Поверхность. Рентгеновские, синхротронные и нейтронные исследования, 2021, № 9, стр. 71-75
Структура и свойства CrAlSiC пленок, осажденных вакуумно-плазменным способом в различных условиях
А. П. Рубштейн a, *, А. Б. Владимиров a, С. А. Плотников a, Е. Г. Волкова a
a Институт физики металлов им. М.Н. Михеева УрО РАН
620108 Екатеринбург, Россия
* E-mail: rubshtein@imp.uran.ru
Поступила в редакцию 12.01.2021
После доработки 25.02.2021
Принята к публикации 28.02.2021
Аннотация
Исследованы пленки CrAlSiC, осажденные в различных условиях генерации углеродной плазмы. Процесс нанесения CrAlSiC(I) происходил при одновременной работе плазменных источников катодно-дугового разряда с Cr–Al–Si-катодом и импульсного катодно-дугового разряда с графитовым катодом. Процесс CrAlSiC(II) – одновременной работе источника катодно-дугового разряда с Cr–Al–Si-катодом и газоразрядного устройства для генерации несамостоятельного разряда в аргон-ацетиленовой смеси. Структура пленок исследована с помощью электронной микроскопии и рамановской спектроскопии. Твердость и модуль упругости определены методом индентирования, коэффициент трения – при возвратно-поступательном движении стального шарика в условиях сухого трения. Установлено, что способ генерирования углеродной плазмы в процессе осаждения пленок (распыление графита или деструкция ацетилена) оказывает существенное влияние на структуру и свойства CrAlSiC. Пленка CrAlSiC(I) состоит из аморфной фазы с включениями нанозерен карбида кремния размером 10–30 нм. На поверхности имеются выступы размером 2–4 мкм. Такая структура обеспечивает высокую твердость и низкий коэффициент трения. В пленке CrAlSiC(II) кристаллические образования в аморфной матрице не обнаружены. На поверхности имеются пузыревидные образования размером до 15 мкм. По твердости и стойкости при фрикционном воздействии эта пленка уступает CrAlSiC(I), которая может быть рекомендована для практического использования.
ВВЕДЕНИЕ
Твердые пленки являются технологически перспективным материалом для увеличения ресурса работы различных изделий, подверженных износу. Интенсивно развиваются технологии осаждения покрытий, свойства которых определяются структурными элементами наноразмерного масштаба [1–4]. Разрушение материала, структура которого включает зерна микронного размера, происходит вследствие распространения трещин, возникающих в местах концентрации дислокаций у различных дефектов [5]. В наноструктурированных материалах с размерами зерна менее ста нанометров реализуется другой механизм разрушения. Особенность таких материалов состоит в наличии большого количества межзеренных границ с количеством атомов, сравнимым с их количеством в зернах. Границы тормозят движение и генерацию дислокаций, препятствуя зарождению, ветвлению и распространению трещин, что позволяет создавать уникальные свойства наноматериалов [6, 7]. К таким материалам относятся нанокомпозитные пленочные структуры, включающие аморфную матрицу и кристаллические включения карбидов, нитридов, карбонитридов переходных металлов. Исследуется физическая природа образования таких структур, влияние матрицы, легирующих элементов и размеров кристаллитов на их физико-механические и трибологические свойства [4, 8].
В настоящей работе исследованы пленки CrAlSiC(I) и CrAlSiC(II), осажденные в технологических условиях, отличающихся способом получения углеродной плазмы: импульсно-дуговое распыление графитового катода или плазмохимическая деструкция ацетилена. Источником Cr, Al и Si в обоих процессах служила Cr–Al–Si-мишень, распыляемая дуговым способом. Основная цель работы состояла в изучении структуры пленок и ее влиянии на механические свойства.
ЭКСПЕРИМЕНТ
Осаждение CrAlSiC пленок на кремниевые пластины проводили в установке УВНИПА-1-001 (АО “Кварц”, г. Калининград, Россия). Пластины очищали в смеси дистиллированной воды и этанола в ультразвуковой ванне с последующим ионным травлением в вакууме. Для нанесения пленок первого типа CrAlSiC(I) одновременно использовали источник плазмы катодно-дугового разряда с катодом состава Cr0.35Al0.55Si0.08 и источник плазмы импульсного катодно-дугового разряда с графитовым катодом. Частота импульсов дуги составляла 15 Гц, напряжение разряда – 300 В, давление – 3 × 10−3 Па. Для нанесения пленок второго типа CrAlSiC(II) одновременно использовали источник плазмы катодно-дугового разряда с катодом состава Cr0.35Al0.55Si0.08 и газоразрядное устройство для генерации несамостоятельного разряда в аргон-ацетиленовой смеси (30% Ar, 70% C2H2, P = 0.2 Па, напряжение несамостоятельного разряда 300 В, ток разряда 3А).
Растровая электронная микроскопия (РЭМ, QUANTA 200, “FEI”, Нидерланды), просвечивающая электронная микроскопия (ПЭМ, JEM-200CX, “JEOL Ltd”, Япония) и рамановская спектроскопия использованы для изучения структуры пленок.
Механические характеристики определяли методом индентирования на приборе NanoTest 600 (“Micro Materials Ltd”, Великобритания) с использованием алмазной пирамиды Берковича (индентор) при нагрузках от 1 до 256 мН. Твердость определяли по максимуму на зависимости f = H(d), где Н – твердость, d – глубина внедрения индентора.
Трибологические свойства пленок изучали на высокоскоростном приборе для испытания на трение и износ MFT-R4000 (Lanzhou Huahui Inst. Techn. Co., Китай). Испытания проводили при 25°C и относительной влажности 33% в условиях сухого скольжения. В качестве контртела использовали шарик из стали GCr15 (стандарт GB, 179–207 НВ, $\emptyset $ 6 мм), скорость скольжения – 20 мм/с, нагрузка – 3 Н.
РЕЗУЛЬТАТЫ И ОБСУЖДЕНИЕ
Толщина h и состав пленок приведены в табл. 1. Соотношение атомов хрома и алюминия (Cr/Al = = 0.4) в CrAlSiC(II) ниже, чем в распыляемом катоде (Cr/Al = 0.4), что может быть связано с разными коэффициентами распыления хрома и алюминия или экранированием в плазме ионов хрома ионами углерода. Увеличение содержания Al, как правило, сопровождается низкой кристаллизацией и увеличением доли аморфной составляющей [9, 10]. Наличие аргона в CrAlSiC(II) свидетельствует об образовании замкнутых пор.
Таблица 1.
Толщина и состав пленок
Пленка | h, нм | CCr/CAl | CC, ат. % | СSi, ат. % | CO, ат. % | СAr, ат. % |
---|---|---|---|---|---|---|
CrAlSiC(I) | 4000 | 0.6 | 14.6 | 5.9 | 4.2 | – |
CrAlSiC(II) | 3800 | 0.4 | 17.6 | 7.8 | 9.0 | 6.6 |
На рис. 1 представлены электронномикроскопические изображения пленок с соответствующими картинами дифракции электронов. В CrAlSiC(I) на фоне аморфной матрицы видны случайно расположенные нанозерна размером 10–30 нм (рис. 1а). Узкие и широкие диффузные кольца на картине микродифракции подтверждают наличие в пленке аморфной компоненты с нанокристаллическими включениями. Присутствие зерен SiC в CrAlSiC(I) было установлено ранее методом рентгеновской дифракции [11]. Точная идентификация фаз по электронограммам затруднена, но можно предположить присутствие в пленке также CrxAl(Si)1– xC и метастабильных CrC фаз. CrAlSiC(II) также состоит из аморфной компоненты с нанозернами размером менее 10 нм (рис. 1б). Размытые диффузные линии на картине микродифракции характерны для аморфного состояния. Однако линии более узкие, что может свидетельствовать о начале кристаллизации.
Рис. 1.
РЭМ-изображения пленок и соответствующие картины дифракции электронов (левый верхний угол). а – CrAlSiC(I), б – CrAlSiC(II).
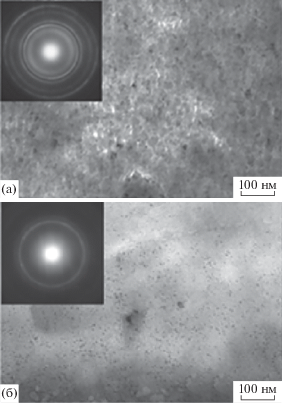
Наличие широкой полосы в диапазоне 1000–1800 см–1 на рамановских спектрах обоих пленок указывает на формирование в них непрерывного кластера углерода (рис. 2). Полосы в диапазоне (700–800) см–1 связаны с образованием металл-углеродных связей Me–C. Отличительной чертой спектра CrAlSiC(II) является отсутствие выраженного перехода между двумя (1000–1800) см–1 и (700–800) см–1 полосами спектра. Размытый переход, скорее всего, связан с началом образования зерен в пленке, что было обнаружено при изучении структуры пленки методом электронной микроскопии. Для качественной оценки количества sp3- и sp2-связанного углерода было рассчитано соотношение интегральных интенсивностей D и G пиков ID/IG. Отношение ID/IG. уменьшается с увеличением содержания sp3-связей. Более высокое значение ID/IG. = 2.07 для CrAlSiC(I) по сравнению с CrAlSiC(II) (ID/IG. = 0.89) означает графитизацию углеродной матрицы в результате роста нанозерен.
Результаты определения твердости (НIT) и модуля упругости (EIT), приведены в табл. 2. Твердость CrAlSiC(I) в 1.5 раза превышает твердость CrAlSiC(II), несмотря на высокое содержание sp2-связанного углерода. Известно, что твердость и модуль упругости углеродных пленок зависят от количества sp3-связей. Большое содержание sp3 обеспечивает, как правило, высокую твердость. Однако, некоторые теоретические и экспериментальные исследования показали, что высокая степень беспорядка связей sp2 может повышать твердость углеродных пленок [12, 13]. Кроме того, присутствие зерен SiC в CrAlSiC(I) размером 10–30 нм также оказывает влияние на твердость пленки.
Таблица 2.
Механические характеристики пленок
Пленка | НIT, ГПА | ЕIT, ГПа | Н/Е, | H3/E2, ГПа | We | fср | fmax |
---|---|---|---|---|---|---|---|
CrAlSiC(I) | 15.8 ± 0.6 | 232 ± 12 | 0.07 | 0.07 | 0.23 | 0.04 | 0.05 |
CrAlSiC(II) | 10.6 ± 0.2 | 138 ± 2 | 0.08 | 0.06 | 0.24 | 0.13 | 0.29 |
Твердость – основная характеристика износостойких материалов. Однако, многочисленные исследования показали, что параметры, сочетающие твердость и модуль упругости, например, H/E и H3/E2, являются не менее важными показателями износостойкости. Для сравнительной оценки стойкости материала к упругой деформации разрушения используется отношение HIT/EIT, называемое индексом пластичности, а для оценки сопротивления пластической деформации применяется параметр ${{H_{{{\text{IT}}}}^{{\text{3}}}} \mathord{\left/ {\vphantom {{H_{{{\text{IT}}}}^{{\text{3}}}} {E_{{{\text{IT}}}}^{{\text{2}}}}}} \right. \kern-0em} {E_{{{\text{IT}}}}^{{\text{2}}}}}.$ В качестве показателя прочности поверхностного слоя, связанного с упругим восстановлением, используется параметр We = hmax – hp/hmax, где hmax и hp, соответственно, максимальная глубина внедрения индентора и глубина после упругого восстановления при индентировании [14–16]. Как видно из табл. 2, эти показатели для пленок, осажденных в разных условиях, имеют близкие значения.
Тем не менее, трибологические тесты показали существенное отличие коэффициента трения f пленок в условиях сухого трения (рис. 3). Для CrAlSiC(I) при возрастании времени испытания (или количества циклов возвратно-поступательного движения) наблюдается небольшое изменение коэффициента трения (fср = 0.04, fmax = 0.05). Кривая зависимости коэффициента трения от времени скольжения индентора для CrAlSiC(II) после 6 мин испытания приобретает синусоидальный характер, коэффициент трения колеблется в широких пределах (fср = 0,13, fmax = 0.29). Синусоидальный характер зависимости f(t) появляется при разрушении пленки. Изучение морфологии поверхности с применением РЭМ показало, что поверхность пленок неоднородна. Выступы с отчетливыми гранями размером 2–4 мкм присущи CrAlSiC(I), пузыревидные выступы размером 5–15 мкм – CrAlSiC(II). Ранее было показано, что выступы на поверхности CrAlSiC(I) при фрикционном воздействии выкрашиваются, оказывают полирующий эффект, снижая коэффициент трения. Нарушение целостности CrAlSiC(II) при царапании алмазным индентором происходит в результате отслоения фрагментов пленки в местах образования пузыревидных дефектов [17].
ЗАКЛЮЧЕНИЕ
Проведен сравнительный анализ пленок CrAlSiC, полученных в разных условиях генерирования углеродной плазмы: распыление графита или деструкция углеводорода. Изучена структура, определены механические характеристики, измерены коэффициенты трения. Пленка CrAlSiC(I), полученная при одновременной работе дугового источника с Cr–Al–Si-катодом и импульсно-дугового с графитовым катодом, состоит из аморфной фазы с включениями нанозерен карбида кремния размером 10–30 нм. На поверхности формируются выступы размером 2–4 мкм. Такая структура обеспечивает высокую твердость и низкий коэффициент трения. Пленка CrAlSiC(II), полученная при одновременной работе дугового источника с Cr–Al–Si-катодом и газоразрядного устройства с аргон-ацетиленовой смесью, по твердости и стойкости уступает CrAlSiC(I). Несмотря на близкие значения показателей HIT/EIT, ${{H_{{{\text{IT}}}}^{{\text{3}}}} \mathord{\left/ {\vphantom {{H_{{{\text{IT}}}}^{{\text{3}}}} {E_{{{\text{IT}}}}^{{\text{2}}}}}} \right. \kern-0em} {E_{{{\text{IT}}}}^{{\text{2}}}}}$ и We, при тестировании в одинаковых условиях фрикционного воздействия пленки ведут себя по-разному. Коэффициент трения CrAlSiC(I) меняется незначительно, в то время как для CrAlSiC(II) характерны резкие колебания коэффициента трения, свидетельствующие о нарушении целостности пленки. Макродефекты, образующиеся в процессе осаждения пленок на их поверхности, наряду с твердостью, оказывают влияние на их стойкость.
Список литературы
Kumar N., Natarajan G., Pandian R., Bahuguna A., Srivastava S.K., Ravindran T.R., Rajagopalan S., Dash S., Tyagi A.K., Dumpala R., Ramachandra Rao M.S. // Surf. Coat. Technol. 2014. V. 258. P. 557. https://doi.org/10.1016/j.surfcoat.2014.08.038
Vladimirov A.B., Plotnikov S.A., Trakhtenberg I.Sh., Rubshtein A.P., Volkova E.G. // Prot. Met. Phys. Chem. Surf. 2015. V. 51. P. 230. https://doi.org/7868/S0044185615020199
Trakhtenberg I.Sh., Gavrilov N.V., Emlin D.R., Plotnikov S.A., Vladimirov A.B., Volkova E.G., Rubshtein A.P. // Phys. Metals Metallogr. 2014. V. 115. P. 723. https://doi.org/10.1134/S0031918X14070102
Rubshtein A.P., Vladimirov A.B., Korkh Yu.V. Ponosov Y.S., Plotnikov S.A. // Surf. Coat. Technol. 2017. V. 309. P. 680. https://doi.org/10.1016/j.surfcoat.2016.11.020
Финкель В.М. Физические основы торможения разрушения. М.: Металлургия, 1977. 359 с.
Gleiter H. // Acta Mater. 2000. V.48. P. 1. https://doi.org/10.1016/S1359-6454(99)00285-2
Верещака А.С., Верещака А.А. // Упрочняющие технологии и покрытия. 2005. № 9. С. 9.
Rubshtein A.P., Gao K., Vladimirov A.B., Plotnikov S.A., Zhang B., Zhang J. // Surf. Coat. Technol. 2019. V. 377. P. 124912. https://doi.org/10.1016/j.surfcoat.2019.124912
Fu T.C., Li G.W. // Appl. Surf. Sci. 2006. V. 253. P. 1260. https://doi.org/10.1016/j.apsusc.2006.01.069
Rubshtein A.P., Vladimirov A.B., Plotnikov S.A. // Sol. Stat. Phenom. 2018. V. 279. P. 160. https://doi.org/10.4028/www.scietific.net/SSP.279.153
Rubshtein A.P., Vladimirov A.B., Plotnikov S.A // J. Physics: Conference Series. 2019. V. 1281. P. 12065. https://doi.org/10.1088/1742-6596/1281/1/012065
Jiang J.L., Wang Q., Huang H., Wang Y.B., Zhang X., Hao J.Y. // Surf. Coat. Technol. 2014. V. 240. P. 419. https://doi.org/10.1016/j.surfcoat.2013.12.067
Rybachuk M., Bell J.M. // Thin Solid Films. 2007. V. 515. P. 7855 https://doi.org/10.1016/j.tsf.2007.04.040
Тополянский П.А., Ермаков С.А., Соснин Н.А., Тополянский А.П. // Металлообработка. 2013. № 4(76). С. 28.
Leyland A., Matthews A. // Wear. 2000. V. 246. P. 1. https://doi.org/10.1016/S0043-1648(00)00488-9
Штанский Д.В., Кулинич С.А., Левашов Е.А., Moore J.J. Физика твердого тела. 2003. Т. 45(6). С. 1122.
Рубштейн А.П., Завалишин В.А., Владимиров А.Б., Плотников С.А. C. // Вакуумная техника и технологии – 2020. Труды 27-й Всероссийской научно-технической конференции с международным участием / Под ред. Д.К. Кострина и С.А. Марцынюкова. Санкт-Петербург: Изд-во СПбГЭТУ “ЛЭТИ”. С. 123. https://vtt.etu.ru/assets/files/sbornik_vtt-2020.pdf.
Дополнительные материалы отсутствуют.
Инструменты
Поверхность. Рентгеновские, синхротронные и нейтронные исследования