Проблемы машиностроения и надежности машин, 2021, № 4, стр. 50-58
Повышение надежности технологического процесса штамповки с кручением изделий из алюминиевого сплава
П. А. Петров 1, *, А. Г. Матвеев 1, Б. Ю. Сапрыкин 1, М. А. Петров 1, И. А. Бурлаков 1, У. Ш. Диксит 2
1 Московский политехнический университет
Москва, Россия
2 Индийский институт технологии Гувахати
Гувахати, Индия
* E-mail: petrov_p@mail.ru
Поступила в редакцию 03.10.2020
После доработки 29.03.2021
Принята к публикации 26.04.2021
Аннотация
В настоящей статье представлены методологические подходы к повышению точности расчета сложного малоизученного технологического процесса штамповки кручением на основе компьютерного имитационного моделирования. Представлена методика постановки обратной задачи для одного из известных типов испытаний на сжатие образцов из алюминиевого сплава; приведены результаты моделирования испытаний и их сравнение с данными, полученными при проведении экспериментов. Рассмотрено испытание на сжатие сплошных цилиндрических образцов. Представлена схема реализации обратной задачи (инверсионного метода). Полученные результаты можно применить при подготовке исходных данных на этапе разработки либо оптимизации технологического процесса штамповки кручением на основе компьютерного имитационного моделирования в специализированных программах, например, программе QFORM.
Тонкостенные осесимметричные поковки без фланца и с фланцем, из алюминиевых сплавов (АМг2, АМг3, АМг6 и т.п.), нашли свое применением во многих отраслях промышленности, в т.ч. судостроении, авиастроении и автомобилестроении. Учитывая сложность геометрии, поковки можно изготовить за более, чем одну операцию обработки давлением. Традиционным способом изготовления таких поковок является холодная либо горячая объемная штамповка из мерной заготовки, а также горячая изотермическая штамповка.
При производстве вышеуказанных поковок, контактное взаимодействие заготовки и инструмента играет существенную роль при оценке стойкости инструмента; оказывает существенное влияние на штампуемость материала заготовки и на качество конечного изделия. Одной из современных прогрессивных технологий штамповки, позволяющей изготавливать тонкостенные осесимметричные поковки, является технология штамповки с кручением [1].
В теоретическом плане на технологическую эффективность процесса осесимметричной осадки с кручением было указано в работах Г.Д. Полосаткина, С.П. Буркина и Б.Р. Картака, А.Н. Леванова, В.Н. Субича [1], А.Д. Хвана [2] и др. Наиболее системный подход к проектированию оборудования, теоретическому анализу кинематики течения деформируемого материала и практическому освоению технологии штамповки с кручением представлен В.Н. Субичем и его учениками в их работах, например, в монографии [1].
Для технологии штамповки с кручением характерно, что остаются малоизученными вопросы контактного взаимодействия заготовки и инструмента, характер течения материала на контактной поверхности, топология микронеровностей на контактной поверхности и их изменение в процессе скольжения деформируемого материала по контактной поверхности, условия теплообмена между заготовкой и инструментом, выбор технологической смазки [1].
Отсутствие теоретического обоснования механики контактного и теплового взаимодействия деформируемого слоя и инструмента не позволяет дать рекомендации для разработки технологических процессов штамповки с кручением и их рациональных режимов выполнения для изготовления тонкостенных осесимметричных поковок из алюминиевых сплавов с различным состоянием поставки (литая заготовка; прессованный или прокатанный пруток; заготовка, полученная по технологии SLM либо EBM) на основе применения компьютерного имитационного моделирования.
В работе [3] предложена конечно-элементная модель процесса осадки с кручением (рис. 1) для исследования процесса теплопереноса при деформировании цилиндрической заготовки при температуре 20°С.
Рис. 1.
Конечно-элементная модель осадки с кручением: (a) – первый этап процесса (осесимметричная осадка); (б) – второй этап процесса (осесимметричная осадка с кручением).
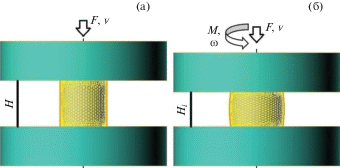
Рассматриваемая модель (рис. 1) является первичной и требующей уточнения таких параметров, как сопротивление материала заготовки пластической деформации (кривые текучести) и контактное трение (модель трения и значение фактора трения).
Как показывают результаты виртуальных испытаний работы [3], тепловой эффект контактного трения является наиболее сильным механизмом теплопереноса в процессе осадки с кручением; тепловой эффект пластической деформации рассматривается как константа материала в заданных температурно-скоростных условиях деформирования и играет второстепенную роль. Анализируя результаты работы Б.А. Кривицкого [4] можно отметить, что даже при горячей деформации тепловой эффект за счет пластической деформации не превышает 50–60°С. В случае же осадки с кручением суммарный тепловой эффект наблюдается много большим. На рис. 2 представлены результаты расчета поля температуры в сечении деформируемой заготовки, полученные с применением программы компьютерного моделирования QFORM.
Рис. 2.
Распределение температуры при деформировании заготовки на втором этапе процесса (осесимметричная осадка с кручением): (a) – приращение температуры от контактного трения; (б) – максимальное приращение температуры в процессе.
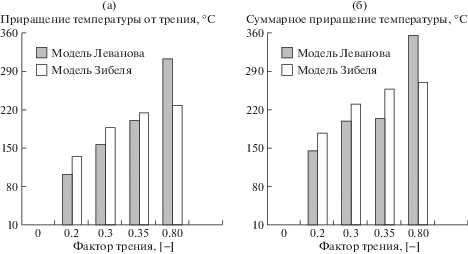
Для алюминиевого сплава, например, АМг2, АМг3 либо АМг6, температура нагрева в диапазоне от 200 до 400°С соответствует теплой и полугорячей деформации. То есть модель сопротивления деформации, описывающая изменение напряжения текучести в заданных температурно-скоростных условиях, должна быть работоспособной как при холодной пластической деформации, так и при теплой и полугорячей деформации. Выявленная особенность теплопереноса в процессе осадки с кручением накладывает дополнительное требование на подготовку исходных данных о сопротивлении материала деформации для выполнения компьютерного имитационного моделирования.
При подготовке данных для имитационного моделирования в специализированных САЕ-системах помимо данных о сопротивлении деформации, необходимо задать характеристики технологической смазки (показатель трения и модель контактного трения). Точность выполнения расчетов при моделировании определяется достоверностью задаваемых исходных данных [5–7], адекватностью математической модели, например, модели сопротивления деформации, а также надежностью выбранных методов оптимизации для построения модели процесса либо объекта [8]. Это утверждение основано на результатах исследований, связанных с применением компьютерного имитационного моделирования [5–7].
Целью настоящей статьи является формализация методики постановки обратной задачи для испытания на сжатие образцов алюминиевого сплава и последующего применения полученных данных при САЕ-моделировании. В качестве испытания рассматривается испытание на сжатие сплошных цилиндрических образцов.
Рассмотрим алгоритм обработки результатов экспериментов, методика которых известна [9] и схему постановки обратной задачи, которые в последующем можно использовать для автоматизации обработки данных эксперимента.
Испытание на сжатие цилиндрических образцов
Алгоритм обработки экспериментальных результатов включает три этапа:
1. Первичная обработка экспериментальных кривых текучести (рис. 3), в том числе: 1) нормализация данных – основываясь на данных эксперимента формируется новый массив данных, включающий значения параметров: времени (t), накопленной деформации (ε), перемещения инструмента (Δh), напряжения текучести (σ) и силы деформирования (P); новый массив данных имеет меньшее число значений для каждого из пяти параметров; в результате нормализации кривые текучести, полученные для различных значений скорости деформации имеют одинаковое число точек, что упрощает последующую обработку данных (программный код – ПК1); 2) сглаживание экспериментальной кривой текучести – процедура, обеспечивающая получение гладкой кривой текучести и индикаторной диаграммы без выраженных колебаний значений; колебание значений возникает при записи данных в контроллер испытательной машины во время проведения испытания (программный код – ПК2); 3) определение средней экспериментальной кривой текучести для фиксированной температуры испытания и заданной скорости деформации (программный код – ПК3); 4) объединение средних экспериментальных кривых текучести и визуализация результатов – кривые текучести, входящие при объединении в набор, соответствуют одной и той же номинальной температуре испытания, но различным скоростям деформации (программный код – ПК4; пример объединенных кривых текучести для температуры 340°С (рис. 4));
Рис. 4.
Пример объединения экспериментальных кривых текучести (алюминиевый сплав АМг3, температура 340°С): 1 – 0.1 с–1; 2 – 1.0 с–1; 3 – 10.0 с–1; 4 – 30.0 с–1.
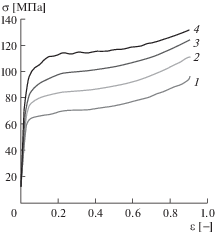
2. Построение изотермической кривой текучести (рис. 5):
1) корректировка экспериментальной кривой текучести с учетом колебания скорости деформации в процессе монотонного нагружения относительно номинального значения скорости деформации (программный код – ПК5; пример колебаний в ходе испытания текущего значения скорости деформации относительно ее номинального значения представлен на рис. 6); 2) корректировка экспериментальной кривой текучести с учетом влияния контактного трения на сопротивление деформации [9] (программный код – ПК6); 3) корректировка экспериментальной кривой текучести с учетом влияния теплового эффекта пластической деформации на сопротивление деформации [9] (программный код – ПК7); 4) корректировка экспериментальной кривой текучести с учетом влияния теплового эффекта контактного трения на сопротивление деформации [9] (программный код – ПК8); 5) построение изотермической кривой текучести для заданной температуры и скорости деформации, а также объединение изотермических кривых текучести, соответствующих одной и той же номинальной температуре испытания, но различным скоростям деформации, в набор данных, визуализированных в одной системе координат (программный код – ПК9).
Рис. 6.
Пример колебания скорости деформации в процессе монотонного нагружения (испытательная машина марки INSTRON VHS400kN) образца при температуре 340°С: (а) – номинальная скорость деформации 0.1 с–1; (б) – номинальная скорость деформации 1.0 с–1; (в) – номинальная скорость деформации 10.0 с–1; 1 – значение в эксперименте; 2 – сглаживание; 3 – среднее значение; 4 – номинальное значение.
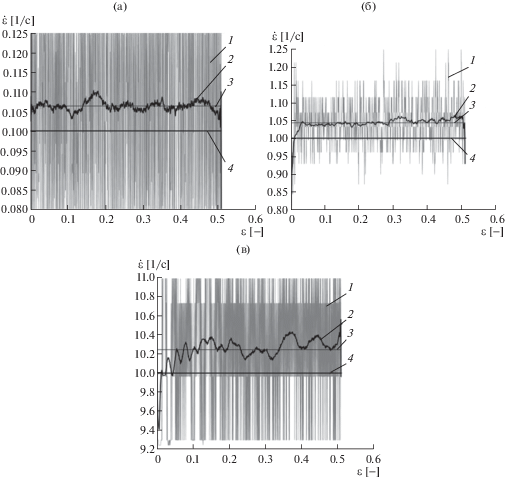
3. Формирование фрагмента базы данных материалов для компьютерного моделирования процессов пластического деформирования с применением CAE-систем.
В завершение первичной обработке кривых текучести (шаг 1) принимается решение о дальнейшем применении результатов. В случае если полученные кривые имеют ярко выраженную немонотонность, обусловленную погрешностью эксперимента, неверным выбором/заданием программы нагружения, либо ошибками обработки при сборе данных на испытательной машине, результаты первичной обработки должны быть уточнены путем проведения повторного эксперимента.
В завершение построения изотермической кривой текучести (рис. 5, шаг 2) принимается решение о включении полученных результатов в базу данных материалов пригодную для выполнения CAE-моделирования либо о выполнении еще одного расчета и построении новой кривой текучести соответствующей другим температурно-скоростным условиям деформирования.
Для устранения выявленной погрешности в найденных кривых текучести применялся метод постановки обратной задачи (инверсионный метод).
Существенным преимуществом метода постановки обратной задачи перед обычными аналитическими методами корректировки кривых текучести является то, что в программе QFORM, благодаря учету градиента температур и скоростей деформации по сечению образца, расчет ведется не по одной кривой текучести, построенной для определенной температуры и скорости деформации, а по группе соседних кривых (для других ближайших температур и скоростей деформации), каждая из которых оказывает влияние на итоговый график силы, а, следовательно, и на корректировку каждой из соседних кривых текучести, тогда как в обычных аналитических методах кривые текучести корректируются отдельно.
Метод инверсионного анализа можно описать алгоритмом (рис. 7), в котором кривые текучести корректируются в соответствии с расхождениями в диаграммах сил (экспериментальной и расчетной), и после каждой корректировки моделирование осадки цилиндрического образца повторяется, до тех пор, пока не будет достигнута требуемая сходимость расчетного и экспериментального результатов, составляющая ±2.5%
(1)
$\delta = \left| {\frac{{{{P}_{{{\text{QFORM}}}}} - {{P}_{{{\text{эксп}}}}}}}{{{{P}_{{{\text{эксп}}}}}}} \times 100\% } \right| \leqslant 2.5\% ,$В качестве примера, на рис. 8 представлены результаты, полученные после проведения циклов корректировок для кривых текучести при температуре 340°С.
Рис. 8.
Кривые текучести сплава АМг3 при температуре 340°С: 1 – экспериментальная кривая текучести; 2 – кривая текучести с учетом компенсации контактного трения; 3 – “изотермическая” кривая текучести.
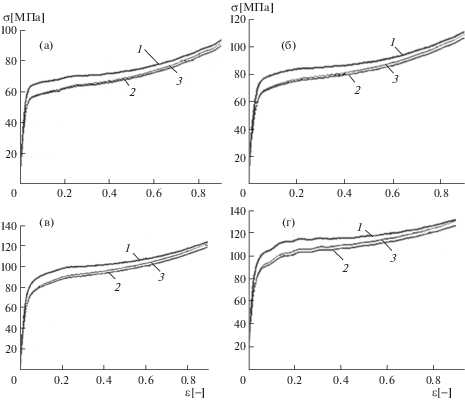
Заключение и выводы. 1. Выполнен анализ теплопереноса в процессе осадки с кручением и установлено, что наиболее важным механизмоv теплопереноса является тепловой эффект контактного трения, приводящий к приращению температуры от 102 до 312°С (рис. 2) в зависимости от модели контактного трения и значения фактора трения. 2. Подготовка исходных данных для компьютерного имитационного моделирования процесса осадки с кручением при температуре 20°С предполагает выбор модели сопротивления деформации и модели контактного трения. 3. Модель сопротивления деформации должна быть задана в широком диапазоне температурно-скоростных условий деформирования, несмотря на то, что пластическая деформация при осадке с кручением осуществляется при температуре окружающей среды и начальной температуре заготовки 20°С. Рекомендуемый диапазон температуры от 20 до 400°С. 4. В статье предложен алгоритм обработки результатов испытания на сжатие образцов алюминиевых сплавов, в частности, сплава АМг2, АМг3, АМг6. Представлены результаты обработки (рис. 8), которые можно применить для компьютерного имитационного моделирования процесса осадки с кручением.
Список литературы
Субич В.Н., Демин В.А., Шестаков Н.А., Власов А.В. Штамповка с кручением. Монография. М.: МГИУ, 2008. 389 с.
Хван А.Д. Упрочнение материалов реверсивным пластическим сдвигом // Известия Тульского государственного университета. Технические науки. 2019. № 5. С. 114.
Petrov P., Matveev A., Kulikov M., Stepanov B., Petrov M., Burlakov I. Uday Shanker Dixit. Finite-Element Modelling of Forging with Torsion: Investigation of Heat Effect // Procedia Manufacturing. 2020. № 47. P. 274.
Кривицкий Б.А. Исследование деформационного разогрева образца при испытаниях кручением // Кузнечно-штамповочное производство. Обработка материалов давлением. 2011. № 6. С. 36.
Сухоруков Р.Ю. Моделирование технологических процессов изготовления осесимметричных деталей газотурбинных двигателей из жаропрочных сплавов методом раскатки в сверхпластических условиях // Проблемы машиностроения и надежности машин. 2020. № 2. С. 80.
Алисин В.В., Рощин М.Н. Численный анализ тепловых потоков в процессе плавления покрытий лазером // Проблемы машиностроения и надежности машин. 2019. № 4. С. 93.
Pietrzyk M., Madej L., Rauch L., Szeliga D. Computational Materials Engineering. 1st Edition. Achieving High Accuracy and Efficiency in Metals Processing Simulations. Butterworth-Heinemann, 2015. 376 p. ISBN: 978-0-12-416707-0
Bodunrin M.O. Flow stress prediction using hyperbolic-sine Arrhenius constants optimised by simple generalised reduced gradient refinement // Journal of Materials Research and Technology. 2020. V. 9. Iss. 2. P. 2376.
Воронков В.И., Потапенко К.Е., Петров П.А., Выдумкина С.В. Получение уточненных данных по сопротивлению пластической деформации при горячей объемной штамповке алюминиевых сплавов АД35 и АД31 // Авиационные материалы и технологии. 2017. № 1 (46). С. 3.
Дополнительные материалы отсутствуют.
Инструменты
Проблемы машиностроения и надежности машин