Проблемы машиностроения и надежности машин, 2022, № 4, стр. 54-62
Влияние морфологии контактных поверхностей на распределение температурного поля в устройствах для струйной цементации грунтов
В. И. Новиков *
Санкт-Петербургский государственный архитектурно-строительный университет
Санкт-Петербург, Россия
* E-mail: vitalynewage@gmail.com
Поступила в редакцию 04.03.2021
После доработки 09.11.2021
Принята к публикации 20.12.2021
- EDN: IOAHTN
- DOI: 10.31857/S0235711922020109
Аннотация
Рассмотрены проблемы, возникающие при построении модели, описывающей распределение температурного поля в узле “гидросъемник–буровой вал”, используемого в устройствах сверх высокого давления для струйной цементации грунтов. Описано влияние изменения морфологии металлической поверхности на распределение температурного поля за счет применения определенного вида обработки контактных поверхностей деталей устройств для струйной цементации грунтов. Показаны, твердотельная модель участка бурового вала и полученное методом конечных элементов, распределение температурного поля в элементах гидросъемника бурового става, возникающее в процессе его эксплуатации и факторы, существенно влияющие на тепловой баланс рассмотренного конструктивного узла.
Сегодня процесс строительства, включая крупномасштабное, любых сооружений, подразумевает выполнение различных работ в сложных гидрогеологических условиях, которые характеризуются наличием обводненных, неустойчивых или слабых грунтов и подземных напорных вод. Ситуацию усложняет присутствие городской застройки, что ведет к необходимости применения специальных способов производства работ и соответствующего оборудования. Анализируя отечественный и мировой опыт решения таких задач, следует отметить, что последнее десятилетние наиболее распространенным стало применение технологии струйной цементации грунтов (СЦГ). Общепринятое английское наименование – jet-grouting. Связанно это с тем, что при CЦГ отсутствуют значительные по объему земляные работы, которые требуют существенных материальных и финансовых затрат, не требуется переноса имеющихся коммуникаций, а так же больших площадей, что напрямую определяет длительность возведения конструкций и экологическую нагрузку на окружающую среду. Технология струйной цементации является высокопроизводительной, есть возможность создавать на различной глубине и разнообразные по формам и размерам грунтоцементные конструкции (своды, стены, сваи, и т.п.). При СЦГ можно проводить работы, как с поверхности, так и в стесненных условиях (в подвалах или закрытых помещениях и пространствах), что находит широкое применение при работах в городских условиях. К основным преимуществам такой технологии, относительно аналогичных, относятся отсутствие динамического воздействия на близлежащие здания и сооружения, гибкость и маневренность, что позволяет по необходимости оперативно вносить корректировки в используемые на данном этапе проведения работ технологические режимы.
Несмотря на перечисленные достоинства более широкое применение CЦГ сдерживается отсутствием нормативной документации и достаточно высокой сложностью оборудования. Поскольку технология считается довольно новой, подавляющая масса публикаций по данной тематике посвящена общим вопросам применения СЦГ в различных условиях [1, 2], так же рассматривается влияние создаваемых грунтобетонных колон на состояние грунта, дорог, фундаментов зданий, тоннелей и котлованов [3], подробно рассмотрены изменения и прогнозирование прочностных характеристик получаемого грунтобетона и конструкции в зависимости от технологических параметров [4]. Хотя в последние несколько лет значительно увеличилось количество публикаций, рассматривающих частные вопросы или иные возможности применения [5], но по-прежнему лишь в небольшом количестве работ приводятся применяемые агрегаты и освещаются проблемы конструирования оборудования для технологии СЦГ [6, 7].
Типовая конструктивная схема СЦГ содержит источник высокого давления, средства передачи высоконапорной струи цементного раствора и технологический инструмент (гидромонитор). Поскольку не всегда есть возможность расположить источник давления и технологический инструмент в непосредственной близости друг от друга, передающие звенья могут быть довольно протяженными, вследствие чего снижается надежность и появляются значительные гидравлические потери по длине и увеличиваются эксплуатационные затраты. Основным таким звеном в передающих магистралях является гидросъемник (вертлюг). Принято применять устройства, сконструированные для бурения, хотя номинальное выдерживаемое ими наибольшее давление, является относительно невысоким и использование вертлюгов в струйной цементации требует некоторой модернизации для обеспечения расширения области эффективного применения метода СЦГ, в противном случае гидросъемник станет сдерживающим фактором в развитии технологии, поскольку, как отмечено в [6], это наиболее часто выходящий из строя элемент.
Постановка задачи. Моделируя влияние обработки контактных поверхностей на напряженно-деформированное состояние и в частности распределение температурного поля в узле “гидросъемник–буровой вал”, воспользуемся методикой, изложенной в [8]. При проведении расчетов необходимо рассмотреть 3D-модель вала не с гладкими поверхностями, а с контактной поверхностью, состоящей из вершин шероховатостей. Для этого построена 3D-модель имитирующая поверхность, которая показана на профилограмме (рис. 1a) с уровнем шероховатости Ra = 1.4 мкм. Поскольку высота неровностей шероховатости крайне невысока, следует создавать конечно-элементную сетку с соответствующим размером элементов, т.е. порядка 0.001 мм и менее. При создании сетки с максимальной длиной стороны элемента в 1 мм, их число составляет 135 785, генерация сетки с размерами в 0.1 мм приводит к увеличению их количества до 2 × 106 элементов и т.д. Если же использовать сетку с максимальной длиной стороны элемента, на порядки превышающей величину неровностей рассматриваемой поверхности, то в процессе генерации сетки происходит “сшивание” (т.е. совмещение) рядом находящихся узлов и контактная поверхность из “шероховатой” преобразуется в “клинообразную”.
Рис. 1.
Высоты неровностей профиля шероховатости: (a) – профилограмма поверхности; (б) – вид той же поверхности при одинаковых вертикальном и горизонтальном масштабах.
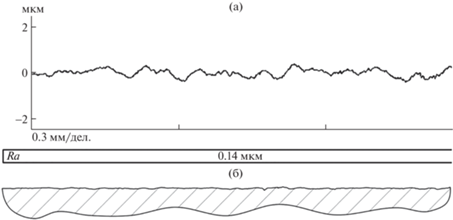
Принимая во внимание последнее утверждение, рациональным будет применение 3D-модели, описанной в [9], с учетом изменения величины тепловой мощности для каждого рассматриваемого уровня высоты неровностей профиля шероховатости моделируемой поверхности бурового вала. Однако тут наиболее частым заблуждением является то, что на профилограмме реальной поверхности выступы имеют островершинный вид [10]. На самом деле этот эффект связан, с различием в масштабах [11] вертикального и горизонтального увеличения профилограммы (рис. 1a), из которой следует, что профиль реальной поверхности при одинаковых значениях вертикального и горизонтального увеличения имеет плавный, пологий вид (рис. 1б).
Анализ влияния электролитно-плазменного полирования на морфологию обработанной поверхности. Качество поверхностного слоя рабочих поверхностей деталей оказывает значительное влияние на срок эксплуатации любых конструктивных узлов и элементов конструкций. Поскольку, при циклических нагрузках, которые испытывают практически все ответственные детали, разрушение начинается на поверхности (или в около поверхностных слоях) локально, в областях концентрации напряжений (деформации соответственно), которые создают повреждения поверхности в результате непосредственно циклического нагружения, либо надрезов в виде следов обработки или воздействия агрессивной среды. Соответственно изменение высоты шероховатости, например, путем применения какой-либо обработки рассматриваемой поверхности бурового вала, в частности полирования, приведет к изменению площади контактной поверхности, а значит и изменению количества, выделяемой в процессе работы устройства сверх высокого давления, теплоты. Что непосредственно влияет на тепловой баланс рассматриваемой системы.
Для изменения величины шероховатости поверхности металлических деталей используются различные методы обработки поверхности, такие как механический, химический или электрохимический. Основным недостатком методов, реализующих химическое и электрохимическое воздействие на обрабатываемую поверхность, является необходимость приготовления, использования и утилизации многокомпонентных электролитов на основе сильных кислот (серной, ортофосфорной, соляной и др.), что влечет за собой высокую токсичность электролитов, коррозию технологического оборудования, вредные условия труда для обслуживающего персонала, экологический вред окружающей среде, высокий расход электролита на единицу обрабатываемой площади; механический метод – это трудоемкий процесс, основными недостатками которого являются: применение высокоточного и дорогостоящего оборудования, проблема механизации и автоматизации полирования деталей сложной формы и тонкостенных изделий, а также образование дефектов в микровпадинах в виде неметаллических включений и следов технологических межоперационных покрытий и др. В отличие от данных технологических методов, электролитно-плазменное полирование (ЭПП) позволяет обрабатывать изделие в среде нетоксичных минеральных электролитов из безопасных и безвредных веществ [12]. Технологически процесс ЭПП можно реализовать несколькими способами. Традиционно применяют более простой метод “погружением”, заключающийся в размещении в ванне с электролитом обрабатываемого изделия с обработкой всех контактирующих с электролитом поверхностей. При использовании второго метода происходит локальное воздействие на обрабатываемую поверхность электролитической плазмы в струе электролита [13]. Метод более сложен с точки зрения применяемого оборудования и изучен недостаточно широко по сравнению с первым способом, соответственно распространен значительно меньше. В результате применения ЭПП с поверхности удаляется наиболее загазованный и богатый инородными включениями слой металла. Метод характеризуется отсутствием силового воздействия на обрабатываемую поверхность, легко поддается механизации и автоматизации, удаляемый с поверхности в процессе обработки металл, легко утилизируется и не требуется специальных очистных сооружений. Степень снижения уровня шероховатости поверхности после электролитно-плазменного полирования значительно зависит не только от начальной шероховатости обрабатываемого изделия, но также большое значение для процесса обработки имеет наличие кривизны обрабатываемой поверхности [14].
Проведенные исследования обработанной ЭПП поверхности показали, что изменяются не только количественные показатели шероховатости поверхности, но и изменяется характер неровностей, совокупность которых и определяет термин “шероховатость поверхности”, т.е. изменяется морфология поверхности объекта обработки, что подтверждается снимками с профилограммами образцов из сталей 30ХГСА и 12Х18Н10Т, которые сделаны с помощью сканирующего зондового микроскопа Solver P-47 Pro с разрешением 5 нм (рис. 2). Основные параметры шероховатостей поверхностей определены с использованием прибора MarSurf PS1. Начальный уровень параметра шероховатости Ra для образцов из сталей 30ХГСА и 12Х18Н10Т составляет 1.353 мкм и 0.395 мкм, после обработки – 0.140 мкм и 0.143 мкм соответственно (рис. 2, профилограммы). Таким образом, после ЭПП произошло не только снижение параметра Ra, но и сглаживание вершин неровностей, что положительно сказывается на напряженно-деформированном состоянии передающих устройств сверхвысокого давления, поскольку, приводит к уменьшению трения, снижению тепловыделения при эксплуатации данного элемента конструкции и износа уплотняющего элемента и повышению надежности такого рода устройств.
Рис. 2.
Морфология (сверху) и профилограмма (снизу) поверхности образца из стали 12Х18Н10Т: (a) – до обработки ЭПП; (б) – после обработки ЭПП.
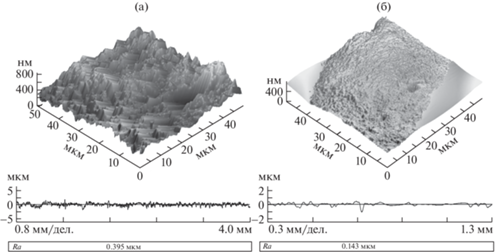
Лучшие антифрикционные свойства обработанной таким способом поверхности связаны, не столько с низкой шероховатостью, сколько с благоприятной морфологией поверхности. В отличие от механических методов обработки при электролитно-плазменном полировании формируется морфология, характеризующаяся низкой высотой и большим радиусом округления выступов и плавностью неровностей профиля с большим периодом. В результате этого период приработки сопряжения, связанный в первую очередь с пластическим деформационным разрушением неровностей при их контакте с поверхностью и формированием равновесной шероховатости, отсутствует или выражен очень слабо. Работа сопряжения сразу начинается с упругого контактирования неровностей. Более низкий коэффициент трения объясняется меньшей площадью фактического пятна контакта с сопряженной поверхностью и большим давлением в области фрикционного контакта и в момент введения смазки происходит скачкообразное уменьшение коэффициента трения более чем на 21% с последующим его постепенным увеличением до исходного уровня на достаточно протяженном промежутке времени, что свидетельствует о хорошем удержании смазочного материала поверхностью вследствие сформированной в процессе обработки топографии, включающей случайные неровности, обусловленные микроструктурой материала. В условиях сухого трения скольжения происходит резкое повышение коэффициента трения – более чем в 4 раза для механически и полированных поверхностей и более чем в 5.5 раза для шлифованной поверхности. Таким образом, благодаря сформированной в процессе обработки благоприятной морфологии поверхности, электролитно-плазменное полирование способствует существенному улучшению характеристик поверхности деталей, работающих в условиях трения скольжения с достаточной и ограниченной подачей смазочного материала [11].
Результаты вычислительного эксперимента и их анализ. Для оценки изменения площади контактной поверхности, при введении предлагаемого вида обработки, рассмотрим модель изменения одиночной высоты неровности профиля шероховатости (рис. 3). Схема отображает изменение высоты неровностей с уровня в Ra = 1 мкм, который можно считать наиболее удобной начальной величиной шероховатости для проведения электролитно-плазменной обработки, до уровня Ra = 0.14 мкм, что является оптимально достижимым для данного вида полирования [12, 14]. Моделируется снятие слоя материала с одной отдельно взятой вершины неровности и несмотря на то, что такая модель не совсем полно отражает реальную картину снижения шероховатости обрабатываемой поверхности, т.к. можно предположить, что пробой газовой анодной оболочки может происходить с равной вероятностью, как на выступах, так и во впадинах профиля обрабатываемой поверхности в областях случайной неоднородности электрического поля, поэтому изменению равновероятно подвергаются не только вершины шероховатости, но и впадины, что не находит отражения, но в данном случае моделирование в таком виде можно использовать, поскольку здесь, для оценки изменения площади контакта поверхностей, важно непосредственно снижение уровня шероховатости.
Обобщая сравнение изменения высоты неровности можно утверждать следующее: согласно схеме (рис. 3) при изменении уровня шероховатости от Ra = 1 мкм до Ra = 0.14 мкм (с промежуточными значениями шероховатости Ra = 0.8 мкм, Ra = = 0.6 мкм и Ra = 0.4 мкм), происходит изменение площади поверхности на 31% (с изменением площади поверхностей для промежуточных значений шероховатости на 12%, 20%, 28% соответственно), при допущении, что рассматриваются площади шаровых сегментов, имитирующих неровность (рис. 3), что позволяет оценить снижение величины выделяемой теплоты, вводя допущение о прямо пропорциональной зависимости данных величин.
Чтобы задать тепловую нагрузку необходимо рассчитать значение температуры, воздействующей на контактные поверхности. При известном значении величины тепловой мощности (при давлении 36 МПа составляет 7.6 кВт [15]) количество выделившейся за то же время теплоты равно произведению мощности на время и составляет 1368 кДж. С другой стороны, количество теплоты можно определить по формуле
где c – удельная теплоемкость вещества (стали), Дж/кг°C; m – масса вещества (составляет 12 кг); ΔT– изменение температуры (от начального значения T1 = 20°C до конечного искомого T2), °C.Задаваемым значением является величина температуры ${{T}_{2}}$ и после преобразования, получаем формулу для расчета ${{T}_{2}}$
Сведем полученные расчетные данные в табл. 1, оценив снижение величины выделяемой тепловой мощности и значения соответствующей температуры T2 для каждого уровня шероховатости, принимая в качестве начальных значений уровень шероховатости в 1 мкм, а значение T2 = 305°С.
Таблица 1.
Таблица зависимости уменьшения количества теплоты от снижения уровня шероховатости
Значение величины шероховатости Ra, мкм | Величина изменения площади поверхности, % | Количество теплоты Q, кДж | Значение температуры T2, °С |
---|---|---|---|
1.0 | 0 | 1368.0 | 305 |
0.80 | 12 | 1203.84 | 214 |
0.60 | 20 | 1094.40 | 196 |
0.40 | 28 | 984.96 | 179 |
0.14 | 31 | 943.92 | 172 |
3D-модель представляет собой цилиндрическую часть бурового вала, передающего давление устройства, длиною 188 мм с внутренним глухим отверстием ∅45 мм, однако будет добавлено два отверстия ∅20 мм, через которые проводится подача водно-цементной смеси во внутреннее отверстие. Построение конечно-элементной модели проведено элементами с максимальной длиной стороны 1.5 мм и сетка конечных элементов сгенерирована с максимальными коэффициентами сгущения на поверхности и разрежения в объеме – 1 и 1.5 соответственно. Конечно-элементная сетка содержит 482 675 элементов и 121 297 узлов.
Рассчитаем распределения температурного поля в выбранном участке бурового вала для каждого из значений шероховатости Ra с учетом температуры, подаваемой водно-цементной смеси 60°С. Результаты расчета представлены на рис. 4, 5 соответственно изменению величины Ra согасно табл. 1.
Рис. 4.
Распределение температурного поля в буровом вале с величиной шероховатости контактных поверхностей Ra = 1 мкм.
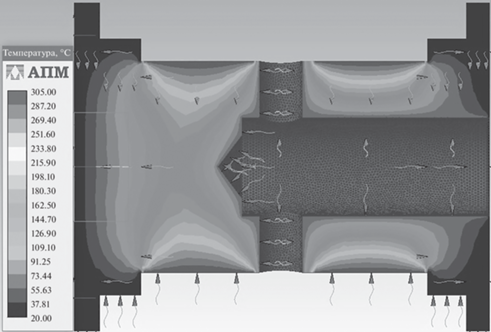
Рис. 5.
Распределение температурного поля в буровом вале с величиной шероховатости контактных поверхностей Ra = 0.14 мкм.
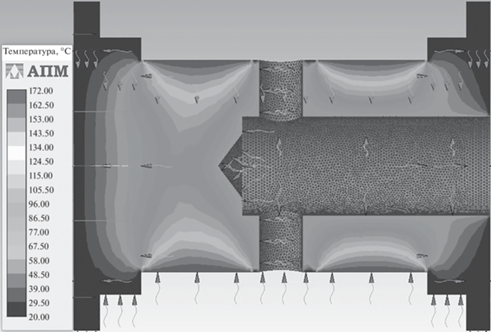
Распределение температуры во всех вариантах качественно имеют идентичный характер, что закономерно и совпадает с результатами, полученными в [9], поскольку существенно изменялось лишь значение количества теплоты (тепловой мощности). Количественно картина распределения меняется в сторону уменьшения значения температуры при уменьшении уровня шероховатости. Если при начальной шероховатости высотой Ra = 1 мкм глубина распределения температуры выше величины 200°С составила около 15 мм, а температура в середине бурового вала порядка 180°С, то начиная с уровня шероховатости Ra = 0.6 мкм, даже с учетом температуры, подаваемой водно-цементной смеси около 60°С, температура контактных поверхностей составляет менее 200°С, а в середине бурового вала порядка 100°С.
Заключение. Полученное, в результате моделирования, распределение температурного поля позволяет оценить состояние с точки зрения распределения, возникающих в процессе эксплуатации этого узла сверхвысокого давления, температур и дать рекомендации по выбору материалов уплотняющих элементов. Анализируя результаты моделирования можно сделать вывод, что при выборе материалов, применяемых в настоящее время для изготовления уплотнительных элементов, необходимо учитывать тепловую нагрузку, возникающую в процессе эксплуатации устройств для струйной цементации грунтов. Соответственно, чтобы обеспечить предсказуемость проектных характеристик конструкций устройств сверхвысокого давления и повысить их эффективность необходимо применять уплотнительные элементы, изготовленные из материалов, способных выдерживать значительные тепловые нагрузки, либо влиять на тепловой баланс путем изменения технологических параметров, что, несомненно, скажется на производительности, либо уменьшать тепловыделение путем изменения морфологии контактных поверхностей за счет введения дополнительной обработки поверхности бурового вала.
Список литературы
Ludemann S.M., Garcia R.S., Barbosa M.G.T., Cavalcante A.L.B. A Contingency Solution using Jet Grouting Barrier for a Dam under Risk of Piping in Brazil // Soils and Rocks, São Paulo. 2018. V. 41 (1). P. 17. https://doi.org/10.28927/SR.411017
Merlini D., Stocker D., Falanesca M., Schuerch R. The Ceneri Base Tunnel: Construction Experience with the Southern Portion of the Flat Railway Line Crossing the Swiss Alps // Engineering. 2018. V. 4. P. 235. https://doi.org/10.1016/j.eng.2017.09.004
Yong T., Ye L., Dalong W. Deep Excavation of the Gate of the Orient in Suzhou Stiff Clay: Composite Earth-Retaining Systems and Dewatering Plans // J. Geotech. Geoenviron. Eng. 2018. V. 144 (3). P. 350. https://doi.org/10.1061/(ASCE)GT.1943-5606.0001837
Toraldo C., Modoni G., Croce P. Reliable definition of the characteristic strength of jet grouted soils by Random Field Theory // Procedia Engineering. 2016. V. 158. P. 416. https://doi.org/10.1016/j.proeng.2016.08.465
Veropalumbo R., Russo F., Viscione N., Biancardo S.A. Rheological Properties Comparing Hot and Cold Bituminous Mastics Containing Jet Grouting Waste // Advances in Materials Science and Engineering. Volume 2020. Article ID 8078527. 16 p. https://doi.org/10.1155/2020/8078527
Гарипов М.В., Головин К.А. Разработка конструкции расширителя прокалывающей установки для закрепления неустойчивых горных пород // Известия Тульского государственного университета. Технические науки. 2013. № 1. С. 326.
Yuan Y., Shen S.L., Wang Z.F., Wu H.N. Automatic Pressure-Control Equipment for Horizontal Jet-grouting // Autom. Constr. 2016. V. 69. P. 11.
Новиков В.И., Пушкарев А.Е., Воронцов И.И. Методика моделирования теплового баланса элементов конструкции строительно-дорожных машин для струйной цементации грунтов // Научно-технический вестник Брянского государственного университета. 2019. № 3. С. 369. https://doi.org/10.22281/2413-9920-2019-05-03-369-376
Новиков В.И., Пушкарев А.Е., Манвелова Н.Е. Моделирование теплового баланса в процессе эксплуатации элементов гидросъемника бурового става для струйной цементации грунтов // Научно-технический вестник Брянского государственного университета. 2020. № 3. С. 404. https://doi.org/10.22281/2413-9920-2020-06-03-404-410
Новиков В.И., Пушкарев А.Е., Щербаков А.П., Кузьмин О.В. Особенности расчета теплового баланса гидросъемника с учетом влияния на шероховатость поверхности электролитно-плазменного полирования // Металлообработка: научно-производственный журнал. 2020. № 4. С. 16. https://doi.org/10.25960/mo.2020.4.16
Синькевич Ю.В. Электроимпульсное полирование на основе железа, хрома и никеля / Синькевич Ю.В. [и др.]. Минск: БНТУ, 2014. 325 с.
Nestler K., Bottger-Hiller F., Adamitzki W., Glowa G., Zeidler H., Schubert A. Plasma Electrolytic Polishing – an Overview of Applied Technologies and Current Challenges to Extend the Polishable Material Range // Proc. CIRP. 2016. V. 42. P. 503. https://doi.org/10.1016/j.procir.2016.02.240
Popov A.I., Novikov V.I., Radkevich M.M. Characteristics of the development of electric discharge between the jet electrolyte cathode and the metal anode at atmospheric pressure // High Temperature. 2019. T. 57. № 4. P. 447. https://doi.org/10.1134/S0018151X19030118
Новиков В.И., Мурашкин С.Л., Фоломкин А.И. Технологические возможности чистовой обработки турбинных лопаток электролитно-плазменным методом // Научно-технические ведомости Санкт-Петербургского государственного политехнического университета. 2012. № 1–2 (147). С. 105.
Головин К.А., Маликов А.А., Пушкарев А.Е. Тепловой режим работы гидросъемника высокого давления на установках гидроструйной цементации // Известия Тульского государственного университета. Технические науки. 2015. № 4. С. 46.
Дополнительные материалы отсутствуют.
Инструменты
Проблемы машиностроения и надежности машин