Поверхность. Рентгеновские, синхротронные и нейтронные исследования, 2019, № 7, стр. 74-81
Влияние микроструктуры металлокерамических порошков на эксплуатационные характеристики газотермических покрытий
А. Е. Чесноков 1, *, А. В. Смирнов 1, И. С. Батраев 2, **
1 Институт теоретической и прикладной механики им. С.А. Христиановича СО РАН
630090 Новосибирск, Россия
2 Институт гидродинамики им. М.А. Лаврентьева СО РАН
630090 Новосибирск, Россия
* E-mail: chae@itam.nsc.ru
** E-mail: ibatraev@gmail.com
Поступила в редакцию 28.07.2018
После доработки 28.09.2018
Принята к публикации 15.11.2018
Аннотация
Проводится сравнительный анализ эксплуатационных характеристик газотермических покрытий, в частности детонационных покрытий, полученных из коммерческого порошка на основе карбида вольфрама WC−Со (12 мас. %) (1342VM, Praxair, США) и металлокерамического порошка состава TiC−Ме (19 об. %) (Ме = NiCr, Co), полученного методом самораспространяющегося высокотемпературного синтеза с последующей сфероидизацией в плазменной струе. Показано, что частицы карбида металлокерамического порошка размером более 3 мкм имеют структурные дефекты в виде трещин и пор. Феноменологически объяснено их возникновение. Установлено, что сфероидизированные частицы наследуют внутреннюю микроструктуру. Они плотные, в то время как пористость частиц на основе карбида вольфрама WC−Со (12 мас. %) достигает 40%. Обнаружено влияние плотности частиц на коэффициент использования порошка и на пористость покрытий. При напылении плотного порошка уменьшается коэффициент его использования от 54 до 33% и увеличивается пористость покрытий от 0.4 до 1.78%. Наилучшей износостойкостью обладает покрытие состава WC−Со (19 об. %) вследствие осколочной формы частиц карбидов размером порядка 1 мкм.
ВВЕДЕНИЕ
Ранее в [1, 2] проведен сравнительный анализ детонационных металлокерамических покрытий. Порошки для напыления получены механическим измельчением компактов, синтезируемых методом самораспространяющегося высокотемпературного синтеза (СВС) из механоактивированных порошковых композиций титан–углерод–нихром и их последующего рассева на фракции 20–45, 45–56, 56–71, 71–90 мкм. Анализ показал, что эксплуатационные свойства покрытия состава TiC–NiCr не уступают покрытиям, полученным из коммерческого порошка Cr3C2− NiCr (21 об. %) (марка 1375VM, Prаxair, США). В результате изучения основных эксплуатационных свойств и микроструктуры покрытий было дано феноменологическое описание абразивной стойкости металлокерамических покрытий состава ТiC–NiCr (n об. %) (n = 30, 40 и 50), характеризующихся максимальным и минимальным объемным износом материала. Установлено, что существуют критические значения размеров карбидных включений и их объемной доли в металлическом связующем, при которых повышается износ покрытия.
В настоящее время можно выделить основной коммерческий порошок состава WC–Co (12 мас. %), используемый для напыления покрытий на поверхность критических узлов высоконагруженных трибомеханических систем [3–5]. Покрытия на основе карбида вольфрама характеризуются высокой износостойкостью, что подтверждают многочисленные работы, в которых авторы исследовали их трибологические свойства [6–8].
Также необходимо отметить, что форма и внутренняя структура напыляемых частиц оказывают значительное влияние на режимы напыления, а также на микроструктуру, физические и механические свойства покрытий. Например, в [9] были показаны преимущества использования сфероидизированных, имеющих в своем составе в основном полые частицы, порошков Al2O3 для термического напыления по сравнению с плотными порошками, полученными измельчением компакта. В частности, для детонационных покрытий при переходе от плотного порошка к сфероидизированному плотному порошку пористость покрытий уменьшается более чем в два раза, а при переходе от плотного порошка к сфероидизированному порошку с полыми частицами уменьшается на порядок. В то же время коэффициент использования порошка составляет 23, 40 и 51%, соответственно, а максимальная микротвердость покрытий достигается при напылении полых частиц.
В этой связи представляет интерес исследование эксплуатационных характеристик детонационных покрытий из металлокерамических сфероидизированных порошков состава TiC−Ме (19 об. %) (Ме = NiCr, Cо), полученных методом СВС, и их сравнение с характеристиками детонационных покрытий, полученных из коммерческого порошка WC−Cо (12 мас. %) (марка 1342VM, Prаxair, США).
ПОЛУЧЕНИЕ ПОРОШКОВОГО ПРОДУКТА ДЛЯ ДЕТОНАЦИОННОГО НАПЫЛЕНИЯ И СВОЙСТВА МЕТАЛЛОКЕРАМИЧЕСКИХ ЧАСТИЦ
Известно, что большие перспективы получения композиционных порошков открываются при использовании СВС, инициируемого в порошках-реагентах, однородно перемешанных с инертным порошком с заданным объемным содержанием. Порошковый продукт получают в процессе механического измельчения синтезированного компакта и разделения его по фракциям. Для металлокерамических частиц характерна осколочная форма. Дальнейшая обработка в плазменной струе, при которой происходит нагрев частиц до температуры плавления металлической матрицы и ее перегрева, позволяет получать сферические металлокерамические частицы.
Синтез металлокерамического сплава в свободном режиме горения осуществляли в порошковой смеси титана (марки ПТОМ2), ламповой сажи (марки П803), кобальта (марки К0) и никель-хромового сплава (марки ПХ20Н80-56-24). Механическую обработку исходных порошков титана и кобальта с частицами размером 20–40 мкм проводили в энергонапряженной планетарной мельнице “Активатор–2SL”. Титан совместно с 10% поверхностно-активного вещества (ламповой сажи) обрабатывали в течение 90 с. Порошковая смесь стехиометрического состава состояла из 81 об. % (Тi + C) и 19 об. % Me (Me = Co, NiCr), которые соответствовали объемной доле металлического связующего коммерческого материала WC−Co (12 мас. %) (марка 1342VM, Prаxair, США). Затем полученная смесь подвергалась механической обработке в течение 60 с. Предварительно реактор продували аргоном и производили поджиг реакционной смеси.
Все синтезированные компакты имели пористую структуру, благодаря которой при кратковременном механическом воздействии они достаточно легко разрушались. Дальнейшая классификация порошкового продукта на вибростенде с использованием аналитических сит позволяла выделять металлокерамические частицы основной фракции с размерами от 20 до 90 мкм.
Рентгенофазовый анализ синтезированного металлокерамического порошка состава TiC−Ме (Ме = NiCr, Co) показал фазы карбида титана и металлического связующего. Частицы полученного порошкового продукта имели форму осколков, в них по всему объему металлического связующего равномерно распределены ультрадисперсные карбидные включения. Размер карбидных включений лежит в широком диапазоне – от десятков нанометров до 15 мкм. Как показано в [1], уменьшение содержания металлического связующего в составе синтезируемого металлокерамического компакта приводит к увеличению размеров карбидного зерна. Изображения частиц получали с помощью растрового электронного микроскопа Evo MA15 (Carl Zeiss) с использованием детектора BSD. Общий вид металлокерамических частиц и их шлиф для фракции 20–45 мкм, далее используемой в работе, представлен на рис. 1.
Рис. 1.
Общий вид (а, б) и шлифы (в, г) металлокерамических частиц состава TiC−Co(19 об. %) (а, в) и TiC−NiCr(19 об. %) (б, г).
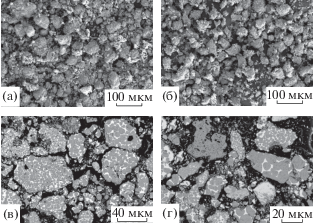
Особенностью структуры частиц карбидов, размер которых больше 3 мкм, является внутренняя дефектность, выраженная в виде продольных трещин и газовых пор. Для объяснения формирования неоднородной структуры карбида воспользуемся соображением, приведенным в [1] в предположении одномерного характера движения фронта горения в порошковой смеси в присутствии металлического связующего с температурой плавления ниже температуры плавления титана (T = 1958 К). Перед фронтом горения порошковой композиции Ti−C−Ме (Ме = NiCr, Co) первоначально возникает слой, в котором частицы металлического связующего плавятся, в то время как ультрадисперсные частицы титана остаются еще в твердом состоянии. Хорошая смачиваемость титана позволяет распределиться жидкому металлическому связующему по отдельным частицам порошка и их агломератам, которые локализуются в объеме расплава. Низкое объемное содержание металлического связующего в составе смеси реагентов приводит к локализации более крупных блоков, состоящих из ультрадисперсных частиц титана и сажи. В отдельных микрообъемах, локализованных металлическим расплавом связующего, можно рассматривать СВС системы Ti–С, который осуществляется в условиях твердофазного горения. Поскольку СВС происходит в свободном режиме горения, а синтез в отдельных микрообъемах протекает в условиях твердофазного горения, то результатом является карбид титана, представляющий собой ячеисто-пористый каркас. В металлическом расплаве СВС отдельного блока происходит в ограниченном объеме, который препятствует росту отдельных карбидных зерен, что приводит к их спеканию по границам контакта. Однако давление, создаваемое расплавом металлического связующего, недостаточно для формирования однородной структуры карбида, что приводит к возникновению указанных выше дефектов. Формирование округлой формы блока карбида титана обусловлено синтезом в расплаве металлического связующего.
Обработку порошка проводили с помощью плазмотрона 2 (рис. 2) с межэлектродной вставкой мощностью до 50 кВт, установленного на водоохлаждаемом реакторе 4, который позволял проводить обработку порошковых материалов в контролируемой атмосфере. Применяли одностороннюю инжекцию обрабатываемого порошка непосредственно перед выходным сечением сопла плазмотрона. Смесь аргон–гелий использовали в качестве основного плазмообразующего газа. В качестве транспортирующего газа для ввода порошка в плазменную струю из дозатора 3 также применяли аргон.
Рис. 2.
Принципиальная схема экспериментальной установки: 1 – баллоны с плазмообразующим газом; 2 – плазмотрон с межэлектродной вставкой; 3 – порошковый дозатор; 4 – водоохлаждаемый реактор; 5 – коллектор порошка.
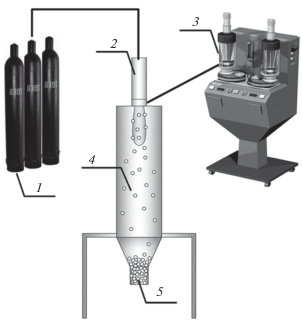
Основными преимуществами плазмотрона с межэлектродной вставкой по сравнению с обычными плазмотронами являются: значительно более низкий уровень низкочастотных пульсаций мощности; низкий уровень пульсаций напряжения или их отсутствие; относительно низкий ток дуги, что приводит к низкому уровню эрозии электрода. Следовательно, напыленные покрытия и обработанный порошок или поверхностный слой не будут загрязнены продуктами эрозии (Cu, W и другими). Кроме того, расход плазменного газа может меняться в относительно широком диапазоне. Поэтому эффективная температура плазмы, удельная энтальпия и скорость также могут меняться в широких пределах. Для эффективной обработки металлокерамического порошка необходимо обеспечить повышенную энтальпию струи наряду с ее протяженностью, чтобы увеличить время пребывания порошка в зоне высокотемпературного нагрева.
Необходимо отметить, что в отличие от длинных аргонно-азотных струй плазмы, выходящих при низких числах Рейнольдса, проблематично достичь длинной ламинарной аргоно-гелиевой струи без примеси кислорода из окружающей атмосферы, начиная с расстояния z/Dn ~ 5. Также следует отметить, что добавление водорода для увеличения энтальпии струи аргона неприемлемо, поскольку струя аргона и водорода становится турбулентной, начиная с выходного сечения сопла плазмотрона. Кроме того, использование водорода приводит к декарбонизации карбида титана.
Оптимальный режим свободной аргонно-гелиевой плазменной струи, истекающей при низких числах Рейнольдса, определяется внутренним диаметром анода Da = 9 мм, выходным диаметром сопла Dn = 11 мм, током дуги I = 250 А, напряжением дуги U = 175 В, расходом основных рабочих газов GAr = 0.4 г/с, GHe = 0.2 г/с, расходом аргона для защиты анода GAr = 0.14 г/с. Для указанных параметров число Рейнольдса Re ~ 150, что соответствует квазиламинарному режиму истечения плазменной струи. Число Рейнольдса рассчитывали по формуле Re = p0Dnu0/μ0, где p0, μ0 и u0 – значения среднемассовой плотности, динамической вязкости и скорости газа, соответствующие среднемассовой температуре T0 при выходе из сопла поперечного сечения Dn. На рис. 3 представлена “теневая” фотография плазменной аргоно-гелиевой струи в заданном режиме работы плазмотрона.
В результате обработки металлокерамических порошков с частицами осколочной формы были получены сферические частицы, морфология и микроструктура которых представлена на рис. 4 и 5. Визуальный анализ шлифа показал, что обработанные частицы наследуют внутреннюю структуру исходных частиц. Размер, форма и распределение зерен карбидов по объему металлического связующего не изменилась, частицы плотные. Гранулометрический состав сфероидизированных частиц приведен в табл. 1. Рентгенофазовый анализ сфероидизированного порошка состава TiCМе (Ме = NiCr, Co) показал наличие фаз карбида титана и металлического связующего.
Рис. 4.
Общий вид (а, б, в) и шлифы (г, д, е) частиц состава TiC−Co (19 об. %) при разном увеличении.
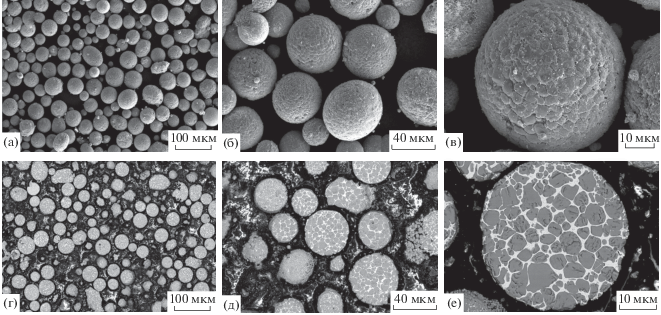
Рис. 5.
Общий вид (а, б, в) и шлифы (г, д, е) частиц состава TiC−NiCr (19 об. %) при разном увеличении.
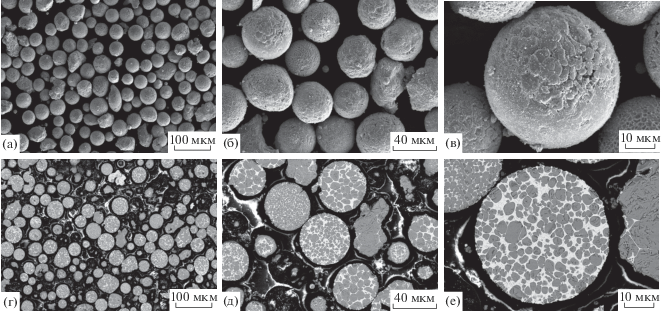
Таблица 1.
Обобщенные результаты характеристик частиц напыляемого порошка
Напыляемый порошок | Средний размер частиц, мкм | Плотность материала, г/см3 |
Скорость частиц, м/c | Температура, К | КИП, % | |||
---|---|---|---|---|---|---|---|---|
d10 | d90 | |||||||
WC−Co (19 об. %) | 34.63 | 14.82 | 485 | 1672 | 54 | |||
22.6 | 46.88 | 596 | 417 | 1767 | 1514 | |||
TiC−Co (19 об. %) | 35.44 | 6.11 | 594 | 1971 | 34 | |||
15.10 | 50.58 | 823 | 498 | 1910 | 1720 | |||
TiC−NiCr (19 об. %) | 31.73 | 5.88 | 648 | 1700 | 33 | |||
6.74 | 48.68 | 963 | 521 | 1786 | 1699 |
ДЕТОНАЦИОННОЕ НАПЫЛЕНИЕ МЕТАЛЛОКЕРАМИЧЕСКИХ ПОРОШКОВ
Детонационные металлокерамические покрытия из твердосплавных композитов на основе карбидов с металлической связкой были получены на промышленном компьютеризированном комплексе детонационного напыления CCDS2000 (Computer Controlled Detonation Spraying), разработанном в ИГиЛ СО РАН [10].
Покрытия для исследований микроструктуры, микротвердости и абразивной стойкости напыляли на стальные пластины (Ст3), толщина покрытия составляла ~300 мкм, дистанция напыления 200 мм. При нанесении покрытий определяли коэффициент использования порошка (КИП), измеряемый в процентах отношения массы напыленного материала к массе материала, инжектированного в ствол детонационной пушки.
Предварительно с помощью программного кода LIH [11] были рассчитаны температура и скорость частиц для исследованных фракций композиционных порошков различного состава в зависимости от их среднеобъемного размера. В табл. 1 представлены обобщенные характеристики частиц напыляемого порошка: фракционный состав исследуемых образцов, включающий средний размер частиц и диапазон основной фракции в интервале d10–d90; плотность материала; скорость частиц и их температура.
Композиционные частицы перед соударением с подложкой находились в твердом, частично или полностью расплавленном состоянии и имели температуру, близкую к температуре плавления металлической связки. Низкое значение КИП (~33%) при формировании покрытий из порошка состава TiC−Ме (19 об. %) (Ме = NiCr и Cо) обусловлено присутствием частиц размером до 15 мкм (табл. 1). Частицы размером менее 5 мкм, для которых характерна низкая кинетическая энергия, уносит поток газа при его натекании на преграду [12]. Композиционные частицы размером от 5 до 15 мкм, как правило, обеднены металлическим связующим (либо оно полностью отсутствует), так как их размер соизмерим с размерами карбидного зерна синтезированного компакта [13], что приводит к рикошету о поверхность формируемого покрытия.
ИССЛЕДОВАНИЕ МИКРОСТРУКТУРЫ И МЕХАНИЧЕСКИХ СВОЙСТВ ДЕТОНАЦИОННЫХ ПОКРЫТИЙ
Для исследования внутренней структуры покрытий были подготовлены шлифы поперечного сечения образцов, структура которых представлена на рис. 6. Покрытия характеризуются как сплошные, без каверн. Наблюдается слоистая структура с четко выраженными границами, образованными деформированными частицами, что указывает на температуру частиц, близкую к температуре плавления металлического связующего, и высокую скорость, оцененные значения которых представлены в табл. 1. В табл. 2 показаны характеристики напыленных покрытий.
Рис. 6.
РЭМ-изображения шлифа металлокерамических покрытий состава: а – WC−Co (19 об. %); б – TiC−Co (19 об. %); в – TiC−NiCr (19 об. %).
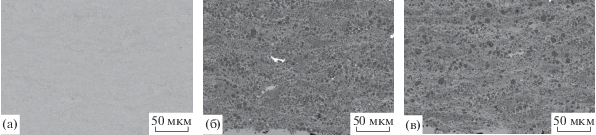
Таблица 2.
Характеристики напыленных металлокерамических покрытий
Напыляемый порошок | Пористость, % | Микротвердость, HV300 | Износ*, мм3 |
---|---|---|---|
WC−Co (19 об. %) | 0.4 | 1283 ± 212 | 0.61 |
TiC−Co (19 об. %) | 1.47 | 831 ± 220 | 3.27 |
TiC−NiCr (19 об. %) | 1.78 | 882 ± 130 | 3.06 |
Микротвердость, как правило, рассматривают в качестве косвенной характеристики износостойкости и/или плотности получаемых покрытий. Микротвердость покрытий HV300 измеряли на твердомере DuraScan-50.
Пористость покрытий, как и ранее [1, 2], определяли с помощью прикладного пакета программ Image Analysis Software, поставляемого вместе с металлографическим микроскопом OLYMPUS GX-51.
Трибологические исследования покрытий на абразивную стойкость проводили в соответствии со стандартом ASTM G65 c максимальной нагрузкой. Более подробное описание процедуры подготовки и испытаний образцов с покрытиями изложены в [1, 2]. Испытание каждого образца осуществляли в три этапа, каждый из которых после 1000 оборотов диска завершался взвешиванием образца с покрытием на аналитических весах с погрешностью 0.5 мг. Объемный износ покрытия определяли как отношение разности масс исходного и потерянного материала покрытия к плотности материала.
Низкая пористость покрытия состава WC− Со (19 об. %) обусловлена, в первую очередь, напылением сферических частиц порошка, каркас которых сформирован из карбидных включений, распределенных в металлическом связующем и характеризующихся высокой внутренней пористостью. Пористость отдельных частиц может достигать 40% (рис. 7). В то же время пористость покрытий, напыленных из порошков на основе карбида титана, выше и связана с напылением сферических плотных частиц (рис. 4 и 5). Таким образом, подтвержден один из результатов [3] детонационного напыления покрытий плотными, а также с высоким объемным содержанием пор, сферическими частицами металлокерамических порошков.
Рис. 7.
РЭМ-изображения шлифа порошковых металлокерамических частиц состава WC−Co (19 об. %) при разном увеличении.
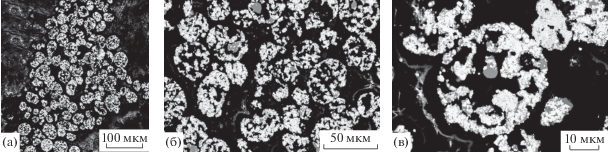
Металлокерамические покрытия, полученные напылением частиц порошков состава TiC−Ме (19 об. %) (Ме = Со и NiCr) и WC−Со (19 об. %), характеризуются различным объемным износом при одинаковой объемной доле металлического связующего. Минимальный износ характерен для покрытия из WC−Со (19 об. %) (табл. 2). Для объяснения этого результата сравним микроструктуры металлокерамических покрытий и проанализируем структуру поверхности следа, оставленного диском во время проведения теста на абразивную стойкость. В [2] установлено, что существуют критические размеры частиц карбидных включений (0.1–0.2 мкм) и их критическая объемная доля в металлическом связующем (меньше 70%), при которых будет наблюдаться повышенный износ покрытия. Металлокерамический материал состава TiC−Ме (19 об. %) (Ме = Со, NiCr), в отличие от металлокерамического материала состава WC−Со (19 об. %), характеризуется широким распределением по размерам твердых включений – от 0.1 до 15 мкм. Как отмечено выше, частицы карбидов, размер которых лежит в диапазоне 0.1–0.2 мкм, не вносят свой вклад в абразивную стойкость покрытия. Обнаруженная дефектная структура частиц карбидов титана размером более 3 мкм приводит к разрушению их по микротрещинам и порам частицами абразива, что также увеличивает массовую потерю материала во время испытаний. Сферическая форма карбидных частиц и их крупный размер (более 3 мкм) обеспечивают низкое механическое сцепление с металлическим связующим, что приводит к выкрашиванию их из объема покрытия. Подтверждением тому являются пустоты округлой формы размером 5 мкм и продольные линии вдоль движения диска (рис. 8).
Рис. 8.
РЭМ-изображения структуры отпечатка диска на металлокерамических покрытиях состава: а – WC−Co (19 об. %); б – TiC−Co (19 об. %); в – TiC−NiCr (19 об. %).
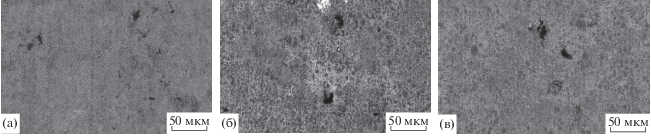
Таким образом, наилучшей износостойкостью обладает покрытие состава WC−Со (19 об. %), поскольку его материал сформирован из частиц карбидов, имеющих форму осколков, характеризующихся небольшим разбросом по размерам (средний размер составляет 1 мкм) (рис. 8) и равномерным распределением внутри металлического связующего.
ЗАКЛЮЧЕНИЕ
В работе представлен объединенный комплекс научно-инженерных разработок, включающий получение сферических частиц металлокерамического порошка с высоким содержанием твердых включений, напыление из него металлокерамических покрытий методом детонации и изучение их эксплуатационных свойств. Научный интерес представляют следующие результаты.
Методом СВС в свободном режиме горения из механоактивированной порошковой реакционной смеси стехиометрического состава, порошка титана, углерода и металлической связки (NiCr, Co) с последующем механическим измельчением и выделением фракции 20–45 мкм получены металлокерамические порошки с частицами осколочной формы и равномерным распределением сферических карбидных включений по объему металлического связующего состава TiC−Ме (19 об. %) (Ме = NiCr, Cо). Отмечена дефектная структура частиц карбидов титана размером больше 3 мкм. В объеме зерен карбидов присутствуют трещины и поры. Феноменологически описан процесс появления данных микроструктурных дефектов.
С помощью аргоно-гелиевой плазменной струи в квазиламинарном режиме (Re ~ 150) проводилась сфероидизация металлокерамических частиц с высоким содержанием карбидной фазы, полученных методом СВС. Исследован их фазовый состав, морфология и микроструктура. Показано, что обработанные частицы наследуют микроструктуру исходных частиц, карбидные включения имеют округлую форму и равномерно распределены в объеме металлического связующего. В частицах карбидов титана размером больше 3 мкм присутствуют те же дефекты – трещины по своему объему и поры.
Исследования подтвердили результаты [3] для детонационного напыления покрытий из металлокерамических порошков, сферические частицы которых были плотными и содержали большое количество пор. При напылении плотного порошка уменьшается КИП (от 54 до 33%) и увеличивается пористость покрытий от 0.4 до 1.78%.
Феноменологически описан процесс снижения абразивной стойкости металлокерамических детонационных покрытий TiC−Ме (19 об. %) (Ме = NiCr и Cо), измеренной в соответствии со стандартом ASTM G65. Показано, что на износостойкость покрытий влияют форма, размер и микроструктура карбидных включений. Наилучшей износостойкостью обладает покрытие состава WC−Со (19 об. %) – потеря объема материала составляет 0.61 мм3 за 1000 оборотов. Необходимо отметить, что частицы карбидов в покрытии приведенного состава имеют форму осколков, образуют узкую фракцию. Средний размер частиц порядка 1 мкм.
БЛАГОДАРНОСТИ
Работа выполнена в рамках Программы фундаментальных научных исследований государственных академий наук на 2013-2020 годы (проект АААА-А17-117030610124-0).
Список литературы
Solonenko O.P., Ovcharenko V.E., Ulianitsky V.Y. et al. // J. Surf. Invest.: Synchrotron Neutron Tech. 2016. V. 10. № 5. P. 1040. https://doi.org/10.1134/S1027451016050402
Ulianitsky V.Y., Batraev I.S., Solonenko O.P., Chesnokov A.E. // J. Surf. Invest.: Synchrotron Neutron Tech. 2018. V. 12. № 2. P. 250. https://doi.org/10.1134/ S1027451018020179
Wang T.-G., Zhao Sh.-Sh., Hua W.-G. et al. // Surf. Coat. Tech. 2009. V. 203. № 12. P. 1637. https:// doi.org/https://doi.org/10.1016/j.surfcoat.2008.12.012
Park S.Y., Kim M.C., Park C.G. // Mater. Sci. Engin. 2007. V. 4. P. 894. https://doi.org/10.1016/j.msea.2006.02.444
Du H., Hua W., Liu J. et al. // Mater. Sci. Engin. 2005. V. 408. № 1–2. P. 202. https://doi.org/https://doi.org/10.1016/ j.msea.2005.08.008
Valentinelli L., Valente T., Casadei F., Fedrizzi L. // Intern. J. Corrosion Processes Corrosion Control. 2004. V. 39. Iss. 4. P. 301. https://doi.org/https://doi.org/10.1179/ 174327804X13884
Guilemany J.M., Dosta S., Nin J., Miguel J.R. // J. Thermal Spray Tech. 2005. V. 14. Iss. 3. P. 405. https://doi.org/10.1361/105996305X59350
Melnyk C., Cerritos R.G., Simi V. et al. // Proceed. Intern. Thermal Spray Conf. Germany, 2011. P. 157.
Ulianitsky V.Yu., Solonenko O.P., Smirnov A.V., Batraev I.S. // Proceed. Intern. Thermal Spray Conf. Barcelona, 2014. P. 668.
Ulianitsky V.Yu., Shtertser A.A., Zlobin S.B., Smurov I.Yu. // J. Thermal Spray Tech. 2011. V. 20. Iss. 4. P. 791. https://doi.org/10.1007/s11666-011-9649-6
Gavrilenko T.P., Nikolaev Yu.A., Ulianitsky V.Yu. et al. // Proceed. Intern. Thermal Spray Conf. Nice, 1998. P. 1475.
Кудинов В.В. Плазменные покрытия. М.: Наука, 1977. 184 с.
Солоненко О.П., Овчаренко В.Е., Чесноков А.Е. // Тр. VI Всерос. конф. “Взаимодействие высококонцентрированных потоков энергии с материалами в перспективных технологиях и медицине”. Новосибирск, 2015. Т. 1. С. 232.
Дополнительные материалы отсутствуют.
Инструменты
Поверхность. Рентгеновские, синхротронные и нейтронные исследования