Поверхность. Рентгеновские, синхротронные и нейтронные исследования, 2021, № 10, стр. 102-107
Ионное азотирование высоколегированных конструкционных сталей с ультрамелкозернистой структурой при различных температурах
Р. С. Есипов 1, Р. А. Абдуллин 1, *, Ю. Г. Хусаинов 1, А. А. Николаев 1
1 Уфимский государственный авиационный технический университет
450103 Уфа, Россия
* E-mail: ravab98@mail.ru
Поступила в редакцию 12.12.2020
После доработки 25.02.2021
Принята к публикации 28.02.2021
Аннотация
Исследован перспективный способ повышения трибологических характеристик поверхности конструкционных высоколегированных сталей с ультрамелкозернистой структурой методом низкотемпературного ионного азотирования в многокомпонентной плазме тлеющего разряда низкого давления. Показано влияние обработки методом интенсивной пластической деформации кручения на структуру и механические свойства поверхности конструкционных материалов. Проанализированы особенности ионного азотирования таких материалов после их измельчения. Проведено сравнение характеристик поверхности образцов с крупнозернистой и ультрамелкозернистой структурами после химико-термической обработки при различной температуре выдерживания. Исследован структурно-фазовый состав поверхности материалов после насыщения азотом при низкой температуре. Показан и определен механизм изнашивания поверхности образцов после деформационной обработки и последующего азотирования в тлеющем разряде низкого давления.
ВВЕДЕНИЕ
В настоящее время в машиностроительной отрасли промышленности растет интерес к конструкционным материалам, которые получены методом интенсивной пластической деформации. Металлы и сплавы после интенсивной пластической деформации имеют ультрамелкозернистую структуру, размер зерен составляет от 100 до 500 нм. Такие материалы показывают высокие значения прочности по сравнению с крупнозернистыми аналогами [1, 2].
Несмотря на высокие физико-механические свойства конструкционных сталей с ультрамелкозернистой структурой, поверхность деталей, работающих в условиях контактных нагрузок, по-прежнему подвергается интенсивному изнашиванию. Поэтому с целью повышения эксплуатационных характеристик такие детали подвергают поверхностной упрочняющей химико-термической обработке. Большое распространение получило азотирование в тлеющем разряде (ионное азотирование) благодаря ряду преимуществ: возможности управления структурно-фазовым составом азотированных слоев, низкому расходу рабочего газа и экологической чистоте процесса обработки [3, 4].
Известно, что эффективное повышение эксплуатационных характеристик поверхности конструкционных сталей происходит при температурах азотирования 550–600°С и длительном выдерживании (до 36 ч) [5]. Однако нагрев сталей, подвергнутых интенсивной пластической деформации до температур свыше 450–500°С, приводит к рекристаллизации и росту зерен структуры, что в свою очередь приводит к снижению механических свойств материала. Следовательно, для повышения эксплуатационных характеристик и сохранения заданных механических свойств основы материала ионное азотирование стали с ультрамелкозернистой структурой необходимо осуществлять в области низких температур (до ~450°С) [6–9]. Поэтому разработка новой технологии низкотемпературного ионного азотирования изделий из конструкционных сталей аустенитного (12Х18Н10Т) и мартенситного (13Х11Н2В2МФ-Ш) классов с ультрамелкозернистой структурой является весьма актуальной задачей.
МЕТОДИКА ИССЛЕДОВАНИЙ
Для исследований были подготовлены образцы конструкционных сталей аустенитного (12Х18Н10Т) и мартенситного (13Х11Н2В2МФ-Ш) классов, вырезанные из калиброванных термообработанных прутков диаметром 20 мм. Термообработку стали 12Х18Н10Т осуществляли путем закалки от 1050°С, а стали 13Х11Н2В2МФ-Ш – в ходе закалки от 1050°С с последующим отжигом при 800°С в течение 1 ч. Образцы с ультрамелкозернистой структурой получали на установке для интенсивной пластической деформации кручения СКРУДЖ-200 Института физики перспективных материалов при температуре 300°С, квазистатическом давлении 6 ГПа и количестве оборотов n = 10. Термическую стабильность сталей после деформации устанавливали методом отжига образцов при температурах 400, 450, 500, 550, 600°С в течение 1 ч.
Ионное азотирование проводили на модернизированной установке ЭЛУ-5М [10] при давлении 150 Па в многокомпонентной атмосфере, содержащей аргон, азот и водород. Диффузионное насыщение осуществляли при температурах 450, 500 и 550°С в течение 6 ч. Микротвердость измеряли методом Виккерса на приборе Struers Duramin-1/-2 при нагрузке 9.8 Н (100 г) и выдерживании в течение 10 с. Испытания поверхности образцов на износостойкость проводили методом “шар по диску” на трибометре Nanovea в режиме сухого трения, в качестве контртела выступал шарик из стали ШХ-15 при нормально направленной к поверхности образца нагрузке 4 Н. Рентгеноструктурный анализ проводили на дифрактометре Rigaku Ultuma IV (CuKα-излучение).
РЕЗУЛЬТАТЫ И ИХ ОБСУЖДЕНИЕ
После термообработки сталь 12Х18Н10Т в исходном состоянии была однофазной – структура представляла собой зерна γ-Fe с гранецентрированной кубической (ГЦК) решеткой, средний размер которых составил 3–4 мкм. Сталь 13Х11Н2В2МФ-Ш в исходном состоянии имела структуру α-Fe с размером зерен 1–1.5 мкм с однородно распределенными по объему частицами карбидов, размер которых составил 150 нм. Исследования в просвечивающем электронном микроскопе образцов сталей, прошедших интенсивную пластическую деформацию кручения, показали, что в результате деформации на поверхности стали 12Х18Н10Т средний размер кристаллитов γ-Fe уменьшился до 150–180 нм. Произошло деформационно-индуцированное мартенситное превращение γ → α', о чем свидетельствует появление рефлексов α'-фазы. На поверхности стали 13Х11Н2В2МФ-Ш после интенсивной пластической деформации кручения размер кристаллитов α-Fe и карбидов составил около 150–190 нм. В результате анализа полученных данных установлено, что после деформации образцы исследуемых сталей имеют ультрамелкозернистую структуру со средним размером зерен 150–90 нм. На рис. 1 приведены результаты радиального измерения поверхностной микротвердости образцов сталей с ультрамелкозернистой структурой, прошедших ионное азотирование в интервале температур 450–550°С.
Рис. 1.
Распределение поверхностной микротвердости по диаметру образцов сталей 12Х18Н10Т (а) и 13Х11Н2В2МФ-Ш (б) с ультрамелкозернистой структурой до и после ионного азотирования при различных температурах (U = 430–470 В, P = 150 Па, t = 6 ч): 1 – после интенсивной пластической деформации кручения; 2 – 450; 3 – 500; 4 – 550°C.
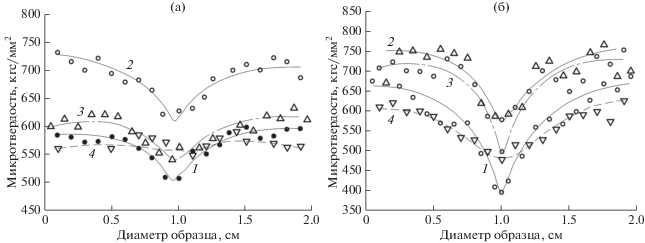
В результате анализа полученных данных (рис. 1) установлено, что после деформации распределение микротвердости образцов неоднородно. На середине радиуса образцов твердость достигает максимальных значений: в случае стали 12Х18Н10Т – около 580 кгс/мм2, в случае стали 13Х11Н2В2МФ-Ш – около 650 кгс/мм2. Максимальная степень упрочнения (22–25%) получена на образцах, прошедших азотирование при температуре 450°C. При увеличении температуры обработки до 500 и 550°C неоднородность распределения микротвердости уменьшается, а поверхностная твердость снижается вследствие начала процессов рекристаллизации ультрамелкозернистых сталей.
На рис. 2 приведены результаты измерения микротвердости по глубине образцов сталей с ультрамелкозернистой структурой после ионного азотирования в интервале температур 450–550°C. Установлено, что на поверхности образцов, прошедших ионное азотирование при температуре 450°C, глубина упрочненного слоя составляет ~70 мкм в случае стали 12Х18Н10Т (рис. 2а) и ~90 мкм в случае стали 13Х11Н2В2МФ-Ш (рис. 2б). По мере проникновения вглубь материала микротвердость плавно снижается до исходного значения. При температуре 500°C микротвердость стали также плавно 12Х18Н10Т уменьшается, а на поверхности стали 13Х11Н2В2МФ-Ш микротвердость увеличивается вследствие выделения карбидов из твердого раствора α-Fe, которые выступают в качестве упрочняющей фазы. При температуре 550°C распределение микротвердости по глубине образцов приобретает вид, соответствующий сталям с крупнозернистой структурой.
Рис. 2.
Распределение микротвердости по глубине поверхностного слоя стали 12Х18Н10Т (а) и 13Х11Н2В2МФ (б) с ультрамелкозернистой структурой после азотирования при различных температурах: 1 – 450; 2 – 500; 3 – 550°С.
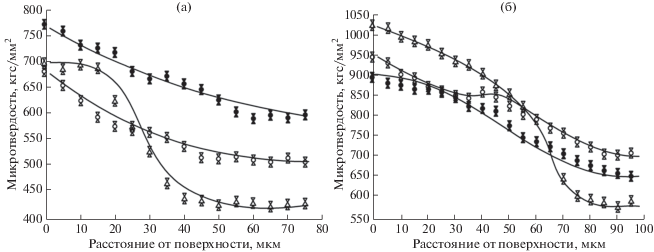
В результате исследования микроструктуры образца стали 13Х11Н2В2МФ-Ш с крупнозернистой структурой, прошедшего низкотемпературное ионное азотирование, установлено, что на поверхности образца появляется модифицированный слой толщиной 35–40 мкм. На поверхности образца с ультрамелкозернистой структурой толщина модифицированного слоя составляет 20–30 мкм в центре и 60–65 мкм на расстоянии ~9 мм от центральной оси образца. Поскольку на периферии образца структура ультрамелкозернистая, интенсификация процесса диффузии азота происходит именно в этой области. В результате анализа полученных данных установлено, что на поверхностях сталей 12Х18Н10Т и 13Х11Н2В2МФ-Ш с ультрамелкозернистой структурой скорость роста модифицированного слоя при ионном азотировании при 450°C в 2–2.5 раза выше, чем в случае стали с крупнозернистой структурой. С ростом температуры ионного азотирования до 500, 550°C скорость роста диффузионного слоя на поверхностях образцов с ультрамелкозернистой и крупнозернистой структурой примерно одинакова. Приведенные данные не различаются и в случае стали 12Х18Н10Т с ультрамелкозернистой структурой. Рост диффузии азота обусловлен наличием в структуре стали, прошедшей интенсивную пластическую деформацию кручения, множества дефектов (вакансий, дислокаций и их скоплений и субзерен). Эти дефекты приводят к низкой энергии активации диффузии азота, что способствует повышению коэффициента диффузии [8, 9, 11].
Результаты структурно-фазового анализа поверхности сталей 12Х18Н10Т и 13Х11Н2В2МФ-Ш с ультрамелкозернистой структурой после ионного азотирования при температуре 450°C приведены на рис. 3. Рентгеноструктурные исследования показали, что низкотемпературное ионное азотирование приводит к формированию на поверхности аустенитной стали 12Х18Н10Т нитридов ε-фазы (Fe2–3N), азотистого твердого раствора γ-Fe[N] c ГЦК-решеткой, CrN и мартенситной α'-фазы; на поверхности мартенситной стали 13Х11Н2В2МФ – нитридов ε-фазы и легирующих элементов Cr, V(N). Поскольку обрабатываемая сталь имеет ультрамелкозернистую структуру, образующиеся фазы, предположительно, мелкодисперсные и выделяются в основном на границах зерен [12, 13]. С увеличением температуры до 500 и 550°С в случае стали 12Х18Н10Т наблюдалось увеличение интенсивности пиков ε-фазы в 1.5 раза. Происходил распад мартенситной фазы и ее превращение в твердый раствор γ-Fe, о чем свидетельствует уменьшение пиков α'-фазы в два–три раза. В случае стали 13Х11Н2В2МФ-Ш с ростом температуры обработки до 500 и 550°С увеличивалась интенсивность пиков ε-фазы и нитрида хрома CrN в 2–2.5 раза.
Рис. 3.
Дифрактограммы образцов сталей 12Х18Н10Т (а) и 13Х11Н2В2МФ-Ш (б) с ультрамелкозернистой структурой после ионного азотирования при температуре 450°С.
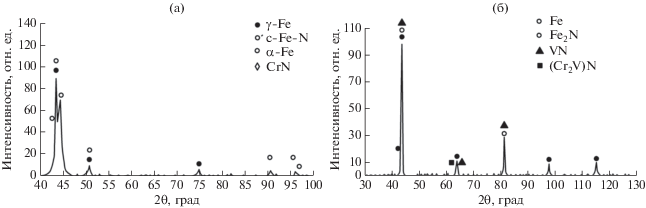
Анализ зависимости коэффициента трения от продолжительности изнашивания образцов (рис. 4) показал, что до азотирования стали 12Х18Н10Т средний коэффициент трения Kf = 0.5; в случае стали 13Х11Н2В2МФ-Ш Kf = 0.85. Длительность этапа приработки для сталей составила примерно 0.25 мин. После низкотемпературного ионного азотирования стали 12Х18Н10Т средний коэффициент трения Kf = 0.4, а в случае стали 13Х11Н2В2МФ-Ш Kf = 0.85. Длительность этапа приработки для сталей с ультрамелкозернистой структурой, прошедших ионное азотирование, составила около 1 мин. Увеличение времени приработки объясняется образованием азотированного слоя повышенной твердости [14].
Рис. 4.
Зависимость коэффициента трения от продолжительности изнашивания образцов стали 12Х18Н10Т (а, б) и 13Х11Н2В2МФ-Ш (в, г) до (а, в) и после (б, г) ионного азотирования при Т = 450°С.
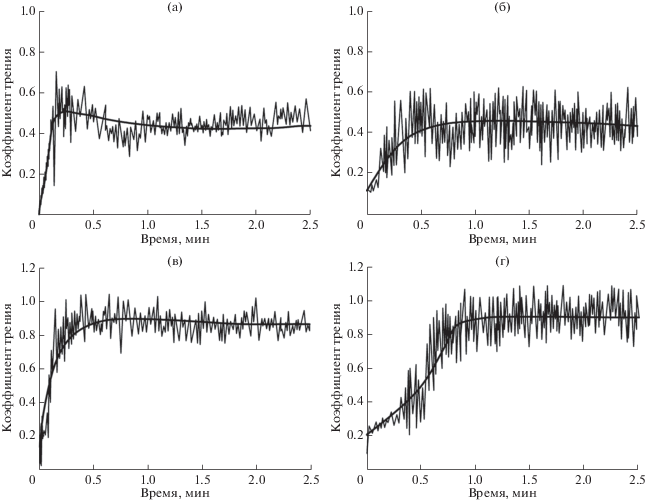
Результаты исследования треков износа с помощью оптического микроскопа показали, что основным механизмом изнашивания поверхности стали 12Х18Н10Т с ультрамелкозернистой структурой является адгезионный износ, поскольку на поверхности наблюдались наплывы и вырывы материала. Преимущественным механизмом износа стали 13Х11Н2В2МФ-Ш с ультрамелкозернистой структурой также является адгезионный износ. Подробные исследования в атомно-силовом микроскопе треков износа образцов, прошедших низкотемпературное ионное азотирование, показали, что основным механизмом изнашивания является абразивный износ, о чем свидетельствует множество царапин. Абразивными частицами являются нитриды ε-фазы и нитриды легирующих элементов [15].
На рис. 5 представлены диаграммы убыли массы образцов после испытания на износ в зависимости от состояния и вида обработки стали. Анализ диаграмм показал, что низкотемпературное ионное азотирование (Т = 450°С) приводит к повышению износостойкости стали 12Х18Н10Т в 1.5, а стали 13Х11Н2В2МФ-Ш – в 1.2 раза. Повышение износостойкости вызвано образованием азотированного слоя, в состав которого входят нитриды ε-фазы и нитрида хрома CrN. При повышении температуры азотирования наблюдается также увеличение износостойкости поверхности образцов. Однако, как было указано ранее, при температурах свыше 450°С происходит деградация ультрамелкозернистой структуры материала и снижение механических свойств.
ЗАКЛЮЧЕНИЕ
Разработан новый способ низкотемпературного ионного азотирования в тлеющем разряде при температуре 450°С, позволяющий повысить износостойкость поверхности сталей 12Х18Н10Т и 13Х11Н2В2МФ-Ш с ультрамелкозернистой структурой до 1.2–1.5 раз. Установлено, что при увеличении содержания аргона от 10 до 70% температура катода растет экспоненциально, а напряжение между электродами уменьшается линейно. Выявлено, что рабочая газовая среда с концентрацией водорода более 15% способствует образованию в диффузионной зоне микротрещин по границам зерен основы. Однако наибольшее увеличение скорости роста упрочненного слоя наблюдается при содержании в рабочем газе 25% водорода, при котором осуществляется эффективное химическое травление оксидной пленки на поверхности сталей. Установлено, что в сталях аустенитного и мартенситного классов с ультрамелкозернистой структурой, полученных методом интенсивной пластической деформации кручения, при низкотемпературном ионном азотировании (450°С) диффузия азота вглубь материала в 2–2.5 раза выше по сравнению с крупнозернистым аналогом. Установлено, что деформационная обработка сталей 12Х18Н10Т и 13Х11Н2ВМФ-Ш методом интенсивной пластической деформации кручения и последующее ионное азотирование приводит к изменению механизма изнашивания поверхности. Изнашивание поверхности стали с ультрамелкозернистой структурой после низкотемпературного ионного азотирования протекает в основном по абразивному механизму по сравнению с исходным состоянием, когда износ происходит по механизму адгезионного типа.
Список литературы
Zrník J., Dobatkin S.V., Raab G., Kraus L. // Mater. Sci. Forum. 2010. V. 654. P. 1223.
Valiev R.Z., Islamgaliev R.K., Alexandrov I.V. // Progress Mater. Sci. 2000. V. 45. № 2. P. 103.
Рамазанов К.Н. // Упрочняющие технологии и покрытия. 2009. № 9. С. 47.
Пастух И.М. // Проблемы трибологии. 2001. № 2. С. 93.
Минкевич А.Н. Химико-термическая обработка металлов и сплавов. М.: Машиностроение, 1965. 331 с.
Tong W.P., Han Z., Wang L.M., Lu J., Lu K. // Surf. Coat. Technol. 2008. V. 202. № 20. P. 4957.
Laleh M., Kargar F., Velashjerdi M. // J. Mater. Eng. Performance. 2013. V. 22. № 5. P. 1304.
Manova D., Mändl S., Neumann H., Rauschenbach B. // Surf. Coat. Technol. 2007. V. 201. № 15. P. 6686.
Xi Y., Liu D., Han D. // Surf. Coat. Technol. 2008. V. 202. № 12. P. 2577.
Рамазанов К.Н., Будилов В.В., Вафин Р.К. // Упрочняющие технологии и покрытия. 2010. № 5. С. 39.
Лахтин Ю.М., Коган Я.Д., Шапошников В.Н. // Металловедение и термическая обработка металлов. 1976. № 6. С. 2.
Лахтин Ю.М., Лахтин Ю.М., Коган Я.Д., Шпис Г.-Й., Бемер З. Теория и технология азотирования. М.: Металлургия, 1991. 320 с.
Бутенко О.И., Лахтин Ю.М. // Металловедение и термическая обработка металлов. 1969. № 6. С. 21.
Будилов В.В., Рамазанов К.Н., Хусаинов Ю.Г., Золотов И.В. // Вестн. УГАТУ. 2015. № 2. С. 3.
Арзамасов Б.Н. Химико-термическая обработка металлов в активизированных газовых средах. М.: Машиностроение, 1979. 224 с.
Дополнительные материалы отсутствуют.
Инструменты
Поверхность. Рентгеновские, синхротронные и нейтронные исследования