Проблемы машиностроения и надежности машин, 2022, № 5, стр. 105-112
Температурная стойкость пластичных смазочных материалов, загущенных сульфонатами кальция
В. Д. Самусенко 1, *, С. С. Стрельникова 1, А. В. Песковец 2, И. А. Буяновский 1, И. Р. Татур 2, О. А. Кальянова 2
1 Институт машиноведения им. А.А. Благонравова РАН
Москва, Россия
2 Российский государственный университет нефти и газа им. И.М. Губкина
Москва, Россия
* E-mail: samusenkovd@gmail.com
Поступила в редакцию 02.04.2022
После доработки 14.05.2022
Принята к публикации 21.06.2022
- EDN: PTIVLA
- DOI: 10.31857/S0235711922050145
Аннотация
Приведены результаты температурных испытаний пластичных смазочных материалов, приготовленных на основе сульфонатов кальция. Для приготовления смазок использовались загустители с разным щелочным числом и базовые масла, отличающиеся по структурно-групповому составу. Испытанные смазки показали схожую динамику изменения коэффициента трения от температуры, что связано с идентичным механизмом действия сульфонатного загустителя при образовании модифицированного поверхностного слоя. Оптимальным сочетанием физико-химических и трибологических свойств обладают образцы с загустителем С-300 “А” и дисперсионными средами – маслами VHVI-4 и С-9.
Существующие тенденции развития науки и техники ставят перед специалистами в области трибологии и химмотологии задачу обеспечить ресурсо- и энергосбережение при функционировании смазываемых тяжелонагруженных узлов трения современных машин и механизмов. Это можно достигнуть путем снижения энергетических потерь и повышения износостойкости сопряженных деталей при трении, т.е. повышения как антифрикционных, так и противоизносных свойств используемых смазочных материалов применительно к конкретным сопряжениям трущихся тел при обязательном учете соблюдения экологических требований [1, 2].
Как известно, в тех случаях, когда сложно обеспечить герметичность узлов трения или необходимо уменьшить расход смазочного материала вплоть до одноразовой его закладки в узел трения для обеспечения всего ресурса его работы, целесообразно применение пластичных смазок. Пластичные смазки представляют собой густой мазеобразный продукт, состоящий из дисперсионной среды (масла) и дисперсной фазы (загустителя). Сульфонатные смазки представляют особенный интерес, т.к. обладают хорошими исходными (обусловленными составом загустителя) противоизносными и противозадирными свойствами.
По современным представлениям [3, 4] основу сульфонатных смазок составляют мицеллярные структуры. Ядро мицеллы – карбонат кальция – может существовать в трех полиморфных модификациях: фатерит, арагонит и кальцит. Во время приготовления смазки необходимо образование именно кальцита для достижения наилучших характеристик, поэтому важно особое внимание уделять технологии приготовления смазочного материала [5]. Кристаллический кальцит, состоящий из ультратонких слоев с относительно большой площадью поверхности, будучи поверхностно активным, покрывает поверхность трения. Затем адсорбированный сульфонат кальция создает сульфонатные цепи, ориентированные перпендикулярно поверхности раздела [6]. Поэтому для смазок, загущенных сульфонатами кальция, характерны отличные противозадирные и противоизносные свойства [7–9], из-за чего отпадает необходимость добавления присадок трибологического назначения, содержащих серу, фосфор, цинк и др., что снижает токсичность получаемого смазочного материала. Кроме того, такие смазки являются хорошими ингибиторами коррозии, а также отличаются повышенной стабильностью к действию воды и даже способны до определенного предела поглощать ее, не меняя своих свойств, что делает возможным их применение в оборудовании, работающем при контакте с водой [10–12]. Таким образом, сульфонатные смазки могут найти применение во многих отраслях промышленности: автомобильная, сельскохозяйственная, строительная, пищевая, горнодобывающая, бумагоделательная, а также в металлургии.
Цель статьи – оценка влияния загустителя и дисперсионной среды сульфонатных пластичных смазочных материалов на температурную стойкость граничных смазочных слоев при трении.
Материалы и методы. Для исследования взяты образцы сульфонатных смазок, приготовленные на загустителях с разным уровнем щелочного числа: сульфонат кальция марки КНД-150 “А” (ТУ 38.1011283-2004), высокощелочной сульфонат кальция С-300 “А” (ТУ 38.301-19-115-99) и синтетический сульфонат кальция ССК-400D (ТУ BY 390401182.022-2011). В качестве дисперсионной среды использовали масло изопарафиновое VHVI-4 (ТУ 38.401-58-415-2014).
Для изучения влияния дисперсионной среды на исследуемые показатели дополнительно приготовлены образцы на следующих дисперсионных средах: масло для производства химических волокон С-9 (ТУ 38-1-01-33-70) с содержанием ароматических углеводородов 20%, полиальфаолефиновое масло ПАО-4 (ТУ 0253-014-54409843-2007), полиалкилбензол марки ПАБ-С (ТУ 2414-025-05766480-2006). В качестве загустителя для этих смазок использовали сульфонат кальция марки С-300 “А”.
В табл. 1 приведены физико-химические характеристики использованных загустителей, а в табл. 2 физико-химические характеристики использованных дисперсионных сред.
Таблица 1.
Физико-химические свойства загустителей
Наименование показателя | КНД-150 “А” | С-300 “А” | ССК-400D |
---|---|---|---|
Вязкость кинематическая при 100°С, мм2/с | 56.8 | 73.3 | 94.4 |
Щелочное число, мг КОН на 1 г продукта | 132.6 | 288.6 | 404.2 |
Массовая доля сульфоната кальция, % | 31 | 31.3 | 31 |
Таблица 2.
Физико-химические свойства дисперсионных сред
Наименование показателя | VHVI-4 | С-9 | ПАО-4 | ПАБ-С |
---|---|---|---|---|
Плотность при 20°С, кг/м3 | 826 | 865 | 818 | 873 |
Вязкость кинематическая при 100°С, мм2/с | 4.4 | 2.7 | 4.1 | 4.33 |
Температура вспышки в открытом тигле, °С | 224 | 150 | 219 | 207 |
Температура застывания, °С | –23 | –48 | –61 | –42 |
Для трибологической оценки приготовленных образцов смазочных материалов использовался температурный метод оценки смазочной способности по ГОСТ 23.221-84 на четырехшариковой машине КТ-2, в которой реализована низкая скорость относительного перемещения трущихся тел (0.24 мм/с), что практически устраняет фрикционный нагрев, а температура в узле трения задается от внешнего источника тепла [13]. Исследование проводили в диапазоне температур 30–300°C. Температура узла трения ступенчато повышалась со скоростью ~4°C в минуту. Коэффициент трения оценивался в течение 60 с через каждые 10°С. Осевая нагрузка на узел трения составляла 108.4 Н (т.е. контактная нагрузка на один шар была равна 44.2 Н, а давление в контакте верхнего и каждого из нижних шариков (по Герцу) составляет примерно 2 ГПа). Частота вращения шпинделя установки составляла 1 мин–1. Для испытаний использовали стандартные подшипниковые шарики из стали 100Cr6 (аналог отечественной стали ШХ15) диаметром 7.94 мм. В качестве регистрируемых параметров выступали температура смазочного материала и значение момента трения, на основе которого определяли коэффициент трения.
Проводилось по три повторных испытания с каждым смазочным материалом, по средним значениям которых, строились зависимости коэффициента трения от температуры.
Результаты и их обсуждение. Все сульфонатные смазки приготовлены по технологии, разработанной на кафедре химии и технологии смазочных материалов и химмотологии РГУ нефти и газа (НИУ) имени И.М. Губкина [5]. Содержание загустителя в испытуемых образцах составляет 67% масс. Основные физико-химические характеристики образцов приведены в табл. 3.
Таблица 3.
Основные физико-химические свойства исследуемых сульфонатных смазок
Наименование показателя | Загуститель КНД-150 “А”, масло VHVI-4 № 1 |
Загуститель С-300 “А”, масло VHVI-4 № 2 |
Загуститель CСK-400D, масло VHVI-4 № 3 |
Загуститель С-300 “А”, масло С-9 № 4 |
Загуститель С-300 “А”, масло ПАО-4 № 5 |
Загуститель С-300 “А”, масло ПАБ-С № 6 |
---|---|---|---|---|---|---|
Температура каплепадения (ГОСТ 6793-74), °С | 235 | >250 | >250 | >250 | >250 | >250 |
Коллоидная стабильность (ГОСТ 7142-74), % масс | 0.57 | 0.49 | 0.29 | 0.33 | 0.23 | 0.36 |
Предел прочности при 20°С (ГОСТ 7143-73, метод Б), Па | 155 | 1260 | 870 | 1060 | 1280 | 1640 |
Эффективная вязкость при 20°С (ГОСТ 7163-84), Па · с | 60 | 844 | 573 | 620 | 620 | 592 |
Анализ результатов (табл. 3) позволяет заключить, что все исследуемые образцы сульфонатных смазок обладают высоким уровнем эксплуатационных характеристик. Сульфонатная смазка № 1 имеет невысокие, по сравнению с другими образцами, значения предела прочности и эффективной вязкости, что объясняется отсутствием в загустителе КНД-150 “А” достаточного количества карбоната кальция для формирования прочной структуры (сульфонаты кальция с большим щелочным числом содержат больше карбоната кальция [14]).
Среди смазок, приготовленных на базе масла VHVI-4 с разными загустителями, оптимальными свойствами обладает образец № 2, у других образцов предел прочности и эффективная вязкость значительно ниже.
Результаты трибологических испытаний всех шести сравниваемых сульфонатных смазок в виде зависимостей коэффициентов трения от температуры приведены на рис. 1. Все испытанные образцы смазочных материалов имеют в общих чертах похожую динамику изменения коэффициента трения от температуры.
Рис. 1.
Зависимости коэффициента трения от температуры сульфонатных смазок: (а) – смазки на масле VHVI-4 с разными загустителями; (б) – смазки с загустителем С-300 “А” на разных маслах. Образцы смазок: 1 – загуститель КНД-150 “А”, масло VHVI-4; 2 – загуститель С-300 “А”, масло VHVI-4; 3 – загуститель CСK-400D, масло VHVI-4; 4 – загуститель С-300 “А”, масло С-9; 5 – загуститель С-300 “А”, масло ПАО-4; 6 – загуститель С-300 “А”, масло ПАБ-С.
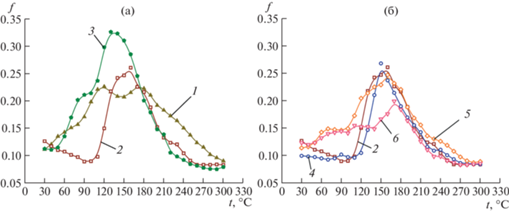
На начальном этапе с повышением температуры происходит разрушение адсорбционного граничного слоя, интенсивность разрушения которого зависит от содержания в смазках поверхностно активных веществ и их способности образовывать прочный граничный смазочный слой на поверхностях трения. В результате дезориентации молекул смазочной среды, образующих граничный слой, и разрушения этого слоя происходит увеличение доли металлического контакта по вершинам неровностей контактирующих тел, что выражается в повышении коэффициента трения. Как загуститель, так и масло в составе смазки значительно влияют на антифрикционные свойства приготовленных образцов.
Начиная с температур 150–170°C, происходит снижение коэффициента трения, что, по-видимому, связано с началом образования на поверхности модифицированного слоя – на поверхностях трения происходит разложение сульфоната кальция, а образовавшийся при этом карбонат кальция высаживается на поверхностях трения, уменьшая участок металлического контакта трущихся тел, что будет снижать коэффициент трения. Далее, по мере повышения температуры все большая доля поверхности контакта покрывается образующимся модифицированным слоем и все меньше становится коэффициент трения. Повышение температуры не только увеличивает скорость образования этого слоя, но и повышает скорость его изнашивания до тех пор, пока не установится равновесие между процессами образования и изнашивания модифицированного слоя, что выражается в стабилизации коэффициента трения на уровне 0.08–0.09.
Идентичное снижение коэффициента трения при образовании модифицированного слоя говорит об одинаковом механизме образования антифрикционного слоя на поверхности. При испытании образца смазки № 1 с меньшим содержанием карбоната кальция, соответственно образование модифицированного слоя происходит менее интенсивно, что выражается в более высоком коэффициенте трения.
В исследуемом интервале температур не была достигнута характерная температура, при которой скорость изнашивания модифицированного слоя превосходит скорость его образования, вследствие чего резко увеличится коэффициент трения.
В табл. 4 приведены значения переходных температур – Tкр (минимальная температура, при которой происходит разрушение смазочного слоя) и Tхм (минимальная температура, при которой происходит эффективное прекращение заедания вследствие образования на поверхностях трения модифицированного слоя, обладающего пониженным сопротивлением сдвигу).
Таблица 4.
Переходные температуры
Переходные температуры | Образцы смазок | |||||
---|---|---|---|---|---|---|
1 | 2 | 3 | 4 | 5 | 6 | |
Tкр, °C | 80 | 110 | 50 | 120 | 100 | 140 |
Tхм, °C | 300 | 260 | 250 | 270 | 280 | 260 |
Для смазок № 2 и № 4 на загустителе С-300 “А” четко видна критическая температура перехода к резкому повышению коэффициента трения; для других образцов так четко выраженной критической температуры не наблюдалось, в основном коэффициент трения постепенно увеличивается, достигая своих максимальных значений. Характерно, что при испытаниях образцов смазок № 2 и № 4 кривые, приведенные на рис. 1б, практически сливаются друг с другом, в то время как коэффициенты трения других исследуемых смазок на начальных участках испытаний показали существенно более высокие значения.
На рис. 2 показаны фотографии пятен износа, показывающие изменение поверхности трения при испытании смазки № 2 в точках – до критической температуры, при которой начинает разрушаться адсорбционный слой, и происходит резкий рост коэффициента трения B; зона максимальных значений коэффициента трения C; температура, при которой на поверхности образовался модифицированный слой и происходит стабилизация коэффициента трения D, конец испытания E.
Рис. 2.
Зависимость коэффициента трения от температуры при испытании смазки № 2 (загуститель С-300 “А”, масло VHVI-4) и микрофотографии пятен износа при характерных температурах.
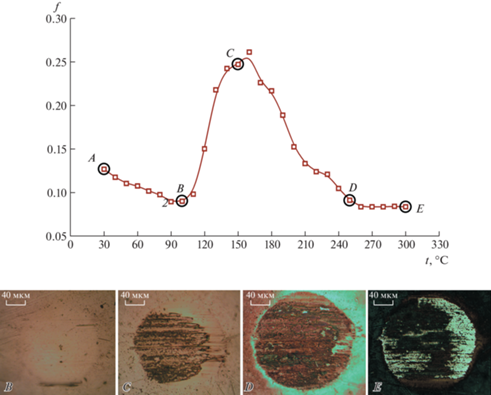
На рис. 3 приведены данные по износу образцов после испытания сульфонатных смазок до температуры 300°C, а на рис. 4 показаны фотографии пятен износа. Наибольший износ получен при испытании образцов № 1 и № 5, а наименьший износ получен при испытании образцов № 2 и № 4. Следует отметить, что разница по износу всех образцов не значительна, за счет небольшого пути трения при испытаниях. Сравнив данные по износу и зависимости коэффициента трения от температуры можно сделать предположение, что основной износ накапливается на начальном этапе испытаний до 150°C.
Рис. 3.
Гистограмма средних значений диаметров пятен износа при испытаниях сульфонатных смазок до 300°C (обозначение образцов смазок соответствует табл. 3).
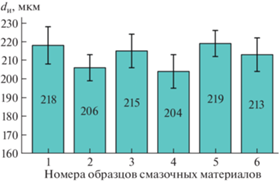
Рис. 4.
Микрофотографии пятен износа при испытаниях сульфонатных смазок до 300°C (обозначение образцов смазок соответствует табл. 3).
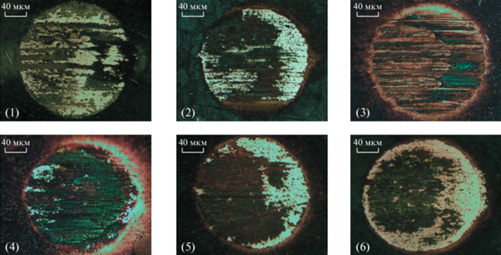
Заключение. Испытанные сульфонатные смазки показали в общих чертах схожую динамику изменения коэффициента трения от температуры. В диапазоне температур 30–160°С на коэффициент трения сульфонатных смазок влияет как дисперсионная среда, так и загуститель, компоненты которых способны образовывать на поверхности трения адсорбционный антифрикционный слой. При температурах свыше 160°С основное влияние на антифрикционные свойства смазок оказывает загуститель, что выражается в однообразном изменении коэффициента трения с повышением температуры. Из этого можно сделать вывод об идентичном механизме действия сульфонатного загустителя в исследуемых композициях. При 300°C коэффициенты трения практически одинаковы, что говорит об одной природе образовавшегося на поверхности трения модифицированного слоя карбоната кальция, вне зависимости от щелочного числа используемого загустителя и типа дисперсионной среды.
Сопоставив физико-химические характеристики исследуемых сульфонатных смазок и результаты испытаний по антифрикционному действию смазочных материалов и износу шариков можно сделать вывод, что среди испытанных образцов оптимальными свойствами обладают смазки, приготовленные на основе сульфоната кальция С-300 “А” и с дисперсионными средами VHVI-4 (№ 2) и С-9 (№ 4).
Список литературы
Евдокимов А.Ю., Фукс И.Г., Любинин И.А. Смазочные материалы в техносфере и биосфере. Экологический аспект. Киев: Атика-Н, 2012. 292 с.
Lugt P.M. Modern advancements in lubricating grease technology // Tribology international. 2016. T. 97. C. 467.
Mackwood W. Calcium sulfonate complex greases // Tribology & Lubrication Technology. 2016. T. 72. № 10. C. 28.
Жорник В.И., Ивахник А.В., Ивахник В.П., Запольский А.В. Структура и свойства комплексной сульфонат кальциевой смазки // Материаловедение в машиностроении. 2018. Т. 42. № 1. С. 44.
Анисимова А.А. Дис. … канд. техн. наук: М.: РГУНиГ им. И.М. Губкина, 2018.
Kobylyansky E.V., Mishchuk O.A., Ishchuk Y.L. Lubricating properties of thixotropic systems based on overbased calcium sulphonate // Lubrication Science. 2004. T. 16. № 3. C. 293.
Márquez-Santiago J. F., Vite-Torres M., Gallardo-Hernandez E. A. Study of Wear on AISI E52100 Steel Using a Lithium Complex Grease and a Calcium Sulfonate Grease // Fracture, Fatigue and Wear. Springer. 2020. C. 727.
Fan X., Li W., Li H. et al. Probing the effect of thickener on tribological properties of lubricating greases // Tribology International. 2018. T. 118. C. 128.
Wang Z., Xia Y., Liu Z. The rheological and tribological properties of calcium sulfonate complex greases // Friction. 2015. T. 3. № 1. C. 28.
Myers J., Myers J., Los N. et al. Grease Evaluation for Continuous Caster Bearings // NLGI Spokesman. 2020. T. 84. № 5. C. 6.
Bosman R., Lugt P.M. The microstructure of calcium sulfonate complex lubricating grease and its change in the presence of water // Tribology transactions. 2018. T. 61. № 5. C. 842.
Zhou Y., Bosman R., Lugt P.M. On the shear stability of dry and water-contaminated calcium sulfonate complex lubricating greases // Tribology transactions. 2019. T. 62. № 4. C. 626.
Буяновский И.А., Лашхи В.Л., Самусенко В.Д. Развитие температурного метода оценки смазочной способности масел // Мир нефтепродуктов. Вестник нефтяных компаний. 2017. № 2. С. 28.
Чудиновских А.Л., Лашхи В.Л. Химмотологические аспекты действия детергентов в моторных маслах. М.: ООО “Издательский дом Недра”, 2015. 156 с.
Дополнительные материалы отсутствуют.
Инструменты
Проблемы машиностроения и надежности машин