Поверхность. Рентгеновские, синхротронные и нейтронные исследования, 2020, № 6, стр. 82-87
Исследование термической стабильности наноструктурных алюмоматричных композиционных материалов, модифицированных фуллереном С60
И. А. Евдокимов *, Р. Р. Хайруллин a, b, **, С. В. Прокудин a, Р. Х. Баграмов a, В. В. Аксененков a, С. А. Перфилов a, А. А. Поздняков a, А. С. Усеинов a
a Технологический институт сверхтвердых и новых углеродных материалов
108840 Москва, Троицк, Россия
b Московский физико-технический институт
141701 Московская область, Долгопрудный, Россия
* E-mail: ivan_911@mail.ru
** E-mail: radionovi4@bk.ru
Поступила в редакцию 30.10.2019
После доработки 25.12.2019
Принята к публикации 26.12.2019
Аннотация
Исследовано влияние термической обработки на структуру, фазовый состав и механические свойства наноструктурных алюмоматричных композиционных материалов, модифицированных фуллереном С60. Методом индентирования и одноосного сжатия в интервале температур от 25 до 350°C изучены прочность, твердость и модуль упругости исследуемых материалов. Установлена зона температурной стабильности структуры и фазового состава композитов и возможный температурный интервал эксплуатации изделий на их основе.
ВВЕДЕНИЕ
Современное материаловедение направлено на создание новых материалов с улучшенными физико-механическими, технологическими и эксплуатационными свойствами для различных областей науки и техники. Наиболее обширный класс конструкционных материалов – это металлы, сплавы и композиты на их основе [1]. Традиционные методы получения и обработки таких материалов зачастую не позволяют добиться требуемого уровня физико-механических свойств. Одним из перспективных методов повышения прочностных характеристик металлических материалов является наноструктурирование в совокупности с дополнительным модифицированием различными ультрадисперсными частицами, волокнами или усами. В последнее десятилетие в данном направлении проведено множество работ и получены наноструктурные композиционные материалы с экстремально высокими прочностными, транспортными, электронными и другими свойствами, востребованными в современной науке и технике [2]. Наиболее изучаемый класс подобных наноструктурных металломатричных композитов – класс композитов на основе алюминия, что обусловлено его широким применением, относительно низкой температурой плавления и привлекательными физико-механическими и химическими свойствами.
В качестве модифицирующей фазы наноструктурных алюмоматричных композитов, как правило, выступают различные ультрадисперсные оксиды, карбиды, нитриды и другие частицы, например, углеродные наноструктуры (УНС) [2]. Каждая из перечисленных выше систем обладает совокупностью тех или иных привлекательных свойств, однако алюмоматричные композиционные материалы, модифицированные углеродными наноструктурами, представляют отдельный вид композитов, так как в данном случае речь идет не только о дисперсном упрочнении наноструктурной матрицы высокомодульными частицами, но и об использовании уникальных свойств УНС [3].
Стоит отметить, что в данном направлении выполнено множество работ, получены прорывные свойства, однако этот класс материалов все еще не нашел своего широкого применения [4–6]. В первую очередь это связано со сложностью получения объемных образцов наноструктурных композитов, их обработки и исследования. Для установления возможных областей применения таких материалов необходимо пройти один из важных этапов характеризации – исследование их термической стабильности и влияния температуры на ключевые механические свойства.
В рамках настоящей работы методами порошковой металлургии получен объемный наноструктурный композиционный материал на основе алюминий-магниевого сплава АМг6, модифицированный фуллереном С60, и исследована его термическая стабильность в интервале температур 25–350°С.
МАТЕРИАЛЫ И МЕТОДЫ ИССЛЕДОВАНИЯ
В качестве исходных материалов для получения наноструктурного композита использовали алюминий-магниевый сплав АМг6 (ГОСТ 4784-97) и фуллерен С60 (99.5%). Механическое легирование исходных материалов проводили в планетарной шаровой мельнице АГО-2У. Для предотвращения окисления и протекания других нежелательных реакций все манипуляции с исходными материалами и наноструктурными порошками осуществляли в заполненном аргоном изолирующем перчаточном боксе, поддерживающем чистоту атмосферы по кислороду и парам воды не хуже 0.1 млн–1. Объемные образцы наноструктурного композиционного материала были получены методом прямой горячей экструзии механолегированных порошковых смесей через фильеру с круглым сечением (степень деформации 6.2, давление истечения материала 1.5–1.7 ГПа).
Образцы для структурных исследований методами оптической (Olimpus BX51), растровой (JSM-7600F) и просвечивающей (JEM-2010) электронной микроскопии подвергали механической полировке и химическому травлению. Рентгенофазовый анализ (РФА) порошков выполняли на дифрактометре PANalytical Empyrean (CuKα-излучение). На основании полученных дифрактограмм с помощью программы MAUD методом функциональных параметров определяли средний размер кристаллитов (областей когерентного рассеяния). Исследования методом спектроскопии комбинационного рассеяния света (КРС) проводили с помощью установки на базе спектрометра TRAIX 552 и детектора CCD Spec-10, 2KBUV 2048 × 512. В качестве возбуждающего излучения применяли лазер BeamLok 2065-7S (Spectra-Physics) с длиной волны 512 нм и лазер WaveTrain с длиной волны 257 нм. Термическую стабильность полученных материалов исследовали методом дифференциальной сканирующей калориметрии (ДСК) на установке Perkin Elmer DSC8000.
Механические свойства (твердость и модуль упругости) измеряли с использованием нанотвердомера “НаноСкан-4D” оснащенного выокотемпературным измерительным модулем, методом инструментального индентирования в соответствии с ISO 14577. Исследование прочности образцов при сжатии проводили на универсальной испытательной машине Instron 5982, оснащенной высокотемпературным испытательным модулем.
РЕЗУЛЬТАТЫ И ИХ ОБСУЖДЕНИЕ
Образцы наноструктурных алюмоматричных композиционных материалов, модифицированных фуллереном С60, были получены методом совместного размола исходных компонентов в планетарной шаровой мельнице АГО-2У в атмосфере аргона. Подробно особенности получения порошков таких материалов описаны в [7].
Методом рентгеноструктурного анализа (рис. 1а) и растровой электронной микроскопии (РЭМ) (рис. 1б) было установлено, что средний размер кристаллитов алюминия в полученных порошках составляет 50–60 нм. Наноструктурированные металлические материалы, как правило, метастабильны и при приложении к ним внешнего воздействия, в частности температуры, переходят в энергетически более выгодное состояние. В случае металлов это может быть рекристаллизация, распад твердого раствора и другие структурно-фазовые превращения. Для исследования термической стабильности полученных порошков наноструктурного композита был применен метод ДСК. В интервале температур 290–310°С на кривых ДСК наблюдаются экзо- и эндотермические пики (рис. 2).
Рис. 1.
Исследование структуры порошков наноструктурного композиционного материала методами: а – РФА (1 – алюминий 99.9%, 2 – исходный сплав АМг6, 3 – порошок АМг6 + 0.3 мас. % фуллерена С60 после механического легирования); б – РЭМ-изображение порошка композита АМг6 + 0.3 мас. % фуллерена С60 после механического легирования.
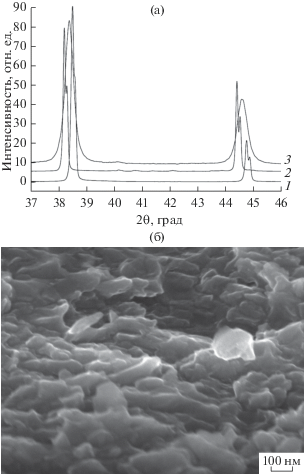
Рис. 2.
Исследование порошка наноструктурного композиционного материала, методом ДСК: 1 – первое измерение; 2 – повторное измерение.
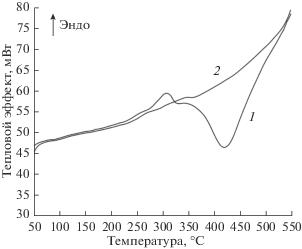
Для выявления обратимости происходящих превращений каждый образец был подвергнут испытанию дважды. Было установлено, что превращения, происходящие при нагреве до 290°С и выше, необратимы. Методом КРС и РФА было установлено, что наблюдаемые тепловые эффекты вызваны процессами рекристаллизации (средний размер кристаллитов после испытания увеличился до 130–140 нм) и образованием карбида алюминия Al4C3 (рис. 3). Таким образом, на основании полученных данных был установлен температурный интервал стабильности структуры и фазового состава полученных порошков наноструктурного композита 270–290°С и определены параметры получения его объемных образцов (рис. 4).
Рис. 3.
Исследование структуры и фазового состава наноструктурного композиционного материала после термической обработки методом: а – РФА (1 – порошок композита после механического легирования, 2 – композит после экструзии при 270°С, 3 – экструдированный композит после отжига при 400°С); б – КРС (1 – композит после экструзии при 270°С, 2 – экструдированный композит после отжига при 400°С).
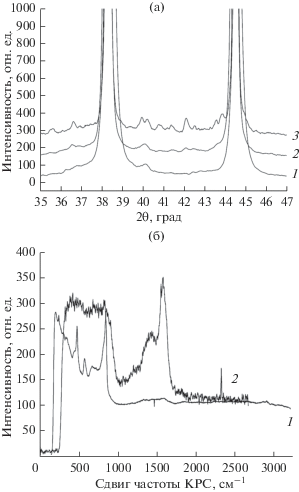
Рис. 4.
Внешний вид экструдатов наноструктурного композиционного материала и приготовленных образцов для испытаний.
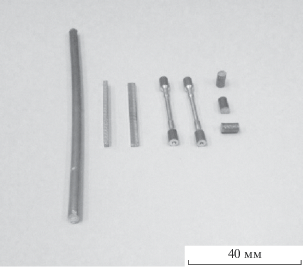
Как известно, особенностью экструдированных материалов является анизотропия структуры и свойств. Для оценки ее влияния были испытаны образцы, вырезанные вдоль и поперек оси экструзии. Вследствие резкого разупрочнения алюминиевых сплавов при высоких температурах диапазон их эксплуатации сплавов, как правило, составляет 120–250°С и крайне редко превышает 300°С. Поэтому механические свойства полученных образцов измеряли в диапазоне температур 25–350°C [8]. Измерение твердости и модуля упругости проводили методом инструментального индентирования с помощью нанотвердомера “НаноСкан-4D” [9, 10]. Нагрев и контроль температуры подготовленных образцов осуществляли с использованием встраиваемого высокотемпературного модуля, позволяющего осуществлять гомогенный нагрев образца и поддерживать заданную температуру с точностью ±0.1°C. Твердость измеряли в соответствии с рекомендациями ГОСТ Р 8.748-2011 (ИСО 14577-1:2002) [11]. На рис. 5 приведены графики зависимости твердости образцов наноструктурного композиционного материала от температуры испытания. Кривые демонстрируют немонотонное убывание твердости. В области температур 25–200°С наблюдается плавное снижение прочностных характеристик на 8–12%. Стоит отметить, что многократное испытание того же образца в данной температурной области показало стабильность значений твердости при каждой итерации. Такая стабильность свойств подтверждает отсутствие в наноструктурных композиционных материалах каких-либо структурно-фазовых превращений, способных негативно повлиять на результаты испытания. В диапазоне температур 200–300°С наблюдается резкое, но обратимое падение свойств композита до характеристик исходного матричного сплава. Значения твердости и модуля упругости изменяются квазилинейно, что позволяет прогнозировать прочность материала при испытании или эксплуатации. При испытании наноструктурного композита выше 300°С наблюдается дальнейшее ухудшение свойств, однако в данном случае оно необратимо. Повторное испытание перегретых выше 300°С образцов показало существенное (более чем на 50%) ослабление свойств даже при 25°С. Такое поведение материала полностью согласуется с результатами исследований методами ДСК, РФА и КРС.
В дополнение к испытаниям методом индентирования полученные образцы были испытаны методом одноосного сжатия при различных температурах. На рис. 6 представлены результаты проведенных исследований. Из представленных данных видно, что предел прочности при сжатии снижается с увеличением температуры и достигает минимума при 300–350°С. Характер изменения свойств образцов при сжатии идентичен результатам индентирования, описанным выше. Разницу в динамике изменения прочности/твердости/модуля упругости можно объяснить объемным фактором.
Рис. 5.
Зависимость твердости образцов наноструктурного композиционного материала от температуры испытания: 1 – вдоль оси экструзии; 2 – поперек оси экструзии.
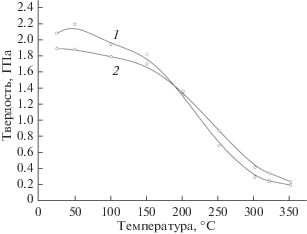
Рис. 6.
Результаты испытания методом одноосного сжатия образцов наноструктурного композиционного материала при различных температурах.
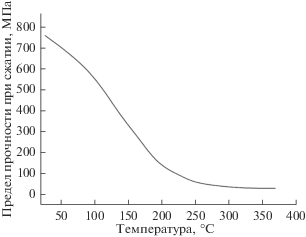
Согласно данным РЭМ полученные наноструктурные композиты обладают сложной иерархической структурой – наноразмерные кристаллиты (50–60 нм) объединены в прочные высокоплотные агломераты (5–10 мкм), которые в свою очередь составляют агрегаты размером порядка 50–150 мкм (рис. 7). При измерении твердости и модуля упругости испытание проводится в масштабах одного агломерата – высокоплотного и прочного образования, в то время как при испытании на сжатие, свойства образца дифференциальны: они охватывают как свойства самих кристаллитов, агрегатов и агломератов, так и границ, пор, включений и других дефектов между ними. Тем не менее, по сравнению с матричным сплавом АМг6 полученные наноструктурные композиционные материалы обладают большей термостойкостью, т.е. демонстрируют меньшее снижение предела прочности/твердости/модуля упругости при увеличении температуры на 1°С, что характеризует их как материалы, потенциально пригодные для эксплуатации при температурах 25–200°С. Сам по себе сплав АМг6 не является жаропрочным, однако его наноструктурирование и модифицирование УНС позволили улучшить его физико-механические свойства и повысить термическую стабильность. В дальнейшем подобный подход может быть применен к системам жаропрочных сплавов типа Д19, АК6, АК8, АК4-1, Д20, 1201 и так далее.
ЗАКЛЮЧЕНИЕ
По сравнению с исходным сплавом АМг6 наноструктурные композиционные материалы на его основе обладают лучшими механическими свойствами при повышенных температурах. Отсутствует сильная анизотропия твердости и модуля упругости (вдоль и поперек оси экструзии), характерная для традиционных материалов после аналогичной обработки. При нагревании композита выше 300°С происходят необратимые структурно-фазовые превращения, в результате которых его механические свойства резко снижаются. Наноструктурирование в совокупности с модифицированием УНС может быть рассмотрено как один из способов увеличения термической стабильности композитов на основе алюминия и других металлов. Увеличение термической стабильности может быть объяснено тем, что УНС, располагаясь по границам кристаллитов, замедляют или полностью исключают диффузионные процессы, связанные с массопереносом при рекристаллизации матричного сплава при повышенных температурах.
Список литературы
Metal Matrix Composites. Soviet Advanced Composites Technology Series (V. 3) / Ed. Fridlyander J.N. Dordrecht: Springer, 1994. 704 p.
Casati R., Vedani M. // Metals. 2014. V. 4. P. 65.
Thostenson E.T., Ren Z.F., Chou T.W. // Compos. Sci. Technol. 2001. V. 61. P. 1899.
Murashkin M.Yu., Kil’mametov A.R., Valiev R.Z. // Phys. Metals Metallogr. 2008. V. 106. № 1. P. 90.
Borgonovo C., Apelian D. // Mater. Sci. Forum. 2011. V. 678. P. 1.
Popov M., Medvedev V., Blank V. et al. // J. Appl. Phys. 2010. V. 108. № 9. P. 094 317.
Evdokimov I.A., Perfilov S.A., Pozdnyakov A.A. et al. // Inorg. Mater.: Appl. Res. 2018. V. 9. № 3. P. 472.
Каблов Е.Н. // Все материалы. Энциклопедический справ. 2008. № 3. С. 2.
Maslenikov I., Useinov A., Birykov A., Reshetov V. // IOP Conf. Ser.: Mater. Sci. Eng. 2017. V. 256. P. 012 003. https://doi.org/10.1088/1757-899X/256/1/012003
Gladkikh E.V., Kravchuk K.S., Useinov A.S. et al. // IOP Conf. Ser.: Mater. Sci. Eng. 2018. V. 443. P. 012 007.
ГОСТ Р 8.748-2011 (ИСО 14577-1:2002) ГСИ. Металлы и сплавы. Измерение твердости и других характеристик материалов при инструментальном индентировании. Ч. 1. Метод испытаний.
Дополнительные материалы отсутствуют.
Инструменты
Поверхность. Рентгеновские, синхротронные и нейтронные исследования