Поверхность. Рентгеновские, синхротронные и нейтронные исследования, 2021, № 8, стр. 76-81
Влияние облучения импульсным электронным пучком на структуру поверхности неэквиатомного высокоэнтропийного сплава системы Al–Co–Cr–Fe–Ni
К. А. Осинцев a, b, В. Е. Громов a, С. В. Коновалов a, b, *, Ю. Ф. Иванов a, c, И. А. Панченко a, С. Чэнь a, b
a Сибирский государственный индустриальный университет
654007 Новокузнецк, Россия
b Самарский национальный исследовательский университет им. акад. С.П. Королева
443086 Самара, Россия
c Институт сильноточной электроники Сибирского отделения Российской академии наук
634055 Томск, Россия
* E-mail: ksv@ssau.ru
Поступила в редакцию 27.11.2020
После доработки 26.01.2021
Принята к публикации 30.01.2021
Аннотация
Проведено электронно-микроскопическое исследование поверхности высокоэнтропийного сплава системы Al–Co–Cr–Fe–Ni, полученного с помощью проволочно-дугового аддитивного производства и облученного импульсным электронным пучком. Показано, что сплав является поликристаллическим агрегатом с размером зерен (4–15) мкм и обладает неэквиатомным составом с повышенным содержанием алюминия и никеля. Установлено, что приграничные объемы сплава (объемы, расположенные вдоль границ зерен) обогащены атомами хрома и железа, объем зерен обогащен атомами никеля и алюминия, кобальт распределен в сплаве квазиоднородно. Показано, что облучение высокоэнтропийного сплава импульсным электронным пучком приводит к фрагментации поверхностного слоя образцов микротрещинами, сопровождается гомогенизацией поверхностного слоя и образованием субмикро- нанокристаллической (100–200 нм) структуры. Изменение элементного состава поверхностного слоя образцов высокоэнтропийного сплава после облучения в вакууме импульсным электронным пучком не выявлено.
ВВЕДЕНИЕ
Одним из стремительно развивающихся направлений современного материаловедения является разработка и исследование относительно нового класса материалов – высокоэнтропийных сплавов (ВЭС) [1–3]. Повышенное внимание к этим сплавам вызвано их необычными свойствами, микроструктурой и композиционным составом [4]. В отличие от традиционных сплавов, ВЭС состоят из нескольких основных элементов (не менее 5), содержание каждого из которых может варьироваться от 5 до 35 ат. % [5]. Это приводит к возникновению различных эффектов, таких как высокая энтропия смешения элементов, низкая скорость диффузии и сильное искажение кристаллической решетки, что обуславливает высокую термическую стабильность, прочность и твердость высокоэнтропийных сплавов [6, 7].
В настоящее время известны различные способы получения ВЭС, включающие как традиционные методы (вакуумная дуговая плавка [8]), так и аддитивные технологии (селективное лазерное плавление (selective laser melting) [9], прямое осаждение металла (direct metal deposition) [10], плавление электронным пучком (electron beam melting) [11] и лазерная наплавка (laser cladding) [12]). В одной из последних работ был предложен инновационный метод изготовления высокоэнтропийных сплавов с помощью проволочно-дугового аддитивного производства с использованием комбинированной проволоки из нескольких жил (combined cable wire arc additive manufacturing) [13]. Сплав системы Al–Co–Cr–Fe–Ni, полученный этим методом продемонстрировал возможность изготовления больших деталей из высокоэнтропийных материалов с высокой скоростью, что являлось недоступным при других методах аддитивного производства.
За последние десятилетия внешние энергетические воздействия, такие как лазерные пучки, пучки ионов и электронов, привлекли большое внимание в области модификации поверхности [14, 15]. Известно, что такого рода модификация позволяет улучшить свойства поверхности (например, твердость и коррозионную стойкость) в результате образования мелкозернистой структуры из сильно переохлажденного расплава и метастабильных фазовых превращений, а также благодаря деформационному упрочнению, вызванному термическими напряжениями [16, 17].
Поверхностная обработка высокоэнтропийных сплавов с помощью электронных пучков была также применена в ряде работ с целью улучшения поверхностных свойств, гомогенизации элементного состава и измельчения зеренной структуры [18, 19].
Целью настоящей работы являлось исследование структуры и элементного состава высокоэнтропийного сплава, изготовленного методом проволочно-дугового аддитивного производства с использованием комбинированной проволоки из нескольких жил и подвергнутого облучению импульсным электронным пучком.
МАТЕРИАЛ И МЕТОДИКИ ИССЛЕДОВАНИЯ
Для изготовления объемных образцов в качестве исходного материала была использована проволока, состоящая из трех жил различного состава: алюминиевая проволока (Al = 99.95%, диаметр 0.5 мм), хромоникелевая проволока Х20Н80 (Cr = 20%, Ni = 80%, диаметр 0.4 мм), а также проволока из прецизионного сплава 29НК (Co = = 17%, Fe = 54%, Ni = 29%, диаметр 0.4 мм). Диаметр комбинированной проволоки составлял = = 1 мм. Образцы были получены послойным нанесением на подложку из стали с помощью плавления проволоки в атмосфере инертного газа (Ar = 99.99%) [13]. Использовался следующий режим нанесения слоев: скорость подачи проволоки 8 м/мин, напряжение 17 В, скорость движения горелки 0.3 м/мин, температура подогрева подложки = 250°С. Исходные образцы имели размеры 60 × 140 × 20 мм. Для облучения электронным пучком образцы размером 10 × 10 × 5 мм вырезали из средней части исходных образцов. Обработку поверхности сплава осуществляли на установке “СОЛО” [20] при следующих параметрах: энергия ускоренных электронов 18 кэВ, плотность энергии пучка электронов ES = 10, 15, 20, 25, 30 Дж/см2, длительность импульса пучка электронов 200 мкс, количество импульсов 3. Облучение проводили в вакууме при давлении остаточного газа (аргон) в камере установки 0.02 Па. Травление поверхности исходных образцов для выявления микроструктуры осуществляли раствором HNO3 и HCL в соотношении 1 : 3. Структуру и элементный состав поверхности облученных образцов изучали методами растровой электронной микроскопии (прибор “LEO EVO 50”, Carl Zeiss) с энергодисперсионным анализатором INCA-energy.
РЕЗУЛЬТАТЫ ИССЛЕДОВАНИЯ И ИХ ОБСУЖДЕНИЕ
Характерное изображение структуры образцов ВЭС в исходном состоянии, полученное методом растровой электронной микроскопии (РЭМ), представлено на рис. 1. Травление поверхности образцов ВЭС приводит к выявлению зеренной структуры (рис. 1а). Размеры зерен изменяются в пределах от 4 до 15 мкм. Вдоль границ зерен выявляются включения второй фазы (рис. 1б, включения указаны стрелками).
Рис. 1.
РЭМ-изображение структуры поверхности ВЭС в исходном состоянии: а – увеличение ×1000, б – увеличение ×10 000. Стрелками указаны включения второй фазы.
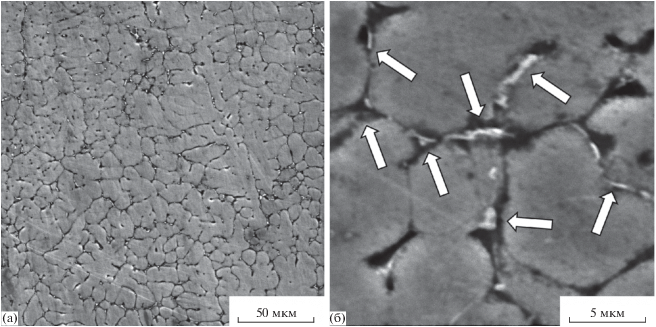
Элементный состав сплава перед облучением импульсным электронным пучком определяли методом рентгеноспектрального микроанализа (РСМА). На рис. 2а приведен энергетический спектр участка сплава, РЭМ-изображение которого представлено на рис. 2б.
Отчетливо видно, что в исследуемом материале присутствуют атомы алюминия, железа, никеля, хрома и кобальта. Результаты количественного анализа элементного состава исследуемого сплава до энергетического воздействия (усреднение осуществляли по пяти произвольно выбранным участкам) приведены в табл. 1. в строке с индексом “0”. Отчетливо видно, что основными элементами исследуемого сплава являются алюминий (36.5 ат. %) и никель (33.7 ат. %). Железо, хром и кобальт присутствуют в сравнительно меньшем количестве. Таким образом, использованный в настоящей работе метод изготовления материала приводит к формированию ВЭС неэквиатомного состава с повышенным содержанием алюминия и никеля.
Таблица 1.
Элементный состав поверхностного слоя ВСЭ в исходном состоянии и после облучения импульсным электронным пучком
ES, Дж/см2 | Концентрация, ат. % | ||||
---|---|---|---|---|---|
Al | Cr | Fe | Co | Ni | |
0 | 36.5 | 8.6 | 16.4 | 4.9 | 33.7 |
10 | 33.1 | 8.8 | 16.8 | 5.0 | 36.3 |
15 | 34.4 | 8.2 | 16.0 | 5.0 | 36.4 |
20 | 34.8 | 7.4 | 15.3 | 5.3 | 37.2 |
25 | 34.1 | 8.3 | 16.4 | 5.0 | 36.2 |
30 | 32.8 | 8.0 | 16.0 | 5.3 | 37.9 |
Методами картирования установлено, что границы зерен и примыкающие к ним области обогащены атомами хрома и железа, объем зерен обогащен атомами никеля и алюминия, кобальт распределен в сплаве квазиоднородно. Таким образом, в полученном сплаве наблюдается группирование атомов элементов по различным областям.
Облучение ВЭС импульсным электронным пучком приводит к существенному преобразованию структуры поверхностного слоя материала.
Выполненные исследования показали, что независимо от плотности энергии пучка электронов (в указанном выше диапазоне), поверхность облученного сплава разделяется на мелкие фрагменты посредством микротрещин (рис. 3а, 3б). При этом размеры фрагментов достигают нескольких сотен микрометров, существенно превышая размеры зерен исходного сплава.
Рис. 3.
РЭМ-изображения структуры поверхности образцов высокоэнтропийного сплава, облученного импульсным электронным пучком (200 мкс, 3 имп.) при различных плотностях энергии пучка электронов: а – 10 Дж/см2, б–г, д (врезка) – 30 Дж/см2.
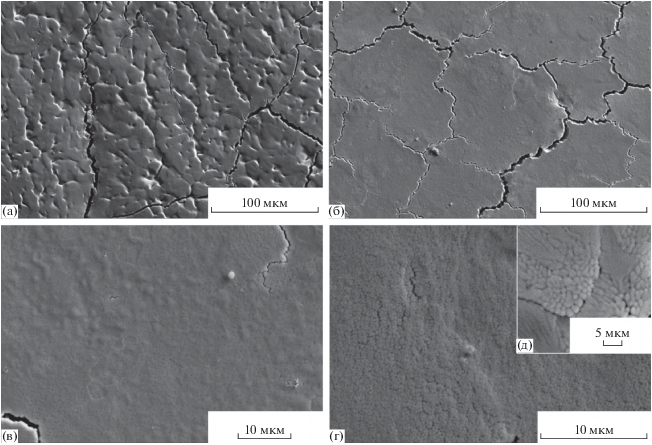
Увеличение плотности энергии пучка электронов до 30 Дж/см2 приводит к формированию поверхностного слоя, зеренная структура которого при сравнительно малых увеличениях не выявляется (рис. 3б). Последнее позволяет предположить, что высокоскоростное плавление и последующая высокоскоростная кристаллизация, имеющие место при облучении материала импульсным электронным пучком, приводит к гомогенизации поверхностного слоя образца, т.е. к формированию однородного по элементному составу сплава. В этом случае границы зерен не выявляются.
Исследование облученного сплава при больших увеличениях позволило выявить формирование в поверхностном слое субмикро- нанокристаллической структуры (рис. 3в–3д). Размеры кристаллитов изменяются в пределах от 100 до 200 нм (рис. 3г, 3д).
Методом картирования установлено, что приграничные объемы сплава (объемы, расположенные вдоль границ зерен) в исходном состоянии обогащены атомами хрома и железа, объем зерен обогащен атомами никеля и алюминия, атомы кобальта распределены в сплаве квазиоднородно.
Существует вероятность, что облучение сплава импульсным электронным пучком в режиме плавления поверхностного слоя может привести к неконтролируемому изменению элементного состава материала, связанного с удалением поверхностных загрязнений [21]. Выполненные методом РСМА исследования элементного состава поверхностного слоя ВЭС, облученного импульсным электронным пучком, не подтвердили данное предположение. Действительно, как следует из анализа результатов, приведенных в табл. 1, элементный состав поверхностного слоя сплава практически не зависит от плотности энергии пучка электронов и в пределах ошибки измерения повторяет элементный состав исходного материала.
ЗАКЛЮЧЕНИЕ
Методом проволочно-дугового аддитивного производства получен неэквиатомный высокоэнтропийный сплав системы Al–Co–Cr–Fe–Ni. Показано, что сплав является поликристаллическим агрегатом, размеры зерен которого изменяется в пределах (4–15) мкм. Вдоль границ зерен выявляются включения второй фазы. Установлено, что приграничные объемы сплава (объемы, расположенные вдоль границ зерен) обогащены атомами хрома и железа, объем зерен обогащен атомами никеля и алюминия, кобальт распределен в сплаве квазиоднородно. Показано, что облучение ВЭС импульсным электронным пучком приводит к фрагментации поверхностного слоя образцов микротрещинами. Размеры фрагментов достигают нескольких сотен микрометров, существенно превышая размеры зерен исходного сплава. Установлено, что облучение ВЭС импульсным электронным пучком (30 Дж/см2, 200 мкс, 3 имп.) сопровождается гомогенизацией поверхностного слоя образцов и образованием субмикро- нанокристаллической структуры с размером кристаллитов 100–200 нм. Показано, что облучение ВЭС в вакууме импульсным электронным пучком с теми же параметрами не приводит к изменению элементного состава сплава.
Список литературы
Miracle D.B., Senkov O.N. // Acta Mater. Elsevier Ltd. 2017. V. 122. P. 448. https://doi.org/10.1016/j.actamat.2016.08.081
Tsai M.-H., Yeh J.-W. // Mater. Res. Lett. 2014. V. 2. № 3. P. 107. https://doi.org/10.1080/21663831.2014.912690
Ye Y.F., Wang Q., Lu J., Liu C.T., Yang Y. // Mater. Today. 2016. V. 19. № 6. P. 349. https://doi.org/10.1016/j.mattod.2015.11.026
Zhang Y., Zuo T.T., Tang Z., Gao M.C., Dahmen K.A., Liaw P.K. // Prog. Mater. Sci. Elsevier Ltd. 2014. V. 61. P. 1. https://doi.org/10.1016/j.pmatsci.2013.10.001
Cantor B., Chang I.H., Knight P., Vincent A.B. // Mater. Sci. Eng. A. 2004. V. 375–377. № 1–2. P. 213. https://doi.org/10.1016/j.msea.2003.10.257
Karati A., Guruvidyathri K., Hariharan V.S., Murty B.S. // Scr. Mater. Elsevier Ltd. 2019. V. 162. P. 465. https://doi.org/10.1016/j.scriptamat.2018.12.017
Zhang Y., Zuo T.T., Tang Z., Gao M.C., Dahmen K.A., Liaw P.K. // Prog. Mater. Sci. 2014. V. 61. P. 1. https://doi.org/10.1016/j.pmatsci.2013.10.001
Yurchenko N.Y., Stepanov N.D., Shaysultanov D.G., Tikhonovsky M.A., Salishchev G.A. // Mater. Charact. 2016. V. 121. P. 125. https://doi.org/10.1016/j.matchar.2016.09.039
Niu P.D., Li R.D., Yuan T.C., Zhu S.Y., Chen C., Wang M.B. // Intermetallics. 2019. V. 104. P. 24. https://doi.org/10.1016/j.intermet.2018.10.018
Sistla H.R., Newkirk J.W., Frank Liou F. // Mater. Des. Elsevier Ltd. 2015. V. 81. P. 113. https://doi.org/10.1016/j.matdes.2015.05.027
Shiratori H., Fujieda T., Yamanaka K., Koizumi Y., Kuwabara K., Kato T. // Mater. Sci. Eng. A. Elsevier, 2016. V. 656. P. 39. https://doi.org/10.1016/j.msea.2016.01.019
Geng Y., Konovalov S.V., Chen X. // Prog. Phys. Met. 2020. V. 21. № 1. P. 26. https://doi.org/10.15407/ufm.21.01.026
Shen Q., Kong X., Chen X. // J. Mater. Sci. Technol. Elsevier Ltd. 2021. V. 74. P. 136. https://doi.org/10.1016/j.jmst.2020.10.037
Panin S.V., Vlasov I.V., Sergeev V.P., Maruschak P.O., Sunder R., Ovechkin B.B. // Int. J. Fatigue. 2015. V. 76. P. 3. https://doi.org/10.1016/j.ijfatigue.2014.10.011
Surzhikov A.P., Frangulyan T.S., Ghyngazov S.A., Vasil’ev I.P. // Tech. Phys. Lett. 2014. V. 40. № 9. P. 762. https://doi.org/10.1134/S1063785014090144
Nahmany M., Hooper Z., Stern A., Geanta V., Voiculescu I. // Metallogr. Microstruct. Anal. Springer US. 2016. V. 5. № 3. P. 229. https://doi.org/10.1007/s13632-016-0276-y
Moskvina V.A., Astafurova E.G., Ramazanov K.N., Maier G.G., Astafurov S.V., Melnikov E.V. // Mater. Charact. Elsevier. 2019. V. 153. P. 372. https://doi.org/10.1016/j.matchar.2019.05.029
Lyu P., Chen Y., Liu Z., Cai J., Zhang C., Jin Y. // Appl. Surf. Sci. Elsevier B.V. 2020. V. 504. P. 144453. https://doi.org/10.1016/j.apsusc.2019.144453
Cai J., Zu Z., Li C., Lyu P., Guan Q., Li Y. // Oxid. Met. 2020. V. 94. P. 1. https://doi.org/10.1007/s11085-020-10007-6
Ivanov Y.F., Gromov V.E., Konovalov S.V. // Arab. J. Sci. Eng. 2009. V. 34. № 2. P. 233. https://doi.org/10.111/J.2191-4281
He J., Yang J., Zhao W., Long J., Lan C., Liu E., Chen X., Li J., Yang Z., Dong P., Wang T., Shi J. // Appl. Surf. Sci. 2020. V. 515. P. 145990. https://doi.org/10.1016/j.apsusc.2020.145990
Дополнительные материалы отсутствуют.
Инструменты
Поверхность. Рентгеновские, синхротронные и нейтронные исследования