Поверхность. Рентгеновские, синхротронные и нейтронные исследования, 2019, № 3, стр. 55-61
Анализ состава и структуры оксидов Fe2O3, подвергнутых магнитоимпульсной обработке
А. А. Вирюс 1, М. Н. Шипко 2, 3, *, М. А. Степович 2, 4, Т. П. Каминская 5, В. В. Коровушкин 6, А. И. Тихонов 3, Е. С. Савченко 6
1 Институт экспериментальной минералогии РАН
142432 Черноголовка, Россия
2 Ивановский государственный университет,
153025 Иваново, Россия
3 Ивановский государственный энергетический университет им. В.И. Ленина,
153003 Иваново, Россия
4 Калужский государственный университет им. К.Э. Циолковского
248023 Калуга, Россия
5 Московский государственный университет им. М.В. Ломоносова
119991 Москва, Россия
6 Национальный исследовательский технологический университет “МИСиС”,
119991 Москва, Россия
* E-mail: michael-1946@mail.ru
Поступила в редакцию 26.03.2018
После доработки 22.06.2018
Принята к публикации 22.06.2018
Аннотация
Методами растровой электронной и сканирующей зондовой микроскопии, рентгеноспектрального микроанализа и мессбауэровской спектроскопии исследованы структура и состав порошков железной руды (гематита) до и после воздействия слабых импульсных магнитных полей. Объектами исследования служили образцы гематита, являющегося структурообразующим элементом при изготовлении гексагональных ферритов бария и стронция, после их измельчения в аттриторе.
ВВЕДЕНИЕ
Повышение эксплуатационных параметров материалов является важной технологической задачей, которая может быть решена различными методами. Наиболее известными и широко используемыми в промышленном производстве являются следующие классические методы: упрочнение легированием, упрочнение пластическим деформированием, упрочнение термическими методами, в том числе поверхностная закалка, обработка лазером и электроискровое легирование, некоторые другие (цементация или азотирование стали, нитроцементация и т.п.) [1–3], а также плазменная обработка [4–6]. Возможно использование и иных, в настоящее время еще не нашедших широкого промышленного применения, но перспективных и экономичных методов повышения эксплуатационных характеристик материалов, основанных на использовании электромагнитных излучений [7, 8]. Данные методы сравнительно просто реализуются [9] и не требуют использования дорогостоящего оборудования [9–11].
Методы, основанные на использовании электромагнитных излучений, главным образом используются для исследования стали и сплавов [9–15], в меньшей степени – других материалов [16–18] и исходного сырья, состав и качество которого могут во многом определять эксплуатационные параметры изготовленных из них изделий. Поэтому изучение возможностей магнитоимпульсного воздействия на исходное сырье, используемое для производства изделий, с целью сравнения эффективности электромагнитного воздействия на исходное сырье (а впоследствии и на готовое изделие) и выбор на этой основе экономичных и эффективных путей повышения эксплуатационных характеристик изделий является весьма важной задачей. В развитии такого подхода в настоящей работе исследованы структура и состав порошков железной руды, гематита, являющегося структурообразующим элементом при изготовлении гексагональных ферритов бария и стронция, и изучено влияние на это сырье воздействия слабых импульсных магнитных полей.
МЕТОДИКА ЭКСПЕРИМЕНТА
Объектами исследования служили образцы гематита после их измельчения в аттриторе. Магнитоимпульсную обработку гематита осуществляли в импульсном магнитном поле напряженностью 100–300 кА/м с длительностью импульсов 0.1–0.2 с и интервалом между импульсами 1–2 с [9–11].
Микроструктура и элементный состав образцов изучались в растровом электронном микроскопе (РЭМ) Tescan Vega II XMU с энергодисперсионным рентгеновским спектрометром INCAx-sight. При проведении исследований порошок крепился на проводящий углеродный скотч и исследовался без напыления на него проводящей пленки. Условия анализа для всех образцов были следующие: ускоряющее напряжение 20 кВ, ток поглощенных электронов 400 пА, диаметр зонда 210 нм, рабочее расстояние 25 мм.
В субмикрометровом и нанометровом диапазонах структуру поверхности исследовали методом сканирующей зондовой микроскопии (СЗМ). Использовали сканирующий зондовый микроскоп SMENA-А (платформа “Solar”) фирмы NT-MDT (Москва, Зеленоград). Исследования проводили в полуконтактном режиме микроскопа (tapping mode) в модах топографии и фазового контраста с добавлением режима “section analize”. Режим топографии показывает изменения амплитуды колебания кантилевера из-за вариации рельефа поверхности, а режим фазового контраста фиксирует сдвиг фазы колебаний кантилевера при его взаимодействии с участками поверхности, имеющими различные локальные физико-механические свойства. Измерения проводились кантилевером НА-NС ETALON с резонансной частотой F = 462 кГц.
Исследования фазового и структурного состояний образцов выполнены при комнатной и температуре жидкого азота методом мессбауэровской спектроскопии на установке MS-1104 Em с автоматической обработкой спектров по программе Univem Ms (изомерный сдвиг спектров определяли относительно α-Fe).
ЭКСПЕРИМЕНТАЛЬНЫЕ РЕЗУЛЬТАТЫ И ИХ ОБСУЖДЕНИЕ
На рис. 1 представлены микрофотографии порошка гематита, полученные в РЭМ в режиме обратно рассеянных электронов. Используя рис. 1а (небольшое увеличение) можно оценить размеры всех частиц образца гематита, закрепленных на столике. Полученная при большем увеличении микрофотография (рис. 1б) позволяет описать размеры и форму частиц. Кроме того, на этом рисунке указаны области (на рис. 1б − точки), в которых проводился микроанализ.
Рис. 1.
Общий вид порошка гематита (а). Участок порошка, на котором отмечены точками области, в которых проводился микроанализ (б). Микрофотографии получены в РЭМ в режиме обратно рассеянных электронов.
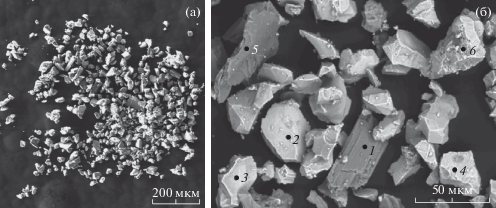
Примененный к исследованию гематитовой руды метод рентгеноспектрального микроанализа, обладая высокой локальностью, позволил исследовать частицы гематита и провести оценку наличия и состава примесей в гематитовом порошке. Результаты исследования представлены в табл. 1: в первом столбце указаны номера областей, в которых проводился микроанализ, в остальных столбцах указан элементный состав анализируемых областей и дополнительные сведения об образцах. Содержание элементов, входящих в состав анализируемых минералов (за исключением кислорода), дано в мас. %. Содержание кислорода рассчитано по стехиометрии минерала.
Таблица 1.
Результаты локального рентгеноспектрального микроанализа частиц порошка гематита
№ | Содержание, мас. % | Минерал | ||||||||
---|---|---|---|---|---|---|---|---|---|---|
Na | Mg | Si | K | Ca | Fe | O | Сумма | Формула | Название | |
1 | 10.3 ± 0.9 | 25.5 ± 0.9 | – | – | 24.5 ± 1.3 | 39.7 | 100.0 | NaFeSi2O6 | Эгирин | |
2 | – | – | – | – | – | 69.6 ± 1.9 | 30.4 | 100.0 | Fe2O3 | Гематит |
3 | – | – | – | – | – | 70.0 ± 2.0 | 30.0 | 100.0 | Fe2O3 | Гематит |
4 | – | – | – | – | – | 70.0 ± 1.9 | 30.0 | 100.0 | Fe2O3 | Гематит |
5 | – | 7.7 ± 0.4 | – | – | 40.6 ± 0.7 | 23.8 ± 0.9 | 27.9 | 100.0 | – | Оксид |
6 | 0.8 ± 0.5 | – | 3.2 ± 0.4 | 0.3 ± 0.2 | – | 64.2 ± 1.8 | 31.5 | 100.0 | – | Гематит |
Согласно результатам рентгеноспектрального микроанализа можно предположить, что полученные рентгеновские спектры из областей 2, 3, 4, 6, соответствующие светлым фазам образцов, принадлежат оксиду железа. Спектр области 1 (темная фаза на рис. 1б) соответствует железосодержащему силикату, а спектр области 5 (темная фаза на рис. 1б) соответствует железо- и магнийсодержащему оксиду кальция. Судя по данным рентгеноспектрального микроанализа области 6, оксид железа содержит примеси Si, Na, Fe или в анализируемом минерале имеется включение какого-либо силиката, который мог попасть в область возбуждения рентгеновского излучения.
Суммируя результаты рентгеноспектрального микроанализа (табл. 1), можно сказать, что минералы, отмеченные на рис. 1б цифрами 2, 3, 4 и 6, по составу соответствуют гематиту. Из примесей в порошке присутствуют эгирин 1 (табл. 1) и оксид кальция 5 (табл. 1). На рис. 1 эгирин представлен в виде темных минералов, форма которых близка к прямоугольной, оксид кальция – в виде тонких пластин темно-серого цвета.
Согласно результатам СЗМ, частицы гематита имеют слоистую (кружевную) чешуйчатую структуру (рис. 2), наиболее рельефно чешуйчатая микроструктура просматривается на трехмерных изображениях (рис. 3).
Так как частицы имеют довольно плоскую чешуйчатую структуру, то выделить на микрофотографии зерна и получить их распределение по размерам (сделать grain-анализ) не представляется возможным. Исследования поверхности показали, что для слоистой структуры поверхности характерными являются толщины слоев примерно от 0.5 до 1 мкм. Так, на рис. 4а явно видны три слоя структуры, небольшая часть еще одного слоя видна в нижнем правом углу рисунка и элемент еще одного слоя проглядывается в верхнем левом углу рисунка. Отметим, что каждый из слоев (в свою очередь) имеет зернистую структуру, состоящую из довольно плоских зерен шириной от 200 до 500 нм. На микрофотографиях это наблюдается не всегда четко, поэтому для оценки геометрических размеров такой структуры использовался анализ профиля поверхности вдоль отрезков прямых линий внутри слоев. Так, на рис. 4б показан характерный профиль сечения вдоль одного из выбранных направлений внутри слоя, дающий представление о характерных размерах зерен внутри слоев.
Рис. 4.
Микроструктура частицы гематита, полученная методом СЗМ (а). Профиль сечения, полученный вдоль чешуйчатой частицы гематита (б).
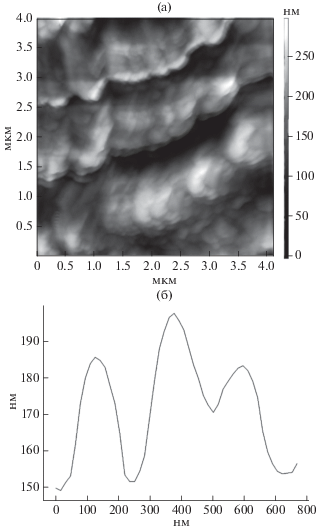
Для другого типа частиц исследованного порошка характерным было наличие зерен овальной формы с размерами от 50 до 150 нм в диаметре (рис. 5а). Кроме того, виден участок поверхности порошка гематита, в котором наблюдается нарушение слоистости: в центре этого участка поверхности порошка возникает слой, идущий вниз, а левее и правее – слои, идущие вверх. Однако и в данном случае также наиболее рельефно микроструктура видна на трехмерных изображениях (рис. 5б).
Рис. 5.
Микроструктура частиц гематита, полученная методом СЗМ (а). Трехмерная микроструктура поверхности частицы гематита, полученная методом СЗМ (б).
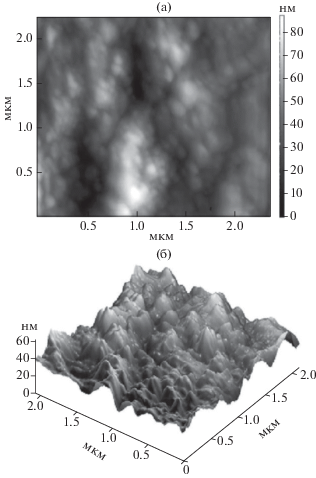
Мессбауэровский спектр исследованного порошка показан на рис. 6, а параметры мессбауэровских спектров представлены в табл. 2. Анализ мессбауэровских данных показал, что в результате магнитоимпульсной обработки возможно появление дополнительной модификации Fe2O3. Существенной особенностью такой модификации (в отличие от α- и γ-Fe2O3) является повышенная концентрация катионных вакансий, их упорядоченное расположение и смещение ионов Fe3+ из положения равновесия, что обеспечивает высокую степень ковалентного переноса электронов от ионов железа на атомы кислорода. Петля магнитного гистерезиса порошка гематита исходного состава представлена на рис. 7, а магнитные характеристики порошка гематита исходного состава и того же порошка после магнитноимпульсной обработки представлены в табл. 3.
Таблица 2.
Параметры мессбауэровского спектра исходного порошка гематитового состава
Компоненты спектра | Изомерный сдвиг δ, мм/с | Квадрупольное расщепление Δ, мм/с | Магнитные поля на ядрах Fe57Нэф, кЭ | Площади компонент S, отн. ед. | Минерал |
---|---|---|---|---|---|
С1(Fe3+) | 0.37 | –0.20 | 517 | 81.6 | Гематит |
С2(Fe3+) | 0.25 | 0.05 | 494 | 4.3 | Магнетит (Feтет) |
С3(Fe3+ + Fe2+) | 0.66 | 0.02 | 461 | 5.9 | Магнетит (Feокт) |
Д1(Fe3+) | 0.42 | 0.24 | 0 | 3.0 | Эгирин |
Д2(Fe2+) | 1.15 | 1.72 | 0 | 5.2 | Доломит |
Таблица 3.
Магнитные характеристики исходного порошка гематита и порошка гематита, подвергнутого магнитоимпульсной обработке
Число импульсов | Намагниченность насыщения Ms, А · м2/кг |
Намагниченность остаточная Mr, А · м2/кг |
Коэрцитивная сила Hc, кА/м | Отношение Mr/Ms | Площадь петли, кЭ · А · м2/кг |
---|---|---|---|---|---|
Исходный | 6.66 | 0.70 | 14.0 | 0.104 | 420.5 |
10 | 6.64 | 0.69 | 13.3 | 0.103 | 608.1 |
30 | 6.64 | 0.70 | 13.7 | 0.106 | 588.0 |
50 | 6.63 | 0.66 | 12.8 | 0.099 | 564.4 |
Согласно результатам мессбауэровской спектроскопии, при комнатной температуре не обнаружено изменений в параметрах сверхтонкой структуры спектров ядерного гамма-резонанса оксидов железа после воздействия от 50 до 80 импульсами. Однако при температуре 550 К и выше температурная зависимость квадрупольного расщепления заметно отличается для исходного оксида железа до и после его обработки магнитными импульсами: для исходного оксида железа наблюдается типичная для α-Fe2O3 зависимость квадрупольного расщепления, а после магнитоимпульсного воздействия (50 импульсов) наблюдается заметное увеличение квадрупольного расщепления при температуре 700 К, что свойственно структуре γ-Fe2O3. Температурная зависимость квадрупольного расщепления Fe2O3, обработанного 80-ю импульсами, имеет характер, не свойственный ни для α-Fe2O3, ни для γ-Fe2O3. Наблюдаемое более резкое изменение квадрупольного расщепления с ростом температуры невозможно связать только со значительным отклонением симметрии локального окружения ионов Fe3+ из положения равновесия. При упорядочении катионных вакансий и смещении ионов Fe3+ из идеальных октаэдрических положений возможно появление дополнительной модификации Fe2O3 (табл. 4). Существенной особенностью такой модификации (в отличие от α- и γ-Fe2O3) является повышенная концентрация катионных вакансий, их упорядоченное расположение и смещение ионов Fe3+ из положения равновесия, обеспечивающих высокую степень ковалентного переноса электронов от ионов железа на атомы кислорода.
ЗАКЛЮЧЕНИЕ
Проведено изучение поверхностной структуры и состава порошков железной руды, гематита, являющегося структурообразующим элементом при изготовлении гексагональных ферритов бария и стронция. Установлено, что исследованный гематитовый порошок, кроме основного минерала (гематита) содержит железосодержащие силикаты и железо- и магнийсодержащие оксиды кальция. Проведенные исследования показали, что в результате обработки слабыми импульсами магнитного поля возможно появление дополнительной модификации Fe2O3. Существенной особенностью такой модификации (в отличие от α- и γ-Fe2O3) является повышенная концентрация катионных вакансий, их упорядоченное расположение и смещение ионов Fe3+ из положения равновесия, что обеспечивает высокую степень ковалентного переноса электронов от ионов железа на атомы кислорода.
БЛАГОДАРНОСТИ
Исследования проведены при частичной финансовой поддержке Министерства образования и науки РФ (проектная часть государственного задания, НИТУ “МИСиС”, соглашение о предоставлении субсидии от 27.06.2014 г. № 14.575.21.0030 (RFMEFI57514X0030)), а также Российского фонда фундаментальных исследований (проект № 16-03-00515).
Список литературы
Бородавко В.И., Ивашко В.С., Клименко С.А., Хейфец М.Л. Обработка и упрочнение поверхностей при изготовлении и восстановлении деталей / Ред. Хейфец М.Л., Клименко С.А. Минск: Беларус. навука, 2013. 463 с.
Бурцев В.М., Васильев А.С., Гемба И.Н. и др. Технология машиностроения: учебн. для вузов: в 2 т. / Ред. Дальский А.М., Кондаков А.И. Т. 1. Основы технологии машиностроения. 3-е изд., испр. и перераб. М.: МГТУ им. Н.Э. Баумана, 2011. 478 с.
Горобей Н.Н., Лукьяненко А.С. // Современное машиностроение. Наука и образование: Матер. IV межд. научно-практической конф. СПб.: СПбГПУ, 2014. С. 1119.
Воробьев В.Ф., Помельникова А.С., Шипко М.Н., Степович М.А. // Поверхность. Рентген., синхротр. и нейтрон. исслед. 2011. № 12. С. 88.
Шипко М.Н., Костишин В.Г., Степович М.А., Коровушкин В.В. // Поверхность. Рентген., синхротр. и нейтрон. исслед. 2017. № 1. С. 89.
Степович М.А., Шипко М.Н., Костишин В.Г., Коровушкин В.В. // Поверхность. Рентген., синхротр. и нейтрон. исслед. 2017. № 2. С. 32.
Альшиц В.И., Даринская Е.В., Колдаева М.В., Петржик Е.А. // Кристаллография. 2003. Т. 48. № 5. С. 826.
Шипко М.Н., Помельникова А.С., Шипко Г.А. Физико-химические особенности технологий поверхностного упрочнения сталей и сплавов. Иваново: ИГЭУ, 2008. 144 с.
Староверов Б.А., Степович М.А., Шипко М.Н. // Промышленные АСУ и контроллеры. 2011. № 8. С. 1.
Шипко М.Н., Степович М.А., Полетаев В.А., Костюк В.Х. // Вестник ИГЭУ. 2011. Вып. 5. С. 49.
Шипко М.Н., Степович М.А., Староверов Б.А., Костюк В.Х. // Промышленные АСУ и контроллеры. 2012. № 1. С. 2.
Заблоцкий А.В., Вирюс А.А., Каминская Т.П. и др. // Нано- и микросистемная техника. 2013. № 7. С. 2.
Вирюс А.А., Каминская Т.П., Шипко М.Н., Степович М.А. // Физика и xимия обработки материалов. 2013. № 2. С. 71.
Каминская Т.П., Коровушкин В.В., Попов В.В. и др. // Поверхность. Рентген., синхротр. и нейтрон. исслед. 2014. № 12. С. 26.
Степович М.А., Шипко М.Н., Коровушкин В.В., Игошин И.П. // Научный поиск. 2013. № 4 (10). С. 63.
Коровушкин В.В., Костишин В.Г., Степович М.А., Шипко М.Н. // Известия РАН. Серия физическая. 2016. Т. 80. № 12. С. 1643.
Shipko M.N., Kostishyn V.G., Korovushkin V.V., Isaev I.M., Stepovich M.A., Tikhonov A.I., Savchenko E.S. // Journal of Nano- and Electronic Physics. 2016. V. 8. № 3. P. 03004.
Коровушкин В.В., Костишин В.Г., Степович М.А., Шипко М.Н. // Известия РАН. Серия физическая. 2016. Т. 80. № 12. С. 1643.
Дополнительные материалы отсутствуют.
Инструменты
Поверхность. Рентгеновские, синхротронные и нейтронные исследования