Поверхность. Рентгеновские, синхротронные и нейтронные исследования, 2020, № 10, стр. 34-41
Послойный анализ субструктуры Cr–Ni–Ti покрытия, полученного методом селективного лазерного плавления
А. А. Голубева a, b, С. В. Коновалов a, b, *, Ю. Ф. Иванов c, К. А. Осинцев b, И. А. Комиссарова d
a Nanjing University of Science and Technology
210094 Nanjing, China
b Самарский национальный исследовательский университет имени академика С.П. Королева
443086 Самара, Россия
c Институт сильноточной электроники Сибирского отделения Российской академии наук
634055 Томск, Россия
d Сибирский государственный индустриальный университет
654041 Новокузнецк, Россия
* E-mail: ksv@ssau.ru
Поступила в редакцию 17.02.2020
После доработки 23.03.2020
Принята к публикации 27.03.2020
Аннотация
В данной работе было проведено электронно-микроскопическое исследование композиционного материала, состоящего из хромоникелевого и титанового сплавов и полученного методом селективного лазерного плавления. Титановый сплав марки ВТ20 использовался в качестве подложки, на которую было нанесено покрытие из сплава марки ВВ751П по двухпроходной стратегии движения лазерного луча в сплавляемом слое. С помощью просвечивающей электронной микроскопии установлены изменения в микроструктуре материала в зависимости от расстояния от поверхности плавления. Слой покрытия имеет толщину 100–120 мкм. Слой титанового сплава, находящийся на расстоянии ≈150 мкм от поверхности плавления, представляет собой ультратонкую пластинчатую (игольчатую) структуру твердого раствора на основе α-титана с поперечными размерами пластин 12–17 нм. По мере удаления от переходного слоя на расстояние ≈250 мкм происходит увеличение поперечных размеров пластинчатой структуры до 110–170 нм. На глубине ≈300 мкм выявляется поликристаллическая структура с размером зерен 1.0–1.5 мкм. Высказано предположение, что формирование пластинчатой структуры является следствием высокоскоростного полиморфного α → β → α превращения, осуществляемого в результате быстрой кристаллизации переплавленного слоя. Формирование подслоя с мелкозернистой структурой является следствием термического влияния на структуру титанового сплава исходного состояния.
ВВЕДЕНИЕ
Титановые сплавы обладают высокой удельной прочностью при относительно низкой плотности, исключительной биосовместимостью, коррозионной стойкостью, жесткостью и хорошими свойствами ползучести при высокой температуре, благодаря которым в настоящее время являются перспективными материалами для применения в аэрокосмической, энергетической, химической и медицинской промышленностях [1, 2]. Однако низкие трибологические свойства и микротвердость, которыми обладают эти материалы, ограничивают их широкое использование в деталях машин и конструкциях, работающих в условиях износа и трения [3]. Указанные недостатки могут быть устранены модификацией поверхности и нанесением покрытий. Традиционные методы модификации поверхности, такие как пескоструйная обработка, плазменное напыление и щелочная обработка имеют ограниченное улучшение свойств и/или ограничение по геометрии заготовок [4, 5]. Эти процессы требуют больших затрат времени и ресурсов. Кроме того, эти методы, особенно плазменное напыление, могут вызывать значительные остаточные напряжения на границе раздела подложка–покрытие. Это может привести к расслаиванию, что также является критической проблемой [6]. В связи с этим в последние десятилетия активно разрабатываются различные новые технологии модификации поверхности, включая обработку трением перемешивания [7], механическую обработку поверхности истиранием [8], ионную имплантацию [9], лазерную модификацию поверхности [10, 11], электронно-пучковую обработку [12–14], микродуговое оксидирование [15], нанесение электроискровых покрытий [16], ионное азотирование [17] и т.д. В настоящей работе нанесение покрытия на титановый сплав предложено осуществить, применив один из методов аддитивного производства – селективное лазерное плавление. Особенностью этой технологии является то, что она позволяет создавать объемные изделия сложной формы послойным расплавлением металлического порошка с помощью мощного лазера по заданной модели [18]. Перспективность и преимущество использования селективного лазерного плавления для нанесения покрытий, по сравнению с традиционными методами, состоит в том, что эта технология позволяет за счет сильного проплавления слоя порошка и поверхности подложки сформировать устойчивое к отслоению покрытие, обладает высокой энерго- и ресурсоэффективностью, а также точностью [19]. Так, в работе [19] была показана возможность производства термобарьерного покрытия из сплава NiCrAlY на подложку из суперсплава IN625. В результате обработки данных по 15-ти опробованным режимам, отличающимся энергией лазера от 100 до 350 Вт и скоростью сканирования от 600 до 800 мм/с, был определен оптимальный режим, который при мощности лазера 250 Вт и скорости сканирования 800 мм/с формирует покрытие с наименьшей остаточной пористостью ≤0.1%, гладким твердым профилем и низким уровнем остаточных напряжений. К настоящему времени было проведено несколько исследований по производству композиционных материалов с помощью селективного лазерного плавления [20–22]. В этих работах были соединены алюминиевый и медный сплавы [20], сталь и медный сплав [21], сталь и оловянная бронза [22]. Результаты представленных исследований показали, что этот способ формирует между двумя материалами зону диффузионного смешивания элементов, что обеспечивает прочное соединение с высокой адгезией.
Настоящая работа является продолжением исследования [23], в котором был представлен послойный анализ покрытия из хромоникелевого сплава ВВ751П, нанесенного на подложку из титанового сплава ВТ20 с помощью селективного лазерного плавления. Целью настоящей работы является исследование микроструктуры слоя, расположенного в подложке из титанового сплава ВТ20 и переходного слоя, сформированного селективным лазерным плавлением порошкового хромоникелевого сплава ВВ751П.
МАТЕРИАЛ И МЕТОДИКИ ИССЛЕДОВАНИЯ
В качестве материала подложки были использованы образцы псевдо-α титанового сплава ВТ20 с размерами 200 × 25 × 4 мм3, находящиеся в состоянии поставки в соответствии с ГОСТ 22 178-76. Титановый сплав ВТ20 был выбран в связи с тем, что он используется в ответственных деталях газотурбинных двигателей, подвергающихся наибольшему нагружению, и повышение его прочностных и трибологических характеристик является одной из важнейших проблем авиационного двигателестроения [2]. Данный сплав титана содержит в качестве легирующих компонентов Fe (<0.25%), C (<0.1%), Si (<0.15%), Mo (0.5–2%), V (0.8–2.5%), N (<0.05%), Al (5.5–7%), O (<0.15%), H (<0.015%), прочие примеси (<0.3%) в соответствии с ГОСТ 19 807-91.
В качестве материала для нанесения покрытия был выбран порошковый жаропрочный никелевый сплав ВВ751П, в качестве легирующих элементов содержащий Al (3.7–4.2%), Co (14–16%), Cr (10–12%), Fe (<1%), Mo (4–5%), Nb (3.0–3.5%), Ti (2.5–3.1%), V (0.4–0.8%), W (2.5–3.5%) в соответствии с ГОСТ Р 52 802-2007 [24, 25]. Размер частиц равен 50 мкм, доля частиц, больших 50 мкм составляет не более 20%, в соответствии с сертификатом, выданным ОАО “Всероссийский институт легких сплавов”. Электронно-микроскопическое изображение порошкового сплава ВВ751П представлено на рис. 1. Этот сплав обладает повышенной длительной прочностью, уменьшенной чувствительностью к надрезу и, как следствие, приводит к повышению ресурса, а также снижению скорости распространения усталостной трещины при рабочих температурах [24].
Рис. 1.
Электронно-микроскопическое изображение порошкового сплава ВВ751П, полученное методом сканирующей электронной микроскопии.
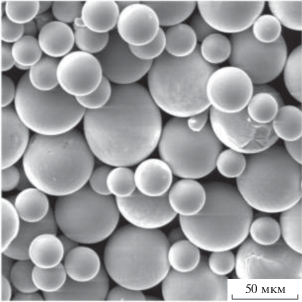
Формирование покрытий произведено на промышленном лазерном принтере SLM 280 HL (SLM Solutions, Германия). В качестве системообразующей стратегии, позволяющей достичь максимальной плотности образцов, была использована двухпроходная стратегия движения лазерного луча в сплавляемом слое [26]. Была применена стратегия сканирования порошкового слоя лазером, которая разбивает слой на квадратные сектора, что позволяет, как показано в работе [27], значительно уменьшить остаточные напряжения. Параметры лазерного луча были выбраны, исходя из оптимальных, разработанных в [28] и обеспечивающих хорошую адгезию покрытия к подложке: мощность лазерного излучения – 325 Вт, скорость движения лазера – 760 мм/с, толщина слоя – 50 мкм, шаг при сканировании лазером – 120 мкм, защитная среда – аргон. После нанесения покрытия образцы оставались в камере до полного остывания.
Электронно-микроскопические исследования проводились методами просвечивающей электронной дифракционной микроскопии на приборе JEM 2100F (JEOL, Япония) [29, 30]. Фольги для исследований готовили методом ионного утонения пластинок толщиной 0.2–0.3 мм, вырезанных электроискровым методом из массивного образца перпендикулярно поверхности.
РЕЗУЛЬТАТЫ ИССЛЕДОВАНИЯ И ИХ ОБСУЖДЕНИЕ
Характерное электронно-микроскопическое изображение структуры титанового сплава ВТ20 в исходном состоянии представлено на рис. 2. Дефектная субструктура исследуемого сплава представлена полосовой субструктурой и субзернами. Поперечные размеры полосовой субструктуры изменяются в пределах от 0.2 до 0.7 мкм. Поперечные размеры субзерен изменяются в пределах от 0.45 до 1.4 мкм. Соотношение полосовой и субзеренной структуры составляет 0.4 : 0.6 соответственно. Относительное содержание полосовой и субзеренной структуры определено по соотношению площадей, занятых на электронно-микроскопических изображениях той или иной структурой.
Рис. 2.
Электронно-микроскопическое изображение структуры титанового сплава ВТ20 в исходном состоянии.
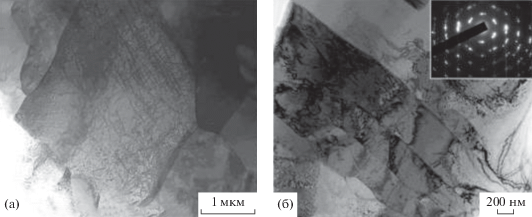
В объеме субзерен присутствует дислокационная структура в виде хаотически распределенных дислокаций или дислокационных сеток (рис. 2а). Скалярная плотность дислокаций составляет 2.8 × 1010 см–2. Дефектная субструктура исходного титанового сплава находится в разориентированном состоянии (рис. 3б). Анализ микроэлектронограмм дает основание заключить, что величина азимутальной составляющей полного угла разориентации структуры составляет 0.19 рад. В объеме пластин и субзерен присутствуют изгибные экстинкционные контуры (рис. 3), что свидетельствует о кривизне-кручении кристаллической решетки материала [31]. В большинстве случаев контуры начинаются и заканчиваются на границах раздела пластин или субзерен. Последнее свидетельствует о том, что источниками кривизны-кручения кристаллической решетки исходного титанового сплава ВТ20 (концентраторами напряжения) являются границы раздела дефектной субструктуры. Причиной формирования кривизны-кручения кристаллической решетки являются внутренние поля напряжений, обусловленные, по всей видимости, несовместностью деформации контактирующих друг с другом пластин или субзерен.
Рис. 3.
Электронно-микроскопическое изображение структуры титанового сплава ВТ20 в исходном состоянии. Стрелками указаны изгибные экстинкционные контуры.
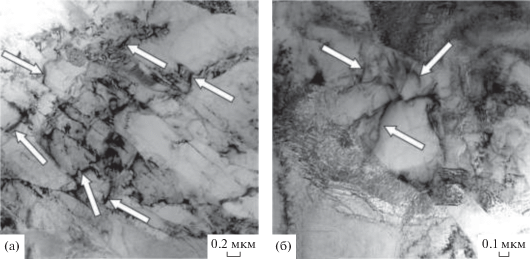
Формирование покрытия селективным лазерным плавлением порошка ВВ751П на титановом сплаве ВТ20 образует четыре характерные области в микроструктуре подложки, отличающиеся размером зерен.
Опираясь на результаты микрорентгеноспектрального анализа элементного состава, представленные в работе [23], будем называть переходным слоем, отделяющим спеченный порошок сплава ВВ751П от подложки, слой, расположенный на глубине 100–120 мкм.
Характерное электронно-микроскопическое изображение структуры материала переходного слоя представлено на рис. 4. Переходный слой спеченного порошка является твердым раствором на основе α-титана и имеет слаборазориентированную субзеренную структуру (рис. 4а). По границам субзерен располагаются включения вторых фаз. Размеры субзерен изменяются в пределах 1.5–3.2 мкм; размеры включений вторых фаз составляют 150–200 нм. При большем удалении от поверхности плавления относительное содержание включений второй фазы снижается, включения располагаются в объеме зерен хаотически, субзеренная структура не выявляется (рис. 4б).
Рис. 4.
Электронно-микроскопическое изображение структуры, формирующейся в слое, соединяющем спеченный порошок хромоникелевого сплава ВВ751П с подложкой из титанового сплава ВТ20; а – структура слоя со стороны спеченного порошка; б – структура слоя со стороны подложки.
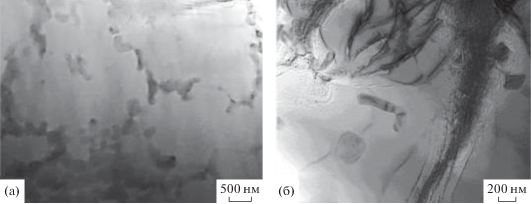
На расстоянии ≈150 мкм от поверхности плавления наблюдается поликристаллическая структура, в объеме зерен которой выявляется субструктура пластинчатого типа (рис. 5). Поперечные размеры пластин изменяются в пределах 12–17 нм (рис. 5в, 5г). Анализ микроэлектронограмм, полученных с данного слоя материала, свидетельствует о том, что формирующаяся структура является твердым раствором на основе α-титана.
Рис. 5.
Электронно-микроскопическое изображение структуры, формирующейся в слое, расположенном на глубине ≈150 мкм; а – светлое поле; б – микроэлектронограмма; в, г – темные поля, полученные в рефлексах [101] α-Ti (в) и [100]α-Ti (г). На (б) стрелками указаны рефлексы, в которых получены темные поля: 1 – для (в); 2 – для (г).
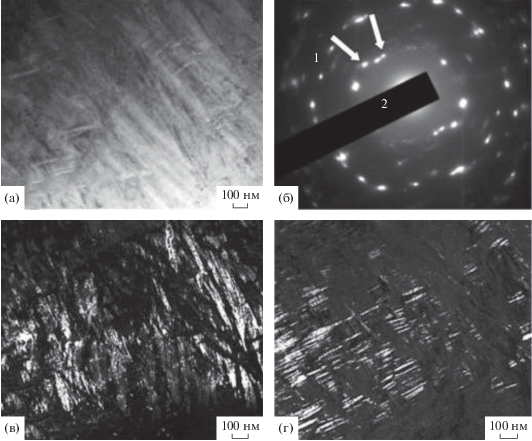
На глубине ≈250 мкм пластинчатая структура имеет существенно большие поперечные размеры пластин, изменяющиеся в пределах 110–170 нм. На глубине ≈300 мкм выявляется поликристаллическая структура с размером зерен 10–15 мкм (рис. 6). В объеме зерен наблюдается дислокационная субструктура, представленная хаотически распределенными дислокациями. Скалярная плотность дислокаций 3 × 1010 см–2.
Рис. 6.
Электронно-микроскопическое изображение структуры, формирующейся в слое, расположенном на глубине ≈300 мкм; а – светлое поле; б – темное поле, полученное в рефлексе [110] α-Ti; в – микроэлектронограмма. На (в) стрелкой указан рефлекс, в котором получено темное поле.
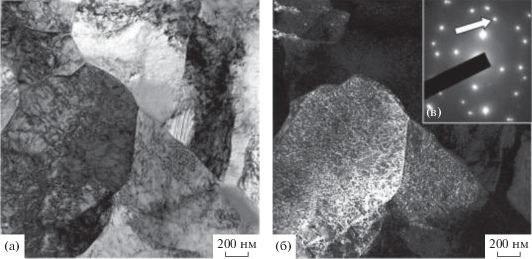
Таким образом, нанесение покрытий с помощью селективного лазерного плавления порошка сплава ВВ751П на подложку из сплава ВТ20 сопровождается формированием в прилегающем слое подложки структуры, характеризующейся закономерным изменением параметров дефектной субструктуры материала. А именно, (1) формированием слоя титанового сплава с ультратонкой пластинчатой (игольчатой) структурой твердого раствора на основе α-титана с поперечными размерами пластин 12–17 нм на расстоянии ≈150 мкм от поверхности плавления; (2) увеличением поперечных размеров пластинчатой структуры до 110–170 нм по мере удаления от переходного слоя на расстояние ≈250 мкм; (3) формированием на глубине ≈300 мкм слоя с размером зерен 1.0–1.5 мкм. Сравнивая дислокационные субструктуры исходного титанового сплава и композиционного материала, полученного селективным лазерным плавлением, можно сделать вывод, что нанесение покрытия увеличивает скалярную плотность дислокаций в объеме зерен с 2.8 × 1010 до 3 × 1010 см–2. Формирование пластинчатой структуры является следствием высокоскоростного полиморфного α → β → α превращения; формирование подслоя с мелкозернистой структурой является следствием скоростного термического преобразования структуры титана исходного состояния.
ЗАКЛЮЧЕНИЕ
Показано, что дефектная структура сплава ВТ20 в исходном состоянии представлена полосовой субструктурой и субзернами. Установлено, что селективное лазерное плавление сопровождается формированием, наряду с покрытием, переходного слоя и слоя термического влияния, характеризующихся состоянием дефектной субструктуры, элементного и фазового состава. Показано, что переходный слой сформирован зернами твердого раствора на основе α-титана и имеет слаборазориентированную субзеренную структуру. По границам субзерен располагаются включения вторых фаз субмикронных (150–200 нм) размеров. При удалении от поверхности плавления относительное содержание включений второй фазы снижается, включения располагаются в объеме зерен хаотическим образом, субзеренная структура не выявляется. Слой термического влияния имеет поликристаллическую структуру, сформированную твердым раствором на основе α-титана, в объеме зерен которого выявляется субструктура пластинчатого (игольчатого) типа с ультрамалым (12–17 нм) поперечным размером пластин. При удалении от поверхности плавления поперечные размеры пластин многократно увеличиваются. На расстоянии ≈300 мкм от поверхности плавления формируется поликристаллическая структура с размером зерен 1.0–1.5 мкм. Высказано предположение, что формирование пластинчатой структуры является следствием высокоскоростного полиморфного α → β → α превращения; формирование подслоя с мелкозернистой структурой является результатом скоростного термического преобразования структуры титана исходного состояния.
Список литературы
Banerjee D., Williams J.C. // Acta Mater. 2013. V. 61. № 3. P. 844. https://doi.org/10.1016/j.actamat.2012.10.043
Бурков A.A. // Письма о материалах. 2015. Т. 5. № 4. С. 371. https://doi.org/10.22226/2410-3535-2015-4-371-375
Mao Y.S., Wang L., Chen K.M., Wang S.Q., Cui X.H. // Wear. 2013. V. 297. № 1–2. P. 1032. https://doi.org/10.1016/j.wear.2012.11.063
Zhang L.C., Chen L.Y., Wang L. Preprint Adv. Eng. Mater. 2020. https://onlinelibrary.wiley.com/doi/full/ 10.1002/adem.201901258
Fomin A.A., Gusev V.G. // Russian Engineering Research. 2013. V. 33 № 11. P. 646. https://doi.org/10.3103/S1068798X13110087
Zhao H., Zhang J., Wang Z., Lin P., Wang Z. // J. Adhes. Sci. Technol. 2015. V. 29. № 10. P. 991. https://doi.org/10.1080/01694243.2015.1011736
Farias A., Batalha G.F., Prados E.F., Magnabosco R., Delijaicov S. // Wear. 2013. V. 302. № 1–2. P. 1327. https://doi.org/10.1016/j.wear.2012.10.025
Alikhani Chamgordani S., Miresmaeili R., Aliofkhazraei M. // Tribol. Int. 2018. V. 119. P. 744. https://doi.org/10.1016/j.triboint.2017.11.044
Poltavtseva V.P., Ghyngazov S.A., Satpaev D.A. // Russ. Phys. J. 2019. V. 61. № 11. P. 2012. https://doi.org/10.1007/s11182-019-01631-0
Telegin S.V. Lyasnikova A.V., Dudareva O.A., Grishina I.P., Markelova O.A., Lyasnikov V.N. // J. Surf. Investig. 2019. V. 13. № 2. P. 228. https://doi.org/10.1134/S1027451019020174
Okipnyi I.B., Maruschak P.O., Zakiev V.I., Mocharskyi V.S. // J. Fail. Anal. Prev. 2014. V. 14. № 5. P. 668. https://doi.org/10.1007/s11668-014-9869-4
Zhang C. Lv P., Xia H., Yang Z., Konovalov S., Chen X., Guan Q. // Vacuum. 2019. V. 167. P. 263. https://doi.org/10.1016/j.vacuum.2019.06.022
Ivanov Y.F., Koval N.N., Gorbunov S.V., Vorobyov S.V., Konovalov S.V., Gromov V.E. // Russ. Phys. J. 2011. V. 54, № 5. P. 575. https://doi.org/10.1007/s11182-011-9654-8
Guo G., Tang G., Ma X., Sun M., Ozur G.E. // Surf. Coatings Technol. 2013. V. 229. P. 140. https://doi.org/10.1016/j.surfcoat.2012.08.009
Guo Q., Xu D., Yang W., Guo Y., Yang Z., Li J., Gao P. // Surf. Coatings Technol. 2020. V. 386. P. 125 454. https://doi.org/10.1016/j.surfcoat.2020.125454
Ageev E.V., Altukhov A.Y., Pikalov S.V. // Int. J. Appl. Eng. Res. 2015. V. 10. № 19. P. 40613.
Budilov V.V., Ramazanov K.N., Zolotov I.V., Khucnutdinov R.F., Starovoitov S.V. // J. of Eng. Sci. and Tech. 2015. V. 8. P. 22.
Агаповичев А.В., Сотов А.В. // Математическое моделирование в естественных науках. 2016. Т. 1. С. 7.
Lee J., Terner M., Copin E., Lours P., Hong H.U. // Add. Manuf., 2020. V. 31, P. 100 998. https://doi.org/10.1016/j.addma.2019.100998
Sing S.L., Lam L.P., Zhang D.Q., Liu Z.H., Chua C.K. // Mater. Charact. 2015. V. 107. P. 220. https://doi.org/10.1016/j.matchar.2015.07.007
Liu Z.H., Zhang D.Q., Sing S.L., Chua C.K., Loh L.E. // Mater. Charact. 2014. V. 94. P. 116–125. https://doi.org/10.1016/j.matchar.2014.05.001
Chen J., Yang Y., Song C., Zhang M., Wu S., Wang D. // Mater. Sci. Eng. A. 2019. V. 752. P. 75. https://doi.org/10.1016/j.msea.2019.02.097
Комиссарова И.А., Осинцев К.А., Голубева А.А., Коновалов С.В., Смелов В.Г., Носова Е.А., Никитина Ю.В. // Фундаментальные проблемы современного материаловедения. 2019. Т. 3. С. 399. https://doi.org/10.25712/ASTU.1811-1416.2019.03.017
Патент 2 368 683 (РФ). Порошковый жаропрочный никелевый сплав / Открытое Акционерное Общество “Всероссийский Институт Легких сплавов” (ОАО ВИЛС), Министерство промышленности и торговли Российской Федерации. Гарибов Г.С. Гриц Н.М., Востриков А.В., Федоренко Е.А., Волков А.М. 2009.
Гарибов Г.С., Гриц Н.М., Востриков А.В., Федоренко Е.А., Волков А.М. // Технология легких сплавов. 2012. Т. 3. С. 64.
Волосова М.А., Окунькова А.А. // Известия Самарского научного центра Российской академии наук. 2012. Т. 14. № 4 (2). С. 587.
Yasa E., Deckers J., Kruth J.-P., Rombouts M., Luyten J. // ASME 2010 10th Biennial Conference on Engineering Systems Design and Analysis. 2016. C. 9.
Патент 2 713 255 (РФ). Способ формирования композиционного материала методом селективного лазерного плавления порошка жаропрочного никелевого сплава на подложке из титанового сплава / “Самарский национальный исследовательский университет имени академика С.П. Королeва”. Коновалов С.В., Носова Е.А., Смелов В.Г., Осинцев К.А. 2020.
Конева Н.А., Киселева С.Ф., Попова Н.А. Эволюция структуры и внутренние поля напряжений. Deutschland: Lamp Lambert Academic Publishing, 2017. 148 с.
Wang R., Tao J., Du K., Wang Y., Ge B., Li F., Liu W., Wu L., Liu H., Zhang Y., Yao Y., Duan X. // Springer Tracts Mod. Phys. 2018. V. 272. P. 69. https://doi.org/10.1007/978-981-13-0454-5
Ivanov Y.F., Gromov V.E., Glezer A.M., Peregudov O.A., Morozov K.V. // Bull. Russ. Acad. Sci. Phys. 2016. V. 80. № 12. P. 1483. https://doi.org/10.3103/S1062873816120078
Дополнительные материалы отсутствуют.
Инструменты
Поверхность. Рентгеновские, синхротронные и нейтронные исследования