Поверхность. Рентгеновские, синхротронные и нейтронные исследования, 2020, № 3, стр. 62-70
Исследование влияния плазменного тонкопленочного покрытия системы Si−O−C−N на поверхностное упрочнение быстрорежущей стали
В. А. Коротков a, И. А. Растегаев b, *, Д. Л. Мерсон b, М. А. Афанасьев b
a Нижнетагильский технологический институт (филиал)
Уральского федерального университета
622031 Нижний Тагил, Россия
b Тольяттинский государственный университет
445020 Тольятти, Россия
* E-mail: RastIgAev@yandex.ru
Поступила в редакцию 03.05.2019
После доработки 15.06.2019
Принята к публикации 15.06.2019
Аннотация
Представлены результаты исследования изменения прочностных свойств поверхности изделия из быстрорежущей инструментальной (HSS) стали типа Р6М5 после ее упрочнения нанесением микронного покрытия системы Si−O−C−N. Исследование проведено путем сравнения свойств поверхности, оцененных одними и теми же способами до и после нанесения покрытия. При этом образец перед нанесением покрытия прошел полный цикл механической и термической обработки, предусмотренной для изделия. Приводятся результаты оценки адгезионной прочности покрытия с помощью предложенного способа пересчета, получено соответствие между индексом разрушения покрытия методики VDI 3198:1992-08 и коэффициентом отслоения. Само исследование проведено путем индентирования и царапания поверхности инденторами HV, HRC и HRB-типа в диапазоне изменения нагрузок 0.1−200 Н, что позволило сымитировать разный уровень контактного давления в приповерхностном слое основы и на границе раздела основа−покрытие. Показано, что нанесение тонкопленочного покрытия системы Si−O−C−N плазменным способом позволяет дополнительно к стандартной термообработке HSS-стали повысить стойкость поверхности к внедрению и царапанию их более твердыми телами. Проанализированы причины полученного положительного эффекта и описаны границы целесообразности применения плазменного упрочнения в зависимости от контактной задачи. Полученные результаты позволяют рассматривать способ дополнительного плазменного упрочнения HSS-стали, как перспективный для внедрения.
ВВЕДЕНИЕ
Использование плазменных технологий является интенсивно развивающимся направлением обработки металлов и сплавов [1–4]. Среди них сравнительно новый способ нанесения тонкопленочного плазменного покрытия занимает особое место, т.к. позволяет при нормальной температуре уже готовому изделию придать новые свойства рабочей поверхности без изменения его размеров [1]. Это расширяет эксплуатационные характеристики материалов сверх тех, которые удается достичь классической термической обработкой [5, 6]. Нанесение покрытия приводит к тому, что поверхность изделия начинает работать как композитный материал, свойства которого отличны как от свойств основы, так и материала покрытия, что затрудняет прогнозирование работоспособности изделия в целом. Целью настоящей работы является исследование поверхности быстрорежущей стали с плазменным тонкопленочным покрытием (ПТП) при различных условиях контактного воздействия.
В работах [7–9] показано, что износостойкость и срок службы изделия с защитными покрытиями во многом определяется способностью рабочих поверхностей сопротивляться внедрению контртела без разрушения покрытия. Последнее, в свою очередь, определяется: толщиной покрытия, механическими характеристиками материала покрытия и основы и прочностью адгезионных связей между ними [1, 10−13 и др.]. Анализ показывает, что основной причиной разрушения поверхности с защитными покрытиями являются когезионные поперечные (радиальные) трещины в покрытии и боковые (латеральные) когезионные и адгезионные трещины, находящиеся соответственно в покрытии и на границе основа−покрытие, а также неупрочненный подповерхностный слой материала основы [9, 11, 12 и др.]. При этом исследования комплексных механических характеристик пары основа-покрытие применительно к контактным задачам механики разрушения приводятся к схемам вдавливания и царапания поверхности твердым индентором [7–13]. Известно [8, 9, 14 и др.], что инденторы сферической и конической формы (“тупые”) инициируют появление радиальных трещин, а пирамидальный и др. граненые инденторы (“острые”) – еще и боковых (латеральных) трещин. Таким образом, варьирование типом индентора в сочетании с изменением прилагаемой к нему нагрузки позволяет изменять условия нагружения на границе раздела основа−покрытие в широком диапазоне, что и используется в настоящей работе.
МАТЕРИАЛЫ И МЕТОДИКА ИССЛЕДОВАНИЙ
Для исследования была выбрана сталь HSS (С − 0.89, W − 5.06, Mo − 4.68, Si − 0.34, V − 1.74, Cr − 4.91, Fe − 80.95 мас. %), которая является импортным аналогом отечественной инструментальной стали Р6М5. Образцы вырезались электроэрозионным способом из перьевого сверла в виде параллелепипеда с линейными размерами 69 × 19 мм и толщиной 14 мм. Благодаря такой процедуре подготовки, образцы проходили механическую и термическую обработку полностью идентичную всему изделию, что подтверждалось металлографическими исследованиями, выполненными в соответствии с работами [15–17] на металлографическом микроскопе ZEISS Axiovert 40 МАТ с программой оценки качества структуры материалов Thixomet Pro. Микроструктура образца соответствовала закаленной стали и состояла из мартенсита, карбидов и остаточного аустенита (рис. 1). Размер игл мартенсита соответствовали 4−5 баллу, содержание карбидной фазы составило 2.0 ± 0.3%, карбидная неоднородность − 1 балл. Далее на образцы материала с одной стороны в условиях воздушной атмосферы наносилось плазменным способом тонкопленочное покрытие [1, 18], причем в качестве источника энергии использовалась плазменная струя, истекающая из малогабаритного плазмотрона, дополненного плазмохимическим реактором. В ней происходит разложение паров кремнийорганического препарата, из которых на поверхности изделия формируется покрытие системы Si−O−C−N [1, 18]. Нанесение покрытия осуществлялось послойно перемещением плазменной струи по поверхности. Толщину каждого слоя варьировали в пределах 2−10 нм, ширину полосы нанесения слоя 8−10 мм. С целью минимального термического воздействия на материал основы плазменная струя перемещалась со скоростью 3−150 мм/с.
Рис. 1
. Микроструктура (а) и РСМА-спектр участка поверхности образца со стороны нанесения покрытия (б) и с обратной стороны (в). Элементы с существенным отличием в спектре выделены закрашенной рамкой.
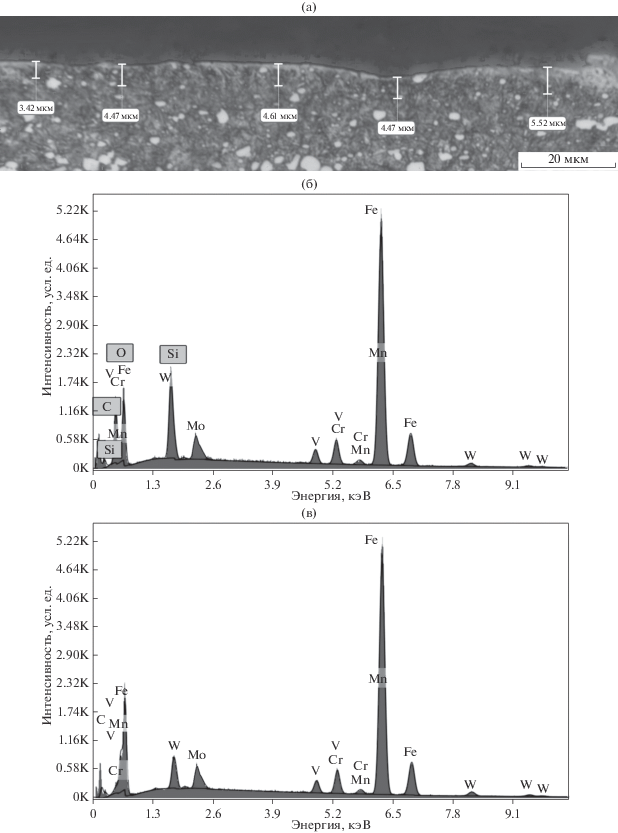
Оценка прочностных характеристик проводилось индентированием и царапанием образца материала основы и образца основы с покрытием. При индентировании использовались “острый” пирамидальный индентор Виккерса (тип HV) и два “тупых”: конический Роквелла С (тип HRC, радиус при вершине 200 мкм) и сферический Роквелла В (тип HRB, диаметр 1.588 мм). При испытании царапанием также использовались инденторы HRC и HRB-типа, а для исключения возможности поломки индентора и оборудования вместо индентора HV использовался “острый” нестандартный индентор конической формы с углом раскрытия 120° и радиусом при вершине R, равным 100 мкм. Индентирование и царапание проводилось при усилиях вдавливания от 0.1 до 200 Н на скретч-тестере Nanovea P-Macro. Кроме того, сверх этого диапазона нагрузок в соответствии с [19] проводилось внедрение индентора HRC с усилиями от 588.4 до 1471 Н на стационарном твердомере Time Group TH-300. Измерение всех повреждений проводилось на лазерном сканирующем конфокальном микроскопе (ЛСКМ) Olympus LEXT OLS4000 по 2D и 3D-сканам, полученным сшивкой трехсот сканов изображений по оси Z при увеличениях ×400, ×1000 и ×2000 (в зависимости от размера повреждения), что является эффективным инструментом для измерения глубинных повреждений [20]. Соответствие покрытия системе Si−O−C−N обеспечивалось качеством органического препарата и технологией его нанесения [1, 18]. Контроль химического состава покрытия осуществляли методом рентгеноспектрального микроанализа (РСМА), микроструктуру основы и покрытия, а также толщину покрытия определяли методом растровой электронной микроскопии (РЭМ), при этом использовался сканирующий электронный микроскоп ZEISS Sigma, оснащенный EDS/EDX анализатором EDAX “Appolo X”.
Для оценки адгезионной прочности покрытий зачастую используют коэффициент отслоения KО [21, 22 и др.] или индекс разрушения HF [19, 23, 24 и др.]. Параметры KО и HF основаны на оценке площади повреждения покрытия, при этом KО позволяет получать численный результат, а индексы HF отражают лишь ранг повреждения. Для обеспечения обоснованного пересчета результатов между значениями KО и индексами HF в настоящей работе было установлено соответствие между ними (табл. 1), которое получено следующим образом. Известно [21, 22], что KО определяется как:
где: SO – видимая площадь проекции отслоения/скола покрытия с отделением от основы (зона черного цвета в табл. 1), SI – площадь проекции повреждения/лунки оставленной индентором (зона серого цвета в табл. 1). С учетом этого были оцифрованы площади отслоения (SO) и следа интентора (SI) на регламентируемой визуальной шкале оценочных признаков повреждения методики [19] (табл. 1), и по соотношению (1) получены расчетные предельные значения KОР. Тогда разброс значений KО, соответствующих рангам шкалы HF, будет заключен в диапазонах [KО] ограниченных KОР. В табл. 1 при установке [KО] также было принято, что индекс HF1 соответствует ситуации SO < SI (KО < 0), HF2 − ситуации SO ≈ ≈ SI (KО ≈ 0), а HF3−HF6 ситуации − SO > SI (KО > 0).Измерение твердости и модуля упругости проводилось на том же оборудовании, что и индентирование с царапанием, в соответствии с методиками, описанными в работах [25–27] и [28, 29]. Исследование царапанием проводилось в соответствии [30] (линейно нарастающее нагружение индентора и одновременное его смещение вдоль образца). Скорость нагружения составляла 19.9 Н/мм, путь царапания − 10 мм. Данный подход, в отличие от режима царапания при постоянной силе на индентор, позволяет имитировать несколько режимов нагружения и исследовать механизмы накопления повреждений в поверхностных и приповерхностных слоях в задаваемом диапазоне изменения нагрузки.
РЕЗУЛЬТАТЫ ИССЛЕДОВАНИЙ И ИХ ОБСУЖДЕНИЕ
Средняя твердость и приведенный модуль упругости материала основы (HSS-сталь) до нанесения покрытия составляли 735 ± 6 HV и 210 ± ± 22 ГПа соответственно. В результате нанесения покрытия произошло изменение микроструктуры материала основы в подповерхностной зоне на глубине 4.5 ± 1.1 мкм. В ней установлен распад остаточного аустенита с формированием мартенситно-карбидной структуры без изменения размера и неоднородности зерен и карбидной фазы. Толщина покрытия составила 0.8 ± 0.4 мкм, причем покрытие соответствовало системе Si−O−C−N, поскольку на РСМА-спектрах основы с покрытием обнаруживаются пики элементов Si (0.54 мас. % и 1.42 ат. %) и O (0.25 мас. % и 0.96 ат. %), отсутствующие на РСМА-спектре основы (рис. 1), а также наблюдается увеличение концентрации элемента С в среднем в 1.7 раза по весовому и в 2 раза по атомному проценту содержания. Результаты РСМА картирования химических элементов и анализ стехиометрических соотношений углерода, кислорода и кремния говорит в пользу того что их количества достаточно для образования соединений SiC и SiO2. Однако учитывая диэлектрические свойства покрытия можно заключить, что поверхностный слой сформирован преимущественно оксидом кремния SiO2. Тот факт, что он образовался в результате напыления, также подтверждается результатами рентгеноспектрального микроанализа по кислороду и кремнию вдоль зоны линейного сканирования, проходящей в плоскости шлифа перпендикулярно поверхности с покрытием (на рисунках не представлено). Известно, что мартенситно-карбидная структура и фаза SiO2 обладает высокой твердостью, а сам процесс нанесения покрытия сопровождается заполнением микронеровностей поверхности, поэтому после нанесения ПТП ожидаемо уменьшение шероховатости и увеличение твердости.
Результаты оценки прочности поверхности индентированием в сопоставлении коэффициента отслоения (КО) с индексом повреждения (HF) для всех типов инденторов и нагрузок приведены на рис. 2. При внедрении HV-индентора покрытие всегда скалывается за пределами контактной площади индентора и преимущественно по границе основа−покрытие, что отчетливо видно на рис. 3, на котором показано, что на материале основы в месте скола не остается следов химических элементов, принадлежащих покрытию.
Рис. 2.
Общий вид повреждений и результаты оценки адгезионной прочности покрытия инденторами: Виккерса (◼), Роквелла С (▼), Роквелла В (⚫). Размер области, показанной в верхней части рисунка для индентора Виккерса, при нагрузках до 5 Н составляет 45 × 45 мкм, до 100 Н − 196 × 196 мкм, в нижней части для индентора Роквелла С при нагрузках до 200 Н − 258 × 258 мкм, до 1500 Н − 646 × 646 мкм.
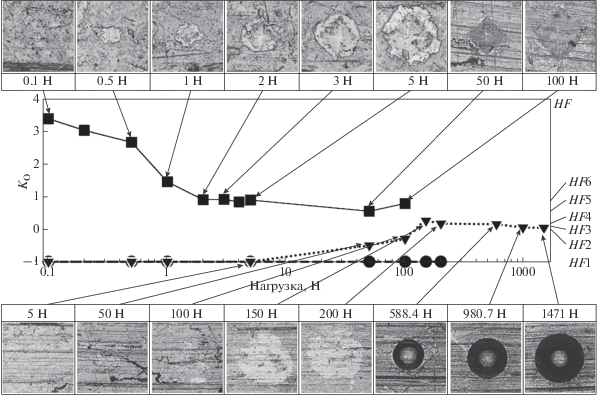
Рис. 3.
Общий вид повреждения (а), увеличенные его фрагменты (б, в), карты распределения С (г), Si (д) и O (е) по площади сканирования при РСМА переходной зоны “покрытие/основа”, показанного на фрагменте (в).
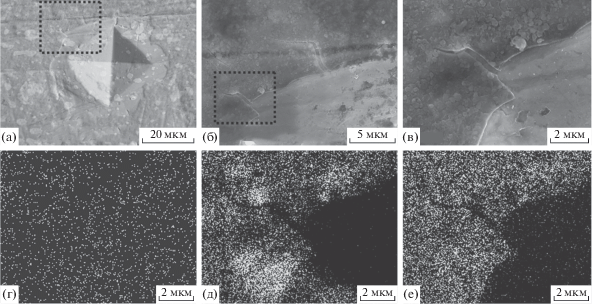
Сколы от латеральных трещин привели к тому, что для индентора HV индексы повреждения HF5 в диапазоне усилий 0.1−3 Н получились высокие (4−100 Н), соответствующие HF6. При внедрении индентора HRC с малыми нагрузками покрытие разрушается в пределах контактной площади путем образования радиальных трещин с частичным выкрашиванием по их сетке. При больших глубинах внедрения покрытие скалывается и по краям контактной площади. Поэтому для индентора HRC индексы повреждения меняются с HF1 (0.1−130 Н) до HF2 (200−1471 Н) с максимумом HF4 в диапазоне 130−200 Н. Последнее связано с изменением условий контактирования (переходом от сферической к конической части). При внедрении шарового индентора HRB сколов и видимых повреждений на покрытии не обнаружено даже при наличии остаточной деформации материала основы, поэтому индекс повреждения составляет HF1 во всем исследованном диапазоне нагружения. Таким образом, при внедрении индентора HV превалирует адгезионный механизм разрушения покрытия, а при внедрении HRC и HRB инденторов – когезионный.
Согласно [19] значения индексов до HF4 считаются приемлемыми для эксплуатации, а выше – нет. Следовательно, по адгезионной прочности покрытие не может быть признано работоспособным при контактировании с телами в условиях высоких контактных давлений (аналогичных внедрению индентора HV-типа), а во всех остальных случаях (более приближенных к реальным условиям эксплуатации) адгезионную прочность можно признать достаточной для применения данного способа упрочнения. При этом, если площадь повреждения после внедрения индентора HV отнести к глубине повреждения, то получаем, что величина отношения при нагрузке индентирования ниже 0.2 Н и выше 2 Н выходит на постоянный уровень, т.е. незначительно изменяется с изменением нагрузки, что косвенно также отражает изменение параметра KO (рис. 2). Поэтому можно считать, что твердость, полученная на нагрузках ниже 0.2 Н, в большей мере отображает свойства покрытия, а твердость, полученная при нагрузках выше 2 Н, – комплексное свойство основы с покрытием. При нагрузке на индентор 0.1 Н среднее значение твердости покрытия составляет около 2576 HV (против 810 HV у основы). Комплексная твердость основного материала с покрытием (полученная при нагрузках выше 2 Н) в среднем увеличилась примерно в 1.27 раз (до 940 ± 98 HV), а приведенный модуль упругости в 2.45 раз (до 515 ± 66 ГПа). При этом максимальное упрочнение основы произошло на глубину до 6.7 ± 0.4 мкм, т.к. при измерении твердости с увеличением нагрузки именно, начиная с этой глубины внедрения индентора HV, значение твердости выходит на постоянный уровень. Полученный результат с вычетом толщины покрытия хорошо согласуется с толщиной выявленной мартенситно-карбидной зоны (рис. 1), твердость которой выше мартенситно-карбидно-аустенитной основы [5]. Из этого следует, что, несмотря на небольшую величину адгезионной прочности ПТП, оно увеличивает сопротивление внедрению в поверхность индентора любого типа по сравнению с исходной термообработкой материала образца изделия.
Результаты оценки сопротивления поверхности царапанию (рис. 4) показали, что при наличии покрытия начальный динамический коэффициент трения (f) в среднем меньше, чем без покрытия в 1.3, 1.5 и 1.1 раз соответственно для нестандартного
конического индентора, инденторов HRC и HRB. Это объясняется изменением шероховатости
поверхности, которая после нанесения ПТП уменьшилась в среднем в 1.16 раз. Максимальная
глубина проникновения (повреждения) индентором (h) основы с покрытием и без него за испытание до максимальной нагрузки в 200 Н также
уменьшилась в среднем в 1.23, 1.05 и 1.18 раз, соответственно, что связано с показанным
выше эффектом упрочнения поверхностного слоя после нанесения ПТП. По этой же причине
остаточная деформация на основе с покрытием наблюдается при нагрузках на индентор
в среднем в 1.2, 1.5 и 1.3 раза соответственно выше, чем при царапании основы без
покрытия. При этом микроскопия царапин покрытия показала наличие двух основных критических
точек: первая – точка начала разрушения покрытия, вторая – точка начала задира поверхности
основного материала резанием (на рис. 4 обозначены и
). При пересчете данных с пути трения (длины царапины) на нагрузку критические точки
соответствуют 95 ± 5 Н и 119 ± 8 Н для нестандартного конического индентора, 96 ±
4 Н и 135 ± 12 Н для индентора HRC, 156 ± 10 Н для индентора HRB (вторая точка для
индентора HRB лежит выше 200 Н). Отсюда следует, что путь трения до критических точек
различный для разных инденторов, что связано с отличающимся радиусом контактной области
инденторов (величиной контактного давления). При этом наличие двух критических точек
характерно для хрупкого механизма разрушения покрытия, где пластическое деформирование
поверхности основного материала (задир) происходит после растрескивания и скалывания
покрытия (что и наблюдается в нашем случае), и свидетельствует о невысоком сопротивлении
покрытия зарождению и росту трещин. При этом следует выделить, что вторая критическая
точка возникает на глубинах внедрения в поверхность с ПТП нестандартного конического
индентора около 7.0 мкм и индентора HRC 5.3 мкм. Такая глубина внедрения соответствующих
инденторов в поверхность без ПТП приходится в среднем на нагрузку 116.5 Н и 54 Н.
Таким образом, получаем, что ПТП повышает стойкость по нагрузке внедрения в 1.02 и
в 2.5 раза соответственно. Следовательно, применение ПТП обеспечивает несущественное
повышение стойкости поверхности к повреждению “острыми” контактирующими телами, но
с увеличением радиуса контртела (снижения контактного давления) стойкость поверхности
увеличивается существенно (более чем в 2.5 раза).
ЗАКЛЮЧЕНИЕ
Сравнительный анализ HSS-стали типа Р6М5 с покрытием и без него показал, что нанесение плазменного покрытия системы Si−O−C−N толщиной около 1 мкм позволяет дополнительно к стандартной термообработке повысить ее стойкость к механическому повреждению. При этом само по себе покрытие является достаточно хрупким, поэтому при условии высоких контактных давлений положительный эффект в основном обеспечивается упрочненным при нанесении ПТП подповерхностным слоем материала основы, т.к. покрытие скалывается и выкрашивается в начальный момент контактирования. При средних и низких контактных давлениях положительный эффект комплексный и достигается как за счет прочности покрытия, так и за счет упрочнения поверхностного и подповерхностного слоя основы и снижения шероховатости поверхности. За счет ПТП на образце из HSS-стали поверхностная твердость увеличена в 3.18 раз (до 2576 HV), комплексная твердость поверхности с подповерхностным слоем увеличена в 1.27 раз (до 973 HV), шероховатость поверхности уменьшена в 1.16 раз. Стойкость поверхности с покрытием к повреждению царапанием индентором типа HV почти не изменяется, по сравнению с исходным состоянием материала, а к инденторам типа HRC и HRB увеличивается, более чем в 2.5 раза. При этом адгезионная прочность покрытия соответствует требованиям VDI 3198:1992-08 [19], т.к. повреждения при внедрении индентора HRC не превышают допустимых норм. Упрочнение покрытием системы Si−O−C−N целесообразно проводить для изделий, работающих при нормальных условиях контактных давлений (не экстремальных).
Список литературы
Соснин Н.А., Ермаков С.А., Тополянский П.А. Плазменные технологии. Руководство для инженеров. СПб: Изд-во политехн. ун-та, 2013. 406 с.
Шеченко О.И. Управление структурой, составом и свойствами покрытий при плазменной наплавке. Нижний Тагил: НТИ (ф) УГТУ-УПИ, 2006. 290 с.
Кривобоков В.П., Сочугов Н.С., Соловьев А.А. Плазменные покрытия (свойства и применение). Томск: Изд-во Томского политехнического университета, 2011. 136 с.
Калита В.И., Комлев Д.И. Плазменные покрытия с нанокристаллической и аморфной структурой. М.: Лидер М, 2008. 388 с.
Геллер Ю.А. Инструментальные стали. М.: Металлургия, 1975. 584 с.
Гуляев А.П. Металловедение. М.: Металлургия, 1986. 544 с.
Громаковский Д.Г., Кудюров Л.В., Серебряков Н.Н. Исследование и расчет изнашивания деталей узлов трения машин. М.: Машиностроение, 2012. 219 с.
Морозов Е.М., Зернин М.В. Контактные задачи механики разрушения. М.: Книжный дом Либроком, 2010. 544 с.
Головин Ю.В. Наноиндентирование и его возможности. М.: Машиностроение, 2009. 312 с.
Voronin N.A. // J. Frict. Wear. 2010. V. 31. № 4. P. 241.
Панин С.В., Алхимов А.П., Клименов В.А. и др. // Физическая мезомеханика. 2000. Т. 3. № 4. С. 97
Adhesion Measurement of Films and Coatings. V. 2 / Ed. Mittal K.L. VSP BV, 2001. 351 p.
Antonyuk V.S., Soroka E.B., Kalinichenko V.I. // J. Superhard Mater. 2008. V. 30. № 2. P. 133.
Булычев С.И., Алехин В.П. Испытание материалов непрерывным вдавливанием индентора. М.: Машиностроение, 1990. 224 с.
ГОСТ 5639-82. Стали и сплавы. Методы выявления и определения величины зерна.
ГОСТ 8233-56. Сталь. Эталоны микроструктуры.
ГОСТ 19265-73. Прутки и полосы из быстрорежущей стали. Технические условия.
Тополянский Г.Л., Соснин Н.А. // Сварочное производство. 1989. № 5. С. 30.
VDI 3198:1992-08. Coating (CVD, PVD) of Cold Forging Tools.
Растегаев И.А., Афанасьев М.А. // Известия Самарского научного центра РАН. 2015. Т. 17. Специальный выпуск № 1. С. 187.
Даньков А.В., Береговский В.В., Арутюнова И.Ф., Комаров Н.В. // Известия ВУЗ. Порошковая металлургия и функциональные покрытия. 2015. № 1. С. 62.
Табаков В.П. Формирование износостойких ионно-плазменных покрытий режущего инструмента. М.: Машиностроение, 2008. 311 с.
Vidakis N., Antoniadis A., Bilalis N. // J. Mater. Process. Tech. 2003. 143–144. P. 481.
Bhaskar S. V., Kudal H.N. // Arch. Mech. Tech. Mater. 2017. V. 37. P. 50.
ГОСТ 9450-76. Измерение микротвердости вдавливанием алмазных наконечников.
ISO 6507-1: 2005. Metallic materials. Vickers hardness test. Part 1. Test method.
ISO 6508-1: 2016. Metallic materials. Rockwell hardness test. Part 1. Test method.
ISO 14 577-1:2002 Metallic materials. Instrumented indentation test for hardness and materials parameters. Part 1. Test method.
ISO 14 577-4:2007 Metallic materials. Instrumented indentation test for hardness and materials parameters. Part 4. Test method for metallic and non-metallic coatings.
ASTM D 7027-05. Standard Test Method for Evaluation of Scratch Resistance of Polymeric Coatings and Plastics Using an Instrumented Scratch Machine.
Дополнительные материалы отсутствуют.
Инструменты
Поверхность. Рентгеновские, синхротронные и нейтронные исследования