСЕ от номинальных значений, придавая процессу сборки трудоемкий итерационный характер. Блок-схема (рис. 2а) демонстрирует такой характер сборки привода. Из-за высокой трудоемкости регулировка ЭГС часто заканчивается при получении характеристик изделий, удовлетворяющих требованиям технической документации, но не оптимальных.
Рассмотрим процесс сборки ЭГС с позиций теории управления. В общем случае, для изделия с возможностью регулировки процесс сборки можно описать схемой управления с обратной связью (рис. 3а), где в роли объекта управления выступает процесс сборки A, в роли выходного сигнала объекта – полученный по результатам испытаний вектор измеренных значений характеристик изделия Zm, а в роли регулятора – исполнитель T, специалист, руководящий сборкой. В ходе сборки и выполнения регулировок исполнитель по результатам испытаний сравнивает измеренные значения характеристик изделия Zm с номинальными (требуемыми) Zn и предпринимает корректирующие действия: выполняет или изменяет регулировки, набор которых можно описать вектором Y. На схеме векторы X и Q – соответственно вектор измеренных значений параметров поступивших на участок сборки ДСЕ и вектор внешних по отношению к процессу сборки параметров испытательного оборудования и режимов испытаний, оказывающих влияние на результаты измерения характеристик изделия. В случае сборки ЭГС к составляющим вектора Q можно отнести: температуру рабочей жидкости при испытаниях, давление рабочей жидкости на входе в ЭГС, жесткость крепления привода в испытательном стенде и т.п. Данные параметры режимов испытаний и оборудования непостоянны и меняются в определенных границах от образца к образцу.
Рис. 3.
Схема управления процессом сборки: (а) – без учета измеренных значений параметров составляющих ДСЕ; (б) – при управлении процессом с учетом данных об измеренных значениях параметров составляющих ДСЕ; T – исполнитель; A – процесс сборки; C – регулятор; I – идентификатор.
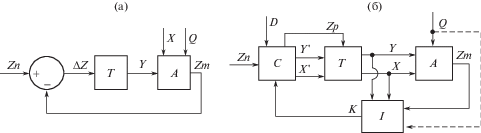
Как можно убедиться на примере ЭГС, сборка изделий без учета измеренных значений параметров составляющих ДСЕ имеет недостатки: 1) до начала сборки невозможно спрогнозировать, какие значения будут иметь характеристики собираемых изделий, выполнение регулировок в процессе сборки носит итерационный характер; 2) воздействовать на характеристики собираемых изделий можно только путем регулировок; 3) не учитывается партионность изготовления, при сборке очередного изделия исполнитель руководствуется результатами испытания только одного, собираемого в данный момент изделия, нет возможности до сборки определить целесообразность изменения состава сборочных комплектов для улучшения или выравнивания значений характеристик изделий в партии.
Сборку ЭГС при управлении процессом с учетом данных об измеренных значениях параметров составляющих ДСЕ можно описать схемой рис. 3б. В отличие от рассмотренного выше случая в процесс сборки включены блок регулятор C и блок идентификатор I. Регулятор – программное обеспечение (ПО), выполняющее подбор деталей в сборочные комплекты по их параметрам X ' и подбор параметров регулировок Y ' изделий с помощью математической модели изделия. Подбор осуществляется путем решения задачи оптимизации: сочетание деталей в комплектах и параметры регулировок должны обеспечивать сборку партии изделий с наибольшими относительными величинами отклонений прогнозируемых значений характеристик от предельно допустимых значений. Идентификатор – ПО, уточняющее параметры K математической модели, используемой регулятором. Уточнение происходит по результатам испытаний изделия.
В соответствии со схемой рис. 3б сборка изделий происходит следующим образом. До начала сборки на основе данных об измеренных значениях параметров изготовленных на данный момент ДСЕ (массив данных D) регулятором C автоматически производится распределение деталей по сборочным комплектам и подбор регулировок для сборки партии изделий. Для каждого изделия в отдельности результаты прогноза его характеристик Zp, рекомендуемое сочетание деталей в сборочном комплекте X ', а также подобранные параметры регулировок Y ', поступают к исполнителю T. Исполнитель, руководствуясь личным опытом, принимает окончательное решение, какие сочетания ДСЕ использовать, начинается сборка11. В ходе сборки по результатам отдельных регулировок и испытаний (при получении новой информации о собираемом изделии) математическая модель изделия для каждого образца уточняется идентификатором I, соответственно уточняются прогнозируемые значения характеристик будущего изделия. Уточнение ряда параметров математической модели необходимо по той причине, что результаты прогноза характеристик ЭГС чувствительны даже к их небольшому отклонению, но задать с требуемой точностью все параметры математической модели до начала сборки невозможно. Например, до начала сборки, при подборе ДСЕ в сборочные комплекты и подборе параметров регулировок, используется величина математического ожидания передаточного отношения механизма обратной связи ЭГС. Действительное же значение для каждого образца можно определить только в ходе сборки, так как сам механизм формируется при сборке, а величина его передаточного отношения зависит от сочетания размеров и отклонений форм поверхностей большого количества деталей. Также данные, полученные в ходе сборки, данные о параметрах ДСЕ и данные о действительных параметрах режимов испытаний изделий Q, позволяют идентифицировать, контролировать и учитывать параметры испытательного оборудования, влияющие на результаты испытаний (рис. 3б, пунктирная линия). При каждом уточнении модели регулятор предлагает исполнителю два сценария продолжения сборки: 1) ранее выполненные регулировки не изменяются, регулятор подбирает значения регулировок, которые только предстоит выполнить; 2) все параметры регулировок, в том числе и ранее выполненных, изменяются на оптимальные, полученные для уточненной модели. В зависимости от того, насколько новые прогнозируемые значения отдельных характеристик изделия удалены от предельно допустимых значений, исполнитель продолжает сборку, возвращается к ранее выполненным регулировкам, принимает решение о замене или доработке отдельных ДСЕ для получения требуемых характеристик будущего изделия.
Преимущества рассмотренного способа организации сборки изделий по сравнению со сборкой изделий без учета измеренных значений параметров составляющих ДСЕ следующие: 1) до начала сборки становится возможным спрогнозировать характеристики будущих изделий и построить процесс регулировки так, чтобы сократить количество итераций; 2) подбор деталей в сборочные комплекты, как и подбор регулировок, становится инструментом воздействия на характеристики будущих изделий и дает возможность улучшить их; 3) до начала сборки известны прогнозируемые значения характеристик всех изделий в партии, сборка отдельных изделий может вестись с их учетом для получения партии изделий с близкими значениями характеристик.
Для оценки влияния управления на процесс сборки изделий был проанализирован ход сборки и составлена блок-схема процесса сборки ЭГС при внедрении управления (рис. 2б). Сравнение блок-схем (рис. 2), демонстрирует: благодаря внедрению управления из процесса сборки исключено шесть циклов регулировки-контроля характеристик и повторной регулировки или замены деталей. Это позволяет снизить трудоемкость сборки одного ЭГС на 20%, что составляет 11% от общей трудоемкости изготовления изделия. В ходе сборки возможны итерации, вызванные уточнением математической модели, но количество их минимально.
Для оценки результатов внедрения управления сборкой было смоделировано изготовление 1000 ЭГС и получены распределения их характеристик при случайном подборе ДСЕ в сборочные комплекты и при сборке изделий партиями по 2 и 4 изделия. В качестве примера (рис. 4) приведены распределения одной из характеристик ЭГС. К выбранной i-й характеристике предъявляется требование, чтобы ее значение было не меньше предельно допустимой величины [zmin i]. Существует вероятность сборки изделия, значения i-й характеристики которого не будут удовлетворять требованиям технической документации. Сравнение распределений демонстрирует, что управление сборкой позволяет сместить значения характеристики изделий вправо от минимальной допустимой величины и уменьшить разброс значений. Это происходит за счет подбора лучших сочетаний ДСЕ в сборочных комплектах, подбора параметров регулировок и изменения значений прочих, связанных с ней характеристик. Изменение прочих характеристик происходит так, чтобы для всех изделий в партии по всем характеристикам относительные величины отклонений их значений от предельно допустимых величин были не менее чем у рассматриваемой характеристики. Благодаря этому ожидается снижение вероятности сборки негодного ЭГС с 8.4% – при случайном формировании сборочных комплектов, до 1% – при управлении сборкой ЭГС и сборке их партиями всего по четыре изделия.
Рис. 4.
Гистограмма распределения значений i-й характеристики: при случайном подборе ДСЕ (), при управлении процессом и сборке изделий партиями по два изделия (
), при управлении процессом и сборке изделий партиями по четыре изделия (
), zi – значение i-й характеристики, N(zi) – число изделий с значением i-й характеристики в пределах диапазона, [zmin i] – минимальное допустимое значение i-й характеристики.
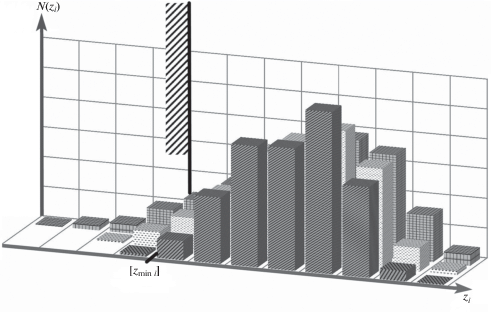
Опыт организации управления сборкой ЭГС, исходя из измеренных значений параметров составляющих ДСЕ, демонстрирует, что данный подход к производству можно распространить на любые изделия, для которых с помощью математической модели можно установить связь между параметрами составляющих ДСЕ и характеристиками готового изделия. Управление сборкой может применяться как с целью обеспечения сборки годных изделий, если составляющие ДСЕ изготавливаются с заведомо расширенными полями допусков на значения параметров, так и с целью улучшения характеристик, снижения трудоемкости регулировок изделий. Более того, предложенный подход к изготовлению позволяет качественно преобразовать процесс сборки, а полученные при этом данные можно использовать на других этапах жизненного цикла изделий. Например, данные о параметрах составляющих ДСЕ и характеристиках готовых изделий позволяют вести мониторинг качества изготовления, определять пути повышения качества и модернизации изделий. Уточненные в процессе сборки математические модели отдельных образцов изделий можно использовать в системах управления изделиями, а также для автоматизации контроля технического состояния изделий при эксплуатации.
Список литературы
Сазанов А.А. Повышение эффективности изготовления топливных форсунок ГТД путем функционально-ориентированной сборки: Дис. … канд. техн. наук. Рыбинск, 2014. 166 с.
Смирнова Е.В. Разработка и исследование технологии адаптивно-селективной сборки для многоэлементных инфракрасных приемников: Автореф. дис. … канд. техн. наук. Спб., 2011. 19 с.
Kannan R., Selladurai V. Optimization of Characteristic Parameters of Turbocharger Assembly using GA // Manufacturing and industrial engineering, 2011. Iss. 1. P. 39.
Безъязычный В.Ф., Непомилуев В.В., Семенов А.Н. Обеспечение качества изделий при сборке: Монография / В.Ф. Безъязычный, В.В. Непомилуев, А.Н. Семенов. М.: Издательский дом “Спектр”, 2012. 204 с.
Недайвода А.К. Технологические основы обеспечения качества ракетно-космической техники. М.: Машиностроение, 1998. 240 с.
Сорокин М.Н., Ануров Ю.Н. Анализ собираемости изделий типа “вал–втулка” при селективной сборке // Сборка в машиностроении и приборостроении. 2012. № 1. С. 23.
Непомилуев В.В. Исследование возможностей повышения качества изделий при сборке // Сборка в машиностроении и приборостроении. 2007. № 10. С. 9.
Дополнительные материалы отсутствуют.
Инструменты
Проблемы машиностроения и надежности машин