Проблемы машиностроения и надежности машин, 2022, № 4, стр. 90-96
Формирование деталей из сплава с эффектом памяти формы
И. С. Сплавский *
Институт машиноведения им. А.А. Благонравова РАН
Россия, Москва
* E-mail: spl-igor@yandex.ru
Поступила в редакцию 20.03.2021
Принята к публикации 20.04.2022
- EDN: JJWVNY
- DOI: 10.31857/S0235711922040149
Аннотация
В статье представлены методы формирования деталей из сплава с эффектом памяти формы с помощью применения современных методов обратного выдавливания, который существенно экономит использование дорогостоящего сплава типа “нитинол” и исключает процесс сверления труднообрабатывающего сплава. Описаны способы и условия применения высокотемпературной термообработки при формировании деталей из сплава с эффектом памяти формы.
Создание соединений трубопроводов является традиционной и наиболее отработанной в производственном отношении сферой применения сплавов с эффектом памяти формы (ЭПФ). В настоящее время в США налажено крупное производство широкой номенклатуры муфт из сплавов на основе никелида титана, которые используются для получения высокоресурсных соединений труб гидросистем самолетов и вертолетов, а также трубопроводных коммуникаций для водных и подводных кораблей. В силу высокой эксплуатационной безопасности и простоты сборки весьма перспективным является их применение при монтаже и ремонте трубопроводов атомных электростанций вместо аргонно-дуговой сварки, а также для соединения коммуникаций стационарных и мобильных водородных реакторов. Надежность таких соединений определяется уровнем контактного давления между трубой и силовыми поясками муфт, величина которого зависит от энергетики сплава при термическом восстановлении заданной деформации мартенситной неупругости в процессе фазового превращения. Поэтому основной силовой характеристикой таких материалов является величина реактивного напряжения термомеханического возврата. Обычно при сертификации сплава его измеряют в условиях абсолютно жесткого противодействия при предварительной деформации мартенсита неупругости растяжением на 8%, определяемого объемом памяти материала.
Для опытно-промышленных партий полуфабрикатов, получаемых прессованием или прокаткой, эти напряжения находятся в пределах 200–350 МПа [1]. Высокотемпературная механическая обработка (ВТМО) давлением, способствует формированию регламентированной структуры, позволяет повысить не только механические свойства аустенитной (B2) фазы, но и силовые термомеханические (примерно в 2 раза) характеристики сплавов на основе никелида титана. Следовательно, отработка соответствующих режимов ВТМО представляет определенный практический интерес.
Установлено, что полуфабрикаты из сплавов типа “нитинол” после прокатки или прессования в интервале температур 150–1050°С обладают высокой пластичностью и способны выдерживать значительную деформацию без изменения термомеханических характеристик [2]. Следовательно, для изготовления полуфабрикатов типа втулок или трубных заготовок целесообразно применение таких способов переработки как горячая высадка, выдавливание, поперечно-винтовая прокатка и т.д.
На рис. 1а, б проиллюстрирована технологическая пластичность сплавов TH1-K (Ni – 54.8%, Тi – 42.0%, Fe – 3.2%) [3] в виде кривых сопротивления деформации сжатием в зависимости от температуры и скорости деформирования. Согласно анализу полученных данных видно, что эти диаграммы имеют характерный вид кривых насыщения с максимумом; при этом величина напряжений определяется температурой и скоростью деформирования. При заданных режимах ВТМО эти напряжения стабилизируются и приобретают значения установившегося процесса горячей деформации, при котором скорость деформационного упрочнения совпадает со скоростью температурного разупрочнения. Таким образом, для сплавов типа TH1 и THI-K установившаяся стадия горячей деформации в рекомендуемом диапазоне скоростей наблюдается в широком интервале температур 700–1000°С.
Рис. 1.
Влияние температуры и скорости деформирования на технологичную пластичность сплава ТН1-К при сжатии: (а) – $\varepsilon '$ = 0.1 с–1; (б) – $\varepsilon '$ = 0.5 c–1. 1 – t = 600°C; 2 – 700°C; 3 – 800°C; 4 – 900°C; 5 – 1000°C; 6 – 1050°C.
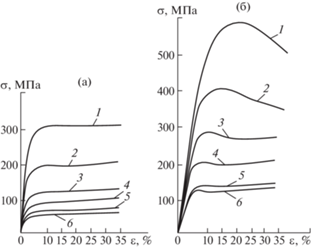
Результаты экспериментальных исследований технологической пластичности сплава ТН1-К при сжатием в зависимости от температуры и скорости деформирования представлена в табл. 1.
Таблица 1.
Максимальное (σmax) и установившееся (σуст) напряжение процесса при сжатии образцов из сплава ТН1-К (Ni – 54.8%, Тi – 42.0%, Fe –3.2%) в зависимости от температуры t,°C и скорости деформирования $\varepsilon '$
№ п/п | $\varepsilon '$, с–1 | t,°C | 600 | 700 | 800 | 900 | 1000 | 1150 |
---|---|---|---|---|---|---|---|---|
1 | 0.1 | σmax, МПа | 306 | 198 | 120 | 89 | 67 | 56 |
σуст, МПа | 306 | 198 | 120 | 89 | 67 | 56 | ||
2 | 0.5 | σmax, МПа | 600 | 408 | 288 | 206 | 136 | 127 |
σуст, МПа | – | 350 | 268 | 198 | 134 | 125 |
Установлено, что в зависимости от температуры при заданной скорости деформирования формируются различные виды структур зерна. Так высокие температуры способствуют образованию динамически рекристаллизованных зерен с размерами 3‒4 мкм. Деформация в интервале температур от 700–850°С приводит к формированию динамически полипонизованной субструктуры с зернами размерами около 2 мкм с мало и среднеугловой разориентированности. Для интервала температур 500–700°С характерна субструктура ячеистости с повышенной плотностью дефектов.
Влияние режимов ВТМО на механические свойства В2 фазы [4] и развиваемую величину реактивных напряжений σR (генерируемых при нагреве предварительно сформированного материала растяжением на 8%) в условиях абсолютно жесткого противодействия, представлено на диаграммах на рис. 2.
Рис. 2.
Влияние температур ВТМО сплава на механические (1– σв; 2 – σ0.2; 3 – δ) характеристики В2 фазы и величину напряжений термомеханического возврата σR при восстановлении в условиях абсолютно жесткого противодействия после деформации растяжением 8%.
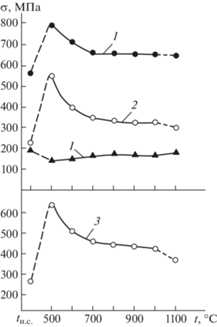
Приведенные данные констатируют, что максимум упрочнения В2 фазы наблюдается после ВТМО при температурах 500–600°С. На данных режимах обработки (рис. 2, нижняя диаграмма), реализуется повышение генерируемых напряжений σR более чем в 2 раза.
Установлено, что в регламентируемых пределах ВТМО величина объема памяти формы для сплавов на основе никелида титана остается как у исходного материала и определяется от вида (растяжение, сжатие, кручение или их комбинация) производимой деформации.
Высокая стоимость муфт из сплава с ЭПФ из прутков определяется не только исходной ценой никелида титана, но и значительной трудоемкостью при изготовлении механической обработкой. В связи с плохой обрабатываемостью [5], основную трудоемкость составляет сверление. Низкий коэффициент использования материала (КИМ) определяется тем, что основная часть материала при сверлении уходит в стружку.
Освоение прогрессивных технологий получение пустотелых заготовок является настоятельной практической необходимостью. При изготовлении полуфабрикатов типа “стакан” эффективно применение процесса обратного выдавливания, технологическая схема которого представлена на рис. 3 [6].
Рис. 3.
Технологическая схема процесса обратного выдавливания: 1 – пуансон, 2 – направляющая, 3 – матрица, 4 – заготовка, 5 – вкладыш.
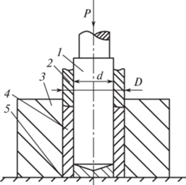
Производство пустотелых заготовок с максимально приближенными геометрическими размерами позволяет не только значительно повысить КИМ, исключить трудновыполнимую операцию сверления отверстия, но и сформировать благоприятную структуру материала с повышенными термомеханическими характеристиками.
При обратном выдавливании металл заготовки 4 течет навстречу пуансону 1 в кольцевой зазор между пуансоном и матрицей 3. Толщина стяжки получаемых заготовок составляет 3–5 мм при отношении ее длины к диаметру не более 4-х. Точность изготовления размеров и шероховатость поверхностей такие же как и при обработке резанием.
Предварительно мерная заготовка протачивается по наружной поверхности для удаления дефектного слоя. Процесс обратного выдавливания реализуется в изотермических условиях, для чего цилиндрическая заготовка, направляющая и пуансон нагреваются в матрице до температуры 850°С. Кратковременность индукционного нагрева в значительной степени влияет не только на качество поверхности деформируемого материала, но и значительно повышает стойкость деформирующего инструмента.
Расчетное усилие, необходимое для формообразования определяется соотношением
где D, d – наружный и внутренний диаметры заготовки; q – удельное усилие деформирования.С достаточной для практического применения точностью удельное усилие можно считать равным напряжению установившегося процесса деформации В2 фазы. Согласно рис. 1 при температуре t = 800°С и скорости деформации $\varepsilon '$ = 0.1 c–1; σуст = 120 МПа.
Так для заготовок с D = 16.5 и d = 10.5 мм расчетное значение усилия составляет P = = 5.2 Кн. Для сравнения, экспериментальные значения находятся в пределах 12.5–13.8 Кн.
На данных режимах пластической деформации методом обратного выдавливания для муфт из сплава с ЭПФ была изготовлена опытная партия заготовок двух типоразмеров. На рис. 4 представлена фотография поперечного сечения заготовки из сплава ТН1-К с наружным диаметром 36 мм. Отметим, что при обратном выдавливании КИМ повышается от 0.65 до 0.8, а физико-механические характеристики материала (рис. 2) на указанных режимах обработки практично не меняются, при этом реактивные напряжения при растяжении возрастают до σR = 450 МПа.
Контрольные испытания кольцевых образцов одного типоразмера из исходного материала и из пустотелых стаканов на усилия при страгивании показали, что температура мартенситных напряжений практически не отличается, а усилие страгивания из исходного материала примерно на 80% ниже [7].
Анализ микроструктуры полуфабрикатов муфт показал на некоторую ее неоднородность по сечению. Так в верхней части заготовки отмечается текстура вытянутых зерен в направлении вектора усилия деформации, средняя часть характеризуется слабо выраженными границами деформирования, а донная часть – четкостью границ зерен с полосчатым рельефом, как и в структуре исходного горячекатаного прутка.
Качество формования заготовок определяет соответствие заданным размерам при отсутствии внутренних и внешних дефектов в виде микротрещин, расслоений и структурных превращений материала, что подтверждается металлографическими и рентгеноструктурными исследованиями. При контроле ультразвуковым и люминесцентным методами дефектов в виде трещин, волосовин и расслоений на поверхностях заготовок не обнаружено.
Для создания направленной субструктуры горячего наклепа материала при скорости деформации $\varepsilon '$ = 0.4–0.5 с–1 и температуре 600–650°С с целью повышения напряжений термомеханического возврата σR осуществляется обжатие заготовок со степенью деформации 0.3–0.5.
Схематически технологическая схема обжима представлена на рис. 5.
Рис. 5.
Схема ВТМО при обжиме заготовки: 1 – заготовка после обратного выдавливания; 2 – матрица; 3 – пуансон-толкатель.
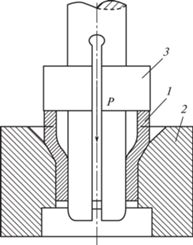
Разработанные режимы процесса обратного выдавливания заготовок из никелида титана применимы для мелкосерийного производства.
Метод характеризует более высокие механические свойства В2 фазы материала по сравнению с исходным состоянием, а также повышенной энергетикой при реализации термического формовосстановления.
Интервалы температур фазовых превращений (Мн, Мк – температуры начала и конца мартенситных превращений и Ан, Ак – температуры начала и конца аустенитных превращений) и объем полностью восстанавливаемой деформации в области мартенситной неупругости практически не меняются.
Список литературы
Lotkov A., Grishkov V., Timkin V., Baturin A., Zhapova D. Yield stress in titanium nickelide-based alloys with thermoelastic martensitic transformations // Materials Science and Engineering A. 2019. V. 744. P. 74.
Kajiwara S. Characteristic features of shape memory effect and related transformation behavior in Fe-based alloys // Materials Science and Engineering A-Structural Materials Properties Microstructure and Processing. 1999. V. 273. P. 67. https://doi.org/10.1016/S0921-5093(99)00290-7
Khasyanova D.U. Technological support for the quality of manufacturing TMS couplings and assembly of pipelines. Thesis for the competition. Uch. Step. Cand. Science. Moscow: MGUPI, 2012. 115 p.
Khasyanova D.U. Improving the Reliability of Permanent Pipeline Connections by Using the Shape Memory Effect in Thermomechanical Couplings // J. Mach. Manuf. Reliab. 2019. V. 48. P. 88. https://doi.org/10.3103/S1052618819010096
Khasyanova D.U. Peculiar features of welding and brazing of alloys with shape memory // J. Mach. Manuf. Reliab. 2021. V. 50. P. 143. https://doi.org/10.3103/S1052618821020084
Lotkov A.I., Meisner L.L., Grishkov V.N. Titanium nickelide-based alloys: Surface modification with ion beams, plasma flows, and chemical treatment // Physics of Metals and Metallography. 2005. V. 99 (5). P. 508.
Shishkin S.V., Makhutov N.A. Calculation and design of power structures on alloys with shape memory effect. Regular and chaotic dynamics. M.: SIC, 2007. 412 p.
Дополнительные материалы отсутствуют.
Инструменты
Проблемы машиностроения и надежности машин