Поверхность. Рентгеновские, синхротронные и нейтронные исследования, 2021, № 12, стр. 79-84
Изучение формирования пленки вторичных структур при скольжении пары трения “алюминиевый сплав–сталь”
Т. И. Муравьева a, *, И. В. Шкалей a, **, О. О. Щербакова a, Д. Л. Загорский b
a Институт проблем механики им. А.Ю. Ишлинского РАН
119526 Москва, Россия
b Российский государственный университет нефти и газа
(Национальный исследовательский университет) им. И.М. Губкина
119991 Москва, Россия
* E-mail: muravyeva@list.ru
** E-mail: ioann_shiva@list.ru
Поступила в редакцию 25.05.2021
После доработки 27.06.2021
Принята к публикации 30.06.2021
Аннотация
Изучены процессы, происходящие на контактной поверхности при трении многокомпонентного антифрикционного алюминиевого сплава Al–20% Sn–5% Si (колодка) по стали марки Ст45 (ролик), в частности, эффект самосмазывания. Использована комплексная методика микроскопических исследований поверхности, включающая растровую электронную и сканирующую зондовую микроскопию. Установлена корреляция между данными, полученными двумя методами микроскопии. Изучена как исходная поверхность образцов, так и поверхность после трибологических испытаний в экстремальных условиях трения (без смазки). Оценены структурные изменения поверхности при трении. Установлено, что в процессе трения происходит выделение мягкой фазовой составляющей сплава и массоперенос химических элементов с одной контактной поверхности на другую. Изучение поверхностей контактной пары позволило оценить особенности массопереноса между колодкой и роликом. Выявлено, что при минимальных условиях нагружения эффект самосмазывания проявляется незначительно и происходит интенсивный перенос железа с поверхности ролика на поверхность колодки. При увеличении нагрузки (в определенных диапазонах) выделение мягкой фазы усиливается, что изменяет характер поверхности и протекающие на ней процессы. Показано, что в результате сложных механических и физико-химических процессов на контактной поверхности формируется пленка вторичных структур. Эта пленка, в зависимости от условий трения, может играть различную роль: не только защищать поверхность от разрушения, но и способствовать задиру.
ВВЕДЕНИЕ
Улучшение эксплуатационных свойств материалов, используемых в узлах трения, в частности в подшипниках скольжения, является актуальной задачей в машиностроении. Основным материалом для изготовления таких узлов обычно служит дорогостоящая бронза [1, 2]. Однако в последнее время в качестве альтернативы бронзе все чаще используют более дешевые алюминиевые сплавы [3–8], в которых удачно сочетаются эксплуатационные и технологические свойства. Эти сплавы обладают достаточной усталостной прочностью, коррозионной стойкостью в маслах, имеют сравнительно высокую задиростойкость и хорошие трибологические свойства [9, 10]. Также важным является и экологический аспект – при использовании алюминиевых сплавов заметно уменьшаются вредные выделения в окружающую среду [11]. Создание новых алюминиевых сплавов возможно путем оптимального подбора легирующих элементов. Научной основой оптимизации составов сплавов являются фазовые диаграммы многокомпонентных систем [12].
Основной особенностью антифрикционных сплавов является выделение на поверхности в процессе трения (при разогреве поверхности и деформации зерен в приповерхностных слоях алюминиевой матрицы) мягкой фазовой составляющей [13, 14], наличие которой обеспечивает постоянную структурную самоорганизацию, сопровождающуюся формированием пленки вторичных структур на поверхности. Изучению новых алюминиевых сплавов посвящено множество работ. Так, в [15–18] изучены антифрикционные материалы на алюминиевой основе, используемые в подшипниках скольжения, и проведена оценка их трибологических свойств. Исследована структура, шероховатость и элементный состав контактной поверхности пар трения скольжения. Колодку изготавливали из алюминиевых антифрикционных сплавов А020-1, АО10С2. В качестве контртела использовали ролик из высокопрочного чугуна марки ВЧ-70. Испытания проводили со смазкой стандартным маслом марки М14В2. На основании проведенных исследований было показано, что в активной трибологической области создается значительная гетерогенность структуры и состава, которые в значительной степени отличаются от исходных. Проведен анализ особенностей структурного механизма массопереноса (между колодкой и роликом), результатом которого было формирование пленки вторичных структур на контактной поверхности при работе узла трения в нормальных условиях (со смазкой).
Целью настоящей работы было изучение формирования пленки вторичных структур на контактной поверхности в процессе трибологических испытаний в экстремальных условиях (в режиме без смазки). Для исследования этого процесса в работе был выбран аналогичный экспериментальный сплав состава Al–20% Sn–5% Si. Предполагалось, что высокое содержание олова в сплаве будет способствовать выделению большого количества мягкой фазовой составляющей на контактной поверхности. Кремний добавляли в его состав с целью улучшения литейных свойств. При концентрации кремния 5%, как правило, достигается наилучший баланс между механическими и технологическими свойствами.
ОБРАЗЦЫ И МЕТОДЫ
Объектом исследования служил экспериментальный антифрикционный сплав системы Al–20% Sn–5% Si с примесями (менее 0.05%) меди, свинца и висмута. Сплав был изготовлен методом литья в графитовые изложницы в НИТУ “МИСиС” в рамках проведения совместных научно-исследовательских работ.
Условия эксплуатации моделировали на трибометре Т-05 по схеме колодка–ролик. Колодка была изготовлена из исследуемого сплава, а ролик – из стали марки Ст45. Испытания проводили при различных давлениях (0.3, 0.5 МПа) и скоростях скольжения (1, 2 м/с). Изменяя эти величины, задавали различные условия эксплуатации узла трения. Во время испытаний применяли экспресс-методику – без смазки. С одной стороны, сокращалось время проведения эксперимента, а с другой – появлялась возможность моделировать экстремальные условия трения.
Для изучения исходной структуры сплава готовили шлифы. Заготовки шлифов фиксировали в самотвердеющей пластмассе SpeciFix-20 Kit, дальнейшую шлифовку и полировку проводили с использованием комплекса TegraPol-25 и TegraForce-5 (компания Struers).
Поверхность сплава до и после трибологических испытаний изучали с использованием комплекса методов электронной и зондовой микроскопии, который дал возможность получить более полную информацию о состоянии поверхности. Помимо топографии электронная микроскопия позволила изучить элементный состав, а зондовая – пространственную геометрию поверхности.
Электронно-микроскопические исследования проводили в растровом электронном микроскопе (РЭМ) FEI Quanta-650. Специальная подготовка образцов не требовалась. Исследования проводили в высоком вакууме с использованием детектора вторичных электронов. Ускоряющее напряжение составляло 25 кВ, увеличение – от ×300 до ×1000. Для детальных исследований элементного состава применяли аналитическое оборудование EDAX, включающее энергодисперсионный микроанализатор.
Поверхность с нанометровым разрешением исследовали в сканирующем зондовом микроскопе (СЗМ) Smart SPMTM (компания AIST-NT) в режиме тейпинга. Применяли кантилевер AIST-NT, fpN10 с жесткостью балки 10–20 Н/м, резонансной частотой 200–300 кГц и радиусом кривизны острия около 20 нм. Максимальное поле сканирования составляло 100 × 100 мкм. Особенностью данного микроскопа является наличие встроенной оптической камеры для предварительного выбора нужного участка поверхности.
РЕЗУЛЬТАТЫ И ИХ ОБСУЖДЕНИЕ
Методами РЭМ и СЗМ были исследованы одни и те же области исходных поверхностей образцов. Изображения представлены на рис. 1, а соответствующий элементный состав и параметры профилей секущих линий приведены в табл. 1.
Рис. 1.
Исходная поверхность образца: а – РЭМ-изображение (стрелками указаны области химического анализа); б – СЗМ-изображение (указаны секущие линии).
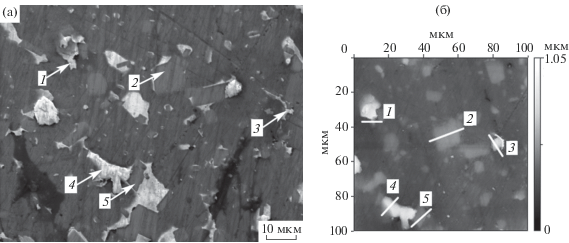
Таблица 1.
Химический состав и параметры рельефа поверхности образца
№ участков и секущих | Содержание элементов, мас. % | Максимальная высота фаз, нм | ||
---|---|---|---|---|
Al | Si | Sn | ||
1 | 3.53 | – | 96.47 | 262 |
2 | 1.58 | 98.42 | – | 212 |
3 | 1.22 | 0.99 | 97.79 | 421 |
4 | 1.19 | – | 98.81 | 565 |
5 | 1.58 | 91.72 | 6.70 | 219 |
Анализ полученных результатов позволил оценить рельеф и состав поверхности. Применение метода электронной микроскопии дало возможность идентифицировать различные фазы на поверхности алюминиевой матрицы. Так, светлые включения представляют собой мягкую фазовую составляющую сплава – олово. Другая фаза – кремний. Однако на РЭМ-изображениях данный химический элемент слабо различим (это связано с близостью атомных номеров Al и Si). Использование зондовой микроскопии позволило визуализировать кремний на поверхности. Кроме того, данным методом микроскопии были определены пространственные характеристики поверхности. Было установлено, что мягкие фазы имеют высоту профилей около 300–600 нм, а кремний – около 200 нм.
Ниже приведены результаты, полученные при исследовании поверхности образцов после трибологических испытаний. На рис. 2 показаны РЭМ-изображения, а в табл. 2 дан химический состав поверхности колодки, испытанной при давлении 0.3 МПа при скоростях 1 и 2 м/с. Из рисунка видно, что после трибологических испытаний уже при минимальных условиях нагружения (рис. 2а) на поверхности образуется рельеф, формируются продольные полосы, появляются отдельные частицы. Из результатов рентгеноспектрального анализа следует, что при скорости 1 м/с на поверхности колодки в большом количестве присутствуют железо (28.77%) и кислород (20.59%). Это свидетельствует о том, что в процессе приработки железо с поверхности стального ролика переносится на колодку. Концентрация алюминия, олова и кремния уменьшается (табл. 2). Наличие на поверхности кислорода можно объяснить активными окислительными процессами, происходящимии в контактной зоне. Эффект самосмазывания в данных условиях проявляется незначительно. Можно предположить, что разогрев контактных поверхностей в данных условиях трения недостаточен для выделения необходимого количества мягкой фазовой составляющей сплава (олова). Дальнейшие исследования показали, что при более высокой скорости скольжения (2 м/с) железо на поверхности колодки фактически отсутствует (0.17%), а содержание олова увеличивается почти в два раза.
Рис. 2.
РЭМ-изображения поверхности колодки после испытаний при давлении 0.3 МПа и скорости: а – 1; б – 2 м/с.
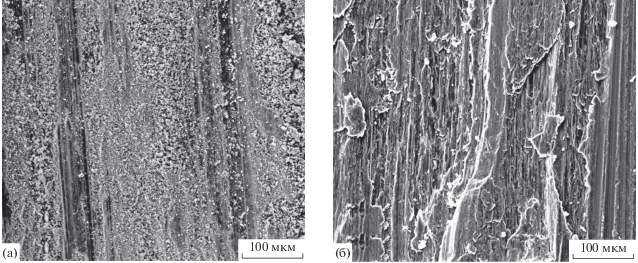
Таблица 2.
Химический состав поверхности колодки после испытаний при давлении 0.3 МПа
Скорость, м/с | Химический состав, мас. % | ||||
---|---|---|---|---|---|
O | Al | Si | Sn | Fe | |
1 | 20.59 | 38.43 | 2.85 | 9.36 | 28.77 |
2 | 1.21 | 76.91 | 6.67 | 15.04 | 0.17 |
Последующие испытания проводили при давлении 0.5 МПа. Полученные РЭМ-изображения и химический состав поверхности колодки представлены на рис. 3 и в табл. 3 соответственно. Из рис. 3 и табл. 3 следует, что топография и химический состав при данном давлении с увеличением скорости практически не меняются.
Рис. 3.
РЭМ-изображения поверхности колодки после испытаний при давлении 0.5 МПа и скорости: а – 1; б – 2 м/с.
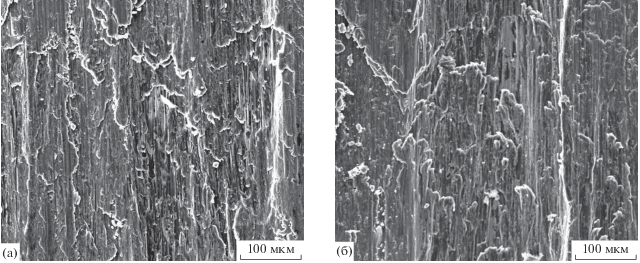
Таблица 3.
Химический состав поверхности колодки после испытаний при давлении 0.5 МПа
Скорость, м/с | Химический состав, мас. % | ||||
---|---|---|---|---|---|
O | Al | Si | Sn | Fe | |
1 | 1.01 | 74.21 | 7.97 | 16.68 | 0.13 |
2 | 1.08 | 73.76 | 8.87 | 16.11 | 0.18 |
Большой интерес представляет изучение состояние поверхности ролика. Анализ полученных данных показал, что в результате процесса микросхватывания в зоне трения происходит массоперенос химических элементов на контактных поверхностях (колодки и ролика). Кроме того, на этих поверхностях при трении протекают сложные механические и физико-химические процессы. Совокупность вышеперечисленных факторов приводит к формированию пленки вторичных структур на поверхности ролика. В случае стандартных испытаний в смазке на ролике образуется равномерно распределенная по поверхности пленка вторичных структур, защищающая поверхность от разрушения [14, 19]. В настоящей работе испытания проводили в экстремальных условиях по экспресс-методике – без смазки. Увеличение давления обусловило формирование неоднородной пленки вторичных структур и развитие макрорельефа, что могло впоследствии привести к задиру. На рис. 4 в качестве примера дано РЭМ-изображение поверхности ролика, испытанного при давлении 0.5 МПа и скорости 1 м/с. Рисунок иллюстрирует, что на светлой стальной поверхности ролика имеются темные области. Рентгеноспектральный анализ показал, что данные области содержат в своем составе химические элементы исследуемого сплава (в том числе около 18% мягкой фазы – олова). Данный факт свидетельствует о неравномерно формирующейся пленке вторичных структур на поверхности ролика.
Рис. 4.
РЭМ-изображение поверхности ролика после испытаний при давлении 0.5 МПа и скорости 1 м/с: 1 – поверхность ролика; 2 – пленка вторичных структур.
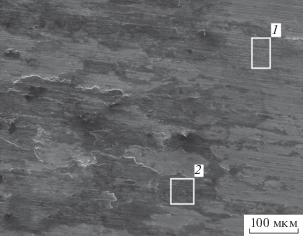
Для изучения рельефа поверхности ролика и оценки толщины этой пленки был применен метод СЗМ. Изучали области на границе “стальная поверхность ролика–пленка вторичных структур”. На рис. 5 приведено СЗМ-изображение различных областей поверхности ролика с проведенными секущими линиями и соответствующими им профилями. Толщину пленки вторичных структур оценивали по изменению профиля поверхности ролика.
Рис. 5.
Поверхности ролика после испытаний при давлении 0.5 МПа и скорости 1 м/с: а – СЗМ-изображение (слева) области 1 с профилем секущей 1 (справа); б – СЗМ-изображение (слева) области 2 с профилем секущей 2 (справа).
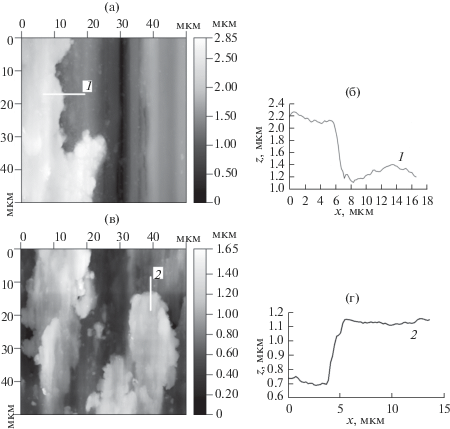
Установлено, что в первой области толщина слоя составляет около 950 нм, во второй – 424 нм. Были проведены исследования нескольких различных областей на поверхности ролика, которые показали, что толщина сформировавшейся пленки вторичных структур различна в разных областях и неравномерно распределена по поверхности ролика.
ЗАКЛЮЧЕНИЕ
Комплексные микроскопические исследования показали, что на контактных поверхностях колодки из исследуемого сплава Al–20% Sn–5% Si и ролика из стали марки Ст45 в процессе трения происходят существенные изменения. При повышении давления и температуры в зоне контакта имеет место массоперенос химических элементов с одной поверхности на другую. В результате массопереноса и других сложных механических и физико-химических процессов, протекающих в зоне контакта при трении, на поверхности стального ролика формируется пленка вторичных структур. Данная пленка в стандартных условиях испытаний (со смазкой) равномерным тонким слоем покрывает поверхность и, играя роль твердой смазки, защищает поверхность ролика от разрушения. Примененная в настоящей работе экспресс-методика (экстремальный режим – без смазки) способствовала формированию пленки неравномерной толщины и развитию макрорельефа, что в свою очередь может приводить к образованию задира (при давлении более 0.5 МПа). Также было выявлено, что на начальной стадии трибологических испытаний при скорости скольжения 1 м/с и давлении 0.3 МПа имеет место процесс “обратного переноса” железа с ролика на колодку.
Список литературы
Арзамасов Б.Н., Соловьёва Т.В., Герасимов С.А. и др. Справочник по конструкционным материалам: Справочник. М.: Изд-во МГТУ им. Н.Э. Баумана, 2005. 640 с.
Осинцев О.Е., Федоров В.Н. Медь и медные сплавы. М.: Интермет Инжиниринг, 2005. 360 с.
Dong B., Wu Zh., Wang P., Ke Ch., Liu Sh., Jie J. // J. Alloys Compds. 2021. V. 874. P. 159756.
Lucchetta M.C., Saporitia F., Audebert F. // J. Alloys Compds. 2019. V. 805. P. 709.
Guo Zh., Liu X., Xue J. // J. Alloys Compds. 2019. V. 797. P. 883.
Liu X., Zeng M.Q., Ma Y., Zhu M. // Wear. 2008. V. 265. P. 1857.
Prasad B.K. // Wear. 2004. V. 257. P. 110.
Миронов А.Е., Гершман И.С., Овечкин А.В., Гершман Е.И. // Трение и износ. 2015. Т. 15. № 5. С. 334.
Буше Н.А. Подшипники из алюминиевых сплавов. М.: Транспорт, 1974. 225 с.
Mwanza M.C., Joyce M.R., Lee K.K., Syngellakis S., Reed P.A.S. // Int. J. Fatigue. 2003. V. 25. Iss. 9–11. P. 1135.
Bertelli F., Freitas E.S., Cheung N., Arenas M.A., Conde A., Damborenea J., Garcia A. // J. Alloys Compds. 2017. V. 695. P. 3621.
Белов Н.А. Фазовый состав алюминиевых сплавов. М.: МИСиС, 2009. 392 с.
Schouwenaars R., Jacobo V.H., Ortiz A. // Wear. 2007. V. 263. Iss. 1–6. P. 727.
Щербакова О.О., Муравьева Т.И., Загорский Д.Л., Мезрин А.М., Сачек Б.Я. // Физическая мезомеханика. 2018. Т. 21. № 4. С. 97.
Курбаткин И.И., Буше Н.А., Горячева И.Г., Зайчиков А.В. // Трение и износ. 2006. Т. 27. № 4. С. 355.
Курбаткин И.И., Муравьева Т.И. // Трение и смазка в машинах и механизмах. 2012. № 1. С. 38.
Муравьева Т.И., Курбаткин И.И. Процессы массопереноса в условиях фрикционного взаимодействия // Сб. тез. XXIV Рос. конф. по электронной микроскопии. Черноголовка, 2012. С. 111.
Курбаткин И.И., Муравьева Т.И. Исследование состава, структуры и трибологических свойств поверхности контакта в парах трения скольжения // Сб. докл. междунар. науч.-тех. конф. “Новые материалы и технологии глубокой переработки сырья – основа инновационного развития экономики России”. Москва, 2012. С. 186.
Щербакова О.О., Муравьева Т.И., Загорский Д.Л. Исследование морфологии и состава поверхности антифрикционных железосодержащих алюминиевых сплавов после трибологических тестов в смазочной среде // Сб. докл. “Методологические аспекты сканирующей зондовой микроскопии”. Минск, 2018. С. 182.
Дополнительные материалы отсутствуют.
Инструменты
Поверхность. Рентгеновские, синхротронные и нейтронные исследования