Проблемы машиностроения и надежности машин, 2021, № 6, стр. 21-32
Повышение надежности штамповки поковок из расплава управлением технологическим режимом
Е. Н. Сосенушкин 1, *, Е. А. Яновская 1, Т. А. Кинжаев 2
1 Московский государственный технологический университет “СТАНКИН”
Москва, Россия
2 ЗАО “Эс Энд Эй”
Москва, Россия
* E-mail: sen@stankin.ru
Поступила в редакцию 01.04.2021
После доработки 07.06.2021
Принята к публикации 24.08.2021
Аннотация
Надежность жидкой штамповки и качество поковок во многом определяется условиями кристаллизации, зависящими от изменения во времени теплового баланса в системе “жидкий металл–двухфазная зона–твердая фаза–инструмент”. Обсуждается математическая модель процесса затвердевания расплава в двухфазной зоне при формообразовании поковки жидкой штамповкой из сплава АК7. Из совместного решения уравнений теплопроводности Фурье для расплава, двухфазной зоны и твердой корки устанавливается кинетика затвердевания, от которой зависит формирование структуры. Оценено влияние внешнего давления на температурные поля и составляющие времени затвердевания полых тонкостенных поковок.
Обработка давлением кристаллизующегося металла, представляющая собой комбинацию технологий литья под давлением и горячей объемной штамповки в закрытых штампах, при реализации которой можно обойтись без операции разрезки сортового проката на мерные заготовки и без предварительного формообразования сложных по геометрии поковок. Увеличивается коэффициент использования металла (КИМ) до значений 0.95 за счет снижения припусков на дальнейшую механическую обработку и отсутствия литниковых систем; силовые параметры снижаются в 3–5 раз при реализации технологии. Качество поковок определяется технологическими параметрами процесса жидкой штамповки, к которым относятся сила деформирования, температурные интервалы заливки расплавленного металла в полость штампа, температура элементов штампа, а также время заполнения полости штампа и кристаллизации [1], величина которого имеет особое значение при штамповке тонкостенных поковок [2]. Влияние на структуру металла поковки оказывают условия кристаллизации, в частности, интенсивность теплового стока от расплава к инструменту и далее в окружающую среду [3–6], а также величина внешнего давления. В виду сложности кристаллизации металла под высоким давлением и последующей доштамповки, прогнозирование временных и температурных параметров является актуальной задачей математического моделирования [7–10].
Целью статьи является создание математической модели затвердевания поковки в интервале температур для управления технологическими параметрами жидкой штамповки полых тонкостенных изделий.
Моделирование процессов теплообмена при затвердевании. Представляется логичным построение математической модели теплопередачи на границе контактирующих тел, используя уравнение теплопроводности Фурье [11], в сочетании с граничными условиями, однозначно характеризующими теплообмен. В начальный момент времени температура распределяется в теле равномерно, т.е. при t = 0, T = T0. Размеры поковки и штампа известны из их чертежей, а физические свойства соприкасающихся тел определяются из справочных таблиц. В качестве граничного условия будем использовать равенство тепловых потоков на поверхности соприкосновения жидкой фазы кристаллизующегося сплава с материалом штампа [12]
Схема процесса затвердевания металла полой поковки в двухфазной зоне представлена на рис. 1, где ТL – температура ликвидуса; ТE – температура условного фронта кристаллизации; ТS – температура солидуса; Т41(–x, t) = Т42(x, t) = Т4(t) – температура пуансона и матрицы штампа; R41, R42 – радиусы пуансона и матрицы; s = R42 – R41 – толщина стенки поковки; ξ(t) – толщина твердой корки; k1(t), k3(t) – координаты фронтов начала и конца кристаллизации; k2(t) – координата условного фронта кристаллизации.
Структурно технология жидкой штамповки выглядит следующим образом: 1) плавка металла в электропечи при температуре рабочего пространства Т, К; 2) дозирование расплава по объему Vr, (м3) и заливка в штамп при температуре Тz, (К) за время tz (с); 3) временной этап t1 (с) отвода теплоты перегрева T1, (К); 4) временной этап t2 (с) отвода скрытой теплоты кристаллизации при затвердевании поковки в интервале температур ликвидуса и солидуса [TL, TS] при температуре кристаллизации Т2, (К) под действием внешнего давления p, (МПа); 5) этап охлаждения поковки в полости штампа с одновременной доштамповкой и последующее выталкивание из матрицы.
Воспользуемся уравнением теплопроводности, которое для расплава при температуре перегрева T1 имеет вид
Для двухфазной зоны использовано уравнение теплопроводности в общем виде c учетом внутренних тепловых источников, равномерно распределенных по объему [12]
В соответствии с допущением, что функция ψ(T), характеризует количество твердой фазы в двухфазной зоне при скорости приращения твердой фазы $\frac{{\partial \psi }}{{\partial t}}$ = $\frac{{\partial \psi }}{{\partial T}} \cdot \frac{{\partial T}}{{\partial t}}$ = = $\mu \frac{{\partial T}}{{\partial t}}$, ($\mu = \frac{{\partial \psi }}{{\partial T}}$ – темп кристаллизации сплава внутри интервала температур [TL, TS]), конкретизировав значение функции $\psi = \sqrt {xt} $, найдем частную производную по времени $\frac{{\partial \psi }}{{\partial t}}$ = $\frac{1}{2}\frac{{\sqrt x }}{{\sqrt t }}$. В простейшем случае учета доли твердой фазы при кристаллизации используют соотношение $\psi \left( {{{T}_{2}}} \right)$ = $\frac{{{{T}_{L}} - {{T}_{2}}}}{{{{T}_{L}} - {{T}_{S}}}}$.
Уравнение теплопроводности для твердой корки
Учтем равенство тепловых потоков на фронте кристаллизации
По аналогии в конце процесса на границе фронта кристаллизации
Условия однозначности на границах
Учет физических процессов в двухфазной зоне. Выберем внутри интервала кристаллизации сплава температуру ${{T}_{E}}$ = $\frac{1}{2}\left( {{{T}_{L}} - {{T}_{S}}} \right)$, при которой кристаллизация проходит полностью, а кинетика затвердевания определяется скоростью приращения твердой корки $U(t) = \frac{{\partial \xi }}{{\partial t}}$. Поэтому справедливо дифференциальное уравнение затвердевания Стефана при замене координаты k3(t) на k2(t). Тогда дифференциальное уравнение затвердевания запишется [12]
Условия равенства тепловых потоков
Влияние многослойного зазора между контактирующими телами. Для ослабления интенсивности теплообмена между расплавом и штампом на поверхность последнего наносят слой технологической смазки, из которой при контакте с расплавом жидкая фаза испаряется, а входящие в ее состав компоненты частично выгорают, образуя воздушно-газовую прослойку. Твердые компоненты, например, графит, оседают на поверхности инструмента. В результате зазор между поковкой и штампом заполняют слои из названных компонент что создает термическое сопротивление (м2 К)/Вт, оцениваемое как
где xgap – толщина зазора, м; λgap – эффективный коэффициент теплопроводности вещества, заполняющего зазор, Вт/(м К).Обратная величина термического сопротивления названа коэффициентом теплопередачи через зазор. В многослойном зазоре этот коэффициент равен
Небольшая интенсивность теплообмена расплава со штампом и штампа с окружающей средой дает возможность пренебречь неравномерностью тепловых полей в сечениях поковки и штампа. Постоянство термического сопротивления зазора и температурного напора для расплава в подвижном и неподвижном состоянии означает, что величина теплового потока из расплава в штамп через зазор остается неизменной в обоих случаях. Течение металла при заливке вызывает потерю части теплоты расплавом, которая прогревает штамп.
Временные параметры процесса затвердевания. Уравнение теплового баланса в системе “расплав–штамп” с учетом передачи разного количества тепла при контакте пуансона и матрицы за время dt
Изменение теплосодержания расплава за это же время
где $V = {{V}_{{42}}} - {{V}_{{41}}}$ – объем поковки, м3.Уравнение теплового баланса запишется
Решая относительно времени dt, после интегрирования и исключения постоянной интегрирования С (при граничных условиях t = 0 $\ln \,|{\kern 1pt} \left( {{{T}_{1}} - {{T}_{{41}}}} \right)d{{s}_{{41}}}$ + $\left( {{{T}_{1}} - {{T}_{{42}}}} \right)d{{s}_{{42}}}{\kern 1pt} |$ = 0, поэтому С = 0) получим
(1)
$t = - \frac{1}{\beta }\frac{{{{c}_{1}}{{\gamma }_{1}}\left( {d{{V}_{{42}}} - d{{V}_{{41}}}} \right)}}{{\left( {d{{s}_{{41}}} + d{{s}_{{42}}}} \right)}}\ln \left| {\left( {{{T}_{1}} - {{T}_{{41}}}} \right)d{{s}_{{41}}} + \left( {{{T}_{1}} - {{T}_{{42}}}} \right)d{{s}_{{42}}}} \right|.$Влияние внешнего давления на температурные поля зависит от его величины и времени действия на затвердевающий металл в период его кристаллизации. Практика показывает, что уменьшение пористости происходит в гораздо большей степени, чем это происходило бы согласно закону Бойля–Мариотта. Дело в том, что кроме спрессовывающего действия давления на газовую пористость оно также увеличивает растворимость газов в жидком металле. Авторами работы [13] доказано, что при штамповке поковок из жидкого алюминия давление, порядка 200 МПа полностью устраняет газовую пористость поковок при максимальной плотности сплава γ = 2740 кг/м3 и повышенными твердостью HB 120 и пределом прочности σВ = 400 МПа. Это явление объясняется с точки зрения термодинамики процесса, т.к. в равновесной двухфазной системе температура связана с давлением известным законом Клапейрона–Клаузиуса $\frac{{d{{T}_{{cr}}}}}{{dp}}$ = $\frac{{\Delta V{{T}_{{cr}}}}}{L}$, из которого определяют изменение температуры кристаллизации расплава как функцию, зависящую от внешнего давления p = 100–250 МПа
где V3 – объем затвердевшей поковки, м3.Температура, при которой расплав заливается в полость штампа, зависит от температурного интервала затвердевания и чем он шире, тем ниже может быть температура заливки расплава. Этому условию отвечает зависимость, предложенная А.И. Вейником
где ${{b}_{i}} = \sqrt {{{\lambda }_{i}}{{c}_{i}}{{\gamma }_{i}}} $ – коэффициент тепловой аккумуляции (i = 1.4): для штампа индекс i = 4.Относительная температура заливки
Теперь можно определить время заливки порции расплава в штамп
Важным параметром является время отвода теплоты перегрева, для расчета которого используем зависимость (1), зная величины объемов и площадей контакта деталей штампа. Уравнение упрощается при подстановке вместо функции ln, первых членов сходящегося ряда
(2)
${{t}_{1}} = \frac{{{{R}_{{pr}}}\xi (T){{c}_{1}}{{\gamma }_{1}}}}{{{{\lambda }_{1}}}}\frac{{{{T}_{{oh}}}}}{{\Delta T}},$Температура поверхности штампа при контакте с расплавом определяется
а при образовании твердой корки толщиной ξ(t) температура контакта ее со штампом найдем по аналогииВремя отвода скрытой теплоты кристаллизации в интервале температур можно определить, воспользовавшись рекомендациями автора работы [12]
(3)
${{t}_{2}} = {{\left[ {\frac{{{{R}_{{pr}}}{{\gamma }_{2}}{{l}_{{ef}}}\psi \left( {{{T}_{2}}} \right)}}{{1.13{{b}_{4}}\left( {{{T}_{L}} - {{T}_{4}}} \right)}} + \sqrt {{{t}_{1}}} } \right]}^{2}},$Объем затвердевшего металла за время t2
Таким образом, длительность выдержки под давлением при затвердевании поковки определяется суммой компонент (2) и (3) $t = {{t}_{1}} + {{t}_{2}}$.
Достоверность математической модели затвердевания расплава в двухфазной зоне проверена при следующих исходных данных.
Геометрические параметры поковки. Диаметр фланца – 200 мм; диаметр донного выступа – 120 мм; высота поковки – 65 мм; радиус закругления донной части – 35 мм; штамповочные уклоны: внешний 5°, внутренний 7°; толщина фланца – 3 мм; толщина дна – 8 мм.
При жидкой штамповке полых осесимметричных поковок высота подъема расплава в канале штампа зависит от температуры заливки, температуры штампа, скорости перемещения ползуна и геометрии канала. Связав систему координат с пуансоном, при условии неразрывности струи расплава авторами [2] обосновано соотношение скоростей
где ${{v}_{k}}$, ${{v}_{{41}}}$ – соответственно скорость течения расплава в канале штампа и скорость перемещения пуансона; R41, R42 – радиусы пуансона и матрицы.Найдем высоту подъема расплава в канале штампа до затвердевания
Теплофизические характеристики штампуемого сплава в жидком и твердом состоянии; вещества, заполняющего зазор между расплавом пуансона и матрицы, а также материала инструмента взяты из технической литературы [13, 14]. Взаимосвязь внешнего давления с температурными факторами в процессе кристаллизации алюминиевого сплава АК7 с учетом физических процессов в двухфазной зоне при штамповке полой поковки представлена в виде графиков на рис. 2, где 1 – TL температура ликвидуса; 2 – TZ температура заливки; 3 – Tcr температура кристаллизации; 4 – Tk(cr) температура контакта расплава со штампом; 5 – TS температура солидуса; 6 – Tk(hard) температура контакта штампа с твердой коркой. С увеличением давления на расплав и температура заливки повышается не только температура кристаллизации, но и температуры контакта штампа с расплавом и твердой коркой в процессе затвердевания, не выходя за пределы температурного интервала [TL, TS].
При одинаковой начальной температуре штампа 473 К температура контакта поверхности штампа с расплавом мало отличается от температуры кристаллизации – линии графика практически совпадают, при этом возникает температурный напор 389 К. При давлении 100 МПа температура кристаллизации не переходит линию солидуса данного сплава, а температура перегрева колеблется в небольших пределах – 3.01 К. При повышении давления до 240 МПа температура заливки выравнивается с температурой ликвидуса сплава, а температура кристаллизации продолжает находиться в средней части интервала температур [TL, TS]. Таким образом, под влиянием внешнего давления сплав кристаллизуется раньше при температурах выше температуры солидуса. Данная особенность подтверждается практикой литейного производства, где стремятся снижать температуру перегрева во избежание горячих трещин [12]. С увеличением давления, приложенного к расплаву, или при уменьшении его температуры в нем будет достигнуто большее переохлаждение относительно новой температуры кристаллизации и тем более мелкозернистая структура образуется при затвердевании.
В результате кристаллизации поверхностных слоев металла с образованием твердой корки температурный напор на поверхности контакта снижается в среднем на 23 К. В диапазоне прикладываемого давления средний перегрев расплава составляет 37 К, а время отвода теплоты перегрева требуется небольшое, средняя величина которого составляет от 1.11 до 1.60 с. Продолжительность отвода температуры перегрева зависит от температуры поверхности контакта со штампом, а сама температура перегрева влияет на долю твердой фазы в двухфазной зоне затвердевания. В соответствии с линейным законом изменения доли твердой фазы от температуры, характер этого изменения показан на рис. 3, где Toh – температура перегрева расплава; Ψ(T) – доля твердой фазы в двухфазной зоне. Если уменьшать температуру перегрева возрастает доля твердой фазы в двухфазной зоне затвердевания, что не противоречит физике процесса.
Рис. 3.
Влияние температуры перегрева расплава на долю твердой фазы при затвердевании в интервале температур.
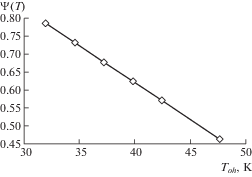
Графики на рис. 4, где 1 – TZ температура заливки; 2 – Tcr температура кристаллизации; 3 – Tk(cr) температура контакта расплава со штампом; 4 – Tk(hard) температура контакта штампа с твердой коркой, показывают, что управление температурой предварительного нагрева штампа позволяет изменять температурные параметры затвердевающего расплава.
После заливки расплава и начала процесса деформирования часть тепла переходит в штамп, расплав переохлаждается и его температура падает до значения температуры кристаллизации. Поэтому, как показывает график, температура на контактной поверхности ненамного отличается от температуры кристаллизации. Поскольку материал поковки постоянно контактирует с поверхностью штампа, часть металла кристаллизуется с образованием твердой корки толщиной ξ(t), условия теплообмена изменяются, и температура на контактной поверхности снижается.
Следует обеспечить условия заполнения полости штампа расплавом до его полного затвердевания, что оказывает влияние на качество поковки. Управлять процессом заполнения штампа удается регулированием скорости перемещения ползуна гидравлического пресса.
Кривые на рис. 5, где 1 – Tz = 973 K; 2 – Tz = 1003 K; 3 – Tz = 1033 K; 4 – Tz = 1063 K, показывают, что управляя температурой заливки расплава в штамп и скоростью перемещения ползуна пресса можно добиться непрерывного течения расплава в канале штампа с его выдавливанием на необходимую высоту, равную высоте стенки тонкостенной полой поковки до момента полного затвердевания. В примере использована поковка с высотой стенки 50 мм, расплав на высоту такой величины поднимется до затвердевания при температуре заливки 973 К и скорости перемещения инструмента 1 мм/с. В соответствии с рис. 5 при снижении скорости перемещения ползуна и одновременном увеличении температуры заливки расплава в штамп, или, наоборот, увеличивая рабочую скорость пресса с более длительным выстоем ползуна в конце рабочего хода без сброса давления, интенсивность охлаждения при плотном контакте обеспечивает необходимые условия полной кристаллизации металла и удаления поковки из штампа без дефектов.
Рис. 5.
Зависимость высоты стенки поковки при заполнении штампа от скорости перемещения ползуна и температуры заливки.
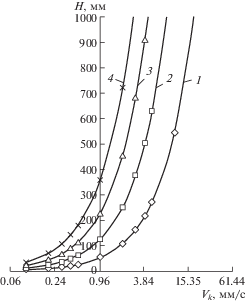
Экспериментальные исследования были проведены для проверки адекватности математической модели и выбора предпочтительных технологических параметров изготовления тонкостенных осесимметричных поковок способом штамповки кристаллизующегося под давлением металла. Штамповка производилась с помощью гидравлического пресса модели ДБ2432А номинальной силой 1600 кН. Плавка алюминия осуществлялась в электрической тигельной печи ПП50, с максимальной температурой нагрева 1373 К. Плавление 10 кг шихты заняло 1 час 30 мин. В качестве смазочного материала применялся коллоидно-графитовый водный раствор ПСВ ТУ 113-08-5015184-76-91, разработанный ОАО “Воскресенские минеральные удобрения”. Смазка наносилась на формообразующие поверхности пуансона и матрицы с помощью кисти непосредственно перед каждой заливкой жидкого металла. Заливка расплавленного металла в матрицу осуществлялась вручную мерным ковшом, подогретым до температуры 400–450 К. Матрица и пуансон были предварительно разогреты с помощью двух трубчатых электронагревателей до температуры, равной 470 К. После заливки жидкого металла в штамп пуансон внедряется в объем жидкого металла, который заполняет образующиеся при смыкании штампа каналы. Выдержка металла под давлением до полной кристаллизации осуществлялась в течение 98 секунд.
Исследование структуры металла полученных поковок. Из одной поковки опытно-промышленной партии, полученной в ходе экспериментальной штамповки, были вырезаны образцы для дальнейшего исследования структуры и механических свойств металла.
В результате макроанализа не было обнаружено структурных дефектов. По сравнению с классическими методами литья практически отсутствовали макроскопическая пористость, усадочная раковина и трещины в металле поковки.
Микроанализ проводится с целью исследования микроструктуры и фазового состава сплава, а также оценки размеров, формы и особенностей распределения различных фаз. Сплав АК7 является доэвтектическим, поэтому в его структуре преобладают зерна α-раствора кремния в алюминии, а по границам этих зерен сосредоточено небольшое количество эвтектики, представляющей собой зерна кремния, окруженные α-фазой. Различный размер зерна α-фазы на различных участках и в различных зонах одного участка связан с различием скоростей охлаждения у матрицы, у пуансона, в глубине металла, а также в донной части поковки, как показано на рис. 6, где 1 – область фланца; 2 – переходная область из стенки в донную часть; 3 – донная часть вблизи оси симметрии. Давление также существенно влияет на условия кристаллизации, сдвигая термодинамическое равновесие и измельчая зерно α-фазы путем уменьшения времени отвода тепла от застывающей поковки.
Рис. 6.
Темплет поковки, полученной жидкой штамповкой с микроструктурой характерных участков, снятой при увеличении ×500.
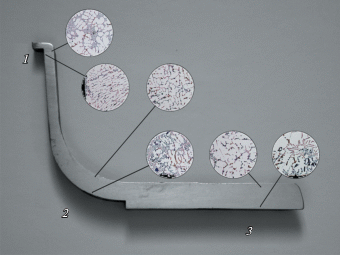
Крупной пористости, которую можно было бы оценить в соответствии с ГОСТ 1583-93, не обнаружено. Это является несомненным достоинством штамповки кристаллизующегося металла по сравнению с традиционными методами формообразования литьем, т.к. улучшает физико-механические свойства полученного металла. Обнаружена микропористость со средним диаметром пор 10 мкм, которая приблизительно одинакова как в различных участках поковки, так и по ее сечению.
Выводы. 1. Специфические условия затвердевания сплавов в интервале температур с образованием двухфазной зоны описаны математической моделью затвердевания применительно к технологии штамповки кристаллизующегося под давлением металла. С помощью разработанной модели проведен анализ технологических параметров процесса жидкой штамповки полой тонкостенной поковки из литейного сплава АК7. Рассчитаны температурные и временные параметры технологического процесса кристаллизующегося под давлением алюминиевого сплава, управление которыми позволяет влиять на процесс затвердевания и формообразования структуры полых тонкостенных поковок. 2. Проведенное экспериментальное исследование подтвердило возможность изготовления полых осесимметричных поковок с тонкими стенками необходимой высоты способом штамповки кристаллизующегося под давлением металла. 3. Управление теоретически обоснованными технологическими параметрами процесса жидкой штамповки позволяет обеспечить повышенное качество и равномерность структуры поковок, изготовленных из сплава АК7. При штамповке других поковок, близких по форме и размерам к исследуемой, технологические параметры можно рекомендовать в качестве отправной точки, которые при необходимости уточняются в зависимости от конкретных размеров, конфигурации и марки материала.
Список литературы
Yong P., Shuncheng W., Kaihong Z., Wenjun Q., Hexing C., Haitao Z. Influence of the pressing time during the liquid stamping of the deformable aluminum alloy 6061 on its mechanical // Tezhong zhuzao ji youse hejin= Spec. Cast. And Nonferrous Alloys. 2013. V. 33. № 12. P. 1152.
Кирдеев Ю.П., Белоусов И.Я., Ракогон А.И. Изготовление деталей с высокими тонкими стенками штамповкой кристаллизующегося алюминия // Кузнечно-штамповочное производство. 2002. № 3. С. 9.
Zhong G., Wu Y., Zou C., Qiu C. et al. Microstructure and properties of high strength and toughness AlSiMgMn alloys fabricated by squeeze casting // Tezhong zhuzao ji youse hejin= Spec/ Cast. And Nonferrous Alloys. 2017. V. 37. № 12. P. 1277.
Liu J., Yin Y., Duan C., Xu M. et al. Squeezing casting scroll hlate of automotive air conditioning compressor // Tezhong zhuzao ji youse hejin= Spec/ Cast. And Nonferrous Alloys. 2017. V. 37. № 9. P. 979.
Белоусов И.Я., Сапрыкин А.А., Сивак Б.А. Особенности процесса жидкой штамповки заготовок поршней двигателей внутреннего сгорания // Сб. трудов конференции “Неделя металлов в Москве”. М.: ОАО АХК “ВНИИМЕТМАШ” им. академика А.И. Целикова. 2008. С. 423.
Портной М.Р., Кузин В.В. Влияние асимметричного теплового потока на неоднородность напряжений в поверхности элементов структуры оксидной керамики при глухой заделке сферического зерна // Вестник МГТУ “Станкин”. 2016. № 2 (37). С. 21.
Cao L., Sun F., Chen T., Teng Z. et al. Numerical simulation of liquid-solid conversion affecting flow behavior during casting filling process // Jinshu xuebao=Acta met.sin. 2017. 53. № 11. P. 1521.
Попов В.Н., Юшканов А.А., Рудный Д.А. Математическое моделирование процессов переноса тепла в плоском канале при малых градиентах давления // Вестник МГТУ. “Станкин”. 2012. № 1 (24). С. 98.
Дмитриенко Г.С., Уварова Л.А. Моделирование теплопереноса в области с фрактальной границей // Вестник МГТУ. “Станкин”. 2012. № 1 (19). С. 50.
Гришин Л.Г., Солодухо О.Д., Иоффе Г.А., Сапрыкин А.А. Температурные условия процесса и стойкость штампов при жидкой штамповке стальных заготовок // Кузнечно-штамповочное производство. 1996. № 2. С. 4.
Сосенушкин Е.Н. Штамповка кристаллизующегося металла // Вестник МГТУ. “Станкин”. 2010. № 2. С. 12.
Баландин Г.Ф. Теория формирования отливки: Основы тепловой теории. Затвердевание и охлаждение отливки. М.: Изд-во МГТУ им. Н.Э. Баумана, 1998. 360 с.
Крушенко Г.Г. Получение деталей транспортного средства жидкой штамповкой из сплава АК7 // Вестник СибГАУ. 2016. Т. 17. № 1. С. 194.
Бабичев А.П., Бабушкина Н.А., Братковский А.М. и др. Физические величины: Справочник / Под ред. И.С. Григорьева, Е.З. Мейлихова. М.: Энергоатомиздат, 1991. 1232 с.
Араманович И.Г., Левин В.И. Уравнения математической физики. М.: Наука, 1964. 288 с.
Дополнительные материалы отсутствуют.
Инструменты
Проблемы машиностроения и надежности машин