Поверхность. Рентгеновские, синхротронные и нейтронные исследования, 2022, № 1, стр. 24-29
Исследование термической стабильности литых и микрокристаллических сплавов Al–2.5Mg–Sc–Zr
А. В. Нохрин a, Я. С. Шадрина a, *, В. Н. Чувильдеев a, В. И. Копылов a, b, А. А. Бобров a, К. В. Лихницкий a
a Нижегородский государственный университет им. Н.И. Лобачевского
603950 Нижний Новгород, Россия
b Физико-технический институт Национальной Академии Наук Беларуси
220141 Минск, Беларусь
* E-mail: janashadr@gmail.com
Поступила в редакцию 12.04.2021
После доработки 22.05.2021
Принята к публикации 27.05.2021
- EDN: WTCWLO
- DOI: 10.31857/S1028096022010113
Аннотация
Представлены результаты исследований структуры и микротвердости при отжиге литых и микрокристаллических алюминиевых сплавов Al–2.5% Mg–Sc–Zr с суммарным содержанием Sc и Zr, равным 0.32%. Содержание Sc варьируется от 0.1 до 0.22% с интервалом в 0.02%, пропорционально изменяется концентрация Zr в сплаве. В исходном состоянии литые сплавы характеризуются однородной крупнозернистой макроструктурой. Микрокристаллические сплавы получены путем равноканального углового прессования и имеют в исходном состоянии однородную мелкозернистую структуру. Определена температура начала рекристаллизации микрокристаллических сплавов. Определены механизмы и температура начала выделения частиц из пересыщенного твердого раствора в литых и микрокристаллических сплавах согласно уравнению Джонсона–Мела–Аврами–Колмогорова. Установлено, что частичное замещение скандия цирконием приводит к монотонному увеличению термической стабильности твердого раствора Sc и Zr в алюминии.
ВВЕДЕНИЕ
Высокопрочные микрокристаллические алюминиевые сплавы активно разрабатываются в качестве перспективных материалов в отраслях, где актуальной проблемой является снижение веса готовых изделий при условии сохранения необходимых физико-механических характеристик. Одним из эффективных легирующих элементов для сплавов системы Al–Mg является скандий. Небольшая добавка скандия (0.2–0.3 мас. %) способствует повышению прочностных характеристик деформируемых алюминиевых сплавов на 100–150 МПа [1]. Высокая термическая стабильность свойств микрокристаллических сплавов обеспечивается за счет контролируемого распада Sc в Al, приводящего к образованию наночастиц Al3Sc [2–8]. Эти частицы имеют высокую скорость роста, что приводит к увеличению размера зерна при отжиге микрокристаллических сплавов. Следует также отметить дороговизну скандия, что снижает перспективы применения сплавов Al–Sc в промышленности и обусловливает практическую актуальность задачи поиска легирующих элементов, которые могут заменить скандий, обеспечив сохранение высоких механических свойств сплавов.
Перспективной является частичная замена скандия редкоземельными элементами (РЗЭ) или переходными металлами (ПМ) с более низким коэффициентом диффузии в алюминии, чем у скандия, и высокой растворимостью в фазе Al3М (М–РЗЭ, ПМ). Это позволяет повысить термическую стабильность частиц Al3(Sc,M), а в ряде случаев сформировать частицы со структурой “ядро Al3Sc–оболочка Al3M” с малой скоростью роста [9].
Целью работы является изучение возможности частичной замены скандия на цирконий при легировании микрокристаллических сплавов Al–Mg с пониженным содержанием магния и исследование распада твердого раствора в этих сплавах.
ТЕОРЕТИЧЕСКИЙ АНАЛИЗ
Удельное электросопротивление (УЭС) сплава пропорционально содержанию примеси в твердом растворе, что позволяет рассчитать величину УЭС сплава через вклады отдельных легирующих элементов (ЛЭ):
(1)
$\rho = {{\rho }_{0}} + \Delta {{\rho }_{1}}{{С}_{1}} + \Delta {{\rho }_{2}}{{С}_{2}} + ... + \Delta {{\rho }_{n}}{{С}_{n}},$Сопоставление теоретической ρth и экспериментально измеренной ρexp величины УЭС позволяет оценить концентрацию ЛЭ в твердом растворе сплава и объемную долю выделившихся частиц второй фазы f.
Кинетика изменения величины f при распаде твердого раствора может быть описана уравнением Джонсона–Мела–Аврами–Колмогорова [12]:
(2)
$f = {{f}_{{{\text{max}}}}}(1 - {\text{exp(}}{\kern 1pt} - {\kern 1pt} {{({t \mathord{\left/ {\vphantom {t \tau }} \right. \kern-0em} \tau })}^{n}}{\text{)}}),$МЕТОДИКА
Объектами исследования являются сплавы Al–2.5% Mg–Sc–Zr (здесь и далее мас. %). Суммарное содержание скандия и циркония варьируется от 0.10 до 0.22% с интервалом в 0.02%, пропорционально изменяется концентрация циркония в сплаве. Слитки размером 20 × 20 × 160 мм получены методом индукционного литья (литьевая машина INDUTHERM VTC-200). Микрокристаллическая структура сформирована с использованием технологии равноканального углового прессования (РКУП) (гидравлический пресс Ficep HF 400L) при температуре 225°С, число циклов N = 4. Отжиг образцов проводили в воздушной печи СНОЛ. Исследование микроструктуры проводили с использованием интерференционного микроскопа Leica IM DRM и растрового электронного микроскопа JEOL JSM-6490 с энергодисперсионным микроанализатором Oxford Instruments INCA 350. Микротвердость (HV) измеряли твердомером HVS-1000. Измерение УЭС выполняли вихретоковым методом при помощи прибора SIGMATEST 2.069.
ЭКСПЕРИМЕНТАЛЬНЫЕ РЕЗУЛЬТАТЫ
В исходном состоянии литые сплавы Al–2.5% Mg–Sc–Zr имеют однородную крупнозернистую структуру в центральной части слитков и структуру столбчатых кристаллов на краях слитков. В структуре сплавов с суммарным содержанием скандия и циркония >0.30% наблюдаются первичные частицы Al3Sc и Al3Zr. Результаты исследований показывают, что экспериментальные значения УЭС близки к своим теоретически значениям (табл. 1). Это позволяет сделать вывод о том, что большая часть скандия и циркония находится в твердом растворе алюминия.
Таблица 1.
Значения удельного электросопротивления для литых и микрокристаллических сплавов Al–2.5% Mg–Sc–Zr
Содержание скандия и циркония, мас. % | 0.22Sc + + 0.10Zr |
0.20Sc + + 0.12Zr |
0.18Sc + + 0.14Zr |
0.16Sc + + 0.16Zr |
0.14Sc + + 0.18Zr |
0.12Sc + + 0.20Zr |
0.10Sc + + 0.22Zr |
---|---|---|---|---|---|---|---|
Литые сплавы (ρexp, мкОм · см) | 4.50 | 4.59 | 4.37 | 4.62 | 4.55 | 4.54 | 4.50 |
Микрокристаллические сплавы (ρexp, мкОм · см) |
4.49 | 4.46 | 4.58 | 4.50 | 4.56 | 4.57 | 4.48 |
Расчет (ρth, мкОм · см) | 4.62 | 4.62 | 4.61 | 4.61 | 4.60 | 4.60 | 4.59 |
Расчет (ρmin, мкОм · см) | 3.98 |
После РКУП сплавы имеют однородную микрокристаллическую структуру со средним размером зерна ~0.5 мкм. Результаты исследований, представленные в табл. 1 показывают, что величина УЭС микрокристаллических сплавов близка к УЭС литых сплавов. Это позволяет сделать вывод о том, что в процессе РКУП не произошло деформационно-стимулированного распада твердого раствора.
На рис. 1 показаны зависимости микротвердости и УЭС от температуры отжига литых сплавов Al–2.5% Mg–Sc–Zr. Анализ результатов показывает, что температура начала распада твердого раствора составляет ~275°С, а замещение скандия цирконием приводит к увеличению термической устойчивости твердого раствора скандия и циркония в алюминии – снижению интенсивности уменьшения микротвердости и УЭС при повышении температуры отжига. По результатам энергодисперсионного анализа большинство выделившихся частиц содержат одновременно скандий и цирконий. Наибольший эффект упрочнения при отжиге литых сплавов наблюдается для сплавов с повышенным содержанием скандия. Отжиг литых сплавов при повышенных температурах 475–500°С приводит к повышению УЭС, что связано с растворением ранее выпавших частиц Al3Sc.
Рис. 1.
Зависимости микротвердости (а) и УЭС (б) от температуры 30-минутного отжига литых сплавов Al–2.5%Mg–Sc–Zr с различным содержанием скандия и циркония: 1 – Al–2.5% Mg–0.10% Sc–0.22% Zr; 2 – Al–2.5% Mg–0.12% Sc–0.20% Zr; 3 – Al–2.5% Mg–0.14% Sc–0.18% Zr; 4 – Al–2.5% Mg–0.16% Sc–0.16% Zr; 5 – Al–2.5% Mg–0.18% Sc–0.14% Zr; 6 – Al–2.5% Mg–0.20% Sc–0.12% Zr; 7 – Al–2.5% Mg–0.22% Sc–0.10% Zr.
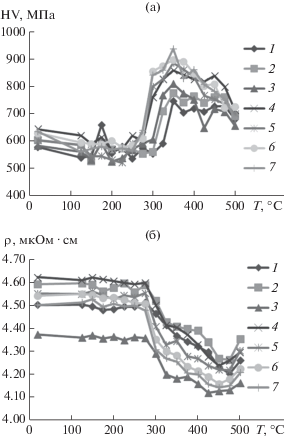
На рис. 2 показаны зависимости микротвердости и УЭС от температуры отжига микрокристаллических сплавов Al–2.5% Mg–Sc–Zr. Исследования микроструктуры отожженных микрокристаллических сплавов показывают, что температура начала рекристаллизации составляет 375–400°С. На рис. 3 представлены фотографии микроструктуры сплавов после отжига при температуре 450°С в течение 30 мин, средний размер зерна во всех сплавах составляет ~1.5–2 мкм. Обнаружено, что зависимости УЭС от температуры отжига для всех микрокристаллических сплавов имеют две стадии: стадия небольшого снижения УЭС при отжиге до температуры 300°С и стадия быстрого снижения УЭС (рис. 2). Температура начала распада пересыщенного твердого раствора составляет ~275–300°С и достаточно слабо зависит от содержания скандия и циркония. Отметим также, что, не смотря на высокую микротвердость микрокристаллических сплавов в состоянии после РКУП, после отжига при температуре 500°С микротвердость микрокристаллических сплавов Al–2.5% Mg–Sc–Zr оказывается ниже, чем микротвердость литых сплавов того же состава после аналогичного отжига. Полученный результат указывает на быстрый рост частиц при отжиге микрокристаллических сплавов, что (в соответствии с уравнением Орована) приводит к снижению вклада частиц в прочность микрокристаллических сплава.
Рис. 2.
Зависимости микротвердости (а) и УЭС (б) от температуры 30-минутного отжига микрокристаллических сплавов Al–2.5% Mg–Sc–Zr (обозначения сплавов – см. рис. 1).
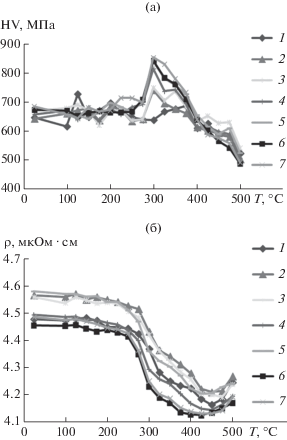
Рис. 3.
Фотографии микроструктуры микрокристаллических сплавов Al–2.5% Mg–Sc–Zr после отжига при 450°С (30 мин) (обозначения сплавов – см. рис. 1).
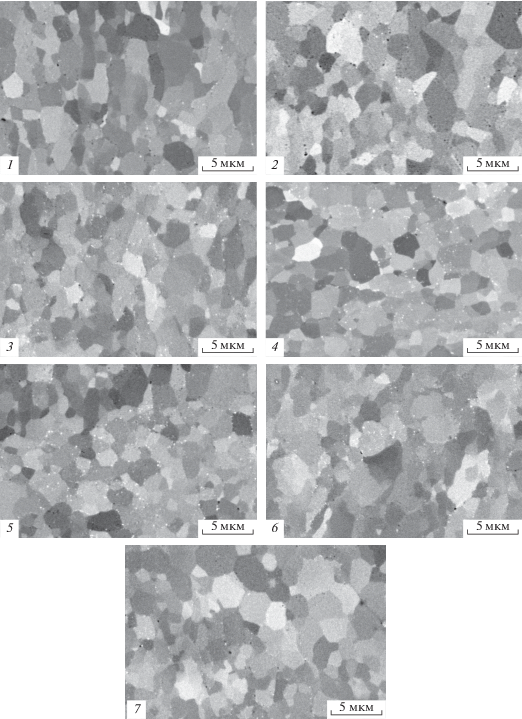
На основании анализа результатов исследования зависимостей УЭС от времени отжига (рис. 4) с использованием уравнений (2), (3) определены значения коэффициента n и, как следствие, механизм выделения частиц второй фазы при отжиге литых и микрокристаллических сплавов.
Рис. 4.
Анализ кинетики распада твердого раствора в микрокристаллическом сплаве Al–2.5% Mg–0.16% Sc–0.16% Zr. Зависимости ∆ρ от времени отжига (а) и зависимости ρ(t) в двойных логарифмических координатах ln ln((ρmax– ρmin)(ρ – ρmin)) – ln t (б).
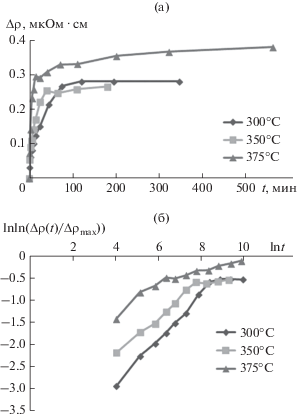
Показано, что в литых сплавах увеличение концентрации скандия от 0.10 до 0.22% приводит к увеличению коэффициента n от 0.9–1.40 до 1.92–2.76, что, по нашему мнению, свидетельствует о преимущественном выделении частиц Al3Sc в объеме кристаллической решетки (n ~ 1.5), а частиц Al3Zr – на границах дендритов и ядрах дислокаций. Отметим, что это достаточно неожиданный результат, поскольку обычно предполагается, что скандий концентрируется на границах зерен алюминиевых сплавов, а цирконий – в объеме кристаллической решетки [11]. В микрокристаллических сплавах выделение частиц происходит по ядрам дислокаций и по границам зерен (n < 1), что может быть обусловлено повышенной плотностью дислокаций в микрокристаллических сплавах, в том числе – повышенной плотностью дислокаций в неравновесных границах зерен микрокристаллических сплавов.
ЗАКЛЮЧЕНИЕ
Исследованы особенности распада пересыщенного твердого раствора в литых и микрокристаллических сплавах Al–2.5% Mg–Sc–Zr с различным содержанием скандия и циркония. Показано, что температура начала распада пересыщенного твердого раствора составляет 275–300°С и слабо зависит от содержания скандия и циркония. Установлено, что в литых сплавах процесс распада имеет двухстадийный характер и происходит за счет выделения частиц Al3Sc в объеме кристаллической решетки, а частиц Al3Zr – по ядрам дислокаций и границам зерен. В микрокристаллических алюминиевых сплавах выделение частиц происходит только по ядрам дислокаций и границам зерен. Наибольший эффект упрочнения при отжиге литых сплавов наблюдается для сплавов с повышенным содержанием скандия. Исследования процессов рекристаллизации показали, что температура начала рекристаллизации в микрокристаллических сплавах составляет 375–400°С. Установлено, что частичное замещение скандия цирконием приводит к монотонному увеличению термической стабильности твердого раствора Sc и Zr в алюминии.
Список литературы
Елагин В.И. // Легирование деформируемых алюминиевых сплавов переходными металлами. М.: Металлургия, 1975. 248 с.
Vinogradov A., Washikita A., Kitagawa K., Kopylov V.I. // Materials Science and Engineering A. 2003. V. 349. P. 318.https://doi.org/10.1016/S0921-5093(02)00813-4
Dobatkin S., Estrin Y., Zakharov V.V., Rostova T., Ukolova O., Chirkova A. // International J. Materials Research. 2009. V. 100. P. 1697.https://doi.org/10.3139/146.110237
Zhemchuzhnikova D., Mironov S., Kaibyshev R. // Metallurgical and Materials Transactions A. 2016. V. 48. P. 150.https://doi.org/10.1007/s11661-016-3843-6
Mikhaylovskaya A.V., Yakovtseva O.A., Cheverikin V.V., Kotov A.D., Portnoy V.K. // Materials Science and Engineering A. 2016. V. 659. P. 225.https://doi.org/10.1016/j.msea.2016.02.061
Estrin Y., Vinogradov A. // International J. Fatigue. 2010. V. 32. P. 898.https://doi.org/10.1016/j.ijfatigue.2009.06.022
Dobatkin S.V., Zakharov V.V., Vinogradov A.Yu., Kitagawa K., Krasil’nikov N.A., Rostova T.D., Bastarash E.N. // Russian Meallurgy (Metally). 2006. V. 6. P. 533.https://doi.org/10.1134/S0036029506060115
Nokhrin A., Shadrina I., Chuvil’deev V., Kopylov V. // Materials. 2019. V. 12. № 316.https://doi.org/10.3390/ma12020316
Booth-Morrison Ch., Dunand D.C., Seidman D.N. // Acta Materialia. 2011. V. 59. P. 7029.https://doi.org/10.1016/j.actamat.2011.07.057
Чувильдеев В.Н., Нохрин А.В., Смирнова Е.С., Копылов В.И. // Металлы. 2012. № 6. С. 82.
Хэтч Дж.Е. // Алюминий. Свойства и физическое металловедение. М.: Металургия, 1989. С. 422.
Чувильдеев В.Н., Смирнова Е.С., Копылов В.И. // Металлы. 2012. № 4. С. 70.
Дополнительные материалы отсутствуют.
Инструменты
Поверхность. Рентгеновские, синхротронные и нейтронные исследования