Поверхность. Рентгеновские, синхротронные и нейтронные исследования, 2019, № 3, стр. 106-112
Исследование эрозионного износа покрытий с применением подвижной струи гетерогенного потока ограниченной площади
С. А. Борисов 1, С. В. Добровольский 1, Ю. И. Глуховская 1, *, П. В. Никитин 1
1 Московский авиационный институт (национальный исследовательский университет)
125993 Москва, Россия
* E-mail: gljul@bk.ru
Поступила в редакцию 23.01.2018
После доработки 25.07.2018
Принята к публикации 25.07.2018
Аннотация
Рассматривается и обосновывается возможность исследования эрозионного износа покрытий полномасштабных летательных аппаратов с применением подвижной струи гетерогенного потока ограниченной площади в качестве альтернативы традиционным методам исследований с использованием масштабных моделей образцов, аэродинамических труб и гидроударных стендов. Приводятся экспериментальные данные разрушения покрытия в зависимости от времени воздействия струи потока ограниченной площади, демонстрирующие линейный характер зависимости площади разрушения покрытия от времени. Предлагается математическая модель для расчета износа материала покрытия. Описан состав возможной экспериментальной установки, действующей на этих принципах.
ВВЕДЕНИЕ
Современные покрытия обшивки летательных аппаратов обеспечивают защиту от механических повреждений, тепловых воздействий и т.д. Покрытия летающих аппаратов на малых высотах и больших скоростях подвергаются сильному эрозионному износу, негативно влияющему на их свойства.
Значения наработки до износа разных покрытий (время и температурные условия, за которое покрытие потеряет свои свойства) есть в ГОСТах, но испытания таких покрытий идеализированы: моделируется поток, направленный на небольшую пластину с покрытием. Но на практике воздушный поток может двигаться по касательной траектории ко всем поверхностям корпуса летательного аппарата, при этом возникают области ускорения и торможения, уплотнения, вихрей и другие явления. Поэтому для получения более объективной картины необходимо выполнять анализ эрозионного износа покрытия всего корпуса летательного аппарата, что является очень дорогим исследованием.
В настоящее время существуют два стендовых метода исследования эрозионного износа обшивки летательного аппарата: установки на базе аэродинамических труб и гидроударные стенды [1]. В первом случае можно испытывать аппараты в натуральную величину, но в ограниченном диапазоне скоростей, так как при росте скорости становится невозможным проведение испытания без уменьшения исследуемого образца. Стоимость подобных установок очень высокая. Кроме того, подобный стенд обычно имеет значительные габаритные размеры. Второй вариант обеспечивает результаты исследований в широком диапазоне скоростей, но исследуемые образцы (как правило) имеют площадь не более 4 см2. В вакуумную камеру помещаются два испытуемых образца, установленные на концах поворотной штанги. Раскручиваясь на штанге по принципу карусели, образцы достигают скорости ~550 м/с. Затем в камеру подается жидкость в виде капель, которые сталкиваются с поверхностью образца. Примерами подобных экспериментальных установок являются аэродинамическая труба ЦАГИ Т-101 и гидроударный стенд “Эрозия-М” (МЭИ).
Существующие методы исследования не могут в полной мере описать процесс эрозионного износа покрытий, так как малые толщины покрытий, которые сложно обеспечить технологически, не позволяют создать адекватную масштабную модель летательных аппаратов. Иными словами, при масштабном уменьшении модели летательных аппаратов технологически невозможно пропорционально уменьшить толщину покрытия. В свою очередь, исследование подобных явлений на основе небольших плоских пластин не дают полной картины, особенно в геометрически сложных зонах, например, на стыке крыла и фюзеляжа, передних кромках крыльев, носовом обтекателе летательного аппарата и т.д.
Для повышения качества подобных исследований рассмотрим возможность создания экспериментальной установки, которая позволяла бы испытывать износ покрытия обшивки летательного аппарата в натуральную величину и имела бы существенно меньшую стоимость по сравнению с установкой на базе аэродинамической трубы.
КОНЦЕПЦИЯ ЭКСПЕРИМЕНТАЛЬНОЙ УСТАНОВКИ
Для создания такой экспериментальной установки необходимо исследовать процесс перемещения гетерогенного потока [2] относительно поверхности летательного аппарата и найти зависимость между временем разрушения и площадью разрушаемой поверхности.
Для этих целей использовалась установка ДИМЕТ-М21СК, предназначенная для исследования эрозионного износа, способная перемещать струю гетерогенного потока относительно исследуемого образца в плоскости (две степени свободы перемещения). Принципиальная схема модуля установки, задействованного в эксперименте, изображена на рис. 1 . На этой установке была проведена серия экспериментов, в которых пошагово увеличивалась площадь воздействия (в два и три раза). Для испытания использовалась медная пластинка толщиной 0.1 мм, диаметр сопла составлял 6 мм, скорость потока – 250 м/с, углы атаки струи потока α = 90°, 70°, 45° и 20°. Усредненные результаты серии экспериментов представлены в табл. 1 с пояснением расчета площади разрушения пластины на рис. 2 , где радиус сопла R = 3 мм, площадь сечения сопла SC = πR2, площадь сегментов следа разрушения пластины вне сечения сопла вдоль направления перемещения SΔ = 4R2 – SC.
Рис. 1.
Принципиальная схема установки: 1 – компрессор, 2 – манометр компрессора, 3 – отсечной клапан, 4 – модуль подготовки воздуха, 5 – фильтр регулятор, 6 – манометр давления в магистрали, 7 – блок управления подачи воздуха и твердой фазы, 8 – электропневмоклапан, 9 – датчик расхода воздуха, 10 – плоский нагреватель, 11 – державка, 12 – дозатор ПВ-85М, 13 – блок управления дозатором ПВ-85М, 14 – манометр давления воздуха на входе в смеситель, 15 – омический нагреватель воздуха, 16 – блок управления температурой воздуха на входе в ускоритель, 17 – смеситель, 18 – ускоритель гетерогенного потока, 19 – исследуемый образец, 20 – термопара на исследуемом образце, 21 – сканирующее устройство, 22 – блок управления сканирующим устройством, 23 – пылезащитная камера, 24 – установка сбора пыли и очистки воздуха, 25 – трубопровод, 26 – кабель управления, 27 – термопара реле-регулятора температуры ТРМ502.
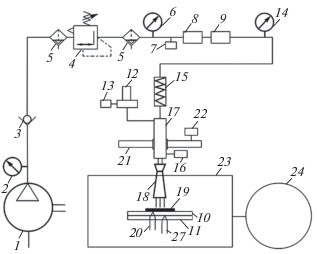
Таблица 1.
Усредненные результаты времени разрушения в зависимости от угла направления струи α
Угол направле-ния струи α, градусы | Переме-щение сопла, мм | Площадь воздействия, мм2 | Время воздействия, с |
---|---|---|---|
90 | 0 | 28.27 | 5.48 |
12 | 64.27 | 9.16 | |
24 | 136.27 | 19.24 | |
48 | 280.27 | 37.34 | |
70 | 0 | 28.27 | 4.90 |
12 | 64.27 | 9.45 | |
24 | 136.27 | 16.39 | |
48 | 280.27 | 37.96 | |
45 | 0 | 28.27 | 5.73 |
12 | 64.27 | 10.87 | |
24 | 136.27 | 27.06 | |
48 | 280.27 | 53.45 | |
20 | 0 | 28.27 | 25.51 |
12 | 64.27 | 45.83 | |
24 | 136.27 | 114.81 | |
48 | 280.27 | 227.47 |
В результате установлена приближенно линейная зависимость площади разрушаемой поверхности S от времени разрушения t (рис. 3 ). Характерные всплески на кривых в первые секунды можно объяснить повышенным износом поверхности пластины при включении установки до перехода в установившийся режим перемещения сопла.
Можно сделать вывод о том, что при увеличении площади в n раз, в такое же число раз увеличивается и время разрушения. Таким образом, можно использовать перемещение струи гетерогенного потока ограниченной площади относительно летательного аппарата для исследования износа покрытия обшивки, как если бы оно подвергалось воздействию полномасштабного потока.
Для испытания полноразмерных летательных аппаратов необходимо использовать установку, подобную той, на которой была исследована линейность процесса разрушения, но она должна быть смонтирована на подвижном манипуляторе, способном двигаться по направляющим вдоль летательного аппарата. На рис. 4 представлена концептуальная модель подвижной установки: гетерогенный поток, состоящий из воздуха и абразивных частиц, по заданной программе перемещается относительно неподвижного корпуса летательного аппарата с помощью манипулятора. Так решается проблема длины летательного аппарата, а его симметричность позволяет обдувать только одну сторону.
Рис. 4.
Концептуальная модель подвижной установки: 1 – сопло струи гетерогенного потока, 2 – манипулятор, 3 – подвижный стол на продольных направляющих, 4 – пульт системы управления, 5 – компрессорная станция, 6 – полноразмерный летательный аппарат.
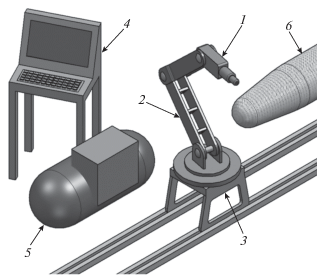
Такая установка не занимает много места, быстро разворачивается и легко эксплуатируется. Небольшие размеры рабочей области (струи) позволяют создать непрерывный поток, используя компрессорную станцию. Стоимость эксплуатации такой установки значительно ниже, чем установки на базе аэродинамической трубы, а малые размеры позволяют использовать ее в различных организациях: от малых предприятий до исследовательских институтов.
МАТЕМАТИЧЕСКАЯ МОДЕЛЬ ИЗНОСА ПОКРЫТИЯ
Рассмотрим гетерогенный поток, состоящий из воздуха и увлажненной атмосферной пыли. Атмосферная пыль представляет собой абразивные частицы размером от 1 до 20 мкм, способные продолжительное время держаться в воздухе. Основная масса частиц находится на высоте 500–600 метров от поверхности земли. При попадании в облако абразивных частиц поверхность летательный аппарат испытывает эрозионный износ трех типов, вызывающий повреждение покрытия [3–6]:
1) упругое внедрение – разрушение происходит из-за фрикционно-контактной усталости;
2) полидеформационное разрушение – пластические деформации покрытия;
3) микрорезание – хрупкое и вязкое разрушение, не являющееся постоянным во времени.
При малых скоростях гетерогенного потока деформирование материала производится (в основном) вершинами зерен частиц. С увеличением скорости размеры лунок определяются характерным диаметром частицы [7, 8]. В общем случае при внедрении частицы в поверхность происходит упругопластическая деформация покрытия. Сначала происходит упругое деформирование. Для большинства применяемых металлов и сплавов величина упругого внедрения частицы в поверхность покрытия на несколько порядков меньше радиуса скругления вершин абразивной частицы. Поэтому можно пренебречь упругой деформацией и считать, что слой покрытия подвергается только пластической деформации.
Для численного моделирования процесса взаимодействия абразивных частиц с поверхностью покрытия предлагается взять за основу модель струйной гидроабразивной обработки деталей из работы [9] при следующих допущениях:
1) частица считается абсолютно жесткой и в момент удара не разрушается;
2) частица представляет собой шар радиусом R;
3) масса исследуемого объекта значительно больше массы частицы;
4) учитывается только скольжение частицы по поверхности, вращение и возможные перекатывания частицы при ударе не учитываются;
5) слой покрытия, на который воздействуют частицы, обладает только свойством пластической деформации.
Средний объем пластически выдавленного материала считается равным объему лунки, которая образуется при ударе частицы о поверхность. В общем случае удар частицы проходит этапы внедрения и вытеснения. Внедрение начинается при касании частицы с поверхностью покрытия и заканчивается, когда нормальная составляющая скорости частицы становится ${\text{р а в н о й }}$ нулю. В зависимости от максимальной глубины внедрения возможны два случая движения частицы на этом этапе. В первом случае максимальная глубина внедрения ${{h}_{{{\text{max}}}}}$ не превышает значение h = $R\left( {1--{cos\alpha }} \right),$ и движение частицы можно рассматривать как внедрение сферы по нормали к поверхности (рис. 5).
В этом случае деформированный объем приближенно вычисляется как $\Delta {{V}_{{11}}} = {\pi }Rh_{{{\text{max}}}}^{2}.$
Если максимальная глубина внедрения больше значения $R\left( {1--{cos\alpha }} \right),$ то деформированный объем будет равен: $\Delta {{V}_{{{\text{12}}}}} = 0.5\Delta {{V}_{{11}}} + \Delta {{V}_{{{\text{el}}1}}},$ где $\Delta {{V}_{{{\text{el}}1}}}$ – объем части эллипсоида с полуосями: $a = {{h}_{{{\text{max}}}}},$ $b = \sqrt {2R{{h}_{{{\text{max}}}}}} ,$ c = $\left[ {R\left( {1--{cos\alpha }} \right)} \right.$ + ${{\left. {{{h}_{{{\text{max}}}}}\cos {\alpha }} \right]} \mathord{\left/ {\vphantom {{\left. {{{h}_{{{\text{max}}}}}\cos {\alpha }} \right]} {\sin {\alpha }}}} \right. \kern-0em} {\sin {\alpha }}}.$ Схема внедрения частицы для этого случая показана на рис. 6.
Для второго случая внедрения частицы по нормали деформированный объем будет равен: $\Delta {{V}_{{12}}}$ = = 0.5πR$h_{{{\text{max}}}}^{2}$ + [πhmax$\sqrt {2R{{h}_{{{\text{max}}}}}} $(R – hmax) cos α)]/(3 sin α).
На этапе вытеснения движение частицы определяется тангенциальной составляющей ее скорости. По результатам исследования следов, оставленных абразивными частицами на обрабатываемой поверхности при струйном распылении, на этом этапе продолжается пластическое деформирование материала покрытия [7, 8]. На рис. 7 изображена схема движения частицы на этом этапе.
Для первого и второго случая внедрения частицы на этапе вытеснения деформированный объем покрытия можно определить как ΔV2 = = $\Delta {{V}_{{{\text{el}}2}}}--0.5\Delta {{V}_{{11}}},$ где $\Delta {{V}_{{{\text{el}}2}}}$ – объем части эллипсоида с полуосями: $a = {{h}_{{{\text{max}}}}},$ $b = \sqrt {2R{{h}_{{{\text{max}}}}}} ,$ c = = $[R\left( {1--\cos {{{\alpha }}_{{\text{K}}}}} \right)$ + ${{{{h}_{{{\text{max}}}}}\cos {{{\alpha }}_{{\text{K}}}}]} \mathord{\left/ {\vphantom {{{{h}_{{{\text{max}}}}}\cos {{{\alpha }}_{{\text{K}}}}]} {\sin {{{\alpha }}_{{\text{K}}}}}}} \right. \kern-0em} {\sin {{{\alpha }}_{{\text{K}}}}}},$ ${{{\alpha }}_{{\text{K}}}}$ – угол отскока частицы.
Получаем формулу для вычисления объема:
Общий деформированный объем равен сумме деформированных объемов на этапах внедрения и вытеснения: $\Delta {{V}_{{{\text{def}}}}} = \Delta {{V}_{{1{\text{*}}}}} + \Delta {{V}_{2}},$ где $\Delta {{V}_{{1{\text{*}}}}}$ – это ${{V}_{{1\Delta 1}}}$ или $\Delta {{V}_{{12}}}$ для первого и второго случая внедрения частицы соответственно.
Если в данный момент времени с поверхностью контактируют q частиц, то суммарный деформированный объем равен:
Число частиц, взаимодействующих с поверхностью в данный момент времени на площади, охватываемой струей гетерогенного потока, можно определить следующим образом [9]. Массовый расход потока из увлажненных абразивных частиц через сечение струи можно представить как ${{m}_{{{\text{sus}}}}} = {{m}_{{{\text{ab}}}}} + {{m}_{{{\text{fl}}}}}$ или
(2)
${{V}_{{{\text{sus}}}}}{{{\rho }}_{{{\text{sus}}}}} = {{V}_{{{\text{ab}}}}}{{{\rho }}_{{{\text{ab}}}}} + {{V}_{{{\text{fl}}}}}{{{\rho }}_{{{\text{fl}}}}}.$Здесь ${{m}_{{{\text{ab}}}}},$ ${{V}_{{{\text{ab}}}}},$ ${{{\rho }}_{{{\text{ab}}}}}$ – масса, объем и плотность абразивного материала (атмосферной пыли), ${{m}_{{{\text{fl}}}}},$ ${{V}_{{{\text{fl}}}}},$ ${{{\rho }}_{{{\text{fl}}}}}$ – масса, объем и плотность воздуха текучей составляющей потока, ${{m}_{{{\text{sus}}}}},$ ${{V}_{{{\text{sus}}}}},$ ${{{\rho }}_{{{\text{sus}}}}}$ – масса, объем и плотность суспензии, из которой состоит гетерогенный поток.
Количество абразивных частиц в потоке характеризуется концентрацией:
(3)
$K = {{{{V}_{{{\text{ab}}.{\text{wet}}}}}} \mathord{\left/ {\vphantom {{{{V}_{{{\text{ab}}.{\text{wet}}}}}} {{{V}_{{{\text{sus}}}}}}}} \right. \kern-0em} {{{V}_{{{\text{sus}}}}}}},$С другой стороны,
(4)
$\quad{{V}_{{{\text{ab}}.{\text{wet}}}}} = {{{{V}_{{{\text{ab}}}}}{{{\rho }}_{{{\text{ab}}}}}} \mathord{\left/ {\vphantom {{{{V}_{{{\text{ab}}}}}{{{\rho }}_{{{\text{ab}}}}}} {{{{\rho }}_{{{\text{ab}}.{\text{bulk}}}}}}}} \right. \kern-0em} {{{{\rho }}_{{{\text{ab}}.{\text{bulk}}}}}}},$Подставляя (3) и (4) в (2), получим:
(5)
${{{\rho }}_{{{\text{sus}}}}} = {{{\rho }}_{{{\text{fl}}}}} + K\left( {{{{\rho }}_{{{\text{ab}}}}}--{{{\rho }}_{{{\text{fl}}}}}} \right){{{{{\rho }}_{{{\text{ab}}.{\text{bulk}}}}}} \mathord{\left/ {\vphantom {{{{{\rho }}_{{{\text{ab}}.{\text{bulk}}}}}} {{{{\rho }}_{{{\text{ab}}}}}}}} \right. \kern-0em} {{{{\rho }}_{{{\text{ab}}}}}}}.$Объем одной частицы равен ${{4{\pi }{{R}^{3}}} \mathord{\left/ {\vphantom {{4{\pi }{{R}^{3}}} 3}} \right. \kern-0em} 3},$ тогда объемный расход абразивного материала можно вычислить как
(6)
$\quad{{V}_{{{\text{ab}}}}} = {{q{\;}4{\pi }{{R}^{3}}} \mathord{\left/ {\vphantom {{q{\;}4{\pi }{{R}^{3}}} 3}} \right. \kern-0em} 3}.$Подставляя (6) в (4) и учитывая (3) и (5), получим:
(7)
$\begin{gathered} q = 3K{{m}_{{{\text{sus}}}}}{{{{{\rho }}_{{{\text{ab}}.{\text{bulk}}}}}} \mathord{\left/ {\vphantom {{{{{\rho }}_{{{\text{ab}}.{\text{bulk}}}}}} {4{\pi }{{R}^{3}}{{{\rho }}_{{{\text{ab}}}}}}}} \right. \kern-0em} {4{\pi }{{R}^{3}}{{{\rho }}_{{{\text{ab}}}}}}} \times \\ \times \,\,\left[ {{{{\rho }}_{{{\text{fl}}}}} + K\left( {{{{\rho }}_{{{\text{ab}}}}}--{{{\rho }}_{{{\text{fl}}}}}} \right){{{{{\rho }}_{{{\text{ab}}.{\text{bulk}}}}}} \mathord{\left/ {\vphantom {{{{{\rho }}_{{{\text{ab}}.{\text{bulk}}}}}} {{{{\rho }}_{{{\text{ab}}}}}}}} \right. \kern-0em} {{{{\rho }}_{{{\text{ab}}}}}}}} \right]. \\ \end{gathered} $Экспериментально установлено [10], что отношение среднего объема удаленного материала покрытия при ударе под углом $90^\circ $ одной частицы ($\Delta {{V}_{{{\text{rem}}}}}$) к среднему объему пластически выдавленного материала ($\Delta {{V}_{{{\text{def}}}}}$) – есть величина постоянная $k = {{\Delta {{V}_{{{\text{rem}}}}}} \mathord{\left/ {\vphantom {{\Delta {{V}_{{{\text{rem}}}}}} {\Delta {{V}_{{{\text{def}}}}}}}} \right. \kern-0em} {\Delta {{V}_{{{\text{def}}}}}}}.$ Однако характер деформации поверхности покрытия при косом ударе абразивной частицы зависит от угла атаки, и коэффициент k является функцией угла атаки α и радиуса частицы R, т.е. можно записать:
Для определения суммарного удаленного объема материала покрытия подставим (1) и (7) в (8):
(9)
$\begin{gathered} {{V}_{{{\text{rem}}}}} = 3{{k}_{{{\alpha },{\text{R}}}}}K{{m}_{{{\text{sus}}}}}{{{\rho }}_{{{\text{ab}}.{\text{bulk}}}}}{{{{V}_{{{\text{def}}}}}} \mathord{\left/ {\vphantom {{{{V}_{{{\text{def}}}}}} {4{\pi }{{R}^{3}}}}} \right. \kern-0em} {4{\pi }{{R}^{3}}}}{{{\rho }}_{{{\text{ab}}}}} \times \\ \times \,\,\left[ {{{{\rho }}_{{{\text{fl}}}}} + } \right.\left. {{{K\left( {{{{\rho }}_{{{\text{ab}}}}}--{{{\rho }}_{{{\text{fl}}}}}} \right){{{\rho }}_{{{\text{ab}}.{\text{bulk}}}}}} \mathord{\left/ {\vphantom {{K\left( {{{{\rho }}_{{{\text{ab}}}}}--{{{\rho }}_{{{\text{fl}}}}}} \right){{{\rho }}_{{{\text{ab}}.{\text{bulk}}}}}} {{{{\rho }}_{{{\text{ab}}}}}}}} \right. \kern-0em} {{{{\rho }}_{{{\text{ab}}}}}}}} \right]. \\ \end{gathered} $Учитывая выражения для вычисления $\Delta {{V}_{{{\text{def}}}}},$ полученные ранее для первого и второго случая внедрения частицы, можно записать следующие выражения для вычисления массового съема материала покрытия с плотностью ${{{\rho }}_{{\text{m}}}}{\text{:}}$
для первого случая внедрения
для второго случая внедрения
В этих выражениях S – коэффициент площади поверхности, учитывающий возможное непопадание струи гетерогенного потока на поверхность покрытия.
Дальнейшее развитие математической модели зависит от учета различных сил, действующих на абразивную частицу, и других факторов. Например, это может быть сила сопротивления, действующая на частицу при ее движении по слою покрытия, или гидродинамическая сила торможения частицы в потоке суспензии.
ЗАКЛЮЧЕНИЕ
Предложенная методика анализа износа поверхности покрытия корпуса летательного аппарата с помощью подвижной струи гетерогенного потока ограниченной площади в случае ее реализации позволит с меньшими затратами и более точно выявлять на корпусе области, подверженные интенсивному износу. Определив такие области, можно локально создать защитные покрытия увеличенной толщины холодным газодинамическим методом (НТГДМ-технология).
Список литературы
Обеспечение износостойкости изделий. Метод испытаний на износостойкость материалов и деталей при гидроэрозионном изнашивании дисперсными частицами (ГОСТ 23.219-84).
Никитин П.В. Гетерогенные потоки в инновационных технологиях. Монография. М.: Изд-во Янус-К, 2010. 245 с.
Икрамов У.А. Расчетные методы абразивного износа. М.: Машиностроение, 1987. 288 с.
Кащеев В.Н. Процессы в зоне фрикционного контакта металлов. М.: Машиностроение, 1978. 212 с.
Крагельский И.В., Добычин М.Н., Комбалов В.С. Основы расчетов на трение и износ. М.: Машиностроение, 1977. 526 с.
Мартынов А.И. Основы метода обработки деталей свободным абразивом, уплотненным инерционными силами. Саратов: Издательство Саратовского университета, 1981. 212 с.
Шманев В.А., Мещеряков А.В., Второв Е.А. // Поверхностный слой, точность и эксплуатационные свойства машин и приборов. М.: МДНТП, 1986. С. 12.
Эрозия: Перевод с английского // Под ред. Прис К. М.: Мир, 1982. 462 с.
Шманев В.А., Шулепов А.П., Мещеряков А.В. // Струйная гидроабразивная обработка деталей ГТД. М.: Машиностроение, 1995. С. 23.
Непомнящий Е.Ф. // Трение и износ под воздействием струи твердых сферических частиц // Контактное взаимодействие твердых тел, расчет сил трения и износа. М.: Наука, 1971. С. 190.
Дополнительные материалы отсутствуют.
Инструменты
Поверхность. Рентгеновские, синхротронные и нейтронные исследования