Поверхность. Рентгеновские, синхротронные и нейтронные исследования, 2021, № 2, стр. 94-101
Структурные изменения поверхности сплава АК5М2 при воздействии интенсивного импульсного электронного пучка
С. В. Коновалов a, b, c, *, Ю. Ф. Иванов d, Д. В. Загуляев b, Д. Ф. Якупов b, А. М. Устинов b, Д. А. Косинов b
a Nanjing University of Science and Technology
210094 Nanjing, China
b Сибирский государственный индустриальный университет
654007 Новокузнецк, Россия
c Самарский национальный исследовательский университет им. акад. С.П. Королева
443086 Самара, Россия
d Институт сильноточной электроники Сибирского отделения Российской академии наук
634055 Томск, Россия
* E-mail: ksv@ssau.ru
Поступила в редакцию 10.05.2020
После доработки 17.07.2020
Принята к публикации 22.07.2020
Аннотация
Проведена обработка поверхности Al–Si сплава марки АК5М2 интенсивным импульсным электронным пучком в различных режимах (энергия ускоренных электронов 17 кэВ, плотность энергии пучка электронов 10, 20, 30, 40 и 50 Дж/см2, длительность импульсов 50 и 200 мкс, количество импульсов 3, частота следования импульсов 0.3 с–1). Выполнен анализ микротвердости, а также методами растровой электронной микроскопии и рентгенофазового анализа исследован элементный и фазовый состав и состояние дефектной субструктуры поверхностного слоя. Показано, что увеличение микротвердости Al–Si-сплава обусловлено формированием субмикроразмерной структуры высокоскоростной ячеистой кристаллизации, обогащением твердого раствора на основе алюминия легирующими и примесными элементами, повторным выделением наноразмерных частиц упрочняющих фаз. Высказано предположение, что более высокие значения микротвердости, выявленные в сплаве, облученном при 50 Дж/см2, 50 мкс, по сравнению со сплавом, облученном при 50 Дж/см2, 200 мкс, обусловлены процессом отпуска материала, имеющими большее развитие при большей длительности воздействия пучка электронов в импульсе.
ВВЕДЕНИЕ
Развитие современной техники требует применения новых конструкционных материалов с повышенными эксплуатационными и технологическими параметрами. Однако, обработка таких материалов и полученных из них изделий традиционными методами затруднительна. Поэтому одной из важных задач является создание и внедрение качественно новых технологических процессов, в том числе с использованием внешних энергетических воздействий. Модификация поверхностных свойств материалов является достаточно перспективным направлением. Большой объем выполненных работ показал высокую эффективность этих методов в качестве уникального инструмента для изменения поверхностных свойств металлических материалов. Выбор способов модифицирования поверхности достаточно широк. Это традиционные виды химико-термической и термомеханической обработок [1, 2], лазерная [3, 4], плазменная, ультразвуковая обработка [5, 6], электровзрывное легирование [7], электронные и ионные пучки [8–11].
Метод воздействия высокоэнергетическими сильноточными электронными пучками является перспективным и эффективным методом модификации поверхности металлов и сплавов. Его важным преимуществом является более высокая эффективность поглощения энергии, а не введение (как в легировании) других примесей [12–15]. Импульсное плавление способно растворять частицы второй фазы, а сверхбыстрое охлаждение из жидкого состояния приводит к образованию в поверхностных слоях расплавленного слоя неравновесных структурно-фазовых состояний, в то время как сверхбыстрое затвердевание приводит к образованию структуры, содержащей твердые растворы, наноразмерные сегрегации второй фазы и частицы аморфной фазы [16]. Вследствие сверхбыстрых тепловых циклов электронно-пучковая обработка используется как для повышения износостойкости, коррозионной стойкости, твердости, так и усталостной выносливости металлических материалов [13, 17–21]. Однако, для развития возможности практического использования данного метода необходимо проведение комплексных исследований по установлению закономерностей эволюции структуры при электронно-пучковой обработке.
В связи с этим целью настоящей работы являлся анализ элементного и фазового состава, состояния дефектной субструктуры и микротвердости поверхностного слоя сплава АК5М2, подвергнутого облучению интенсивным импульсным электронным пучком.
МАТЕРИАЛ И МЕТОДИКА ИССЛЕДОВАНИЯ
В качестве материала исследования использован алюминиевый литейный сплав АК5М2 (силумин) [22], следующего элементного состава: 90.5 масс. % Al, 0.64 масс. % Fe, 5.39 масс. % Si, 0.24 масс. % Mn, 0.17 масс. % Ni, 1.33 масс. % Cu, 0.65 масс. % Mg, 1.08 масс. % Zn. Образцы имели форму параллелепипеда с размерами 15 × 15 × 5 мм.
Облучение образцов силумина интенсивным импульсным электронным пучком, как и в работах [20, 21, 23], осуществляли на установке СОЛО. Параметры пучка электронов: энергия ускоренных электронов составляла 17 кэВ, плотность энергии пучка электронов – 10, 20, 30, 40 и 50 Дж/см2, длительность импульсов – 50 и 200 мкс, количество импульсов – 3, частота следования импульсов – 0/3 с–1; давление остаточного газа (аргон) в рабочей камере установки – 2 × 10–2 Па.
Таблица 1.
Результаты элементного анализа поверхностного слоя сплава АК5М2, облученного импульсным электронным пучком
Режим облучения | Элементы, масс. % | |||||
---|---|---|---|---|---|---|
Es, Дж/см2 | τ, мкс | Mg | Al | Si | Fe | Cu |
10 | 50 | 0.65 | 87.29 | 8.04 | 1.15 | 2.87 |
200 | 0.53 | 87.76 | 7.97 | 1.05 | 2.68 | |
30 | 50 | 0.6 | 91.41 | 4.13 | 1.05 | 2.8 |
200 | 0.58 | 91.32 | 4.09 | 1.0 | 3.02 | |
50 | 50 | 0.62 | 91.42 | 4.15 | 1.0 | 2.82 |
200 | 0.60 | 91.68 | 3.95 | 0.96 | 2.81 |
Исследования элементного и фазового состава, состояния дефектной субструктуры проводили методами растровой электронной микроскопии [24] (прибор Philips SEM-515 с микроанализатором EDAX ECON IV) и рентгенофазового анализа [25] (рентгеновский дифрактометр Shimadzu XRD 6000). Механические свойства характеризовали микротвердостью, определенной на приборе HVS-100 при нагрузке на индентор 1 Н, средние значение микротвердости определяли по 10 отпечаткам.
РЕЗУЛЬТАТЫ ИССЛЕДОВАНИЯ И ИХ ОБСУЖДЕНИЕ
В результате анализа данных по микротвердости поверхности облучения образцов сплава марки АК5М2, подвергнутых обработке электронным пучком в различных режимах (рис. 1), установлена ее зависимость от длительности импульсов пучка электронов. При длительности импульсов 50 мкс микротвердость поверхностного слоя увеличивается с ростом плотности энергии пучка электронов, почти в два раза превышая микротвердость исходного материала (520 МПа). В случае задания длительности импульсов пучка электронов 200 мкс микротвердость поверхности при плотности энергии пучка электронов 30 Дж/см2 превышает микротвердость исходного материала в ≈1.7 раза.
Рис. 1.
Изменение микротвердости поверхности облучения сплава АК5М2 при разной плотности энергии пучка электронов.
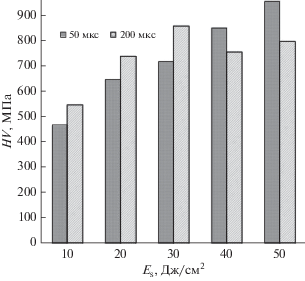
Из анализа структуры поверхности образцов сплава марки АК5М2 в исходном состоянии и обработанных электронным пучком, установлено, что исследуемый сплав в исходном состоянии является поликристаллическим агрегатом, сформированным зернами твердого раствора на основе алюминия (рис. 2а) и зернами эвтектики Al–Si (рис. 2б, зерна эвтектики указаны стрелками). Как правило, зерна эвтектики располагаются вдоль границ и в стыках границ зерен алюминия. Размер зерен алюминия изменяется в пределах от 30 до 100 мкм; размер зерен эвтектики Al–Si изменяется в пределах от 11 до 26 мкм. Дополнительными фазами исследуемого материала являются интерметаллиды, имеющие форму “иероглифов” (рис. 2в, включения указаны стрелками), игольчатую, глобулярную и (существенно реже) осколочную форму (рис. 2а, 2г). Продольные размеры частиц игольчатой формы часто превышают размеры зерен (рис. 2б, 2г), что указывает на их формирование до образования зерен алюминия. Частицы глобулярной формы располагаются преимущественно вдоль границ зерен алюминия (рис. 2в, 2г). При механической полировке образцов такие частицы часто выкрашиваются (рис. 2а), что может указывать на их плохую связь с границами зерен. Следует ожидать, что наличие в сплаве частиц интерметаллидов (независимо от их морфологии) будет способствовать охрупчиванию материала при механической нагрузке.
Облучение сплава АК5М2 интенсивным импульсным электронным пучком привело к изменению структуры поверхности образцов. При плотности энергии пучка электронов 10 Дж/см2 наблюдается интенсивное травление границ зерен (рис. 3). При этом степень травления границ зерен усиливается при уменьшении длительности импульса от 200 до 50 мкс. Размеры зерен сплава, подвергнутого облучению при длительности импульса 200 мкс (рис. 3а, 3в), практически не изменяются; при длительности импульса 50 мкс незначительно увеличиваются и изменяются в интервале от 35 до 112 мкм (рис. 3б, 3г). Независимо от длительности импульса облучение сплава электронным пучком с плотностью энергии 10 Дж/см2 не приводит к очистке поверхностного слоя от частиц интерметаллидов (рис. 3в, 3г).
Рис. 3.
Структура поверхности сплава АК5М2, подвергнутого облучению импульсным электронным пучком при следующих параметрах: а, в – 10 Дж/см2, 200 мкс; б, г – 10 Дж/см2, 50 мкс.
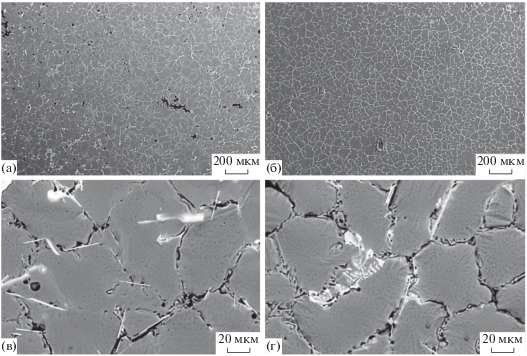
Увеличение плотности энергии пучка электронов до 30 Дж/см2 приводит к формированию в поверхностном слое микропор и микротрещин. Независимо от длительности импульсов облучение сплава при плотности энергии пучка 30 Дж/см2 приводит к растворению первичных включений интерметаллидов. В отдельных случаях на облучаемой поверхности обнаруживаются островки, содержащие частицы округлой формы, размеры которых изменяются в пределах 2–3 мкм (при длительности импульса пучка электронов 200 мкс) и в пределах 2–10 мкм (при длительности импульса пучка электронов 50 мкс). Можно предположить, что образование микротрещин обусловлено формированием в поверхностном слое растягивающих напряжений, являющихся следствием высоких скоростей охлаждения поверхностного слоя материала из расплавленного состояния.
При плотности энергии пучка электронов 50 Дж/см2 области, ограниченные трещинами, увеличиваются независимо от длительности импульса (рис. 4а, 4б), т.е. плотность трещин на единицу поверхности образца снижается. Данный факт говорит об уменьшении величины растягивающих напряжений по сравнению с образцами, подвергнутыми электронно-пучковой обработке при плотности энергии пучка электронов 30 Дж/см2.
Рис. 4.
Структура поверхности силумина, подвергнутого облучению импульсным электронным пучком при следующих параметрах: а, в – 50 Дж/см2, 200 мкс; б, г – 50 Дж/см2, 50 мкс.
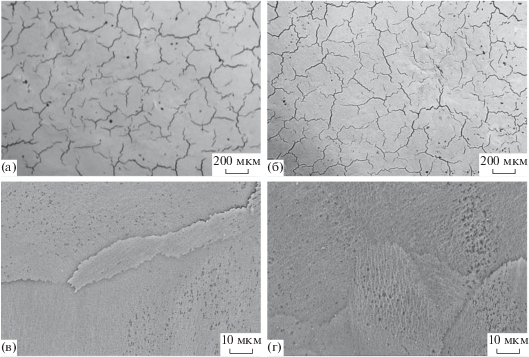
Облучение сплава электронным пучком с плотностью энергии 50 Дж/см2 независимо от длительности импульса пучка приводит к полному растворению в поверхностном слое частиц инерметаллидов (рис. 4). В объеме зерен формируется структура высокоскоростной ячеистой кристаллизации, размеры которой изменяются в пределах 500–800 нм (рис. 4в, 4г).
Элементный состав поверхностного слоя облученного материала анализировали методами микрорентгеноспектрального анализа. Энергетические спектры (рис. 5б) получали с выделенных площадей образца (рис. 5а). Результаты микрорентгеноспектрального анализа приведены в табл. 1. Анализируя результаты, приведенные в табл. 1, можно отметить, что на элементный состав модифицированного слоя более существенное влияние оказывает плотность энергии пучка электронов, а не длительность импульса пучка.
Рис. 5.
Электронно-микроскопическое изображение участка поверхности облученного (30 Дж/см2, 50 мкс) образца (а); энергетические спектры, полученные с участка поверхности, выделенного на (а) рамкой, (б).
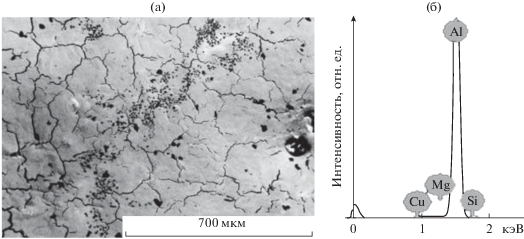
Фазовый состав модифицированного электронным пучком поверхностного слоя силумина изучали методами рентгеноструктурного анализа. Установлено, что в исходном состоянии основными фазами исследуемого материала являются твердый раствор на основе алюминия, кремний и интерметаллиды, одним из которых является фаза состава Fe2Al9Si2 (рис. 6). Анализ дифракционных максимумов алюминия показал, что они расщеплены (вставка на рис. 6). Это позволяет говорить о существовании двух твердых растворов на основе алюминия, различающихся параметром кристаллической решетки и, следовательно, концентрацией легирующих элементов. Для определенности обозначим твердый раствор на основе алюминия с большим параметром кристаллической решетки Al1, с меньшим параметром кристаллической решетки – Al2. Установлено, что в сплаве АК5М2 перед облучением электронным пучком относительное содержание фазы Al1 – 75.1 масс. %, фазы Al2 – 20.0 масс. %, остальное – кремний.
Рис. 6.
Участок рентгенограммы силумина в исходном состоянии. Стрелками указано расположение дифракционных линий фазы Al2.
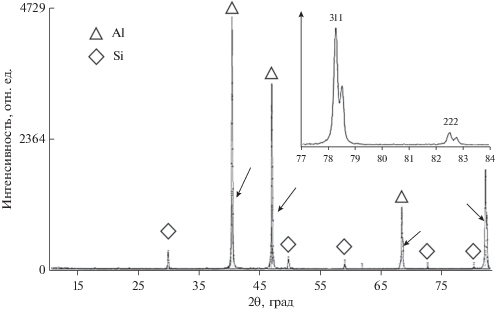
Обнаружено, что при облучении сплава импульсным электронным пучком увеличение плотности энергии пучка электронов при длительности импульса 50 мкс приводит к увеличению относительного содержания фазы Al2 (рис. 7, кривая 2). При длительности импульса 200 мкс относительное содержание фазы Al2 достигает максимального значения, равного ≈99 масс. %, при плотности энергии пучка электронов 30 Дж/см2 (рис. 7, кривая 1).
Рис. 7.
Изменение относительного содержания фазы Al2 в поверхностном слое силумина, подвергнутого облучению импульсным электронным пучком, в зависимости от плотности энергии пучка электронов.
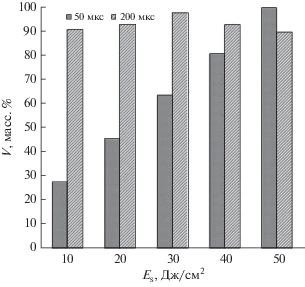
Облучение силумина импульсным электронным пучком сопровождается изменением параметра кристаллической решетки фаз Al1 и Al2 (рис. 8). Анализируя результаты, представленные на рис. 8, можно отметить, что параметр кристаллической решетки фазы Al1 (рис. 8а) независимо от длительности импульса изменяется по кривой с минимумом, достигаемым при плотности энергии пучка электронов 30 Дж/см2. При плотности энергии пучка 50 Дж/см2 параметр кристаллической решетки фазы Al1 превышает параметр кристаллической решетки фазы Al1 исходного состояния (а = 4.048 Å).
Рис. 8.
Изменение параметра кристаллической решетки фазы Al1 (а) и фазы Al2 (б), формирующихся в поверхностном слое силумина, подвергнутого облучению импульсным электронным пучком.
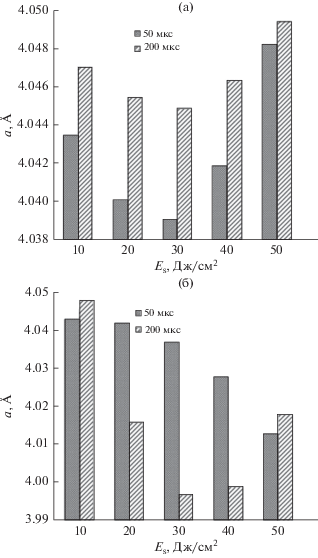
Параметр кристаллической решетки фазы Al2 при длительности импульсов пучка 200 мкс изменяется подобно параметру кристаллической решетки фазы Al1, достигая минимума при плотности энергии пучка электронов 30 Дж/см2 (рис. 8б, кривая 1). При длительно импульса пучка электронов 50 мкс (рис. 8б, кривая 2) параметр кристаллической решетки фазы Al2 снижается при увеличении плотности энергии пучка электронов, достигая минимума при плотности энергии пучка электронов 50 Дж/см2.
Очевидно, что основной причиной выявленного изменения параметра кристаллической решетки фаз Al1 и Al2 является изменение концентрации легирующих элементов в твердом растворе данных фаз. Из анализа справочной литературы следует, что радиусы атомов кремния, меди, никеля, железа и марганца меньше, а радиус атома магния больше радиуса атома алюминия. Следовательно, величина параметра кристаллической решетки фаз Al1 и Al2 определяется концентрацией данных элементов в твердом растворе. Зависимость параметра кристаллической решетки фаз Al1 и Al2 от длительности импульсов и плотности энергии пучка электронов будет определяться процессами растворения частиц кремния и интерметаллидов и их повторного выделения, имеющих место при облучении материала импульсным электронным пучком.
Результаты, полученные при анализе структуры и фазового состава поверхностного слоя силумина, позволяют предположить, что увеличение микротвердости материала, имеющее место при длительности импульсов пучка электронов 50 и 200 мкс (рис. 1), обусловлено формированием субмикроразмерной структуры высокоскоростной ячеистой кристаллизации (рис. 4), обогащением твердого раствора на основе алюминия легирующими и примесными элементами, повторным выделением наноразмерных частиц упрочняющих фаз (кремния и интерметаллидов). Более высокие значения твердости, выявленные в сплаве, облученном при 50 Дж/см2 в течение 50 мкс, по сравнению со сплавом, облученном при 50 Дж/см2 в течение 200 мкс, обусловлены, по всей видимости, процессами отпуска материала, имеющими большее развитие при большей длительности воздействия пучка электронов в импульсе.
ЗАКЛЮЧЕНИЕ
Показано, что величина микротвердости поверхностного слоя сплава АК5М2 зависит от параметров облучения и при длительности импульсов 50 мкс и плотности энергии пучка электронов 50 Дж/см2 достигает значения 1100 МПа, что превышает микротвердость исходного материала более чем в два раза. Установлено, что облучение сплава электронным пучком с плотностью энергии 50 Дж/см2 независимо от длительности импульса пучка приводит к полному растворению в поверхностном слое частиц инерметаллидов и кремния. В объеме зерен формируется структура высокоскоростной ячеистой кристаллизации, размеры которой изменяются в пределах от 500 до 800) нм. Выявлено существование в силумине исходного состояния двух твердых растворов на основе алюминия, различающихся параметром кристаллической решетки и, следовательно, концентрацией легирующих элементов. Обнаружено, что облучение сплава импульсным электронным пучком сопровождается снижением параметра кристаллической решетки твердого раствора на основе алюминия, что обусловлено насыщением данной фазы легирующими и примесными элементами.
Список литературы
Sheremetyev V., Kudryashova A., Dubinskiy S., Galkin S., Prokoshkin S., Brailovski V. // J. Alloys Compd. 2018. V. 737. P. 678.https://doi.org/10.1016/j.jallcom.2017.12.119
Ditenberg I.A., Smirnov I.V., Tsverova A.S., Tyumentsev A.N., Grinyaev K.V., Chernov V.M., Potapenko M.M. // Russ. Phys. J. 2018. V. 61. P. 1506.https://doi.org/10.1007/s11182-018-1563-7
Okipnyi I.B., Maruschak P.O., Zakiev V.I., Mocharskyi V.S. // J. Fail. Anal. Prev. 2014. V. 14. P. 668.https://doi.org/10.1007/s11668-014-9869-4
Telegin S.V., Lyasnikova A. V., Dudareva O.A., Grishina I.P., Markelova O.A., Lyasnikov V.N. // J. Surf. Investig.: X-Ray, Synchrotron Neutron Tech. 2019. V. 13. P. 2281.https://doi.org/10.1134/S1027451019020174
Kuz’min E.V., Peev A.P., Kuz’min S.V., Lysak V.I. // Phys. Met. Metallogr. 2017. V. 118. P. 820.https://doi.org/10.1134/S0031918X17060059
Timoshkin I.Y., Nikitin K.V., Nikitin V.I., Deev V.B. // Russ. J. Non-Ferrous Met. 2016. V. 57. P. 419.https://doi.org/10.3103/S1067821216050163
Romanov D.A., Protopopov E.V. // Steel Transl. 2017. V. 47. P. 782.https://doi.org/10.3103/S0967091217120105
Panin S.V., Vlasov I.V., Sergeev V.P., Maruschak P.O., Sunder R., Ovechkin B.B. // Int. J. Fatigue. 2015. V. 76. P. 3.https://doi.org/10.1016/j.ijfatigue.2014.10.011
Ghyngazov S.A., Vasil’ev I.P., Surzhikov A.P., Frangulyan T.S., Chernyavskii A.V. // Tech. Phys. 2015. V. 60. P. 128.https://doi.org/10.1134/S1063784215010120
Khusainov Y.G., Ramazanov K.N. // Inorg. Mater. Appl. Res. 2019. V. 10. P. 544.https://doi.org/10.1134/S207511331903016X
Feng H., Wang G., Wu G., Jin W., Wu H., Chu P.K. // Surf. Coatings Technol. 2016. V. 306. P. 140.https://doi.org/10.1016/j.surfcoat.2016.05.059
Cai J., Yang S.Z., Ji L., Guan Q.F., Wang Z.P., Han Z.Y. // Surf. Coatings Technol. 2014. V. 251. P. 217.https://doi.org/10.1016/j.surfcoat.2014.04.029
Luo D., Tang G., Ma X., Gu L., Sun M., Wang L. // Appl. Surf. Sci. 2015. V. 351. P. 1069.https://doi.org/10.1016/j.apsusc.2015.06.014
Guan Q.F., Zou H., Zou G.T., Wu A.M., Hao S.Z., Zou J.X., Qin Y., Dong C., Zhang Q.Y. // Surf. Coatings Technol. 2005. V. 196. P. 145.https://doi.org/10.1016/j.surfcoat.2004.08.104
Ivanov Y.F., Gromov V.E., Konovalov S.V., Zagulyaev D.V., Petrikova E.A., Semin A.P. // Prog. Phys. Met. 2018. V. 19. P. 195.https://doi.org/10.15407/ufm.19.02.195
Yan P., Grosdidier T., Zhang X., Zou J. // Mater. Des. 2018. V. 159. P. 1.https://doi.org/10.1016/j.matdes.2018.08.033
Guo G., Tang G., Ma X., Sun M., Ozur G.E. // Surf. Coatings Technol. 2013. V. 229. P. 140.https://doi.org/10.1016/j.surfcoat.2012.08.009
Hao Y., Gao B., Tu G.F., Li S.W., Hao S.Z., Dong C. // Appl. Surf. Sci. 2011. V. 257. P. 3913.https://doi.org/10.1016/j.apsusc.2010.11.118
Krysina O.V., Teresov A.D., Moskvin P.V., Koval N.N., Ivanov Y.F., Akhmadeev Y.H., Lopatin I.V. // Russ. Phys. J. 2019. V. 62. P. 1139.https://doi.org/10.1007/s11182-019-01828-3
Konovalov S.V., Komissarova I.A., Kosinov D.A., Ivanov Y.F., Ivanova O.V., Gromov V.E. // Lett. Mater. 2017. V. 7. P. 266.https://doi.org/10.22226/2410-3535-2017-3-266-271
Gromov V.E., Gorbunov S.V., Ivanov Y.F., Vorobiev S.V., Konovalov S.V. // J. Surf. Investig. 2011. V. 5. P. 974.https://doi.org/10.1134/S1027451011100107
Belov N.A., Eskin D.G., Aksenov A.A. Multicomponent Phase Diagrams. Elsevier, 2005. https://doi.org/10.1016/B978-0-08-044537-3.X5000-8
Ivanov Y.F., Koval N.N., Gorbunov S.V., Vorobyov S.V., Konovalov S.V., Gromov V.E. // Russ. Phys. J. 2011. V. 54. P. 575.https://doi.org/10.1007/s11182-011-9654-8
Egerton R.F. Physical Principles of Electron Microscopy. Boston, MA: Springer US, 2005.https://doi.org/10.1007/b136495
X-Ray and Neutron Structure Analysis in Materials Science, Hašek J., Ed. Boston, MA: Springer US, 1989.https://doi.org/10.1007/978-1-4613-0767-9
Дополнительные материалы отсутствуют.
Инструменты
Поверхность. Рентгеновские, синхротронные и нейтронные исследования