Поверхность. Рентгеновские, синхротронные и нейтронные исследования, 2021, № 4, стр. 59-69
Плазмодинамический синтез кубического карбида вольфрама и исследование влияния параметров газообразной среды
А. А. Сивков a, b, И. И. Шаненков a, b, Ю. Л. Шаненкова a, b, Д. С. Никитин b, *, И. А. Рахматуллин b, А. И. Циммерман b, Н. С. Шаненкова b
a College of Communication Engineering, Jilin University
130023 Changchun, PR China
b Инженерная школа энергетики, Национальный исследовательский
Томский политехнический университет
634050 Томск, Россия
* E-mail: nikitindmsr@yandex.ru
Поступила в редакцию 28.02.2020
После доработки 25.05.2020
Принята к публикации 28.05.2020
Аннотация
Кубический карбид вольфрама WC1 –x получен в сверхзвуковой струе углерод-вольфрамовой электроразрядной плазмы, генерированной коаксиальным магнитоплазменным ускорителем с графитовыми электродами. Кристаллическая фаза WC1 –x с массовым содержанием в продукте до 90% формируется в виде нанодисперсных частиц средними размерами до ~20 нм. В работе проанализировано влияние параметров газообразной среды (давление, тип) на процесс развития ударно-волновой структуры плазменной струи, истекающей в свободное пространство камеры-реактора, и на формирование частиц продукта синтеза. Определены наиболее оптимальные диапазоны давления и тип газообразной среды камеры-реактора, а также показана возможность управления фазовым и гранулометрическим составом продукта плазмодинамического синтеза в системе W–C.
ВВЕДЕНИЕ
Карбиды вольфрама находят широкое применение при изготовлении металлообрабатывающих инструментов, изделий, требующих высокой твердости и коррозионной стойкости, высокотвердых и износостойких сплавов [1–3]. Авторами работы [4, 5] была показана принципиальная возможность существования кубической фазы карбида вольфрама со стехиометрией WC1 –x, где X = 0.6–1.0, синтез которой осуществляется в достаточно узком интервале температур и соотношений атомарных масс углерода и вольфрама. Такие особенности затрудняют синтез данной кубической модификации карбида вольфрама большинством известных способов и крайне редко удается достичь высокой чистоты его выхода. Одним из путей, позволяющих синтезировать WC1 –x с высокой чистотой, является метод прямого плазмодинамического синтеза, осуществляемый при распылении электроразрядной вольфрам- и углеродсодержащей плазменной струи в свободное пространство рабочей камеры-реактора, заполненной инертной газовой атмосферой (аргон). В данной работе проведены исследования по оценке влияния параметров газообразной среды (давления и типа) на характеристики синтезируемых материалов системы “вольфрам–углерод” и определены наиболее оптимальные параметры с позиции получения максимальной чистоты выхода кубического карбида вольфрама при минимальном среднем размере частиц [6, 7].
ЭКСПЕРИМЕНТАЛЬНАЯ ЧАСТЬ
Плазмодинамический синтез кубического карбида вольфрама осуществлялся в системе, принципиально состоящей из емкостного накопителя энергии, коаксиального магнитоплазменного ускорителя (КМПУ) и рабочей камеры-реактора. Емкостной накопитель энергии предназначен для импульсного электропитания КМПУ, который представляет собой устройство для генерации и ускорения электроразрядной плазмы. Основные принципы формирования дугового разряда, его ускорения в коаксиальной системе и синтеза наночастиц подробно рассмотрены ранее в работах [8, 9]. В рамках данного исследования было изучено влияние величины давления газообразного аргона, наполняющего рабочую камеру-реактор (форвакуум, 5 × 104 Па, 1 × 105 Па, 2 × 105 Па), и типа газообразной среды (аргон, азот) на фазовый и гранулометрический состав синтезируемых материалов системы “вольфрам–углерод”.
Для этого проведена серия экспериментов, основные энергетические параметры которой оставались неизменными: емкость накопителя энергии C = 6/0 мФ, зарядное напряжение Uзар = 3/0 кВ, величина накопленной энергии Wc = 27.0 кДж. В качестве исходного прекурсора плазмодинамической реакции использовалась смесь порошков вольфрама, полученного методом электровзрыва проводников, и ультрадисперсного углерода (сажа). Соотношение атомарных масс вольфрама и углерода в исходной смеси также оставалось неизменным и составляло [C]/[W] = 1.0. Камера-реактор предварительно вакуумировалась, после чего наполнялась необходимой газообразной средой при требуемом уровне давления, что контролировалось высокопрецизионным манометром.
В процессе истечения гиперзвуковой струи электроразрядной плазмы осуществлялась фоторегистрация с использованием высокоскоростной камеры Photron Fast CAM 1.1, после чего производилась обработка полученных данных с построением зависимостей скорости фронта головной ударной волны от расстояния, пройденного от среза ускорительного канала КМПУ. Фазовый состав и кристаллическая структура порошкообразных продуктов плазмодинамического синтеза исследовались методом рентгеновской дифрактометрии XRD (дифрактометр Shimadzu XRD 7000S, оснащенный монохроматором, CuKα-излучение) с последующей обработкой в программной среде PowderCell 2.4 с использованием базы данных PDF4+. Анализ гранулометрического состава проводился методом просвечивающей электронной микроскопии (ПЭМ), при этом использовали электронный микроскоп Phillips CM12, с последующим построением гистограмм распределения частиц по размерам на основании данных серии светлопольных изображений.
РЕЗУЛЬТАТЫ И ОБСУЖДЕНИЕ
Ранее проведенные исследования позволили установить принципиальную возможность получения кубического карбида вольфрама в системе плазмодинамического синтеза при проведении процесса в условиях распыления плазменной струи в атмосферу рабочей камеры-реактора, заполненной аргоном при нормальных условиях [10–12]. Известно, что в рассматриваемой системе давление газа существенно влияет на параметры плазменной струи, распыление дисперсного материала с границы головной ударной волны и, соответственно, гранулометрический и фазовый состав частиц [13, 14]. В этой связи проведена серия экспериментов по определению наиболее оптимальных параметров давления газовой среды с позиции получения максимального выхода фазы кубического карбида вольфрама. В качестве исследуемого газа был выбран аргон для предотвращения загрязнения конечного продукта примесными фазами, формирование которых возможно в условиях распыления материала в химически активную среду.
На рис. 1 приведены фотограммы процессов формирования и развития ударно-волновой структуры плазменной струи во времени в процессе ее истечения в газовую среду при различном давлении. Известные геометрические размеры ускорителя позволяют провести оценку скорости плазменной структуры при ее вылете из ускорительного канала и дальнейшем развитии для построения кривой закона движения ударного фронта – зависимости удлинения струи в осевом направлении от времени l(t). Аппроксимации полученной аналитической функции и ее дифференцирование дают функцию затухания скорости во времени υ(t) или от расстояния от среза ускорительного канала υ(l). Ее экстраполяция к срезу ускорительного канала на интервале времени менее 5/0 мкс дает оценочное значение скорости ударного фронта на срезе ускорительного канала υс.
Рис. 1.
Фотограммы вылета плазмы из ствола при разных давлениях в камере, а – 1 × 104 Па, б – 5 × 104 Па, в – 1 × 105 Па, г – 2 × 105 Па.
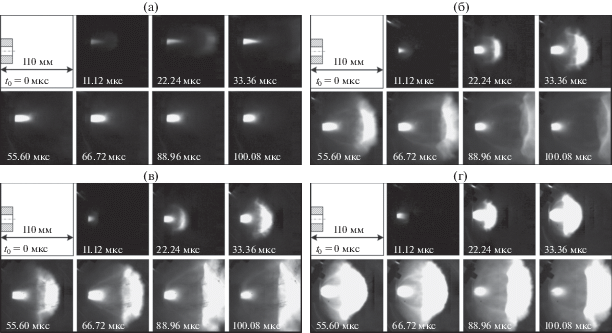
Характерной особенностью процесса развития ударно-волновой структуры струи является очень быстрое увеличение площади фронтальной поверхности головной ударной волны, испытывающей газодинамическое сопротивление покоящейся газообразной среды. На этапе формирования первой “бочки” ударно-волновой структуры (рис. 2) форма фронта головной ударной волны близка к сферической. С ее свободной поверхности, как это видно из рис. 2, происходит “смывание” и распыление в газообразной среде материала струи, накапливаемого в скачке уплотнения.
Рис. 2.
Кривые затухания скорости υ и кадр прямого скачка уплотнения ударно-волновой структуры плазменной струи: 1 – срез ускорительного канала; 2 – косой скачок уплотнения; 3 – висячий скачок; 4 – граница первой“бочки”; 5 – диск Маха; 6 – граница второй “бочки”; 7 – головная ударная волна.
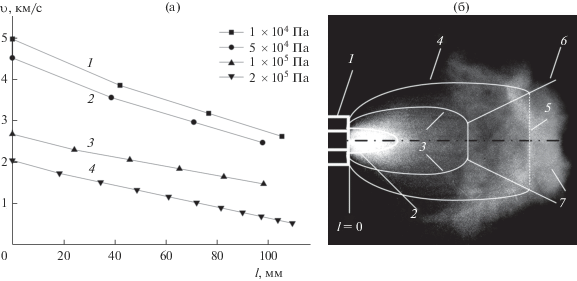
Распыленный в жидкой фазе материал кристаллизуется с образованием высокодисперсных частиц, размеры которых обусловлены скоростью распыления и параметрами состояния газообразной среды в камере-реакторе. В соответствии с классическими закономерностями газовой динамики сверхзвуковых течений, в свободном пространстве скорость фронта головной ударной волны быстро затухает за счет сопротивления покоящейся среды в условиях очень быстрого увеличения площади фронта головной ударной волны. По самым общим представлениям [4, 5] замедление А прямо пропорционально квадрату скорости υ и параметру замедления k:
Это выражение качественно показывает, что замедление сильно возрастает с увеличением начальной скорости.
Фотограммы (рис. 2) демонстрируют формирование “бочкообразной” ударно-волновой структуры, границей первой “бочки” которой является диск Маха – скачок уплотнения в виде яркосветящегося диска в плоскости, перпендикулярной продольной оси течения. По мере нарастания мощности разряда и скорости течения он смещается вправо. Его положение в пространстве стабилизируется после прекращения роста мощности разряда на расстоянии около 120 мм от среза ускорительного канала (рис. 2). Визуально наблюдаемый интервал стабильного положения скачка уплотнения Маха является этапом квазистационарного течения. В этом скачке уплотнения накапливается материал струи, скорость массопереноса снижается до дозвуковой, возрастают давление и температура, о чем свидетельствует яркое свечение этой области.
За диском Маха формируется вторая “бочка” за счет возобновления сверхзвукового течения материала, накопленного в области уплотнения. Далее по мере снижения мощности разряда и скорости течения в ускорительном канале бочкообразная структура постепенно сжимается, диск Маха смещается в обратном направлении, и течение переходит в дозвуковой режим. В дозвуковом режиме происходит “ненужная” эрозия электрода-ствола, и из ускорительного канала выносится эродированный углерод (миллиметрового и микронного размеров), который является примесным и который уже имеет возможности вступить в плазмохимическую реакцию с вольфрамом, ранее вылетевшим из канала в камеру-реактор. Это эффект является основным недостатком плазмодинамического метода, так как не только загрязняется материал, но и снижается эффективность использования как электромагнитной энергии, так и расходного материала ствола коаксиального ускорителя.
Представленные на рис. 2 скорости затухания электроразрядной плазменной струи по мере прохождения ударно-волновой структуры в свободном пространстве камеры-реактора демонстрируют значительное влияние давления в камере на начальную скорость струи υс, а также на замедление сформированной плазменной струи в целом. Отмеченные ранее параметры, влияющие на характеристики скорости и замедления плазменной струи подтверждают, что плотность газообразной среды $\rho $ оказывает непосредственное влияние на формирование и протекание ударно-волновой плазменной электроэрозионной структуры. При давлении в камере-реакторе $\rho $ равном 1 × 104 Па (форвакуум) скорость плазменной струи на срезе ускорительного канала достигает υс ≈ 5 км/с. Увеличение давления от 1 × 104 до 2 × × 105 Па сопровождается уменьшением υс (с ~5.0 до ~2.0 км/с). Такое уменьшение скорости потока и ее переход из гиперзвуковой в сверхзвуковую несомненно должен сказываться на распылении материала и формировании частиц различного гранулометрического и фазового состава.
На рис. 3 представлены результаты XRD-анализа продуктов, синтезированных при форвакууме (давление 1 × 104 Па, рис. 3а) и при давлении 5 × 104 Па (рис. 3б), а также участки главных максимумов основных фаз системы W–C (рис. 3в–3е). В табл. 1 приведены количественные значения массы эродированного с поверхности ускорительного канала графитового материала m1, массы порошкообразных продуктов m2, а также результаты полнопрофильного рентгеноструктурного анализа полученных дифрактограмм: процентное содержание каждой из фаз ω, средний размер областей когерентного рассеивания (ОКР), уровень микроискажений решетки Δd/d × 10–3 и ее параметры (a, b, c). Кроме того, для всех материалов определялась степень кристалличности ξ с использованием специального программного обеспечения.
Рис. 3.
Данные XRD-анализа продуктов, полученных при разных величинах давления в камере-реакторе: а – XRD-картина продукта, синтезированного при Р = 1 × 104 Па; б – типичная XRD-картина, характерная для продуктов, полученных при Р = 0.5–3.0 атм.; в–е – выделенные участки 2θ с основными максимумами фаз системы W–C-продуктов, синтезированных при давлениях 5 × 104 Па, 1 × 105 Па, 2 × 105 Па.
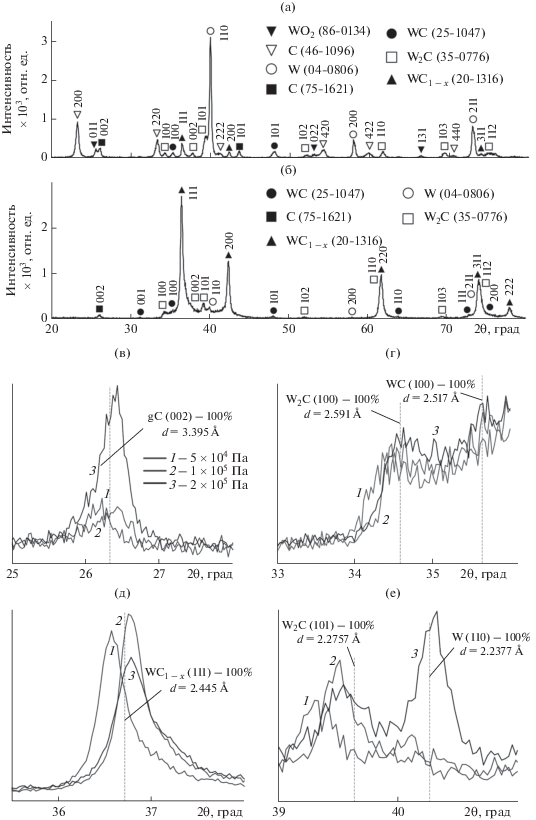
Таблица 1.
Результаты полнопрофильного рентгенофазового анализа продуктов, полученных при давлениях 1 × 104, 5 × 104, 1 × 105, 2 × 105 Па
P, МПа | m1, г | m2, г | ξ, % | Параметр | Фазовый состав, % | |||||
---|---|---|---|---|---|---|---|---|---|---|
WC1 – x | W2C | W | WC | WO2 | WO3 | |||||
0.1 | 0.20 | 0.12 | 86.0 | ω, % | 4.00 | 9.95 | 45.83 | 0.89 | 14.53 | 24.81 |
ОКР, нм | 14.74 | 25.98 | 43.66 | 23.17 | 15.50 | 17.22 | ||||
Δd/d × 10–3, отн. ед. | 3.62 | 0.50 | 1.01 | 1.46 | 1.87 | 0.93 | ||||
a | 4.251 | 2.987 | 3.161 | 2.896 | 5.649 | 7.433 | ||||
b | – | – | – | – | 4.820 | 7.507 | ||||
c | – | 4.717 | – | 2.843 | 5.503 | 7.640 | ||||
P, МПа | m1, г | m2, г | ξ, % | Параметр | Фазовый состав, % | |||||
WC1 – x | W2C | W | WC | С | ||||||
0.5 | 0.20 | 0.33 | 57.4 | ω, % | 88.37 | 3.94 | 1.62 | 3.94 | 2.75 | |
ОКР, нм | 32.82 | 11.13 | 27.26 | 136.81 | 9.29 | |||||
Δd/d × 10–3, отн. ед. | 5.28 | 1.63 | 3.07 | 3.30 | 7.10 | |||||
a | 4.250 | 3.000 | 3.178 | 2.925 | 2.570 | |||||
c | – | 4.770 | – | 2.855 | 6.839 | |||||
P, МПа | m1, г | m2, г | ξ, % | Параметр | Фазовый состав, % | |||||
WC1 – x | W2C | W | WC | С | ||||||
1.0 | 0.40 | 0.28 | 56.7 | ω, % | 90.06 | 3.49 | 1.24 | 3.21 | 2.00 | |
ОКР, нм | 37.56 | 14.14 | 19.00 | 18.16 | 44.54 | |||||
Δd/d × 10–3, отн. ед. | 4.15 | 2.81 | 3.06 | 1.81 | 4.33 | |||||
a | 4.234 | 3.000 | 3.164 | 2.915 | 2.370 | |||||
c | – | 4.780 | – | 2.847 | 6.890 | |||||
P, МПа | m1, г | m2, г | ξ, % | Параметр | Фазовый состав, % | |||||
WC1 – x | W2C | W | WC | С | ||||||
2.0 | 0.15 | 0.35 | 49.5 | ω, % | 71.37 | 9.77 | 5.56 | 5.85 | 7.45 | |
ОКР, нм | 23.46 | 8.31 | 30.86 | 155.00 | 37.09 | |||||
Δd/d × 10–3, отн. ед. | 4.00 | 6.15 | 0.87 | 0.72 | 3.90 | |||||
a | 4.242 | 2.995 | 3.172 | 2.917 | 2.480 | |||||
c | – | 4.802 | – | 2.846 | 6.789 |
Анализ фазового состава показал, что продукт, полученный при форвакууме (рис. 1а и табл. 1), преимущественно состоит из металлического вольфрама W (№ 00‑04‑806, кубический, пространственная группа (SG): Im-3m (no. 164), a = = 3.1648 Å) и оксидов вольфрама WO3 (№ 00-46-1096, кубический, SG: Р 4/n2-1/c 2/c (no. 130), a = = 5.2759 Å, b = 5.2759 Å, c =7 .8462 Å) и WO2 (№ 00-86-134, моноклинная структура, SG: Р21/с (no. 14), a = 5.57690 Å, b = 4.89860 Å, с = 5.66440 Å), содержание которых составляет около 45 и до 40% соответственно. Кроме того, в незначительных количествах обнаружены карбиды вольфрама (α‑W2C (№ 00-035-0776, гексагональный, SG: Р-3m1 (no. 164), a = 2.997049 Å, с = 4.72793 Å), WC (№ 00‑051‑0939, гексагональный, SG: Р-6m2 (no.187), a = 2.906319 Å, с = 2.837548 Å)) и кубический WC1 –х (№ 00-020-1316, кубический, SG: Fm‑3m (no. 225), a = 4.2355 Å), суммарное содержание которых не превышает 15%.
Доминирование в продукте оксидных фаз и металлического вольфрама объясняется только тем, что в данном режиме в разреженной атмосфере остаются следы воздушной атмосферы ввиду несовершенства системы вакуумирования. Присутствие окислителя (кислорода) приводит к сгоранию большей части эродированного углерода и углерода, входящего в состав прекурсора. Это обуславливает формирование чистого металлического карбида вольфрама из-за недостатка углерода. Кроме того, часть распыляемого вольфрама также реагирует с кислородом с образованием оксидов WO2 и WO3. Таким образом, несмотря на высокие скорости распыления (что должно приводить к получению более дисперсного продукта), данный режим является неудовлетворительным с позиции получения продукта с высоким содержанием кубического карбида вольфрама (согласно результатам XRD-анализа, приведенным в табл. 1, WC1 –x = 4.00%).
Основной доминирующей фазой продуктов, полученных при более высоких давлениях (5 × × 104 Па и выше), является кристаллическая фаза кубической сингонии WC1 –х (№ 00-020-1316, SG: Fm‑3m (no. 225), параметры решетки a = 4.2355 Å) (рис. 4б–4е). В продукте обнаружено присутствие в небольших количествах исходных реагентов (Cgrafit и W), а также гексагональных фаз карбида вольфрама WC и W2C. Как было отмечено ранее, в полном объеме представлена только XRD-картина продукта, синтезированного при давлении 5 × 104 Па. Однако, рассматривая более детально рефлексы основных фаз на выделенных областях 2θ (рис. 4в–4е), можно увидеть небольшие различия в составе продуктов плазмодинамического синтеза. При давлениях 5 × 104 и 1 × 105 Па дифрактограммы продукта отличаются минимальной интенсивностью максимума, соответствующего основному кристаллографическому направлению плоскостей (002) графитоподобного углерода (рис. 4в), что (в конечном счете) отражается на его минимальном массовом содержании в составе этих порошков (на уровне 2%). При этом дальнейшее увеличение давления приводит к росту содержания углерода.
Рис. 4.
Гистограммы распределения частиц по размерам, ПЭМ-изображения продукта, полученного при: а – 1 × 104 Па, б – 5 × 104 Па, в – 1 × 105 Па, г – 2 × 105 Па.
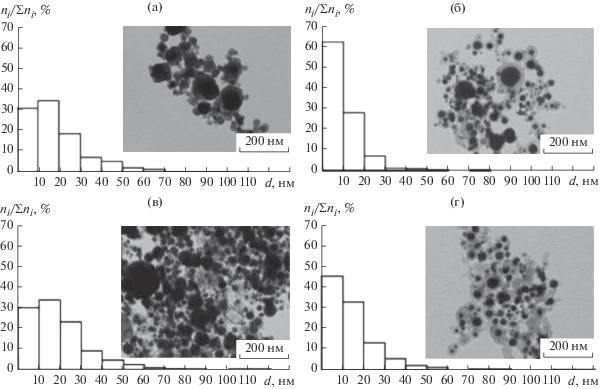
Это может объясняться только тем, что скорость плазменного потока в таком режиме существенно ниже (рис. 2). Происходит торможение фронта головной ударной волны и интенсивный разогрев углеродного электрода-ствола вблизи среза ускорительного канала. Это приводит к его чрезмерной электроэрозии и попаданию в плазменный поток избыточного углерода, который кристаллизуется в чистом виде без образования карбидов.
Анализ положения на оси 2θ рефлексов основной фазы WC1 –x (рис. 3д) показал его практическое постоянство, лишь в случае эксперимента, полученного при давлении 5 × 104 Па, наблюдается его некоторое смещение в область больших межплоскостных расстояний. Это может определяться изменением параметра решетки и, соответственно, стехиометрией соединения. При этом интенсивности находятся практически на одинаковом уровне (за исключением эксперимента с Р = 2 × 105 Па). Выделенные участки для других вольфрамсодержащих фаз (рис. 3г, 3е) дают основание утверждать, что во всех представленных экспериментах уровни отражений фаз W2C и WC постоянны, однако за счет снижения интенсивности WC1 –x и роста содержания углерода суммарное их содержание в режиме работы с давлением 2 × 105 Па несколько возрастает. Таким образом, анализ фазового состава продуктов синтеза позволил выявить наиболее оптимальный диапазон давлений: 5 × 104–1 × 105 Па, позволяющий получать фазу кубического карбида вольфрама с чистотой до ~90 мас. %.
Полученные при разных давлениях продукты были исследованы методами просвечивающей электронной микроскопии. По сериям светлопольных ПЭМ-снимков определялись средние размеры частиц и строились гистограммы их распределения (рис. 4). Практическое отсутствие углерода и наличие оксидных фаз обуславливает явно видимое отличие частиц порошка, синтезированного при давлении 1 × 104 Па. Данный продукт характеризуется отсутствием углеродной матрицы, которая присуща продуктам плазмодинамического синтеза системы W–C, полученным в обычных условиях, и состоит (в основном) из кристаллитов неправильной формы с естественной огранкой.
Анализ ПЭМ-снимков продуктов, полученных при давлениях Р = 5 × 104–2 × 105 Па, показывает незначительные отличия синтезированных частиц друг от друга. Все они имеют ядро округлой формы из плотного материала с ореолом из аморфного углерода. Гистограммы распределения частиц по размерам показывают, что для всех проведенных экспериментов их основная масса лежит в диапазоне размеров от нескольких нанометров до 30 нм. Однако наличие наиболее мелких частиц (1–10 нм) характерно для продукта, полученного при давлении 5 × 104 Па. Изменение размеров частиц напрямую связано с давлением в камере-реакторе в импульсном плазмодинамическом процессе, а именно с развиваемыми скоростями плазменной структуры, которые задают скорость кристаллизации частиц. При уменьшении давления возрастает скорость ударно-волновой плазменной структуры как на срезе ускорительного канала, так и на всем рассматриваемом диапазоне расстояний в целом. Это обуславливает более высокую скорость распыления частиц и, соответственно, скорость охлаждения и кристаллизации частиц, которые также при этом возрастают. В таких условиях происходит формирование наиболее мелких частиц практически одинакового размера. Таким образом, установлено, что изменением давления в рабочей камере-реакторе можно управлять не только фазовым составом синтезируемых материалов, но и дисперсностью частиц, добиваясь преимущественного их содержания в диапазоне до 20 нм.
В качестве альтернативы изменению давления в рабочей камере-реакторе была исследована возможность управления фазовым и гранулометрическим составом за счет использования другого типа газовой атмосферы. Для этого проведены сравнительные эксперименты в азоте и аргоне при одинаковом давлении 1 × 105 Па. XRD-картины синтезированных при этом материалов приведены на рис. 5, а результаты полнопрофильного рентгенофазового анализа сведены в табл. 2.
Рис. 5.
Данные XRD-анализа продуктов, полученных при разных типах газообразной среды при давлении 1 × 105 Па: а – азот, б – аргон.
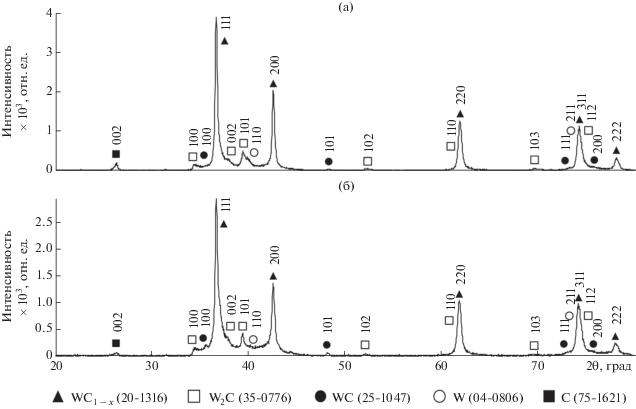
Таблица 2.
Результаты полнопрофильного рентгенофазового анализа продуктов, полученных в газообразной среде азота и аргона (при давлении 1 × 105 Па)
№ | m1, г | m2, г | ξ, % | Параметр | Фазовый состав, % | ||||
---|---|---|---|---|---|---|---|---|---|
WC1 –x | W2C | W | WC | С | |||||
N2 | 0.28 | 0.41 | 64.0 | ω, % | 91.10 | 3.43 | 0.95 | 1.53 | 2.99 |
ОКР, нм | 28.37 | 12.58 | 17.80 | 45.81 | 39.19 | ||||
Δd/d × 10–3, отн. ед. | 3.50 | 2.66 | 3.15 | 1.06 | 4.46 | ||||
a | 4.237 | 2.991 | 3.173 | 2.908 | 2.515 | ||||
c | – | 4.779 | – | 2.836 | 6.762 | ||||
№ | m1, г | m2, г | ξ, % | Параметр | Фазовый состав, % | ||||
WC1 –x | W2C | W | WC | С | |||||
Ar | 0.40 | 0.28 | 56.7 | ω, % | 90.06 | 3.49 | 1.24 | 3.21 | 2.00 |
ОКР, нм | 37.56 | 14.14 | 19.00 | 18.16 | 44.54 | ||||
Δd/d × 10–3, отн. ед. | 4.15 | 2.80 | 3.06 | 1.81 | 4.33 | ||||
a | 4.234 | 3.002 | 3.161 | 2.915 | 2.370 | ||||
c | – | 4.779 | – | 2.847 | 6.889 |
Выбор азота в качестве альтернативной среды обусловлен его широким распространением, высокой энергией связи молекул и, соответственно, инертностью по отношению к вольфраму и углероду. Сравнение полученных дифрактограмм свидетельствует о практической идентичности полученных результатов и подтверждает отсутствие нитридных фаз в продуктах, полученных в атмосфере азота (рис. 5а). При этом чистота выхода кубической фазы карбида вольфрама даже несколько выше, чем в экспериментах с аргоном (табл. 2).
По всей видимости, это также связано с особенностями распыления вольфрам-углеродной плазмы. При реализации процесса синтеза в азотной атмосфере скорость плазменного потока должна быть выше из-за меньшего сопротивления среды. Это будет приводить к увеличению скорости распыления, получению более мелких частиц и созданию благоприятных условий для формирования именно кубической фазы карбида вольфрама. Данные предположения подтверждаются результатами просвечивающей электронной микроскопии и гистограммами распределения частиц по размерам, согласно которым наблюдается уменьшение их среднего размера при распылении плазменного потока в азотсодержащую атмосферу, наполняющую камеру-реактор (рис. 6). Это является положительным результатом проведенных исследований, поскольку подтверждает возможность реализации плазмодинамического синтеза кубического карбида вольфрама высокой чистоты при использовании более дешевого и распространенного газа (N2).
ЗАКЛЮЧЕНИЕ
В работе представлены результаты по плазмодинамическому синтезу материалов с преимущественным содержанием кубического карбида вольфрама в системе на основе коаксиального магнитоплазменного ускорителя. Исследовано влияние параметров газообразной среды (давление, тип) на процесс формирования и развития ударно-волновой структуры плазменной струи электроразрядной плазмы, истекающей в свободное пространство, а также на фазовый и гранулометрический состав синтезируемых при этом материалов. Определены наиболее оптимальные диапазоны давления и тип газообразной среды, позволяющие не только синтезировать кубический карбид вольфрама с чистотой до ~90 мас. %, но и управлять средним размером получаемых частиц.
Список литературы
Tanaka S., Bataev I., Oda H. et al. // Adv. Powder Technol. 2018. V. 29. № 10. P. 2447.
Zheng H.J., Yu A.M., Ma C.A. // Chin. Chem. Lett. 2011. V. 22. № 4. P. 497.
Chen Z., Qin M., Chen P. et al. // Int. J. Hydrogen Energy. 2016. V. 41. № 30. P. 13005.
Курлов А.С., Гусев А.И. // Неорганические материалы. 2006. Т. 42. № 2. С. 156.
Kurlov A.S., Gusev A.I. // Springer Ser. Mater. Sci. 2013. V. 184. P. 34.
Pak A., Sivkov A., Shanenkov I. et al. // Int. J. Refract. Met. Hard Mater. 2015. V. 48. P. 51.
Сивков А.А., Пак А.Я., Рахматуллин И.А. и др. // Российские нанотехнологии. 2014. Т. 9. № 11–12. С. 63.
Герасимов Д.Ю. Электроэрозионный износ канала коаксиального магнитоплазменного ускорителя: Дис. … канд. техн. наук: 05.14.12. Томск: ТПУ, 2005. 190 с.
Шаненкова Ю.Л. Нанесение медного покрытия на алюминиевые контактные поверхности плазмодинамическим методом: Дис. … канд. техн. наук: 05.14.12. Томск: ТПУ, 2019. 157 с.
Шаненков И.И. Плазмодинамический синтез дисперсных оксидов железа с высоким содержанием эпсилон фазы в высокоскоростной струе электроразрядной плазмы: Дис. … канд. техн. наук: 05.14.12, 05.09.02. Томск: ТПУ, 2018. 156 с.
Никитин Д.С. Плазмодинамический синтез ультрадисперсного карбида кремния. Дис. … канд. техн. наук. Томск, ТПУ, 2019.
Рахматуллин И.А. Получение ультрадисперсного карбида бора в сверхзвуковой струе электроразрядной плазмы: Дис. … канд. техн. наук: 05.14.12. Томск: ТПУ, 2015. 156 с.
Лебедев А.Д., Урюков Б.А. Импульсные ускорители плазмы высокого давления. Монография. АН СССР. Сиб. отделение. Ин-т теплофизики, 1990. 292 с.
Златин Н.А., Красильщиков А.П., Мишин Г.И. и др. Баллистические установки и их применение в экспериментальных исследованиях. М.: Наука, 1974. 344 с.
Дополнительные материалы отсутствуют.
Инструменты
Поверхность. Рентгеновские, синхротронные и нейтронные исследования