Поверхность. Рентгеновские, синхротронные и нейтронные исследования, 2021, № 5, стр. 68-75
Микротопография и микроструктура поверхности быстрорежущей стали после газолазерной резки
Л. Е. Афанасьева a, *, В. В. Измайлов a, М. В. Новоселова a
a Тверской государственный технический университет
170026 Тверь, Россия
* E-mail: ludmila.a@mail.ru
Поступила в редакцию 20.05.2020
После доработки 25.08.2020
Принята к публикации 29.08.2020
Аннотация
Представлены результаты экспериментальных исследований шероховатости поверхности и микроструктуры быстрорежущей стали марки Р6М5 после газолазерной резки. Показано, что параметры шероховатости поверхности исследованных образцов соответствуют типичным значениям параметров шероховатости поверхностей после таких видов механической обработки, как точение или шлифование. При газолазерной резке в приповерхностном слое образовалась зона закалки протяженностью до 110 мкм, обладающая повышенной микротвердостью до 10 600 ± 160 МПа. Кратковременный отпуск в интервале температур Ас1–620°С не привел к распаду мартенсита, переходная зона или зона отпуска не выявлена.
ВВЕДЕНИЕ
Качество поверхности деталей, в том числе ее микрогеометрия, является важной составляющей качества промышленных и бытовых технических изделий в целом [1]. В большинстве случаев при применении традиционных методов обработки деталей микрогеометрия их поверхностей, включающая микрошероховатость и волнистость, формируется в результате воздействия режущего инструмента (резца, фрезы, абразивного зерна). Исследованию микрогеометрии технических поверхностей, полученных традиционными методами механической обработки, посвящено значительное количество работ [2–5]. В научной литературе накоплен большой объем статистических данных по параметрам микрогеометрии поверхностей после различных видов обработки и разработаны теоретические модели, связывающие эти параметры с режимами обработки и механическими свойствами материалов.
Вместе с тем, в настоящее время широко применяются технологии обработки, основанные на иных физических принципах, нежели воздействие режущего инструмента. Примером может служить газолазерная резка, являющаяся одним из первых технологических применений лазеров для обработки материалов. С помощью лазерного излучения возможно разделение практически любых металлов и сплавов независимо от их теплофизических свойств. Продукты разрушения удаляются потоком вспомогательного газа [6–9]. Одним из основных показателей качества реза при газолазерной резке является шероховатость образующихся поверхностей.
Физика процессов удаления расплава при газолазерной резке сложна и требует создания аналитических и численных моделей, учитывающих законы гидродинамики, газодинамики, теплофизики, оптики, физики твердого тела. На текущий момент механизмы удаления расплава при газолазерной резке с использованием непрерывного лазерного излучения до конца не понятны и эта проблема остается весьма актуальной. В решении задач энергетической эффективности и технологического качества процесса газолазерной резки велика роль экспериментальных методов исследования. Накоплен значительный опыт и разработаны технологические рекомендации, позволяющие разделять углеродистые, низколегированные стали и некоторые сплавы цветных металлов с высокой производительностью и качеством. Для высоколегированных быстрорежущих сталей вопросы технологического качества процесса газолазерной резки и места этой технологии в изготовлении инструментов практически не разработаны.
Целью данной работы является исследование микроструктуры и комплекса параметров микрогеометрии поверхностей образцов быстрорежущей стали, полученных в результате газолазерной резки.
МАТЕРИАЛЫ И МЕТОДЫ
Для проведения исследований использовали заготовки быстрорежущей стали марки Р6М5 (ГОСТ 19 265-73) размером 120 × 40 × 3.3 мм упрочненные с помощью объемной закалки и трехкратного отпуска при температуре 560°С. Газолазерную резку заготовок выполняли на технологическом лазерном комплексе BySprint 3015 компании Bystronic на режимах: мощность излучения – 1800 Вт; скорость резки – 0.017 м/с; давление вспомогательного газа азота – 0.9 МПа. Размеры пятна нагрева, следовательно, распределение плотности мощности излучения по нему, можно изменять с помощью фокусировки луча лазера относительно поверхности образца. В данных исследованиях расстояние между положением перетяжки фокуса и верхней поверхностью образца варьировали в интервале 2.7–4.5 мм (табл. 1).
Таблица 1.
Положение фокуса над поверхностью образца
Номер образца | 1 | 2 | 3 | 4 |
---|---|---|---|---|
Положение перетяжки фокуса от верхней поверхности образца f, мм | 2.7 | 3.1 | 3.5 | 4.5 |
Количественную оценку шероховатости поверхности реза выполняли по поперечным профилограммам (перпендикулярно ходу лазерного луча), полученным с помощью профилографа-профилометра. Профилограммы были сняты на различных расстояниях x от верхней поверхности реза: x = 0.5, 1.5, 2.5 мм. Определяли следующие параметры микрогеометрии.
Стандартные параметры (ГОСТ Р ИСО 4287-2014): для профиля шероховатости: Ra – среднее арифметическое отклонение профиля; Rp – максимальная высота пика профиля; Rt – общая высота профиля; RSm – средняя ширина элементов профиля (средний шаг неровностей профиля);
для профиля волнистости: Wt – общая высота профиля; WSm – средняя ширина элементов профиля.
Нестандартные параметры шероховатости: tm – относительная опорная длина профиля на уровне средней линии; rm – средний радиус кривизны вершин выступов шероховатости; ν – параметр степенной аппроксимации опорной кривой tp = = tmεν, где tp – относительная опорная длина профиля на уровне p (расстояние от линии выступов профиля до выбранного сечения профиля), ε = = p/Rp.
Комплексные параметры шероховатости: параметр μ, характеризующий степень симметричности профиля шероховатости, μ = 1 – Rp/Rt [10]; параметр
аналогичный параметру, предложенному В.С. Комбаловым [11].
Помимо вышеперечисленных точечных (дискретных) параметров, выраженных одним единственным числом, для характеристики микрогеометрии поверхности использовали также гибридный параметр, в качестве которого выступает кривая опорной поверхности (кривая Эббота–Файрстоуна). Она наглядно характеризует распределение материала в шероховатом слое.
Для полноты анализа и возможности сравнения параметров микрогеометрии исследованных поверхностей с параметрами, приводимыми в литературных источниках, в данной работе определяли параметр шероховатости R10z – высоту неровностей профиля по десяти точкам. Это не что иное, как параметр Rz в его прежнем понимании, как его определял ГОСТ 2789-73 в редакциях до 2017 г. По этому параметру, наряду с другими, накоплен большой объем статистических данных, и было бы неразумно игнорировать их.
Выбор указанных параметров микрогеометрии обусловлен тем, что, согласно результатам многочисленных исследований (например, [3] и [12]) эти параметры оказывают существенное влияние на различные эксплуатационные свойства функциональных поверхностей деталей, таких, как:
1) интенсивность износа поверхностей в процессе нормального изнашивания (Ra, Rt, Wt, RSm, tm);
2) контактные деформации и контактная жесткость (Ra, Rt, Wt, RSm);
несущая способность (Δ, Rp, Rt, rm, tm и ν);
3) коэффициент концентрации напряжений (Rt, Rp, tm, RSm);
4) скорость коррозии поверхностного слоя (Rt, Rp, tm, RSm) и др.
Исследования микроструктуры поверхности реза и в зоне термического влияния проводили с использованием растрового электронного микроскопа (РЭМ) модели Tescan Vega SBU II и металлографического микроскопа Carl Zeiss Axio Vert.A1MAT. Микротвердость измеряли на приборе ПМТ-3 согласно ГОСТ 9450-76 при усилии 0.98 Н.
РЕЗУЛЬТАТЫ И ИХ ОБСУЖДЕНИЕ
Параметры шероховатости поверхности реза
При газолазерной резке различают стационарный характер разделения материала, когда жидкая ванна расплава существует по всей длине канала реза, и нестационарный, характеризуемый периодическим выносом расплавленного металла из зоны обработки [6–9]. Стационарный режим резки характеризуется тем, что скорости плавления металла в направлении реза и удаления расплавленного металла в каждом сечении канала равны. При таком режиме достигается наибольшее качество поверхности реза.
При меньших скоростях газолазерной резки имеет место нестационарный, т.е. неустановившийся характер разрушения. Перед движущимся лазерным лучом образуется расплавленный участок, удаляемый газовой струей, причем этот процесс носит периодический релаксационный характер. В этом случае поверхность реза имеет характерную бороздчатую структуру [6–9].
Типичная профилограмма поверхности реза представлена на рис. 1, параметры микрогеометрии исследованных поверхностей – в табл. 2. Базовая длина lr принята равной 0.8 мм, в соответствии с рекомендациями [3], исходя из величин параметра Ra (практически для всех исследованных образцов Ra < 2 мкм). Соответственно, длина оценки ln принята равной пятикратной базовой длине, т.е. ln = 4 мм.
Таблица 2.
Параметры шероховатости и волнистости поверхности реза
№ образца | x, мм | Ra, мкм | Rt, мкм | Rp, мкм | R10z, мкм | RSm, мкм | tm | ν | rm, мм | Δ | μ | Wt, мкм |
WSm, мм |
---|---|---|---|---|---|---|---|---|---|---|---|---|---|
1 | 0.5 | 2.5 | 18 | 8.5 | 10.8 | 250 | 0.52 | 2.5 | 0.63 | 0.037 | 0.53 | – | – |
1.5 | 1.1 | 9 | 4.0 | 6.8 | 238 | 0.42 | 2.0 | 0.80 | 0.017 | 0.56 | – | – | |
2.5 | 1.3 | 11 | 4.5 | 6.6 | 250 | 0.45 | 2.1 | 0.40 | 0.040 | 0.59 | – | – | |
2 | 0.5 | 1.8 | 17 | 7.5 | 9.5 | 250 | 0.38 | 2.2 | 0.38 | 0.069 | 0.54 | 10 | 2.0 |
1.5 | 1.2 | 11 | 5.0 | 7.8 | 250 | 0.38 | 2.1 | 0.58 | 0.030 | 0.50 | – | – | |
2.5 | 1.2 | 10 | 4.8 | 6.8 | 250 | 0.48 | 2.8 | 1.23 | 0.011 | 0.53 | 10 | 2.7 | |
3 | 0.5 | 1.7 | 13 | 6.0 | 7.2 | 250 | 0.50 | 2.5 | 1.03 | 0.017 | 0.56 | – | – |
1.5 | 1.2 | 9 | 4.5 | 6.2 | 250 | 0.50 | 2.7 | 0.79 | 0.015 | 0.55 | 10 | 2.5 | |
2.5 | 1.9 | 16 | 7.5 | 11.4 | 263 | 0.50 | 2.9 | 0.33 | 0.062 | 0.52 | 10 | 2.5 | |
4 | 0.5 | 1.3 | 12 | 5.0 | 6.3 | 250 | 0.44 | 2.4 | 0.57 | 0.030 | 0.58 | 10 | 2.7 |
1.5 | 1.2 | 9 | 4.0 | 6.0 | 220 | 0.46 | 2.1 | 0.78 | 0.017 | 0.56 | 10 | 2.7 | |
2.5 | 1.7 | 13 | 6.5 | 9.4 | 250 | 0.41 | 2.1 | 0.66 | 0.030 | 0.50 | 10 | 2.7 |
Как видно из рис. 1, на поверхности газолазерного реза прослеживаются два вида отклонений от идеальной формы – длинноволновые (волнистость) с отношением шага к высоте более 50, и коротковолновые (шероховатость) с отношением шага к высоте менее 50. Однако на некоторых образцах четко выраженной волнистости не наблюдалось (табл. 2).
Несмотря на то, что механизмы образования шероховатости и волнистости при газолазерной резке и механической обработке различны, высотные параметры шероховатости исследованных образцов соответствуют типичным значениям высотных параметров таких видов механической обработки, как торцевое фрезерование (Ra = 1.25–5 мкм) или плоское шлифование (Ra = = 0.3–5 мкм) [3, 13]. Они также близки к минимальным значениям высотного параметра шероховатости, полученным в работе [6] R10z ∼ 10 мкм.
Абсолютные rm и относительные rm/Rt величины радиусов кривизны вершин выступов шероховатости, значения параметров степенной аппроксимации начального участка опорных кривых ν и tm также в целом согласуются с соответствующими величинами для указанных выше механических методов обработки [13].
Вид опорных кривых (рис. 2) свидетельствует о практически симметричном распределении материала по высоте шероховатого слоя. Можно заключить, что на поверхности отсутствуют аномально высокие выступы и аномально глубокие впадины. Об этом же свидетельствуют величины параметра μ профиля поверхности реза, предложенного в работе [10]. Они близки к величине μ = 0.5 (симметричный профиль), немного превышая ее. Такие поверхности обладают повышенной жесткостью и износостойкостью, хорошей маслоемкостью, т.е. имеют совокупность положительных эксплуатационных свойств.
Рис. 2.
Опорные кривые: $\rlap{--} \Diamond $ расстояние от верхней поверхности реза х = 0.5 мм и $\rlap{--} \square $ х = 1.5 мм.
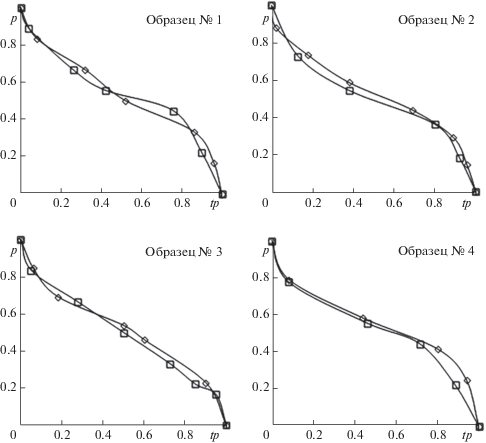
Для полноты анализа представляет интерес сопоставить корреляционные связи различных параметров шероховатости для поверхностей после механической обработки и после газолазерной резки. Подобное сопоставление приведено в табл. 3 и на рис. 3.
Таблица 3.
Соотношения параметров шероховатости поверхностей после механической обработки и газолазерной резки
Рис. 3.
Параметры шероховатости поверхности при различных положениях перетяжки фокуса относительно верхней поверхности образца: $\rlap{--} \Diamond $ расстояние от верхней поверхности реза х = 0.5 мм, $\rlap{--} \square $ х = 1.0 мм, $\rlap{--} \triangle $ х = 2.5 мм.
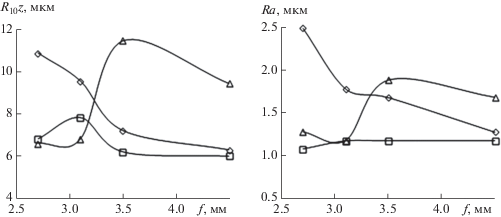
Из анализа табл. 3 и рис. 3 следует, что, несмотря на различную природу шероховатости после механической обработки и после газолазерной резки, корреляционные соотношения соответствующих параметров в обоих случаях близки, хотя для шероховатости поверхности после газолазерной резки соответствующие величины в целом несколько больше, чем для поверхностей после механической обработки.
Исследования микроструктуры
Исследования микроструктуры сталей в зоне термического влияния при газолазерной резке проводились в ряде работ, например, [16–18]. Отмечается, что для сталей, испытывающих при нагреве и охлаждении фазовые превращения, зона термического влияния имеет слоистое строение. Выделяются следующие участки: зона закалки, в которую входит закалка из жидкой фазы и из твердой фазы и зона отпуска (для предварительно закаленных сталей). Зона закалки отличается высокой устойчивостью к действию химических травителей и на оптических изображениях выглядит светлой.
Между зоной закалки и основным металлом располагается переходная зона или зона отпуска. На этом участке возможно понижение микротвердости, связанное с распадом мартенсита и образованием структур отпуска – троостита или сорбита. Степень разупрочнения стали в зоне отпуска и ее протяженность зависят от режимов газолазерной резки. Чем меньше по длительности будет термическое воздействие, тем выше твердость стали в зоне отпуска [17].
Структурные превращения, проходящие в зоне термического влияния, могут изменить свойства материала, в частности, привести к дополнительному упрочнению поверхностей реза [16–18]. Этот факт наряду с макро- и микрогеометрическими свойствами поверхности реза является одним из основных критериев, определяющих место лазерной обработки в технологическом процессе изготовления изделий и качество обработки.
РЭМ-изображение поверхности реза показано на рис. 4а. Видно, что на микроуровне поверхность реза представлена каплевидной структурой, характерной для поверхностей, формирующихся при свободной кристаллизации. Поверхностные дендриты растут в виде сферолитов. Отсутствует направленность в росте кристаллов по отношению к внешнему тепловому потоку.
Рис. 4.
РЭМ-изображения: поверхности реза (а); микроструктуры стали в зоне закалки из жидкой фазы (б) и вне зоны термического влияния (в).
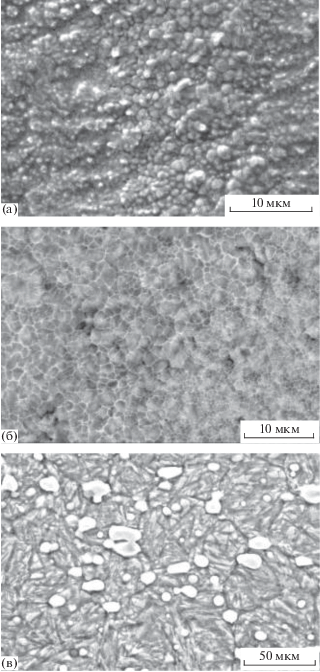
На рис. 4б показана микроструктура стали в зоне закалки из жидкой фазы (продольный шлиф). Сталь имеет ячеистое строение со средним размером дендритных ячеек 1–3 мкм, по границам ячеек выделяются эвтектические карбиды в виде тонких прослоек. Сплавы с таким типом морфологии кристаллической структуры, как правило, обладают улучшенными механическими свойствами [16–18].
Многими исследователями изучались вопросы влияния условий кристаллизации на размер дендритной ячейки. В частности, в работе [19] для быстрорежущей стали дана зависимость между скоростью охлаждения расплава vохл и размером дендритной ячейки d, мкм, образующейся при этих условиях кристаллизации: d = ${\text{59}}{v}_{{{\text{охл}}}}^{{ - 0.{\text{34}}}}.$
Используя эту зависимость, несложно оценить среднюю скорость охлаждения расплава в зоне закалки из жидкой фазы при газолазерной резке. Она составляет около 0.6 × 104 °С/с в областях, где размер дендритной ячейки d = 3 мкм и 1.6 × × 105 °С/с при d = 1 мкм. В зоне закалки из жидкой фазы произошла высокоскоростная перекристаллизация поверхностных слоев реза на глубину до 35–40 мкм (рис. 5).
Рис. 5.
Микроструктура стали Р6М5 в зоне термического влияния (поперечный шлиф). Оптическое изображение.
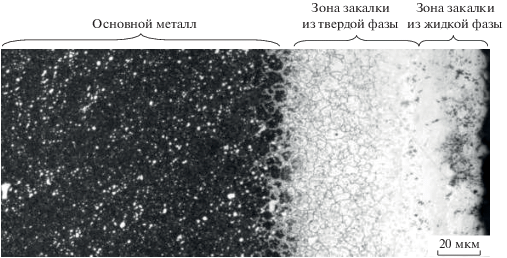
На рис. 4в представлено РЭМ-изображение микроструктуры быстрорежущей стали Р6М5 вне зоны термического влияния. После традиционной термообработки, заключающейся в объемной закалке и трехкратном отпуске, сталь имеет структуру мартенсит и карбиды, микротвердость 9100 ± 190 МПа. Сравнивая микроструктуру стали в зоне закалки из жидкой фазы и вне зоны термического влияния, можно отметить, что при повторном плавлении и высокоскоростной кристаллизации значительная часть карбидов растворяется в металлической матрице, упрочняя ее. Сталь в зоне закалки из жидкой фазы имеет повышенную микротвердость 10 400 ± 200 МПа.
Протяженность зоны закалки из твердой фазы 65–70 мкм (рис. 5). Нижняя граница зоны закалки из твердой фазы определяется нагревом до температуры точки Ас1, при которой в стали образуется аустенит. Для быстрорежущей стали марки Р6М5 эта температура равна 820°С. В этой зоне произошла повторная закалка металлической матрицы. Сталь имеет также повышенную микротвердость 10 600 ± 160 МПа.
Зона отпуска образуется при нагреве стали ниже точки Ас1 в интервале температур 820–620°С. Нижняя граница этого интервала соответствует теплостойкости стали Р6М5. Как показали проведенные исследования, кратковременный отпуск в интервале температур 820–620°С не привел к распаду мартенсита. На изучаемых образцах между зоной закалки и основным металлом не выявлено участков с изменениями в микроструктуре и пониженной микротвердостью.
ЗАКЛЮЧЕНИЕ
Для исследованных образцов поверхностей быстрорежущей стали после газолазерной резки значения основных параметров шероховатости соответствуют типичным средним значениям аналогичных параметров для поверхностей после таких видов механической обработки, как точение или плоское шлифование. Во многих случаях такие поверхности могут использоваться без последующей чистовой обработки.
При тепловом воздействии лазерного излучения в быстрорежущей стали формируется зона закалки протяженностью до 110 мкм с повышенной микротвердостью до 10 600 ± 160 МПа. Газолазерная резка не привела к распаду мартенсита в зоне нагрева Ас1–620°С, переходная зона или зона отпуска не выявлена.
Список литературы
Клепиков В.В., Порошин В.В., Голов В.А. Качество изделий. М.: МГИУ, 2008. 288 с.
Дунин-Барковский И.В., Карташова А.Н. Измерение и анализ шероховатости, волнистости и некруглости поверхности. М.: Машиностроение, 1978. 232 с.
Уайтхауз Д. Метрология поверхностей. Принципы, промышленные методы и приборы. Долгопрудный: Издательский Дом “Интеллект”, 2009. 472 с.
Thomas T.R. Rough surfaces. London: Imperial College Press, 1999. 278 p.
Григорьев А.Я. Физика и микрогеометрия технических поверхностей. Минск: Беларуская навука, 2016. 247 с.
Оришич А.М., Фомин В.М. Актуальные проблемы физики лазерной резки металлов. Новосибирск: Изд-во СО РАН, 2012. 176 с.
Sobih M., Crouse P.L., Li L. // Applied Physics A: Materials Science and Processing. 2008. V. 90(1). P. 171. https://doi.org/10.1007/s00339-007-4247-7
Li L., Sobih M., Crouse P.L. // CIRP Annals. 2007. V. 56(1). P. 193. https://doi.org/10.1016/j.cirp.2007.05.047
Karatas C., Keles O., Uslan I., Usta Y. // J. Materials Processing Technology. 2006. V. 172(1). P. 22. https://doi.org/10.1016/j.jmatprotec.2005.08.017
Измайлов В.В., Новоселова М.В. // Вестник Тверского государственного технического университета. Серия “Технические науки”. 2020. № 3(7). С. 5. https://doi.org/10.46573/2658-5030-2020-3-5-13
Комбалов В.С. Оценка триботехнических свойств контактирующих поверхностей. М.: Наука, 1983. 136 с.
Суслов А.Г., Федоров В.П., Горленко О.А. Технологическое обеспечение и повышение эксплуатационных свойств деталей и их соединений. М.: Машиностроение. 2006. 448 с.
Рыжов Э.В. Технологические методы повышения износостойкости деталей машин. Киев: Наукова думка, 1984. 272 с.
Экслер Л.И. // Метрологические и технологические исследования качества поверхности. Рига: Зинатне, 1976. С. 37.
Дьяченко П.Е., Вайнштейн В.Э., Карпова Т.М. // Качество поверхности. М.: Изд. АН СССР, 1959. № 4. С. 3.
Безъязычный В.Ф., Семенов А.А. // Упрочняющие технологии и покрытия. 2013. № 7. С. 35.
Афанасьева Л.Е., Барабонова И.А., Раткевич Г.В., Новоселова М.В., Гречишкин Р.М. // Поверхность. Рентген., синхротр. и нейтрон. исслед. 2016. № 12. С. 46. https://doi.org/10.7868/S0207352816100036
Афанасьева Л.Е., Барабонова И.А., Зубков Н.С., Разумов М.С. // Металловедение и термическая обработка металлов. 2009. № 7(649). С. 36.
Benyounis K.Y., Fakron O.M., Abboud J.H. // Materials and Design. 2009. V. 30. № 3. P. 674–678. https://doi.org/10.1016/j.matdes.2008.05.030
Дополнительные материалы отсутствуют.
Инструменты
Поверхность. Рентгеновские, синхротронные и нейтронные исследования