Поверхность. Рентгеновские, синхротронные и нейтронные исследования, 2019, № 2, стр. 89-96
Метод получения кристаллической структуры типа С14 и С36 фаз Лавеса интерметаллических сплавов-накопителей на основе Ti–Cr
Т. Л. Мурашкина 1, *, М. С. Сыртанов 1, А. С. Шабунин 1, Р. С. Лаптев 1
1 Национальный исследовательский Томский политехнический университет,
634050 Томск, Россия
* E-mail: tanjuffka@tpu.ru
Поступила в редакцию 27.01.2018
После доработки 27.02.2018
Принята к публикации 25.02.2018
Аннотация
Показана возможность получения материалов-накопителей водорода на основе интерметаллических соединений TiCr2 методами плавления в плазме аномального тлеющего разряда и электронно-лучевой плавки. Использование метода плавления в плазме аномального тлеющего разряда приводит к формированию фазы Лавеса со структурным типом С36, в то время как электронно-лучевая плавка позволяет получить фазу Лавеса типа С14. Установлено, что формирование фаз Лавеса различного структурного типа связано с разными скоростями охлаждения, что обусловлено особенностями методов синтеза интерметаллических соединений.
ВВЕДЕНИЕ
Перспективными материалами-накопителями водорода являются интерметаллические соединения типа АВ2, среди которых особо выделяются фазы Лавеса. Фазы Лавеса образуются при соотношении атомных радиусов элементов ~1.22. Согласно правилу Бернауэра, различают несколько структурных типов фаз Лавеса (С14, С15 и С36) в зависимости от числа внешних электронов. Многочисленные исследования соединений на основе титана показывают применимость данных материалов как гидридообразующего класса, обладающего необходимыми свойствами при взаимодействии с водородом, а именно низким давлением плато при температурах в диапазоне от –100 до 100°C. Наиболее перспективными являются псевдо-бинарные соединения на основе Ti–Cr с добавлением легирующих элементов Zr, V, Mn, Fe, Co, Ni [1–6], которые представлены преимущественно кубической структурой С15 или смесью кубической с гексагональными типами С14 и С36 [7–9]. Соединение TiCr2 лежит на границе зон существования фаз С36 и С15, что делает его интересным для получения соединения с одним структурным типом и детального изучения кинетики и циклической стабильности при взаимодействии с водородом.
В зависимости от метода получения интерметаллические сплавы обладают совершенно разными свойствами из-за структуры, которая включает и кристаллические, и аморфные фазы. Такие структуры, разделенные на чрезвычайно мелкие зерна, ряд исследователей охарактеризовал как “стеклообразные” неупорядоченные границы зерен. Поколение новых метастабильных фаз или материалов с аморфными фазами по границам зерен имеет иной характер поведения водорода в материале, что обусловлено большим количеством дефектов, в которых может локализоваться водород [10].
Обычно интерметаллические соединения получают дуговой плавкой с последующим отжигом [1, 4–6, 11–13], а также индукционной плавкой, в том числе высокочастотной [14, 15] и во взвешенном состоянии (RF melting, RF levitation melting, magnetic levitation melting) [16–18]. Для синтеза высоко-активированных нанокристаллических порошков используют неравновесные методы обработки, такие как механическое сплавление или механосинтез с применением высокоэнергетических шаровых мельниц [2, 19–21]. Перечисленные методы синтеза интерметаллических соединений обладают рядом недостатков, таких как загрязнение сплава, материалом используемых электродов и неравномерный нагрев в объеме образца. С активным развитием аддитивных технологий электронно-лучевая плавка представляет интерес для получения интерметаллических сплавов благодаря высокой степени чистоты синтезируемых материалов [22, 23]. Более того, широко используемым методом получения интерметаллидных покрытий с незначительным содержанием примесей является плазма аномального тлеющего разряда. Потенциально данный метод является перспективным для получения фаз Лавеса за счет равномерного и контролируемого нагрева и охлаждения в процессе плавления [24]. В настоящее время отсутствуют литературные данные о формировании интерметаллического соединения TiCr2 методами электронно-лучевой плавки и в плазме аномального тлеющего разряда.
МАТЕРИАЛЫ И МЕТОДЫ
В качестве исходных материалов использовались металлические порошки титана (чистота 99%) и хрома (чистота 99.8%). Соотношение Ti/Cr было рассчитано для состава TiCr2. Процесс получения смеси порошков исходных металлов проводили в высокоэнергетической шаровой мельнице Sample Prep 8000M-230 Mixer/Mill с использованием металлических барабанов из карбидовольфрама и металлических шаров диаметром 10 мм. Соотношение порошка и шаров составляло 3 : 1, смешивание осуществлялось в течение 60 мин при частоте вращения барабана 875 оборотов в минуту.
Получение интерметаллических сплавов осуществляли двумя способами. Метод плавления в плазме аномального тлеющего разряда был реализован на установке “КВО”, разработанной в Томском политехническом университете, с использованием графитовых тиглей в режимах, приведенных в табл. 1. Для гомогенизации образцов сплавы были подвергнуты переплавке несколько раз.
Таблица 1.
Технологические параметры сплавления на установке “КВО”
Остаточное давление рабочей камеры | 5 × 10–4 Па |
Рабочее давление | 3 × 10–1 Па |
Рабочий газ | Аргон |
Мощность | 3 кВт |
Ток магнетронного разряда | 5.0–5.5 А |
Напряжение питания магнетрона | 550–600 В |
Метод электронно-лучевой плавки в вакууме был реализован с помощью установки ЭЛУ-5, разработанной (СО РАН ИФПМ), оборудованной электронно-лучевой пушкой с плазменным катодом [25]. Образцы для плавки предварительно консолидировали с помощью системы искрового плазменного спекания SPS10-4 [26] производства GT Advanced Technologies (США) путем прессования смешанных порошков в таблетки диаметром 10 мм и высотой 5 мм. Полученные таблетки плавили на медной подложке в вакуумной камере при давлении 5 × 10–5 Торр расфокусированным электронным лучом при ускоряющем напряжении 30 кВ и токе луча до 100 мА до образования капли расплавленного металла. Время выдержки расплавленной капли – до полного окончания процесса химической реакции между компонентами смеси.
Морфологию и элементный анализ исходных металлических порошков и полученных сплавов исследовали с помощью растрового электронного микроскопа на основе системы с электронным и сфокусированным ионным пучками Quanta 200 3D (EDAX, Нидерланды) в высоком вакууме при ускоряющем напряжении 20 кВ. Рентгеноструктурный анализ проводился путем анализа дифрактограмм, полученных на рентгеновском дифрактометре Shimadzu XRD-7000S. В ходе проведения эксперимента использовались следующие параметры съемки: скорость сканирования – 2° в мин, шаг сканирования – 0.03°, диапазон углов составлял 20°–90°, накопление в точке – 1.5″. Средний размер кристаллитов по областям когерентного рассеяния определялся по уравнению Дебая–Шеррера с учетом инструментального уширения. Инструментальное уширение было рассчитано по стандартному образцу кремниевого порошка и составило 0.1. Анализ дифракционных картин был проведен при помощи использования базы данных PDF4+ и программы полнопрофильного анализа Powder Cell 2.4.
РЕЗУЛЬТАТЫ И ИХ ОБСУЖДЕНИЕ
На первом этапе работы проводилось исследование морфологии, элементного и фазового состава исходных металлических материалов. На рис. 1 представлены изображения исходных порошков титана и хрома при увеличениях ×1000 и ×5000.
Исходные металлические порошки титана и хрома имеют неправильную (иррегулярную) форму и развитую поверхность частиц, причем порошки представлены в виде цепочек зерен, восстановленных в процессе получения порошка. Средний размер частиц титана составляет 30 ± 10 мкм, хрома – 15 ± 5 мкм. Результаты энергодисперсионного рентгеноспектрального микроанализа, представленные на рис. 1, показывают наличие только титана и хрома в соответствующих порошках.
Для определения структурно-фазового состояния порошков титана и хрома был проведен рентгеноструктурный анализ, результаты которого представлены на рис. 2, откуда следует присутствие характерной кубической фазы (ОЦК) в исходном порошке хрома. Параметры решетки и размеры кристаллитов по областям когерентного рассеяния представлены в табл. 2. В исходном титановом порошке, помимо гексагональной фазы α-Ti (ГПУ), установлено наличие примеси в виде δ-TiH (ГЦК) в количестве 14 об. %. Наличие гидридной фазы связано с технологией получения титанового порошка. Порошок титана получают восстановлением оксидов металлов гидридом кальция. В результате химической реакции получают титан, оксид кальция и водород. Так как процесс восстановления протекает при высоких температурах (свыше 800°С), может проходить взаимодействие титана с водородом с последующим образованием гидридной фазы.
Таблица 2.
Результаты рентгеноструктурного исследования исходных материалов
Образец | Обнаруженные фазы | Содержание фаз, об. % | Параметры решетки, Å | Размер кристаллитов по ОКР, нм | |
---|---|---|---|---|---|
а | с | ||||
Cr (исходный порошок) | Cr (ОЦК) | 100 | 2.884 | >300 | |
Ti (исходный порошок) | Ti | 86 | 2.948 | 4.681 | 79 |
TiH1.5 (ГЦК) | 14 | 4.399 | 71 |
После смешивания порошков в необходимом соотношении в мельнице был проведен морфологический анализ на предмет изменения формы и размеров частиц (рис. 3).
Анализ микрофотографий смешанных порошков свидетельствует о равномерном перемешивании, форма и размер частиц остались прежними (средний размер частиц составляет 20 ± 10 мкм), за исключением небольших растрескиваний по границам зерен в результате механического воздействия шарами высокоэнергетической мельницы и трением между крупными частицами порошка. Рентгеноспектральный микроанализ данных смесей также показал однородность и отсутствие примесей.
На следующем этапе работы проводилось сплавление порошковых материалов с целью формирования стехиометрической фазы TiCr2. Результаты исследования структурно-фазового состояния сплавов TiCr2, полученных в плазме аномального тлеющего разряда и электронно-лучевой плавкой, представлены на рис. 4.
Рис. 4.
Дифрактограммы сплавов TiCr2, полученных в плазме аномального тлеющего разряда (а) и электронно-лучевой плавкой (б).
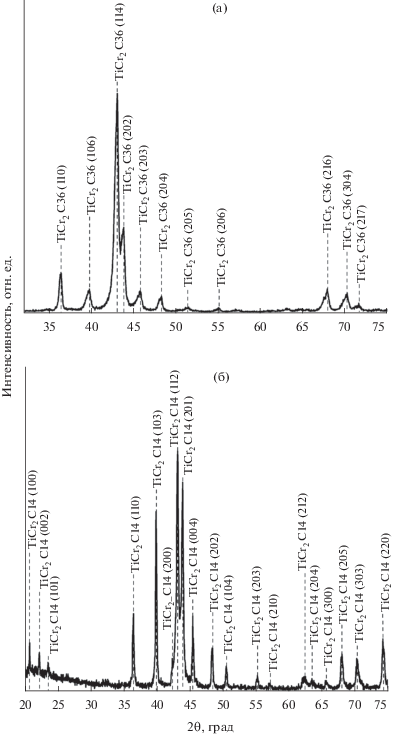
Фазовый анализ сплава, полученного в плазме аномального тлеющего разряда, показал наличие гексагональной фазы TiCr2 соответствующей фазе Лавеса типа С36. На дифрактограмме сплава, сформированного методом электронно-лучевой плавки, наблюдаются рефлексы, принадлежащие фазе TiCr2, соответствующей фазе Лавеса типа С14. Параметры решетки и размер областей когерентного рассеяния представлены в табл. 3. В процессе получения сплава TiCr2 в плазме аномального тлеющего разряда происходит образование фазы Лавеса гексагональной структуры типа С36, а при использовании электронно-лучевой плавки получается структура высокотемпературного типа С14 [27, 28], причем образованные фазы характеризуются наличием только одного структурного типа. Формирование различных структур С36 и С14 указанными методами связано со скоростью охлаждения расплава. Получение фазы Лавеса типа С36 связано с медленным теплоотводом от графитового тигля, обусловленное конструкционными особенностями установки “КВО” [24]. Формирование структуры С14 сопровождается большей скоростью охлаждения.
Таблица 3.
Результаты рентгеноструктурного исследования сплавов TiCr2
Метод | Обнаруженные фазы | Содержание фаз, об. % | Параметры решетки, Å | Размер кристаллитов по ОКР, нм | |
---|---|---|---|---|---|
а | с | ||||
Плазма аномально тлеющего разряда | TiCr2 (C36) | 100 | 4.928 | 15.983 | 28 |
Электронно-лучевая плавка | TiCr2 (C14) | 100 | 4.915 | 7.955 | 102 |
Для использования сплавов в качестве материалов-накопителей водорода необходимо проводить измельчение в порошок с целью повышения эффективности сорбционной емкости. Сплавы TiCr2 были подвергнуты механическому измельчению, микроскопические изображения частиц представлены на рис. 5.
Результаты растровой электронной микроскопии свидетельствуют о полной переплавке образцов в объеме материала и отсутствии вкраплений порошка. В объеме и на поверхности частиц присутствуют микропоры. Согласно результатам рентгеноспектрального микроанализа (рис. 5б), полученные сплавы на основе титан-хром имеют стехиометрический состав: Ti – 32.99 мас. %, Cr – 67.01 мас. %. Элементный анализ сплавов подтверждает получение необходимой фазы TiCr2, что хорошо согласуется с результатами рентгеновской дифрактометрии. Не смотря на проведение процесса сплавления в графитовых тиглях, в образцах отсутствует углерод и другие примеси (в том числе кислород).
ЗАКЛЮЧЕНИЕ
Методами плавления в плазме аномального тлеющего разряда и электронно-лучевой плавки были получены интерметаллические соединения TiCr2. Использование метода плавления в плазме аномального тлеющего разряда приводит к формированию фазы Лавеса со структурным типом С36 (параметры решетки a = 4.928 Å, c = 15.983 Å), в то время как электронно-лучевая плавка позволяет получить фазу Лавеса типа С14 (параметры решетки a = 4.915 Å, c = 7.955 Å). Формирование фаз Лавеса различного структурного типа связано с разными скоростями охлаждения, что обусловлено особенностями методов синтеза интерметаллических соединений. Растровая электронная микроскопия указывает на полную переплавку порошков по всему объему исследуемых образцов. Рентгеноструктурный анализ и рентгеноспектральный микроанализ не показали наличие примесей в полученных сплавах, что свидетельствует о перспективе применения данных методов для получения интерметаллических материалов-накопителей водорода.
Дальнейшие исследования будут направлены на изучение эволюции дефектной структуры в процессе циклов многократного гидрирования/дегидрирования интерметаллических соединений на основе Ti–Cr.
Список литературы
Cao Z., Ouyang L., Wang H. et al. // International J. Hydrogen Energy. 2015. V. 40. № 6. P. 2717. doi 10.1016/j.ijhydene.2014.12.093
Chen Z., Xiao X., Chen L. et al. // International J. Hydrogen Energy. 2013. V. 38. № 29. P. 12 803. doi 10.1016/j.ijhydene.2013.07.073
Sato R., Tajima I., Nakagawa T. et al. // J. Alloys Compd. 2013. V. 580. P. S21. doi 10.1016/j.jallcom.2013.02.019
Tsukahara M. // Materials Transactions. 2011. V. 52. № 1. P. 68. doi 10.2320/matertrans.M2010216
Kawasuso A., Arashima H., Maekawa M. et al. // J. Alloys Compd. 2009. V. 486. № 1. P. 278. doi 10.1016/ j.jallcom.2009.06.125
Martinez A., dos Santos D.S. // Materials Research. 2012. V. 15. № 5. P. 809. doi 10.1590/S1516-14392012005000093
Takeichi N., Takeshita H.T., Tanaka H. et al. // Materials Letters. 2003. V. 57. № 8. P. 1395. doi 10.1016/ S0167-577X(02)00995-3
Takeichi N., Takeshita H.T., Oishi T. et al. // Materials Transactions. 2002. V. 43. № 8. P. 2161.
Amira S., Santos S. F., Huot J. // Intermetallics. 2010. V. 18. № 1. P. 140. doi 10.1016/j.intermet.2009.07.004
Benjamin J.S. // Sc. American. 1976. V. 234. P. 40.
Okada M., Kuriiwa T., Tamura T. et al. // J. Alloys Compd. 2002. V. 330. P. 511. doi 10.1016/S0925-8388(01)01647-4
Shashikala K., Banerjee S., Kumar A. et al. // International J. Hydrogen Energy. 2009. V. 34. № 16. P. 6684. doi 10.1016/j.ijhydene.2009.06.065
Hang Z., Xiao X., Li S. et al. // J. Alloys Compd. 2012. V. 529. P. 128. doi 10.1016/j.jallcom.2012.03.044
Yadav T.P., Shahi R.R., Srivastava O.N. // International J. Hydrogen Energy. 2012. V. 37. № 4. P. 3689. doi 10.1016/j.ijhydene.2011.04.210
Kumar V., Pukazhselvan D., Tyagi A.K. et al. // Materials for Renewable and Sustainable Energy. 2013. V. 2. № 2. P. 12. doi 10.1007/s40243-013-0012-3
Qu H., Du J., Pu C. et al. // International J. Hydrogen Energy. 2015. V. 40. № 6. P. 2729. doi 10.1016/ j.ijhydene.2014.12.089
Wang X., Chen R., Zhang Y. et al. // J. Alloys Compd. 2006. V. 420. №. 1. P. 322. doi 10.1016/j.jallcom.2005.11.001
Jurczyk M. // J. Optoelectronics and Advanced Materials. 2006. V. 8. № 2. P. 418.
Liang G., Huot J., Schulz R. // J. Alloys Compd. 2001. V. 320. P. 133. doi 10.1016/S0925-8388(01)00929-X
Huot J., Ravnsbæk D.B., Zhang J. et al. // Progress in Materials Science. 2013. V. 58. № 1. P. 30. doi 10.1016/ j.pmatsci.2012.07.001
Dos Santos D.S., Bououdina M., Fruchart D. // International J. Hydrogen Energy. 2003. V. 28. № 11. P. 1237. doi 10.1016/S0360-3199(03)00006-5
Valkov S., Petrov P., Lazarova R. et al. // Appl. Surf. Sci. 2016. V. 389. P. 768. doi 10.1016/j.apsusc.2016.07.170
Sakamoto K., Yoshikawa K., Kusamichi T. et al. // ISIJ International. 1992. V. 32. № 5. P. 616.
Sidelev D.V., Bleykher G.A., Bestetti M. et al. // Vacuum. 2017. V. 143. P. 479. doi 10.1016/j.vacuum.2017.03.020
Панин В.Е., Белюк С.И., Дураков В.Г. и др. // Сварочное производство. 2000. № 2. С. 34.
Nikulina A.A., Smirnov A.I., Bataev A.A. et al. // Materials Characterization. 2017. V. 129. P. 252. doi 10.1016/j.matchar.2017.05.018
Baumann W., Leineweber A., Mittemeijer E.J. // Intermetallics. 2011. V. 19. № 4. P. 526. doi 10.1016/j.intermet.2010.11.027
Baumann W., Leineweber A. // J. Alloys Compd. 2010. V. 505. № 2. P. 492. doi 10.1016/j.jallcom.2010.06.117
Дополнительные материалы отсутствуют.
Инструменты
Поверхность. Рентгеновские, синхротронные и нейтронные исследования