Поверхность. Рентгеновские, синхротронные и нейтронные исследования, 2022, № 1, стр. 86-95
Влияние трансмембранного давления на морфологию поверхности и кинетические характеристики пористых пленок МФФК-3 и ПП-190
С. И. Лазарев a, С. А. Нагорнов b, С. В. Ковалев a, c, *, Д. Н. Коновалов a, **, А. Ю. Корнев b
a Тамбовский государственный технический университет
392000 Тамбов, Россия
b Всероссийский научно-исследовательский институт использования
техники и нефтепродуктов в сельском хозяйстве
392000 Тамбов, Россия
c Тамбовский государственный университет им. Г.Р. Державина
392000 Тамбов, Россия
* E-mail: sseedd@mail.ru
** E-mail: kdn1979dom@mail.ru
Поступила в редакцию 22.03.21
После доработки 07.05.2021
Принята к публикации 14.05.2021
- EDN: JBBWCG
- DOI: 10.31857/S1028096022010095
Аннотация
Рассмотрена проблема очистки биотоплива с использованием методов микрофильтрации и предварительной фильтрации при различном трансмембранном давлении. Приведена схема экспериментальной установки для проведения процесса микрофильтрации. Одним из главных элементов установки является рабочая ячейка плоскокамерного типа, конструкция которой подробно описана. Для осуществления процесса мембранной очистки подобраны рабочие образцы микрофильтрационной мембраны МФФК-3 и предварительного фильтра ПП-190 производства ООО НПП “Технофильтр”, г. Владимир. Получены кинетические зависимости удельного выходного потока для пористых пленок МФФК-3 и ПП-190 в зависимости от времени при различном трансмембранном давлении. На зависимостях наблюдаются четыре периода изменения удельного выходного потока, где формируются гелевые сгустки на мембране МФФК-3 и фильтре ПП-190. Приведены зависимости содержания воды в фильтрате от трансмембранного давления. Для отделения воды от Э-фазы необходимо поддержание давления в баромембранной системе не менее 0.5 МПа. Проведены электронно-микроскопические исследования исходных и рабочих образцов пористых пленок МФФК-3 и ПП-190. Хроматографический анализ пермеата и концентрата после микрофильтрационной очистки показал, что через мембранную перегородку проходят такие компоненты, как метанол, маргариноолеиновая, олеиновая, бегеновая, уруковая, доказадиеновая кислоты, образуя на поверхности динамический гелевой слой, предотвращающий пропускание молекул воды.
ВВЕДЕНИЕ
На промышленных предприятиях машиностроения, химической, биологической промышленности для разделения, очистки технологических растворов применяют фильтрацию, баромембранные и другие процессы, в том числе микро- и ультрафильтрацию. Но существует проблема с подбором мембран, которые могли бы обладать высокими показателями для качественного разделения растворенных веществ и высокой производительностью во времени, поэтому исследования таких процессов являются актуальной задачей [1–3]. В [4, 5] методами рентгенографии, растровой и просвечивающей электронной микроскопии исследовано влияние ряда факторов на структуру аморфных сплавов на основе алюминия, железа и кобальта.
При очистке биологических, пищевых жидкостей, а также топлива и масел мембранные процессы сопровождаются образованием осадка и гелевых сгустков, своеобразным воздействием компонентов водной среды, эмульсий на поверхность активного слоя мембран. Фильтрационные, баромембранные процессы требуют современного конструктивного оформления аппаратов, обеспечивающих высокое качество очистки и разделения, хорошую производительность при малых энергозатратах [6–8].
Имеется небольшое количество публикаций, посвященных исследованию фильтрации, мембранной технологии для очистки, разделения топлив и масел. В [9] отмечается, что наиболее выгодным сырьем для производства биодизеля (транспортного топлива, альтернативного нефтяному дизелю) являются осадки канализационных очистных предприятий, донные илы, извлекаемые из водоемов при восстановлении качества воды, так как практически не требуются экономические затраты на производство этого сырья. Кроме того, происходит утилизация таких отходов.
В [10] доказано, что коронная обработка полиакрилонитрильных и полиэфирсульфоновых мембран в поле униполярного коронного разряда позволяет повысить производительность мембранной очистки эмульсий типа “масло в воде” при уменьшении токсичности пермеатов. Для очистки отработанных моторных масел в [11] предлагается мембранная технология разделения жидких полидисперсных систем, которая позволяет снизить энергоемкость перерабатывающего производства.
В [12] приведены данные экспериментальных исследований, доказывающие влияние технологических параметров на производительность и качество электромембранного разделения трехкомпонентного раствора органическое вещество–неорганическая соль–вода. Материалы исследований [13] показывают эффективность физико-химических методов очистки дизельного топлив от смол, серы и других примесей. Отстаивание и центрифугирование также повышают противоизносные свойства дизельного топлива.
Исследования характеристик дизельного двигателя с турбонаддувом и состава выхлопных газов [14] доказали эффективность применения добавок биотоплива (метанола, бутанола и этанола) в сравнении с очищенным дизельным топливом вследствие отсутствия в составе серы и серной кислоты. В [15] исследованы кинетические характеристики непористых диффузионных мембран, позволяющие эффективно очищать н-бутанол от водных примесей мембранным методом.
В [16] изучено влияние параметров униполярного коронного разряда (время обработки, напряжение) на кинетические характеристики полиэфирсульфоновой мембраны при разделении модельных эмульсий типа “нефть в воде”. Получены изображения с изменениями сорбционной поверхности мембран, обработанных в коронном разряде.
На основе проведенных исследований по регенерации отработанных масел и топлива в [17] разработаны технология и регламент экстракционной очистки (рафинирования). Для очистки и разделения отработанного моторного масла в [18] предложен перспективный баромембранный метод (нанофильтрация).
В [19] изучен баромембранный процесс очистки и разделения моторных масел с применением микрофильтрационных мембран (полимерных, металлокерамических, керамических, углеродных). Доказано, что на кинетические характеристики процесса микрофильтрации оказывает влияние материал мембраны и ее размеры.
В [20] исследован процесс ультрафильтрации отработанного моторного масла, позволяющий определить температуру вспышки системы масло–присадка, разделив его на компоненты. Понизить температуру вспышки очищенного масла можно, добавляя реагент на основе химических элементов, из которых состоит применяемая в масле присадка. Обзор работ [1–20] позволяет отметить, что повышение качества топлива, снижающего количество вредных выбросов в атмосферу, в настоящее время является актуальной задачей и относится к приоритетным направлениям развития экономики и промышленности как в Российской Федерации, так и за ее пределами. Поэтому целью работы было проведение кинетических, электронно-микроскопических и хроматографических исследований влияния трансмембранного давления на морфологию поверхности и кинетические характеристики пористых пленок МФФК-3, ПП-190 в процессе мембранной очистки биотоплива.
ЭКСПЕРИМЕНТАЛЬНАЯ ЧАСТЬ
Объектами исследования были смесь метилового эфира растительного масла (Э-фаза) и воды в соотношении 1 : 1 (объем 5 л), а также исходные и рабочие образцы микрофильтрационной мембраны МФФК-3, предварительного фильтра ПП-190 (производство ООО НПП “Технофильтр”, г. Владимир), характеристики которых представлены в табл. 1, 2 [21].
Таблица 1.
Характеристики микрофильтрационной мембраны МФФК-3
Средний диаметр пор, мкм | Производительность по этиловому спирту, при Р = 0.05 МПа J, дм3/(м2 · ч), |
Точка пузырька по этанолу | Рабочее давление, кПа · (кгс/см2) | Максимальная температура, К | Диапазон pH |
---|---|---|---|---|---|
0.45 | Не менее 7500 | 56 | Не менее 0.56 | 353 | 1–13 |
Таблица 2.
Характеристики предварительного фильтра ПП-190
Эффективность удержания частиц, мкм | Начальная производительность по дистиллированной воде, при P = 0.05 МПа, см3/см2 мин | Максимальный перепад давления, МПа | Максимальная температура, К | Диапазон pH | |
---|---|---|---|---|---|
Не менее 98% | Не менее 95% | ||||
3 | 2 | Не менее 400 | 0.5 при 293 К, 0.2 при 353 К | 363 | 2–13 |
Микрофильтрационная фторопластовая композиционная гидрофобная мембрана типа МФФК представляет собой пористый полимерный пленочный материал на основе фторопласта Ф42Л на подложке из нетканых материалов (полипропилен, лавсан) с размером пор 0.45 мкм и общей пористостью 80–85 [21]. Полипропиленовые фильтры марки ПП используют для предварительной и тонкой осветляющей фильтрации жидкостей с высоким уровнем отделения частиц или для снижения нагрузки на мембранные фильтры [21].
Методика исследования состояла в следующем. Эксперимент по исследованию кинетических характеристик пористых пленок при микрофильтрационном разделении технологических растворов проводили на установке, представленной на рис. 1 [3]. Исходный раствор из расходной емкости 1 через вентиль Вр1 подавали в плунжерный насос 2 марки НД 100/63, который создавал рабочее давление и направлял исходный раствор через вентиль высокого давления Вр2 в гидроаккумулятор 6, сглаживающий пульсации давления и расхода раствора в системе. Гидроаккумулятор 6 представляет собой цилиндрический бак объемом 3.5 л, верхняя часть которого заполнена воздухом, сжатым компрессором высокого давления 9 через вентиль Вр7 до давления, составляющего 30–40% от рабочего. Давление воздуха в гидроаккумуляторе 6 фиксировали с помощью манометра 7. В случае превышения давления воздух стравливали вентилем Вр8. Из гидроаккумулятора 6 исходный раствор через вентиль Вр4 подавали в рабочую ячейку 3, давление контролировали с помощью образцового манометра 8. Электроконтактный манометр 12 с помощью электроконтактного реле выключал плунжерный насос 2 при превышении давления выше установленного значения [22].
Рис. 1.
Схема лабораторной баромембранной установки: 1 – расходная емкость; 2 – плунжерный насос НД 100/63; 3 – рабочая ячейка; 4 – дроссель; 5 – поплавковые ротаметры; 6 – гидроаккумулятор; 7 – манометр; 8 – образцовый манометр; 9 – компрессор высокого давления; 10 – термометр; 11 – емкости; 12 – электроконтактный манометр.
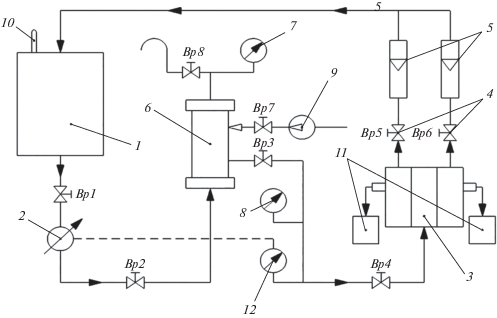
Разделяемый раствор в виде ретентата, пройдя рабочую ячейку 3 через дроссели 4 и поплавковые ротаметры 5, возвращался обратно в расходную емкость 1. Расход раствора задавали рабочим ходом плунжерного насоса 2. Температуру раствора в системе определяли с помощью термометра 10. Жидкость в виде пермеата, прошедшая в процессе разделения через мембраны рабочей ячейки 3, собиралась в емкости 11 [22]. Трубопроводы, плунжер насоса, игольчатые вентили, соприкасающиеся с насосом, были изготовлены из нержавеющей стали. Колебания давления и расхода на описанной установке не превышали 5% от установленного значения [22].
Одним из главных элементов установки является рабочая ячейка плоскокамерного типа, в которой непосредственно происходит процесс микрофильтрационного разделения. Конструкция микрофильтрационной ячейки представлена на рис. 2 [3]. Ячейка представляет собой двухкамерный разделительный модуль, выполненный из нержавеющей стали. Рабочий раствор подается в штуцер ввода исходного раствора 4 ячейки и равномерно распределяется по камерам разделения, образованным двумя мембранами 11 и поверхностями средней части 1, и выходит по штуцерам вывода ретентата 5. Часть раствора под действием избыточного давления проникает через мембраны 11, затем через ватман 12, служащий прокладкой под микрофильтрационной мембраной, далее через пористую подложку 13, затем через металлическую сетку 14, выполненную из нержавеющей стали, и по каналам, сделанным в штуцерах, попадает в сборники пермеата (бюксы объемом 50 мл). С каждой стороны ячейки на диэлектрических фланцах корпуса 2 расположены по три штуцера вывода пермеата 6. Для уплотнения фланцев 2 со средней частью 1 ячейки используют прокладки 7 из паронита толщиной (0.3–2) × 10–3 м. Ячейка стягивается шестью болтами 8 при помощи шайб 9 и гаек 10. Для равномерного распределения стягивающего усилия используют металлические пластины 3. Размеры камер разделения ячейки в собранном виде составляют 0.06 × 0.13 × (0.0003–0.002) м. Рабочая площадь мембран в каждой камере разделения равна 7.8 × 10–3 м2 [22].
Рис. 2.
Схема микрофильтрационной ячейки: 1 – средняя часть ячейки; 2 – диэлектрический фланец корпуса; 3 – металлическая пластина; 4 – штуцер ввода исходного раствора; 5 – штуцеры вывода ретентата; 6 – штуцеры вывода пермеата; 7 – прокладка; 8 – болт; 9 – шайба; 10 – гайка; 11 – мембрана; 12 – ватман; 13 – пористая подложка; 14 – металлическая сетка.
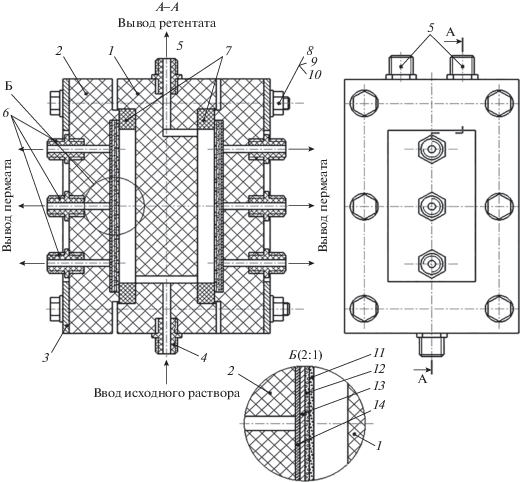
Перед проведением экспериментальных исследований требуется выполнить подготовительные операции, для чего в начале эксперимента необходимо осмотреть образцы исследуемых пористых пленок на наличие дефектов. После этого микрофильтрационную мембрану вымачивают в дистиллированной воде для удаления глицерина с поверхности активного слоя и порового пространства. Непосредственно перед проведением эксперимента мембраны погружали в исследуемые растворы. После предварительной подготовки пористые пленки устанавливают в разделительный модуль. Мембрану необходимо расположить на подложке (ватмане) так, чтобы она не имела контакта с металлическими поверхностями. Мембрану располагают к разделяемому раствору активным слоем. Затем баромембранный модуль устанавливают на лабораторную установку. Необходимый расход для обеспечения требуемой скорости в межмембранном канале регулируется ходом плунжера насоса 2 (рис. 1). Рубашка плунжера насоса 2 охлаждается водой, подаваемой из центральной магистрали водоснабжения. Затем при закрытых вентилях 4 включают плунжерный насос 2. В течение 30 мин проводят холостой опыт для стабилизации трансмембранного давления. Затем выключают установку, сбрасывается давление в системе. Пермеат из емкостей 11 сливается в расходную емкость 1, и установка не используется в течение нескольких часов. После выдерживания оставшийся раствор в установке возвращается в расходную емкость 1. Запускают установку, выводят на рабочий режим и проводят контрольный опыт в течение 4 ч для обжатия мембран и приведения их в рабочее состояние. В зависимости от производительности мембран и необходимого количества собранного в течение 0.5–2 ч пермеата проводят рабочий опыт. Для фиксации времени проведения эксперимента используют секундомер, с помощью мерного цилиндра измеряют объем собранного пермеата, а в полученном объеме пермеата определяют концентрацию растворенных веществ. После проведения рабочего эксперимента трансмембранное давление сбрасывают, установка отключают [22].
Удельный выходной поток, полученный через мембранную перегородку, рассчитывают по следующей зависимости [23, 24]:
где V – объем собранного пермеата [м3]; Fм– рабочая площадь мембраны [м2]; $\tau $ – время проведения эксперимента [с].Следующим этапом экспериментов были электронно-микроскопические исследования исходных и рабочих образцов пористых пленок МФФК-3, ПП-190. Поверхности заранее выбранных для эксперимента воздушно-сухих и рабочих образцов пористых пленок МФФК-3, ПП-190 изучали с помощью растрового электронного микроскопа (РЭМ) JEOL JSM 6510 при различном увеличении и многократной повторяемости эксперимента. На рис. 3, 4 представлены выборки РЭМ-изображений исходных образцов пористых пленок МФФК-3 и ПП-190.
Рис. 4.
РЭМ-изображения воздушно-сухих образцов предварительного фильтра ПП-190, полученные с разным увеличением: а – ×400; б – ×550; в – ×2000; г – ×3500.
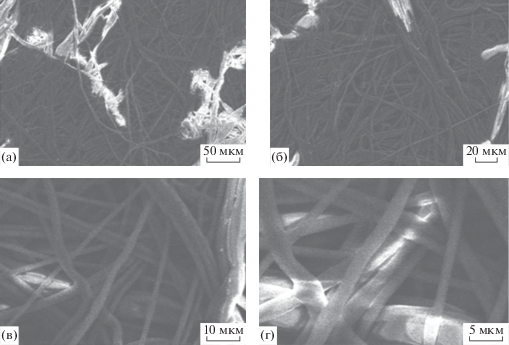
Полученные образцы пермеата и ретентата после фильтрации через мембрану МФФК-3 (рис. 5) анализировали на содержание растворенных компонентов при помощи хроматографии, а также определяли концентрацию воды, плотность и вязкость раствора. Для проведения хроматографического анализа использовали метод внутреннего стандарта. При приготовлении калибровочных образцов и внутреннего стандарта использовали хроматографически чистые вещества. Анализ проводили в соответствии с инструкцией работы на хроматографе. Для анализа использовали аппаратно-программный комплекс “Кристалл 4000М” с пламенно-ионизационным детектором, поток делили в соотношении 1 : 30, диапазон формируемых давлений 20–250 кПа.
Рис. 5.
Образцы пермеата (фильтрата) при давлении 0.15 (1), 0.25 (2), 0.35 (3), 0.50 МПа (4) и ретентата (концентрата) (5).
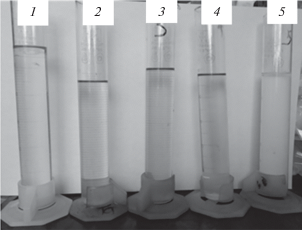
Технические данные аппаратно-программного комплекса “Кристалл 4000М”: температура колонки 170–280°С; скорость подъема 15 град/мин; температура детектора 290°С; температура испарителя 280°С; количество изотерм – одна; скорость охлаждения от 280 до 50°С за 16 мин; температурная стабильность 0.1°С; расход газа-носителя от 10 до 100 мл/мин.
РЕЗУЛЬТАТЫ И ИХ ОБСУЖДЕНИЕ
На рис. 6, 7 представлены зависимости удельного выходного потока для пористых пленок МФФК-3 и ПП-190 от времени эксперимента при различном трансмембранном давлении. Анализ зависимости функции J = f(τ, Р) мембранной системы (рис. 6) показал, что с увеличением продолжительности экспериментальных исследований удельный выходной поток пермеата мембраны МФФК-3 снижается. Особенно четко это наблюдается в интервале 600–1200 с при трансмембранном давлении 0.15 МПа (первый период). Это, вероятно, связано с частичным блокированием пор органическими соединениями, содержащимися в исходном растворе. Однако далее устанавливается период (второй период 1200–5400 с), в течение которого, вероятно, некоторые органические соединения (кислоты) исходного раствора на поверхности мембраны создают примембранный гелевой слой, а другие движутся над ним. Таким образом, можно предположить, что над поверхностью мембраны из оставшихся элементов формируется динамический гелевой слой, причем его формирование заканчивается уплотнением примембранного слоя во временном интервале 5400–7200 с (третий период) (рис. 6). Подобное утверждение может быть связано с тем, что с течением времени в исходном растворе появляется больше воды за счет концентрирования, а эфира и других кислот – меньше за счет проникания их в пермеат. Дальнейшее фильтрование происходит в установившемся режиме 7200–10800 с (четвертый период).
Рис. 6.
Зависимость удельного выходного потока для мембраны МФФК-3 от времени эксперимента при различном трансмембранном давлении.
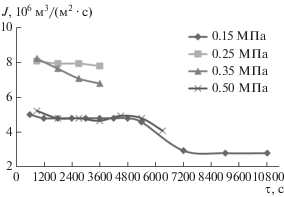
Рис. 7.
Зависимость удельного выходного потока для предварительного фильтра ПП-190 от времени эксперимента при различном трансмембранном давлении.
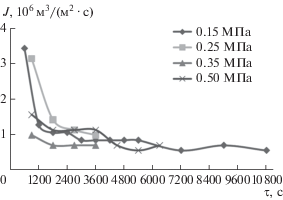
Тем не менее с ростом трансмембранного давления от 0.15 до 0.25 МПа наблюдается увеличение удельного выходного потока, что связано с возрастанием движущей силы процесса баромембранного разделения. При дальнейшем увеличении трансмембранного давления удельный выходной поток на мембране снижается. Вероятно, основная причина – изменение концентрации ретентата, а также его кинематической вязкости и плотности в связи с проницанием в пермеат части воды.
Анализ зависимости функции J = f(τ, Р) мембранной системы (рис. 7) показал, что с увеличением продолжительности экспериментальных исследований удельный выходной поток пермеата предварительного фильтра ПП-190 подчиняется уравнению фильтрования в интегральной форме при постоянном трансмембранном давлении. С течением времени скорость фильтрования уменьшается по нелинейному закону (так как сопротивление осадка увеличивается), а удельный объем фильтрата и высота слоя осадка увеличиваются [25]. С ростом трансмембранного давления от 0.15 до 0.35 МПа также отмечается уменьшение удельного выходного потока.
На рис. 8, 9 представлены РЭМ-изображения рабочих образцов микрофильтрационной мембраны МФФК-3 и предварительного фильтра ПП-190. Анализ изображений образцов пористых пленок МФФК-3 и ПП-190 (воздушно-сухих и рабочих образцов), полученных при различных увеличениях до и после действия трансмембранного давления, показывает морфологические особенности их поверхности. Фиксируются остаточные гелевые сгустки, которые отчетливо видны на рис. 8а–8в, в отличие от предварительного фильтра ПП-190 (рис. 9), на изображениях которых такие образования отсутствуют.
Рис. 8.
РЭМ-изображения рабочих образцов микрофильтрационной мембраны МФФК-3, полученные с разным увеличением: а – ×370; б – ×1800; в – ×3500; г – ×7000.
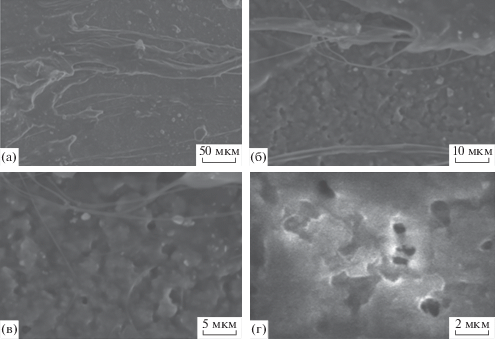
Рис. 9.
РЭМ-изображения рабочих образцов предварительного фильтра ПП-190, полученные с разным увеличением: а – ×650; б – ×1800; в – ×3000.
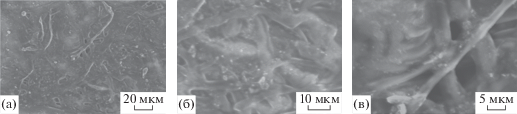
При сравнении РЭМ-изображений исходных и рабочих образцов (рис. 3, 8) можно отметить, что действительно на поверхности активного слоя видны гелевые образования. В случае предварительного фильтра такие образования отсутствуют. Поверхность рабочего образца предварительного фильтра забита продуктами разделения исходного раствора, что отмечается при сравнении рис. 4 и 9 и также подтверждается экспериментальными исследованиями кинетических характеристик, где с течением времени происходит снижение удельного выходного потока. Поэтому при работе с пористыми пленками МФФК-3, ПП-190 при действии трансмембранного давления их активный слой может изменять свою структуру. Это, вероятно, может привести к снижению или увеличению доли кристаллических или аморфных областей в активном слое мембраны, что влияет на разделительные характеристики пористых пленок МФФК-3 и ПП-190.
Хроматографическим методом обнаружено, что после мембранной фильтрации смеси метилового эфира растительного масла (Э-фаза) и воды изменяется ее компонентный состав (табл. 3). Учитывая, что процесс микрофильтрационного разделения показал свою эффективность, анализ хроматограмм проводят именно после баромембранного разделения. Фиксируют различие хроматограмм пермеата и концентрата после разделения. Анализ показал, что после разделения через микрофильтрационную мембрану проходят такие компоненты, как метанол, маргариноолеиновая, олеиновая, бегеновая, уруковая, доказадиеновая кислоты, образуя на поверхности частичный динамический гелевой слой и затормаживая пропускание молекул воды. Концентрация, например, метанола в образце № 1 пермеата (при трансмембранном давлении 0.15 МПа) превышает более чем в три раза концентрацию в образце № 4 (при трансмембранном давлении 0.5 МПа), что хорошо коррелирует с полученными данными кинетических характеристик мембранного разделения. Однако под действием трансмембранного давления происходит проскок небольшого количества воды.
Таблица 3.
Изменение компонентного состава смеси метилового эфира растительного масла (Э-фаза) и воды после микрофильтрационной очистки
Наименование компонента | Концентрация, % | ||
---|---|---|---|
Образец № 1 | Образец № 4 | Образец № 5 | |
Метанол | 6.048 | 1.899 | 1.056 |
Маргариноолеиновая кислота | 5.680 | 5.822 | 6.608 |
Олеиновая кислота | 8.660 | 9.075 | 9.128 |
Бегеновая кислота | – | 6.194 | 2.997 |
Эруковая кислота | 1.070 | 7.151 | 5.386 |
Доказадиеновая кислота | 6.027 | 1.898 | 2.164 |
Результаты анализа образцов пермеата и ретентата после микрофильтрационной очистки на мембране МФФК-3 на содержание воды, плотность, вязкость, представлены в табл. 4. По результатам проведенных исследований установлено, что принципиально процесс микрофильтрационной очистки позволяет разделить воду и Э-фазу, однако сразу после разделения остаточное содержание воды в любой пробе все еще достаточно высокое по сравнению с нормами как для дизельного топлива (не более 200 мг/кг), так и для эфиров (не более 500 мг/кг).
Таблица 4.
Физико-химические характеристики образцов пермеата и концентрата
Показатель | Номер пробы | ||||
---|---|---|---|---|---|
1 | 2 | 3 | 4 | 5 | |
Вязкость кинематическая при 293 К, мм2/с | 6.01 | 5.68 | 5.48 | 5.51 | 4.28 |
Вязкость кинематическая при 313 К, мм2/с | 3.94 | 3.97 | 4.24 | 4.15 | 3.18 |
Плотность, кг/м3 | 893.3 | 889.6 | 883.4 | 883.4 | 940 |
Содержание воды, % | 1.6 | 1.2 | 0.6 | 0.4 | 40 |
pH водной вытяжки | 8.1 | 7.6 | 7.2 | 6.8 | 12 |
После отстаивания в течение нескольких часов часть воды выпала на дно емкости, и в объеме ее содержание снизилось (рис. 10, 11). Таким образом, для отделения воды от Э-фазы необходимо поддержание давления в баромембранной системе не менее 0.5 МПа, однако при этом количество воды остается слишком большим (0.18%), и для доведения ее содержания до нормы – от 0.02% для дизельного топлива до 0.05% для биодизеля – нужно проводить доочистку или вторично разделять полученный пермеат. Минимального значения 0.05% удалось достичь при отстаивании и декантировании верхнего слоя образца.
ЗАКЛЮЧЕНИЕ
Проведенные исследования кинетическим, электронно-микроскопическим и хроматографическим методами в процессе микрофильтрационной очистки позволяют сделать следующие выводы.
Получены кинетические зависимости удельного выходного потока для пористых пленок МФФК-3 и ПП-190 в зависимости от времени при различном трансмембранном давлении. Отмечены четыре периода изменения удельного выходного потока, где формируются гелевые сгустки на мембране МФФК-3, которые существенно влияют на процесс баромембранного разделения, а предфильтр ПП-190 засоряется (забивается). Приведены зависимости содержания воды в пермеате от трансмембранного давления. Для отделения воды от Э-фазы необходимо поддерживать давление в мембранной системе не менее 0.5 МПа.
Электронно-микроскопические исследования исходных и рабочих образцов микрофильтрационной мембраны МФФК-3 показывают, что на поверхностности активного слоя осаждаются гелевые сгустки, вероятно, продукты органических кислот, а предфильтр ПП-190 засоряется (забивается) продуктами разделения Э-фазы. Хроматографический анализ пермеата и концентрата после микрофильтрационной очистки показал, что через мембранную перегородку проходят такие компоненты, как метанол, маргариноолеиновая, олеиновая, бегеновая, уруковая, доказадиеновая кислоты, а некоторые из них служат для образования на поверхности динамического гелевого слоя, затормаживающего пропускание молекул воды.
Результаты исследований на растровом электронном микроскопе получены с использованием оснащения Центра коллективного пользования научным оборудованием ТГУ имени Г.Р. Державина.
Список литературы
Фазуллин Д.Д., Яровикова Д.А., Маврин Г.В., Шайхиев И.Г., Дряхлов В.О. // Вестн. технолог. ун-та. 2021. Т. 24. № 1. С. 57.
Воронюк И.В., Елисеева Т.В., Селеменев В.Ф. // Сорбционные и хроматографические процессы. 2020. Т. 20. № 6. С. 765. https://doi.org/10.17308/sorpchrom.2020.20/3145
Лазарев С.И. Научные основы электрохимических и баромембранных методов очистки, выделения и получения органических веществ из промышленных стоков. Дис. … д-ра тех. наук: 05.17.03. Тамбов: ТГУ, 2001. 543 с.
Abrosimova G.E., Aronin A.S. // Phys. Solid State. 2017. V. 59. № 11. P. 2248. https://doi.org/10.21883/FTT.2017.11.45066.142
Abrosimova G.E., Aronin A.S. // J. Surf. Invest.: X-ray, Synchrotron Neutron Tech. 2018. V. 12. № 3. P. 492. https://doi.org/10.1134/S1027451018030023
Lazarev S.I., Kovalev S.V., Kovaleva O.A., Konovalov D.N. // Russ. Eng. Res. 2020. V. 40. № 3. P. 198. https://doi.org/10.3103/S1068798X20030168
Ковалев С.В., Лазарев С.И., Ковалева О.А., Коновалов Д.Н. // Вестн. машиностроения. 2020. № 2. С. 34.
Kovalev S.V., Lazarev S.I., Konovalov D.N., Lua P. // Chem. Petroleum Eng. 2020. V. 56. № 1–2. P. 109. https://doi.org/10.1007/s10556-020-00747-2
Kuchkina A.Yu., Sushchik N.N. // J. Sib. Federal Univ. Biol. 2014. V. 7. № 1. P. 14. http://elib.sfu-kras.ru/ handle/2311/13340
Сафина Г.Ш., Дряхлов В.О., Галиханов М.Ф., Шайхиев Т.И., Фридланд С.В. // Вестн. технолог. ун-та. 2015. Т. 18. № 14. С. 229.
Пахотина И.Н., Осадчий Ю.П., Пахотин Н.Е. // Информационная среда вуза. 2016. № 1 (23). С. 241.
Липин А.Г., Бурчу М.П., Липин А.А. // Современные наукоемкие технологии. Региональное приложение. 2013. № 3 (35). С. 98.
Остриков В.В., Вигдорович В.И., Оробинский В.И., Афоничев Д.Н., Забродский И.А. // Химия и технология топлив и масел. 2018. № 5(609). С. 53.
Дэсин П. // Химия и технология топлив и масел. 2018. № 1(605). С. 20.
Пулялина А.Ю., Файков И.И., Нестерова В.П., Подешво И.В., Полоцкая Г.А. // Мембраны и мембранные технологии. 2019. Т. 9. № 5. С. 348. https://doi.org/10.1134/S2218117219050079
Шайхиев И.Г., Дряхлов В.О., Галиханов М.Ф. Фазуллин Д.Д., Маврин Г.В. // Перспективные материалы. 2020. № 6. С. 30.
Дмитриева З.Т. // Химия и технология топлив и масел. 2017. № 4(602). С. 50.
Пахотин Н.Е., Осадчий Ю.П., Пахотина И.Н. // Современные материалы, техника и технологии. 2017. № 7(15). С. 63.
Гриценко В.О., Орлов Н.С. // Мембраны. Сер. Критические технологии. 2002. № 16. С. 10.
Морозов И.В., Осадчий Ю.П., Маркелов А.В., Пахотин Н.Е., Крикунов А.В. // Аграрный вестн. Верхневолжья. 2018. № 2(23). С. 87.
https://www.technofilter.ru/catalog/laboratory-filtration/filtry-dlya-laboratoriy/ (дата обращения: 07.02.2021).
Абоносимов О.А. Научные и практические основы электробаромембранной технологии в процессах химической водоподготовки и регенерации промышленных растворов. Автореф. дис. … д-ра тех. наук: 05.17.03. Тамбов: ФГБОУ ВО ТГТУ, 2016. 364 с.
Дытнерский Ю.И. Обратный осмос и ультрафильтрация. М.: Химия, 1978. 352 с.
Свитцов А.А. Введение в мембранную технологию. М.: ДеЛи принт, 2007. 208 с.
Голубев Г.В. // Вестн. Нижегородского ун-та им. Н.И. Лобачевского. 2011. № 4(3). С. 725.
Дополнительные материалы отсутствуют.
Инструменты
Поверхность. Рентгеновские, синхротронные и нейтронные исследования