Поверхность. Рентгеновские, синхротронные и нейтронные исследования, 2020, № 8, стр. 86-96
Изучение изменения поверхности алюминиевых сплавов в процессе трения методами микроскопии и рентгеновского анализа
О. О. Щербакова a, *, Т. И. Муравьёва a, **, И. В. Шкалей a, Д. Л. Загорский a, b, И. Ю. Цуканов a
a Институт проблем механики им. А.Ю. Ишлинского РАН
119526 Москва, Россия
b Российский государственный университет нефти и газа им И.М. Губкина
119991 Москва, Россия
* E-mail: shcherbakovaoo@mail.ru
** E-mail: muravyeva@list.ru
Поступила в редакцию 14.12.2019
После доработки 15.01.2020
Принята к публикации 18.01.2020
Аннотация
В работе оценивалось влияние введения добавок легкоплавких легирующих элементов в антифрикционные алюминиевые сплавы на изменение поверхности после трибологических испытаний. Описаны составы и проведена подготовка образцов. Для исследования применялась комбинация методов электронной микроскопии (с элементным анализом), а также зондовой микроскопии (с модами токов растекания и анализа теплопроводности). Показано, что после термообработки в обоих сплавах фазовые составляющие приобретают глобулярную форму. В процессе трения происходит деформация зерен, выделение мягкой фазы на поверхность и массоперенос. Твердые фазовые составляющие материала колодки выступают в качестве абразива, в то время как на ролике массоперенос приводит к формированию пленки вторичных структур переменной толщины (при определенных условиях она утолщается, что может привести к образованию задира). Анализ срезов позволил установить наличие приповерхностного слоя (толщиной 50–100 мкм) с измененной структурой. Методом СЗМ установлено, что карта теплопроводности на микроуровне коррелирует с картой электропроводности. Был проведен рентгеноструктурный анализ поверхностей до и после трибоиспытаний, который показал, что период решетки уменьшается, ее деформация увеличивается и появляется текстура.
ВВЕДЕНИЕ
Тенденцией последних лет в машиностроении является замена дорогостоящих бронз алюминиевыми сплавами. Такая замена целесообразна в ряде направлений использования, в частности, при разработке подшипниковых узлов [1, 2]. При этом сохранение и улучшение высоких эксплуатационных свойств является актуальной задачей [3–5]. Эта задача может быть решена, в частности, за счет научно обоснованного выбора сплава (основы и легирующих элементов). Сплавы на основе алюминия отвечают основным требованиям, обладая при этом сопоставимыми с бронзами антифрикционными характеристиками. В работах [6–8] показано, что в качестве антифрикционных материалов для подшипниковых узлов одними из оптимальных считаются сплавы системы Al–5% Si–4% Cu–6% Sn. Известно также, что изменение количества составляющих элементов и/или добавки других металлов (например, легкоплавких) может влиять на структуру и свойства сплавов данной системы.
Для оценки эффективности различных составов проводятся исследования эксплуатационных характеристик – в первую очередь это трибологические испытания [8, 9]. При проведении последних оцениваются не только сами трибологические свойства, но и исследуются изменения, происходящие на контактных поверхностях и в приповерхностных слоях при трении. Эти исследования проводятся комплексом различных методов, прежде всего, микроскопических и дифракционных.
Наиболее эффективны здесь комбинированные исследования, проводимые различными, взаимодополняющими методами. Так, проводятся электронномикроскопические исследования (СЭМ) поверхностей не только во вторичных, но и в обратно отраженных электронах, что значительно повышает возможности исследования, и это позволяет точнее изучать морфологию поверхности и визуализировать ее фазовый состав. Важнейшей особенностью современных исследований является одновременное проведение элементного (рентгеноспектрального) анализа. Метод СЭМ используется и для оценки состояния приповерхностных слоев на срезах образцов.
Ценность исследований на сканирующем зондовом микроскопе (СЗМ) заключается как в получении топографических изображений поверхности, дополняющих СЭМ – исследования поверхности [10], так и в возможности использования дополнительных мод. Среди множества последних можно отметить измерение латеральных сил (напрямую связанных с фрикционными свойствами), поверхностных тепло- и электропроводности.
Рентгеноструктурный анализ, один из самых широко распространенных методов исследования, к сожалению, почти не применяется в исследованиях изменений на поверхностях трения. Проведение таких исследований может дать информацию о параметре решетки поверхностных слоев материала, о деформации этой решетки и о наличии и изменении текстуры.
Целью настоящей работы было изучение изменений поверхности новых антифрикционных алюминиевых сплавов, происходящих в процессе трения, с применением комплекса вышеупомянутых методов.
МАТЕРИАЛЫ И МЕТОДЫ ИССЛЕДОВАНИЯ
Образцы
В работе изучались образцы двух экономно легированных сплавов на основе системы Al–5% Si–4% Cu–4% Sn. Известно, что состав сплава определяется рядом факторов. Сплав должен обладать достаточной твердостью и хорошей формозаполняемостью (высокими литейными свойствами), что и обеспечивает композиция Al–5% Si–4% Cu [11]. Также сплав должен содержать достаточное количество легкоплавких элементов, что важно для уменьшения трения и обеспечения сопротивления задиру при сухом трении или в условиях смазки. Известно, что в экстремальных условиях трения на контактной поверхности происходит выделение этих элементов, которые защищают поверхность, выполняя функцию твердой смазки [12, 13]. Ранее проведенные исследования показали, что добавка Bi в сплав-основу увеличивает заполняемость формы, а добавка Cd повышает прочность и твердость сплава [11]. На основе этого были предложены два сплава, расчетный химический состав которых приведен в табл. 1.
Таблица 1.
Химический состав исследуемых сплавов
Номер сплава | Содержание компонента, % | ||||||
---|---|---|---|---|---|---|---|
Al | Si | Cu | Sn | Bi | Pb | Cd | |
1 | Основа | 5 | 4 | 4 | 0.5 | 0.5 | 0.5 |
2 | 5 | 4 | 4 | 0.5 | 0.5 | – |
Образцы подвергались термообработке, которая заключалась в нагреве до 500°С с последующей закалкой в воду и старением. Данный режим термообработки был ранее подобран для сплавов сходного состава в работе [11].
Подготовка образцов
Для изучения топографии и элементного состава исходной поверхности литых и термообработанных сплавов были приготовлены шлифы. Это делалось с использованием шлифовально-полировального комплекса “TegraPol-25” и “TegraForce-5” (“Struers”, Дания). Для исследования приповерхностных слоев после испытаний на программируемом отрезном станке “Accutom-5” (“Struers”, Дания) были изготовлены торцевые срезы образцов, которые также шлифовали и полировали.
Трибологические испытания
Трибологические испытания сплавов проводили на трибометре Т-05 по схеме колодка (из исследуемого материала) – ролик (контртело из стали Ст45), с пошаговым изменением нагрузки. Данная контактная пара исследовалась по ранее отработанной методике [8]. Исследования проводились при давлениях 0.5 МПа и 1 Мпа, без смазки. Отметим, что данные режимы позволяют ускорить эксперимент (проводить экспресс-испытания), при давлении 1МПа для данных сплавов моделируются условия близкие к экстремальным.
Для рентгеноструктурных исследований были проведены специальные трибологические испытания на трибометре UMT-3 по схеме “пальчик–плоскость” с возвратно-поступательным движением. Пальчик представлял собой торец цилиндра диаметром 6 мм из исследуемых сплавов, плоскость – контртело в виде пластины размером 20 × 40 × 10 мм из стали марки Ст45. Испытания проводились с постоянной нагрузкой на пальчик 5 Н, скорость перемещения составляла 5 мм/с, длина хода – 15 мм.
Микроскопические исследования
В работе применялась комплексная методика микроскопических исследований.
Электронная микроскопия
Электронно-микроскопические исследования проводили на сканирующем электронном микроскопе Quanta-650 (комп. “FEI”) с аналитическим оборудованием EDAX (включающем рентгеноспектральный микроанализатор EDS и дифракционную камеру EBSD). Использовались одновременно два режима вторичных и обратно отраженных электронов с ускоряющим напряжением до 25 кВ. Исследовались образцы до и после термообработки, а также до и после трибологических испытаний.
Зондовая микроскопия
Исследования на наноуровне проводились с использованием различных методов зондовой микроскопии. Исследование электрических и теплопроводящих свойств поверхности сплавов проводилось в НТ-МДТ (Зеленоград) на приборе Нтегра Прима (НТ-МДТ). Применялись кантилеверы с жесткостью 50 Н/м. При этом предварительное измерение рельефа поверхности осуществлялось в контактном и полуконтактном режиме. Проводилось измерение карты тока поверхностного растекания и теплопроводности образцов.
При измерении тока растекания между поверхностью образца и зондом подавалось постоянное напряжение до 10 В и для различных точек поверхности измерялся протекающий ток. Теплопроводность оценивалась с помощью приставки сканирующей тепловой микроскопии (СТМ) с использованием специального зонда, к концу которого, представляющего собой сопротивление, прикладывалось напряжение заданной величины. Температура зонда измерялась по изменению его сопротивления, встроенного в плечо моста Уинстона. Для определения теплопроводности поверхности зонд сначала нагревался до определенной температуры, которая при взаимодействии с поверхностью изменялась. В условиях достаточно медленного сканирования, когда можно пренебречь переходными процессами, температура зонда изменялась обратно пропорционально теплопроводности материала в области его контакта с поверхностью. Таким образом, регистрируемая при этом разница температур давала информацию о теплопроводящих свойствах образцов.
Рентгеноструктурный анализ
Рентгеноструктурные исследования поверхности образцов до и после трибоиспытаний проводились на рентгеновском дифрактометре Rigaku Ultima IV. Анализ дифрактограмм осуществляется на основе программного продукта PDXL (Rigaku) с использованием базы данных PDF-2. Количественный анализ проводится с использованием метода Ритвельда, реализованного в пакете программ PDXL (Rigaku). Дифрактограммы снимались в симметричном режиме, диапазон сканирования составлял от 20 до 170, “шаг 0.05°”, скорость детектора 3°/мин.
РЕЗУЛЬТАТЫ И ИХ ОБСУЖДЕНИЕ
Влияние термообработки
Для обоих образцов была исследована структура исходной поверхности образцов и ее изменение в результате термообработки. На рис. 1 показаны поверхности сплавов № 1 и № 2 (полученные методом СЭМ в литом состоянии и после термообработки). В табл. 2 приведен химический состав выделенных исследуемых областей.
Рис. 1.
СЭМ-изображения (во вторичных электронах) исходной поверхности сплавов: а – № 1 в литом состоянии; б – № 1 в термообработанном состоянии; в – № 2 в литом состоянии; г – № 2 в термообработанном состоянии.
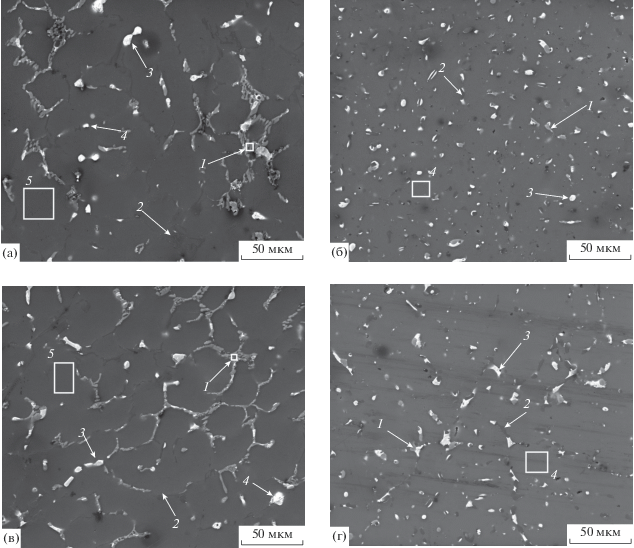
Таблица 2.
Химический состав поверхностей сплавов № 1 и № 2 в литом и термообработанном состоянии
№ образца | № исследуемого участка | Установленный химический состав, масс. % | ||||||
---|---|---|---|---|---|---|---|---|
Al | Si | Sn | Cu | Pb | Bi | Cd | ||
№ 1 Литой |
1 (Al2Cu) | 44.07 | 1.46 | 3.52 | 49.01 | 0.90 | 0.70 | 0.34 |
2 (Al-Si) | 45.62 | 51.28 | 0.67 | 1.39 | 0.45 | 0.36 | 0.23 | |
3 (Мягкая фаза) | 1.86 | 0.03 | 89.05 | 1.38 | 1.95 | 1.89 | 3.84 | |
4 (Мягкая фаза) | 5.44 | – | 27.72 | 0.17 | 9.78 | 53.65 | 3.24 | |
5 (Матрица) | 96.39 | 1.41 | 0.01 | 1.09 | 0.41 | 0.25 | 0.44 | |
All area | 90.58 | 2.83 | 1.88 | 3.67 | 0.59 | 0.33 | 0.12 | |
№ 1 Термообработанный |
1 (Al2Cu) | 42.32 | 1.37 | 1.10 | 53.93 | 0.58 | 0.60 | 0.10 |
2 (Al-Si) | 33.90 | 57.87 | 5.47 | 1.44 | 0.75 | 0.40 | 0.17 | |
3 (Мягкая фаза) | 6.79 | 1.69 | 84.89 | 1.53 | 1.19 | 2.87 | 1.04 | |
4 (Матрица) | 93.64 | 1.24 | 0.05 | 3.81 | 0.55 | 0.55 | 0.16 | |
All area | 89.05 | 4.51 | 1.38 | 4.07 | 0.48 | 0.41 | 0.10 | |
№ 2 Литой |
1 (Al2Cu) | 51.58 | 1.36 | 3.78 | 42.31 | 0.54 | 0.43 | – |
2 (Al-Si) | 57.00 | 39.08 | 1.16 | 1.84 | 0.49 | 0.43 | – | |
3 (Мягкая фаза) | 2.84 | 0.00 | 88.98 | 0.77 | 2.67 | 4.74 | – | |
4 (Мягкая фаза) | 2.38 | 0.00 | 58.12 | 0.02 | 20.83 | 18.65 | – | |
5 (Матрица) | 97.60 | 0.62 | 0.02 | 1.19 | 0.30 | 0.27 | – | |
All area | 88.54 | 3.63 | 2.71 | 3.95 | 0.52 | 0.65 | – | |
№ 2 Термообработанный |
1 (Al2Cu) | 42.66 | 0.16 | 2.00 | 53.91 | 0.88 | 0.39 | – |
2 (Al-Si) | 30.01 | 60.61 | 6.74 | 1.47 | 0.62 | 0.55 | – | |
3 (Мягкая фаза) | 4.46 | – | 82.65 | 2.87 | 1.03 | 8.99 | – | |
4 (Матрица) | 94.85 | 0.27 | 0.01 | 4.05 | 0.41 | 0.41 | – | |
All area | 87.23 | 4.80 | 3.12 | 4.30 | 0.29 | 0.26 | – |
Анализ СЭМ изображений и табл. 2 показывает, что несмотря на некоторое различие состава (сплав № 1 содержит в своем составе Сd) оба сплава близки по структуре и содержат в своем составе сходные фазы. Ранее, для сплавов сходного состава было показано, что термообработка приводит к сфероидизации отдельных фаз и к значительному растворению меди в алюминиевой матрице [10, 14, 15]. В настоящей работе показано, что термообработка приводит к аналогичным изменениям. Так, после термообработки удлиненные фазовые составляющие сплава – кремниевые и легкоплавкие фазы, принявшие более компактную округлую форму.
Зондовая микроскопия
Для обоих образцов применялись новые методы изучения свойств поверхности, включающие комбинацию исследования топографии поверхности и изучения поверхности дополнительными модами зондовой микроскопии. С помощью дополнительных мод СЗМ были проведены измерения карты тока поверхностного растекания и теплопроводности образцов. Отметим, что при этом электропроводность и теплопроводность были измерены независимо. На рис. 2 представлены полученные изображения образца № 2 в литом и термообработанном состоянии – приведены изображения рельефа и карты температуры.
Рис. 2.
СЗМ-изображения топографии образца № 2: а – топография литого образца; б – карта отклонения температуры зонда от номинального значения литого образца; в – топография термообработанного образца; г – карта отклонения температуры зонда от номинального термообработанного образца.
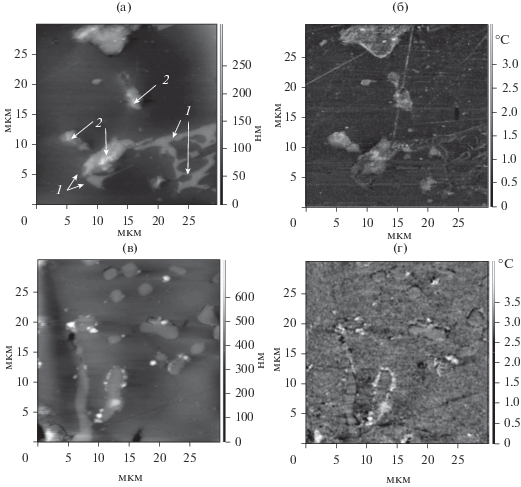
Более высокая температура зонда соответствует более светлым областям на изображении и качественно свидетельствует об их меньшей теплопроводности. На рис. 2а, 2б можно выделить участки рельефа (фаза 1), на которых температура зонда фактически такая же, как и матрицы (твердые фазовые включения – Al2Cu или Al–Si), т.е. их теплопроводности одинаковы. На участках, обозначенных цифрой 2 (мягкая фазовая составляющая Sn–Pb–Bi), зонд имеет наибольшую температуру, т.е. в этих местах имеется наибольшее тепловое сопротивление при теплообмене. На остальных участках температура зонда имеет промежуточное значение, но выше, чем температура матрицы.
На термообработанном образце распределение температуры зонда имеет более однородный характер (рис. 2г): более высокая температура, соответствующая меньшей теплопроводности, наблюдается только на примесях, локализованных в основном на границах фазы – Al–Si, включения которой имеют овальную форму. Теплопроводность фазы Al–Si не сильно отличается от теплопроводности матрицы. Другая фаза Al2Cu не наблюдается именно на данном исследуемом участке, поскольку при термообработке медь значительно растворяется в Al-матрице. Из полученных результатов можно сделать вывод, что значения теплопроводности у термообработанных образцов несколько ниже, чем у литых. Это связано с растворением некоторого количества фазовых составляющих в алюминии.
Сопоставление карт теплопроводности и поверхностной проводимости образца № 2 в литом состоянии представлено на рис. 3. Один и тот же участок был просканирован вначале в режиме тепловой микроскопии, а затем в режиме поверхностной проводимости (измерение тока).
Рис. 3.
СЗМ-изображения поверхности литого образца № 2: а – топография (17 × 17 мкм); б – карта отклонения температуры зонда от номинального значения (17 × 17 мкм); в – карта распределения тока растекания (18 × 18 мкм).
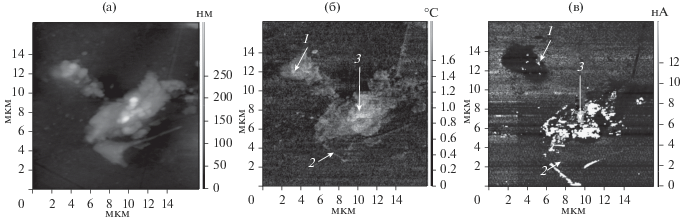
Сопоставление рис. 3б и 3в показывает, что полного соответствия между теплопроводностью поверхности и ее электрической проводимостью нет. Причин этого может быть несколько: наличие областей, покрытых непроводящим окислом, изменение площади контакта между зондом и поверхностью в различных точках рельефа поверхности, отличие фазового состава в различных областях. Однако в большинстве случаев для измеренных образцов корреляция между электропроводностью и теплопроводностью существует, что качественно согласуется с законом Видемана–Франца для металлов. Такой вывод дает возможность при оценке тепловых характеристик поверхности заменить трудоемкую операцию получения карты отклонения темепратуры зонда на простую операцию определения токов растекания.
СЭМ-исследования влияния трибологических испытаний на структуру поверхности
При испытаниях на износ было установлено, что у обоих сплавов наблюдается задир при давлении 1.0 МПа. Результаты исследований показали, что сплав № 2 обладает более высокой изностойкостью. На рис. 4 в качестве примера приведены СЭМ-изображения поверхностей контактных пар (колодок и роликов) сплавов № 1 и № 2 после трибоиспытаний при максимальном давлении 1.0 МПа. В табл. 3 и 4, соответственно, приведен элементный состав для колодок и роликов при давлениях 0.5 и 1.0 МПа.
Рис. 4.
СЭМ-изображение (в обратно отраженных электронах) контактной пары колодка – ролик после трибологических испытаний при давлении 1 МПа: а – поверхность колодки из сплава № 1; б – поверхность ролика после испытания сплава № 1; в – поверхность колодки из сплава № 2; г – поверхность ролика после испытания сплава № 2.
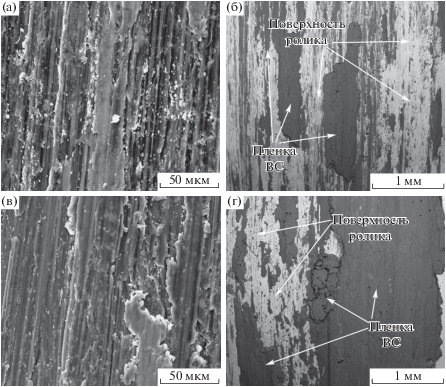
Таблица 3.
Химический состав поверхностей колодок после испытаний из сплавов № 1 и № 2
Давление | Колодка из сплава | Содержание элементов, масc. % | ||||||||
---|---|---|---|---|---|---|---|---|---|---|
O | Al | Si | Cu | Sn | Fe | Pb | Bi | Cd | ||
0.5 МПа | № 1 | 0.6 | 85.5 | 6.9 | 3.4 | 2.7 | 0.2 | 0.3 | 0.1 | 0.3 |
№ 2 | 16.8 | 65.6 | 4.8 | 3.1 | 2.6 | 6.5 | 0.4 | 0.2 | – | |
1.0 МПа | № 1 | 15.3 | 72.5 | 5.7 | 2.7 | 2.4 | 0.2 | 0.6 | 0.2 | 0.4 |
№ 2 | 11.3 | 75.9 | 6.5 | 2.9 | 2.6 | 0.2 | 0.4 | 0.2 | – |
Таблица 4.
Химический состав поверхностей роликов после испытаний сплавов № 1 и № 2
Давление | Ролик (контактная пара) | Содержание элементов, маcс. % | |||||||||
---|---|---|---|---|---|---|---|---|---|---|---|
O | Al | Si | Cd | Sn | Cr | Fe | Cu | Pb | Bi | ||
0.5 МПа | № 1 | 2.9 | 44.6 | 1.4 | 0.1 | 0.9 | 0.9 | 47.4 | 1.1 | 0.4 | 0.3 |
№ 2 | 8.3 | 29.3 | 1.3 | – | 0.9 | 1.1 | 57.3 | 1.1 | 0.4 | 0.3 | |
1.0 МПа | № 1 | 2.7 | 50.2 | 1.3 | 0.1 | 1.1 | 0.8 | 41.4 | 1.5 | 0.5 | 0.4 |
№ 2 | 13.1 | 69.5 | 4.5 | – | 2.4 | 0.2 | 7.2 | 2.4 | 0.4 | 0.3 |
Исследования показали, что топография и химический состав поверхности после испытаний при различных давлениях сильно различается. Так, при минимальных давлениях на поверхности колодки из сплава № 2 с меньшим содержанием легкоплавких элементов обнаружено железо (табл. 3). Это связано с тем, что ввиду малого количества смазывающего компонента твердые фазовые составляющие сплава выступают в качестве абразива, провоцируя массоперенос железа со стальной поверхности контртела. В тоже время на поверхности ролика также происходит массоперенос материала колодки, приводящий к формированию пленки вторичных структур (ВС-темная фаза на СЭМ-изображении рис. 4б, 4г). С увеличением давления неравномерно нанесенная пленка ВС утолщается, что приводит к развитию макрорельефа и способствует образованию задира. При моделировании экстремальных условий (увеличении давления до 1 МПа, без смазки) имеет место сильный нагрев трущихся поверхностей: происходит расплавление не только легкоплавкой фазы, но и самой алюминиевой матрицы, которая переносится на поверхность ролика. При этом изменяется характер контакта (алюминий по алюминию) и прекращается перенос железа с поверхности ролика на поверхность колодки.
Торцевые срезы
Для более полного изучения процессов, происходящих в зоне контакта при трении, были приготовлены срезы колодок после испытаний, которые позволили исследовать приповерхностные слои сплавов. На рис. 5 в качестве примера приведены СЭМ – изображения среза колодки из сплава № 2 после трибологических испытаний при максимальном давлении 1 МПа. Для идентификации фаз и оценки их изменений (рис. 5б, 5в, 5г) представлены карты распределения отдельных химических элементов.
Рис. 5.
Изображение поверхности косого среза колодки из сплава № 2 после трибологических испытаний при давлении 1 МПа: а – СЭМ-изображение (во вторичных электронах); карта распределения отдельных элементов: б – Sn, в – Si, г – Cu.
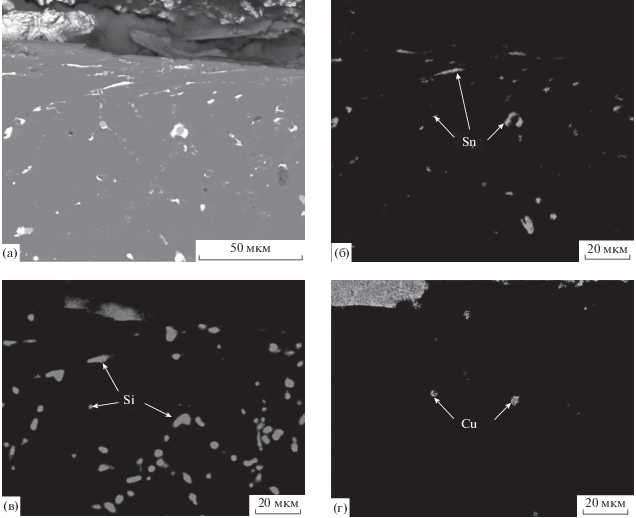
При изучении срезов всех образцов видно, что в приповерхностной области структура заметно отличается от структуры в объеме. Так, на ней прослеживаются фазовые составляющие, упорядоченные в направлении трения (“дорожки”). Это связано с тем, что в процессе трения в приповерхностных слоях происходит деформирование зерен и дендритных ячеек алюминиевой матрицы, приводящее к изменению геометрии этих составляющих. Исследования срезов всех сплавов позволяют оценить толщину деформированного слоя: для обоих сплавов это 20–30 мкм (для давлений 0.5 МПа) и 50–80 мкм (для давлений 1 МПа).
Рентгеноструктурные исследования поверхности
С помощью рентгеноструктурного анализа были получены результаты количественного анализа поверхностей образцов (табл. 5) и рентгенограммы до и после трибологических испытаний. В качестве примера на рис. 6 приведены данные для образца № 2 после трибологических испытаний.
Таблица 5.
Результаты количественного анализа поверхностей образцов до и после трибологических испытаний
№ образца | Название фазы (формула) | Пространственная группа | Содержание, % |
---|---|---|---|
№ 1 до испытаний |
Al | Fm-3m | 94 ± 2 |
Si | Fd-3m | 4.49 ± 1.9 | |
Sn | I41/amd | 1.0 ± 0.1 | |
(Bi0.625 Pb0.375) | P63/mmc | 0.57 ± 0.11 | |
№ 1 после испытаний |
Si | Fd-3m | 32 ± 2 |
Al | Fm-3m | 43.7 ± 1.9 | |
Sn | I41/amd | 11.1 ± 1.0 | |
Cu15 Si4 | I-43d | 5.3 ± 1.5 | |
Bi | I4/mcm | 8.0 ± 1.1 | |
№ 2 до испытаний |
Al | Fm-3m | 53.9 ± 0.9 |
Si | Fd-3m | 15.5 ± 0.8 | |
Sn | I41/amd | 29.7 ± 1.3 | |
Bi | Im-3m | 0.9 ± 0.1 | |
№ 2 после испытаний |
Al | Fm-3m | 41.1 ± 0.8 |
Si | Fd-3m | 22.8 ± 1.3 | |
Sn | I41/amd | 36.1 ± 1.9 |
Анализ графиков позволяет сделать вывод о том, что рентгеноструктурный анализ не выявил наличие интерметаллидов в сплаве. По данным исследования образец является смесью различных фаз – твердых растворов соответствующих элементов. Во всех образцах основными фазами являются алюминиевая и кремниевая. Причем фаза на основе Al (решетка – кубическая, гранецентрированная, типа меди; Fm-3m) является доминирующей. Кремний при анализе показывает себя как чистый компонент, но в действительности является эвтектикой Si + Al. Отметим, что оцененное рентгеновским методом содержание олова значительно выше, чем его заявленное содержание в объеме. Очевидно, это связано с различием содержания олова в объеме (задаваемым при получении) и его содержанием на поверхности (измеряемое рентгеновским методом). Также наблюдается сильное изменение концентрации олова (табл. 5) на поверхности после трибоиспытаний, что, очевидно, связано как с его переходом из объемных слоев к поверхности, а с поверхности – на контртело. Отметим, что первый процесс приводит к повышению концентрации олова на поверхности колодки, а второй – к уменьшению.
В табл. 6 представлены полученные величины периода решетки алюминиевой фазы в обоих сплавах до и после испытаний.
Таблица 6.
Значения периода решетки алюминиевых сплавов
Образец | Период решетки | |
---|---|---|
до испытаний | после испытаний | |
№ 1 | 4.051106 | 4.050606 |
№ 2 | 4.051123 | 4.042944 |
Отметим, что в исходном состоянии оба образца имеют практически одинаковые параметры решетки. После трибоиспытаний значения периода решетки уменьшается в обоих случаях, однако для образца № 2 этот эффект выражен значительно сильнее. Сам эффект может быть связан с изменением состава твердого раствора алюминия. Другой причиной может быть деформация (сжатие) решетки. Сильное различие эффекта в двух образцах объясняется, очевидно, различием в их химических составах (наличием кадмия в образце № 1).
Полученные результаты позволяют также определить микродеформацию образцов. Известно, что микродеформацию вызывает непостоянство расстояний между атомными плоскостями, вызываемое, например, различными дефектами решетки. При этом микродеформация кристаллической решетки определяется как ∆d/d = 0–1, где ∆d – средняя величина отклонения периода от его среднего значения d. Рассчитанные значения деформации приведены в табл. 7.
Таблица 7.
Значения микродеформации
Образец | Микродеформация, % | |
---|---|---|
до испытаний | после испытаний | |
№ 1 | 0.185 ± 0.005 | 0.198 ± 0.012 |
№ 2 | 0.125 ± 0.007 | 0.190 ± 0.012 |
Видно, что в исходном состоянии микродеформации сплава № 1 и сплава № 2 заметно различаются: очевидно, это связано с наличием кадмия в составе первого сплава.
Видно, что для обоих образцов трибоиспытания приводят к увеличению деформации, однако для второго образца этот эффект значительно выше (это находится в соответствии с данными по периодам решетки). Значения деформации могут свидетельствовать, в частности, о степени дефектности кристаллической решетки. Так, для второго образца, где наблюдается изменение от 0.125 до 0.190%, можно оценить диапазон плотности дислокаций в 108–109 (это значение соответствует состоянию с минимальными дефектами в кристаллической решетке).
По параметрам рентгенограмм была сделана попытка оценить степень текстурированности образцов. Известно, что текстура возникает в результате направленного внешнего воздействия, (например, в процессе деформации при трении) и может характеризовать это воздействие. Полученные данные приведены в табл. 8.
Таблица 8.
Полюсная плотность для различных плоскостей, исследуемых образцов до и после трибоиспытаний
PHKL | Образец №1 | Образец №2 | ||
---|---|---|---|---|
до испытаний | после испытаний | до испытаний | после испытаний | |
111 | 0.6 | 0.7 | 2.4 | 1.0 |
200 | 1.2 | 1.0 | 1.0 | 1.6 |
220 | 1.0 | 1.6 | 0.4 | 1.1 |
311 | 1.1 | 0.8 | 0.9 | 0.8 |
331 | 1.9 | 0.3 | 0.8 | 2.1 |
Из анализа табл. 8 можно предположить некоторое изменение текстуры в процессе трибоиспытаний, например, в образце № 2 об этом свидетельствует изменение интенсивности линий (111) и (220) примерно в 2.5–3 раза (уменьшение и увеличение, соответственно). Для образца 1 также наблюдаются изменения, хотя они и имеют менее выраженный характер. Изменение интенсивности линий может свидетельствовать о появлении в поверхностном слое преимущественного направления кристаллографической ориентации после трибоиспытаний. Полученные данные имеют лишь качественный характер. Для получения точных данных необходимо проведение измерений с использованием текстурной приставки.
ВЫВОДЫ
Было установлено, что после термообработки в обоих сплавах фазовые составляющие приобретают глобулярную форму. Так, после термообработки удлиненные фазовые составляющие сплава – кремниевые и легкоплавкие фазы приобрели более компактную округлую форму. Можно также предположить, что медь растворяется в алюминиевой матрице.
Установлена существенная неоднородность поверхностной теплопроводности литого образца, которая коррелирует с фазовым составом поверхности. Показано, что температурная обработка образца приводит к более однородной поверхностной теплопроводности. При этом фазы с меньшей теплопроводностью концентрируются на границах фаз с более высокой теплопроводностью. В целом методами СЗМ показано, что картина теплопроводности на микроуровне коррелирует с картиной электропроводности. Это позволяет для оценки тепловых свойств измерять электропроводность (что значительно проще).
Анализ СЭМ-изображений показал, что в процессе трения происходит деформация зерен, выделение мягкой фазы на поверхность и массоперенос. При исследовании поверхностей контактной пары после трибоиспытаний установлено, что твердые фазовые составляющие сплава выступают в качестве абразива. При этом наблюдается перенос железа со стальной поверхности контртела. На поверхности ролика происходит массоперенос материала колодки, приводящий к формированию пленки вторичных структур. С увеличением давления эта неравномерно сформированная пленка утолщается, что приводит к развитию макрорельефа и способствует появлению задира.
Изучение срезов методами СЭМ позволило сделать вывод об образовании приповерхностного слоя (30–80 мкм). В этом слое наблюдается деформация зерен, что и приводит к наблюдаемому выделению легкоплавких элементов.
Рентгеновские исследования показали, что при трибоиспытаниях значения периода решетки уменьшаются, что может быть связано как с изменением состава твердого раствора алюминия, так и с деформацией кристаллической решетки. Также показано, что трибоиспытания приводят к увеличению деформации и появлению текстуры.
Список литературы
Арзамасов Б.Н., Соловьёва Т.В., Герасимов С.А. и др. Справочник по конструкционным материалам: Справочник. М.: МГТУ, 2005. 640 с.
Ünlü B.S., Atik E. // Materials and Design. 2009. № 30. P. 1381. https://doi.org/10.1016/j.matdes.2008.06.069
Миронов А.Е., Гершман И.С., Овечкин А.В., Гершман Е.И. // Трение и износ. 2015. Т. 36. № 3. С. 334. https://doi.org/10.3103/S1068366615030095
Буше Н.А., Миронов А.Е., Маркова Т.Ф. // Железные дороги мира. 2003. № 11. С. 44.
Mironov A., Podrabinnik P., Kuznetsov E. // Materials Today: Proceedings. 2019. V. 11. Part 1. P. 197. https://doi.org/10.1016/j.matpr.2018.12.131
Белов Н.А., Михайлина А.О., Алабин А.Н., Столярова О.О. // Металловедение и термическая обработка металлов. 2016. № 4. С. 11. https://doi.org/10.1007/s11041-016-9988-5
Белов Н.А., Столярова О.О., Яковлева А.О. // Металлы. 2016. № 2. С. 35. https://doi.org/10.1134/S0036029516030034
Сачек Б.Я., Мезрин А.М., Муравьёва Т.И. и др. // Трение и износ. 2015. Т. 36. № 2. С. 137. https://doi.org/10.3103/S1068366615020142
Сачек Б.Я., Мезрин А.М., Муравьёва Т.И., Столярова О.О // Трение и износ. 2016. Т. 37. № 5. С. 606. https://doi.org/10.3103/S1068366616050160
Столярова О.О., Муравьева Т.И., Загорский Д.Л., Белов Н.А. // Физическая мезомеханика. 2016. Т. 19. № 5. С. 105.
Яковлева А.О., Белов Н.А., Базлова Т.А., Шкалей И.В. // Физика металлов и металловедение. 2018. Т. 119. № 1. С. 36. https://doi.org/10.1134/S0031918X18010167
Курбаткин И.И., Муравьева Т.И. // Трение и смазка в машинах и механизмах. 2012. № 1. С. 38.
Горячева И.Г., Курбаткин И.И., Буше Н.А. // Заводская лаборатория. Диагностика материалов. 2008. Т. 74. № 4. С. 51.
Металловедение: в 2-х т. / Под общей редакцией Золоторевского В.С. Т. II: Термическая обработка. Сплавы. М.: Издательский дом МИСиС, 2009. 528 с.
Щербакова О.О., Муравьёва Т.И., Загорский Д.Л. // Письма о материалах. 2018. Т. 8. № 2. С. 123. https://doi.org/10.22226/2410-3535-2018-2-123-128
Дополнительные материалы отсутствуют.
Инструменты
Поверхность. Рентгеновские, синхротронные и нейтронные исследования