Проблемы машиностроения и надежности машин, 2021, № 6, стр. 43-51
Влияние прочности компонентов композиционных материалов на их физико-механические свойства
Ю. Е. Кисель 1, 2, И. Н. Кравченко 3, *, А. И. Купреенко 1, Ю. А. Кузнецов 4, М. Н. Ерофеев 3, С. А. Величко 5, О. В. Бармина 3
1 Брянский государственный аграрный университет
Брянск, Россия
2 Брянский государственный инженерно-технологический университет
Брянск, Россия
3 Институт машиноведения им. А.А. Благонравова РАН
Москва, Россия
4 Орловский государственный аграрный университет им. Н.В. Парахина
Орел, Россия
5 Национальный исследовательский Мордовский государственный университет им. Н.П. Огарёва
Саранск, Россия
* E-mail: kravchenko-in71@yandex.ru
Поступила в редакцию 17.02.2021
После доработки 01.08.2021
Принята к публикации 24.08.2021
Аннотация
Предложены теоретические зависимости для определения оптимального объемного содержания наполнителя в износостойких дисперсно-упрочненных композитах, с точки зрения соотношения прочностных свойств их компонентов. Показано, что прочность и износостойкость композита определяется природой его компонентов, структурными параметрами, а также прочностью межфазных связей.
Нанесение электролитического железа, сплавов и композитов на его основе является перспективным методом восстановления и упрочнения деталей машин [1]. Оно позволяет автоматизировать техпроцесс, получать покрытия с заданными свойствами без термического воздействия на деталь, получать поверхность в пределах допуска на размер и шероховатость. Введение в “чистое” электролитическое железо твердых дисперсных частиц (оксидов, боридов, карбидов) позволяет получить на поверхности деталей композит, обладающий в десятки раз повышенной прочностью и износостойкостью в сравнении с высоколегированными сталями и покрытиями, полученными другими способами [2–6].
В соответствии с классической теорией прочности, “лепестковой” теорией изнашивания Н.П. Су, термофлуктационной теорией С.Н. Журкова и В.Р. Регеля, адгезионной Е. Арчарда и Е. Хорнбогена, энергетической Г. Флейшера и Г. Грегера трение и изнашивание электрохимических композитов обусловлено сочетанием свойств материалов основы (матрицы) и частиц наполнителя (дисперсной фазы), их поверхностной энергией, структурными особенностями и внешними условиями [7–10].
Высокую износостойкость композитов связывают с тем, что твердые частицы дисперсной фазы, выступая в процессе изнашивания из матрицы покрытия, становятся площадками контакта, которые при трении наиболее интенсивно нагружаются. В случае приложения распределенной по поверхности контакта нагрузки, напряжения в приповерхностном слое матрицы композита существенно ниже, чем в приповерхностном слое твердых включений. Под нагрузкой одинаково деформируется как матрица, так и включения. Вместе с тем, поскольку модуль упругости матрицы значительно ниже, чем модуль упругости твердых включений, напряжения в поверхностном слое матрицы оказываются существенно меньшими [11].
Недостаточная изученность связей физико-механических свойств и структуры покрытий, формируемой электролизом, ограничивает практическое применение гальванических композитов.
Для устранения этих недостатков проведены исследования, цель которых заключается в изучении и сопоставлении структурных и прочностных свойств компонентов композита для определения их влияния на износостойкость материала.
Материалы и методы исследования. В качестве объекта исследования выступали образцы с износостойкими электрохимическими композиционными покрытиями на основе железа и его сплавов.
Для изучения влияния прочностных свойств матрицы на износостойкость композиционного материала были выбраны железоникелевые (как менее прочные) и железокобальтовые (как более прочные) покрытия, механические свойства которых изучены ранее [12, 13]. Для исследования влияния состава и прочности наполнителя на свойства композитов выбраны микропорошки электрокорунда белого промышленного изготовления (марок М14, М20).
Износостойкие композиционные покрытия наносили на образцы из стали 35 толщиной 0.5 ± 0.1 мм. Композиты на основе железоникелевого сплава получали из электролита следующего состава, кг/м3: FeCl2·4H2O – 550–600; NiSO4·7H2O – 80–90; Na2H4C4O6·2H2O –1–1.5; при плотности тока 35–40 А/дм2, рН = 0.7–1.0, температуре 313–318 К. Железокобальтовые композиты наносили из электролита следующего состава, кг/м3: FeCl2·4H2O – 550–600; CoSO4·7H2O – 90–100; Al2(SO4)3·18 H2O – 80; при плотности тока 30–35 А/дм2, рН = 0.7–1.0, температуре 313–318 К.
Электролит-суспензию готовили введением в электролиты микропорошков электрокорунда белого марок М14 и М20 (ГОСТ 3647-80). Содержание порошков изменяли в пределах 25–150 кг/м3.
При нанесении композиционных покрытий использовали специальную ванну (рис. 1). Конструкция ванны с выпуклым дном и перегородкой, отделяющей пропеллерную мешалку от зоны расположения электродов, позволяла создавать восходящий поток с равномерным распределением частиц во всем объеме электролита. Раствор подогревали и стабилизировали по температуре с точностью ±5°С при помощи термостата. Кислотность контролировали ионометром ЭВ-74.
Рис. 1.
Ванна с выпуклым дном и перфорированной перегородкой для нанесения покрытий: 1 – анод; 2 – катод; 3 – термометр; 4 – мешалка; 5 – расходомер Вентури; 6 – контактный нагреватель.
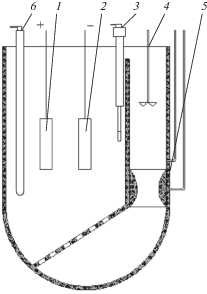
Электролиты готовили из реактивов квалификации “ХЧ” и “ЧДА”, которые корректировали по концентрации компонентов и рН добавлением соответствующих кислот и солей. Состав электролитов поддерживали в пределах ±1 кг/м3 и контролировали с помощью количественного химического анализа по стандартным методикам. Анодное декапирование проводили в электролите: H2SO4 – 300–350 кг/м3; FeCl2·4H2O – 20–22 кг/м3.
Исследования абразивной износостойкости проводили по схеме резиновый ролик-колодка в соответствии с ГОСТ 23.208-79. При этом условия работы трущейся пары следующие: Р = 44 Н, n = 60 мин–1. Взвешивание образцов проводили на аналитических весах ВЛР-200М с точностью до 5.0 × 10–8 кг.
Исследование микроструктуры покрытий проводили с помощью микроскопов МИМ-8, МБС-9. Объемное содержание частиц наполнителя в композиционном материале определяли стереометрическим анализом методом случайных секущих в комбинации с линейным методом [14, 15].
Опытные данные обрабатывали методами математической статистики. Для построения функциональных зависимостей использовали регрессионный анализ [16, 17].
Результаты исследований и их обсуждение. На этапе теоретических исследований определяли оптимальный состав композита в зависимости от размеров частиц наполнителя, их прочности и условий взаимосвязи между составляющими композита.
Рассматривая взаимосвязь структуры, прочности и износостойкости композита будем основываться на соотношениях дискретной и континуальной теорий дислокаций, уравнениях связи нормальных и тангенциальных напряжений и условиях прочности частиц дисперсного наполнителя на разрыв и отрыв [7].
Причинами разрушения композиционного материала будем считать: 1) нарушения адгезии между фазами по поверхности их раздела (по мере деформации пустоты растут и в момент, предшествующий разрушению, соединяются друг с другом); 2) растрескивание самих частиц, так как прочность и характер разрушения частиц зависят от их размера (с уменьшением размеров частиц их прочность растет и в идеале может достичь прочности материала на сдвиг).
Принимаем, что прочность частиц σр зависит от их размера в соответствии с соотношением Гриффитса–Орована [9]
где γр – удельная энергия разрушения частицы; Gр – модуль сдвига частицы; d – диаметр частиц; μр – коэффициент Пуассона включений.Для определения прочности материала матрицы σт воспользуемся тем же соотношением, заменив размер частиц расстоянием между ними
где γт – удельная энергия разрушения матрицы; Gт – модуль сдвига матрицы; λ – расстояние между частицами; μт – коэффициент Пуассона матрицы.Частицы наполнителя более прочные, чем матрица композита, задерживают его разрушениею, препятствуя распространению трещин. Рассмотрим явление в рамках дискретной и континуальной теорий, учитывая воздействие на препятствие как одностороннего, так и двухстороннего скопления дислокаций.
Среднее сдвиговое напряжение τ при одностороннем скоплении дислокаций [9]
где G, μ – соответственно модуль сдвига и коэффициент Пуассона материала; b – вектор Бюргерса; d – размер зерна материала.Для двустороннего скопления дислокаций [9]
Наибольший размер неразрушающихся частиц можно установить из равенства теоретической прочности частиц на разрыв и прочности по Гриффитсу–Оровану, зависящей от размеров
где αр – коэффициент, зависящий от типа укладки частиц наполнителя в композите; τр – сдвиговое напряжение в частицах наполнителя.Подставляя в формулу (3) выражение (5) с учетом того, что при хрупком разрушении частиц теоретическое значение энергии разрушения выражается соотношением
где Gр, bр – соответственно модуль сдвига и вектор Бюргерса; Ср – постоянная, зависящая от свойств материала наполнителя, получим соотношение для наибольшей прочности частицСогласно дискретной теории для роста трещины в пределах одного зерна (dрд) и для континуальной теории при эллиптической ($d_{{р{\text{к}}}}^{{\text{э}}}$) и цилиндрической ($d_{{р{\text{к}}}}^{{\text{ц}}}$) формах трещин
(8)
${{d}_{р}}_{{\text{д}}} = ({\text{2/}}\alpha _{p}^{2}){{b}_{р}}{{С}_{р}}{\text{/}}(1--{{\mu }_{р}});$(9)
$d_{{р{\text{к}}}}^{{\text{э}}} = ({\text{4/}}\alpha _{p}^{2}){{b}_{р}}{{С}_{р}}{\text{/}}(1--{{\mu }_{р}});$(10)
$d_{{р{\text{д}}}}^{{\text{ц}}} = ({\text{8/}}\pi \alpha _{p}^{2}){{b}_{р}}{{С}_{р}}{\text{/}}(1--{{\mu }_{р}}).$Минимальное расстояние между частицами, отвечающее наивысшей прочности определяется из условия теоретической прочности на сдвиг композиции в соответствии с уравнением (4)
(11)
$\tau _{p}^{2} = {\text{1/}}(1--{{\mu }_{р}})({{G}_{т}}{{b}_{т}}{{G}_{р}}){\text{/}}(\pi \lambda {{С}_{р}}).$Подставляя значения величин для дискретной теории, получим критическое расстояние между частицами (λд)
(12)
${{\lambda }_{{\text{д}}}} = {\text{1/}}(1--\mu )({{G}_{т}}{{b}_{т}}{{С}_{р}}){\text{/}}(\pi {{G}_{р}}).$С помощью преобразования γ = Gтbт/Ст и Ст ≈ Ср – для матрицы выражение (12) примет вид
(13)
${{\lambda }_{{\text{д}}}} = {\text{1/}}(1--\mu )({{\gamma }_{т}}{\text{/}}{{\gamma }_{р}}){{b}_{р}}{{С}_{т}}{\text{/}}\pi .$Для континуальной теории прочности выражение для распределения критического расстояния между частицами (λк)
(14)
${{\lambda }_{{\text{к}}}} = {\text{1/}}(1--\mu )({{\gamma }_{т}}{\text{/}}{{\gamma }_{р}}){{b}_{р}}{{С}_{р}}.$Коэффициент концентрации напряжений в ДФ (Kр) можно определить по соотношению
(15)
${{{\mathbf{K}}}_{p}} = {{\sigma }_{р}}{\text{/}}{{\sigma }_{{\text{к}}}} = \beta \lambda {\text{/}}d.$В идеальном случае наивысшая прочность композита может быть равна теоретической прочности частиц. Поэтому будет справедливо соотношение
Тогда коэффициент концентрации напряжений в дисперсных частицах при выражении λ через объемное содержание наполнителя в композите V будет
(16)
${{K}_{р}} = (\lambda {\text{/}}{{d}_{{\text{э}}}})({{d}_{{\text{к}}}}{\text{/}}{{\lambda }_{{\text{к}}}}) = ({{d}_{{\text{к}}}}{\text{/}}{{\lambda }_{{\text{к}}}})(\sqrt {\pi {\text{/3}}V} - \sqrt {{\text{2/3}}} ).$С учетом выражения (1) определим Kр композита через физические параметры компонентов фаз и объемного содержания наполнителя в композите:
– для дискретной теории
(17)
${{K}_{р}}_{{\text{д}}} = (2\pi {\text{/}}{{a}^{2}})({{\gamma }_{р}}{\text{/}}{{\gamma }_{т}})(\sqrt {\pi {\text{/3}}V} - \sqrt {{\text{2/3}}} );$– для континуальной теории (при прохождении через композит эллиптических трещин или петель дислокаций)
(18)
$K_{{р{\text{к}}}}^{{\text{э}}} = (2\pi {\text{/}}{{\alpha }^{2}})({{\gamma }_{р}}{\text{/}}{{\gamma }_{т}})(\sqrt {\pi {\text{/3}}V} - \sqrt {{\text{2/3}}} ),$(19)
$K_{{р{\text{к}}}}^{{\text{ц}}} = ({\text{8/}}{{\alpha }^{2}})({{\gamma }_{р}}{\text{/}}{{\gamma }_{т}}){\text{ }}(\sqrt {\pi {\text{/3}}V} - \sqrt {{\text{2/3}}} ).$Коэффициент концентрации напряжений в матрице композиции (Kт) можно рассчитать, используя известное правило смесей
Выполним расчет содержания наполнителя в композите, отвечающего наивысшей прочности композиционного материала при его разрушении, когда трещина проходит через связующие и дисперсные частицы. Условием такого разрушения будет отношение
(21)
${{\sigma }_{р}}{\text{/}}{{\sigma }_{{\text{к}}}} = {{K}_{р}} = \beta {{\lambda }_{{\text{к}}}}{\text{/}}{{d}_{{\text{к}}}}\quad {\text{или}}\quad \sigma _{p}^{2}{\text{/}}\sigma _{{\text{к}}}^{2} = K_{p}^{2} = {{(\beta {{\lambda }_{{\text{к}}}}{\text{/}}{{d}_{{\text{к}}}})}^{2}}.$Так как расчет необходимо выполнить для всех случаев разрушения, рассмотрим его принципы на одном из вариантов, например, при применении к изучению прочности композита дискретной теории дислокаций и прохождения трещин внутри одного зерна.
Соотношение σр/σк для такого случая будет равно
(22)
$\frac{{\frac{{2{{\gamma }_{р}}{{G}_{р}}}}{{(1 - \mu ){{d}_{к}}}}}}{{\alpha _{p}^{2}\frac{{{{G}_{m}}{{b}_{m}}{{G}_{р}}}}{{\pi (1 - \mu )\lambda {{C}_{р}}}}}} = \frac{{2\pi }}{{\alpha _{р}^{2}}}\frac{\lambda }{{{{d}_{р}}}}\frac{{{{\gamma }_{р}}}}{{{{\gamma }_{m}}}}.$Из соотношения (21) следует
(23)
$\sigma _{p}^{2}{\text{/}}\sigma _{{\text{к}}}^{2} = 4{{\lambda }_{{\text{к}}}}{\text{/}}{{(\pi {{d}_{{\text{к}}}})}^{2}} = \frac{{2\pi }}{{\alpha _{р}^{2}}}\frac{\lambda }{{{{d}_{р}}}}\frac{{{{\gamma }_{р}}}}{{{{\gamma }_{m}}}}.$Выражение (22) позволяет определить отношение λ/d для искомого случая в виде
(24)
$\frac{\lambda }{{{{d}_{р}}}} = \frac{{{{\pi }^{3}}}}{{8\alpha _{р}^{2}}}\frac{{{{\gamma }_{р}}}}{{{{\gamma }_{m}}}}.$Учитывая зависимость объемного содержания от соотношения λ/d
можно получить выражение, связывающее объемное содержание с прочностными свойствами компонентов композита(26)
$\frac{\lambda }{{{{d}_{р}}}} = \frac{{{{\pi }^{3}}}}{{8\alpha _{р}^{2}}}\frac{{{{\gamma }_{р}}}}{{{{\gamma }_{m}}}} = \sqrt {\frac{\pi }{{3V}}} - \sqrt {\frac{2}{3}} .$Из выражения (25) получим объемное содержание наполнителя, отвечающее наивысшей прочности композита в рамках дискретной теории
(27)
$V = \frac{\pi }{3}\frac{1}{{{{{\left( {\frac{{{{\pi }^{3}}}}{{8\alpha _{р}^{2}}}\frac{{{{\gamma }_{р}}}}{{{{\gamma }_{m}}}} + \sqrt {\frac{2}{3}} } \right)}}^{2}}}}.$Аналогичным образом получим соотношения при прохождении трещин через поликристаллы в рамках континуальной теории
(28)
$V = \frac{\pi }{3}\frac{1}{{{{{\left( {\frac{{{{\pi }^{3}}}}{{\alpha _{р}^{2}}}\frac{{{{\gamma }_{р}}}}{{{{\gamma }_{m}}}} + \sqrt {\frac{2}{3}} } \right)}}^{2}}}},$(29)
$V = \frac{\pi }{3}\frac{1}{{{{{\left( {\frac{1}{{\alpha _{р}^{2}}}\frac{{{{\gamma }_{р}}}}{{{{\gamma }_{m}}}} + \sqrt {\frac{2}{3}} } \right)}}^{2}}}},$(30)
$V = \frac{\pi }{3}\frac{1}{{{{{\left( {\frac{8}{{\alpha _{р}^{2}}}\frac{{{{\gamma }_{р}}}}{{{{\gamma }_{m}}}} + \sqrt {\frac{2}{3}} } \right)}}^{2}}}}.$Соотношения (28)–(30) предполагают наличие идеальной связи между частицами наполнителя и матрицей, которая может находиться в пределах 0 ≤ σр–m ≤ σр. Ее действительное значение можно изменять, варьируя величиной γр/γm (для электролитического железа $\gamma _{m}^{{{\text{(Fe)}}}}$ = 2000 эрг/см2; меди $\gamma _{m}^{{{\text{(Cu)}}}}$ = 1200 эрг/см2; никеля $\gamma _{m}^{{{\text{(Ni)}}}}$ = 1700 эрг/см2; электрокорунда γр = 3600 эрг/см2) [2, 4].
Результаты проверки полученных соотношений на примере композита железо-электрокорунд, никель-электрокорунд и медь-электрокорунд показали [18–24], что наиболее близки к действительным результаты расчета, основанные на континуальной теории, когда трещины моделируются как двухсторонние скопления дислокаций эллиптической формы. Соответственно объемное содержание, отвечающее наивысшей прочности покрытий по (28), в зависимости от прочностных свойств матрицы с включением электрокорунда, показано на рис. 2.
Рис. 2.
Влияние прочности матрицы и прочности связи дисперсных частиц и матрицы на оптимальное объемное содержание наполнителя (электрокорунд белый) в электрохимических композитах на основе: 1 – меди; 2 – никеля; 3 – железа; 4 – по выражению (28).
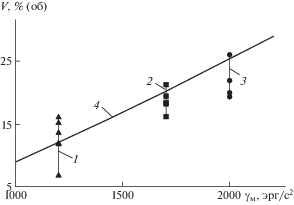
Следует заметить, что результаты теоретических и экспериментальных исследований достаточно хорошо согласуются (рис. 2). Таким образом, подтверждается возможность повышения износостойкости композитов с ростом прочности матрицы при введении в железо кобальта, никеля и других элементов.
Электроосаждаемые сплавы и композиты имеют более совершенную структуру (рис. 3), высокие упругопластические свойства, износостойкость, прочность сцепления с основой и меньшие внутренние напряжения в сравнении с “чистым” электролитическим железом [12, 18, 19, 21, 24].
Рис. 3.
Структура композита железо-никель электрокорунд белый (×400): (а) – без наполнителя; (б) – М10; (в) – М20.
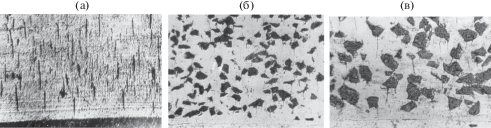
Исследования абразивной износостойкости композитов на основе железа и его сплавов (железо-никель, железо-кобальт) показали, что их абразивный износ в значительной мере зависит от размеров и объемного содержания дисперсных частиц в материале (рис. 4).
Рис. 4.
Влияние размера (d) и содержания (V) наполнителя на износ композитов железо-никель (1) и железо-кобальт (2) электрокорунд белый.
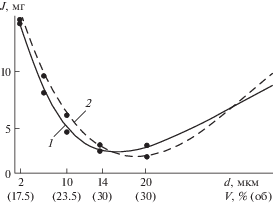
Износ композита с ростом содержания наполнителя в покрытии уменьшался и проходил через минимум при содержании микропорошков 18–24% (об.). Необходимо отметить, что наибольшая износостойкость композитов на основе железокобальтовых покрытий оказалась выше при несколько большем объемном содержании наполнителя: V ≈ 22–24% (об.), чем у композитов на железоникелевой основе V ≈ 18–20% (об.).
Заключение. Теоретическим анализом структурно-прочностных свойств композиционных покрытий показано, что прочность гетерофазного материала определяется природой его компонентов, структурными параметрами, а также прочностью межфазных связей. Предложены расчетные формулы для определения оптимального объемного содержания наполнителя в износостойких композитах.
Список литературы
Гурьянов Г.В., Кисель Ю.Е. Износостойкие электрохимические сплавы и композиты на основе железа. Брянск, 2015. 98 с.
Вишняков Л.Р., Грудина Т.В., Кадыров В.Х. и др. Композиционные материалы: Справочник // Под общ. ред. Д.М. Карпиноса. Киев: Наукова думка, 1985. 592 с.
Антропов Л.И., Лебединский Ю.Н. Композиционные электрохимические покрытия и материалы. Киев: Техника, 1986. 95 с.
Бородин И.Н. Порошковая гальванотехника. М.: Машиностроение, 1990. 240 с.
Целуйкин В.Н. Трибологические свойства композиционных электрохимических покрытий на основе никеля // Трение и износ. 2010. Т. 31. № 5. С. 475.
Кисель Ю.Е., Горьков А.С. Оптимизация износостойкости композитов по их установившейся шероховатости // Вестник Брянского государственного технического университета. 2011. № 4 (32). С. 26.
Айнбиндер С.Б. Параметры шероховатости контртела, определяющие износостойкость полиэтилена // Трение и износ. 1981. Т. 2. № 1. С. 12.
Рыбакова Л.М., Куксенова Л.И. Структура и износостойкость металла. М.: Машиностроение, 1982. 212 с.
Мартин Д.У. Микромеханизмы дисперсионного твердения сплавов // Пер. с англ. М.Ю. Матвеева. М.: Металлургия, 1983. 168 с.
Крагельский И.В., Михин Н.М. Узлы трения машин: Справочник. М.: Машиностроение, 1984. 280 с.
Kisel Y.E., Serpik I.N., Markaryants L.M., Bezik V.A., Guryanov G.V., Bezik D.A. Calculation of the elastic Characteristics of Composite Materials with Dispersed Inclusions // International Journal of Applied Engineering Research. 2015. T. 10. № 24. C. 44018.
Кисель Ю.Е., Гурьянов Г.В. Структура и некоторые прочностные свойства электролитических сплавов железа // Упрочняющие технологии и покрытия. 2009. № 7. С. 25.
Кисель Ю.Е. Повышение долговечности деталей сельскохозяйственной техники электротермической обработкой композиционных электрохимических покрытий: Дис. … д-ра техн. наук. Брянск, 2014. 249 с.
Салтыков С.А. Стереометрическая металлография. М.: Металлургия, 1976. 270 с.
Домбровский Ю.М. Стереология. М.: Ростов н/Д: Дон. гос. техн. ун-т, 2002. 101 с.
Гмурман В.Е. Теория вероятностей и математическая статистика. М.: Высшая школа, 2003. 479 с.
Юдин М.И. Планирование эксперимента и обработка его результатов. Краснодар: КГАУ, 2004. 239 с.
Сафонов В.В., Шишурин С.А., Сёмочкин В.С. Наномодифицированные химические покрытия с улучшенными физико-механическими свойствами // Инновации в АПК: Проблемы и перспективы. 2014. № 3. С. 18.
Серебровский В.В., Серебровский В.И., Сафронов Р.И., Гнездилова Ю.П., Калуцкий Е.С. Электроосаждение железоборидных покрытий // Электрика. 2015. № 11. С. 33.
Стекольникова Н.Ю., Стекольников Ю.А., Максимов Д.И., Астанин В.К. Восстановление изношенных изделий сельскохозяйственной техники гальваническим хромированием // Вестник Тамбов. гос. техн. ун-та. 2016. Т. 22. № 4. С. 679.
Kisel J.E., Guryanov G.V. Wear Resistance of Composite Coatings Based on Iron Alloys // IOP Conf. Ser.: Mater. Sci. Eng. 2018. 450 032047.
Degtyar L.A., Zhukova I.Y., Mishurov V.I. Experience and perspectives of electrodeposition from electrolytes-colloids of nickel plating // Materials Science Forum. 2019. T. 945. C. 682.
Дегтярь Л.А., Иванина И.С., Жукова И.Ю. Особенности формирования композитных электрохимических покрытий на основе никеля и наноструктурного диборида циркония // Вестник Донского государственного технического университета. 2019. Т. 19. № 1. С. 31.
Belous N.M., Kisel Yu.E., Guryanov G.V., Markaryants L.M. Enhancement of wear resistance of mulcher teeth with the help of electrochemical coats // E3S Web of Conferences 193, 01019 (2020) ICMTMTE 2020.
Дополнительные материалы отсутствуют.
Инструменты
Проблемы машиностроения и надежности машин