Поверхность. Рентгеновские, синхротронные и нейтронные исследования, 2021, № 1, стр. 98-101
Технология нанесения покрытий системы Ti–Al–N с аморфно-кристаллической структурой
А. А. Маслов a, *, Р. Ш. Нагимов a, А. Ю. Назаров a, Э. Л. Варданян a
a Уфимский государственный авиационный технический университет
450022 Уфа, Россия
* E-mail: alexey.maslov2011@gmail.com
Поступила в редакцию 21.03.2020
После доработки 16.04.2020
Принята к публикации 20.04.2020
Аннотация
Проведен анализ методов формирования аморфных и кристалло-аморфных материалов и покрытий. Изучены факторы, влияющие на формирование аморфной структуры в материалах. На образцы из быстрорежущей стали нанесены покрытия из плазмы вакуумно-дугового разряда с двух однокомпонентных катодов из титана и алюминия. С помощью рентгеноструктурного анализа определено влияние расположения образца в камере относительно центра на степень кристалличности структуры покрытия. Проведены исследования влияния скорости вращения рабочего стола вокруг оси на процентное содержание аморфной фазы в интерметаллидных покрытиях. Установлено, что наибольшее содержание аморфной составляющей наблюдается у образцов, наиболее удаленных от оси стола. Это связано с тем, что образцы находились в условиях относительно быстрого охлаждения. По результатам исследований разработана технология нанесения покрытий на основе интерметаллидов системы (Ti, Al)N с аморфно-кристаллической структурой из плазмы вакуумного дугового разряда с двух однокомпонентных катодов.
ВВЕДЕНИЕ
Стремительное развитие промышленности влечет за собой рост требований к процессу обработки материалов, в особенности к режущему инструменту. Распространение труднообрабатываемых жаропрочных материалов диктует необходимость применения износостойкого и высокопроизводительного режущего инструмента [1, 2]. Одним из методов повышения долговечности инструментов является нанесение защитных покрытий при помощи ионно-плазменного осаждения. Особый интерес представляют собой покрытия с аморфной структурой, поскольку отсутствие кристаллической решетки предполагает отсутствие в ней дефектов, что предполагает более высокие прочностные характеристики [3] аморфных покрытий и их химическую стойкость [4].
Аморфное состояние металлов в сплавах является метастабильным состоянием [4], поэтому существуют термодинамические стимулы перехода его в кристаллическое состояние. Процесс перехода аморфной фазы в кристаллическую связан с преодолением энергетического барьера, поэтому энергия активации этого процесса зависит от природы кристаллизующей фазы. На сегодняшний день существует большое количество технологий получения аморфно-кристаллической структуры: различные виды закалки из расплава [6], тепловое или деформационное воздействие [7], импульсная фотонная и лазерная обработка [8], ионная имплантации и ряд других. Однако данные способы получения аморфно-кристаллической структуры малоприменимы к нанесению защитных покрытий на режущий инструмент.
Нанесение износостойких покрытий на рабочие поверхности инструмента является наиболее эффективным способом обеспечения оптимального сочетания “твердость–пластичность” [9, 10]. Наиболее распространенным на сегодняшний день является покрытие на основе интерметаллидов системы (Ti, Al)N. Нанесение такого покрытия позволяет повысить износостойкость и работоспособность режущего и долбежного инструмента при сохранении его точности [11, 12].
Целью данной работы является исследование влияния режимов осаждения на содержание аморфной составляющей в покрытиях на основе интерметаллидов системы (Ti, Al)N, полученных из плазмы вакуумно-дугового разряда.
МЕТОДИКА ИССЛЕДОВАНИЙ
Для исследования аморфно-кристаллической структуры покрытий использовались образцы из быстрорежущей стали Р12Ф2К8М3-МП, на поверхность которых было нанесено покрытие (Ti, Al)N при помощи модернизированной установки ННВ-6.6 И1. Нанесение покрытий проводилось в среде азота.
Схема проведения эксперимента при одновременном осаждении покрытия из двух электродуговых испарителей с однокомпонентными катодами с вращением рабочего стола вокруг своей оси при различных скоростях (ω = 1–14 об./мин) и с ассистированием процесса плазменным источником с накаленным катодом представлена на рис. 1. Один образец был закреплен в центре рабочего стола (R1), еще три образца крепились на различных радиусах от его оси – 8 (R2), 15 (R3), 22 см (R4).
Для выявления аморфной структуры проводился рентгеноструктурный анализ на установке Rigaku IV: использовалось CuKα-излучение при напряжении 30 кВ и токе 20 мА. Угловой интервал сьемки 2θ = 10°–100°.
После осаждения покрытия из двух электродуговых испарителей с однокомпонентными катодами были произведены рентгеноструктурный анализ, а также расчеты степени кристалличности для всех образцов. Наиболее надежно определяется степень кристалличности рентгеновским методом.
Ионно-плазменные покрытия после напыления имеют быстрозакаленную структуру и содержат значительный объем аморфной фазы, о чем свидетельствует наличие аморфного гало помимо четких рефлексов на дифрактограммах образцов с покрытиями.
Для того, чтобы оценить, какую долю объема покрытия занимают кристаллические области, используют оценку степени кристалличности. Рассмотрим образец с покрытием, имеющего массу m. Пусть масса всех кристаллических областей в этом образце равна mk, а масса всех аморфных – ma.
Тогда
Отсюда следует, чтоТак как на рентгенограмме образцов с интерметаллидным покрытием кроме рефлексов имеется аморфное гало, то обычно полагают, что интегральная интенсивность аморфного гало пропорциональна массовой доле аморфных областей.
Поэтому кривую интенсивности рассеянных покрытием рентгеновских лучей разделяют на несколько кривых, характеризующих рассеяние от кристаллических и аморфных областей. Площадь под этими кривыми пропорциональна интегральной интенсивности рассеяния рентгеновских лучей. Измерив эти площади, можно по отношению интегральных интенсивностей определить степень кристалличности. При помощи полученных графиков можно определить площадь аморфной и кристаллической фазы (рис. 2) [14, 15].
Рис. 2.
Кривая распределения интенсивности рентгеновских лучей при дифракции с поверхности исследуемых образцов: 1 – результирующая кривая, 2 – рассеяние на кристаллитах, 3 – рассеяние на аморфных областях.
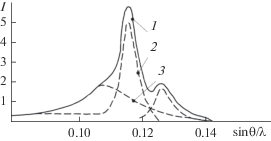
Степень кристалличности определяется по формуле:
где Sкр – площадь кристаллической структуры, Sa – площадь аморфной структуры.РЕЗУЛЬТАТЫ И ИХ ОБСУЖДЕНИЕ
Дифрактограммы образцов с интерметаллидными покрытиями, полученными осаждением с двух однокомпонентных катодов из плазмы дугового разряда, представлены на рис. 3, 4.
Из результатов рентгеноструктурного анализа следует, что при увеличении расстояния от оси стола степень кристалличности нанесенного материала падает, кроме того, согласно данным рентгеноструктурного анализа, высокое содержание аморфной структуры наблюдается в диапазоне оборотов ω = 3–7 об./мин.
Результаты расчетов степени кристалличности покрытий, осажденных в среде N2, от угловой скорости стола и расстояния от его центра приведены в табл. 1.
Таблица 1.
Степень кристалличности покрытий, осажденных из плазмы вакуумно-дугового разряда
Скорость вращения стола ω, об./мин | Расстояние от центра стола R, см | |||
---|---|---|---|---|
0 | 8 | 15 | 22 | |
1 | 76.94 | 78.39 | 78.08 | 74.16 |
3 | 72.09 | 73.7 | 73.2 | 70.6 |
7 | 73.2 | 73.3 | 73.2 | 70 |
14 | 75.5 | 81.9 | 78.3 | 75.4 |
Зависимости степени кристалличности от угловой скорости и расстояния от центра стола представлены на рис. 5.
Рис. 5.
Зависимость степени кристалличности структуры x покрытий от угловой скорости и расстояния от центра рабочего стола R.
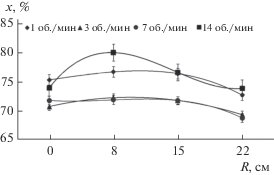
В результате вычислений установлено, что наибольшей степенью кристалличности обладает покрытие на образце, полученном при следующих условиях: скорость вращения стола: ω = = 14 об./мин, радиус закрепления образца R = 8 cм. Наибольшее содержание аморфной составляющий выявлено у образцов со следующими параметрами нанесения покрытия:
1. Скорость вращения стола составляет ω = = 3 об./мин, радиус закрепления образца – R = = 22 см;
2. Скорость вращения стола – ω = 7 об./мин, радиус закрепления образца – R = 22 cм.
ЗАКЛЮЧЕНИЕ
Проведен анализ методов формирования аморфных и кристалло-аморфных материалов и покрытий. Изучены факторы, влияющие на формирование аморфной структуры в материалах. Напыление покрытий проводились из плазмы вакуумно-дугового разряда с двух однокомпонентных катодов из титана и алюминия. Проведены расчеты степени кристалличности образцов с покрытиями. С помощью рентгеноструктурного анализа определено влияние расположения образца в камере относительно центра на степень кристалличности структуры покрытия. Проведены исследования влияния скорости вращения рабочего стола вокруг оси на процентное содержание аморфной фазы в интерметаллидных покрытиях. Установлено, что наибольшее содержание аморфной составляющей наблюдается у образцов, наиболее удаленных от оси стола. Это связано с тем, что образцы находились в условиях относительно быстрого охлаждения. По результатам проведенных исследований разработан способ получения аморфно-кристаллических покрытий (Ti, Al)N из плазмы вакуумно-дугового разряда. Разработанная технология может быть применена для повышения эксплуатационных свойств металлорежущих инструментов.
Список литературы
Локтев Д., Ямашкин Е. // Наноиндустрия. 2007. № 4. С. 18.
Григорьев С.Н. Методы повышения стойкости режущего инструмента: учебник для студентов втузов. М.: Машиностроение, 2009. 368 с.
Kou H., Lu J., Li Y. // Advanced Materials. 2014. V. 26. № 31. C. 5518. https://doi.org/10.1002/adma.201401595
Ноженков М.В. // Поверхность. Рентген., синхротр. и нейтрон. исслед. 2015. № 5. С. 100.
Asami K. et al. // Corrosion Science. 1976. V. 16. № 12. C. 909. https://doi.org/10.1016/S0010-938X(76)80010-8
Бетехтин В.И., Кадомцев А.Г., Толочко О.В. // Физика твердого тела. Т. 43. № 10. С. 1815.
Зельдович В.И., Фролова Н.Ю., Пилюгин В.П., Гундырев В.М., Пацелов А.М. // Физика металлов и металловедение. 2005. Т. 99. № 4. С. 90.
Balla V.K., Bandyopadhyay A. // Surfaceand Coatings Technology. 2010. V. 205. № 7. C. 2661. https://doi.org/10.1016/j.surfcoat.2010.10.029
Григорьев С.Н., Табаков В.П., Волосова М.А. // Старый Оскол: ТНТ. 2011. Т. 379.
Гуревич Я.Л. Режимы резания труднообрабатываемых материалов: Справочник. 2-е изд., перераб. и доп. М.: Машиностроение, 1986. 240 с.
Варданян Э.Л. Композиционные покрытия на основе интерметаллидов системы Ti–Al и технологии их нанесения из плазмы вакуумно-дугового разряда: Дис. ... канд. техн. наук: 05.16.06. М.: Рос. гос. технол. ун-т им. КЭ Циолковского (МАТИ), 2015. 133 с.
Шехтман С.Р. Разработка новых материалов для защитных ионно-плазменных покрытий с СМК структурой и технологий их нанесения на лопатки ГТД: Дис. ... д-ра техн. наук: 05.16.06. М.: Рос. гос. технол. ун-т им. К.Э. Циолковского (МАТИ), 2015. 294 с.
Аверко-Антонович Ю.И., Бикмуллин Р.Т. Методы исследования структуры и свойств полимеров. КГТУ. Казань, 2002. 604 с.
Лебедев Ю.А., Королев Ю.М., Поликарпов В.М., Игнатьева Л.Н., Антипоев Е.М. // Кристаллография. 2010. Т. 55. № 4. С. 651.
Абросимова Г.Е., Аронин А.С., Холстинина Н.Н. // Физика твердого тела. 2010. Т. 52. № 3. С. 417.
Дополнительные материалы отсутствуют.
Инструменты
Поверхность. Рентгеновские, синхротронные и нейтронные исследования