Поверхность. Рентгеновские, синхротронные и нейтронные исследования, 2021, № 4, стр. 47-58
Фазовый состав и трибологические характеристики поверхностных слоев углеродистых инструментальных сталей после лазерной обработки на воздухе
А. В. Сидашов a, А. Т. Козаков b, *, С. И. Яресько c, **, Н. Г. Каковкина c, Д. С. Мантуров a
a Ростовский государственный университет путей сообщения
344038 Ростов-на-Дону, Россия
b Научно-исследовательский институт физики Южного федерального университета
344090 Ростов-на-Дону, Россия
c Самарский филиал Московского Физического института им. П.Н. Лебедева Российской академии наук
443011 Самара, Россия
* E-mail: kozakov_a@mail.ru
** E-mail: yarsi54@gmail.com
Поступила в редакцию 15.04.2020
После доработки 17.06.2020
Принята к публикации 20.06.2020
Аннотация
Представлены результаты исследований фазового состава оксидного слоя, образующегося на поверхности углеродистых инструментальных сталей У8 и У10 после лазерной обработки на воздухе с использованием квазинепрерывного лазерного источника. Методом рентгеновской фотоэлектронной спектроскопии на системе анализа поверхности фирмы SPECS с использованием AlKα1,2-линии получены данные о строении границ раздела оксид–металл. Установлено, что толщина полностью окисленных поверхностных слоев составляет 38.7 и 99.0 нм, соответственно, для сталей У8 и У10. Показано, что толщина переходного слоя, расположенного на границе раздела с немодифицированным объемом стали и состоящего из оксида FeO и атомов железа для стали У10, примерно в два раза меньше, чем у стали У8 (составляет 81.0 нм). Определен состав оксидов поверхности сталей после лазерной обработки. Для стали У8 поверхность представляет собой в основном пленку вюстита, наличие которой определяет низкие характеристики износа поверхности зоны лазерного воздействия, напротив, более толстый оксидный слой модифицированной стали У10, содержащий оксиды Fe2O3, Fe3O4 с лучшими прочностными характеристиками, обеспечивает более высокую износостойкость поверхности стали У10 после лазерной обработки при трибоиспытаниях. Для стали У10 скорость износа модифицированной поверхности уменьшается более чем в два раза, в то время как для стали У8 этот показатель составляет ~17%.
ВВЕДЕНИЕ
Лазерное воздействие в зависимости от параметров, схем и способов обработки, газовой среды, элементного состава, а также способов объемной термообработки сталей оказывает многофакторное влияние на состояние их поверхностного и приповерхностных слоев, которое служит предметом многочисленных исследований [1–4]. Для улучшения трибологических свойств материалов наряду с методами лазерной модификации [1–4] эффективно лазерное текстурирование поверхности с использованием различных технологических схем и методов прямой лазерной обработки (ЛО) [5–9]. Метод успешно применяется для конструкционных материалов [5–7], в том числе и керамик (например, на основе карбида кремния [6, 7]), и обеспечивает снижение коэффициента трения и повышение эксплуатационных характеристик деталей машин и механизмов.
Одним из существенных результатов лазерного воздействия, не связанного с изменением микрорельефа поверхности, является образование на поверхности стали тонкой оксидной пленки при ЛО в воздушной среде. Исследования кинетики нагрева металлов, анализ роста, структуры и оптических свойств оксидных слоев, образующихся при нагреве металлов лазерным излучением (ЛИ), позволили уточнить физические представления о термохимических механизмах взаимодействия интенсивного ЛИ с веществом [10–13] и существенно продвинуться в понимании происходящих процессов окисления металлов.
Позднее [14–20] при исследовании влияния ЛИ на кинетику образования оксидных пленок на поверхности легированных сталей (AISI 329 (аналог – сталь 08X25H4M2), AISI 304 (аналог – сталь 08Х18Н10), 9ХС, Р6М5, ст. 45 и др.) установлено, что в зависимости от элементного состава сталей меняется как толщина пленок, так и фазовый состав по толщине пленки, а также соотношение между оксидами железа различной валентности и оксидами легирующих элементов. Влияние ЛО на воздухе на поведение режущего инструмента из теплостойких сталей типа Р9K5 выражается (прежде всего) в увеличении стабильности свойств поверхности зоны лазерного воздействия (ЗЛВ) при резании в зоне контакта инструмент–деталь [21]. Лазерная обработка на воздухе не только стабилизирует процесс изнашивания инструмента и минимизирует скорость его износа, но и приводит к существенному расширение диапазона режимов резания, при котором достигается его наименьший износ.
Диапазон толщин оксидных пленок, образующихся на массивных металлических подложках при их нагреве без оплавления лазерным импульсом миллисекундной длительности, достаточно широк: от покровных (≤0.1 нм, для хрома и тантала) до достаточно толстых (~100 нм, для титана и сталей) [22]. При воздействии непрерывного ЛИ толщина оксидных пленок может достигать десятка микрометров [23] и более. Известно, что оксидные пленки металлов, имеющие толщину 100–200 нм, играют большую роль в снижении коэффициента трения в зоне контакта [21, 24–28], понижении интенсивности поля напряжений на рабочих поверхностях инструмента, температурной и силовой нагруженности режущего клина и увеличении стойкости инструмента [3, 28]. Общепризнано, что формирование защитных оксидных образований препятствует сильному износу и снижает трение [26, 27]. Степень этого явления зависит от толщины и состава слоев оксида. Влияние пленок на износ металлорежущего инструмента многогранно. По данным К.Б. Усманова и Г.И. Якунина [26] поверхностные пленки могут также вызывать упрочнение металла за счет подавления поверхностных источников дислокаций и за счет растворения части пленки в сильно деформированных поверхностных слоях и последующего блокирования дислокаций “атмосферами Коттрела”. При этом “барьерный эффект” пленки так же, как и упрочненного поверхностного слоя, зависит от температурно-скоростных условий деформирования. Вторичные структуры поверхности ЗЛВ в виде пленок оксидов наряду со структурно-модифицированным слоем, простирающимся вплоть до глубин 900 мкм (в ряде случаев и больше), оказывают влияние на эксплуатационные характеристики сталей различного состава, назначения, структуры, в том числе и углеродистых инструментальных сталей [4, 29–31].
В этой связи представляется интересным изучение фазового состава оксидов железа поверхности ЗЛВ и его распределения по толщине в тонком поверхностном оксидном слое, сформированном лазерным излучением одинаковой мощности, не только в инструментальных теплостойких сталях [15, 16], но и в инструментальных углеродистых сталях, отличающихся содержанием лишь одного элемента – углерода. Таковыми являются углеродистые стали У8 и У10, широко применяющиеся при изготовлении инструментов, работающих в условиях, не вызывающих разогрева режущей кромки, и ряда износостойких деталей. Наиболее часто эти стали используются для изготовления метрологических средств контроля формы и размеров деталей и инструмента (например, калибров различного назначения). К качеству изготовления калибров предъявляются повышенные требования по точности изготовления, износостойкости, постоянству рабочих размеров. Лазерная обработка является эффективным методом сохранения высокой износостойкости поверхностных слоев указанных сталей и выполнения вышеуказанных требований.
Целью настоящей работы является исследование структуры и фазового состава тонких оксидных пленок поверхности ЗЛВ инструментальных углеродистых сталей У8 и У10, анализ распределения по глубине структурных составляющих оксидов и их влияния на трибологические характеристики поверхности ЗЛВ.
ЭКСПЕРИМЕНТАЛЬНАЯ ЧАСТЬ
Лазерная обработка (ЛО) образцов сталей У8 и У10 размерами 10 × 10 × 1.5 мм проводилась с использованием оптоволоконного иттербиевого квазинепрерывного лазерного источника ЛК‑150/1500-QCW-AC с длиной волны 1.07 мкм. Мощность лазерного излучения составляла 130 Вт, скорость обработки – 3 мм/с. Во всех экспериментах частота следования импульсов была равна 25 кГц при длительности единичного импульса 20 мкс. Режимы облучения выбирались таким образом, чтобы исключить оплавление поверхности. Лазерный луч передвигался по поверхности образца параллельно одной из сторон, формируя полосы шириной 0.6–0.8 мм, расстояние между центрами полос составляло ~0.4–0.5 мм. В результате вся облученная область образца представляла собой достаточно однородную структуру. На рис. 1а представлен внешний вид поверхности образца после ЛО, а на рис. 1б – изображение микрорельефа участка поверхности ЗЛВ, полученное в растровом электронном микроскопе (РЭМ).
Рис. 1.
Поверхность образца (сталь У8) после ЛО: a – внешний вид, ×5; б – РЭM-изображение микрорельефа поверхности.
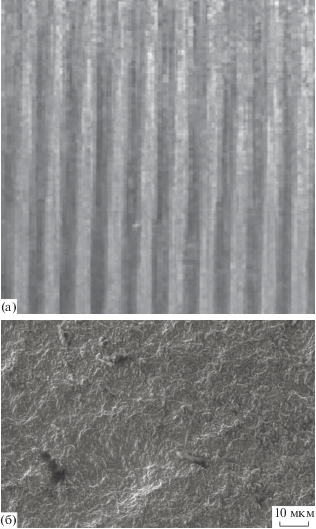
Ионное профилирование образцов осуществлялось в камере предварительной обработки системы анализа поверхности SPECS. Ионная пушка была прикреплена к фланцу камеры предварительной обработки таким образом, что облучение ионным пучком проводилось строго вертикально. Профилирование ионами Ar+ осуществлялось в течение 10–13 ч с интервалом 5–10 минут при следующих параметрах работы ионной пушки: Uуск = 2.99 кэВ, ток пучка I = 10 мА и давление аргона не более 4.5 × 10–3 Па.
Качественный и количественный анализ химического состава поверхности и приповерхностных слоев образцов углеродистых инструментальных сталей осуществляли методом рентгеновской фотоэлектронной спектроскопии (РФЭС) с использованием системы анализа поверхности (SPECS, Германия). В качестве возбуждающего излучения была использована AlKα – рентгеновская монохроматизированная линия с энергией 1486.6 эВ. Энергетическое разрешение анализатора составляло 0.45 эВ на линии Ag3d3/2. В качестве внешнего стандарта для определения энергий связи была использована линия С1s углерода, энергию которой принимали равной 285 эВ. Вакуум при съемке поддерживался на уровне 8 × × 10–8 Па.
Микроструктурный анализ выполняли на поперечных шлифах. Для выявления структуры основного металла и структуры ЗЛВ использовали 4% раствор HNO3 в этиловом спирте. Металлографический анализ проводили с помощью оптического микроскопа NEOPHOT-30 (Carl Zeiss) и растрового электронного микроскопа EVO 50 EP при увеличении от 100 до 14 000 крат.
Трибологические исследования осуществлялись с помощью трибометра версии 6.2.8 фирмы “Anton Paar GmbH” в режиме линейного движения в условиях окружающей среды при относительной влажности 50%. Полная амплитуда возвратно-поступательного движения составляла 1 мм, частота колебаний – 10 Гц при вертикальной нагрузке 5 Н. Контртело представляло собой шар диаметром 6 нм из корунда Al2O3.
Fe2p-, O1s- и C1s-РФЭС-спектры поверхности ЗЛВ сталей У8 и У10
Спектры внутренних 2p-уровней атомов железа для сталей У8 и У10, полученные при различном времени ионного профилирования поверхности после ЛО, представлены на рис. 2 и 3 соответственно. Съемка спектров осуществлялась каждые 5 мин в течение первого часа травления, затем с интервалом в 10 мин до тех пор, пока концентрация кислорода не составила менее 7 ат. %. На рис. 2 и 3 представлены не все полученные спектры, а лишь те, профили которых демонстрируют наиболее существенные детали процесса окисления железа.
Рис. 2.
Fe2p-РФЭС-спектры, полученные после травления ЗЛВ стали У8: 1 – исходная поверхность, 2 – 30 мин, 3 – 4 ч, 4 – 9 ч, 5 – 12 ч.
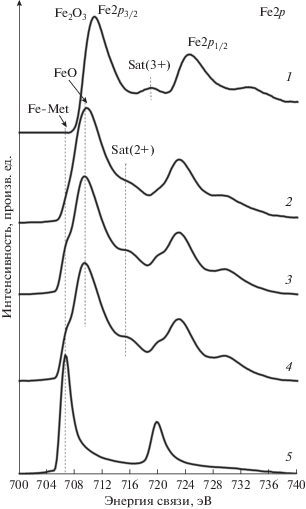
Рис. 3.
Fe2p-РФЭС-спектры, полученные после травления ЗЛВ стали У10: 1 – исходная поверхность, 2 – 4 ч, 3 – 7 ч, 4 – 9 ч, 5 – 10 ч.
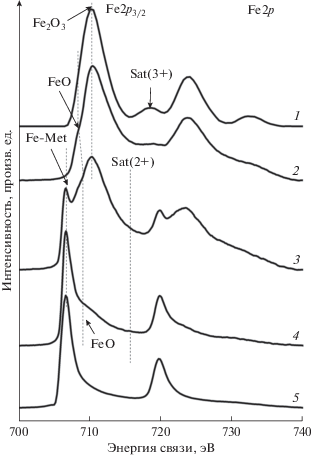
Fe2p-спектры (рис. 2 и 3) состоят в основном из двух пиков Fe2p3/2 и Fe2p1/2, отвечающих эмиссии электрона из 2p3/2 и 2p1/2-уровней железа, разделенных спин-орбитальным взаимодействием. Кроме этих основных линий на спектрах имеются детали тонкой структуры, для обозначения которых на рисунках приведены вертикальные штриховые линии (рис. 2 и 3). Эти линии относятся к т.н. сателлитам переноса заряда Sat. (+2) и Sat. (+3), по которым легко идентифицировать находится ли ион железа в двухвалентном или трехвалентном состоянии [16, 32]. Энергетическое положение пиков Fe2p3/2 и Fe2p1/2 служит при этом дополнительным признаком, позволяющим различить, в окисленном или не окисленном состоянии находится железо, а также определить степень окисления.
Компонента Fe2p3/2-уровня, имеющая энергию в диапазоне 706.7–707.8 эВ, согласно [33, 34] относится к неокисленному железу. Компонента Fe2p3/2-уровня с энергией в диапазоне 710.3–710.7 эВ – к оксиду Fe3O4, компонента с энергией в диапазоне 711.0–711.5 эВ – к Fe2O3 и компонента с энергией 709.5 эВ – к FeO. При этом дополнительным признаком присутствия магнетита Fe3O4 в исследуемом слое является наличие в профиле Fe2p3/2,1/2-спектра характерной особенности с энергией, отстоящей от максимума спектра на расстоянии 1.8 эВ в сторону меньших энергий связи и отсутствие сателлита переноса заряда Sat. (+3) с энергией около 718.5 эВ [32, 35].
Учитывая вышесказанное, следует отметить, что на поверхности образцов сталей У8 и У10, сформированной в результате ЛО, а также в нижерасположенных слоях ионы железа находятся в различном окисленном состоянии. Более детальный анализ показывает, что распределения химических связей железа с кислородом по глубине окисленного слоя железа в сталях У8 и У10, определяемые по энергетическому положению и тонкой структуре Fe2p3/2,1/2-спектров, не идентичны (рис. 2 и 3), хотя обе эти стали являются аналогами. Компонента Fe–Ме, свидетельствующая о наличии в исследуемом слое железа в металлическом состоянии, для стали У8 появляется после времени травления, равного 4 ч, а для стали У10 – 6 ч. Это может быть индикатором большей толщины оксидного слоя на поверхности ЗЛВ стали У10 по сравнению со сталью У8. При этом следует отметить (рис. 4), что и глубина ЗЛВ с модифицированной структурой после ЛО для стали У10 (~100 мкм) также больше, чем для стали У8 (~60 мкм).
На рис. 5 приведены O1s-рентгеновские фотоэлектронные спектры, полученные с поверхности и по глубине сталей У8 и У10 после ЛО. Видно (рис. 5), что вблизи поверхности рентгеновские фотоэлектронные спектры кислорода обеих сталей (спектр 4 для стали У8 и спектр 8 для стали У10) имеют по три компоненты A, B и C. Компонента А имеет энергию в диапазоне 529.9–530.2 эВ. Эту компоненту можно отнести к кислороду одного из оксидов железа (для зарегистрированных на поверхностях обеих сталей оксидов железа энергия O1s-линии меняется незначительно) [33, 34]. Компоненту В при энергии ~531.7–531.9 эВ мы относим к адсорбированному кислороду, а компоненту С при энергии в диапазоне 533.1–534.0 эВ – к кислороду воды и/или гидроксильной группе [32, 33].
Рис. 5.
O1s-РФЭС-спектры, полученные после травления ЗЛВ стали У8 (слева) и стали У10 (справа): 1 – 8 ч, 2 – 4 ч, 3 – 15 мин, 4 – исходная поверхность, 5 – 10 ч, 6 – 6 ч, 7 – 3 ч, 8 – исходная поверхность.
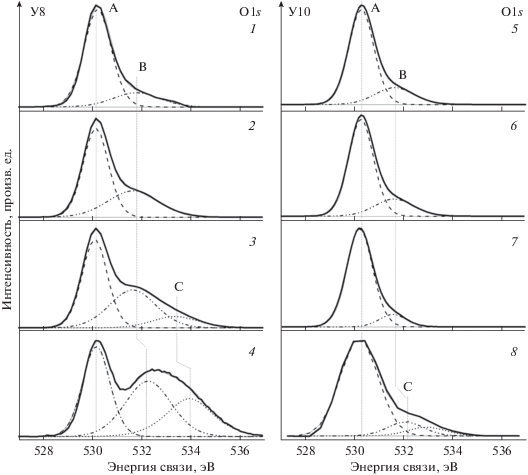
В дальнейшем по мере стравливания с поверхности атомов элементов поверхности в спектре кислорода остаются только две компоненты: А, относящаяся к оксиду железа, и B (слабоинтенсивная), относящаяся к адсорбированному кислороду. При дальнейшем травлении компоненту B не удается удалить полностью. Следовательно, она может относиться либо к кислороду, растворенному в сталях, либо к кислороду, находящемуся на межзеренных границах в сталях.
На рис. 6 приведены C1s-рентгеновские фотоэлектронные спектры, полученные с поверхности и по глубине ЗЛВ стали У8.
Рис. 6.
С1s-РФЭС-спектры, полученные после травления ЗЛВ стали У8: 1 – исходная поверхность, 2 – 30 мин, 3 – 9 ч, 4 – 13 ч.
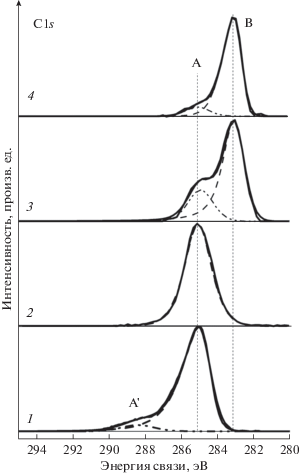
Углерод на исходной поверхности находится в одном состоянии, соответствующем углеводородному загрязнению с Есв = 285 эВ (компонента А). Компонента A' относится к связям углерода с OH-группами. В процессе ионного травления в спектре углерода при сохранении компоненты A, относящейся к углеводородным загрязнениям, появляется ещё компонента B с энергетическим положением около 283.0 эВ. Данную компоненту можно отнести к карбидной структурной составляющей сталей, присутствующей в зоне закалки после ЛО согласно данным металлографического анализа.
Следует отметить, что уже после 20 мин ионного травления общее количество зафиксированного углерода (от загрязнений и в связи с металлом сплава) в анализируемом поверхностном слое становится существенно меньше. На глубине, соответствующей 9 и 13 ч ионного травления, содержание углерода уменьшается примерно до 0.2 ат. %. Изменение C1s-спектра по глубине для стали У10 происходит аналогично. На поверхности он имеет две компоненты, относящиеся к углеводородному загрязнению с Есв = 285 эВ (основная) и к связям углерода с OH-группами (слабоинтенсивная). По мере исчезновения основной компоненты начинает появляться компонента с энергией связи около 283.0 эВ, которую мы относим к карбидной структурной составляющей сталей.
Фазовый состав оксидных слоев по глубине ЗЛВ для сталей У8 и У10
Распределения концентраций железа, кислорода и углерода по глубине оксидных слоев, образующихся на поверхности ЗЛВ сталей У8 и У10, приведены на рис. 7a, 7б соответственно.
Рис. 7.
Концентрации элементов по глубине в зависимости от времени ионного травления после ЛО: a – сталь У8, б – сталь У10.
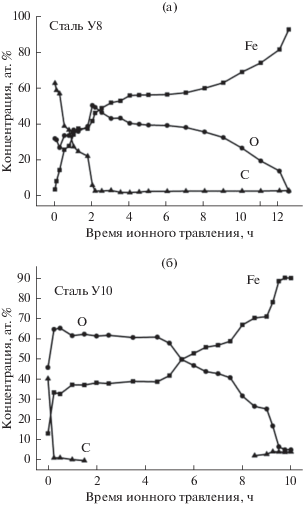
Сравнение представленных данных свидетельствует о различии в сформированных оксидных слоях на поверхности обеих сталей уже на стадии исследования концентрационных зависимостей по глубине. Углерод и кислород на поверхности представлены типичными для сталей, находящихся в условиях воздействия окружающей среды, поверхностными загрязнениями (хотя на их концентрацию может влиять и содержание углерода в сталях, более правильно, обогащение им поверхности под действием лазерного излучения). Кроме того, их концентрации также определяются видом оксида, сформировавшегося в условиях высокоскоростного лазерного нагрева. В самом поверхностном слое концентрации углерода, кислорода и железа для сталей У8 и У10 равны 63, 32, 4 ат. % (рис. 7а) и 40, 46 и 14 ат. % (рис. 7б) соответственно. Содержание углерода и кислорода по глубине уменьшается для обеих сталей. Однако в стали У8 содержание углерода становится близким к объемному (3.5 ат. %) только на глубине, соответствующей 2 ч ионного травления, а для стали У10 оно резко уменьшается и становится равным объемному уже на глубине, соответствующей 0.3 ч ионного травления.
Содержание кислорода встали У8 после удаления поверхностных загрязнений по углероду и кислороду, начиная с 1 и до 2 ч ионного травления, совпадает с содержанием железа (рис. 7а), что может свидетельствовать о формировании в этом слое соединения FeO. После 2 ч травления содержание кислорода в исследуемом оксидном слое постепенно уменьшается, оставаясь меньше концентрации железа, что говорит об изменении степени окисления железа по глубине оксидного слоя. Поведение концентрационных зависимостей по железу и кислороду для стали У10 отличается по сравнению со сталью У8. После удаления поверхностных загрязнений до точки травления 5.5 ч содержание кислорода превышает содержание железа в 1.6 раза. Эта цифра близка к отношению концентраций кислорода и железа в оксиде Fe2O3.
Для более точной оценки химического состояния железа Fe2p-спектры железа сталей У8 и У10, полученные в течение всего времени травления по глубине окисного слоя, были разложены на компоненты, отвечающие той или иной валентности железа. Процедура разложения описана в работах [16, 32]. На рис. 8a и 8б приведены результаты этого разложения, анализ которых позволяет существенно уточнить данные, представленные на рис. 7a, 7б.
Рис. 8.
Распределение оксидов железа по глубине оксидных слоев после ЛО: а – сталь У8, б – сталь У10.
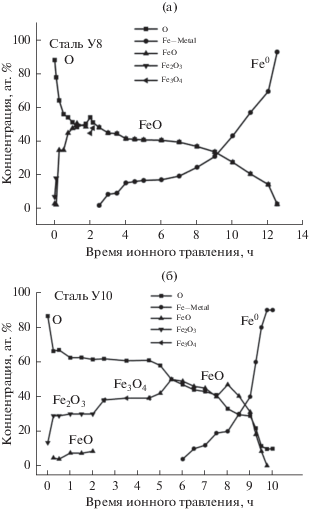
Изучение распределения оксидов железа по глубине оксидных слоев после ЛО показывает, что на поверхности обеих сталей атомы железа находятся в двух окисленных состояниях Fe2+ и Fe3+, свидетельствующих о наличии двух оксидов FeO и Fe2O3 (рис. 8а, 8б). Для стали У8 слой, в котором сосуществуют оксиды FeO и Fe2O3, очень тонок. Но для стали У10 поверхностный слой, содержащий оксиды FeO и Fe2O3, простирается вглубь до 2 ч ионного травления.
Для стали У8 после 15 мин травления и до 2 ч (включительно) оксидный слой представляется состоящим лишь из железа в окисленном состоянии Fe2+, что согласуется с данными, приведенными на рис. 7a. Состояние поверхности, соответствующее промежутку времени травления между 2 и 2.5 ч, представлено тонким слоем оксида Fe3O4. Начиная с 2.5 ч травления, на исследуемой глубине впервые появляется чистое железо и железо в степени окисления Fe2+.
В стали У10 также имеется тонкий слой Fe3O4, расположенный выше слоя, где методом РФЭС обнаруживается чистое железо. Под слоем состава Fe3O4 находится слой, состоящий из смеси оксида FeO и железа в нулевой степени окисления, т.е. Fe–Ме, в котором концентрация оксида FeO постепенно уменьшается, а концентрация железа Fe0 увеличивается, пока не станет равной концентрации железа в объеме стали.
ОБСУЖДЕНИЕ РЕЗУЛЬТАТОВ
Лазерная обработка обоих видов сталей привела к модификации их фазового состава на глубинах до 100 мкм, что находится в согласии с известными литературными данными [1–4]. Особый интерес представляет анализ установленных изменений тонкого поверхностного слоя, связанных с образованием индуцированных лазерным излучением вторичных оксидных структур поверхности ЗЛВ. Факторы, обуславливающие изменение структуры сталей на поверхности ЗЛВ, отличаются от факторов, определяющих ее изменение по глубине зоны термического влияния. В первом случае нагретый выше температуры фазовых превращений металл мог взаимодействовать с кислородом воздуха. Приповерхностные слои металла окислялись, образуя оксиды различной стехиометрии, формульный состав которых, толщины и относительное расположение представлены на рис. 8а и 8б для сталей У8 и У10 соответственно.
Как показано выше, несмотря на то, что концентрационные кривые на рис. 7a, а также кривые, характеризующие фазовый состав оксидов (рис. 8а, 8б), количественно отличаются друг от друга, качественная картина окисления сталей при ЛО примерно одинакова. Основываясь на данных рис. 8, на рис. 9 схематично представлено взаимное расположение и толщины различных оксидов на сталях У8 и У10.
Абсолютные глубины расположения оксидных слоев установить достаточно сложно: они зависят от многих факторов [33], определяются временем работы ионной пушки, плотностью ионного пучка и т.д. Согласно ранее полученным данным [16], скорость ионного травления сталей с помощью используемой ионной пушки равна ~0.3 нм/мин. Неопределенность вышеуказанной скорости ионного травления при профилировании глубины составляет около 1%. Используя это значение и зная время прохождения оксидных слоев (например, рис. 8) при ионном травлении, были определены толщины оксидных слоев в сталях У8 и У10, обсуждаемые ниже.
Видно, что в обеих сталях приповерхностный слой состоит из оксидов FeO и Fe2O3 (рис. 8, 9). Для стали У8 этот слой смеси оксидов очень тонок (1.5 нм), что практически равно глубине анализа методом РФЭС. Для стали У10 этот слой значительно толще и достигает 36.0 нм. Для стали У8 с ростом глубины смесь оксидов FeO и Fe2O3 сменяется слоем оксида FeO (34.5 нм), сразу за которым находится тонкий слой оксида состава Fe3O4 (2.7 нм). Последний сменяется слоем (186.3 нм), состоящим из смеси оксида FeO и атомов железа Fe0 (рис. 9). Общая толщина только оксидов на поверхности стали У8 составляет всего 38.7 нм, но вместе с переходным слоем из оксида FeO и атомов железа Fe0 на границе с основой стали толщину окисленного слоя стали У8 можно оценить равной 225.0 нм.
Качественно картина расположения оксидов на поверхности стали У10 практически не отличается от таковой для стали У8, но наблюдается количественная разница в толщинах оксидных слоев с одинаковым фазовым составом (рис. 9). Так, слой состава Fe3O4 стали У10 существенно толще и составляет 45.0 нм. Слой состава FeO стали У10 находится ниже слоя Fe3O4 и имеет толщину 18.0 нм. Он граничит с переходным слоем, расположенным на границе раздела с немодифицированным объемом стали У10, и состоящим из оксида FeO и атомов железа Fe0 с толщиной, меньшей примерно в два раза, чем у стали У8 и равной 81.0 нм. Толщина только оксидов на поверхности стали У10 более чем в два раза превышает таковую для стали У8 и составляет 99.0 нм. Однако общая толщина оксидного слоя стали У10 вместе с переходным слоем из оксида FeO и атомов железа Fe0 на границе с основой стали несколько меньше по сравнению с общей толщиной слоя оксидов стали У8 и составляет 180.0 нм.
Установленное расположение слоев оксидов, сформировавшихся в условиях высокотемпературного, высокоскоростного лазерного нагрева, достаточно хорошо коррелирует с взаимным расположением оксидных слоев, полученных при высокотемпературном изотермическом окислении [36].
Наиболее существенное отличие окисления в условиях лазерного нагрева от изотермического состоит в том, что скорость лазерного окисления зависит не только от температуры мишени, но и от интенсивности падающего ЛИ [37]. В результате полный диффузионный поток, являющийся движущей силой окисления, будет определяться не только слагаемым, пропорциональным градиенту концентрации (этот поток приводит к закону Вагнера [36]), но и слагаемым, пропорциональным градиенту температуры, величина которого в основном определяется коэффициентом термо-эдс оксида (α). Для значений термо-эдс меньше нуля (например, для Fe3O4 α = −430 мкВ/град и для FeO α = −500 мкВ/град, в то время как для Fe2O3 α = 380 мкВ/град [38]) происходит ослабление окисления с ростом интенсивности излучения, и термодиффузионные процессы не оказывают влияния на скорость лазерного окисления. Поэтому можно считать, что процесс образования оксидов FeO и Fe3O4 подчиняется параболическому закону Вагнера:
Предполагая, что слои оксидов на железе растут параболически и пропорционально, оценим толщину оксидных пленок железа, например, пленки оксида Fe3O4 на стали У10. Согласно оценкам, для полученных экспериментально параметров ЗЛВ (рис. 4б) характерное время действия лазерного источника для достижения требуемой глубины упрочненного слоя составляет ~1.5 мс. В этом случае при температуре поверхности на 15−20% меньше температуры плавления стали, что соответствует реальным условиям проведения эксперимента, получаем для пленки оксида Fe3O4 значение для толщины, ограниченное диффузионными процессами, равное 34.6−48.5 нм, что находится в хорошем согласии с экспериментальными данными.
Полученные оценки также хорошо коррелируют с толщинами оксидных слоев, сформированными на поверхностях легированной инструментальной стали 9ХС и быстрорежущей инструментальной стали Р6M5 после импульсной ЛО [3, 16], и согласуются с результатами расчета [22], согласно которым на массивных металлах и сталях при их нагреве без плавления импульсом миллисекундной длительности образуются достаточно толстые (~100 нм) оксидные пленки.
ТРИБОЛОГИЧЕСКИЕ ХАРАКТЕРИСТИКИ ОКСИДОВ ПОВЕРХНОСТИ ЗЛВ
Для оценки степени влияния фазового состава оксидов поверхности ЗЛВ, полученных на сталях У8 и У10, на их трибологические характеристики были проведены испытания на изнашивание, результаты которых представлены на рис. 10 и 11 для сталей У8 и У10 соответственно. Измерения проводились как для окисленной поверхности после лазерной модификации, так и для поверхностей сталей в исходном необлученном состоянии. На рис. 10 и 11 приведены зависимости коэффициентов трения тестового шара из корунда (Al2O3) для модифицированных (кривые 1) и исходных (кривые 2) поверхностей обеих сталей У8 и У10 соответственно. На вставках a, б этих рисунков приведены изображения следа износа на поверхности тестового шара при скольжении по модифицированной и исходной поверхностям соответственно.
Рис. 10.
Коэффициенты трения в зависимости от пройденного пути: 1 – для модифицированной поверхности стали У8, 2 – для исходной поверхности стали У8; a, б – изображения следа износа на поверхности тестового шара при скольжении по модифицированной и исходной поверхности соответственно.
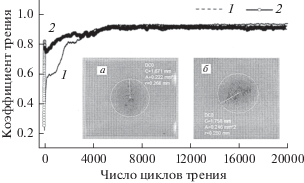
Рис. 11.
Коэффициенты трения в зависимости от пройденного пути: 1 – для модифицированной поверхности стали У10, 2 – для исходной поверхности стали У10; a, б – изображения следа износа на поверхности тестового шара при скольжении по модифицированной и исходной поверхности соответственно.
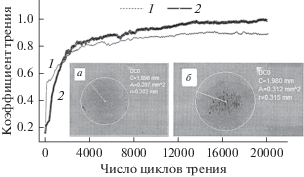
Некоторые трибологические данные, позволяющие вместе с данными рис. 10 и 11 оценить влияние оксидных слоев на процесс трения в зависимости от их фазового состава, приведены в табл. 1.
Таблица 1.
Трибологические характеристики процесса трения, проводимого по схеме шар–плоскость, для корундового шара и поверхности сталей У8 и У10
Марка стали, состояние обработки | Скорость износа стали, V × 10–10, мм3/Н/м |
Скорость износа шара, V × 10–10, мм3/Н/м |
Площадь следа износа на поверхности шара, мм2 | Коэффициент трения, μ |
---|---|---|---|---|
У8, исходная | 11.7 | 3.2 | 246 | 0.92 |
У8, после ЛО | 9.7 | 2.6 | 222 | 0.94 |
У10, исходная | 16.9 | 4.4 | 312 | 0.92 |
У10, после ЛО | 7.10 | 5.2 | 287 | 0.88 |
Из-за малой толщины оксидных пленок невозможно измерить их микротвердость непосредственно на поверхности сталей. Имеющиеся литературные данные [38] по прочностным характеристикам отдельных оксидов представлены в табл. 2. Видно, что самыми низкими значениями твердости обладает оксид FeO (табл. 2), который по результатам РФЭС-анализа непосредственно граничит с немодифицированным объемом сталей. Область его существования по глубине вместе с железом Fe0 по объему примерно в два раза больше у стали У8 (186.3 нм), чем у стали У10 (81.0 нм). Фактически для стали У8 оксид FeO является основным компонентом по всей толщине окисленного модифицированного слоя. По прочностным характеристикам оксид Fe3O4 незначительно превосходит оксид FeO (табл. 2), но его толщина для стали У8 невелика и составляет 2.7 нм (рис. 9). Наконец, самым большим значением микротвердости обладает оксид Fe2O3, образующий самый верхний слой стали У8 толщиной 1.5 нм. Толщины оксидов Fe2O3 и Fe3O4 стали У10 существенно превышают толщины соответствующих оксидов стали У8 и равны в сумме 81.0 нм (рис. 8, 9). Поэтому для стали У8 достаточно 4000–5000 циклов трения (рис. 10), чтобы произошло истирание тонкого оксидного слоя и коэффициент трения модифицированной стали приблизился к его значению для немодифицированной стали У8. В то же время более толстый оксидный слой модифицированной стали У10, содержащий оксиды Fe2O3, Fe3O4 с лучшими прочностными характеристиками, обеспечивает более высокую сопротивляемость изнашиванию, чем необлученная поверхность стали на протяжении 50 000 циклов трения (графики на рис. 10 и 11 приведены только для 20 000 циклов трения).
Таблица 2.
Прочностные характеристики оксидов железа [38]
Оксид, формула, минерал |
Твердость по минералогической шкале | Микротвердость | |
---|---|---|---|
Микротвердость, МПа | Нагрузка, P × 10–5, Н | ||
FeO, вюстит | 5.0 | 5393.85–5398.07 | 49 035–98 070 |
Fe3O4, магнетит | 5.5–6.5 | 4677.94–7884.83 | 49 035 |
Fe2O3, гематит | 6.75 | 10 983.84–6864.9 | 49 035 |
Для стали У8 наличие пленки вюстита на поверхности ЗЛВ определяет ее низкие износные характеристики. Напротив, для стали У10 скорость износа модифицированной поверхности при наличии оксидов Fe2O3, Fe3O4 с более высокими прочностными характеристиками уменьшается более чем в два раза, в то время как для стали У8 этот показатель составляет ~17% (табл. 1).
Представленные результаты свидетельствуют о том, что на трибомеханические характеристики и динамику изнашивания модифицированной поверхности существенное влияние оказывает слой оксидов на поверхности ЗЛВ, имеющий сложное строение по глубине, при этом его структура определяет износные характеристики модифицированной поверхности.
Нагрев поверхности сталей лазерным излучением на воздухе кроме окислительных процессов инициирует в приповерхностных слоях диффузионные процессы, приводящие к аустенизации с полным растворением карбидной фазы, а на стадии охлаждения – к закалке с образованием мартенсита и остаточного аустенита. Принимая во внимание, что в зоне закалки микротвердость превосходит микротвердость основного металла на 40–45%, можно предположить, что трибологические характеристики поверхности сталей после ЛО определяются совместным влиянием как пленок оксидов, так структурно модифицированной зоны. Причем в зависимости от условий нагружения превалирующее влияние на изнашивание оказывает та или иная структурная составляющая ЗЛВ.
ЗАКЛЮЧЕНИЕ
Для углеродистых инструментальных сталей У8 и У10 выполнено исследование структуры и фазового состава оксидных пленок поверхности ЗЛВ, установлено распределение по глубине фазовых составляющих оксидного слоя и их влияние на износные характеристики поверхности при ее модификации на воздухе. В результате проведенных экспериментов:
1) методом РФЭС с ионным травлением показано, что оксидные пленки на поверхности ЗЛВ обеих сталей имеют качественно совпадающее слоистое строение, однако при этом существуют количественные отличия в толщинах отдельных фазовых слоев;
2) установлено, что фазовые составляющие оксидных пленок располагаются по направлению от основного металла к поверхности в следующей последовательности: наиболее глубоко расположен слой, содержащий FeO и атомы железа, далее следует слой оксида состава Fe3O4 и, наконец, – внешний слой, преимущественно состоящий из смеси оксидов FeO и Fe2O3. Толщины полностью окисленных поверхностных слоев в сталях У8 и У10 составляют ~38.7 и 99.0 нм соответственно. Однако общая толщина оксидного слоя вместе с переходным слоем из оксида FeO и атомов железа Fe–Ме больше на 20% для стали У8, чем для стали У10, и составляет 225.0 нм;
3) установлено, что для стали У8 поверхностная пленка вюстита (FeO) толщиной 34.5 нм определяет низкие износные характеристики поверхности ЗЛВ, напротив, более толстый оксидный слой модифицированной стали У10, содержащий оксиды Fe2O3, Fe3O4 с лучшими прочностными характеристиками, обеспечивает более высокую износостойкость стали У10 после ЛО. Для модифицированной поверхности стали У10 скорость износа уменьшается более чем в два раза, в то время как для стали У8 этот показатель составляет всего 17%;
4) показано, что трибологические свойства поверхности стали после ЛО определяются комбинированным воздействием как оксидных пленок, так и структурно модифицированной зоны. Наличие износостойких структурных составляющих после лазерной обработки обусловливает повышение деформационных характеристик сталей.
Список литературы
Ready John F., Farson D.F., Feeley T. LIA Handbook of Laser Materials Processing. Berlin: Springer, 2001. 715 p.
Steen W.M., Mazumder J. Laser Material Processing. London: Springer, 2010. 558 p.
Козаков А.Т., Яресько С.И., Сидашов А.В. Модификация и анализ поверхности сталей и сплавов. Ростов н/Д: Изд-во ФГБОУ ВПО РГУПС, 2015. 378 с.
Григорьянц А.Г., Шиганов И.Н., Мисюров А.И. Технологические процессы лазерной обработки: учеб. пособие для вузов / Ред. Григорьянц А.Г. М.: Изд-во МГТУ им. Н.Э. Баумана, 2006. 664 с.
Mao B., Siddaiah A., Liao Y., Menezes P.L. // J. Manuf. Process. 2020. V. 53. P. 153. https://doi.org/10.1016/j.jmapro.2020.02.009
Murzin S.P., Balyakin V.B. // Opt. Laser. Technol. 2017. V. 88. P. 96. https://doi.org/10.1016/j.optlastec.2016.09.007
Murzin S.P., Balyakin V.B., Melnikov A.A., Vasiliev N.N., Lichtner P.I. // Comput. Opt. 2015. V. 39(1). P. 64. https://doi.org/10.18287/0134-2452-2015-39-1-64-69
Vilhena L.M., Sedlaček M., Podgornik B., Vižintin J., Babnik A., Možina J. // Tribol. Int. 2009. V. 42. P. 1496. https://doi.org/10.1016/j.triboint.2009.06.003
Shariff S.M., Koppoju S., Pal T.K., Gadhe P, Joshi S.V. // Materials Sciences and Applications. 2015. V. 6. P. 889. https://doi.org/10.4236/msa.2015.610091
Бункин Ф.В., Кириченко Н.А., Лукьянчук Б.С. // УФН. 1982. Т. 138. Вып. 1. С. 45. https://doi.org/10.3367/UFNr.0138.198209b.0045
Прохоров А.М., Конов В.И., Урсу И., Михэилеску И.Н. Взаимодействие лазерного излучения с металлами. М.: Наука; Бухарест: Editura Academiei, 1988. 537 с.
Карлов Н.В., Кириченко Н.А., Лукьянчук Б.С. Лазерная термохимия: учеб. рук. М.: ЦентрКом, 1995. 368 с.
Углов А.А., Волков А.А., Сагдединов О.Г., Кривоногов Ю.Ю. // Инженерно-физический журн. 1990. Т. 58. № 3. С. 389. (англ.)https://doi.org/10.1007/BF00871453
Cui C.Y., Cui X.G., Ren X.D., Qi M.J., Hu J.D., Wang Y.M. // Appl. Surf. Science. 2014. V. 305. P. 817. https://doi.org/10.1016/j.apsusc.2014.04.025
Kozakov A.T., Yaresko S.I. // Inorganic Materials: Applied Research. 2011. V. 2. Iss. 3. P. 254. https://doi.org/10.1134/S2075113311030130
Козаков А.Т., Яресько С.И., Колесников В.И., Сидашов А.В. // Поверхность. Рентген., синхротр. и нейтрон. исслед. 2011. № 5. С. 26. (англ.)https://doi.org/10.1134/S1027451011050089
Yang J., Lian J., Bai H., Cui W., Guo Z. // ISIJ International. 2005. V. 45. № 5. P. 730. https://doi.org/10.2355/isijinternational.45.730
Lian J., Dong Q., Guo Z., Xu Q., Yang J., Hu J., Guan Q., Chen B. // Materials Science and Engineering A. 2005. V. 391, № 1–2. P. 210. https://doi.org/10.1016/j.msea.2004.08.077
Liu Y.H., Hu J.D., Zhao L., Guo Z.X., Chumakov A.N., Bosak N.A. // Optics & Laser Techn. 2010. V. 42. P. 647.https://doi.org/10.1016/j.optlastec.2009.11.004
Cui C.Y., Cui X.G., Zhao Q., Hu J.D., Liu Y.H., Wang Y.M. // Optics & Laser Technology. 2012. V. 44. P. 815. https://doi.org/10.1016/j.optlastec.2011.11.025
Яресько С.И. // Инженерно-физический журн. 2014. Т. 87. № 1. С. 245. (англ.)https://doi.org/10.1007/s10891-014-1008-2
Бонч-Бруевич А.М., Либенсон М.Н. // Изв. АН СССР. Сер. физ. 1982. Т. 46. № 6. С. 1104.
Арзуов М.И. и др. Исследование кинетики нагрева металлов в газовой среде излучением непрерывного и импульсно-периодического CO2-лазера // Препр. ФИАН. М.: ФИАН, 1977. № 152. 44 с.
Quinn T.F.J. // Brit. J. Appl. Phys. 1962. V. 13. № 1. P. 33. https://doi.org/10.1088/0508-3443/13/1/308
Sakrani S.B., Sullivan J.L. // Proc. SPIE. 1998. V. 3175. P. 176. https://doi.org/10.1117/12.300662
Усманов К.Б., Якунин Г.И. Влияние внешних сред на износ и стойкость режущих инструментов. Ташкент: Изд-во “Фан” УзССР, 1984. 160 с.
Любарский И.М., Палатник Л.С. Металлофизика трения. М.: Металлургия, 1976. 176 с.
Яресько С.И. // Упрочняющие технологии и покрытия. 2009. № 3. С. 40.
Коршунов Л.Г., Макаров А.В., Осинцева А.Л. // Трение и износ. 1988. Т. 9. № 1. С. 52.
Макаров А.В., Коршунов Л.Г., Осинцева А.Л. // Трение и износ. 1991. Т. 12. № 5. С. 870.
Ohmura E., Takamachi Y., Inoue K. // Trans. Jap. Soc. Mech. Eng. A. 1990. V. 56. № 526. P. 1496.
Kozakov A.T., Kochur A.G., Googlev K.A., Nikolsky A.V., Raevskii I.P., Smotrakov V.G., Yeremkin V.V. // J Electron Spectrosc Relat Phenom. 2011. V. 184. Iss. 1–2. P. 16. https://doi.org/10.1016/j.elspec.2010.10.004
Анализ поверхности методами оже- и рентгеновской фотоэлектронной спектроскопии / Ред. Бриггс Д., Сих М.П. М.: Мир, 1987. 600с.
Нефедов В.И. Рентгеноэлектронная спектроскопия химических соединений. М.: Химия, 1984. 256 с.
Yamashita T., Hayes P. // Appl. Surf. Sci. 2008. V. 254. Iss. 8. P. 2441. https://doi.org/10.1016/j.apsusc.2007.09.063
Кубашевский О., Гопкинс Б. Окисление металлов и сплавов. М.: Металлургия, 1965. 428с.
Алимов Д.Т., Бобырев В.А., Бункин Ф.В., Кириченко Н.А., Лукьянчук Б.С., Митин Ю.Н., Омельченко А.И., Симакин А.В., Хабибуллаев П.К. // Докл. АН СССР. 1983. Т. 268. № 4. С. 850.
Физико-химические свойства окислов: Справочник / Ред. Самсонова Г.В. М.: Металлургия, 1978. 472 с.
Дополнительные материалы отсутствуют.
Инструменты
Поверхность. Рентгеновские, синхротронные и нейтронные исследования