Поверхность. Рентгеновские, синхротронные и нейтронные исследования, 2020, № 8, стр. 102-107
Портативный прибор для измерения твердости методом инструментального индентирования
Е. В. Гладких a, b, *, И. И. Маслеников b, В. Н. Решетов c, А. С. Усеинов b
a Московский физико-технический институт
141701 Московская область, Долгопрудный, Россия
b Технологический институт сверхтвердых и новых углеродных материалов
108840 Москва, Троицк, Россия
c Национальный исследовательский ядерный университет “МИФИ”
115409 Москва, Россия
* E-mail: ekat.gladkih@yandex.ru
Поступила в редакцию 15.10.2019
После доработки 25.12.2019
Принята к публикации 27.12.2019
Аннотация
Описан прибор, способный осуществлять измерение твердости материалов методом инструментального индентирования в условиях промышленного производства, а также контроль трубопроводов, мостов, железнодорожного полотна, судовых механизмов и других изделий, эксплуатируемых на открытом воздухе. Ключевыми составными частями прибора являются: элемент, прикладывающий нагрузку (электромагнитный актюатор), измеритель перемещения (дифференциальный емкостной датчик, установленный на рабочем штоке) и индентор (алмазный наконечник типа пирамиды Берковича с диаметром основания 800 мкм и радиусом острия 100 нм). Максимальное усилие, которое может быть приложено к образцу, составляет 10 Н, а максимальное перемещение индентора при индентировании достигает 150 мкм. Для удобства измерения массивных и тонких образцов конструкция портативного твердомера предусматривает две различные насадки. Основной отличительной особенностью прибора является измерение твердости и модуля Юнга материала в едином рабочем цикле. Проведены испытания прибора на различных материалах: сталях марок 40Х13 и 08Х18Н10Т (в том числе на образцах, прошедших процедуру старения), алюминии, плавленом кварце, поликарбонате, ламинированных древесных панелях. Определены требования к уровню шероховатости тестируемых поверхностей и диапазону нагрузок при осуществлении инструментального индентирования портативным прибором. Значения твердости и модуля упругости хорошо совпадают с данными, полученными с помощью лабораторных твердомеров.
ВВЕДЕНИЕ
Производственная деятельность ставит перед материаловедами сложные задачи, требуя создания конструкционных материалов с уникальными свойствами [1]. Разработка технологий, направленных на улучшение функциональных характеристик механизмов и конструкций, тесно связана с механическими свойствами используемых материалов. Например, если необходимо уменьшить массу какого-либо конструктивного элемента, сохраняя жесткость изделия, необходим материал с высокой прочностью и большим модулем Юнга. Для большинства конструкционных материалов на основе различных сплавов существует однозначная взаимосвязь между твердостью и прочностью материала [2, 3]. Благодаря этой взаимосвязи очень часто разрушающие испытания на прочность можно заменить неразрушающими испытаниями на твердость.
Развитие материаловедения привело к появлению твердых, прочных и легких материалов. Однако свойства таких материалов часто сильно зависят от технологии их обработки и могут заметно варьироваться от партии к партии [4, 5]. Чтобы отличить хороший материал от плохого, приходится исследовать его механические свойства. Самый простой и надежный способ – измерение свойств с помощью специального оборудования в лабораторных условиях [6]. Однако это не всегда удобно в условиях промышленного производства и просто неосуществимо при работе с оборудованием и механизмами, находящимися в непрерывной эксплуатации. Яркими примерами такого рода изделий являются элементы конструкций АЭС, ТЭС, ГЭС, корабли, самолеты, трубопроводы и мосты.
Механические свойства металлов и сплавов, а также других твердых материалов можно исследовать различными методами, например, методом микроиндентирования [7, 8]. Он основан на вдавливании наконечника известной формы в материал и дальнейшем определении размеров остаточного отпечатка. Такой процесс требует применения специальных устройств, поскольку невозможно вручную приложить нагрузку к наконечнику с требуемой точностью [9].
Первые твердомеры имели только наконечник с актюатором [10]. Значения твердости рассчитывали путем деления приложенной нагрузки на площадь отпечатка, определяемой по оптическому изображению. Современные модели твердомеров оснащены не только микроскопами, но и атомно-силовыми микроскопами для измерения геометрии гораздо меньших отпечатков [11]. Метод, разработанный Оливером и Фарром, исключил необходимость получения изображения отпечатка. Вместо этого было предложено анализировать кривую нагрузки–разгружения [12].
Перед современными разработчиками испытательного оборудования, предназначенного для работы на производствах, стоят задачи ускорения и упрощения процедуры измерения, а также повышения надежности и точности измерений. Одним из таких перспективных методов является применение прозрачного индентора [13, 14]. С его помощью становится возможным наблюдать образование различных фаз материала под индентором непосредственно в ходе проведения испытаний [15]. Глобальная цель разработчиков – создание инструмента, способного в автоматическом режиме измерять широкий круг материалов с различными значениями твердости и модуля Юнга. Перефразируя известный принцип ракетчиков “выстрелил и забыл”, можно сказать, что нужен прибор, работающий по принципу “поставил и получил”.
Помимо приборов, предназначенных для измерения свойств материалов в условиях лабораторий, активно развивается оборудование для испытаний в реальных, полевых условиях. В [16] дана классификация различных типов портативных твердомеров. Широко распространены динамические твердомеры, работающие по принципу отскока, а также ультразвуковые или импедансные твердомеры, которые измеряют контактное акустическое сопротивление материала [17]. Полученные с помощью этих устройства данные зависят от массы и жесткости измерительных частей, их пространственного расположения и других факторов, как отмечено в [18]. Измерения с помощью устройств этих типов косвенные: используется соотношение различных механических и физических свойств с твердостью, полученной прямыми методами. Ключевым фактором, влияющим на интерпретацию данных импедансного твердомера, является значение модуля Юнга тестируемого материала. Предполагается, что известен модуль Юнга материала с высокой точностью, его значение берут при обработке первичных данных. Таким образом, приборы не могут быть использованы для измерения твердости материалов с неизвестным модулем Юнга. Данный недостаток отсутствует у приборов, позволяющих измерять твердость и модуль упругости методом инструментального индентирования [19].
Ограничением для применения ультразвуковых твердомеров является невозможность определения твердости неметаллов из-за анизотропии скорости звука в таких материалах [20]. Описываемое в настоящей работе оборудование, основанное на принципах инструментально контролируемого вдавливания, применимо для гораздо более широкого класса материалов.
МЕТОДИКА
Схема устройства
В настоящей работе рассмотрена конструкция портативного твердомера, получившего название iPoRTH, работающего на принципах инструментального индентирования. Его схема приведена на рис. 1. Основные компоненты устройства включают механизм, прикладывающий нагрузку, датчик перемещения и индентор. Элементом приложения силы является электромагнитный актюатор. Датчик перемещения представляет собой емкостной датчик, установленный на рабочем штоке. Прикладываемое к образцу усилие достигает 10 Н, рабочее перемещение индентора составляет 150 мкм. Держатель индентора изготовлен из латуни, рабочий шток – из углепластика, индентор – алмазный наконечник типа пирамиды Берковича с диаметром основания 800 мкм и радиусом острия 100 нм.
Рис. 1.
Схема портативного твердомера с насадками для измерения массивных (а) и тонких (б) образцов: 1 – корпус; 2 – актюатор; 3 – мембраны; 4 – неподвижные емкостные пластины; 5 – подвижная емкостная пластина; 6 – шток; 7 – индентор; 8 – пластина; 9 – винт-ручка.
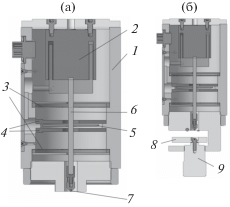
Конструкция портативного твердомера подходит для измерения как массивных, так и тонких образцов благодаря двум различным насадкам (рис. 2). У насадок есть три стальные закаленные шарообразные опоры, к которым прижимается тестируемая поверхность изделия. Измерение небольших и плоских образцов (например, ножей или концевых мер) осуществляется в режиме, когда прижимная пластина рабочей насадки приводит их в плотный контакт с шаровидными опорами.
Процедура измерений
Портативный твердомер iPoRTH предназначен для измерения образцов как в лаборатории, так и в полевых условиях. Чтобы полученные данные правильно отражали механические свойства, необходимо соблюдение ряда условий, характерных для всех методов измерения твердости. Если уровень шероховатости поверхности превосходит 10% ожидаемой глубины индентирования, то поверхность исследуемого образца следует довести до требуемого уровня гладкости с помощью шлифовальной машины или шкурки соответствующей зернистости. В противном случае будет высокая дисперсия полученных значений твердости из-за высокой шероховатости поверхности. Более того, в методе инструментального индентирования, реализованном в данном приборе (как и во всех остальных методах измерения твердости на основе вдавливания острого наконечника) шероховатость поверхности приводит не просто к разбросу измеренных значений твердости, но и смещает оценку, не позволяя получить истинное значение твердости исследуемого материала простым усреднением [21, 22].
Перед началом процедуры испытания оператор должен откалибровать вертикальное местоположение опорных шариков по отношению к острию индентора (опорная головка перемещается вдоль штока путем ее вращения и закрепляется в рабочем положении с помощью контргайки). Наконечник должен быть не ближе, чем на расстоянии 20 мкм от исследуемой поверхности и не дальше, чем на расстоянии 80 мкм от ее. Данную дистанцию определяют “на глаз” и при необходимости контролируют путем вставления щупа в виде полоски обычной писчей бумаги в зазор между индентором и поверхностью. В случае плоских поверхностей эту процедуру осуществляют единовременно при смене рабочей головки и в дальнейшем при реальных измерениях не проводят. При работе с неровными выпуклыми и вогнутыми поверхностями эту процедуру осуществляют в месте измерения.
Необходимо держать прибор прижатым к образцу в течение всего цикла измерения. Усилие прижима должно быть не менее 30 и не более 60 Н. Время процедуры зависит от максимальной нагрузки и в среднем занимает около 1 мин. Угол между перпендикуляром к поверхности образца и линией приложения силы должен быть менее 10°. После завершения вдавливания оператор может переместить прибор на расстояние приблизительно 1 мм от последнего места вдавливания для проведения другого теста.
Базовые принципы метода инструментального индентирования согласно ГОСТ Р 8.748-2011 [23]
Основными измеряемыми параметрами на кривой нагрузка–разгрузка являются твердость Н и наклон кривой разгрузки S:
Оба эти параметра рассчитывают исходя из данных предварительной калибровки формы алмазного индентора, когда снимают зависимость контакной площади от глубины погружения индентора в тестируемый материал ${{A}_{{\text{c}}}}\left( h \right).$ Это стандартная процедура, и она основана на серии испытаний образца с известными свойствами различной нагрузкой. Кривая нагрузки–разгружения, полученная на образце плавленого кварца с максимальной нагрузкой 1 Н, показана на рис. 3. Площадь контактируещего с материалом участка индентора для идеальной пирамиды Берковича зависит квадратично от глубины проникновения индентора:
где ${{h}_{{\text{c}}}}$ и ${{h}_{{{\text{max}}}}}$ – контактная и максимальная глубины индентирования, вычисляемые в соответствии с [19]. Все вычисления выполняются автоматически после измерения с использованием встроенной электроники.РЕЗУЛЬТАТЫ И ИХ ОБСУЖДЕНИЕ
Были исследованы образцы различных типов: плавленый кварц, поликарбонат и сплавы (сталь и алюминий). На рис. 4 представлены полученные в экспериментах кривые нагрузки–разгружения. В табл. 1 приведены значения твердости, полученные с помощью разработанного портативного твердомера и лабораторного прибора (NanoScan-4D, созданного ФГБНУ ТИСНУМ).
Рис. 4.
Кривые нагрузки (сплошные линии) и разгрузки (штриховые линии), полученные для плавленого кварца (1), стали 40Х13 (2), алюминия (3), поликарбоната (4), ДСП с покрытием (5).
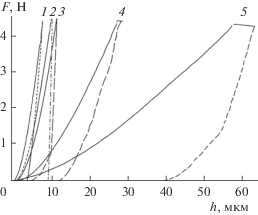
Таблица 1.
Твердость образцов, измеренная переносными и обычными твердомерами
Материал | Твердость, измеренная портативным прибором H, ГПа | Твердость, измеренная лабораторным прибором H, ГПа |
---|---|---|
Стекло | 8.5 ± 0.8 | 9.1 ± 0.2 |
Сталь 40X13 | 1.5 ± 0.3 | 1.6 ± 0.4 |
Сталь 08Х18Н10Т, вблизи сварного шва | 2.6 ± 0.1 | 2.5 ± 0.3 |
Сталь 08Х18Н10Т, основной металл | 3.4 ± 0.4 | 3.2 ± 0.1 |
Сталь 08Х18Н10Т, после старения при 525°C, длительность 2650 ч | 2.4 ± 0.6 | 2.5 ± 0.3 |
Сталь 08Х18Н10Т, после старения при 450°C, длительность 12345 ч | 2.3 ± 0.1 | 2.4 ± 0.2 |
Нож из стали 8Cr13 | 4.7 ± 0.6 | 4.2 ± 0.3 |
Алюминий | 2.5 ± 0.6 | 2.3 ± 0.3 |
Поликарбонат | 0.21 ± 0.01 | 0.21 ± 0.02 |
ДСП с покрытием | 0.5 ± 0.2 | 0.4 ± 0.1 |
Значения модуля упругости конструкционных материалов обычно известны. Однако в случае использования разработанного прибора эта информация не является необходимой для расчета твердости. Модуль Юнга измеряют методом инструментального индентирования с существенно меньшей точностью, чем твердость, и часто эта информация носит служебный характер, особенно в случае металлов и их сплавов, у которых отношение H/E много меньше единицы. Полученные данные о модуле Юнга хорошо согласуются с табличными характеристиками соответствующих материалов.
Как следует из полученных данных, прибор iPoRTH успешно демонстрирует возможность измерения твердости изделий без априорной информации о модуле Юнга материла. В представленных результатах модуль Юнга различных образцов отличался почти на два порядка, как и измеренные значения твердости. Метод инструментального индентирования, описанный в [19, 23], применим также и в случае циклического укола с частичной разгрузкой индентора после каждого нагружения: описанные в указанных стандартах зависимости могут быть применены для каждого цикла, что, соответственно, позволяет получить зависимость измеряемых значений твердости и модуля упругости от глубины. Таким образом, появляется возможность контроля эффектов, связанных с поверхностным упрочнением и умягчением материалов ходе их технологической обработки. Доступный уровень нагружения 10 Н позволяет осуществлять контроль подобных эффектов для глубин от 1.5 до 15 мкм в большинстве конструкционных сталей.
ЗАКЛЮЧЕНИЕ
Представленный в работе портативный твердомер iPoRTH, работающий по принципу статического вдавливания индентора в полном соответствии с методом инструментального индентирования (ГОСТ Р 8.748-2011), позволяет получать значения твердости прямым методом без использования оптических средств наблюдения. Проведенные исследования продемонстрировали возможность использования данного прибора для диагностики механических свойств различных конструкционных материалов, используемых в промышленности. Измеренные значения твердости совпадают со значениями, полученными на лабораторном твердомере с учетом свойственной данному оборудованию погрешности. Величины твердости и модуля упругости были вычислены непосредственно из зависимостей нагрузка–углубление: измерение твердости методом инструментального индентирования в отличие от ультразвуковых методов не требует априорной информации о модуле упругости. Соответствующие значения модуля упругости исследованных материалов близки к характеристикам, указанным в общедоступных источниках.
Следующим этапом разработки портативного твердомера является встраивание модуля Bluetooth для отправки данных на портативный компьютер или телефон для сохранения всей необходимой информации и сырых данных, включая координаты места, где проводилось измерение. Это полезно для диагностики трубопроводов, железнодорожного полотна и сложных конструкций. Полученные результаты подтверждают возможность объективного контроля такой важной механической характеристики, как твердость материала, в промышленном производстве и в полевых условиях с помощью портативного прибора массой не более 1 кг.
Список литературы
Zinkle S.J., Was G.S. // Acta Mater. 2013. V. 61. № 3. P. 735. https://doi.org/10.1016/j.actamat.2012.11.004
Zhang P., Li S.X., Zhang Z.F. // Mater. Sci. Eng. A. 2011. V. 529. P. 62. https://doi.org/10.1016/j.msea.2011.08.061
Brooks I., Lin P., Palumbo G. et al. // Mater. Sci. Eng. A. 2008. V. 491. № 1–2. P. 412. https://doi.org/10.1016/j.msea.2008.02.015
Макаренко К.В., Зенцова Е.А. // Металловедение и термическая обработка металлов. 2018. № 7. С. 3. https://doi.org/10.1007/s11041-018-0293-3
Susanti O., Mochtar M.A., Harjanto S. // Mater. Res. Express. 2017. V. 4. № 3. https://doi.org/10.1088/2053-1591/aa6314
Pantano M.F., Espinosa H.D., Pagnotta L. // J. Mech. Sci. Technol. 2012. V. 26. № 2. P. 545. https://doi.org/10.1007/s12206-011-1214-1
Broitman E. // Tribol. Lett. 2017. V. 65. № 1. https://doi.org/10.1007/s11249-016-0805-5
Koeppel B.J., Subhash G. // Wear. 1999. V. 224. № 1. P. 56. https://doi.org/10.1016/S0043-1648(98)00328-7
Oberg H., Larsson P.L., Magnius O. // J. Test. Eval. 2001. V. 29. № 1. P. 50.
Усеинов А., Кравчук К., Русаков А. и др. // Наноиндустрия. 2016. №. 7. С. 72.
Petzold M., Landgraf J., Füting M., Olaf J.M. // Thin Solid Films. 1995. V. 264. № 2. P. 153. https://doi.org/10.1016/0040-6090(95)05855-9
Oliver W.C., Pharr G.M. // J. Mater. Res. 1992. V. 7. № 6. P. 1564.
Feng C., Kang B.S. // Exp. Mech. 2006. V. 46. № 1. P. 91. https://doi.org/10.1007/s11340-006-5862-5
Маслеников И.И., Решетов В.Н., Усеинов А.С., Доронин М.А. // Приборы и техника эксперимента. 2018. № 5. С. 96. https://doi.org/10.1134/S002044121804022X
Maslenikov I.I., Reshetov V.N., Useinov A.S. // Mater. Transac. 2019. V. 60. № 8. P. 1433. https://doi.org/10.2320/matertrans.md201902
Matyunin V.M., Karimbekov M.A., Marchenkov A.Y., Demidov A.N. // Russ. Metallurgy (Metally). 2016. V. 2016. № 13. P. 1325. https://doi.org/10.1134/S0036029516130115
Fu J., Li F. // Rev. Sci. Instrum. 2015. V. 86. № 10. P. 103 902. https://doi.org/10.1063/1.4932186
Худяков С.А., Струтынский А.В. // Вестн. Морского гос. ун-та. Сер. Судостроение и судоремонт. 2007. Вып. 17. С. 84.
BS EN ISO 14577: 2015. Metallic Materials. Instrumented Indentation Test for Hardness and Materials Parameters.
Yang J., Shahid M., Wan C. et al. // J. Eur. Ceram. Soc. 2017. V. 37. № 2. P. 689. https://doi.org/10.1016/j.jeurceramsoc.2016.08.034
Маслеников И.И., Усеинов А.С., Кравчук К.C., Косцова А.А., Решетов В.Н. // Физика твердого тела. 2018. V. 60. № 11. P. 2259. https://doi.org/10.1134/S1063783418110203
Kim J.-Y. et al. // J. Mater. Res. 2006. V. 21. № 12. P. 2975. https://doi.org/10.1557/jmr.2006.0370
ГОСТ Р 8.748-2011 (ИСО 14577-1:2002) ГСИ. Металлы и сплавы. Измерение твердости и других характеристик материалов при инструментальном индентировании. Ч. 1. Метод испытаний.
Дополнительные материалы отсутствуют.
Инструменты
Поверхность. Рентгеновские, синхротронные и нейтронные исследования