Проблемы машиностроения и надежности машин, 2022, № 2, стр. 103-112
Обзор методов контроля температур фазовых превращений в сплавах с ЭПФ и напряжений термомеханического возврата
И. С. Сплавский *
Институт машиноведения им. А.А. Благонравова РАН
Москва, Россия
* E-mail: spl-igor@yandex.ru
Поступила в редакцию 07.08.2021
После доработки 11.11.2021
Принята к публикации 20.12.2021
- EDN: IAXDXQ
- DOI: 10.31857/S0235711922020146
Аннотация
В статье рассмотрены особенности характеристик сплавов обладающих эффектами памяти формы и сверхупругостью. Представлены принципы проведения контроля термомеханических характеристик материала заготовок перед их непосредственным применением. В статье показаны методы, позволяющие определять температуры фазовых превращений сплавов обладающих эффектом памяти формы на основе TiNi. Проанализированы достоинства и недостатки методов в зависимости от их трудоемкости и достоверности результатов.
Эффект памяти формы (ЭПФ), обнаруженный в интерметаллических соединениях является одним из самых необычных и интересных свойств материала. Из всех известных сплавов с ЭПФ, наибольший интерес для практического применения представляет соединения на основе TiNi, обладающие высокой пластичностью в широком интервале температур, в том числе и криогенных и удовлетворительной обрабатываемостью [1, 2].
Бинарное соединение существует в относительно узком интервале растворимости компонентов Ni и Ti, которое колеблется в пределах от трех до пяти атомарных процентов. При этом температура фазовых превращений, в зависимости от соотношения компонентов, может находиться в широких пределах от +120 до –200°С [3].
Явление ЭПФ связано с термоупругими мартенситными превращениями, происходящими в сплаве. Характер превращений этого типа, в отличие от традиционного термодинамического подхода в конструкционных материалах связан с тем, что обратное мартенситное превращение Ан–Ак обусловлено упругой энергией, накопленной в результате предшествующего прямого Мн–Мк мартенситного превращения [4].
Хотя внешне с микроскопической точки зрения, каких-либо изменений твердого состояния материала при фазовых превращениях не наблюдается, кристаллическая структура претерпевает существенные изменения. Эти превращения сопровождаются значительными изменениями физико-механических свойств материала. При нагреве предварительно деформированного, в пределах мартенситной неупругости, материала накопленная упругая энергия действует в том же направлении, что и химическая движущая сила обратного мартенситного превращения.
Компенсирование затрат энергии нехимического происхождения осуществляется за счет переохлаждения (Мн–Мк) и перегрева (Ан–Ак) материала [5]. Разницу “нехимических Gнх свободных энергий двух фаз по отношению к скрытой теплоте превращения Q можно определить из соотношения
(1)
${{\left[ {0.5\left( {{{{\text{M}}}_{{\text{Н}}}} + {{{\text{А}}}_{{\text{К}}}}} \right) - 0.5\left( {{{{\text{М}}}_{{\text{К}}}} + {{{\text{А}}}_{{\text{Н}}}}} \right)} \right]} \mathord{\left/ {\vphantom {{\left[ {0.5\left( {{{{\text{M}}}_{{\text{Н}}}} + {{{\text{А}}}_{{\text{К}}}}} \right) - 0.5\left( {{{{\text{М}}}_{{\text{К}}}} + {{{\text{А}}}_{{\text{Н}}}}} \right)} \right]} {0.5\left( {{{{\text{M}}}_{{\text{Н}}}} + {{{\text{А}}}_{{\text{К}}}}} \right) \approx \Delta {{{{G}_{{НХ}}}} \mathord{\left/ {\vphantom {{{{G}_{{НХ}}}} {\Delta \sigma }}} \right. \kern-0em} {\Delta \sigma }}}}} \right. \kern-0em} {0.5\left( {{{{\text{M}}}_{{\text{Н}}}} + {{{\text{А}}}_{{\text{К}}}}} \right) \approx \Delta {{{{G}_{{НХ}}}} \mathord{\left/ {\vphantom {{{{G}_{{НХ}}}} {\Delta \sigma }}} \right. \kern-0em} {\Delta \sigma }}}}.$Исходя из соотношения (1), скрытая теплота превращения, составит
(2)
$\Delta Q \approx {{\Delta {{G}_{{НХ}}}\left( {{{{\text{M}}}_{{\text{Н}}}} + {{{\text{А}}}_{{\text{К}}}}} \right)} \mathord{\left/ {\vphantom {{\Delta {{G}_{{НХ}}}\left( {{{{\text{M}}}_{{\text{Н}}}} + {{{\text{А}}}_{{\text{К}}}}} \right)} {\left( {{{{\text{М}}}_{{\text{Н}}}} - {{{\text{М}}}_{{\text{К}}}} + {{{\text{А}}}_{{\text{К}}}} - {{{\text{А}}}_{{\text{Н}}}}} \right)}}} \right. \kern-0em} {\left( {{{{\text{М}}}_{{\text{Н}}}} - {{{\text{М}}}_{{\text{К}}}} + {{{\text{А}}}_{{\text{К}}}} - {{{\text{А}}}_{{\text{Н}}}}} \right)}}.$При проектировании конструкций из материалов с ЭПФ для назначения условий их эксплуатации, контроль температур МП, объем реализуемой памяти εR и генерируемые напряжения термомеханического возврата σR являются основополагающими [6].
В реальных конструкциях, использование свойств ЭПФ может осуществляться как в технологических (ниже температур эксплуатации), так и конструктивных целях, внутри температур эксплуатации.
Рассмотрим существующие методы, позволяющие определять температуры фазовых превращений сплавов обладающих ЭПФ на основе TiNi. Проанализируем достоинства и недостатки методов в зависимости от их трудоемкости и достоверности результатов.
Химический анализ. Стандартный метод по контролю химсостава, применяемый в промышленности для конструкционных материалов позволяет устанавливать концентрацию компонентов сплавов с точностью, не превышающей 0.15%. Прогнозирование температур фазовых превращений, исходя из контроля соотношения компонентов для данных сплавов, не предоставляется возможным, т.к. отклонение от заданного состава, по результатам рентгеноструктурного анализа, на 0.1% изменяет параметры МП ~ на 15°С. Точность определения химического состава компонентов для таких сплавов значительно ниже. Кроме того, сплавы одинакового состава по содержанию компонентов, из-за наличия вторичных фаз (Ti2Ni или TiNi3) в различных участках полуфабрикатов могут существенно изменить в матрице количественный характер их соотношений [7–10].
Методы определения температур МП, происходящих в процессе превращения, подразделяются на прямые (рентгеноструктурный, нейтронография и т.п.) и косвенные, основанные на изменении физико-механических свойств.
Рентгеноструктурный метод. В основном используется для исследовательских целей, широко применяется для определения взаимного расположения атомов в сплаве, определения фазового состава и искажений кристаллической решетки в процессе превращений, величин зерна и т.д. Анализ требует применения специализированного оборудования и подготовленных для этих целей соответствующих образцов. Результаты исследований последовательности фазовых переходов в зависимости от температуры и условий испытаний позволяют с большой точностью определять характеристические точки фазовых превращений кристаллической структуры для испытуемых образцов. Свойства для применяемой партии материала устанавливаются в сравнении с характеристиками образцов [11].
Косвенные методы основаны на исследованиях свойств материала по изменениям дифракций рентгеновских лучей при различных температурах. Установлено, что в диапазоне температур МП наблюдаются аномальные изменения электрического сопротивления, электрохимического потенциала, удельной теплоемкости, модуля упругости, внутреннего трения, твердости и т.д. Косвенные характеристики позволяют с достаточной достоверностью и экономической целесообразностью устанавливать свойства контролируемого материала.
Измерение твердости вследствие быстроты и простоты испытаний, а также возможности без разрушения материала судить о его свойствах, получило широкое применение для контроля качества металла.
При измерении твердости определяется сопротивление пластической деформации слоев металла, близких к поверхности. В металл вдавливается специальный наконечник, который преодолевает сопротивление материала упругим, а затем пластическим деформациям.
Испытание на твердость всегда выполняется одним из первых при изучении свойств нового материала. Результаты исследований зависимости микротвердости H от соотношения компонентов в сравнении с модулем нормальной упругости Е для биметаллического соединения TiNi представлены на рис. 1.
Рис. 1.
Микротвердость (1 и 2) и модуль нормальной упругости (3) в зависимости от химического состава.
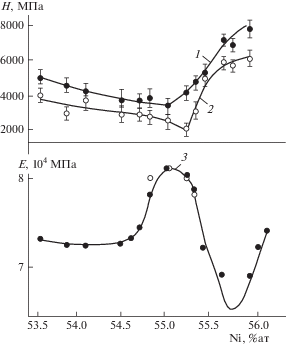
Замерами твердости для конкретной партии материала устанавливаются зависимости влияния от термической и термомеханической обработки на свойства материала. Для металлов со специфическими свойствами, в которых механические и термомеханические характеристики зависят от напряженного состояния в очаге деформации, связь между твердостью и физическими свойствами недостаточно надежна. Существующий в процессе замера значительный разброс показаний микротвердости определяется наличием в матрице интерметаллических (типа Ti2Ni) соединений и зон пластичности превращения.
При фазовых превращениях для определения характеристических точек МП целесообразно применять следующие физические методы.
Акустический способ. Метод основан на температурной зависимости внутреннего трения и модуля Юнга (собственной частоты колебаний) в зависимости от того в каком состоянии находится материал. Внутреннее трение, как и чрезвычайно высокая способность гасить шумы связаны, с теми же физическими явлениями, что и ЭПФ. Внутреннее трение в аустенитной фазе вызвано дефектами решетки. Высокие значения внутреннего трения в мартенситной фазе вызвано движением двойниковых границ, а максимум, наблюдаемый в переходной области температур, обусловлен механизмом МП [12].
Схематически температурная зависимость интенсивности затухания от акустических колебаний представлена на рис. 2.
Рис. 2.
Температурная зависимость интенсивности затухания от акустических колебаний: В2 – аустенитное состояние; В19 – мартенситное состояние.
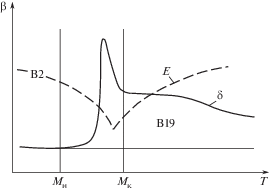
При ударе по полуфабрикату (пруток, лист и т.п.) или детали, находящейся в подвешенном состоянии, возникает звук. Глухой (как по дереву) быстро затухающий звук соответствует мартенситному состоянию, а звонкий – аустенитному.
Сложность установки, обеспечивающей изменение температуры с замером коэффициента затухания контролируемого образца по всему сечению экономически нецелесообразна для промышленного применения.
Метод применим для сравнительного экспресс анализа установления в каком состоянии находится материал (аустенитном – В2 фазе или мартенситном – В19 фазе) по отношению к окружающей температуре (например – комнатной) [13].
Калориметрический метод. Калориметрия дает простой и достаточно точный способ измерения температур превращения. Метод основан на исследовании путем обнаружения и определения величины тепловых эффектов при фазовых превращениях и скрытой теплоты превращения.
Схема установки для калориметрического (термического) анализа представлена на рис. 3, а на рис. 4 характер калориметрической кривой, иллюстрирующей выделение тепла при МП [14].
Рис. 3.
Схема установки для дифференциального термического анализа: 1 – испытуемый образец; 2 – эталонный образец; 3, 4 – термопары; 5 – термокамера; 6 – двухкоординатник.
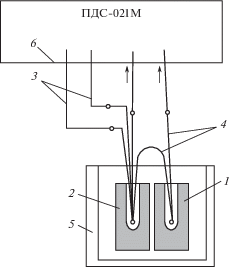
Для фиксирования превращений, протекающих с аномальными тепловыми эффектами, применяется дифференциальный термический анализ. Контроль сводится к выявлению интервалов температур, при которых имеет место аномальное поглощение или выделение тепла.
Эталонный образец, с надежно закрепленной в нем термопарой, изготавливается из той же марки материала, что и испытуемые заготовки, но с такой температурой МП которая заведомо ниже, чем температура испытаний. Термопара подключается к клеммам прибора одной координаты и фиксирует изменение температур образцов в термокамере.
В испытуемый образец или заготовку устанавливается термопара, которая дифференциально подключается к клеммам прибора другой координаты и фиксирует разницу термо-ЭДС при аномальных тепловых эффектах.
Метод позволяет не только проводить измерения температур МП в различных видах полуфабрикатов, но и осуществлять селективный отбор заготовок с необходимым для данной конструкции интервалом температур.
Дилатометрический анализ. Метод основан на свойстве изменения длины образца при нагреве или охлаждении, которые фиксируются датчиками перемещения. В отличие от термического расширения, характеризующегося плавным ходом изменения размеров, при фазовых превращениях происходит их резкое увеличение или уменьшение. Для повышения точности измерений, применяется дифференциальный метод дилатометрического анализа. Метод применим для определения характеристик материала по температурам МП, а при необходимости и сортировки заготовок из которых изготавливаются детали.
Электрический метод. Превращения в сплавах связанные с образование новых фаз или изменением количественных отношений между ними приводит к аномальному поведению электросопротивления ρ. Этот метод применим главным образом для определения критических точек и регистрации изменений свойств материала при фазовых превращениях.
Измерение температурной зависимости электросопротивления проводится потенциометрическим методом. На рис. 5 представлена схема установки по проведению таких измерений.
Рис. 5.
Схема установки электрического метода: 1 – термокамера; 2 – образец; 3 – стабилизатор тока; 4 – источник питания; 5 – амперметр; 6 – компенсатор напряжения.
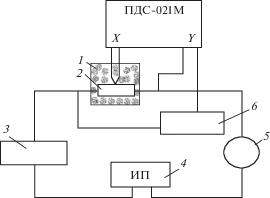
Электрический ток от универсального источника питания напряжением 3–6 В подается на испытуемый образец. Стабилизация тока через образец осуществляется баретором. Для повышения чувствительности измерений используется дифференциальный метод, при котором компенсация постоянной составляющей падения напряжения на образце осуществляется подачей напряжения противоположного знака.
Температурная зависимость электросопротивления записывается на потенциометре ПДС–021М. Допустимая погрешность в измерениях не превышает 1% и определяется в основном ошибкой измерений размеров образцов. Измерения удельного электросопротивления осуществляются на образцах с малым постоянным сечением длиной 15–25 мм (проволока, листы, ленты и т.п.) в широком интервале температур от ‒196 до +500°С.
По резким перегибам на кривой “электросопротивление–температура” отмечаются температуры, соответствующие превращениям.
Характеристическая температурная зависимость электросопротивления для образца в зависимости от режимов термообработки, представлена на рис. 6.
Рис. 6.
Температурная зависимость электросопротивления: 1 – закалка с температурой Т = 800°С; 2 – закалка с температурой Т = 800°С + отжиг 250°С, 0.5 часа; 3 – закалка с температурой Т = 800°С + отжиг 250°С, 1.5 часа; 4 – закалка с температурой Т = 800°С + отжиг 250°С, 5 часов.
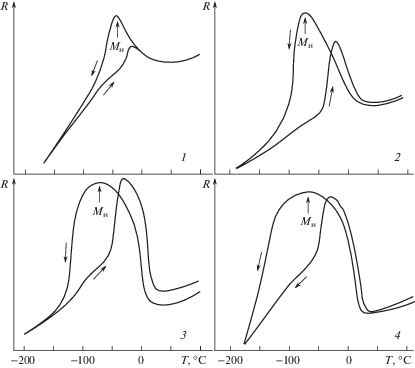
Ультразвуковой метод. В основе метода принят принцип оценки коэффициента затухания, как меры рассеяния и поглощения ультразвуковой энергии в материале при его термоциклировании в интервалах фазовых превращений. Аномальные свойства коэффициента затухания обусловлены изменениями упругих модулей кристаллической решетки, происходящие при охлаждении или нагреве сплава в процессе фазовых превращений [15].
Оценка коэффициента затухания в динамическом режиме осуществляется по изменению уровня (напряжения) 1-го видеоимпульса из серии отраженного от противоположной грани образца эха-импульса.
На рис. 7 представлена диаграмма записи амплитуды 1-го донного эха-импульса при контроле заготовки в процессе фазового перехода по схеме В2 ↔ R ↔ В19 (где В2 – аустенитная фаза, В19 – мартенситная фаза, R – ромбоэдрическая фаза, ↔ – фазовые превращения).
Введение ультразвуковых колебаний в образец с частотой f = 3–5 МГц осуществляется контактным способом. Для обеспечения стабильного контакта между образцом и кварцевым пьезоэлектрическим преобразователем применяется смазка на основе кремнийорганического масла и графитового порошка. Скорость охлаждения и нагрева заготовки должна находиться в пределах ~8 град/мин. Структурная схема ультразвуковой установки с перечнем необходимого для контроля оборудования и конструкция рабочей камеры представлены работе [16].
Этот метод позволяет фиксировать не только температурные точки при прямом (Мн–Мк) и обратном (Ан–Ак) фазовых переходах, но и выявлять неупругое поведение материала при R-переходах. В зависимости от свойств и исходного состояния сплава при охлаждении могут реализовываться от одного до трех фазовых переходов, при которых могут образовываться два независимых продукта превращения. Необходимо отметить, что термоупругие мартенситные превращения В2 ↔ R при охлаждении и нагреве характеризуются отсутствием или очень малой величиной гистерезиса, а превращения В2 ↔ В19 и R ↔ В19 сопровождаются значительным гистерезисом в 20–60°С.
Сплавы на основе TiNi обладают высокими звукопоглощающими свойствами. С целью повышения чувствительности при измерениях затухания по одному из отраженных импульсов к геометрии контролируемых образцов предъявляются следующие требования: 1) образцы должны иметь строго цилиндрическую форму; 2) торцевые поверхности должны быть плоскими и строго параллельными; 3) поверхности торцевых поверхностей должны быть перпендикулярны к оси цилиндра.
Исходя из характеристик применения деталей для конкретных температур эксплуатации ультразвуковой метод позволяет применять те партии материалов, которые отвечают техническим требованиям изделия. Например, для авиационной промышленности нижний порог температур эксплуатации трубопроводов составляет –60°С. Соответственно, температуры мартенситных превращений должны быть ниже –60°С, что требует применения криогенной жидкости при технологической переработке заготовок. Для судостроения, где температуры эксплуатации трубопроводов выше 0°С, нижний порог мартенситных превращений может находиться в пределах –20°С.
Метод применим для 100% контроля (разбраковки) полуфабрикатов диаметром 12–40 мм и длиной 10–100 мм в интервале температур от –196 до +100°С, с автоматической записью результатов. Этот метод является одним из наиболее технологичных способов обеспечивающих неразрушаемый контроль.
Электрохимический потенциал. Метод основан на связи работы выхода электронов с природой твердого тела и его структурным состоянием. Следовательно, любые превращения, проходящие в сплаве, приводят к изменению электронной структуры (межатомные связи) кристалла, в том числе и на поверхностные свойства выхода ЭХП [17].
Зависимость вида и концентрации структурных нарушений кристалла позволяет рассматривать дефекты как независимые компоненты, равновесные с вакуумом. На основе термодинамики межмолекулярного взаимодействия устанавливается зависимость от вида и концентрации структурных изменений. Ход изменения ЭХП качественно согласуется с зависимостью σ ↔ ε (напряжение–деформация). Если рост напряжений, обусловленный фазовыми превращениями, приводит к уменьшению выхода ЭХП, то при σ → const наблюдается ЭХП → const, а при снижении напряжений ЭХП возрастает в виде скачка межфазового потенциала.
Следовательно, процессы, сопровождающиеся генерацией свободной энергии термоупругого МП, могут быть зафиксированы с высокой чувствительностью как выход ЭХП.
Выход ЭХП сравнительными с эталоном неразрушающими методами позволяет определять химический состав детали или заготовки. Определение интервалов температур МП превращений полуфабрикатов для конкретной партии материала позволяет с достаточной точностью производить не только разбраковку по температурам МП, но и осуществлять контроль этих температур на готовых деталях.
С целью определения интервалов МП осуществляется замер разности ЭХП каломельного электрода и исследуемой детали или заготовки (труба, пруток, лист, проволока и т.п.) в криокамере, которая нагревается до температуры 120°С со скоростью 3.5 град/мин, а затем охлаждаются со скоростью 0.5 град /мин.
На основании экспериментальных исследований партии материала, установлены зависимости между значениями ЭХП и уровнем приложенных напряжений на стандартных образцах при одноосном растяжении от 0 до 600 МПа, осуществляется замер ЭХП в точке или на участке поверхности контролируемой детали. В соответствии с установленной зависимостью определяется действующее в детали напряженное состояние на любом этапе ее эксплуатации.
Выводы. В статье рассмотрены принципы проведения контроля термомеханических характеристик материала заготовок перед их применением, показаны различные методы, позволяющие определять температуры фазовых превращений сплавов, обладающих ЭПФ на основе TiNi, были показаны достоинства и недостатки методов в зависимости от их трудоемкости и достоверности результатов. Следует отметить, что ультразвуковой метод контроля фазовых превращений позволяет осуществлять всесторонний контроль физических и термомеханических характеристик. Данный метод применим для 100% контроля, разбраковки заготовок (типа муфт ТМС) диаметрами 12–40 мм и длиной 10–100 мм, в интервалах температур от –196 до +300°С.
Список литературы
Lotkov A.I., Kuznetsov A.V. Elastic properties of Ti-Ni single crystals preceding B2→B19′ and B2→R→B 19' martensitic transformations // Physics of Metals and Metallography. 1988. V. 66 (5). P. 65.
Lotkov A.I., Grishkov V.N., Timkin, Baturin A., Zhapova D. Yield stress in titanium nickelide-based alloys with thermoelastic martensitic transformations // Materials Science and Engineering A. 2019. V. 744. P. 74.
Sittner P., Sedlak P., Seiner H., Sedmak P., Pilch J., Delville R., Heller L., Kaderavek L. On the coupling between martensitic transformation and plasticity in NiTi: Experiments and continuum based modeling // Progress in Materials Science. 2018. V. 98. P. 249. https://doi.org/10.1016/j.pmatsci.2018.07.003
Depriester D., Maynadier A., Lavernhe-Taillard K., Hubert O. Thermomechanical modelling of a NiTi SMA sample submitted to displacement-controlled tensile test // International Journal of Solids and Structures. 2014. V. 51 (10). P. 1901. https://doi.org/10.1016/j.ijsolstr.2014.01.027
Khasyanov U., Romanov A.N., Khasyanova D.U., Khrushchov M.M. Self-Oscillation Conditions in Alloys with the Shape Memory Effect // Journal of Machinery Manufacture and Reliability. 2018. V. 47. № 3. P. 278. https://doi.org/10.3103/S1052618818030081
Хасьянова Д.У. Технологическое обеспечение качества изготовления муфт ТМС и сборки трубопроводов. Автореферат канд. диссерт., М.: МГУПИ, 2012.
Dughaish Z.H. Effect of variation of proton beam energy on the martensitic transformation temperature of shape memory nitinol alloy // Materials Letters. 1997. V. 32 (1). P. 29. https://doi.org/10.1016/S0167-577X(97)00007-4
Ермаков В.П., Коломыцев В.И., Лободюк В.А., Хандрос Л.Г. Связь физических свойств и структурных состояний, возникающих при термомеханической обработке в сплавах // Металлофизика. 1982. Т. 4. № 6. С 23.
Alarcon E., Heller L., Chirani S.A., Sittner P., Kopecek J., Saint-Sulpice L., Calloch S. Fatigue performance of superelastic NiTi near stress-induced martensitic transformation // International Journal of Fatigue. 2016. V. 95. P. 76. https://doi.org/10.1016/j.ijfatigue.2016.10.005
Khasyanova D.U. The mechanism of fretting corrosion of details from alloy with shape memory effect. IOP Conference Series: Materials Science and Engineering. 13. Cep. “XIII International Scientific Conference “Tribology for Mechanical Engineering”, TriboMash 2020" 2020. 012014. https://doi.org/10.1088/1757-899X/996/1/012014
Leyland A., Matthews A. On the significance of the H/E ratio in wear control: a nanocomposite coating approach to optimised tribological behavior // Wear. 2000. V. 246 (1–2). P. 1. https://doi.org/10.1016/S0043-1648(00)00488-9
Bekker A., Brinson L.C. Phase diagram based description of the hysteresis behavior of shape memory alloys // Acta Materialia. 1998. V. 46 (10). P. 3649. https://doi.org/10.1016/S1359-6454(97)00490-4
Khasyanova D.U. Conditions for Operational Reliability and Tightness of Thermomechanical Joining Pipelines Using Couplers // J. Mach. Manuf. Reliab. 2020. V. 49. № 2. P. 110. https://doi.org/10.3103/S1052618820020089
Лифшиц Б.Г. Физические свойства металлов и сплавов. М.: Машиностроительная литература. 1956. С. 22, 309, 331.
Хасьянов У., Хасенов Б.П. Возникновение автоколебаний в сплавах TiNi в процессе быстрого нагрева и охлаждения // Всесоюзная научная конференция “Сверхупругость, эффект памяти формы и их применение в новой технике”. Томск, 1985. С. 48.
Khasyanov U., Ugurchiev U. Ultrasonic Evaluation of the Thermomechanical Characteristics of TiNi Blanks // J. Mach. Manuf. Reliab. 2019. V. 48. P. 368. https://doi.org/10.3103/S1052618819040095
Shishkovsky I.V., Kuznetsov M.V., Morozov Y.G. Porous titanium and nitinol implants synthesized by SHS/SLS: Microstructural and histomorphological analyses of tissue reactions. Int. J Self-Propag. High-Temp. Synth. 2010. V. 19. P. 157. https://doi.org/10.3103/S1061386210020123
Дополнительные материалы отсутствуют.
Инструменты
Проблемы машиностроения и надежности машин