Проблемы машиностроения и надежности машин, 2022, № 4, стр. 81-89
Особенности формообразования полых осесимметричных заготовок из медного сплава БРХ08 с применением ротационных методов
И. А. Бурлаков 1, Д. А. Константинов 1, С. В. Морозов 2, П. А. Петров 3, *, Ву Чонг Бач 3, 4, А. В. Македонов 2, Р. Ю. Сухоруков 5
1 Производственный комплекс “Салют” АО “ОДК”
Москва, Россия
2 Филиал АО “ОДК” НИИД
Москва, Россия
3 Московский политехнический университет
Москва, Россия
4 Университет имени Чан Дай Нгхиа
Хошимин, Вьетнам
5 Институт машиноведения им. А.А. Благонравова РАН
Москва, Россия
* E-mail: petrov_p@mail.ru
Поступила в редакцию 20.01.2021
После доработки 18.04.2022
Принята к публикации 20.04.2022
- EDN: OANKAV
- DOI: 10.31857/S0235711922040058
Аннотация
В статье рассмотрена возможность формообразования точных полых осесимметричных заготовок из медного сплава БРХ08 с применением комбинированной технологии, включающей изотермическую раскатку, ротационную вытяжку и промежуточные термообработки. Технология базировалась на результатах компьютерного моделирования программой QForm VX с применением найденной реологической модели материала, рассчитанной по методу Хензеля–Шпиттеля.
Промышленность в больших количествах применяет полые осесимметричные детали, заготовки которых изготавливают самыми различными методами, преимущественно, гибкой листа с последующей сваркой. В случае необходимости изготовления бесшовных деталей решением является применение ротационных методов пластического формообразования, в частности, изотермической раскатки с последующей холодной ротационной вытяжкой на специализированных станках.
Наиболее существенное преимущество ротационной вытяжки перед другими традиционными способами обработки заключается в том, что она обеспечивает выполнение высоких требований по точности геометрических размеров, разнотолщинности стенок и овальности получаемых оболочек [1, 2]. Вместе с тем процесс дает возможность получать значительную экономию материала за счет использования более простых по форме и способу изготовления заготовок, а также получения более высоких механических свойств готовой детали благодаря упрочняющему эффекту процесса [3, 4].
До недавнего времени, ротационная вытяжка не получала должного распространения в нашей стране. Рядом исследователей, такими как И.П. Ренне, Е.А. Попов, Л.Г. Юдин, С.П. Яковлев [5] и др., велись теоретические работы в этой области, но широкого применения на практике эти работы не нашли. Возможно, это связано с применением ротационной вытяжки для изготовления только осесимметричных деталей.
Несмотря на такое ограничение, налагаемое спецификой процесса, а также на сравнительно невысокую производительность, номенклатура изделий, которые можно получать ротационной вытяжкой, чрезвычайно широка. Это и детали типа оболочек, и цилиндры с одинаковой или переменной толщиной стенки, и стаканы с фланцами и без них, и многие другие [6, 7]. Ротационная вытяжка в ряде случаев является единственно возможным способом изготовления сложнопрофильных деталей.
Еще одним большим преимуществом ротационной вытяжки является относительно невысокая стоимость оборудования и оснастки. В ряде случаев, для получения деталей, возможно применение обычных токарных станков со специальной оснасткой [8].
Широкие возможности применения ротационной вытяжки давно оценили в США, странах Западной Европы, Японии, где данное направление обработки металлов давлением интенсивно развивается.
Развитие техники ротационной обработки металлов обусловлено спросом различных отраслей промышленности и машиностроения при создании изделий новой техники на полые осесимметричные оболочки конической, цилиндрической и криволинейной формы со стенками постоянной и переменной толщины, выполненные из коррозионностойких, высокопрочных и тугоплавких металлов и сплавов.
Целью статьи является разработка технологии изготовления полых высокоточных заготовок из медного сплава БРХ08.
Для достижения поставленной цели необходимо было решить задачи: 1) исследовать прочностные свойства и структуру исходного материала; 2) определить реологические свойства сплава с применением зависимости Хензеля–Шпиттеля; 3) разработать технологическую схему изготовления заготовки детали; 4) выполнить компьютерное моделирование процесса изготовления заготовки с применением найденной реологической модели металла; 5) осуществить экспериментальное моделирование процесса изготовления заготовки; 6) выполнить анализ полученных данных и оценить возможность изготовления полномасштабной заготовки.
Материалы, оборудование и методы исследования. Исходные заготовки представляли собой диски из медного сплава БРХ08 высотой 60 и диаметром 450 мм, химический состав которого: (% мас.) Сu – 99.54; Cr – 0.46.
Микроструктура представляет собой полиэдрические зерна без неметаллических включений (рис. 1).
Рис. 1.
Микроструктура исследуемого образца в продольном сечении: (а) – увеличение ×100; (б) – увеличение ×500.
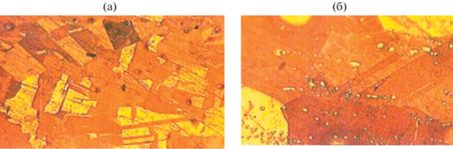
Результаты рентгеноструктурного металлографического анализа (табл. 1, рис. 2) позволили определить выделения фазовых составляющих в виде строчек на основе кремния и хрома, которые, по нашим данным, не оказывают влияния на формообразующие операции.
Таблица 1.
Результаты рентгеноструктурного металлографического анализа
Название спектра | Si | Cr | Cu | Сумма | Сечение |
---|---|---|---|---|---|
Спектр 1 | 0.53 | 39.75 | 59.72 | 100.00 | Продольное сечение |
Спектр 2 | 0.50 | 80.58 | 18.93 | 100.00 | |
Спектр 3 | – | 0.46 | 99.54 | 100.00 |
Рис. 2.
Данные рентгеноструктурного металлографического анализа исследуемого образца: 1, 2, 3 – спектры исследования.
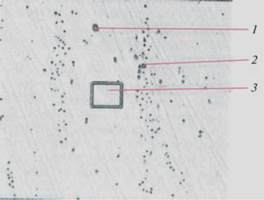
Механические характеристики исходного материала определяли путем испытания цилиндрических образцов (рис. 3а) на растяжение.
Пластические характеристики металла после раскатки находили растяжением плоских образцов (рис. 3б).
Реологическая модель материала была построена на основе результатов испытания осадкой цилиндрических образцов диаметром и высотой 10 мм, изготовленных электроэрозионной вырезкой. Испытание проводили на машине модели LFM50 с постоянными скоростями деформации $\dot {\varepsilon }$ = 10–1, 10–2 и 10–3 с–1 при температурах 20, 400, 600 и 800°С. Интервал температур был выбран на основании результатов моделирования процессов изотермической раскатки и холодной ротационной вытяжки. Скорость деформации поддерживалась постоянной за счет управляемого перемещения траверсы машины. Испытание на растяжение проводили на испытательной машине мод. LFM50 со скоростью 2 мм/мин.
Для моделирования процессов изотермической раскатки и ротационной вытяжки заготовок был применен программный комплекс QForm VX [9]. Основной задачей его было определить рациональную толщину исходной заготовки, обеспечивающую необходимое качество полуфабриката для последующей ротационной вытяжки.
Для определения математической модели сопротивления медного сплава БРХ08 деформации выбрана эмпирическая модель, предложенная Хензелем–Шпиттелем [10], устанавливающая связь между напряжением текучести σi и термомеханическими параметрами
(1)
${{\sigma }_{i}} = A\exp ({{m}_{1}}T){{T}^{{{{m}_{9}}}}}\varepsilon _{i}^{{{{m}_{2}}}}\exp ({{{{m}_{4}}} \mathord{\left/ {\vphantom {{{{m}_{4}}} {{{\varepsilon }_{i}}}}} \right. \kern-0em} {{{\varepsilon }_{i}}}}){{\left( {1 + {{\varepsilon }_{i}}} \right)}^{{{{m}_{5}}T}}}\exp ({{m}_{7}}{{\varepsilon }_{i}})\dot {\varepsilon }_{i}^{{{{m}_{3}}}}\dot {\varepsilon }_{i}^{{{{m}_{8}}T}},$Исходные заготовки подвергали изотермической раскатке за два перехода на стане АЛРД-800 (рис. 4).
Рис. 4.
Схема раскатки плоской заготовки: P – сила прижима заготовки пинолью; V – частота вращения пиноли; S – скорость радиального перемещения роликов.
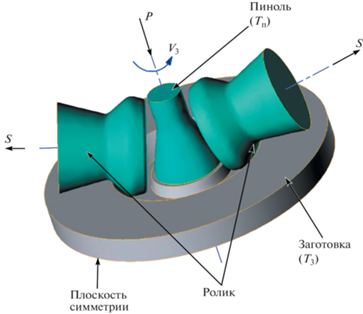
Из полученных полуфабрикатов ротационной вытяжкой на станке фирмы Leifeld PNC-111 получали заготовки готовых деталей деформацией одним роликом. Частота вращения оправки составляла 600 об/мин, осевая подача – 5 мм/мин.
Микроструктуру исследовали с применением бинокулярного микроскопа Olympus Delta c увеличениями 100 и 500. Контроль толщины стенок заготовок проводили при помощи ультразвукового толщиномера “38DL-PLUS”.
Технологическая схема изготовления включала операции: получение исходной заготовки для раскатки, изотермическая раскатка, изготовление промежуточного конического полуфабриката ротационной вытяжкой, промежуточный отжиг, вторая ротационная вытяжка. Учитывая значительные размеры требуемой детали, работы были выполнены на масштабных 1 : 8 моделях – исходная заготовка имела диаметр 112 и толщину 4.8 мм.
Термообработка заготовок из медного сплава БРХ08 проводилась со следующими режимами: нагрев до температуры 625–640°С; выдержка 60 мин; охлаждение на воздухе.
Результаты и обсуждение. Итоговые зависимости были получены для деформации двух типов. Первый тип – это холодная и теплая осадка в температурном интервале 20–400°С, и второй тип – это горячая осадка в температурном интервале 600–800°С. Найденные коэффициенты A, m1, m2, m3, m4, m5, m6, m7, m8 (1) приведены табл. 2.
Таблица 2.
Найденные коэффициенты модели Хензеля–Шпиттеля
Тип деформации | A | m1 | m2 | m3 | m4 | m5 | m7 | m8 | m9 |
---|---|---|---|---|---|---|---|---|---|
20 и 400°С | 10.0491 | – | 0.436 | 0.009 | – | 00004 | –0.924 | 0 | 1.3935 |
600 и 800°С | 10.0134 | – | 0.087 | –0.008 | – | –0.001 | 0.303 | 0 | 0.7614 |
В графическом виде расчетные и экспериментальные данные показаны на рис. 5. Сравнение экспериментальных и расчетных кривых показывает, что среднее отклонение не превышает 9%.
Рис. 5.
Сравнение экспериментальных и расчетных напряжений текучести при осадке образцов с различными скоростями деформации (с–1): (а) – 0.001; (б) – 0.01; (в) – 0.4; при различных температурах: I – 20°С; II – 400°С; III – 600°С; IV – 800 °С; ${\text{ - }}\,{\text{ - }}\,{\text{ - }}$ данные эксперимента; $---$ расчетная кривая (3).

Для моделирования были выбраны исходные заготовки трех толщин – 14, 16 и 18 мм. Исходными данными для расчета являлись: найденная реологическая модель материала; частота вращения заготовки 1.5 об/мин; температура заготовок и инструмента 800°C; деформирование двумя парами роликов, перемещающихся от оси вращения к ободу со скоростью 2.4 мм/мин. Результаты показаны на рис. 6.
Рис. 6.
Моделирование процесса изотермической раскатки. 1 – пиноль; 2 – заготовка; 3 – раскатной ролик.
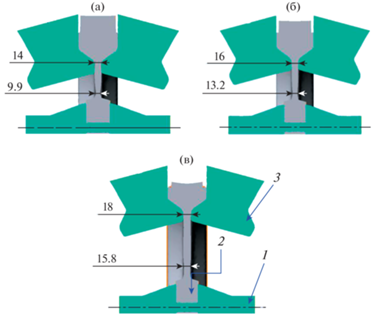
Моделирование позволило установить: 1) в процессе раскатки образуется шейка со значительным утонением материала полотна, что может привести к разрушению заготовки; 2) при начальной толщине полотна 14 и 16 мм утонение может достигать 60%; 3) минимальная толщина полотна, обеспечивающая стабильную толщину и утонение не более 12%, составляет 18 мм.
Влияние изотермической раскатки и термической обработки. Условия выполнения изотермической раскатки на стане АЛРД-800 соответствовали условиям, при которых выполнялось моделирование в программе QFORM. После второго прохода толщина заготовки составляла около 10 мм.
Как видно из рис. 7 изотермическая раскатка позволяет на 6–8% повысить пластичность исходного материала. Последующая термическая обработка повышает пластические характеристики незначительно – на 3–5%.
Рис. 7.
Диаграммы растяжения образцов медного сплава БРХ08: 1 – материал в состоянии поставки; 2 – образцы после изотермической раскатки; 3 – образцы после изотермической раскатки и термической обработки.
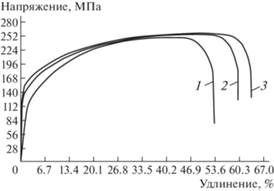
Физическое моделирование технологического процесса получения оболочки. Исходные заготовки изготавливались методом гидроабразивной резки. Ротационная вытяжка осуществлялась за два перехода с промежуточной термической обработкой. Первый переход ротационной вытяжки был выполнен с применением конической оправки, имеющей наклон образующей к оси вращения 21° (рис. 8). Расчетная величина деформации составляла 56%.
Ротационная вытяжка была выполнена методом проецирования [1] одним роликом за один проход с постоянным зазором между оправкой и роликом, который рассчитывался по известной формуле
где t0 – толщина исходной заготовки; t1 – толщина стенки заготовки после ротационной вытяжки; α1 – угол наклона образующей оправки к оси ее вращения.Толщина стенки, определяемая ультразвуковым толщиномером, составила 1.58‒1.67 мм против расчетной 1.72 мм. Разнотолщинность стенки заготовки составила ±0.05 мм. Разнотолщинность объясняется недостаточной жесткостью оправки и деформацией одним роликом, что в дальнейшем учитывалось при программировании процесса РВ.
После первого перехода заготовки были подвергнуты термическому отжигу, режимы которого описаны в разделе “Материалы, оборудование и методы исследования” настоящей статьи.
Второй переход был выполнен на оправке конической формы (рис. 9) с углом конической поверхности к оси вращения α2 = 11°. Формообразование заготовки осуществлялось также методом проецирования, как и на первом переходе.
Расчетная толщина стенки после второго перехода t2 была определена по формуле [1]
В нашем случае она должна составлять 0.86 мм. В действительности толщина составила 0.85–0.95 мм, что вероятно происходит из-за изгиба оправки под действием формообразующего ролика. Инструментальный и визуальный контроль показал соответствие модельной заготовки реальной детали по геометрическим параметрам.
Выводы. 1. Исследование свойств исходного сплава позволило установить, что макро- и микроструктура однородна, пластические характеристики находятся на высоком уровне, а наличие незначительного количества мелких полиэдрических зерен не оказало влияние на механические свойства материала. 2. Найдена реологическая зависимость предела текучести от деформации с применением уравнения Хензеля–Шпиттеля на основе данных, полученных осадкой цилиндрических образцов. 3. Разработана технологическая схема получения заготовки детали, включающая изотермическую раскатку и две операции ротационной вытяжки с промежуточной термообработкой. 4. Выполнено компьютерное моделирование процессов изотермической раскатки и ротационных вытяжек с применением найденной реологической модели материала. 5. Осуществлено экспериментальное моделирование технологического процесса изготовления заготовки детали в масштабе 1 : 8. 6. Анализ полученных данных позволяет сделать вывод о возможности изготовления предложенной технологией полномасштабных заготовок деталей.
Список литературы
Могильный М.И. Ротационная вытяжка оболочковых деталей на станках. М.: Машиностроение, 1983. 190 с.
Корольков В.И. Математическое, методическое и программное обеспечение процессов ротационной вытяжки из листа и труб: Дис. … док. техн. наук. Воронеж: Воронежский гос. техн. ун-т, 1997. 450 с.
Кандаров И.В. Формирование регламентированной структуры в сплаве ВТ6 для повышения эксплуатационных свойств лопаток газотурбинного двигателя. Дис. … канд. техн. наук. Набережные Челны: Казан. (Приволж.) федер. ун-т, 2016. 148 с.
Sakai T., Miura H., Belyakov A., Kaibyshev R., Jonas J.J. Dynamic and post-dynamic recrystallization under hot, cold and severe plastic deformation conditions // Progress in Materials Science. 2014. V. 60. № 1. P. 130.
Юдин Л.Г., Яковлев С.П. Ротационная вытяжка цилиндрических оболочек. М.: Машиностроение, 1984. 128 с.
Раков Д.Л., Сухоруков Р.Ю., Гаврилина Л.В. Анализ и оценка технологий и оборудования для изготовления заготовок длинномерных полых валов газотурбинных двигателей из жаропрочных никелевых и титановых сплавов на базе морфологического подхода // Проблемы машиностроения и оптимизации. 2015. № 4. С. 136.
Утяшев Ф.З., Рааб Г.И. Деформационные методы получения и обработки ультрамелкозернистых и наноструктурных материалов. Уфа: Гилем, 2013. 375 с.
Бурлаков И.А. Ротационная вытяжка деталей газотурбинных двигателей // Заготовительные производства в машиностроении. 2008. № 4. С. 27.
http://qform3d.ru/files_ru/2008_0001_0.pdf (дата обращения 12.03.2017).
Хензель А., Шпиттель Т. Расчет энергосиловых параметров в процессах обработки металлов давлением: Справ. изд. пер. с нем. М.: Металлургия, 1982. 360 с.
Дополнительные материалы отсутствуют.
Инструменты
Проблемы машиностроения и надежности машин