Поверхность. Рентгеновские, синхротронные и нейтронные исследования, 2020, № 4, стр. 40-48
Стойкость к высокотемпературному окислению многослойных покрытий ZrN/SiNx и CrN/SiNx, сформированных магнетронным распылением
И. А. Солодухин a, *, Г. Абади b, **, В. В. Углов a, c, ***, С. В. Злоцкий a, А. А. Малашевич a
a Белорусский государственный университет
220030 Минск, Беларусь
b Pprime Institute, University of Poitiers
186000 Poitiers, France
c Южно-Уральский государственный университет
454080 Челябинск, Россия
* E-mail: solodukhin@bsu.by
** E-mail: Gregory.Abadias@univ-poitiers.fr
*** E-mail: Uglov@bsu.by
Поступила в редакцию 27.07.2019
После доработки 30.08.2019
Принята к публикации 30.08.2019
Аннотация
Многослойные покрытия ZrN/SiNx и CrN/SiNx были сформированы методом магнетронного осаждения последовательным распылением мишеней Zr (Cr) и Si3N4 при варьировании толщины индивидуального слоя от 2 до 10 нм при температуре подложки 300°C (система ZrN/SiNx) и 450°C (система CrN/SiNx). Методом рентгеновской дифрактометрии было выявлено, что многослойные покрытия ZrN/SiNx и CrN/SiNx состоят из нанокристаллических слоев ZrN (CrN) с преимущественной ориентацией (002) и аморфных слоев SiNx. Параметр решетки фазы нитрида металла для пленок ZrN/SiNx и CrN/SiNx больше, чем для слоев мононитридов ZrN и CrN. В случае пленок ZrN/SiNx он увеличивается при уменьшении отношения толщины индивидуального слоя ZrN к толщине индивидуального слоя SiNx, что может быть связано с ростом сжимающих напряжений. Как показали рентгеноспектральный микроанализ состава пленки и растровая электронная микроскопия поверхности, многослойные покрытия ZrN/SiNx и CrN/SiNx обладают большей стойкостью к высокотемпературному окислению (в интервале температур 400−950°C) по сравнению с покрытиями ZrN и CrN. В случае системы ZrN/SiNx эта стойкость повышается при уменьшении отношения толщины индивидуального слоя ZrN к толщине индивидуального слоя SiNx, однако указанный фактор не является предопределяющим для системы CrN/SiNx. В целом, покрытия CrN/SiNx более стабильны в условиях высокотемпературного окисления, чем покрытия ZrN/SiNx.
ВВЕДЕНИЕ
Пленки на основе нитридов переходных металлов (ПМ), такие как TiN, CrN, ZrN и др., получили широкое распространение в качестве твердых защитных покрытий. Одним из важнейших свойств этих покрытий для их практического применения во многих областях промышленности является стойкость к воздействию агрессивных сред, в частности, к высокотемпературному окислению, воздействию химически агрессивных сред (например, растворов солей или кислот), а также ионному облучению. В таких условиях мононитридные пленки зачастую уже перестают выполнять свою защитную функцию. Так, они интенсивно окисляются при достижении температуры 550°C и выше [1, 2].
Повышению стойкости покрытий к окислению способствует добавление как металлических компонент (Al, Zr, Ta и др.) [1, 3–6], так и неметаллических элементов, таких как C или Si [2, 7–11].
Другим вариантом, способствующим повышению стойкости к высокотемпературному окислению (наряду с улучшением механических свойств), является создание многослойных пленочных структур [5, 12–15]. Одной их особенностей данного подхода является возможность получения уникальных механических свойств, отличных от свойств покрытий, представляющих собой один слой. Так, авторы работы [16] показали, что в случае многослойных покрытий CrN/AlN образование и движение дислокаций не является определяющим фактором пластической деформации. Наблюдаемая пластическая деформация главным образом обусловлена вращением нанокристаллитов и зернограничным проскальзыванием для кристаллитов большего размера. Такой неупругий эффект способствует предотвращению либо ослаблению деформации и трещинообразования, что делает многослойную структуру CrN/AlN перспективной в качестве защитного покрытия, в том числе, для подложек из пластичной стали. В работах [17, 18] отмечается, что многослойные покрытия CrVN/TiN и AlCrN/TiVN характеризуются большей износостойкостью по сравнению с покрытиями CrVN и TiN или AlCrN и TiVN. При этом в случае пленки AlCrN/TiVN слои AlCrN эффективно подавляют диффузию кислорода в пленку при высокотемпературном отжиге, что препятствует окислению ванадия [18].
Как показывают исследования, важным фактором, оказывающим влияние на физико-механические свойства многослойных покрытий, является степень взаимодиффузии компонент отдельных монослоев через границу раздела между слоями. Так, отмечается большое отличие свойств многослойных систем ПМ1/ПМ2 от систем М1/М2 [19, 20]. Еще меньшее взаимопроникновение компонент характерно для многослойных покрытий, где слои нитридов переходных металлов чередуются со слоями SiNx, что обусловлено взаимной нерастворимостью этих двух фаз [14, 21, 22]. За счет этого возможно достижение высокой термической стабильности многослойной структуры. Помимо этого, наличие большого количества границ раздела между слоями подавляет формирование столбчатой структуры покрытия [21], что, в свою очередь, препятствует образованию сплошных пор. Указанные выше факторы позволяют рассматривать такие многослойные покрытия в качестве перспективных материалов для применения в условиях высокотемпературной коррозии. Однако, до настоящего времени вопрос окислительной стойкости таких покрытий недостаточно изучен.
В данной работе проводится сравнительный анализ стабильности многослойных покрытий ZrN/SiNx и CrN/SiNx с различным соотношением толщин индивидуальных слоев при отжиге на воздухе.
МЕТОДИКА ЭКСПЕРИМЕНТА
Пленки мононитридов ZrN, CrN, Si3N4, как и многослойные пленки ZrN/SiNx и CrN/SiNx, были сформированы методом реактивного магнетронного распыления в высоковакуумной камере (начальное давление <10–5 Па), оборудованной тремя конфокальными мишенями и криогенным насосом [23]. Покрытия осаждались на подложки Si с тонким поверхностным слоем SiO2 толщиной 10 нм (для предотвращения диффузии компонент покрытия в подложку). С целью проведения элементного анализа пленок в исходном состоянии мононитриды ZrN, CrN, Si3N4 осаждались также на подложки углерода. В ходе осаждения к подложке прикладывалось постоянное напряжение смещения, равное –60 В, при этом подложка вращалась со скоростью 15 об./мин для обеспечения равномерной скорости осаждения по всей площади подложки.
Мишени Zr (99.2% чистоты), Cr (99.95% чистоты) и Si3N4 (99.99% чистоты) диаметром 7.62 см, расположенные на расстоянии 18 см от держателя подложки, распылялись плазмой Ar + N2 в режиме постоянной мощности. Мишени Zr и Cr были задействованы в конфигурации несбалансированного магнетронного распыления с использованием источника постоянного тока, в то время как для мишени Si3N4 использовался высокочастотный источник в режиме сбалансированного магнетронного распыления. Рабочее давление в камере составляло 0.20 Па при осаждении слоев ZrN и CrN и 0.22 Па для слоев SiNx (табл. 1), при этом измерения проводились емкостным датчиком Baratron®. На основе проведенных ранее экспериментов [24, 25] оптимизировалось отношение плотностей потоков газов Ar/N2 в камеру с целью получения близкого к стехиометрическому содержания азота в составе покрытия. Парциальное давление N2 контролировалось в ходе осаждения с помощью масс-спектрометра MKS Microvision.
Таблица 1.
Параметры осаждения и состав покрытий мононитридов ZrN, CrN и Si3N4
Пленка | Tос ,°C | Zr Мощ- ность, Вт |
Cr Мощ-ность, Вт | Si3N4 Мощ-ность, Вт | Рабочее давление, Па | Давление азота, Па | Толщина пленки, нм | Zr, aт. % |
Cr, aт. % |
Si, aт. % |
N, aт. % |
---|---|---|---|---|---|---|---|---|---|---|---|
ZrN | 300 | 300 | − | − | 0.20 | 4.6 × 10–3 | 249 | 46.6 | − | − | 53.4 |
CrN | 450 | − | 200 | − | 0.20 | 6.3 × 10–2 | 259 | − | 54.6 | − | 45.4 |
Si3N4 | 300 | − | − | 176 | 0.22 | 2.4 × 10–2 | 287 | − | − | 43.3 | 56.7 |
Рост пленок мононитридов ZrN и многослойных пленок ZrN/SiNx осуществлялся при температуре подложки 300°C, в то время как для пленок мононитридов CrN и многослойных пленок CrN/SiNx температура подложки составляла 450°C. Пленки Si3N4 были получены при обеих температурах.
В случае многослойных пленок периодический рост слоев контролировался управляемыми с компьютера пневматическими затворами, расположенными на расстоянии 2 см от каждой из мишеней. При этом осаждение начиналось со слоя ZrN (CrN). Более детальное описание процедуры и особенностей формирования многослойных покрытий дано в работе [22]. В табл. 1 приведены условия осаждения покрытий мононитридов, те же самые условия были использованы при формировании отдельных слоев структур ZrN/SiNx и CrN/SiNx, за исключением времени осаждения, которое подбиралось для получения необходимых толщин слоев. Суммарная толщина пленок всех типов составляла около 300 нм. Соотношение толщин отдельных слоев в многослойных пленках ZrN/SiNx составляло: 2 нм/5 нм, 5 нм/5 нм, 5 нм/10 нм, 10 нм/10 нм, 10 нм/5 нм. Для пленок CrN/SiNx − 2 нм/5 нм, 5 нм/5 нм, 5 нм/10 нм, 10 нм/5 нм.
Элементный состав осажденных пленок, а также пленок, подвергнутых отжигу на воздухе, определялся методом рентгеноспектрального микроанализа (РСМА). РСМА проводился с использованием спектрометра Oxford Instruments, сопряженного с растровым электронным микроскопом (РЭМ) JEOL 7001F-TTLS. Спектры РСМА были получены при напряжении 10 кВ и токе зонда 10 нА. В случае пленок Si3N4, отличающихся меньшей плотностью, использовались напряжение 5 кВ и ток зонда 5 нА. Пониженные значения напряжения и тока зонда выбирались с целью исключения вклада подложки (сигнал элемента подложки практически не превышал уровня фона). Количественные расчеты производились с использованием программного обеспечения INCA Energy+. При использовании этого же микроскопа анализировали топографию поверхности пленок после отжига на воздухе.
Для анализа структурно-фазового состояния пленок применялся рентгеноструктурный анализ (РСА). РСА проводился с помощью дифрактометра D8 Bruker, действующего в конфигурации Брэгга-Брентано с использованием излучения CuKα (длина волны 0.15418 нм, детектор Lynx Eye).
Отжиг образцов на воздухе осуществлялся последовательно при различных температурах в интервале 400−950°C. Процесс окисления анализировался путем проведения эксперимента in situ. Образцы размещались на предметном столике, снабженном резистивным нагревателем и помещенном в дифрактометр Bruker D8. Столик представлял собой изготовленный из AlN держатель образца и полусферический графитовый купол, подвергаемый воздушному обдуву. Время съемки в ходе изотермического отжига при каждой из температур составляло 40−60 мин.
РЕЗУЛЬТАТЫ И ИХ ОБСУЖДЕНИЕ
Структурно-фазовый состав исходных многослойных пленок ZrN/SiNx и СrN/SiNx
Элементный состав отдельных слоев в многослойных системах соответствует составу пленок мононитридов ZrN, CrN и Si3N4, приведенному в табл. 1. При исследовании методом РСМА покрытий, осажденных на подложки Si, регистрировался кислород (в пределах 1.5−2.0 ат. %), что может быть обусловлено наличием тонкого оксидного слоя как на поверхности пленки, так и слоя SiO2 толщиной 10 нм на поверхности подложки.
Как было показано методом просвечивающей электронной микроскопии в работе [22], в результате последовательного осаждения отдельных слоев ZrN и SiNx имеет место образование сплошных слоев с плоскопараллельными и четко различимыми границами. При этом даже тонкие слои толщиной 1 нм были достаточно четко различимы, что наглядно демонстрирует отсутствие перемешивания слоев ZrN и SiNx между собой.
На рис. 1, 2 приведены фрагменты рентгенограмм для многослойных пленок ZrN/SiNx и СrN/SiNx. В приведенном интервале углов присутствуют два наиболее интенсивных пика кубической фазы ZrN (111) и (200) и лишь один пик кубической фазы СrN (200). Следует отметить, что во всем исследованном интервале углов отражения (2θ = 20°−65°) не регистрировалось других линий, за исключением мононитрида ZrN, для которого фиксировался слабый рефлекс, соответствующий углу 2θ, равному 56.38° (линия (220)). Поэтому, судить об эволюции структурного состояния фазы ZrN оказывается возможным лишь по линиям (111) и (200), а фазы СrN – по линии (200).
Рис. 1.
Рентгенограммы покрытий мононитрида ZrN и многослойных покрытий ZrN/SiNx с различным отношением толщины слоя ZrN к толщине слоя SiNx в исходном состоянии.

Рис. 2.
Рентгенограммы покрытий мононитрида CrN и многослойных покрытий CrN/SiNx с различным отношением толщины слоя CrN к толщине слоя SiNx в исходном состоянии.
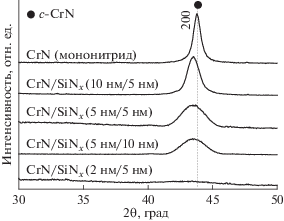
Из рис. 1 следует, что при добавлении промежуточного слоя SiNx между слоями ZrN в них происходит переход от преимущественной ориентации (111) кристаллитов нитрида циркония к ориентации (200). При достижении соотношения толщин слоев ZrN и SiNx, равного 5 нм/5 нм, наблюдается увеличение полной ширины на полувысоте максимума дифракционного пика, а также уменьшение его интенсивности. При соотношении толщин 2 нм/5 нм пленка становится практически рентгеноаморфной.
Наблюдаемая эволюция пиков (111) и (200) фазы ZrN для многослойных пленок может быть связана со следующими изменениями их структуры. Для пленок ZrN/SiNx добавление слоя SiNx приводит к подавлению столбчатого роста зерен фазы ZrN с преимущественной ориентацией (111) и заметному увеличению параметра решетки по сравнению с пленкой мононитрида ZrN (табл. 2). Рост параметра решетки (как правило) сопровождается ростом сжимающих напряжений. В нашем случае, наибольшее увеличение параметра решетки фазы ZrN для многослойных покрытий ZrN/SiNx происходит при уменьшении толщины слоя ZrN до 5 нм и менее. Как отмечалось, при этом имеет место увеличение полной ширины на полувысоте максимума дифракционного пика: от 1.6° для соотношения толщины слоя ZrN к толщине слоя SiNx, равного 10 нм/5 нм, до 3.1° для случая 5 нм/5 нм. Последний факт может свидетельствовать о существенном уменьшении размера кристаллитов в слоях ZrN по мере уменьшения их толщины.
Таблица 2.
Значение параметра решетки фазы нитрида переходного металла: ZrN, либо CrN, в зависимости от вида покрытия
Вид покрытия | Параметр решетки а, Å |
---|---|
Мононитриды | |
ZrN | 4.590 |
CrN | 4.133 |
Многослойные покрытия ZrN/SiNx | |
ZrN/SiNx (10 нм/5 нм) | 4.611 |
ZrN/SiNx (10 нм/10 нм) | 4.613 |
ZrN/SiNx (5 нм/5 нм) | 4.628 |
ZrN/SiNx (5 нм/10 нм) | 4.629 |
ZrN/SiNx (2 нм/5 нм) | − |
Многослойные покрытия СrN/SiNx | |
CrN/SiNx (10 нм/5 нм) | 4.159 |
CrN/SiNx (5 нм/5 нм) | 4.162 |
CrN/SiNx (5 нм/10 нм) | 4.159 |
CrN/SiNx (2 нм/5 нм) | − |
Как уже отмечалось, для покрытия мононитрида CrN регистрируется только дифракционный максимум, соответствующий линии (200). Для многослойных покрытий СrN/SiNx также наблюдается только один пик (рис. 2). При этом значение параметра решетки фазы CrN для многослойных покрытий также существенно больше, чем для пленки мононитрида CrN (табл. 2). Как и в случае пленок ZrN/SiNx, имеет место уширение дифракционного пика по мере уменьшения отношения толщины слоя CrN к толщине слоя SiNx, что может свидетельствовать об уменьшении размера кристаллитов. Однако, угловое положение дифракционного пика существенно не изменяется. Последнее означает, что для рассмотренных соотношений толщин отдельных слоев величина сжимающих напряжений остается на одном уровне.
Таким образом, основными закономерностями изменения структуры фазы ZrN и CrN в многослойных пленках ZrN/SiNx и СrN/SiNx являются:
1) наличие преимущественной ориентации (200);
2) превышение значения параметра решетки по сравнению с параметром решетки для покрытий мононитридов ZrN и CrN, что указывает на наличие сжимающих напряжений;
3) уменьшение размеров кристаллитов при уменьшении толщины слоя ZrN (либо CrN) при постоянной толщине слоя SiNx;
4) многослойные пленки ZrN/SiNx (либо СrN/SiNx) становятся рентгеноаморфными (как и в случае пленки мононитрида Si3N4) при уменьшении толщины слоя ZrN (либо CrN) до 2 нм.
Стойкость к окислению многослойных пленок ZrN/SiNx и СrN/SiNx при отжиге на воздухе
Результаты РСА пленок мононитридов ZrN и CrN в сравнении с многослойными пленками ZrN/SiNx и СrN/SiNx в ходе отжига на воздухе в интервале температур 400−950°C представлены на рис. 3, 4. Из рисунков видно, что окисление пленки ZrN начинается уже при достижении температуры 550°C, и при температуре 700°C дифракционный максимум, соответствующий фазе нитрида циркония, не регистрируется, зато проявляются пики оксидов m-ZrO2 и t-ZrO2 (рис. 3а). В то же время, пленка CrN начинает окисляться при температуре 700°C, и исчезновение пика фазы CrN происходит при температуре 860°C (рис. 4а). При этом появляются пики оксида t-Сr2O3.
Рис. 3.
Рентгенограммы подвергнутых отжигу на воздухе в интервале температур 400−950°C покрытий мононитрида ZrN (a) и многослойных покрытий ZrN/SiNx с различным отношением толщины слоя ZrN к толщине слоя SiNx: 5 нм/5 нм (б), 5 нм/10 нм (в), 2 нм/5 нм (г).
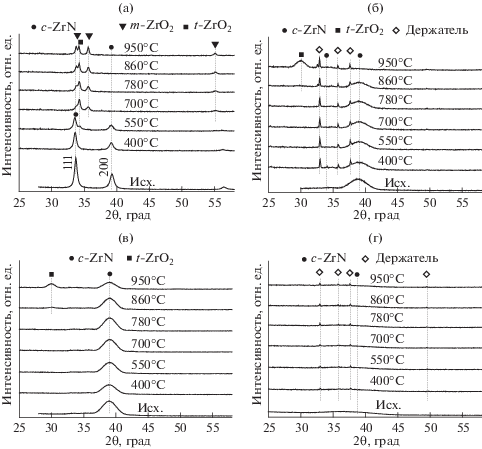
Рис. 4.
Рентгенограммы подвергнутых отжигу на воздухе в интервале температур 400−950°C покрытий мононитрида CrN (а) и многослойных покрытий CrN/SiNx с различным отношением толщины слоя СrN к толщине слоя SiNx: 5 нм/5 нм (б), 5 нм/10 нм (в), 2 нм/5 нм (г).
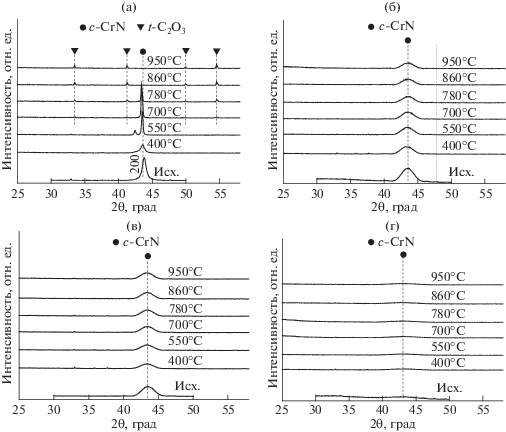
Окисление многослойных структур ZrN/SiNx начинается при температурах 860−950°C (рис. 3б, 3в), и пик оксидной фазы t-ZrO2 начинает заметно проявляться только при 950°C. Для покрытия с отношением толщины слоя ZrN к толщине слоя SiNx, равном 5 нм/5 нм, пик фазы ZrN исчезает лишь при температуре 950°C (рис. 3б). По мере уменьшения отношения толщины слоя ZrN к толщине слоя SiNx стойкость пленки к окислению возрастает, т.е. для покрытий ZrN/SiNx (5 нм/10 нм) пик фазы нитрида циркония регистрируется вплоть до температуры 950°C (рис. 3в). Примечательным является тот факт, что пленка ZrN/SiNx (2 нм/5 нм), являясь рентгеноаморфной в исходном состоянии, остается таковой и после отжига. При этом оксидные фазы в ее составе не обнаруживаются. Последний факт может быть связан с тем, что при той же самой суммарной толщине (∼300 нм) данная пленка состоит из большего количества индивидуальных слоев. Это может способствовать повышению ее стабильности при окислении за счет увеличения плотности границ между слоями, что служит фактором, препятствующим диффузии кислорода вглубь пленки. Близкое к аморфному состояние слоев ZrN в данной пленке, связанное с крайне малым размером зерен, также способствует подавлению диффузии кислорода вдоль границ зерен.
Анализ стойкости к окислению многослойных покрытий CrN/SiNx в ходе отжига на воздухе в интервале температур 400−950°C (рис. 4) свидетельствует об их существенно более высокой стабильности по сравнению с многослойными покрытиями ZrN/SiNx. Для всех рассматриваемых отношений толщин слоя CrN к толщине слоя SiNx, а именно, 5 нм/5 нм, 5 нм/10 нм, 2 нм/5 нм, методом РСА не обнаруживается появления оксидной фазы, и вплоть до температуры 950°C пик фазы CrN практически сохраняет свою интенсивность (рис. 4б, 4в). Структура многослойной пленки CrN/SiNx с отношением толщин индивидуальных слоев 2 нм/5 нм остается рентгеноаморфной при всех температурах отжига (рис. 4г), как и в случае системы ZrN/SiNx (рис. 3г).
Анализ содержания элементов в составе пленок мононитридов ZrN, CrN и многослойных пленок ZrN/SiNx и CrN/SiNx после отжига на воздухе представлен в табл. 3. Из таблицы следует, что, в случае системы ZrN/SiNx наибольшей стойкостью к высокотемпературному окислению обладает пленка с отношением толщины слоя ZrN к толщине слоя SiNx, равном 2 нм/5 нм. Среднее по всей толщине пленки содержание азота для этой пленки после отжига составляет 33.1 ат. %, что значительно выше по сравнению с другими многослойными покрытиями ZrN/SiNx. Следует отметить, что в табл. 3 приводится интегральное содержание элементов, соответствующее всей толщине покрытия. В связи с этим, полученные данные позволяют проводить прежде всего относительное сравнение стойкости к окислению многослойных пленок двух систем – ZrN/SiNx и CrN/SiNx – с одинаковыми соотношениями толщин индивидуальных слоев.
Таблица 3.
Результаты элементного анализа покрытий мононитридов ZrN, CrN и SiNx, а также многослойных покрытий ZrN/SiNx и СrN/SiNx после отжига на воздухе в интервале температур 400−950°C
Пленка | Zr, aт. % |
Сr aт. % |
Si aт. % |
N aт. % |
O aт. % |
---|---|---|---|---|---|
Мононитриды | |||||
ZrN | 27.8 | − | − | − | 72.2 |
CrN | − | 37.3 | − | − | 62.7 |
Si3N4 | − | − | 32.0 | 40.0 | 28.0 |
Многослойные покрытия ZrN/SiNx | |||||
ZrN/SiNx (10 нм/5 нм) | 17.4 | − | 14.0 | 1.0 | 67.6 |
ZrN/SiNx (5 нм/5 нм) | 12.0 | − | 20.1 | 3.6 | 64.3 |
ZrN/SiNx (5 нм/10 нм) | 10.4 | − | 25.7 | 17.8 | 46.1 |
ZrN/SiNx (2 нм/5 нм) | 9.1 | − | 30.3 | 33.1 | 27.5 |
Многослойные покрытия СrN/SiNx | |||||
СrN/SiNx (10 нм/5 нм) | − | 32.6 | 13.8 | 39.3 | 14.3 |
СrN/SiNx (5 нм/5 нм) | − | 20.2 | 21.2 | 41.0 | 17.6 |
СrN/SiNx (5 нм/10 нм) | − | 13.1 | 26.0 | 43.7 | 17.2 |
СrN/SiNx (2 нм/5 нм) | − | 12.2 | 28.5 | 40.2 | 19.1 |
Обращает на себя внимание факт значительно меньшего содержания кислорода в многослойных пленках CrN/SiNx, подвергнутых отжигу на воздухе (табл. 3). В отличие от пленки мононитрида CrN, окислившейся полностью, в многослойных пленках CrN/SiNx содержание кислорода после проведения процедуры отжига составляет 14−19 ат. %. Следует отметить, что в отличие от системы ZrN/SiNx, для пленок CrN/SiNx с соотношениями толщин индивидуальных слоев CrN к SiNx, равным 10 нм/5 нм, 5 нм/5 нм, 5 нм/10 нм, 2 нм/5 нм, степень окисления существенно не изменяется при варьировании указанного соотношения толщин. Тем не менее, наименьшее содержание кислорода в пленке CrN/SiNx с соотношением толщин индивидуальных слоев CrN к SiNx, равным 10 нм/5 нм, связано, по-видимому, с превалирующей ролью оксида хрома как пассивирующей пленки в условиях высокотемпературного отжига. В этом наблюдается явное отличие системы CrN/SiNx от системы ZrN/SiNx, для которой преобладание отношения толщины слоя SiNx к толщине слоя ZrN является фактором, способствующим повышению стойкости покрытия к высокотемпературному окислению.
На рис. 5−7 показана топография поверхности пленок мононитридов ZrN, CrN и Si3N4 (рис. 5), а также многослойных покрытий ZrN/SiNx (рис. 6) и CrN/SiNx (рис. 7), подвергнутых процедуре отжига в интервале температур 400−950°C. Сразу обращает на себя внимание факт высокой степени повреждения в ходе отжига покрытий мононитридов ZrN и CrN (рис. 5а, 5б). В первом случае наблюдается высокая плотность очагов коррозии, приводящих к вспучиванию покрытия (рис. 5а). Во втором случае происходит интенсивное растрескивание и отшелушивание покрытия (рис. 5б). Интенсивное отслаивание в результате отжига наблюдается и для пленок Si3N4 (рис. 5в).
Рис. 5.
Топография поверхности отожженных на воздухе покрытий мононитридов ZrN (а), CrN (б) и Si3N4 (в).
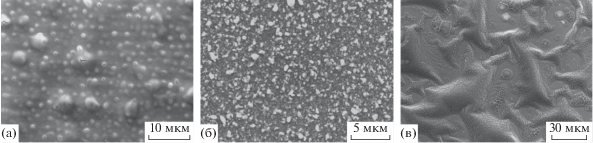
Рис. 6.
Топография поверхности отожженных на воздухе многослойных покрытий ZrN/SiNx с различным отношением толщины слоя ZrN к толщине слоя SiNx: 5 нм/5 нм (а), 5 нм/10 нм (б), 2 нм/5 нм (в).
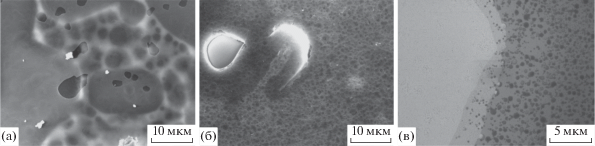
Рис. 7.
Топография поверхности отожженных на воздухе многослойных покрытий CrN/SiNx с различным отношением толщины слоя СrN к толщине слоя SiNx: 5 нм/5 нм (а), 5 нм/10 нм (б), 2 нм/5 нм (в).
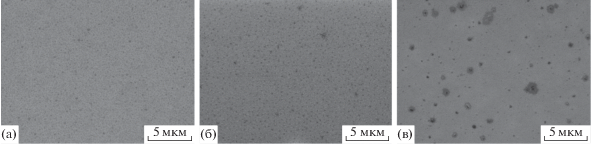
Для покрытий ZrN/SiNx степень повреждения поверхности высокотемпературной коррозией заметно уменьшается по мере уменьшения отношения толщины слоя ZrN к толщине слоя SiNx (рис. 6а−6в).
В случае пленок CrN/SiNx для всех соотношений толщин имеет место возникновение точечных очагов высокотемпературной коррозии (рис. 7а−7в). Однако, эти очаги в большинстве своем не перерастают в комплексы, следствием чего является отсутствие областей отслаивания покрытия, приводящих к нарушению его целостности.
Таким образом, проведенный методами РСА, РСМА и СЭМ анализ многослойных покрытий ZrN/SiNx и CrN/SiNx позволяет сделать вывод об их большей стойкости к высокотемпературному окислению по сравнению с покрытиями мононитридов ZrN и CrN. При этом наибольший эффект дает система CrN/SiNx.
ЗАКЛЮЧЕНИЕ
Сформированные магнетронным распылением многослойные покрытия ZrN/SiNx и CrN/SiNx представляют собой последовательное чередование нанокристаллических слоев фазы ZrN (CrN), обладающей преимущественной ориентацией (002), и аморфных слоев SiNx. Параметр решетки фазы нитрида металла для многослойных структур превышает параметр решетки, соответствующий пленкам мононитридов ZrN и CrN, что свидетельствует о наличии сжимающих напряжений. При формировании многослойных структур ZrN/SiNx и CrN/SiNx уменьшение отношения толщины слоя ZrN (CrN) к толщине слоя SiNx приводит к уменьшению размера кристаллитов фазы нитрида металла.
Анализ многослойных пленок ZrN/SiNx и CrN/SiNx позволяет сделать вывод об их более высокой стойкости к высокотемпературному окислению по сравнению с пленками мононитридов ZrN, CrN и Si3N4.
Стойкость пленок ZrN/SiNx к окислению повышается при уменьшении отношения толщины индивидуального слоя ZrN к толщине индивидуального слоя SiNx, а также при увеличении количества слоев в пленке.
Пленки CrN/SiNx обладают существенно большей стойкостью к высокотемпературному окислению по сравнению с пленками ZrN/SiNx. Соотношение индивидуальных слоев CrN и SiNx при этом не является предопределяющим фактором.
Список литературы
Abadias G., Koutsokeras L.E., Siozios A., Patsalas P. // Thin Solid Films. 2013. V. 538. P. 56. https://doi.org/10.1016/j.tsf.2012.10.119
Barshilia H.C., Deepthi B., Arun Prabhu A.S., Rajam K.S. // Surf. Coat. Technol. 2006. V. 201. P. 329. https://doi.org/10.1016/j.surfcoat.2005.11.124
Harris S.G., Doyle E.D., Vlasveld A.C. et al. // Wear. 2003. V. 254. P. 723. https://doi.org/10.1016/S0043-1648(03)00258-8
Chen L., He L., Xu Y. et al. // Surf. Coat. Technol. 2014. V. 244. P. 87. https://doi.org/10.1016/j.surfcoat.2014.01.063
Koller C.M., Hollerweger R., Sabitzer C. et al. // Surf. Coat. Technol. 2014. V. 259. P. 599. https://doi.org/10.1016/j.surfcoat.2014.10.024
Pfeiler M., Fontalvo G.A., Wagner J. et al. // Tribol. Lett. 2008. V. 30. P. 91. https://doi.org/10.1007/s11249-008-9313-6
Stueber M., Albers U., Leiste H. et al. // Surf. Coat. Technol. 2006. V. 200. P. 6162. https://doi.org/ 10.1016/j.surfcoat.2005.11.012
Wei R., Rincon C., Langa E. // J. Vac. Sci. Technol., A. 2010. V. 28. No. 5. P. 1126. https://doi.org/10.1116/1.3463709
Barshilia H.C., Deepthi B., Rajam K.S. // Surf. Coat. Technol. 2007. V. 201. P. 9468. https://doi.org/ 10.1016/j.surfcoat.2007.04.002
Cheng Y.H., Browne T., Heckerman B., Meletis E.I. // Surf. Coat. Technol. 2010. V. 204. P. 2123. https://doi.org/10.1016/j.surfcoat.2009.11.034
Chena Y.-I., Gaoa Y.-X., Chang L.-C. // Surf. Coat. Technol. 2017. V. 332. P. 72. https://doi.org/ 10.1016/j.surfcoat.2017.09.087
Yalamanchili K., Schramm I.C., Jiménez-Piqué E. et al. // Acta Mater. 2015. V. 89. P. 22. https://doi.org/10.1016/ j.actamat.2015.01.066
Weirather T., Chladil K., Sartory B. et al. // Surf. Coat. Technol. 2014. V. 257. P. 48. https://doi.org/10.1016/ j.surfcoat.2014.06.018
Bai X., Zheng W., An T., Jiang Q. // J. Phys.: Condens. Matter. 2005. V. 17. P. 6405. https://doi.org/10.1088/0953-8984/17/41/011
Saladukhin I.A., Abadias G., Uglov V.V. et al. // Surf. Coat. Technol. 2017. V. 332. P. 428. https:// doi.org/10.1016/j.surfcoat.2017.08.076
Bobzin K., Brögelmann T., Kruppe N.C. et al. // Surf. Coat. Technol. 2017. V. 332. P. 253. https://doi.org/ 10.1016/j.surfcoat.2017.06.092
Contreras E., Galindez Y., Rodas M.A. // Surf. Coat. Technol. 2017. V. 332. P. 214. https://doi.org/ 10.1016/j.surfcoat.2017.07.086
Changa Y.-Y., Wenga S.-Y., Chena C.-H., Fu F.-X. // Surf. Coat. Technol. 2017. V. 332. P. 494. https:// doi.org/10.1016/j.surfcoat.2017.06.080
Peruško D., Webb M.J., Milinović V. et al. // Nucl. Instrum. Methods Phys. Res., Sect. B. 2008. V. 266. P. 1749. https://doi.org/10.1016/j.nimb.2008.02.034
Kim I., Jiao L., Khatkhatay F. et al. // J. Nucl. Mater. 2013. V. 441. P. 47. https://doi.org/10.1016/j.jnucmat. 2013.05.035
Soares T.P., Aguzzoli C., Soares G.V. et al. // Surf. Coat. Technol. 2013. V. 237. P. 170. https://doi.org/ 10.1016/j.surfcoat.2013.09.061
Abadias G., Uglov V.V., Saladukhin I.A. et al. // Surf. Coat. Technol. 2016. V. 308. P. 158. https://doi.org/ 10.1016/j.surfcoat.2016.06.099
Colin J.J., Diot Y., Guerin P. et al. // Rev. Sci. Instrum. 2016. V. 87. P. 023902. https://doi.org/10.1063/1.4940933
Abadias G., Koutsokeras L.E., Dub S.N. et al. // J. Vac. Sci. Technol. 2010. V. A28. P. 541. https://doi.org/10.1116/1.3426296
Simonot L., Babonneau D., Camelio S. et al. // Thin Solid Films. 2010. V. 518. P. 2637. https://doi.org/10.1016/j.tsf.2009.08.005
Дополнительные материалы отсутствуют.
Инструменты
Поверхность. Рентгеновские, синхротронные и нейтронные исследования