Поверхность. Рентгеновские, синхротронные и нейтронные исследования, 2021, № 11, стр. 68-74
Влияние термообработки на физические свойства и морфологию полых субмикронных частиц SiO2
В. М. Масалов a, *, Н. С. Сухинина a, И. И. Ходос b, И. И. Зверькова a, А. А. Жохов a, Г. А. Емельченко a
a Институт физики твердого тела им. Ю.А. Осипьяна РАН
142432 Московская область, Черноголовка, Россия
b Институт проблем технологии микроэлектроники и особочистых материалов РАН
142432 Московская область, Черноголовка, Россия
* E-mail: masalov@issp.ac.ru
Поступила в редакцию 10.04.2021
После доработки 20.06.2021
Принята к публикации 25.06.2021
Аннотация
Темплатным методом с использованием предварительно синтезированных частиц полиметилметакрилата были получены полые частицы диоксида кремния. Установлено влияние типа катализатора (гидроксида аммония и L-аргинина) на величину усадки и механическую прочность кремнеземных оболочек при термообработке. Проведена оценка их исходной пористости. Показана зависимость величины усадки полых частиц от температуры отжига в диапазоне 100–900°С. Установлено, что частицы, полученные с использованием гидроксида аммония в качестве катализатора, имеют большую механическую прочность и менее подвержены деформации в процессе отжига.
ВВЕДЕНИЕ
В последние десятилетия полые нано- и субмикронные частицы диоксида кремния привлекают повышенное внимание исследователей-материаловедов ввиду уникального сочетания их свойств. Кремнезем отличается термической стабильностью, химической инертностью и биосовместимостью. В дополнение к этому полые частицы диоксида кремния обладают низкой плотностью и теплопроводностью, высокой удельной поверхностью, адсорбционной емкостью. Кроме того, имеется возможность получения частиц с высокой степенью монодисперсности [1]. Сочетание в себе таких структурных особенностей, как пористая оболочка и внутренняя полость, предопределяют широкий круг перспективных применений в катализе и адсорбции [2, 3], а высокая биосовместимость открывает возможности для биомедицинских применений: для загрузки и контроля систем высвобождения специальных материалов, таких как лекарства, гены, пептиды [4–6]. Полые сферические нано/микрочастицы кремнезема могут стать основой для разработки теплоизолирующих материалов новых типов благодаря имеющейся возможности регулирования теплофизических свойств путем модификации их размеров и пористости [7]. Большие перспективы имеет использование полых частиц кремнезема в качестве компонентов новых композиционных материалов для повышения их термостойкости, понижения плотности и теплопроводности.
Основным методом получения полых частиц является двухстадийный процесс, включающий синтез гибридных частиц типа “ядро–оболочка” темплатным способом с последующим удалением ядер-темплатов физическими или химическими методами [8, 9]. В качестве темплатов могут быть использованы различные твердые неорганические и органические частицы, а также капли жидкостей и пузырьки воздуха в жидких средах [10]. Из-за плохой монодисперсности и деформируемости мягких шаблонов для получения полых частиц с высокой однородностью предпочтительно использование твердых шаблонов, таких как полимерные монодисперсные частицы [11–15].
Для извлечения полимерных ядер-темплатов чаще всего используют термообработку гибридных частиц. Естественно предположить, что в зависимости от температурных и временных параметров обработки начальные гибридные и конечные полые частицы должны претерпевать геометрические и структурные трансформации. Однако в многочисленных публикациях, посвященных синтезу полых частиц диоксида кремния, в том числе с использованием полимерных частиц в качестве темплатов, как правило, отсутствуют экспериментальные данные о влиянии термообработки на размеры частиц и их морфологию.
Целью работы было исследование трансформации частиц типа “ядро–оболочка” и полых частиц из диоксида кремния в ходе их термообработки.
ЭКСПЕРИМЕНТАЛЬНАЯ ЧАСТЬ
Схема получения полых сферических частиц диоксида кремния представлена на рис. 1. На первой стадии эмульсионным методом [16] были синтезированы монодисперсные сферические частицы полиметилметакрилата (ПММА) диаметром ~440 нм. В качестве инициаторов полимеризации использовали растворимый в воде персульфат калия (0.2 мас. %) и растворимый в мономере (метилметакрилате – ММА) азобисизобутиронитрил (0.2 мас. %).
Затем на втором этапе получали гибридные частицы ПММА–SiO2 типа “ядро–оболочка”, используя синтезированные микросферы ПММА в качестве темплата. Кремнеземные оболочки формировали в ходе гидролиза винилтриметоксисилана (ВТМС) с использованием двух различных катализаторов: гидроксида аммония [17] (частицы типа I) и аминокислоты L-аргинина (частицы типа II). Концентрации катализаторов в водном растворе составляли 0.8 М NH3 и 2 мМ L-аргинина соответственно. Расчетное количество ВТМС добавляли в раствор и проводили синтез при непрерывном перемешивании реакционной смеси с помощью магнитной мешалки. Количество ВТМС рассчитывали, исходя из требуемой толщины SiO2-оболочки, размера сферических ПММА-частиц и концентрации суспензии ПММА. Например, для получения на частицах ПММА диаметром ~440 нм оболочек SiO2 толщиной ~30 нм к 134 г 4 мас. % суспензии ПММА добавляли 6 г ВТМС. Синтез проводили при комнатной температуре в течение 2 ч (частицы типа I) и около 7 ч (частицы типа II). Полученные частицы ПММА–SiO2 сушили и подвергали термообработке в течение 24 ч при различных температурах в интервале 100–1000°С.
Морфологию и размеры частиц контролировали с помощью растрового электронного микроскопа (РЭМ) Zeiss Supra 50 VP и просвечивающего электронного микроскопа (ПЭМ) высокого разрешения JEM-2100. Рентгенофазовый анализ образцов, отожженных при высоких температурах (900–1100°С), проводили с помощью дифрактометра Rigaku (CuKα1-излучение).
РЕЗУЛЬТАТЫ И ИХ ОБСУЖДЕНИЕ
На рис. 2 представлены РЭМ-изображения сферических частиц ПММА диаметром ~440 нм (рис. 2а) и полученных на их основе гибридных частиц ПММА–SiO2 типа “ядро–оболочка” диаметром ~500 нм, синтезированных с использованием разных катализаторов при гидролизе ВТМС (рис. 2б, 2в). Внешне гибридные частицы практически не отличаются друг от друга.
Рис. 2.
РЭМ-изображения частиц ПММА размером ~440 нм (а) и полученных на их основе гибридных частиц ПММА–SiO2 диаметром ~500 нм с использованием в качестве катализаторов гидролиза ВТМС NH4OH (б) и L-аргинина (в).
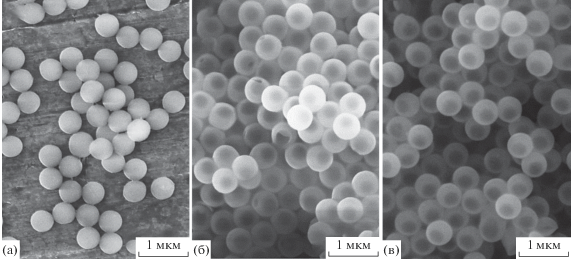
Для преобразования частиц “ядро–оболочка” ПММА–SiO2 в полые сферические частицы диоксида кремния полимерные ядра удаляли в ходе термообработки. При температурах выше 200°С полимер разлагался до мономера ММА и испарялся. Полученные полые частицы демонстрировали практически идеальную сферическую форму (рис. 3). Однако наблюдалось различие в морфологии термообработанных частиц разных типов.
Рис. 3.
РЭМ-изображения частиц ПММА–SiO2 типа “ядро–оболочка”, полученных при использовании в качестве катализатора гидролиза ВТМС NH4OH (a–г) и L-аргинина (д–з), после термообработки в течение 24 ч при температуре: 150 (а, д), 400 (б, е), 800 (в, ж), 900°С (г, з).
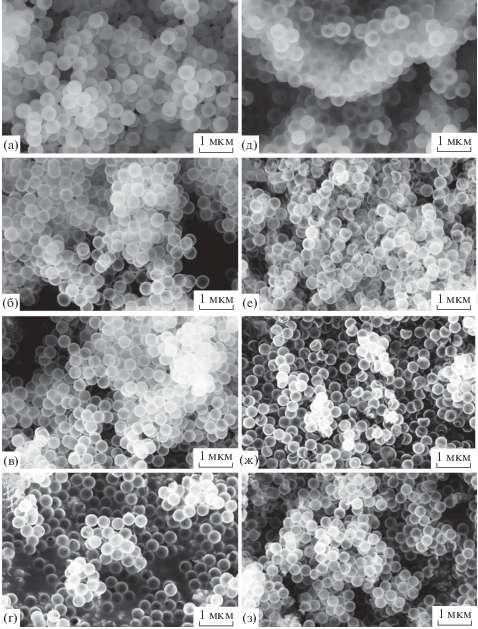
Для оценки влияния температуры отжига на морфологию и размеры частиц была проведена обработка частиц типа I и II при 100, 150, 200, 300, 400, 500, 600, 800, 900 и 1000°С в течение 24 ч при каждой температуре. Исследования отожженных частиц с помощью РЭМ показали, что с ростом температуры отжига диаметр и толщина оболочек полых частиц обоих типов уменьшаются. Частицы типа I сохраняют целостность и сферичность оболочек в интервале 100–900°С (рис. 3а–3г). Полые частицы II типа демонстрируют иное поведение при термообработке (рис. 3д–3з). Они сохраняют сферическую форму до температуры нагрева 100°С. При 150°С у некоторых частиц появляются прогибы оболочки (рис. 3д). С повышением температуры отжига до 500°С доля деформированных частиц увеличивается, и при дальнейшем увеличении температуры практически не меняется (рис. 3ж, 3з).
На вставках на рис. 4в показаны деформированные (слева) и недеформированные (справа) частицы типа II в увеличенном масштабе. Микроструктура оболочки частицы типа I (рис. 4б) выглядит более однородной по сравнению с микроструктурой оболочки частицы типа II (рис. 4г). Размеры областей с разной плотностью в частицах II типа достигают 5–8 нм. Возможно, более однородная структура оболочки частиц типа I является причиной ее более высокой механической прочности и объясняет отсутствие деформаций.
Рис. 4.
ПЭМ-изображения полых частиц диоксида кремния типа I (а, б) и типа II (в, г) после отжига при температуре 600°С в течение 24 ч.
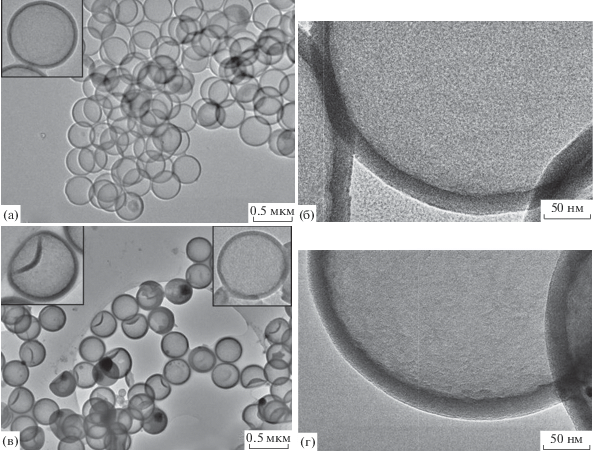
На графиках изменения диаметров частиц I и II типов от температуры в интервале 20–200°С (рис. 5а) показаны пунктирными линиями, так как в этом интервале температур невозможно указать причину изменения диаметра частиц: тепловое влияние пучка электронов микроскопа или предварительная термообработка. В интервале 100–500°С происходит резкое уменьшение диаметров частиц, после чего вплоть до температуры 900°С диаметры частиц изменяются незначительно. Частицы II типа претерпевают несколько большую усадку. В исследуемом интервале температур общее уменьшение диаметров частиц II типа составляет ~30%, а частиц I типа – ~25%. В [17] авторы также отмечают усадку частиц “ядро–оболочка” полистирол–SiO2 в среднем на 18% при нагреве до 450°С. Это хорошо согласуется с данными для частиц типа I. В [18] показано, что после отжига при температуре 500°С полые частицы, оболочки которых были синтезированы с использованием аминокислоты (L-лизин) в качестве катализатора, уменьшили свой размер на ~12%. В настоящих экспериментах частицы, оболочки которых синтезировали с использованием L-аргинина (тип II), при температурах выше 500°С претерпевали усадку ~30%. Такую разницу можно объяснить использованием различных прекурсоров диоксида кремния. Авторы [18] для получения кремнеземной оболочки использовали тетраэтилортосиликат (ТЭОС). Как показали авторы [19], SiO2-оболочки на полистироловых темплатах, полученные из ТЭОС, были более плотными в сравнении с оболочками, полученными из смеси ТЭОС–винилтриэтоксисилан (ВТЭС). Авторы объясняют это тем, что все четыре группы, присоединенные к атому Si в молекуле ТЭОС, гидролизуемые. В молекуле ВТЭС могут гидролизоваться только три этоксигруппы, связанные с атомом Si. Винильная группа в реакцию гидролиза не вступает и, по мнению авторов, при дальнейшей термообработке может быть причиной дополнительной пористости кремнеземной оболочки. Таким образом, молекула ВТЭС выступает не только как прекурсор кремнезема, но и как пороген. Наличие винильной группы в структуре ВТМС, используемого в синтезе, может быть причиной формирования менее плотной оболочки из диоксида кремния, чем при использовании ТЭОС в качестве прекурсора кремнезема.
Рис. 5.
Зависимость диаметра частиц типа I (1) и II (2) от температуры отжига в течение 24 ч (а) и от продолжительности отжига при температуре 500°С (б).
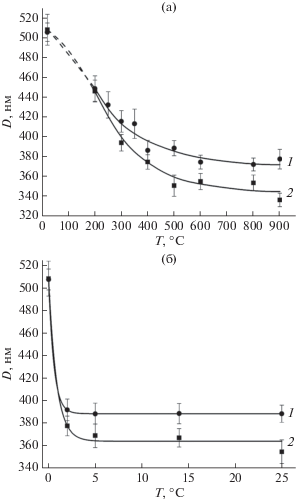
Дополнительно была оценена кинетика процесса усадки частиц обоих видов от времени отжига при температуре 500°С (рис. 5б). Из графика видно, что процесс уменьшения диаметра частиц обоих типов завершается примерно через 3 ч. Исходя из вышеизложенного и учитывая практически равную толщину оболочек исследованных частиц типов I и II (~30 нм), можно предположить, что начальная плотность оболочек частиц типа II меньше, чем частиц типа I. Так как при температурах отжига выше 500°С дальнейшая усадка частиц не наблюдается, можно предположить, что плотность аморфного кремнезема достигает своего максимального значения (2.22 г/см3). Расчеты, произведенные с учетом этого предположения, показывают, что плотность оболочек исходных частиц типа I составляла 0.91 г/см3, а типа II – 0.76 г/см3. Соответственно, величина исходной пористости оболочек может достигать значений ~59% для частиц типа I и ~67.5% для частиц типа II. Большую усадку (большую расчетную исходную пористость) частиц II типа можно объяснить тем, что L-аргинин в ходе синтеза адсорбируется кремнеземной оболочкой и является причиной дополнительной пористости оболочки после его удаления (температура разложения L-аргинина ~240°C).
При температуре отжига ~1000°С происходит потеря сферической формы и спекание частиц обоих типов (рис. 6а, 6в). Исследования с помощью рентгеновской дифракции показывают, что частицы типа I при 1000°С переходят в кристаллическую фазу (α-кристобалит SiO2) (рис. 6б), а частицы типа II при этой температуре остаются преимущественно аморфными (рис. 6г).
ЗАКЛЮЧЕНИЕ
В работе синтезированы полые частицы диоксида кремния темплатным методом на основе сферических частиц ПММА в качестве шаблона с использованием двух катализаторов: гидроксида аммония (тип I) и L-аргинина (тип II). Сферические частицы ПММА диаметром ~440 нм были синтезированы эмульсионным способом. На их поверхностях в ходе гидролиза ВТМС были сформированы оболочки диоксида кремния толщиной ~30 нм. Удаление полимерных ядер осуществляли путем термического разложения ПММА до мономера при температурах выше 200°С. Установлено, что оболочки диоксида кремния, синтезированные с использованием гидроксида аммония в качестве катализатора, имеют большую плотность и механическую прочность, чем оболочки, полученные с использованием L-аргинина. Сферическая форма SiO2-оболочек частиц, синтезированных с использованием гидроксида аммония, сохраняется при отжигах в температурном диапазоне 100–900°C. Для части полых SiO2-частиц, синтезированных с использованием L-аргинина, при нагреве выше 150°С наблюдается деформация в виде вмятин. Частицы двух типов демонстрируют различную усадку при термообработке. В ходе обработки при температуре 900°С в течение 24 ч диаметр полых SiO2-частиц типa I уменьшается на 25%, а частиц типа II – на 30%. На основании полученных данных была проведена оценка исходной пористости оболочек для частиц двух типов, которая составила ~59% (частицы типа I) и ~67.5% (частицы типа II). Выявленные особенности уплотнения кремнеземной оболочки в процессе термообработки позволяют регулировать пористость оболочки полой частицы в широком диапазоне, что открывает дополнительные возможности в областях создания микрокапсул для биомедицинских применений, нанореакторов для катализа и при разработке новых композиционных материалов с улучшенными механическими и теплоизолирующими свойствами.
Список литературы
Bao Y., Shi C., Wang T., Li X., Ma J. // Micropor. Mesopor. Mater. 2016. V. 227. P. 121. https://doi.org/10.1016/j.micromeso.2016.02.040
Kubota Y., Yamaguchi H., Yamada T., Inagaki S., Sugi Y., Tatsumi T. // Top Catal. 2010. V. 53. № 7–10. P. 492. https://doi.org/10.1007/s11244-010-9477-9
Liu N., Zhao S., Yang Z., Liu B. // ACS Appl. Mater. Interfaces. 2019. V. 11. № 50. P. 47008. https://doi.org/10.1021/acsami.9b18355
Zhu Y., Shi J., Shen W., Dong X., Feng J., Ruan M., Li Y. // Angew. Chem. Int. Ed. 2005. V. 44. P. 5083. https://doi.org/10.1002/anie.200501500
Hu. J., Chen M., Fang X., Wu L. // Chem. Soc. Rev. 2011. V. 40. P. 5472. https://doi.org/10.1039/c1cs15103g
Liu J., Liu F., Gao K., Wu J., Xue D. // J. Mater. Chem. 2009. V. 19. P. 6073. https://doi.org/10.1039/b900116f
Gao T., Sandberg L.I.C., Jelle B.P., Gustavsen A. // Fuelling the Future: Advances in Science and Technologies for Energy Generation, Transmission and Storage / Ed. Mendez-Vilas A.A. Boca Raton: Brown Walker Press, 2012. P. 535.
Yamada Y., Mizutani M., Nakamura T., Yano K. // Chem. Mater. 2010 V. 22. P. 1695. https://doi.org/10.1021/cm9031072
Castillo S.I.R., Ouhajji S., Fokker S., Erné B.H., Schneijdenberg C.T.W.M., Thies-Weesie D.M.E., Philipse A.P. // Micropor. Mesopor. Mater. 2014. V. 195. P. 75. https://doi.org/10.1016/j.micromeso.2014.03.047
Ghosh Ch.R., Paria S. // Chem. Rev. 2012. V. 112. P. 2373. https://doi.org/10.1021/cr100449n
Zhu A., Shi Zh., Cai A., Zhao F., Liao T. // Polymer Testing. 2008. V. 27. P. 540. https://doi.org/10.1016/j.polymertesting.2007.11.005
Choi W.S., Koo H.Y., Kim D.-Y. // Langmuir. 2008. V. 24. P. 4633. https://doi.org/10.1021/la703955g
Liu H., Li H., Ding Z., Fu A., Wang H., Guo P., Yu J., Wang C., Zhao X. // J. Cluster Sci. 2012. V. 23. P. 273. https://doi.org/10.1007/s10876-011-0427-x
Huang Z.F., Qu X.Y., Chen Zh. // J. Appl. Polym. Sci. 2015. V. 132. № 19. P. 41919. https://doi.org/10.1002/APP.41919
Mostafa H.Y., Hussain A.I., EL-Masry A.M., Maher A. // Polymer-Plastics Technol. Eng. 2017. V. 56. № 4. P. 411. https://doi.org/10.1080/03602559.2016.1227842
Troitskii B.B., Lokteva A.A., Denisova V.N., Novikova M.A., Konev A.N., Fedyushkin I.L. // Russ. J. Appl. Chem. 2016. V. 89. P. 1132. https://doi.org/10.1134/S1070427216070132
Chu L., Zhang X., Niu W., Wu S., Ma W., Tang B., Zhang Sh. // J. Mater. Chem. C. 2019. V. 7. P. 7411. https://doi.org/10.1039/c9tc01992h
Nandiyanto A.B.D., Akane Y., Ogi T., Okuyama K. // Langmuir. 2012. V. 28. P. 8616. https://doi.org/10.1021/la301457v
Bao Y., Yang Y., Shi C., Ma J. // J. Mater. Sci. 2014. V. 49. P. 8215. https://doi.org/10.1007/s10853-014-8530-7
Дополнительные материалы отсутствуют.
Инструменты
Поверхность. Рентгеновские, синхротронные и нейтронные исследования