Проблемы машиностроения и надежности машин, 2022, № 4, стр. 21-27
Влияние параметров вибрации при электроосаждении композиционных покрытий Ni–SiC из вибрационно-стабилизированной суспензии
А. В. Красиков 1, 2, М. А. Марков 1, 2, В. Л. Красиков 2, И. Н. Кравченко 3, *, М. В. Старицын 1, А. Д. Быкова 1, 2, А. Н. Беляков 1, 2
1 НИЦ “Курчатовский институт” – ЦНИИ КМ “Прометей”
Санкт-Петербург, Россия
2 Санкт-Петербургский государственный технологический институт (технический университет)
Санкт-Петербург, Россия
3 Институт машиноведения им. А.А. Благонравова РАН
Москва, Россия
* E-mail: kravchenko-in71@yandex.ru
Поступила в редакцию 01.03.2022
После доработки 03.04.2022
Принята к публикации 20.04.2022
- EDN: NZBWRK
- DOI: 10.31857/S0235711922040113
Аннотация
Исследовано влияние параметров вибрации на электросаждение композиционного покрытия Ni–SiC из вибрационно-стабилизированной суспензии. Показано, что повышение частоты вибрации приводит к снижению объемной доли включений карбида кремния и небольшому повышению выхода по току. Увеличение амплитуды колебаний увеличивает объемную долю SiC в композиционном покрытии, однако при этом покрытие становится неоднородным и на различных участках образцов осаждается различное количество частиц карбида кремния. На основании проведенных исследований рекомендован режим вибрации для осаждения покрытия Ni–SiC c равномерным распределением частиц карбида кремния.
В настоящее время получение композиционных электрохимических покрытий (КЭП) прямым соосаждением превратилась в самостоятельную область гальванотехники. Для решения задач создания композиционных покрытий, обладающих и коррозионной стойкостью и износостойкостью, необходимо рассматривать не только системы металл–включения, исследуя влияние их природы на эксплуатационные свойства, но и технологию синтеза композиционных слоев.
Среди многих условий, влияющих на свойства покрытий и структуру металлической матрицы, фигурирует такой параметр, как размер частиц твердой фазы, внедренной в металлокерамическое покрытие. При переходе от наноразмерных частиц карбида кремния (50 нм) к субмикронным (500 нм) измельчается размер зерна никелевой матрицы и возрастает микротвердость [1]. Однако, каковы будут свойства покрытия при микронном размере частиц, остается неясным, потому что получать такие покрытия затруднительно. Проблема состоит в том, что при размере частиц порошка, введенного в электролит в 3–7 мкм поддерживать агрегативную устойчивость за счет добавления ПАВ становится практически невозможным.
Поэтому для электроосаждения КЭП из электролитов-суспензий с крупным размером частиц важнейшей проблемой является поддержание агрегативной устойчивости. Для ее решения существует несколько принципиальных подходов, таких как ультразвуковое перемешивание [2, 3], использование ротационных мешалок [4], вращение покрываемой детали [5, 6], вибрация [7], проточное [8] и струйное осаждение [9, 10]. Однако все эти методы применялись по отношению к мелкодисперсным порошкам, взвешенным в электролите. Задача по стабилизации электролитов-суспензий с размером частиц в несколько микрометров и больше практически не рассматривалась. Решение этой задачи по отношению к электролиту с крупными частицами порошка позволило бы обойти непростую задачу по обеспечению доставки частиц к растущему покрытию. Миграция таких частиц под действием электрического поля в электролизере настолько слаба, что доставка твердой фазы к катоду может осуществляться только за счет конвекции. С одной стороны, это можно считать недостатком, но с другой, при использовании правильно выбранных методов доставки частиц, избавляет технологов от необходимости учитывать ионную силу электролита и значение ζ-потенциала. Как следствие, при обеспечении конвекции появляется возможность работать с любыми электролитами, с теми концентрациями и рН, которые удобны технологам. При этом возникает задача обеспечения такого гидродинамического режима, который обеспечивает равномерную доставку частиц армирующей фазы и одновременно позволяет закрепиться им на поверхности покрытия.
Наиболее перспективным методом стабилизации суспензии является вибрационный метод, который позволяет формировать взвеси крупных частиц в электролите с высокой ионной силой и одновременно обеспечивает их доставку к поверхности детали. Однако вопрос о влиянии параметров вибрации на процесс соосаждения микрометровых частиц с металлом остается открытым.
Целью статьи является исследование влияния параметров вибрации на основные свойства композиционных покрытий на примере системы Ni–SiC. Данный вид КЭП нашел практическое применение в автомобильных двигателях [11] и обладает высокой износостойкостью.
Методика исследований. Для исследований использовали стандартный сульфатный электролит (ванна Уоттса) состава NiSO4·7H2O – 250 г/л, NaCl – 10 г/л, H3BO3 – 30 г/л. Для приготовления электролита использовали реактивы с чистотой не ниже “чда” и дистиллированную воду. В электролит было введено 50 г/л карбида кремния модификации 6H размера М5. После введения порошка электролит-суспензию облучали ультразвуком в течение 20 мин, помещая ячейку с электролитом в ультразвуковую ванну ПСБ-4035. После обработки ультразвуком рН электролита смещался в кислую сторону, что было вызвано разрушением агломератов карбида кремния и обновлением поверхности. Поэтому рН корректировали и снова подвергали электролит воздействию ультразвука, после чего снова проверяли рН. При необходимости цикл повторяли. Эксперимент проводили при рН = 2.3.
Образцы для осаждения покрытий изготавливали из медной полосы марки М0 толщиной 0.2 мм. Рабочая часть образцов имела размер 15 × 30 мм. Перед осаждением образцы шлифовали и подвергали стандартной подготовке поверхности по ГОСТ 9.305, т.е. электрохимическому обезжириванию в катодном режиме и химической активации в растворе серной кислоты при комнатной температуре.
Для формирования взвеси частиц в электролите возле дна ванны была расположена вибрирующая площадка с массивом конических отверстий, выполненная из полимера АБС, приводимая в движение вибростендом TiraVib под управлением низкочастотного источника сигналов Г3-112/1. Частота колебаний площадки составляла 50 Гц, амплитуду колебаний регулировали в диапазоне 1–3 мм. Электроосаждение проводили при фиксированной плотности тока 2 А/дм2. Схема установки и расположения образцов в ванне приведены на рис. 1.
Рис. 1.
Схемы: (а) – установка для получения образцов композиционных покрытий; (б) – расположение образца в ванне, вид сверху.
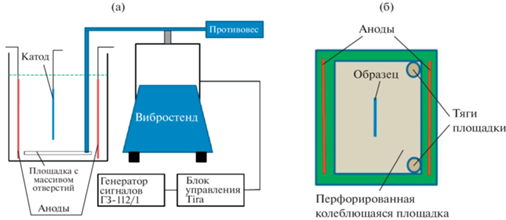
Исследование гранулометрического состава порошка карбида кремния проводили на установке MalvernMastersizer 2000, фазовый анализ покрытий на дифрактометреRigakuUltimaIV. Анализ проводился по базе данных PDF 2 (ICDD). Металлографические исследования проводили на растровом электронном микроскопе TescanVega3. Количество включений в покрытии оценивали с помощью специализированного программного обеспечения IncaFeatures. Для этого измеряли содержание SiC по восьми зонам в различных областях образца. Сходимость результатов измерений, за исключением особо оговоренного случая, составляла ±1.6 об.%. Микротвердость покрытия определяли на микротвердомере ПМТ-3М, при нагрузках 30, 40 и 50 г, выбранных по ГОСТ 9450.
Результаты и обсуждение. При электроосаждении композиционного покрытия Ni–SiC в условиях вибрационно-стабилизированной суспензии формируются матовые серые покрытия. Поэлементное картирование (рис. 2, 3) показывает, что участки с повышенным содержанием углерода соответствуют таковым для повышенного содержания кремния. Примесей кислорода при анализе химического состава покрытий не наблюдается, т.е. все включения являются карбидом кремния. С повышением частоты колебаний вибрирующей площадки наблюдается существенное снижение плотности распределения частиц SiC в композиционном покрытии.
Более детальные исследования влияния частоты колебаний на количество включенного в покрытие карбида кремния (рис. 4а), с ростом частоты происходит планомерное снижение объемной доли армирующих частиц. Так, в покрытии, осажденном при частоте колебаний 10 Гц, объемная доля SiC составила 26%, а при 100 Гц снизилась до 13%. Это соответствует наблюдениям в работе [12], в соответствии с которыми количество включений снижается с увеличением энергии вибрации.
Рис. 4.
Влияние частоты колебаний на объемное содержание карбида кремния (а) и выход по току композиционного покрытия (б).
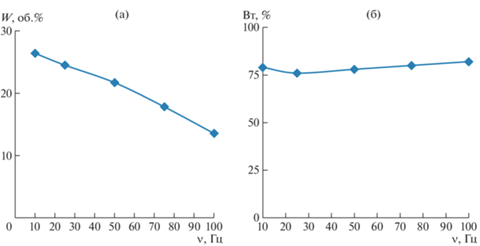
Выход по току полученных композиционных покрытий ниже, чем для классических никелевых и в исследованном диапазоне частот колебаний не превышает 82%, что обусловлено весьма низкой величиной рН. При этом наблюдается слабая зависимость выхода по току композита от частоты колебаний (рис. 4б), согласно которой при повышении частоты выход по току несколько растет.
Очевидно, что выход по току в случае осаждения КЭП складывается из двух составляющих: фарадеевского процесса осаждения никелевой матрицы и включения частиц SiC. С одной стороны, самой очевидной причиной такого поведения системы может быть формирование диффузионного барьера из частиц карбида кремния в прикатодном слое электролита. Формирование подобных пленок вызывает существенное торможение катодных процессов [13, 14], что способствует обогащению растущего покрытия дисперсной фазой. Повышение частоты колебаний, по-видимому, приводит к снижению плотности адсорбционной пленки из карбида кремния и ослабляет диффузионный барьер, увеличивая выход по току.
Микротвердость покрытия также зависит от частоты колебаний и снижается при ее увеличении (рис. 5). Вероятно, это обусловлено ниспадающей зависимостью объемной доли SiC от частоты. Подтверждением этого является зависимость микротвердости покрытия от содержания карбида кремния, которая в изученном диапазоне составов покрытия практически линейна (рис. 6).
Изменение амплитуды колебаний неоднозначно влияет на скорость формирования покрытий. Выход по току покрытия при слишком высокой амплитуде 3 мм весьма низок для ванны Уоттса и составляет 69% (рис. 7а). Вероятно, при таких условиях скорость движения потоков электролита становится настолько велика, что покрытие подвергается воздействию абразивных частиц [15]. Кроме того, высокая скорость движения электролита затрудняет фиксацию частиц SiC на поверхности растущего никеля, что снижает прирост массы образца во время электролиза. Исследование содержания карбида кремния в покрытии с обеих сторон образцов показало, что с увеличением амплитуды колебаний появляется разница между количеством SiC, внедренного в никелевую матрицу на разных поверхностях образцов. Этот разброс существенно увеличивается с возрастанием амплитуды (рис. 7б). Очевидно, что данное явление зависит от геометрии ванны и покрываемой детали, расположения образца относительно дна ванны и других факторов, оказывающих влияние на гидродинамические потоки. Поэтому, несмотря на то, что повышение амплитуды колебаний позволяет локально увеличить содержание включений SiC, обеспечивать равномерность распределения армирующей фазы в таких условиях затруднительно. Соответственно, превышение амплитуды колебаний величины в 1 мм нежелательно.
Рис. 7.
Влияние амплитуды колебаний на выход по току покрытия (а) и объемное содержание в нем карбида кремния (б) при частоте 50 Гц.
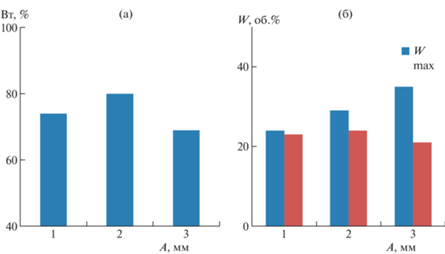
На основании полученных результатов можно констатировать, что параметры вибрации оказывают существенное влияние как на состав композиционного покрытия, так и на его свойства. Для получения покрытий с равномерным распределением SiC и высокой объемной долей оптимальным режимом является частота 10–25 Гц и амплитуда не более 1 мм, что обеспечивает микротвердость композиционного покрытия 780 HV.
Выводы. 1. Исследовано влияние частоты вибрации при осаждении композиционного покрытия Ni–SiC. Установлено, что повышение частоты приводит к обеднению покрытия упрочняющей карбидокремниевой фазой. 2. Оценено влияние амплитуды колебаний на состав, структуру и выход по току композиционного покрытия. Показано, что увеличение амплитуды приводит к возникновению неконтролируемых направленных потоков электролита-суспензии, что значительно увеличивает разброс содержания SiC на различных участках покрытия. 3. Установлено, что повышение частоты колебаний вызывает снижение микротвердости покрытий, что связано со снижением содержания SiC. 4. Обоснован оптимальный режим осаждения покрытия Ni‒SiC, обеспечивающий высокую однородность распределения упрочняющих частиц. Микротвердость покрытия составляет 780 HV.
Список литературы
Pinate S., Ispas A., Leisner P., Zanella C. Electrocodeposition of Ni composites and surface treatment of SiC nano-particles // Surface & Coatings Technology. 2021. V. 406. https://doi.org/10.1016/j.surfcoat.2020.126663
Tudela I., Zhang Y., Pal M., Kerr I., Cobley A. Ultrasound-assisted electrodeposition of composite coatings with particles // Surface and Coatings Technology. 2014. V. 259. Part C. P. 363.
Nath P., Sahu D.K., Mallik A. Physicochemical and corrosion properties of sono-electrodeposited Cu-Ni thin films // Surface and Coatings Technology. 2016. V. 307. Part A. P. 772.
Muralidhara H.B., Nayake Y.A., Balasubramanyam J., Kumar K.Y., Hanumanthappa H., Veena M.S. Electrodeposition of Zn-Graphite nanoparticles composite and their characterization // J. Chem. Pharm. Res. 2012. V. 4. P. 440.
Maurin G., Lavanant A. Electrodeposition of nickel/silicon carbide composite coatings on a rotating disc electrode // Journal of applied electrochemistry. 1995. V. 25. P. 1113.
Badarulzaman N.A., Purwadaria S., Mohamad A.A., Ahmad Z.A. The production of nickel–alumina composite coatingvia electroplating // Ionics 2009. V. 15. P. 603.
Johal C.P.S., Kalantary M.R., Gabe D.R. Vibratory agitation for electrodeposition: Ill electrodeposition of composites // Trans IMF. 1989. V. 67. P. 31.
Lapinski J., Pletcher D., Walsh F.C. The electrodeposition of nickel–graphite composite layers // Surface and Coatings Technology.2011. V. 205. Iss. 21–22. P. 5205.
Osborne S.J., Sweet W.S., Vecchio K.S., Talbot J.B. Electroplating of Copper–Alumina Nanocomposite Films with anImpinging Jet Electrode // Journal of the Electrochemical Society. 2007. V. 154. № 8. P. D394.
Thiemig D., Bund A. Talbot J.B. Electrocodeposition of Nickel Nanocomposites Using an Impinging Jet Electrode // Journal of The Electrochemical Society. 2007. V. 154. № 10. P. D510.
Walsh F.C., Ponce de Leon C. A review of the electrodeposition of metal matrix composite coatings by inclusion of particles in a metal layer: an established and diversifying technology // Transactions of the IMF. 2014. V. 92. № 2. P. 83.
White C., Foster J. A Study of Particle-Cathode Adhesion during the Formation of Electrodeposited Composite Coatings // Transactions of the IMF. 1978. V. 56. Iss. 1. P. 92.
Krasikov A.V., Krasikov V.L. Effect of the Composition of Pyrophosphate Electrolyte on the Kinetics of Cobalt Electrodeposition // Russian journal of applied chemistry. 2009. V. 82. № 5. P. 792.
Красиков В.Л., Александрова Г.С. Особенности катодного выделения водорода из слабокислых растворов, содержащих соль алюминия // Известия СПбГТИ(ТУ). 2012. № 17 (43). С. 31.
Dabholkar A., Sundaram M.M. Mathematical Model for Abrasive Content Estimation in a Pulse-Electroplated Abrasive Microtool // Journal of Manufacturing Processes. 2012. V. 14. Iss. 3. P. 366.
Дополнительные материалы отсутствуют.
Инструменты
Проблемы машиностроения и надежности машин