Проблемы машиностроения и надежности машин, 2021, № 6, стр. 105-112
Влияние температуры сплавления частиц электроэрозионного кобальтохромового порошка на качество аддитивных изделий
Е. В. Агеев 1, *, А. Ю. Алтухов 1, Е. В. Агеева 1
1 Юго-Западный государственный университет
Курск, Россия
* E-mail: ageev_ev@mail.ru
Поступила в редакцию 07.04.2021
После доработки 02.08.2021
Принята к публикации 24.08.2021
Аннотация
В статье представлены результаты изучения влияния температуры сплавления порошка, полученного электроэрозионным диспергированием отходов кобальтохромового сплава в спирте, на пористость, микротвердость и шероховатость аддитивных изделий. Отмечено положительное влияние увеличения температуры сплавления на изменение перечисленных свойств изделий.
Аддитивные технологии (АТ) производства изделий из материалов на основе металлов и сплавов на сегодняшний день – одно из перспективных и активно развивающихся направлений машиностроения [1–6]. Точное получение формы – важнейшая, но далеко не единственная задача, которая решается при производстве деталей. Известно, что высокотемпературное воздействие на материал изделия, которым сопровождается любой из процессов аддитивной обработки, негативно сказывается на вышеперечисленных свойствах. Важнейшей задачей аддитивных технологий является обеспечение качественной структуры материала и высоких эксплуатационных свойств получаемой детали при многократном увеличении производительности [7–14].
Исходя из технологических особенностей применения для аддитивных машин порошковых частиц сферической формы с необходимой зернистостью, предлагается технология электроэрозионного диспергирования (ЭЭД), особенностью которой являются низкая энергоемкость и экологичность [15–17]. Основное преимущество технологии ЭЭД – возможность применения отходов производства, являющихся более дешевыми в сравнении с чистыми компонентами. Помимо этого, она позволяет получать частицы порошка из многокомпонетных сплавов.
Комбинирование металлопорошков, на основе сплава Co–Cr, обладающих различными качествами, соответствующими тем или иным условиям эксплуатации, открывает большие возможности для повышения технических и экономических характеристик изделий, полученных с помощью аддитивных технологий. Решения таких задач будет способствовать развитию разработок интеллектуальных производственных технологий, новых материалов и способов конструирования.
Широкое применение ЭЭД для переработки металлоотходов в порошки с необходимыми свойствами и использование их в АТ-технологиях сдерживает отсутствие в научно-технической литературе сведений о влиянии диспергируемого материала, режимов и условий получения на свойства порошка и возможных областей его практического применения. В связи с этим для оценки возможности использования порошков в АТ-технологиях необходимо провести комплексные экспериментальные исследования.
Задачи повышения свойств изделий решаются применением новых материалов. К таким материалам относятся, прежде всего, порошки-сплавы. При работе с ними необходимо детально изучить их характеристики, свойства и строение.
Основным недостатком порошковых изделий является наличие неравенства концентраций компонентов в различных точках порошкового тела, которое может быть только в исходном состоянии и на промежуточных этапах, либо сохраняться до конца изготовления. Применение таких материалов для изготовления широкой номенклатуры деталей для различных отраслей машиностроения ограничено из-за трудности обеспечения высоких и стабильных механических свойств материала. Для устранения указанных недостатков для аддитивных технологий предлагается использовать порошки-сплавы, полученные из отходов металлических сплавов электроэрозионным диспергированием.
Целью настоящей статьи является изучение влияния температуры сплавления порошка, полученного электроэрозионным диспергированием отходов кобальтохромового сплава в спирте, на пористость, микротвердость и шероховатость аддитивных изделий.
Материалы и методики исследований. Процесс электродиспергирования, т.е. измельчения сплава КХМС “Целлит” (Co – 63%, Cr – 27%, Mo – 5%, Ni – 2%, Fe – 2%) осуществляли на оригинальной установке, представленной на рис. 1.
В результате диспергирования отходов кобальтохромового сплава происходило его разрушение в результате локального воздействия кратковременным электрическим разрядом в рабочей жидкости, с образованием частиц порошка (рис. 2). В качестве рабочей жидкости использовался спирт бутиловый.
Рис. 2.
Растровое электронно-микроскопическое изображение электроэрозионных кобальтохромовых порошков.
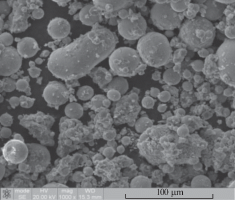
Сплавление электроэрозионных кобальтохромовых порошков осуществляли плазмой на оригинальной установке для послойного нанесения, позволяющей изменять технологические параметры процесса: скорость перемещения сопла (мм/мин), расстояние между соплом и зоной построения (мм) и температуру сплавления (°С) (рис. 3).
При постановке экспериментов по получению образцов аддитивных изделий из частиц кобальтохромового порошка за основной и изменяемый технологический параметр процесса лазерного спекания была принята температура сплавления частиц. Экспериментальные образцы аддитивных изделий получены при следующих температурах: № 1 – 1060°С; № 2 – 1100°С ; № 3 – 1140°С; № 4 – 1180°С.
Аттестация свойств аддитивных изделий, полученных из электроэрозионных кобальтохромовых порошков осуществлялась с использованием современных взаимодополняющих методов физического материаловедения.
Пористость определяли с помощью оптического инвертированного микроскопа Olympus GX51 с программным обеспечением для количественного анализа изображения. Подготовленные образцы не имели следов шлифования, полирования или выкрашивания структурных составляющих. Шлиф изготовляли по поперечному сечению (излому) целого изделия или его части, площадью менее 2 см2.
Программное обеспечение “SIAMS Photolab”, которым оснащен микроскоп, разработано с учетом специфики применения методов цифровой микроскопии и анализа изображений для металлографического анализа соединений.
Цифровое изображение материала в оттенках серого выглядит как набор объектов, обладающих близкими цветовыми, яркостными и морфометрическими признаками. Соответственно, автоматическое выделение измерительной информации связано с неизбежным захватом шумов и помех. Для того чтобы обеспечить достоверность результатов анализа, ПО обладает элементами экспертной системы: в интерактивном режиме оператору предлагается выбрать те из автоматически выделенных объектов, которые, по его мнению, представляют собой дефекты микроструктуры. Поскольку на контролируемой поверхности можно обнаружить как отдельные поры, так и цепочки пор, а также микротрещины, то оператор непрерывным маркером обозначает цепочки пор, а одиночные поры ползучести и микротрещины обозначает маркером как отдельные участки.
Испытания микротвердости образцов по поверхности и поперечному шлифу проводили с помощью автоматической системы анализа микротвердости DM-8 по методу микро-Виккерса при нагрузке на индентор 200 г по десяти отпечаткам со свободным выбором места укола. Время нагружения индентора составило 15 с.
Шероховатость поверхностного слоя изделий определяли на автоматизированном прецизионном контактном профилометре Surtronic 25.
Результаты и их обсуждение. Проведенные экспериментальные исследования позволили установить, что температура сплавления частиц практически не влияет на изменение элементного и фазового состава образцов аддитивных изделий из электроэрозионных кобальтохромовых порошков.
Результаты исследования пористости образцов металлографическим методом приведены в табл. 1.
Таблица 1.
Результаты исследования пористости образцов
Образец | Площадь анализа, мкм2 | Пористость, % | Dmin, мкм | Dmax, мкм | Dmed, мкм |
---|---|---|---|---|---|
№ 1 | 77217.8 | 1.31 | 0.7 | 10.7 | 0.9 |
№ 2 | 76369.6 | 1.25 | 0.1 | 8.6 | 0.3 |
№ 3 | 75310.1 | 0.78 | 0.1 | 5.2 | 0.3 |
№ 4 | 75965.0 | 0.29 | 0.1 | 5.0 | 0.3 |
На рис. 4 представлена микроструктура образцов и гистограмма распределения пор по размеру.
Рис. 4.
Микроструктура образцов: (а) – № 1; (в) – № 2; (д) – № 3; (ж) – № 4 и гистограмма распределения пор по размеру: (б) –№ 1; (г) – № 2; (е) – № 3; (з) – № 4.
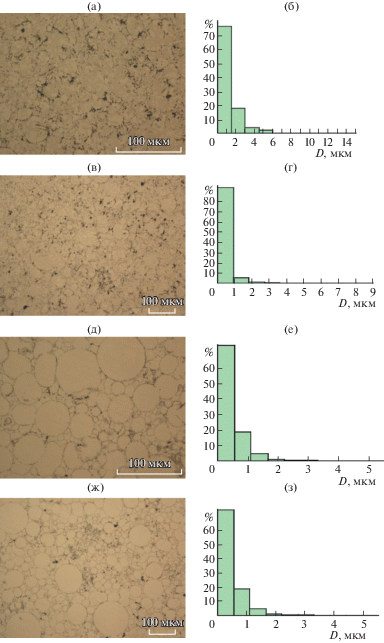
В результате исследования пористости образцов было установлено, что образец № 4, полученный при максимальной температуре сплавления, имеет наименьшую пористость равную 0.29%, а образец № 1, полученный при наименьшей температуре, имеет наибольшую пористость равную 1.31%. Образец № 4, полученный при максимальной температуре сплавления, имеет наименьший размер пор равный 5.0 мкм, а образец № 1, полученный при наименьшей температуре, имеет наибольший размер пор равный 10.7 мкм.
На основании проведенных экспериментальных исследований, показано, что повышение температуры сплавления электроэрозионных кобальтохромовых порошков приводит к снижению размера пор и их количеству.
Микроструктура аддитивных изделий, полученных из электроэрозионных кобальтохромовых порошков, имеет мелкозернистое строение без включений и несплошностей.
Результаты исследования микротвердости полученных образцов приведены в табл. 2.
Таблица 2.
Микротвердость по Виккерсу
Номер отпечатка | Температура сплавления, °С | |||
---|---|---|---|---|
1060 | 1100 | 1140 | 1180 | |
1 | 989 | 950 | 963 | 1417 |
2 | 889 | 976 | 963 | 1268 |
3 | 834 | 1140 | 1003 | 1174 |
4 | 845 | 976 | 1091 | 1091 |
5 | 834 | 1017 | 1394 | 925 |
6 | 794 | 824 | 1175 | 1018 |
7 | 804 | 878 | 1017 | 1076 |
8 | 794 | 655 | 1045 | 1210 |
9 | 765 | 658 | 1307 | 1046 |
10 | 774 | 765 | 1193 | 976 |
Среднее значение (единицы измерения) | 832 | 884 | 1115 | 1120 |
МПа | 8154 | 8663 | 10 927 | 10 976 |
Разброс значений микротвердости аддитивных изделий, полученных из электроэрозионных кобальтохромовых порошков, составляет от 7.94 ГПа до 13.94 ГПа. Образец № 4, полученный при максимальной температуре сплавления, имеет наибольшее среднее значение микротвердости равное 10976 МПа, а образец № 1, полученный при наименьшей температуре, имеет наименьшее среднее значение микротвердости равное 8154 МПа, что связано с их пористостью.
Результаты исследования шероховатости с указанием высоты (h) по ширине профиля (b) микронеровностей аддитивных образцов представлены на рис. 5.
Экспериментально по трем измерениям каждого из образцов установлено, что параметр шероховатости Ra образца № 4 составляет 0.73 мкм; образца № 3 – 1.25 мкм; образца № 2 – 1.52 мкм; образца № 4 – 2.14 мкм соответственно.
Заключение. На основании комплекса экспериментальных исследований, направленных на изучение влияния температуры сплавления частиц электроэрозионного кобальтохромового порошка на свойства аддитивных изделий установлено следующее: 1. Температура сплавления частиц практически не влияет на изменение элементного и фазового состава образцов. Из сопоставления микроструктур спеченных образцов видно, что основные структурные составляющие в целом схожи, что также подтверждает карта распределения элементов в образцах после спекания. Микроструктура аддитивных изделий, полученных из электроэрозионных кобальтохромовых порошков, имеет мелкозернистое строение без включений и несплошностей; 2. Температура сплавления частиц влияет на изменение пористости образцов аддитивных изделий. В результате исследования пористости образцов было установлено, что образцы, полученные при температуре сплавления 1160–1180°С, имеют наименьшую пористость (среднее значение 0.18%). При уменьшении температуры сплавления ниже 1160–1180°С происходит увеличение значения пористости, увеличение температуры приводит к потере размеров и формы образцов. С увеличением температуры сплавления электроэрозионных кобальтохромовых порошков, происходит снижение размера пор и их количество; 3. Температура сплавления частиц влияет на изменение микротвердости. Разброс значений микротвердости аддитивных изделий, полученных из электроэрозионных кобальтохромовых порошков одного состава, в зависимости от изменения температуры, составляет от 8.94 ГПа до 13.94 ГПа. Максимальные значения микротвердости образцов достигаются при температуре сплавления 1180 ± 10°C; 4. Температура сплавления частиц влияет на изменение шероховатости поверхностей аддитивных изделий. С увеличением температуры сплавления электроэрозионных кобальтохромовых порошков, происходит снижение высоты неровностей и шероховатости в целом.
Список литературы
Song B., Dong S., Zhang B. et al. Effects of processing parameters on microstructure and mechanical property of selective laser melted Ti6Al4V // Materials & Design. 2012. V. 35. P. 120.
Song B., Dong S., Coddet P. et al. Fabrication and microstructure characterization of selective laser melted FeAl intermetallic parts // Surface and Coatings Technology. 2012. V. 206. P. 4704.
Wang Z., Guana K., Gaoa M. The microstructure and mechanical properties of deposited-IN718 by selective laser melting // Journal of Alloys and Compounds. 2012. V. 513. P. 518.
Karlsson J., Snis A., Engqvist H., Lausmaa J. Characterization and comparison of materials produced by Electron Beam Melting (EBM) of two different Ti–6Al–4V powder fractions // Journal of Materials Processing Technology. 2013. V. 213 (12). P. 2109.
Safdar A., Wei L.Y., Snis A., Lai Z. Evaluation of microstructural developmentin electron beam melted Ti–6Al–4V // Materials Characterization. 2012. V. 65. P. 8.
Safdar A., He H.Z., Wei L.Y., Snis A. et al. Effect of process parameters settings and thickness on surface roughness of EBM produced Ti–6Al–4V // Rapid Prototyping Journal. 2012. V. 18 (5). P. 401.
Loeber L., Biamino S., Ackelid U. et al. Comparison of Selective Laser and Electron Beam Melted Titanium Aluminides // Conference paper of 22nd International symposium “Solid freeform fabrication proceedings”, University of Texas, Austin, 2011. P. 547.
Biamino S., Penna A., Ackelid U. et al. Electron beam melting of Ti–48Al–2Cr–2Nb alloy: microstructure and mechanical properties investigation // Intermetallics. 2011. V. 19. P. 776.
Gu D.D., Meiners W., Wissenbach K., Poprawe R. Laser additive manufacturing of metallic components: materials, processes and mechanisms // International Materials Reviews. 2012. V. 57 (3). P. 133.
Konovalov S., Gromov V., Panchenko I. Fatigue-induced evolution of AISi 310S steel microstructure after electron beam treatment // Materials. 2020. V. 13. № 20. P. 1.
Geng Y., Konovalo, S.V., Chen X. Research status and application of the high-entropy and traditional alloys fabricated via the laser cladding // Progress in Physics of Metals. 2020. V. 21. № 1. P. 26.
Nevskii S., Sarychev V., Konovalov S. et al. Wave instability on the interface coating/substrate material under heterogeneous plasma flows // Journal of Materials Research and Technology. 2020. № 1. P. 539.
Chen X., Liu K., Guo W. et al. The fabrication of NiTi shape memory alloy by selective laser melting: a review // Rapid Prototyping Journal. 2019. V. 25. № 8. P. 1421.
Konovalov S., Osintsev K., Golubeva A. et al. Surface modification of Ti-based alloy by selective laser melting of Ni-based superalloy powder // Journal of Materials Research and Technology. 2020. V. 9. № 4. P. 8796.
Ageev E. V., Ageeva E. V. Properties of the Coat-ings Fabricated by Plasma-Jet Hard-Facing by Dispersed Mechanical Engineering Wastes // Russian Metallurgy (Metally). 2018. V. 2018. № 6. P. 573.
Latypov R.A., Ageev E.V., Altukhov A.Y., Ageeva E.V. Manufacture of cobalt–chromium powders by the electric discharge dispersion of wastes and their investigation // Russian metallurgy (Metally). 2018. T. 2018. № 12. P. 1177.
Ageev E.V., Latypov R.A. Fabrication and investigation of carbide billets from powders prepared by electroerosive dispersion of tungsten-containing wastes // Russian Journal of Non-Ferrous Metals. 2014. T. 55. № 6. P. 577.
Дополнительные материалы отсутствуют.
Инструменты
Проблемы машиностроения и надежности машин