Поверхность. Рентгеновские, синхротронные и нейтронные исследования, 2021, № 12, стр. 85-90
Структурно-морфологические характеристики поверхностей трения литых эндогенно-армированных алюмоматричных композитов
Е. С. Прусов a, В. Б. Деев b, c, *, А. В. Аборкин a, Э. Х. Ри d, Е. М. Рахуба e
a Владимирский государственный университет
им. Александра Григорьевича и Николая Григорьевича Столетовых
600000 Владимир, Россия
b Wuhan Textile University
0027 Wuhan, 4300 00-4304 00 China
c Национальный исследовательский технологический университет “МИСиС”
119049 Москва, Россия
d Тихоокеанский государственный университет
680035 Хабаровск, Россия
e Институт легких материалов и технологий РУСАЛ
119049 Москва, Россия
* E-mail: deev.vb@mail.ru
Поступила в редакцию 14.12.2020
После доработки 22.03.2021
Принята к публикации 27.03.2021
Аннотация
Изучено влияние температурно-временнóй обработки расплавов Al–Mg–Si на трибологическое поведение литых эндогенно-армированных алюмоматричных композитов Al–Mg2Si и структурно-морфологические параметры поверхностей трения. Показано, что температурно-временнáя обработка расплавов в рациональных режимах приводит к измельчению включений эндогенной армирующей фазы Mg2Si и увеличению их общего количества, способствуя повышению трибологических характеристик алюмоматричных композитов Al–Mg2Si. Методами растровой электронной микроскопии и энергодисперсионного анализа установлено, что на поверхности трения формируется переходный слой, армированный микро- и наночастицами дебриса. Эти частицы обеспечивают градиент механических свойств по глубине, снижая износ переходного слоя. Суммарный анализ закономерностей изменения морфологии и элементного состава поверхностей трения алюмоматричных композитов свидетельствует о сложном характере износа пары трения с присутствием адгезионной, окислительной и абразивной составляющих.
ВВЕДЕНИЕ
Алюмоматричные композиционные материалы, армированные дисперсными частицами тугоплавких неорганических соединений, привлекают внимание исследователей в связи с широким спектром возможных сочетаний механических и трибологических свойств [1]. Однако промышленное использование этих перспективных материалов ограничивается несовершенством технологических процессов их получения, основанных на вводе экзогенных армирующих частиц в матричные расплавы путем механического замешивания. Такие процессы, как правило, сопровождаются окислением и газонасыщением расплавов, коагуляцией и отторжением армирующих частиц вследствие их плохой смачиваемости [2]. Одним из решений обозначенных проблем являются литейно-металлургические технологии эндогенного армирования, реализация которых возможна в системах эвтектического типа, например, Al–Mg–Si [3]. Образующееся в таких системах соединение Mg2Si может эффективно использоваться в качестве армирующей фазы при получении литейных алюмоматричных композиционных материалов, поскольку имеет высокую температуру плавления, малую плотность, высокую твердость, низкий коэффициент термического расширения и высокий модуль упругости [4].
Значительными преимуществми алюмоматричных композитов Al–Mg2Si являются простота их получения и низкая стоимость исходных компонентов. Композиционные материалы Al–Mg2Si характеризуются прочной межфазной связью между матрицей и армирующими частицами, а также отличаются повышенной термодинамической стабильностью, лучшим распределением и дисперсностью армирующих компонентов в сравнении с экзогенно-армированными композитами [5–7]. Однако в результате использования традиционных литейно-металлургических процессов первичные кристаллы Mg2Si, как правило, приобретают грубую морфологию, что приводит к необходимости применения модифицирующей обработки. Для управления структурно-морфологическими параметрами литых композитов Al–Mg2Si к настоящему времени опробованы химические способы модифицирования за счет ввода в расплавы таких элементов, как неодим, висмут, стронций, церий [8–10]. Однако использование дорогостоящих модифицирующих присадок, с одной стороны, может приводить к существенному повышению себестоимости композитов, а с другой стороны, сопровождается накоплением примесей в материалах при повторных переплавах в процессах рециклинга.
В последние годы возрастает интерес исследователей к разработке новых методов получения модифицированной структуры литейных сплавов и композитов за счет наложения различных физических воздействий на их расплавы [11]. В частности, в [12, 13] было показано значительное модифицирующее воздействие ультразвуковой и вибрационной обработки расплавов на изменение дисперсности и морфологии армирующих частиц Mg2Si. Кроме того, сообщают о положительных эффектах поверхностной электрофизической обработки на структуру и трибологическое поведение алюминиевых сплавов [14, 15]. Как было показано ранее, одним из эффективных и экономичных способов управления морфологией и размерами частиц Mg2Si может быть температурно-временнáя обработка расплавов системы Al–Mg–Si [16–18].
Настоящая работа посвящена изучению влияния температурно-временнóй обработки расплавов Al–Mg–Si на трибологическое поведение алюмоматричных композитов Al–Mg2Si и структурно-морфологические параметры изношенных поверхностей.
МЕТОДИКА
Для получения алюмоматричных композитов использовали чистые компоненты: алюминий (≥99.99% Al), магний (≥99.9% Mg), кремний (≥99.0% Si). Компоненты дозировали согласно расчету шихты на объем плавки 500 г, исходя из номинального состава Al + 12.5 мас. % Mg + + 6.7 мас. % Si, что соответствовало содержанию фазы Mg2Si в синтезируемом композите 18 мас. %. Плавку проводили в алундовых тиглях в электрической печи сопротивления. Вначале расплавляли алюминий и перегревали до 720°С, затем добавляли подогретые до 150°С завернутые в алюминиевую фольгу навески магния и кремния с последующим перемешиванием расплава графитовым стержнем. После полного растворения введенных компонентов расплав перегревали до температуры 900°С и выдерживали в течение различного времени (15, 30, 45 и 60 мин) для проведения температурно-временнóй обработки. Температурные режимы плавки контролировали в течение всего эксперимента погружной термопарой ХА с использованием регистратора ВиЭР-104К. После выдерживания снимали с поверхности оксидные плены и разливали расплав при температуре 720°С в вертикальную медную изложницу для получения слитков диаметром 20 мм и высотой 100 мм. Температура изложницы была постоянной (25°С) для всех изготовленных образцов для обеспечения идентичных условий охлаждения. Из полученных слитков вырезали образцы на расстоянии 15 мм от нижнего торца слитка для исследования структуры и трибологических характеристик.
Микроструктуру образцов алюмоматричных композитов изучали в литом состоянии на нетравленых шлифах с помощью цифрового металлографического микроскопа Raztek MRX9-D (Россия). Металлографические образцы готовили по стандартной процедуре. Фазовый состав образцов определяли на рентгеновском дифрактометре D8 ADVANCE (Bruker AXS, Германия) в геометрии Брэгга–Брентано (CuKα-излучение, λ = 1.5406 Å, скорость вращения гониометра 4 град/мин, шаг 2θ 0.05°). Идентификацию фаз осуществляли с помощью программного комплекса Diffrac.Suite на основе базы данных ICDD PDF-2.
Для оценки потенциала использования разработанных композитов в реальных узлах трения проводили сопоставительные трибологические испытания с фрактографическим картированием поверхностей трения с применением растрового электронного микроскопа (РЭМ) TESCAN VEGA3 (Tescan Orsay Holding) с энергодисперсионной приставкой-микроанализатором INCA Energy 15 013 X-act производства Oxford Instruments. Испытания опытных образцов на трение и износ проводили по схеме “неподвижный шарик (ШХ15)–вращающийся диск (образец)” на автоматизированной машине трения Tribometer (CSM Instruments, Швейцария) в соответствии с международными стандартами ASTM G99-959 и DIN 50324. Образцы для испытаний готовили в форме дисков диаметром 20 и высотой 5 мм. Трибологические испытания проводили при нагрузке на индентор 5 Н и линейной скорости вращения образцов 40 см/с в условиях сухого трения. Путь трения во всех опытах составил 500 м.
РЕЗУЛЬТАТЫ И ИХ ОБСУЖДЕНИЕ
Структура композитов Al–Mg2Si в литом состоянии при различном времени выдерживания расплава в процессах его температурно-временнóй обработки приведена на рис. 1. Характерная микроструктура композитов Al–Mg2Si представлена литой матрицей (алюминиевый α-твердый раствор) и частицами первичной фазы Mg2Si. Увеличение продолжительности выдерживания расплава при температурно-временнóй обработке от 15 до 30 мин приводит к значительному уменьшению средних размеров частиц Mg2Si и увеличению их количества. При дальнейшем увеличении длительности выдерживания до 45 мин происходит огрубление морфологии кристаллов Mg2Si и рост их размеров с образованием сложных дендритоподобных комплексов, а выдерживание в течение 60 мин приводит к резкому снижению общего количества частиц в структуре материала, по-видимому, вследствие образования эвтектических колоний в междендритных областях.
Рис. 1.
Структура алюмоматричных композитов Al–Mg2Si в литом состоянии при выдерживании расплава при 900°С в течение 15 (а), 30 (б), 45 (в) и 60 (г) мин.
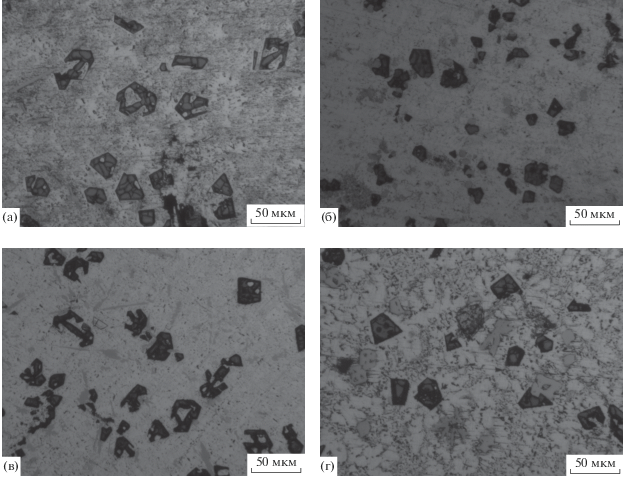
Дифрактограммы литых образцов, полученных при выдерживании в течение 15 и 60 мин, приведены на рис. 2. Рентгеноструктурный анализ выявил в образцах, полученных при выдерживании расплава в течение 15 мин, только две фазы, а именно α-Al и Mg2Si (рис. 2а), в то время как выдерживание при 900°С в течение 60 мин приводит к появлению оксида магния MgO в структуре образцов в заметных количествах (рис. 2б).
Рис. 2.
Дифрактограммы образцов композитов Al–Mg2Si, полученных при температурно-временнóй обработке расплава в течение 15 (а) и 60 мин (б).
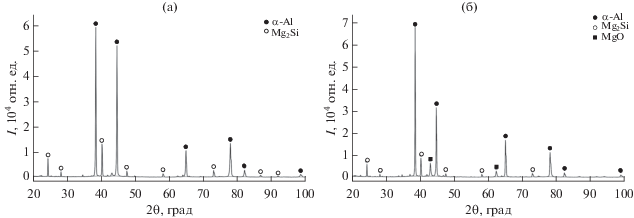
После трибологических испытаний были изучены треки износа на поверхности образцов композитов, полученных в различных условиях температурно-временнóй обработки расплава. Фрактографические изображения поверхностей трения приведены на рис. 3. Сравнительный анализ РЭМ-изображений показывает, что топография треков износа образцов с различным временем изотермического выдерживания качественно одна и та же. Во всех случаях наблюдается характерная морфология с “гребнями”, формирование которых происходит в условиях пластической деформации мягкой матрицы перед движущимся более твердым стальным контртелом и пластической сварки локальных участков контактирующих поверхностей, образовавшихся вследствие молекулярного взаимодействия. Износ в данном случае характеризовался локальным адгезионным схватыванием контактирующих поверхностей с последующим когезионным разрушением зон контакта. Образцы, полученные при выдерживании расплава в течение 30 и 45 мин, демонстрируют более высокие показатели задиростойкости в условиях сухого трения, что обусловливается более благоприятными структурно-морфологическими характеристиками синтезированных композитов. Также характерным является наличие микроцарапин на поверхности трения, ориентированных в направлении скольжения, что свидетельствует о протекании процессов микрорезания в зоне контакта. В роли абразива, по-видимому, выступают окисленные частицы матричного алюминиевого слава. На РЭМ-изображениях отчетливо фиксировали микро- и наноразмерные частицы дебриса.
Рис. 3.
РЭМ-изображения поверхностей изнашивания после трибологических испытаний литых образцов алюмоматричных композитов, полученных при выдерживании расплава при температуре 900°С в течение 15 (а), 30 (б), 45 (в) и 60 мин (г).
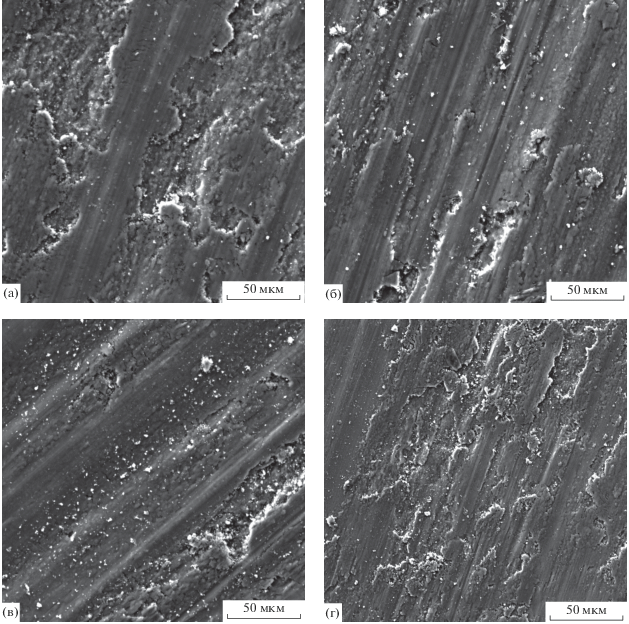
Энергодисперсионный рентгеновский микроанализ, результаты которого представлены в виде картирования поверхности трения, а также в отдельных точках, выявляет во всех образцах как элементы алюмоматричного композита, так и элементы, входящие в состав стального контртела. Для примера на рис. 4 приведены результаты съемки поверхности трения литого образца алюмоматричного композита Al–Mg2Si, полученного при выдерживании расплава при температуре 900°С в течение 15 мин, с использованием характеристического излучения. Во всех случаях поверхности треков трения богаты кислородом. Это обусловлено окислением ювенильных поверхностей, образующихся при деформации за счет фрикционного нагрева при сухом скольжении. Образование слоев оксидов обеспечивает градиент механических свойств по глубине, снижая износ переходного слоя. Микроэлементный анализ частиц дебриса показывает, что в основном они состоят из оксидов алюминия, магния и железа.
Рис. 4.
Съемка поверхности трения литого образца алюмоматричного композита Al–Mg2Si, полученного при выдерживании расплава при температуре 900°С в течение 15 мин, с использованием характеристического излучения.
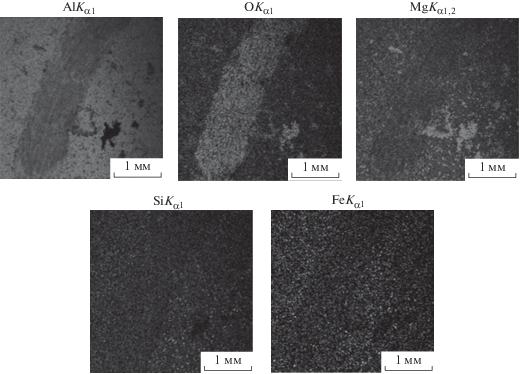
Таким образом, температурно-временнáя обработка расплавов является эффективным способом управления структурно-морфологическими параметрами литых алюмоматричных композитов системы Al–Mg2Si, открывающим возможности для вариации свойств материала как в объеме, так и на поверхности. Полученные результаты свидетельствуют о перспективности применения предложенных решений с позиций формирования заданных эксплуатационных характеристик поверхности (износостойкости, задиростойкости, прирабатываемости и других характеристик), что практически значимо для изготовления изделий трибоузлов из алюмоматричных композитов.
ЗАКЛЮЧЕНИЕ
Применение температурно-временнóй обработки расплавов системы Al–Mg–Si в рациональных режимах (30 мин при T = 900°С) приводит к измельчению включений эндогенной армирующей фазы Mg2Si и увеличению их общего количества, способствуя повышению трибологических характеристик алюмоматричных композитов Al–Mg2Si. Показано, что увеличение продолжительности изотермического выдерживания расплава до 45 мин сопровождается огрублением морфологии кристаллов Mg2Si и формированием сложных дендритоподобных комплексов, а выдерживание в течение 60 мин приводит к резкому снижению доли армирующих частиц и значительному окислению матрицы. При изучении поверхностей трения методами РЭМ и энергодисперсионного анализа установлено, что на поверхности трения формируется переходный слой, армированный микро- и наноразмерными частицами дебриса. Наличие данных частиц обеспечивает градиент механических свойств по глубине, снижая износ переходного слоя. Суммарный анализ закономерностей изменения морфологии и элементного состава поверхностей трения алюмоматричных композитов свидетельствует о сложном характере износа пары трения с присутствием адгезионной, окислительной и абразивной составляющих.
Список литературы
Kumar V.M., Venkatesh C.V. // Mater. Res. Express. 2019. V. 6. № 7. P. 072001. https://doi.org/10.1088/2053-1591/ab0ee3
Wu J., Wang D., Gui M., Cui Y., Yuan G. // Jinshu Xuebao/Acta Metallurgica Sinica. 1999. V. 35. № 1. P. 103.
Chen X., Liu H., Zhan Y., Tang H. // Int. J. Mater. Res. 2016. V. 107. № 9. P. 842. https://doi.org/10.3139/146.111405
Biswas P., Mondal M.K., Roy H., Mandal D. // Canad. Metal. Quarterly. 2017. V. 56. P. 340. https://doi.org/10.1080/00084433.2017.1345058
Qin Q.D., Zhao Y.G., Zhou W. // Wear. 2008. V. 264. P. 654. https://doi.org/10.1016/j.wear.2007.05.008
Barenji R.V. // China Foundry. 2018. V. 15. P. 66. https://doi.org/10.1007/s41230-018-7095-5
Gao Q., Wu S., Lu S., Duan X., Zhong Z. // J. Alloys Compd. 2015. V. 651. P. 521. https://doi.org/10.1016/j.jallcom.2015.08.162
Wu X.-F., Zhang G.-G., Wu F.-F. // Rare Metals. 2013. V. 32. №. 3. P. 284. https://doi.org/10.1007/s12598-013-0030-4
Wu X., Zhang G., Wu F. // Trans. Nonferrous Met. Soc. China. 2013. V. 23. № 6. P. 1532. https://doi.org/10.1016/S1003-6326(13)62627-8
Qin Q., Li W. // Mater. Trans. 2016. V. 57. № 5. P. 618. https://doi.org/10.2320/matertrans.M2015334
Deev V.B., Prusov E.S., Kutsenko A.I. // Metall. Ital. 2018. V. 110. № 2. P. 16.
Ivanov Y.F., Alsaraeva K.V., Gromov V.E., Popova N.A., Konovalov S.V. // J. Surf. Invest.: X-Ray, Syncrhotron Neutron Tech. 2015. V. 9. № 5. P. 1056. https://doi.org/10.1134/S1027451015050328
Ivanov Yu.F., Gromov V.E., Konovalov S.V., Zagulyaev D.V., Petrikova E.A., Semin A.P. // Prog. Phys. Met. 2018. V. 19. № 2. P. 195. https://doi.org/10.15407/ufm.19.02.195
Zhang J., Zhao Y., Xu X., Liu X. // Trans. Nonferr. Met. Soc. China. 2013. V. 23. № 10. P. 2852. https://doi.org/10.1016/S1003-6326(13)62806-X
Saffari S., Akhlaghi F. // Solid State Phenom. 2014. V. 217–218. P. 389. https://doi.org/10.4028/www.scientific.net/ SSP.217-218.389
Nordin N.A., Abubakar T., Hamzah E., Farahany S., Ourdjini A. // Procedia Eng. 2017. V. 184. P. 595. https://doi.org/10.1016/j.proeng.2017.04.144
Prusov E., Deev V., Rakhuba E. Effect of Superheat Melt Treatment on Structure and Mechanical Properties of In-Situ Aluminum Matrix Composites. // Proc. 27th Int. Conf. on Metallurgy and Materials METAL-2018. Brno, 2018. P. 1358.
Deev V., Prusov E., Rakhuba E. // Mater. Sci. Forum. 2019. V. 946. P. 655. https://doi.org/10.4028/www.scientific.net/MSF.946.655
Дополнительные материалы отсутствуют.
Инструменты
Поверхность. Рентгеновские, синхротронные и нейтронные исследования