Поверхность. Рентгеновские, синхротронные и нейтронные исследования, 2021, № 4, стр. 41-46
Поверхностное удельное электросопротивление углерод-углеродных композиционных материалов, полученных по технологии изостатической карбонизации
Д. В. Ярцев a, *, М. Ю. Бамборин b, **, С. А. Колесников a, Е. Г. Чеблакова a, Б. С. Клеусов a
a Научно-исследовательский институт конструкционных материалов
на основе графита “НИИграфит”
111524 Москва, Россия
b Государственный научно-исследовательский и проектный институт
редкометаллической промышленности “Гиредмет”
111524 Москва, Россия
* E-mail: DVYartsev@rosatom.ru
** E-mail: MiYBamborin@giredmet.ru
Поступила в редакцию 11.04.2020
После доработки 22.07.2020
Принята к публикации 25.07.2020
Аннотация
Углерод-углеродные композиционные материалы двух- и четырехмерного армирования на основе структур из углеродной конструкционной нити из полиакрилонитрильного прекурсора получены по технологии изостатической карбонизации каменноугольного пека. Методом рентгеноструктурного анализа проведена оценка различия кристаллического состояния армирующего волокна и коксовой матрицы. С помощью токовихревого метода исследовано изменение уровня поверхностного удельного электрического сопротивления в зависимости от плотности образцов и степени графитации матрицы. Показано влияние степени завершенности формирования внутренней структуры на механическую прочность и уровень удельного электрического сопротивления материала. Показано, что измерение удельного электрического сопротивления токовихревым методом может служить неразрушающим методом информативной оценки изменения структуры материала.
ВВЕДЕНИЕ
В углерод-углеродных композиционных материалах (УУКМ) основой формирования прочности является механическое сцепление компонент (контакт волокна и матрицы) и необходимость преодоления силы трения покоя по их границам. До максимальных технологических температур (2000°С и более) на углеродных границах компонент, однородных по химическому составу и кристаллическому строению, не происходит образования совместных участков вещества. Обжатие углеродной матрицей филаментов углеродной нити создает механическое соединение компонент и этим вносит вклад в формирование прочности композита. Но на различных этапах формирования структуры материала углеродная матрица обладает различной эффективной способностью связывания углеродных филаментов. Последовательное проведение процессов уплотнения уменьшает общую пористость, увеличивает площадь контакта на границах компонент, придает монолитность углеродной матрице и композиту в целом, что отражается на механической прочности и физических свойствах материала, и в частности на уровне удельного электрического сопротивления.
Согласно работе [1], используя токовихревой метод определения поверхностного удельного электрического сопротивления, можно неразрушающим способом отследить степень завершенности формирования внутренней структуры углерод-углеродных композиционных материалов на различных стадиях технологического процесса производства (как на образцах, так и на готовых деталях).
Цель настоящей работы – расширенное исследование возможностей токовихревого метода определения поверхностного удельного электрического сопротивления для изучения степени завершенности формирования внутренней структуры углерод-углеродных композиционных материалов, отличающихся схемой армирования и температурой обработки.
Объектами исследования служили образцы двух- (2D) и четырехмерно (4D) армированных УУКМ на основе углеродной конструкционной нити из полиакрилонитрильного (ПАН) волокна и углеродной матрицы из кокса каменноугольного пека. Карбонизацию проводили в печах под давлением. Технологическая схема изготовления УУКМ описана ранее в работах [2, 3]. Заготовки из УУКМ проходили четыре цикла пропитки и карбонизации под давлением (ПКД). После каждого цикла ПКД проводилась высокотемпературная обработка (ВТО) заготовок при температуре 2170 ± 30°С, достаточной для достижения истинной плотности углеродного вещества матрицы dи ≤ 2.1 г/см3.
С помощью операции ВТО (уровня температуры и времени изотермической выдержки) регулируют не только истинную плотность, но и электро- и теплопроводность углеродного материала, а также скорость окисления и показатели механических и химических свойств [4–10].
Для части заготовок из 4D-УУКМ температура ВТО после первого (с наибольшей прибылью массы и приростом плотности) процесса ПКД составляла 2300 ± 30°С. В свою очередь, часть заготовок из 2D-УУКМ проходила только два цикла ПКД, после которых операция ВТО не проводилась. Температура карбонизации составляла 850°С, и для углеродного вещества матрицы процессы, проходящие при карбонизации, оставались до конца не завершенными. Кажущаяся плотность заготовок, определенная методом гидростатического взвешивания, достигла отметок 1.89 г/см3 для 4D-УУКМ, 1.91 г/см3 для 2D-УУКМ и 1.55 г/см3 для 2D-УУКМ, не прошедшего ВТО.
ЭКСПЕРИМЕНТАЛЬНАЯ ЧАСТЬ
Определение поверхностного удельного электросопротивления токовихревым методом
Токовихревой контроль основан на анализе изменения электромагнитного поля вихревых токов под действием тех или иных неоднородностей объекта контроля. Он используется для обнаружения поверхностных и подповерхностных дефектов в изделиях из металлов, сплавов, графита, полупроводников и других проводящих материалов [11, 12]. Например, с помощью вихретоковых приборов обнаруживают остаточные механические напряжения, выявляют усталостные трещины в металлах на ранних стадиях их развития, контролируют качество термической и химико-термической обработки, состояние поверхностных слоев после механической обработки и т.д. Вихретоковые измерители удельной электрической проводимости широко применяют для сортировки металлических материалов и графитов по маркам (по химическому составу).
Удельное электрическое сопротивление определяли на образцах углеродного материала размерами 150 × 20 × 20 мм (для 4D-УУКМ) и 100 × 10 × × 10 мм (для 2D-УУКМ). За результат для каждого образца принимали среднее арифметическое значение пяти измерений. Величину удельного электрического сопротивления в приповерхностном слое углеродного материала измеряли при помощи преобразователя, создающего на поверхности углеродного материала вихревые токи, контуры и плотность которых различны в местах изменения структуры материала. Схема прибора представлена на рис. 1.
Особенностью трека электрического тока, индуцированного токовихревым способом, является последовательное пересечение в приповерхностном слое электропроводного материала, в данном случае УУКМ, углеродного волокна, жгутов, участков углеродной матрицы разных этапов формирования, а также преодоление контактного сопротивления в местах скопления пор. Глубина проникновения вихревых токов в материал пропорциональна проводимости вещества и, видимо, неоднородна по площади поверхности. Границы раздела углеродных волокон и углеродной матрицы с разными уровнями контактного сопротивления и разнящихся кристаллической структурой, а также пористость, микротрещины на поверхностях раздела углеродных веществ с различными уровнями модулей упругости, температурных коэффициентов линейного расширения, коэффициентов Пуассона увеличивают гетерогенность вещества на пути прохождения электрического тока. В таком случае минимальная проводимость фрагмента структуры становится определяющей, измерение электропроводности токовихревым способом является информативным методом обнаружения в материале участков с низкой электропроводимостью (повышенными значениями удельного электросопротивления).
Определение рентгеноструктурных характеристик углеродных материалов
Рентгеноструктурный анализ, заключающийся в определении размеров кристаллитов (областей когерентного рассеяния) и межплоскостных расстояний в структуре исследуемого компонента УУКМ, а также степени графитации проводили по методике, представленной в статье [9]. Анализ диаграмм “интенсивность рефлекса–угол падения луча” показал бимодальное распределение в образцах УУКМ. По сопоставлению с калибровочными зависимостями для отдельных компонентов композита (углеродное волокно, кокс каменноугольного пека) соответствующие пики диаграммы отнесли к его структурным компонентам.
Таким образом, в настоящей работе проведена оценка различия кристаллического состояния армирующего наполнителя композита и его матрицы.
РЕЗУЛЬТАТЫ И ОБСУЖДЕНИЕ
В табл. 1 представлены результаты рентгеноструктурного анализа образцов 4D-УУКМ, термообработанных при температурах (2170 ± 30)°С и (2300 ± 30)°С, а на рис. 2 – соответствующие зависимости величины поверхностного удельного электрического сопротивления (ρs, мкОм · м) от степени графитации матрицы (gм, %).
Таблица 1.
Результаты рентгеноструктурного анализа образцов 4D-УУКМ
Показатели волокна | Показатели углеродной матрицы | ρs, мкОм · м | |||||
---|---|---|---|---|---|---|---|
d002, нм | g, % | Lc, нм | d002, нм | g, % | Lc, нм | La, нм | |
Температура обработки 2170 ± 30°С | |||||||
0.360 | – | 3 | 0.343 | 14 | 14 | 5 | 16.1 |
0.352 | – | 5 | 0.342 | 23 | 23 | 9 | 15.9 |
0.349 | – | 6 | 0.341 | 33 | 27 | 12 | 16.9 |
0.348 | – | 6 | 0.34 | 45 | 29 | 16 | 14.9 |
0.347 | – | 6 | 0.34 | 51 | 33 | 19 | 14.3 |
0.347 | – | 6 | 0.339 | 60 | 40 | 21 | 16.4 |
0.346 | – | 6 | 0.338 | 65 | 38 | 25 | 20 |
Температура обработки 2300 ± 30°С | |||||||
0.345 | – | 6 | 0.337 | 75 | 41 | 31 | 12.5 |
0.344 | 6 | 7 | 0.337 | 81 | 50 | 39 | 11.5 |
0.339 | 57 | 16 | 0.336 | 92 | 77 | 46 | 9.3 |
0.337 | 79 | 28 | 0.335 | 100 | 136 | 105 | 7.1 |
Рис. 2.
Зависимость величины поверхностного удельного электрического сопротивления 4D-УУКМ от степени графитации матрицы: ◆ – температура обработки 2170°С; ◼ – температура обработки 2300°С.
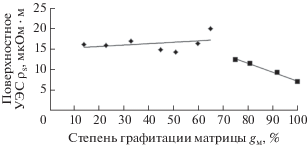
Как видно из данных таблицы 1, для УУКМ со степенью графитации матрицы менее 65% (температура обработки 2170°С) разница в значениях межплоскостного расстояния d002 волокна и матрицы сохраняется в диапазоне 0.007–0.01 нм (за исключением значения gм = 14%, для которого Δd002 составляет 0.017 нм), в свою очередь, размеры кристаллитов Lc углеродной матрицы значительно возрастают по сравнению со значениями Lc для углеродного волокна (остаются на прежнем уровне). ΔLc увеличивается с 11 нм для gм = 14% до 34 нм для gм = 60%. Такая неоднородность структуры не сказывается на значениях ρs, которые лишь незначительно возрастают (рис. 2). При повышении температуры обработки до 2300°С наблюдается графитация углеродного волокна (рост значений gв до 79%). Для УУКМ со степенью графитации матрицы более 75% снижению ρs соответствует повышение совершенства кристаллической решетки (параметры d002, La, Lc).
В табл. 2 представлены результаты рентгеноструктурного анализа и прочностные характеристики образцов 2D- и 4D-УУКМ различного уровня плотности (прошедших от 1 до 4 циклов ПКД), а на рис. 3 – соответствующие зависимости величины поверхностного удельного электрического сопротивления от плотности материала.
Таблица 2.
Свойства образцов УУКМ
№* | dк, г/см3 | Показатели волокна | Показатели углеродной матрицы | σр, МПа | ρs, мкОм · м | |||||
---|---|---|---|---|---|---|---|---|---|---|
d002, нм | Lc, нм | La, нм | d002, нм | g, % | Lc, нм | La, нм | ||||
4D-УУКМ | ||||||||||
1 | 1.13 | 0.349 | 4 | 0.4 | 0.341 | 35 | 29 | 17 | 10.5 | 26.2 |
2 | 1.5 | 0.348 | 4 | 0.4 | 0.341 | 41 | 29 | 17 | 31.5 | 21.8 |
3 | 1.75 | 0.348 | 5 | 0.4 | 0.339 | 50 | 31 | 24 | 70.7 | 20 |
4 | 1.89 | 0.345 | – | 0.63 | 0.337 | 73 | 36 | 28 | 137.5 | 16.5 |
2D-УУКМ | ||||||||||
1 | 1.15 | – | – | – | – | – | – | – | – | 28.5 |
2 | 1.43 | 0.353 | 5 | 12 | 0.340 | 42 | 29 | 41 | 161.8 | 20 |
3 | 1.78 | 0.348 | 4 | 15 | 0.340 | 42 | 27 | 50 | 302.3 | 15 |
4 | 1.91 | 0.347 | 5 | 15 | 0.339 | 59 | 34 | 59 | 393 | 10 |
Рис. 3.
Зависимость величины поверхностного удельного электрического сопротивления от плотности УУКМ: ◆ – 4D-УУКМ; ◼ – 2D-УУКМ.
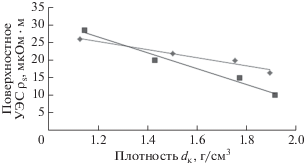
Данные табл. 2 показывают, как с увеличением плотности и ростом предела прочности при растяжении происходит улучшение контактного взаимодействия на границах структурных фаз углеродная матрица–углеродное волокно, выражающееся в совершенствовании внутренней структуры УУКМ. Это является причиной понижения поверхностного удельного электрического сопротивления (рис. 3). На первых двух–трех циклах ПКД–ВТО уровень взаимодействия углеродной матрицы и углеродного волокна невысок. Прохождение каждого дополнительного цикла ПКД–ВТО приводит к понижению ρs на 8–17% для 4D-УУКМ и на 25–33% для 2D-УУКМ. Одновременно улучшаются физические и механические показатели УУКМ. Итоговый четвертый цикл ПКД–ВТО выводит УУКМ на требуемый уровень плотности и приводит к завершенности формирования структуры материала. Причем для двумерного композита структура в значительной степени сформирована уже после третьего цикла ПКД–ВТО, а на четвертом прочность 2D-УУКМ возрастает менее чем в 1.5 раза.
При отклонении температуры обработки от значения (2170 ± 30)°С в меньшую сторону для образцов 4D-УУКМ наблюдались повышенные значения удельного сопротивления. В совокупности со снижением прочности при растяжении это свидетельствует о развитии дефектности на границе раздела углеродный наполнитель (стержень, нить)–углеродная коксовая матрица. Наглядным проявлением плохого контактного взаимодействия на границе раздела фаз в образцах 4D-УУКМ является возникновение механизма “выдергивания” стержней из объема рабочей зоны во время испытаний при растяжении [1], а в образцах 2D-УУКМ – расслоения (рис. 4).
Рис. 4.
Разрушение образцов при растяжении с “вытягиванием” стержней для 4D-УУКМ (а) и с расслоениями для 2D-УУКМ (б).
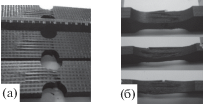
Данные табл. 3 демонстрируют как снижение механической прочности, являющееся результатом неэффективного контактного взаимодействия компонентов композита, находит свое отражение в изменении величины удельного электрического сопротивления, определяемого токовихревым методом.
Таблица 3.
Средние значения физических показателей образцов УУКМ
Показатели | Взаимодействие на границе раздела фаз | |||||
---|---|---|---|---|---|---|
Хорошее | Плохое | |||||
4D | 2D | 4D | 2D | |||
Плотность, г/см3 | 1.89 | 1.91 | 1.78 | 1.89 | 1.91 | 1.78 |
Предел прочности при растяжении, МПа | 137.5 | 393 | 302.3 | 109.3 | 211.5 | – |
ρs, мкОм · м | 16.5 | 10 | 15 | 26 | 15.5 | 20.5 |
В табл. 4 представлены результаты исследования образцов 2D-УУКМ, вырезанных из заготовок, которые проходили только два цикла ПКД без последующих операций ВТО. Температура карбонизации при этом составляла 850°С. Рентгеноструктурный анализ показал, что компоненты (волокно и матрица) представляют собой аморфный углеродный материал. Сравнение данных табл. 4 с данными табл. 2 и 3 подтверждает, что разные показатели удельного электрического сопротивления при одинаковых исходных сырьевых материалах свидетельствуют о различии структуры УУКМ из-за неодинаковой температуры их обработки.
ЗАКЛЮЧЕНИЕ
Проведенные исследования образцов УУКМ, отличающихся схемой армирования и температурой обработки позволили:
1) по результатам рентгеноструктурного анализа установить и оценить различие кристаллического состояния компонентов УУКМ (волокна и матрицы) на всех стадиях уплотнения (циклах ПКД);
2) по результатам измерения поверхностного удельного электрического сопротивления токовихревым методом установить взаимосвязь этого показателя со степенью графитации матрицы и плотностью УУКМ, и тем самым оценить степень завершенности формирования внутренней структуры материала.
Сделанные оценки подтверждаются данными по механической прочности УУКМ:
1) низкие значения предела прочности при растяжении на первых стадиях уплотнения являются результатом неэффективного контактного взаимодействия на границах структурных фаз углеродная матрица–углеродное волокно, при этом уровень поверхностного удельного электрического сопротивления повышен;
2) рост предела прочности на заключительных стадиях уплотнения свидетельствует об улучшении контактного взаимодействия компонентов композита, выражающемся в совершенствовании внутренней структуры УУКМ и понижении уровня поверхностного удельного электрического сопротивления.
Таким образом, из представленных результатов следует, что измерение удельного электрического сопротивления токовихревым методом выявляет различие в структуре образцов УУКМ и может быть информативным неразрушающим методом оценки изменения структуры материала.
Список литературы
Бамборин М.Ю., Воронцов В.А., Колесников С.А. // Новые огнеупоры. 2014. № 2. С. 22.
Колесников С.А., Проценко А.К. // Сб. докл. межд. конф. “Современное состояние и перспективы развития электродной продукции”. Челябинск, 25–26 ноября 2010, С. 259.
Ярцев Д.В., Колесников С.А. // Новые огнеупоры. 2012. № 8. С. 30.
Нагорный В.Г., Котосонов А.С., Островский В.С., Дымов Б.К., Лутков А.И., Ануфриев Ю.П., Барабанов В.Н., Белогорский В.Д., Кутейников А.Ф., Виргильев Ю.С., Соккер Г.А. // Справочник / Ред. Соседов В.П. “Свойства конструкционных материалов на основе графита”. Москва: Металлургия, 1975. 336 с.
Шулепов С.В. Физика углеродных материалов. Челябинск: Металлургия, Челябинское отделение, 1990. 336 с.
Костиков В.И. // Технология производства изделий и интегральных конструкций из композиционных материалов в машиностроении / Ред. Братухин А.Г. и др. М.: Готика, 2003. С. 187.
Разумов Л.Л., Клюев С.К., Комаров А.Б. // Цветные металлы. 1987. № 10. С. 67.
Коломиец В.А. Освоение технологии производства графитов типа МПГ на основе сланцевого кокса в ОАО “Новочеркасский электродный завод”: Автореф. дис. … канд. техн. наук: 05.17.11. Москва, 2003. 27 с.
Бамборин М.Ю., Ярцев Д.В., Колесников С.А. // Новые огнеупоры. 2013. № 8. С. 27.
Бамборин М.Ю., Колесников С.А. // Новые огнеупоры. 2014. № 6. С. 46.
Каневский И.Н., Сальникова Е.Н. Неразрушающие методы контроля: Учеб. Пособие. Владивосток: Изд-во ДВГТУ, 2007. 243 с.
Троицкий В.А. Вихретоковый контроль: Учеб. пособие. Киев: Феникс, 2011. 148 с.
Дополнительные материалы отсутствуют.
Инструменты
Поверхность. Рентгеновские, синхротронные и нейтронные исследования