Поверхность. Рентгеновские, синхротронные и нейтронные исследования, 2021, № 7, стр. 96-103
Влияние лития на структурно-фазовое состояние быстро затвердевшего сплава системы Al–Mg–Li при термической обработке
И. А. Столяр a, *, В. Г. Шепелевич a, E. Wendler b, И. И. Ташлыкова-Бушкевич c, **
a Белорусский государственный университет
220050 Минск, Беларусь
b Университет им. Ф. Шиллера
07743 Йена, Германия
c Белорусский государственный университет информатики и радиоэлектроники
220013 Минск, Беларусь
* E-mail: uyluana@gmail.com
** E-mail: iya.itb@bsuir.by
Поступила в редакцию 14.12.2020
После доработки 24.01.2021
Принята к публикации 28.01.2021
Аннотация
Исследовано влияние лития на структурно-фазовое состояние авиакосмического алюминиевого сплава марки 1421 системы Al–Mg–Li, полученного с помощью высокоскоростной кристаллизации из расплава. Анализ состава приповерхностных слоев образцов сплава, проведенный методом мгновенных ядерных реакций, установил, что при повышенных температурах обработки происходит диффузия лития на поверхность, и его концентрация в тонком приповерхностном слое толщиной 0.1 мкм достигает 38 ат. %, что в 4.8 раз выше расчетного содержания в сплаве. Методом измерения микротвердости определено упрочнение образцов при изотермическом отжиге при температуре 400°C, что связано, по-видимому, с выделением метастабильных фаз, содержащих литий. Результаты рентгеноструктурного анализа свидетельствуют об увеличении доли пероксида лития Li2O2 на поверхности фольг при отжиге.
ВВЕДЕНИЕ
В настоящее время существует повышенный интерес большого количества исследовательских лабораторий к алюминий-магний-литиевым сплавам. Производство лития, являющегося самым легким металлом, постоянно возрастает, поскольку он имеет большое значение в развитии современной техники. Приоритетность изучения сплавов данной группы в значительной мере определяется их использованием в авиакосмической промышленности, поскольку добавка лития в алюминий обеспечивает повышенный модуль упругости и пониженную плотность, позволяя снизить массу самолетных конструкций [1, 2]. Как известно, на свойства материалов оказывают влияние такие факторы, как дисперсность и дефектность микроструктуры, химический состав и многие другие. С одной стороны, в промышленности с помощью разнообразных традиционных методов литья получают алюминиевые сплавы, механические свойства которых уже хорошо изучены. С другой стороны, научный и практический интерес представляют технологии, позволяющие превысить характерную для большинства методов получения микрокристаллических сплавов скорость охлаждения расплава порядка 102 К/с и существенно модифицировать структуру, улучшая, следовательно, физические, коррозионные и технологические свойства материалов на основе алюминия [3]. В частности, методы высокоскоростной кристаллизации (центробежная закалка, спиннингование, атомизация и другие), обеспечивающие скорости охлаждения расплава порядка 106 К/с и выше, позволяют получить материалы, характеризующиеся большей степенью гомогенности и однородности (фазовой и структурной), расширяя область использования разработанных композиций сплавов.
Целью настоящей работы было изучение влияния лития на структурно-фазовое состояние быстро затвердевшего промышленного сплава 1421 системы Al–Mg–Li–Sc–Zr при термической обработке. Алюминиевые сплавы, легированные литием, можно упрочнить с помощью термообработки благодаря переменной растворимости лития и других компонентов в твердом алюминии. Поэтому выбор в настоящей работе температур отжига обусловлен ранее полученными результатами о том, в каких температурных интервалах наблюдается максимальное упрочнение быстро затвердевших фольг данного сплава при изохронном отжиге [4]. Актуальность исследования сплавов системы Al–Mg–Li с помощью метода мгновенных ядерных реакций (МЯР) связана с трудностью определения содержания и распределения лития (Z = 3) в приповерхностных слоях образцов при использовании прямых методов анализа. Одним из преимуществ указанного неразрушающего ядерно-физического метода является уникальная возможность прямого обнаружения и построения концентрационных профилей легких элементов в мишени [5, 6], в то время как данную задачу невозможно решить с помощью такого широко распространенного метода, как рентгеноспектральный микроанализ. Растровые электронные микроскопы, дополнительно оснащенные рентгеновскими спектрометрами, могут регистрировать характеристическое рентгеновское излучение химических элементов образца, возбужденное электронами зонда, только начиная с бериллия (Z = 4). В основе определения профиля распределения примеси по глубине материала методом МЯР лежит зависимость от глубины анализа потерь энергии заряженных частиц, испускаемых в ядерных реакциях, при выходе из образца. В настоящем исследовании использование метода МЯР позволило исследовать элементно-структурные изменения в приповерхностных слоях и на глубине быстро затвердевших образцов при термической обработке. Дополнительно фазовый состав отожженных фольг был изучен методом рентгеноструктурного анализа, а также измерено изменение микротвердости образцов при изотермическом отжиге.
МЕТОДИКА ЭКСПЕРИМЕНТА
Фольги промышленного алюминиевого сплава 1421 (Al(5.8 ат. %)–Mg(8.1 ат. %)–Li(0.03 ат. %)–Zr(0.11 ат. %)–Sc) были получены из жидкой фазы методом одностороннего охлаждения на внутренней поверхности медного цилиндра. Частота вращения цилиндра диаметром 20 см составляла 1500 об./мин. Для изучения отбирали фольги толщиной 40–80 мкм. Скорость охлаждения расплава порядка 106 К/с [7]. При изучении влияния температуры отжига на структурно-фазовый состав и микротвердость фольг сплава 1421 образец фиксировали при каждой температуре посередине между шестью стеклышками (толщина каждого стеклышка около 2 мм) для обеспечения во время экспериментов медленного нагрева и охлаждения фольги со скоростью, не превышающей 10 град/с.
С помощью метода МЯР были изучены обе поверхности свежезакаленных и отожженных при T = 380°C в течение 1 ч фольг сплава 1421: поверхность А, контактирующая с подложкой, и поверхность Б, контактирующая с воздухом. Для идентификации лития и измерения профилей его распределения в образцах использовали ядерную реакцию 7Li(p,α)4He при энергии протонов 1.4 МэВ на ускорителе-тандентроне (3 МВ) JULIA (Jena University Laboratory for Ion Acceleration). Рассеянные на образце протоны и α-частицы, образовавшиеся в результате реакции (p,α), регистрировали детектором с энергетическим разрешением 15 кэВ, установленным под углом обратного рассеяния θ = 170° к направлению пучка ускоренных протонов.
Информация о составе исследуемых образцов была получена в результате обработки энергетических спектров рассеянных частиц с помощью компьютерной программы SIMNRA [8], в которой в пределах статистической погрешности измерений добивались совпадения модельного и экспериментально наблюдаемого спектров, варьируя элементный состав, количество и толщину слоев модельной структуры. Для моделирования части спектров, соответствующих обратно рассеянным протонам, данные о не резерфордовских поперечных сечениях были взяты из базы данных IBANDL [9] и экспериментальных данных для Li [10], C [11], O и Al [12]. Поперечное сечение для ядерной реакции протонов с атомами Li было взято из [13]. Дополнительно была учтена ядерная реакция протонов с атомами Al согласно [14]. В качестве эталонного спектра, полученного при тех же условиях и геометрии, что и в настоящих экспериментах, использовали спектр МЯР образца из ниобата лития (LiNbO3) с известным содержанием лития 20.0 ат. % [15]. Погрешность определения концентрации лития методом МЯР составила от 5 до 11%.
Поскольку в SIMNRA толщина слоев модельной структуры hn определяется в единицах ат/см2, перевод толщины слоев в метрическую шкалу h выполняли по формуле [6]:
Рентгеноструктурное исследование свежезакаленных фольг и фольг, отожженных при температуре 400°С в течение 1 ч, осуществляли на дифрактометре Rigaku Ultima IV с использованием CuKα-излучения. Фазы идентифицировали по базам данных ICCD PDF-2 (2013) и Materials Project [16]. Микротвердость образцов при изотермическом отжиге фольг при температуре 400°С в течение 110 мин измеряли с помощью автоматического микротвердомера MVD 402 Wolpert Wilson Instruments с нагрузкой 50 г в течение 30 с. Погрешность измерения микротвердости не превышала 4%.
РЕЗУЛЬТАТЫ И ИХ ОБСУЖДЕНИЕ
Типичные экспериментальные и модельные энергетические спектры частиц, полученные при облучении свежезакаленных и отожженных фольг сплава 1421 ускоренными протонами, представлены на рис. 1. В области значений энергии до 1.4 МэВ наблюдаются спектры обратно рассеянных протонов, а при энергии от 5.0 МэВ и выше – спектры α-частиц, возникших в реакции 7Li(p,α)4He с 7Li. Обе части спектров моделировали в SIMNRA одновременно. Отмеченные стрелками пики в спектрах обратного рассеяния протонов при энергии 800, 1030, 1120 и 1235 кэВ обусловлены наличием в образцах атомов Li, C, O и Al соответственно. Рассчитанные из спектров МЯР профили глубинного распределения атомов Li в фольгах представлены на рис. 2.
Рис. 1.
Типичные экспериментальные (символы) и построенные с помощью программы SIMNRA (линии) спектры протонов и α-частиц, обратно рассеянных на фольгах сплава 1421: а – поверхность А свежезакаленной фольги; б, в – поверхности А и Б фольги, отожженной при 380°С.
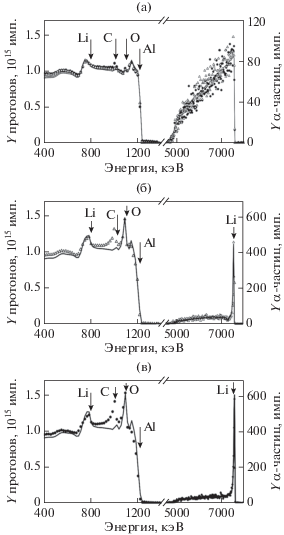
Рис. 2.
Распределение лития в фольге сплава 1421, отожженной при 380°С: сплошная линия – поверхность А; штриховая линия – поверхность Б. Горизонтальная штриховая линия задает профиль распределения лития в свежезакаленной фольге. Профиль условно разделен на два слоя, в которых литий распределен по глубине образца неравномерно (1) и равномерно (2).
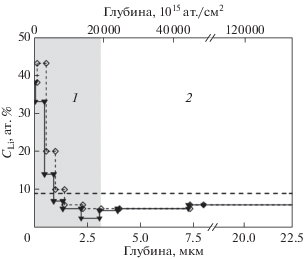
Для свежезакаленной фольги сплава 1421 измеренные спектры обеих поверхностей хорошо согласуются с модельными спектрами. Существенного различия между сторонами А и Б не обнаружено. В качестве примера на рис. 1а показан спектр поверхности А свежезакаленной фольги. Установлено, что тонкий приповерхностный слой фольг содержит углерод (небольшой пик при энергии 1030 кэВ) и оксидированный Al, в то время как Li распределен по глубине фольг равномерно (до глубины 22 мкм). Следует отметить, что с помощью программы SIMNRA нельзя определить содержание Mg в образцах, поскольку различие масс атомов Al и Mg слишком мало. Также нет возможности измерить содержание Sc и Zr в приповерхностном слое фольг из-за малой величины соответствующих сигналов в спектрах. Средняя определенная методом МЯР концентрация Li в фольгах составляет 9 ат. %, что на 11% превышает расчетную концентрацию Li в сплаве (рис. 2).
Типичные энергетические спектры обратно рассеянных протонов и α-частиц, измеренные после отжига фольг сплава 1421 при 380°С, представлены на рис. 1б, 1в. Обнаружено, что в тонком приповерхностном слое толщиной 0.1 мкм поверхностей А и Б концентрация Li достигает в среднем ~38 ат. %, что в 4.8 раз выше его расчетного содержания в сплаве. Затем содержание лития снижается до 5.0 ат. % на глубине 3 мкм (слой 1 на рис. 2). В слое от 3 до 22 мкм (слой 2 на рис. 2) измеренная концентрация лития в среднем составляет 6.0 ат. %, увеличиваясь незначительно с глубиной. Дополнительно установлено, что значительное перераспределение атомов Li при отжиге в направлении поверхности фольг (правая часть рис. 1б, 1в) сопровождается существенным возрастанием содержания кислорода на поверхности. Данные результаты указывают на формирование соединения Li с кислородом на поверхности образцов.
Отметим, что в спектрах протонов, обратно рассеянных на отожженных фольгах, в области энергии ~1.0 МэВ наблюдается широкий пик, который невозможно промоделировать (рис. 1б, 1в). Высокоэнергетический край этого пика нельзя промоделировать обратным рассеянием протонов на атомах углерода или азота (следующий после углерода легкий элемент периодической таблицы Менделеева) на поверхности фольг. При анализе спектров свежезакаленных образцов (рис. 1а) также обнаруживается данный сигнал. Поэтому можно предположить, что наблюдаемый сигнал является результатом неизвестной ядерной реакции. Чтобы идентифицировать реакцию, необходимы дальнейшие исследования. Однако подчеркнем, что присутствие данного пика не влияет на результаты определения методом МЯР концентрации Li в фольгах, поскольку глубинный профиль Li задается формой измеренного спектра α-частиц, возникших в результате ядерной реакции 7Li(p,α)4He. Абсолютное значение концентрации Li определяется выходом Y α-частиц, т.е. высотой сигнала в высокоэнергетической области спектров (рис. 1).
С помощью рентгеноструктурного анализа установлено, что на поверхности свежезакаленных образцов присутствует пероксид лития Li2O2. Рефлексы оксида Li2O в образцах не зафиксированы. На рис. 3 показаны типичные рентгеновские дифрактограммы свежезакаленной и отожженной при 400°С фольг. В нижней части рисунка представлена эталонная штрих-дифрактограмма пероксида лития, положения и относительные интенсивности рефлексов которой взяты из базы данных [16]. При термической обработке с ростом температуры отжига интенсивность линий Li2O2 на дифрактограммах растет, что указывает на увеличение доли пероксида лития и согласуется с результатами, полученными методом МЯР (рис. 3). Дополнительно также определены оксиды MgO и Al2O3 на поверхности фольг сплава 1421 [17].
Рис. 3.
Дифрактограммы свежезакаленной (1) и отожженной при 400°C (2) фольг сплава 1421 и штрих-дифрактограмма пероксида лития (Li2O2, карточка № mp-841 [15]).
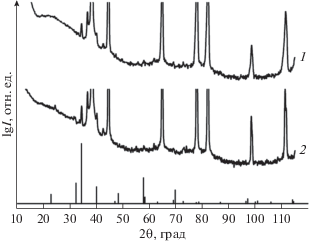
Исследование зависимости Hμ образцов алюминиевого сплава 1421 от температуры отжига демонстрирует эффект упрочнения фольг сплава при отжиге с температурой 400°C (рис. 4). В начале отжига в течение 20 мин наблюдается рост микротвердости до 1.26 ГПа, которая затем незначительно изменяется в течение 110 мин отжига. В среднем величина Hμ составляет 1200 МПа, что на 33% выше микротвердости исходной фольги.
Рис. 4.
Зависимость микротвердости фольг сплава 1421 от продолжительности изотермического отжига при 400°C.
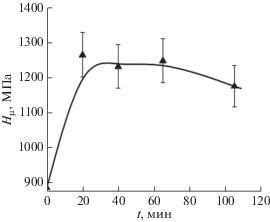
Применение алюминий-литиевых сплавов для создания аэрокосмических аппаратов с меньшей массой позволяет сэкономить горючее, увеличить грузоподъемность и улучшить другие характеристики летательных аппаратов. Действительно, каждый процент лития снижает плотность алюминия на 3%, повышает модуль упругости на 6% и обеспечивает значительный эффект упрочнения сплавов после закалки и искусственного старения [2]. Промышленный сплав 1421, входящий в большую группу сплавов системы Al–Mg–Li, относится к среднепрочным и широко применяется в клепаных и сварных конструкциях. Необходимый уровень прочности сплава в основном определяется содержанием Li, Mg и Sc [18]. За рубежом отсутствует его аналог, поскольку, столкнувшись со значительными трудностями при плавке и литье сплавов системы Al–Mg–Li с редкоземельными элементами, зарубежные фирмы сосредоточили свои усилия главным образом на разработке и освоении более технологичных сплавов систем Al–Li–Cu, Al–Li–Mg–Cu и Al–Zn–Mg–Cu, но уступающих сплаву 1421 по плотности: АА7075, АА7178 и АА7050 [2].
Как известно, с использованием методов сверхбыстрой закалки из расплава получают материалы в состоянии пересыщенного твердого раствора, что, в свою очередь, приводит к более ускоренному по сравнению с литейными алюминиевыми сплавами распаду твердого раствора с выделением вторых фаз в процессе термообработки. На практике для исследования термостабильности быстро затвердевших алюминиевых сплавов широко используют изохронный и изотермический отжиги. Если применение изохронного отжига позволяет найти температуру начала изменения физических свойств образцов, то одно из преимуществ изотермического отжига в технологии производства цветных металлов и сплавов – получение более однородной структуры, поскольку изотермическое выдерживание обеспечивает выравнивание температуры в объеме материала, и все превращения происходят при одинаковой степени переохлаждения. В частности, практический интерес к исследованию температурного воздействия на структуру приповерхностных слоев высоколегированных алюминиевых сплавов, широко используемых в автомобильной и аэрокосмической промышленности, обусловлен тем, что их коррозионная стойкость, как известно, зависит от химической и структурной неоднородности поверхности металла. В то же время действующие механизмы упрочнения в любой системе сплава зависят от температуры, степени приложенного напряжения и размера зерен сплава. При температурах, близких к комнатной, сплавы будут деформироваться в процессе скольжения (пластического течения), которое связано с перемещением дислокаций. Все факторы, препятствующие скольжению, будут повышать твердость сплава. Движение дислокаций может быть затруднено атомами растворенного вещества, выделениями и/или границами зерен/субзерен [19]. Поэтому стратегия повышения твердости быстро затвердевших сплавов заключается в достижении оптимальной комбинации упрочнения твердого раствора за счет увеличения растворимости легирующего элемента в твердой фазе при образовании пересыщенного твердого раствора, упрочнения частицами второй фазы за счет введения большой объемной доли мелких преципитатов, а также зернограничного упрочнения за счет уменьшения размера зерен [19]. При отжиге сплавов такие факторы, как коагуляция выделений, замена менее стабильных выделений более стабильными, потеря когерентности выделений, обеднение матричного твердого раствора легирующим элементом приводят к снижению твердости материала [20].
В современных методах анализа поверхности твердых тел при глубинном профилировании примесей идентификация элементов осуществляется по энергии частиц и излучения, испускаемого материалом, который бомбардируют электроны, ионы или фотоны. Метод МЯР является неразрушающим высокочувствительным методом определения концентрации легких примесей в материале, качественный состав которого уже известен [21]. Одним из важных достоинств метода МЯР является возможность исследования глубинных профилей распределения элементов в приповерхностной области образцов. В качестве анализирующих ионов используют ионы водорода или гелия, а в качестве регистрируемых частиц – вторичные частицы, образовавшиеся в результате ядерной реакции.
В настоящей работе идентификацию лития в фольгах и количественный анализ выполняли с помощью моделирования энергетических спектров α-частиц, образовывавшихся в результате ядерной реакции с протонами 7Li(p,α)4He. Детектирование энергии и числа вторичных частиц позволило построить профили распределения лития по глубине. Установленные закономерности перераспределения Li в результате отжига в быстро затвердевшем сплаве 1421 можно объяснить его диффузией из объема фольг к поверхности при высокотемпературном отжиге, который приводит к распаду пересыщенного твердого раствора и выделению литийсодержащих фаз. На поверхности фольг литий, будучи активным легко окисляемым элементом, вступает в реакцию с кислородом, образуя пероксид лития Li2O2, который распадается при температуре 450°С [22]. Вероятно, оксид лития Li2O не идентифицируется при рентгеновском фазовом анализе свежезакаленных фольг из-за сегрегации на поверхности образцов магния, химическое сродство которого к кислороду выше, чем лития: Mg + Li2O → → 2Li + MgO. Хотя обогащение поверхности свежезакаленных фольг сплава 1421 литием не обнаружено, сегрегационная неоднородность фольг [23], в частности обогащение тонкого приповерхностного слоя фольг магнием (20 ат. %), указывает на существенную роль магния в формировании поверхностного оксида.
Согласно результатам исследований сегрегации легирующих элементов, в сплавах алюминия, в условиях высокоскоростной кристаллизации оксидная пленка на поверхности некоторых сплавов аналогична по составу и структуре оксидной пленке на чистом алюминии, поскольку ряд элементов формируют обогащенный слой под оксидной пленкой [24–29]. Однако процессы роста пленки зависят от метода и условий реализации сверхбыстрой закалки из расплава. Закономерности перераспределения лития в результате термической обработки в алюминиевых сплавах системы Al–Mg–Li (сплав 1421) мало изучены. Однако в редких работах обнаружено обеднение литием приповерхностного слоя сплавов, полученных традиционным способом плавки и литья, в результате высокотемпературного отжига [30]. Сообщается также о разрыхлении пленок Al2O3 из-за присутствия оксидов лития и магния на поверхности образцов сплавов системы Al–Mg–Li [31, 32]. В ультрамелкозернистых сплавах 1420 и 1421, полученных методами интенсивной пластической деформации, после воздействия импульсного лазерного излучения образовавшаяся на поверхности образцов оксидная пленка, как сообщается, состоит в основном из оксидов магния MgO и соединения Li2CO3 и обогащена магнием и литием [33, 34]. Однако в [33, 34] не указывается, во-первых, с помощью какого метода был индентифицирован литий на поверхности образцов, поскольку авторы ссылаются на данные рентгеновского микроанализа, который, как известно, не позволяет исследовать данный вопрос. Во-вторых, отсутствует количественная информация о концентрации лития в приповерхностной области образцов. С учетом вышесказанного можно предположить, что основные причины противоречивости информации о характере распределения лития по глубине сплавов алюминия – это особенности микроструктуры изучаемых образцов, которая, как известно, зависит от способа изготовления материла, а также сложности интерпретации [35] экспериментальных данных, полученных с помощью таких косвенных методов исследования распределения лития в поверхностных слоях, как методы электросопротивления [36] и микротвердости [37, 38].
Необходимо отметить, изучая литийсодержащие фазы с помощью рентгеноструктурного анализа в фольгах сплава 1421, что кроме пероксида Li2O2 в отожженных в интервале температур 280–450°C фольгах присутствует фаза S1 (Al2LiMg) [39]. Дополнительное сопоставление рентгеноструктурных данных и результатов исследования отожженных фольг методами растровой электронной микроскопии, рентгеноспектрального микроанализа [4, 17, 39] и МЯР дает основание идентифицировать обнаруженную ранее в отожженных фольгах метастабильную фазу X как Li-содержащую фазу переменного состава Al(Mg, Sc, Zr, Li)x. Как отмечено выше, по некоторым данным фаза Al(Mg, Sc, Zr, Li)x была также обнаружена в ультрамелкозернистых образцах сплава 1421, полученных в неравновесном состоянии методом равноканального углового прессования [40–42]. Однако в научной литературе пока не найдены сведения о том, как процессы выделения/растворения фазы Al(Mg, Sc, Zr, Li)x влияют на механические свойства сплава 1421. Результаты настоящей работы хорошо согласуются с установленным ранее плато на кривой зависимости Hμ от температуры изохронного отжига в интервале 340–400°C [4] и свидетельствуют о том, что выделение высокодисперсных интерметаллидных частиц – частиц фазы S1 и фазы Х, выделяющейся при отжиге около 300°C, – обуславливает рост микротвердости фольг с увеличением температуры отжига до 400°C.
Обнаруженный эффект многократного повышения содержания Li на поверхности отожженных фольг, а также установленное упрочнение фольг сплава 1421 при высокотемпературном отжиге, обусловленное выделением Li-содержащих фаз, указывает на перспективность продолжения исследования структурно-фазовых превращений, протекающих в процессе термической обработки быстро затвердевших образцов сплава 1421 для улучшения физико-механических свойств сплавов системы Al–Mg–Li.
ЗАКЛЮЧЕНИЕ
С помощью методов МЯР, рентгеноструктурного анализа и измерения микротвердости исследовано влияние лития на структурно-фазовое состояние быстрозатвердевших фольг сплава 1421 системы Al–Mg–Li при высокотемпературном отжиге. Впервые обнаружен эффект перераспределения Li после отжига при 380°C: в приповерхностном слое толщиной 0.1 мкм его концентрация составляет около 38.0 ат. %, что в 4.8 раза выше расчетного содержания лития в сплаве. Различие концентрации Li на поверхности и на максимально детектируемой глубине (22 мкм) отожженных фольг достигает 6.3 раза. Диффундирующий на поверхность фольг при высокоскоростной кристаллизации литий вступает в реакцию с кислородом, образуя пероксид лития Li2O2. При термической обработке с увеличением температуры отжига доля пероксида растет. Обнаружено упрочнение образцов на 33% при изотермическом отжиге при температуре 400°C.
Список литературы
Антипова Т.Н., Лабутин А.А., Олешко А.Ю. // Управление качеством технологических процессов: монография. Королев: Научный консультант, 2015. С. 165.
Dorin T., Vahid A., Lamb J. Fundamentals of Aluminium Metallurgy / Eds. Lumley R.N. Cambridge: Woodhead Publishing Series, 2018. 387 p.
Кузей А.М. Структурно-фазовые превращения в быстрозакаленных алюминиевых сплавах. Минск: Беларуская навука, 2011. 399 с.
Шепелевич В.Г., Бушкевич И.А., Вендлер Э., Ташлыкова-Бушкевич И.И. // Поверхность. Рентген., синхротр. и нейтрон. исслед. 2019. № 6. С. 101. https://doi.org/10.1134/S020735281906012X
Фелдман Л., Майер Д. Основы анализа поверхности и тонких пленок. М.: Мир, 1989. 344 с.
Jeynes C., Colaux J.L. // Analyst. 2016. V. 141. P. 5944. https://doi.org/10.1039/c6an01167e
Мирошниченко И.С. Закалка из жидкого состояния. М.: Металлургия, 1982. 168 с.
Mayer M. SIMNRA, a Simulation Program for the Analysis of NRA, RBS and ERDA. N.Y.: American Institute of Physics, 1999. 541 p.
IBANDL. https://www-nds.iaea.org/exfor/ibandl.htm
Bashkin S. // Phys. Rev. 1951. V. 84. P. 1124. https://doi.org/10.1103/PhysRev.84.1124
Abriola D., Gurbich A.F., Kokkoris M., Lagoyannis A., Panneta V. // Nucl. Instrum. Methods Phys. Res. B. 2011. V. 269. P. 2011. https://doi.org/10.1016/j.nimb.2011.06.002
Gurbich A.F. // Nucl. Instrum. Methods Phys. Res. B. 2010. V. 268. P. 1703. https://doi.org/10.1016/j.nimb.2010.02.011
Wesch W., Rensberg J., Schmidt M., Wendler E. // J. Appl. Phys. 2019. V. 126. P. 125105. https://doi.org/10.1063/1.5116667
Abuzeid M.A., Aly F.M., Antoufiev Y.P., Baranik A.T., Nower T.M., Sorokin P.V. // Nucl. Phys. 1963. V. 45. P. 123. https://doi.org/10.1016/0029-5582(63)90788-0
Schmidt E., Ritter K., Gartner K., Wendler E. // Nucl. Instrum. Methods Phys. Res. B. 2017. V. 409. P. 126. https://doi.org/10.1016/j.nimb.2017.03.111
Materials Project. https://materialsproject.org
Бушкевич И.А., Шепелевич В.Г., Wendler E., Ташлыкова-Бушкевич И.И., Адинцов Н.В., Кочерга М.В. Рентгеноструктурный анализ фазовых превращений в быстрозатвердевшем сплаве Al–Mg–Li–Sc–Zr при отжиге // Матер. 13-й Междунар. конф. “Взаимодействие излучений с твердым телом”. Минск, 2019. С. 505.
Давыдов В.Г., Бер Л.Б., Елагин В.И., Самарина М.В., Колобнев Н.И., Хохлатова Л.Б. // Технология легких сплавов. 1996. № 1. С. 9.
Davis L.A., Das S.K., Li J.C.M., Zedalis M.S. // Int. J. Rapid Solid. 1994. V. 8. P. 73.
Новиков И.И. Теория термической обработки металлов. М.: Металлургия, 1978. 329 с.
Lanford W.A., Parenti M., Nordell B.J. et al. // Nucl. Instrum. Methods Phys. Res. B. 2016. V. 371. P. 211. https://doi.org/10.1016/j.nimb.2015.10.052
Greenwood N.N., Earnshaw A. Chemistry of the Elements. Oxford: Butterworth-Heinemann, 1998. 1343 p.
Бушкевич И.А., Шепелевич В.Г. Элементный и фазовый состав быстрозатвердевшего сплава 1421 системы Al–Li–Mg с добавками Sc и Zr // Матер. 12-й Междунар. конф. “Взаимодействие излучений с твердым телом”. Минск, 2017. С. 211.
Tashlykova-Bushkevich I.I. // Vacuum. 2005. V. 78. № 2–4. P. 529. https://doi.org/10.1016/J.VACUUM.2005.01.080
Tashlykova-Bushkevich I.I. // J. Alloys Compd. 2009. V. 478. P. 229. https://doi.org/10.1016/j.jallcom.2008.12.006
Ликутин В.В., Крайников А.В., Томпсон Дж.Э. // Физика металлов и металловедение. 2004. Т. 97. № 4. С. 58.
Крайников А.В. // Порошковая металлургия. 2010. № 7/8. С. 34.
Кикин П.Ю., Перевезенцев В.Н., Русин Е.Е. // Физика металлов и металловедение. 2015. Т. 116. № 8. С. 854.
Ташлыкова-Бушкевич И.И., Шепелевич В.Г., Амати М., Грегоратти Л., Кискинова М. // Поверхность. Рентген., синхротр. и нейтрон. исслед. 2020. № 1. С. 81.
Фридляндер И.Н., Сандлер В.С., Никольская Т.И. // Металловедение и термическая обработка металлов. 1983. № 7. С. 20.
Воробьев А.И. // Сб. рефератов научно-исследовательских и опытно-конструкторских работ. Сер. 9:53. Металлургия. Вып. 3. 2007. № 3. С. 43.
Дресвянников А.Ф., Колпаков М.Е. // Вестн. Казан. технолог. ун-та. 2016. Т. 19. № 9. С. 36.
Кикин П.Ю., Перевезенцев В.Н., Русин Е.Е., Землякова Н.В. // Металловедение и термическая обработка металлов. 2012. № 8. С. 23.
Кикин П.Ю., Перевезенцев В.Н., Русин Е.Е. // Физика металлов и металловедение. 2015. Т. 116. № 8. С. 854.
Schoeberl T., Kumar S. // J. Alloys Compd. 1997. V. 255. P. 135. https://doi.org/10.1016/S0925-8388(96)02818-6
Minamino Y., Yamane T., Araki H. // Metall. Mater. Trans. A. 1987. V. 18A. P. 1536. https://doi.org/10.1007/BF02646667
Udyavar M.S., Dwarakadasa E.S. // J. Mater. Sci. Lett. 1992. V. 11. P. 490. https://doi.org/10.1007/BF00731114
Papazian J.M., Schulte R.L. // Metall. Mater. Trans. A. 1990. V. 21. P. 39. https://doi.org/10.1007/BF02656422
Бушкевич И.А., Бородын А.В., Фишкина Ю.Э., Ташлыкова-Бушкевич И.И. Термическая стабильность микроструктуры быстрозатвердевшего сплава Al–Mg–Li–Sc–Zr // Сб. докл. VIII Междунар. науч. конф. “Актуальные проблемы физики твердого тела”. Минск: Ковчег, 2018. Т. 1. С. 134.
Buranova Yu., Kulitskkiy V., Peterlechner M., Mogucheva A., Kaibyshev R., Divinski S.V., Wilde G. // Acta Materialia. 2017. V. 124. P. 210. https://doi.org/10.1016/j.actamat.2016.10.064
Kaibyshev R., Shipilova K., Musin F., Motohashi Y. // Mater. Sci. Technol. 2005. V. 21. № 4. P. 408. https://doi.org/10.1179/174328405X36610
Islamgaliev R.K., Yunusova N.F., Valiev R.Z., Tsenev N.K., Perevezentsev V.N., Langdon T.G. // Scripta Materialia. 2003. V. 49. P. 467. https://doi.org/10.1016/S1359-6462(03)00291-4
Дополнительные материалы отсутствуют.
Инструменты
Поверхность. Рентгеновские, синхротронные и нейтронные исследования