Поверхность. Рентгеновские, синхротронные и нейтронные исследования, 2019, № 6, стр. 101-108
Изменение структуры и микротвердости быстрозатвердевших фольг алюминиевого сплава 1421 при отжиге
В. Г. Шепелевич 1, И. А. Бушкевич 1, *, Э. Вендлер 2, И. И. Ташлыкова-Бушкевич 3, **
1 Белорусский государственный университет,
220050 Минск, Беларусь
2 Университет им. Ф. Шиллера,
07743 Йена, Германия
3 Белорусский государственный университет информатики и радиоэлектроники,
220013 Минск, Беларусь
* E-mail: uyluana@gmail.com
** E-mail: iya.itb@bsuir.by
Поступила в редакцию 26.06.2018
После доработки 12.10.2018
Принята к публикации 12.10.2018
Аннотация
В работе изучена связь микроструктуры с микротвердостью алюминиевого сплава марки 1421 системы Al–Mg–Li–Zr–Sc, полученного сверхбыстрой закалкой из расплава. Для исследования быстрозатвердевшего сплав использовались следующие методы: растровая электронная микроскопия в комплексе с рентгеноспектральным микроанализом, метод мгновенных ядерных реакций и, измерение микротвердости при изохронном отжиге. Для определения размера выделений вторых фаз, их объемной доли и удельной поверхности межфазной границы в образцах применялся метод секущих. Установлено, что свежезакаленные быстрозатвердевшие фольги сплава состоят из пересыщенного твердого раствора на основе алюминия. Обнаружено неравномерное распределение лития в приповерхностной области фольг, содержание которого достигает 9.0 ат. %. После отжига при температуре 300°C в структуре фольг кроме магнийсодержащих фаз дополнительно обнаружены выделения (Sc, Zr)-содержащей фазы. При изохронном отжиге фольг наблюдается немонотонное изменение микротвердости в интервалах температур 50–100, 150–210, 230–340°C, обусловленное выделением метастабильных и стабильных фаз. Получено, что нагрев фольг сплава до температуры 340°C приводит к увеличению их микротвердости на 23%, а при температурах выше 400°C происходит ее резкое снижение.
ВВЕДЕНИЕ
Одним из важнейших требований к материалам авиационной техники является стабильность свойств в течение эксплуатации. Алюминиевые сплавы с содержанием Mg менее 7 мас. % обладают свойствами, которые в отожженном, закаленном и состаренном состояниях являются практически одинаковыми. Для пересыщенного твердого раствора магния в алюминии характерны достаточно высокая прочность и хорошая коррозионная стойкость одновременно с повышенной пластичностью [1]. Эффект упрочнения в сплавах системы Al–Mg, легированных литием, был открыт в 1965 г. академиком И.Н. Фриндляндером [2]. Для сплавов системы Al–Mg–Li важно отметить, что их прочность сравнима с прочностью других широко используемых в авиации алюминиевых сплавов. За счет введения лития плотность сплава снижается, а модуль упругости возрастает. При этом особенности термической обработки сплавов системы Al–Mg–Li связаны с наличием упрочняющей фазы δ ' (Al3Li), морфологией распада пересыщенного α-твердого раствора, природой выделяющихся дополнительных фаз и соотношения их объемной доли [3]. Однако в крупнозернистом состоянии Al–Mg–Li-сплавы демонстрируют ограниченную технологическую пластичность и низкие служебные свойства, связанные с локализацией деформации.
В настоящее время большинство алюминиевых сплавов легируют добавками редкоземельных и переходных металлов для повышения их прочностных и коррозионных свойств. Эффект введения Sс обеспечивает в сплавах системы Al–Mg более высокий рост прочностных характеристик, по сравнению с такими, часто используемыми антирекристаллизаторами алюминия, как Mn и Zr [4–6]. О высокой радиационной стойкости сплавов Al–Mg со скандием сообщается в работах [7–9]. Перспективным также считается использование Sc вместе с Zr. Известно, что всего лишь 0.1–0.2 мас. % скандия и циркония увеличивают прочность алюминия в три раза [10]. Цирконий, вводимый вместе со скандием, не только замещает часть дорогостоящего скандия, но вместе с тем дополнительно придает сплавам на основе алюминия высокую прочность, свариваемость и коррозионную стойкость [11], что особенно важно в авиационной технике.
Большое количество работ, посвященных изучению микроструктуры, фазового состава и механических свойств, выполнено для литых образцов промышленного сплава марки 1421 системы Al–Mg–Li–Zr–Sc [12–14]. Однако с целью улучшения свойств сплава активно проводится поиск современных методов модифицирования его структуры: используются методы, основанные на воздействии импульсным лазерным излучением [15], и методы интенсивной пластической деформации (например, равноканальное угловое прессование (РКУП) [16–18]). Поэтому можно заключить, что использование методов сверхбыстрой закалки из расплава (СБЗР) [19] также представляет научный и практический интерес для улучшения физико-механических свойств сплава 1421 и разработки новых алюминиевых сплавов для эксплуатации при повышенных температурах. При СБЗР происходит значительное диспергирование структурных составляющих материала, включая измельчение зерен, уменьшаются размеры частиц вторых фаз, образуются аномально пересыщенные твердые растворы и формируются метастабильные промежуточные фазы.
В данной работе определены морфология, элементный и фазовый состав сплава 1421, полученного при высокоскоростной кристаллизации из расплава, а также выполнено исследование изменения микроструктуры и микротвердости быстрозатвердевших (БЗ) фольг сплава 1421 при отжиге. С этой целью были применены метод растровой электронной микроскопии (РЭМ) с использованием рентгеноспектрального микроанализа (РСМА), метод мгновенных ядерных реакций (МЯР). Методом случайных секущих определены параметры микроструктуры сплавов. Измерена микротвердость по Виккерсу исходных и отожженных образцов.
МЕТОДИКА ЭКСПЕРИМЕНТА
Исследуемые в работе фольги промышленного сплава 1421, элементный состав которого Al–(5.5 мас. %)–Mg(2.2 мас. %)–Li(0.12 мас. %)–Zr(0.2 мас. %)–Sc (0.2 мас. %), были получены сверхбыстрой закалкой из жидкой фазы методом одностороннего охлаждения. Кристаллизация тонкого слоя расплава осуществлялась на внутренней поверхности медного цилиндра диаметром 20 см, вращающегося с частотой 1500 об./мин. Скорость охлаждения расплава была порядка 106 К/с [20]. Толщина изученных фольг составила 40–80 мкм. Для сравнения использовался массивный образец в форме параллелепипеда, вырезанный из литого однородного сплава 1421 и подвергнутый изотермическому отжигу при температуре 300°C в течение 5 ч. Для измерения размера выделений вторых фаз, их объемной доли V и удельной поверхности межфазных границ S в образцах применялся метод секущих [21] с относительной погрешностью 8%.
Морфологию и элементный состав поперечного сечения свежезакаленных фольг, отожженных при температуре 300°C в течение 1 ч, а также гомогенизированного литого образца исследовали, используя растровый электронный микроскоп LEO1455VP с приставкой “HKL CHANNEL5”. Измерения проводили при ускоряющем напряжении 20 кВ в режиме отраженных электронов. Диаметр области генерации рентгеновского излучения составлял около 3 мкм.
Содержание лития в приповерхностной области обеих сторон фольг: поверхности А, контактирующей при закалке с подложкой (медным цилиндром), и противоположной поверхности Б, контактирующей с воздухом, исследовалось методом МЯР с использованием ядерной реакции 7Li(p, α)4 He при энергии протонов 1.4 МэВ, угол обратного рассеяния θ составлял 170°. Данные измерения проводились на ускорителе-тандентроне (3 МэВ) JULIA (JenaUniversity Laboratory for Ion Acceleration), разрешение детектора составляло 15 кэВ. Концентрация лития в фольгах была определена методом МЯР с погрешностью 11% при использовании полученного при тех же условиях и геометрии, что и в настоящих экспериментах, эталонного спектра МЯР от образца из ниобата лития (LiNbO3), содержащего 20.0 ат. % Li [22].
Микротвердость Hµ измеряли с помощью прибора ПМТ-3 с использованием нагрузки 50 г и временем выдержки 60 с. Было исследовано изменение Hµ фольг от времени выдержки при комнатной температуре и при изохронном отжиге. Изохронный отжиг фольг проводился от комнатной температуры до 450°C с интервалом 20°C и выдержкой 30 мин при каждой температуре. Погрешность измерения микротвердости составила 4%.
РЕЗУЛЬТАТЫ И ИХ ОБСУЖДЕНИЕ
Методы РЭМ и РСМА показали, что в объеме свежезакаленных фольг сплава 1421 отсутствуют включения вторых фаз (рис. 1а), т.е. БЗ сплав является пересыщенным α-твердым раствором. На рис. 1в показана микроструктура литого сплава 1421 в обратно отраженных электронах. Результаты локального анализа элементного состава фаз в литом образце приведены в табл. 1. Данные о содержании лития в образце в табл. 1 не представлены из-за ограничений метода РСМА при определении элементов легче бериллия [23].
Рис. 1.
РЭМ-изображения поперечных сечений свежезакаленной (а), отожженной при 300°C (б) фольги и литого образца (в) сплава 1421. Цифрами обозначены области, в которых методом РСМА определяли локальный химический состав образца.
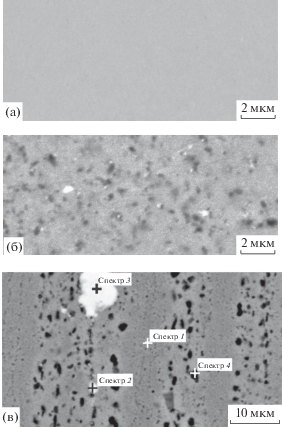
Таблица 1.
Локальный химический состав фаз в гомогенизированном слиткe из сплава 1421
Область анализа | Содержание элементов, мас. % (ат. %) | ||||
---|---|---|---|---|---|
O | Mg | Al | Sc | Zr | |
1 | 0.80 (1.34) |
5.40 (5.92) |
93.80 (92.74) |
– | – |
2 | 1.02 (1.80) |
3.31 (3.84) |
83.35 (88.16) |
7.19 (4.59) |
5.13 (1.61) |
3 | 0.99 (1.96) |
1.37 (1.78) |
68.81 (80.42) |
16.52 (11.59) |
12.31 (4.26) |
4 | 1.27 (2.10) |
5.27 (5.76) |
93.47 (92.13) |
– | – |
Содержание лития для обеих поверхностей фольги сплава 1421 определяли на пучке протонов с помощью резонанса в реакции 7Li(p, α)4 He. Поскольку энергия испущенных α-частиц (продуктов данной ядерной реакции) намного превышает энергию налетающих на образец протонов, это дает возможность бесфоновой регистрации лития, присутствующего в фольге. Сигнал МЯР от лития наблюдается на канале с номером 419 (рис. 2а). Для сравнения на рис. 2б также представлен спектр МЯР эталонного образца LiNbO3 с концентрацией Li 20.0 ат. % [22]. Как видно на рис. 2, экспериментальный и эталонный спектры МЯР подобны. Это позволяет оценочно рассчитать, что содержание лития в приповерхностных слоях фольги составляет примерно 9.0 ат. %, превышая в ∼17 раз расчетное содержания лития в сплаве 1421. Обнаруженный факт обогащения поверхности фольг литием свидетельствует о его неоднородном распределении по их толщине. Данный эффект, по-видимому, вызван действием поверхности фольг и границ зерен как стоков для комплексов “закалочные вакансии–атомы растворенных элементов” [24, 25] и наблюдался нами ранее в БЗ-бинарных сплавах алюминия Al–Ti, V, Cr, Mn, Fe, Co, Ni, Cu, Zn, Ge, Sb [26, 27]. Диффундируя из объема на поверхность образцов, атомы Li (который является активным легкоокисляемым элементом) вступают в реакцию с кислородом воздуха, образуя соединение Li2CO3. В работах [28, 29] сообщается о том, что оксидная пленка на поверхности сплава 1421, полученного методом РКУП, после лазерного импульсного воздействия состоит в основном из Li2CO3 и MgO, как и в случае отожженных при температуре 450°C образцов сплава 1420 (близкого по составу к сплаву 1421).
Рис. 2.
Спектры МЯР от поверхностей А и Б фольги сплава 1421 (а) и эталонного образца из ниобата лития (LiNbO3) (б), полученные под углом θ = 170° при бомбардировке мишеней протонами с энергией 1.4 МэВ.
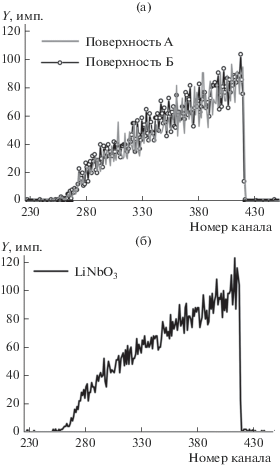
При исследовании микроструктуры литого образца сплава 1421 наблюдается твердый раствор алюминия (табл. 1, область 1 на рис. 1в) с выделениями интерметаллидных фаз. Наряду с выделениями магнийсодержащих фаз, в виде темных частиц обнаружены светлые неравномерно распределенные включения, содержащие Mg, Al, Sc и Zr (области 2, 3 в табл. 1), что указывает на образование соединения Al3(Sc,Zr) [30, 31], в состав которого также могут входить атомы Li [32]. В более поздних работах [18, 33, 34] вместо выше указанной фазы в образцах сплава 1421, полученных в неравновесном состоянии после РКУП, было установлено существование фазы более сложного состава Al(Mg, Sc, Zr, Li)x. Частицы этой фазы, благодаря присутствию в них атомов скандия и циркония, могут быть стабильными и сохраняться до высоких температур.
Размер темных выделений (рис. 1в) меньше области генерации рентгеновского излучения при РСМА, что затрудняет определение локального химического состава магнийсодержащих фаз. Измерения показали, что представленные в табл. 1 данные, полученные для соответствующей области 4 образца, близки к значениям, определенным в области 1 (рис. 1в). Для уточнения состава темных выделений было дополнительно выполнено сканирование распределения элементов в литом образце вдоль линии. Результаты, представленные на рис. 3, показали, что содержание магния в крупных темных выделениях составляет в среднем около 6.0 мас. % (6.1 ат. %). Поэтому можно заключить, что выделения указанной второй фазы соответствуют β-фазе (Al3Mg2) [1, 35]. При этом отметим, что в литом образце сплава 1421 после гомогенизации также могут присутствовать частицы фазы S1 (Al2MgLi), которая, как и β-фаза, выделяется в сплавах системы Al–Mg–Li после выдержки при температуре 300°C [36]. Однако в рамках данного исследования фазы β и S1 не могут быть различимы методами РЭМ и РСМА, и поэтому в дальнейшем здесь будут указываться как магнийсодержащие фазы.
Рис. 3.
РЭМ-изображение литого образца (а) сплава 1421 и данные РСМА, выполненного вдоль заданной линии сканирования, для магния (б), кислорода (в), алюминия (г).
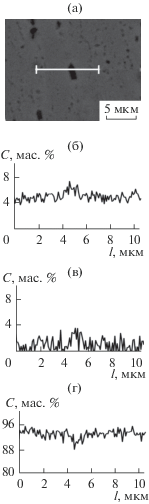
После отжига БЗ фольг при температуре 300°C обнаружено, что (как показано на рис. 1б) в их микроструктуре наблюдаются выделения магнийсодержащих фаз, а также частицы (Sc, Zr)-содержащей фазы, средняя длина хорд которых составляет 0.18 и 0.20 мкм соответственно. Гистограммы распределения по размерным группам хорд случайных секущих на сечениях интерметаллидных частиц в поперечном сечении отожженных фольг, представлены на рис. 4а. Для темных и светлых выделений основная часть хорд попадает в первую размерную группу от 0.05 до 0.15 мкм и во вторую размерную группу от 0.15 до 0.25 мкм соответственно. Выделения этих фаз мелкодисперсны в отличие от выделений вторых фаз в литом образце, где (рис. 4б, в) основная часть хорд на сечениях темных и светлых выделений попадает в размерную группу от 0.3 до 0.5 мкм и в размерную группу от 0.5 до 1.5 мкм соответственно.
Рис. 4.
Распределение хорд сечений выделений магнийсодержащих фаз (◼) и (Sc, Zr)-содержащей фазы (◻) по размерным группам в отожженной при 300°С фольге (а) и литом образце (б, в) сплава 1421.
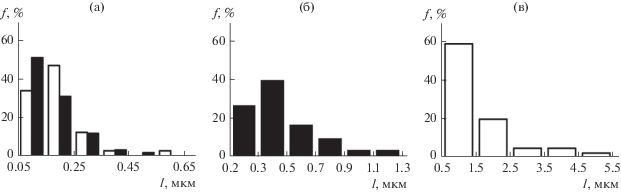
Найдено, что суммарная объемная доля выделений магнийсодержащих фаз в отожженной фольге и гомогенизированном массивном образце приблизительно одинакова и составляет 3.4 и 2.9% соответственно. Однако в результате дисперсности темных выделений в БЗ сплаве после отжига их удельная поверхность межфазных границ возрастает с 0.21 мкм–1 в литом образце до 0.51 мкм–1 в отожженной фольге. Для (Sc, Zr)-содержащей фазы обнаружено, что объемная доля светлых выделений увеличивается (если в литом образце она составляет 0.35%, то в отожженной фольге − 0.46%). Удельная поверхность межфазных границ светлых выделений в литом образце и отожженной фольге составляет 0.08 и 0.40 мкм–1 соответственно, т.е. S возрастает в пять раз с уменьшением размеров частиц при увеличении V на 30% в фольгах после отжига по сравнению с литым образцом.
На рис. 5а представлено изменение микротвердости БЗ сплава 1421 с течением времени выдержки при комнатной температуре. Получено, что микротвердость свежезакаленных фольг составляет 965 МПа, что на 35% больше, чем для литых образцов, для которых Hµ = 627 МПа. Определено, что выдержка фольг в течение 5 ч приводит к увеличению микротвердости на 19%. В дальнейшем Hµ образцов остается практически неизменной. Данное изменение микротвердости в зависимости от времени выдержки можно объяснить образованием повышенной концентрацией вакансий при сверхбыстрой закалке из жидкой фазы. При комнатной температуре вакансии активно диффундируют и формируют кластеры с легирующими элементами, вызывая тем самым увеличение микротвердости при выдержке фольг.
Рис. 5.
Зависимость микротвердости фольг от времени выдерживания при комнатной температуре (а) и от температуры изохронного отжигa (б).
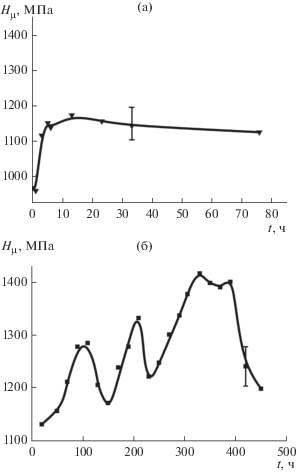
Зависимость микротвердости фольг сплава 1421 от температуры изохронного отжига представлена на рис. 5б. Наблюдается немонотонное изменение Hµ от температуры нагрева. В интервалах температур 50–100°C, 150–210°C, 230–340°C происходит увеличение микротвердости, а затем ее уменьшение. Сложный характер изменения Hµ фольг при изохронном отжиге свидетельствует о протекании структурно-фазовых превращений в БЗ сплаве.
При отжиге БЗ сплава 1421 на начальном этапе наблюдается низкотемпературный максимум микротвердости при температуре около 100°C (рис. 5б). Данное начальное увеличение Hµ фольг можно связать с образованием кластеров легирующих элементов, в котором принимают участие вакансии, образовавшиеся в процессе получения фольг. При дальнейшем росте температуры отжига до 150°C снижение микротвердости целесообразно связать с распадом данных кластеров [37]. Подобный эффект влияния кластеров легирующих элементов на микротвердость при отжиге ранее сообщался нами для БЗ-фольг сплава АMг6 системы Al–Mg–Mn [38] и сплава 6061 системы Al–Mg–Si [39].
Следующий этап изменения микротвердости фольг сплава 1421 объясняется выделением интерметаллидных фаз, содержащих литий. Как было получено для БЗ- порошков сплавов Al–Li–Mg–Zr [40], количество выделений метастабильной δ'-фазы(Al3Li) растет в интервале температур отжига 110–190°С. Дальнейший отжиг порошков вызывает растворение δ'-фазы при 230°С. Дополнительно отметим, что кроме δ'-фазы в сплаве 1421 при отжиге выделяется также упрочняющая фаза S1(Al2MgLi) [40, 41], однако наибольшая плотность ее выделений наблюдается в диапазоне температур 270–370°C.
Рост микротвердости в интервале 260–340°C и последующее плато на кривой зависимости микротвердости от температуры изохронного отжига до 400°C объясняется совместным действием S1-фазы и фазы Al(Mg, Sc, Zr, Li)x, мелкодисперсные выделения которой обнаружены в отожженных при 300°C фольгах (рис. 1б). Как известно, плотность выделений данной (Sc, Zr)-содержащей фазы в ультра мелкозернистых образцах сплава 1421, полученных методом РКУП, максимальна в интервале 340–410°C [34]. Значительное уменьшение микротвердости при нагреве фольг сплава выше 400°C, по-видимому, обусловлено процессами укрупнения интерметаллидных выделений, затем их растворения, а также процессами рекристаллизации [42], сопровождающимися ростом зерен. Дополнительно отметим, что процессы выделения метастабильной β'-фазы (Mg5Al8) начинаются при 47°C и протекают до температуры 277°C [35, 43]. Стабильная β-фаза образуется или при температурах отжига около 200°C из β'-фазы, или непосредственно из пересыщенного твердого раствора при температурах выше 277°C до 375–400°C (рис. 1а). При этом согласно полученным в настоящей работе результатам, данные фазы не оказывают существенного вклада в изменение микротвердости фольг сплава 1421 при отжиге в отличие от БЗ фольг сплавов Al–Mg–Ni и Al–Mg–Fe [38, 39], а также сплавов Al–Mg после интенсивной пластической деформации кручением [44–46]. Для указанных сплавов алюминия, содержащих магний, увеличение микротвердости материалов наблюдается в интервале температур отжига 160–250°C.
В настоящее время в зарубежных лабораториях сплав 1421 не исследован, так как за границей его аналоги имеют другой состав. С одной стороны, это объясняется трудностями при плавке и литье сплавов системы Al–Mg–Li с высокой степенью легирования, достигающей ~11.0 ат. % в сплаве 1421. С другой стороны, для улучшения комплекса механических свойств в алюминиевом сплаве 1421 используется скандий в качестве модифицирующей добавки, но широкое применение Sc ограничивается его высокой ценой и малыми объемами производства. Однако Россия располагает достаточными запасами скандиевого сырья, о чем свидетельствуют успехи ОК “РУСАЛ” в производстве оксида скандия с чистотой более 99% [47]. Поэтому изучение свойств материалов на основе Al, легированных Sc, является актуальной задачей материаловедения.
Полученные в данной работе результаты указывают на перспективность изучения влияния микроструктуры и фазового состава на физико-механические свойства БЗ сплава 1421 для оптимизации режимов его термической обработки, которые определяются термической стабильностью упрочняющих фаз. Установленный рост микротвердости фольг при дополнительной термической обработке представляет практический интерес для улучшения обрабатываемости сплава. Эффект влияния формирования мелкодисперсной (Sc, Zr)-содержащей фазы при температурах около 300°C на механические свойства фольг требует дополнительных исследований, поскольку данная температура удовлетворяет условиям эксплуатации при повышенных температурах и близка к оптимальной для получения массивных образцов путем компактирования.
ЗАКЛЮЧЕНИЕ
Таким образом, исследования, проведенные в настоящей работе, показали, что применение сверхбыстрой закалки из расплава позволяет модифицировать микроструктуру промышленного алюминиевого сплава 1421 и получить фольги с микрокристаллической структурой, которые состоят из пересыщенного твердого раствора. Установлено неоднородное распределение компонентов в объеме БЗ сплава. Поверхность обогащена литием, содержание которого в приповерхностной области обеих сторон фольг более чем в ~17 раз превышает его расчетную концентрацию в сплаве. Отжиг фольг при температуре 300°C в течение 1 ч приводит к распаду пересыщенного раствора и выделению магнийсодержащих фаз и (Sc, Zr)-содержащей фазы, объемная доля частиц которых составляет 3.4 и 0.46% соответственно. Удельная поверхность межфазных границ для выделений магнийсодержащих фаз и (Sc, Zr)-содержащей фазы в отожженной фольге составляет 0.51 и 0.40 мкм–1 соответственно.
При изохронном отжиге быстрозатвердевших фольг происходит немонотонное изменение микротвердости, обусловленное выделением метастабильных и стабильных фаз в различных температурных интервалах. Установлено увеличение микротвердости фольг в интервалах температур 50–100°C, 150–200°C, 230–340°C. Присутствие выделений интерметаллидных фаз, размер которых не превышает 1 мкм, приводит к дисперсионному упрочнению в процессе отжига сплава 1421, полученного высокоскоростной кристаллизацией, а также тормозит процессы рекристаллизации, обеспечивая плато на кривой зависимости микротвердости от температуры изохронного отжига в интервале температур 340−400°C.
Список литературы
Фриндляндер И.Н. Алюминиевые деформируемые конструкционные сплавы. М.: Металлургия, 1979. 208 с.
Фридляндер И.Н., Шамрай В.Ф., Ширяева Н.В. // Металлы. 1965. № 2. С. 153.
Колобнев Н.И. // Металловедение и термическая обработка металлов. 2002. № 7. С. 30.
Могучева А.А., Кайбышев Р.О. // Физика металлов и металловедение. 2008. Т. 106. № 4. С. 439.
Buranova Yu., Kulitskkiy V., Peterlechner M., Mogucheva A., Kaibyshev R., Divinski S.V., Wilde G. // Acta Mater. 2017. V. 124. P. 210.
Яценко С.П., Пасечник Л.А., Скачков В.М. // Наука и техника. 2015. № 3. С. 32.
Платонов Ю.М., Иванов Л.И., Заболотный В.Т., Лазоренко В.М., Товтин В.И. // Цветные металлы. 2011. № 10. С. 82.
Мухачев А.П., Харитонова Е.А., Скипочка Д.Г. // Вопросы атомной науки и техники. 2016. № 1. С. 45.
Яценко С.П., Рубинштейн Г.М., Скачков В.М. // Сб. докл. 5-й междунар. науч.-практ. конф. в рамках специализир. форума “ExpoBuildRussia”. Екатеринбург: УМЦ УПИ, 2016. С. 75.
Захаров В.В., Елагин В.И., Ростова Т.Д., Филатов Ю.А. // Технология легких сплавов. 2010. № 1. С. 67.
Корягин Ю.Д., Смирнов М.A., Чернов С.С., Карева Н.Т. // Вестник ЮУрГУ. 2010. № 34.С. 58.
Belov N.A., Eskin D.G., Aksenov A.A. Multicomponent Phase Diagrams: Applications for Commercial Aluminum Alloys. Oxford: Elsevier Science, 2005. 424 p.
Давыдов В.Т., Елагин В.И., Захаров В.В., Ростова Т.Д. // Цветные металлы и сплавы. 1996. № 8. С. 25.
Гopбyнoв Ю.A. // Engineering & Technologies. 2015. T. 5. № 8. C. 636.
Кикин П.Ю., Пчелинцев А.И., Русин Е.Е., Землякова Н.В. // Металловедение и термическая обработка металлов. 2012. № 8. С. 23.
Мишин И.П. // Научное обозрение. Технические науки. 2014. № 2. С. 64.
Mogucheva A., Kaibyshev R. // Metals. 2016. № 6. P. 254.
Kaibyshev R., Shipilova K., Musin F., Motohashi Y. // Mater. Sci. Technol. 2005. V. 21. № 4. P. 408.
Кузей А.М. Структурно-фазовые превращенияв быстрозакаленных алюминиевых сплавах. Минск: Беларуская навука, 2011. 399 с.
Мирошниченко И.С. Закалка из жидкого состояния. М.: Металлургия, 1982. 168 с.
Салтыков С.А. Стереометрическая металлография. М.: Металлургия, 1976. 272 с.
Schmidt E., Ritter K., Gartner K., Wendler E. // Nucl. Instr. Meth. Phys. Res. B. 2017. V. 409. P. 126.
Векилова Г.В., Иванов А.Н., Ягодкин Ю.Д. Дифракционные и микроскопические методы и приборы для анализа наночастиц и наноматериалов. М.: Изд. Дом МИСиС, 2009. 145 с.
Hirosawa S., Sato T., Kamio A., Flower H.M. // Acta Mater. 2000. V. 48. P. 1797.
Löchte L., Gitt A., Gottstein G., Hurtado I. // Acta Mater. 2000. V. 48. P. 2969.
Tashlykova-Bushkevich I.I. // Proc. 12th Int. Conf. Aluminium Alloys (ICAA12), Yokohama: TMS, 2010. P. 1800.
Tashlykova-Bushkevich I., Itoh G. // Mater. Sci. Forum. 2012. V. 706-709. P. 301.
Кикин П.Ю. Перевезенцев В.Н., Русин Е.Е., Разов Е.Н. // Физика и химия обработки материалов. 2012. № 1. С. 18.
Кикин П.Ю., Пчелинцев А.И., Русин Е.Е. // ЖТФ. 2012. Т. 82. № 2. С. 46.
Елагин В.И., Захаров В.В., Павленко С.Г., Ростова Т.Д. // Физика металлов и металловедение. 1985. Т. 60. № 1. С. 97.
Fuller C.B., Seidman D.N. // Acta Mater. 2005. V. 53. № 20. P. 5415.
Лукина Е.А., Алексеев А.А., Антипов В.В., Зайцев Д.В., Клочкова Ю.Ю. // Металлы. 2009. № 6. С. 60.
Найденкин Е.В., Колобов Ю.Р., Голосов Е.В., Мишин И.П. // Физическая мезомеханика. 2006. № 9. С. 133.
Islamgaliev R.K., Yunusova N.F., Valiev R.Z., Tsenev N.K., Perevezentsev V.N., Langdon T.G. // Scripta Mater. 2003. V. 49. P. 467.
Хэтч Дж.Е. Алюминий: свойства и физическое металловедние. М.: Металлургия, 1989. 422 с.
Колобнев Н.И., Хохлатова Л.Б., Семенова Е.Ю. // Металловедение и технология легких сплавов. 1990. С. 63.
Гольдштейн М.И., Литвинов В.С., Бронфин Б.М. Металлофизика высокопрочных сплавов. М: Металлургия, 1986. 312 с.
Шепелевич В.Г. // Вестник ГГТУ им. П.О. Сухого. 2007. № 1. С. 12.
Гусакова С.В., Сукие М., Шепелевич В.Г. // Cб. трудов 7-й Всероссийской с международным участием научно-технической конференции. М.: МАТИ, 2008. С. 87.
Yu G.-F., Zhang S.-Q., Feng Y.-S., Chai S.-C. // Mater. Sci. Eng. A. 1991. V. 133. P. 274.
Бецофен С.Я., Антипов В.В., Князев М.И. // Деформация и разрушение материалов. 2015. № 11. С. 10.
Гутько Е.С., Шепелевич В.Г. // Физика и химия обработки материалов. 2005. № 4. С. 81.
Землякова Н.В., Кибиткин В.В. // Вестник Тамбовского университета. Серия Естественные и технические науки. 2016. Т. 21. № 3. С. 1000.
Сивцова П.А., Шепелевич В.Г. // Сб. трудов VII Всероссийской с международным участием научно-технической конференции. М.: МАТИ, 2008. С. 10.
Шепелевич В.Г. // Вестник БГУ. Сер. 1, Физика. Математика. Информатика. 2014. № 2. С. 13.
Ценев Н.К., Перевезенцев В.Н., Щербань М.Ю., Ценев А.Н. // ЖТФ. 2010. № 6. С. 68.
Пягай И.Н. // Цветные металлы. 2016. № 7. С. 43.
Дополнительные материалы отсутствуют.
Инструменты
Поверхность. Рентгеновские, синхротронные и нейтронные исследования