Поверхность. Рентгеновские, синхротронные и нейтронные исследования, 2022, № 1, стр. 18-23
Самораспространяющийся высокотемпературный синтез MAX-фазы Ti3SiC2 с использованием различных форм углерода
Н. С. Ларионова a, *, Р. М. Никонова a, В. И. Ладьянов a
a Научный центр металлургической физики и материаловедения (НЦ МФМ)
Удмуртского федерального исследовательского центра Уральского отделения РАН
426067 Ижевск, Россия
* E-mail: larionova_n@udman.ru
Поступила в редакцию 22.05.2021
После доработки 25.06.2021
Принята к публикации 30.06.2021
- EDN: NILKOL
- DOI: 10.31857/S1028096021120104
Аннотация
Методом самораспространяющегося высокотемпературного синтеза получены композиционные материалы 3Ti–Si–2C с использованием различных структурных форм углерода (сажа, углеродные нанотрубки, фуллерит). Фазовый состав образцов исследован методом рентгеноструктурного анализа. Показано, что количество MAX-фазы Ti3SiC2 (фазы Mn + 1AXn, где n = 1, 2, 3, …; M – переходный d-металл; A – p-элемент; X – углерод) в полученных материалах зависит от формы углерода. При использовании сажи обнаружено также формирование карбида TiC, а при использовании углеродных нанотрубок и фуллерита – TiC и Ti5Si3Cx. Во всех образцах присутствуют следы фазы TiSi2. Методом растровой электронной микроскопии показано, что структура образцов с фуллеритом и нанотрубками неоднородна и содержит области, состоящие одновременно из нескольких фаз.
ВВЕДЕНИЕ
Силикокарбид титана Ti3SiC2 – типичный представитель семейства тройных слоистых карбидов со стехиометрией Mn + 1AXn (где n = 1, 2, 3, …; M – переходный d-металл; A – p-элемент; X – углерод), так называемых MAX-фаз, характеризующихся уникальным сочетанием свойств металла и керамики [1–4]. Ti3SiC2 обладает малым электросопротивлением (23 мкОм · см), температурой плавления ~2300°С и высокой окислительной стойкостью при 900°С, небольшим коэффициентом трения (менее 0.15 при трении по стали и нитриду кремния), хорошей радиационной стойкостью. При одинаковой с титаном плотности (~4.52 г/см3) Ti3SiC2 характеризуется значительной жесткостью и твердостью благодаря бóльшему модулю Юнга (325–345 ГПа). В сравнении с карбидом TiC силикокарбид титана – аномально мягкий материал, обладающий большей трещиностойкостью (5–16 МПа · м1/2). Благодаря такой комбинации свойств MAX-фаза Ti3SiC2 привлекает внимание исследователей как перспективный материал высокотемпературной керамики, защитных покрытий, датчиков, электрических контактов и других приложений.
Получить Ti3SiC2 в чистом виде сложно. Метод порошковой металлургии (изначально основной) требует большого числа технологических операций. Вторая фаза (в большинстве случаев TiC, могут быть также TiSi2, SiC, Ti5Si3, Ti5Si3Cx), образующаяся в процессе синтеза, оказывает существенное влияние на свойства MAX-фазы. Поэтому до сих пор актуальным является развитие методов ее синтеза [5–12]. В литературе показана возможность получения Ti3SiC2 чистотой от 92 до 98 мас. % методами горячего прессования in situ [1, 5, 11], механосинтеза с последующим отжигом [6], искрового плазменного спекания [9], магнетронного распыления [10], спекания в импульсном разряде [12]. В качестве исходной реакционной смеси используются как чистые порошки Ti/Si/C [5, 6, 10], так и смеси с карбидами Ti/C/SiC и Ti/Si/TiC [7–9, 11, 12]. Рассматривается эффективность избыточного добавления кремния (по отношению к стехиометрии MAX-фазы) для компенсации его потерь при испарении во время синтеза [5, 7, 12].
Использование метода самораспространяющегося высокотемпературного синтеза (СВС) для получения Ti3SiC2 является экономической альтернативой более успешным, но дорогостоящим методам реактивного спекания и горячего изостатического прессования [13–17]. Для СВС характерно самоподдерживающееся протекание химической реакции, которое происходит без участия внешних источников тепла [18]. Максимальная температура горения при синтезе Ti3SiC2 данным методом может достигать 2373 ± 25 К [15]. В зависимости от условий эксперимента, реакционной смеси и дисперсности порошков разными авторами показана возможность получения методом СВС Ti3SiC2 чистотой до 90 мас. % [13–17].
Одним из важных параметров СВС, оказывающих влияние на фазовый состав образцов, является используемый источник углерода, а именно его структура и термические свойства. Известно, что при избытке углерода в продуктах синтеза увеличивается количество TiC, а при недостатке помимо карбида формируется Ti5Si3 [17]. Авторами [14] показано, что при использовании сажи и графита в результате СВС-реакции формируется, соответственно, 71.5 и 82.5 об. % Ti3SiC2, добавление карбида SiC в обоих случаях приводит к выходу ~85 об. % Ti3SiC2. На основе анализа литературных данных в [17] отмечается, что использование мелкодисперсного графита и высокоактивного углерода повышает выход Ti3SiC2. Влияние источника углерода на формирование MAX-фазы при СВС отмечается также для других составов наноламинатов [19]. Имеются данные [5] о влиянии активированного угля и графита на синтез Ti3SiC2 методом горячего прессования, где чистота MAX-фазы составляет 98 и 87 мас. % соответственно.
Известно, что использование различных наноструктурных форм углерода (фуллеренов, графена, углеродных нанотрубок и наноалмазов) вместо традиционных графита и сажи позволяет существенно улучшить свойства различных металломатричных материалов [20–23], которые определяются их структурой. Исследования влияния, например, фуллеренов и углеродных нанотрубок на формирование MAX-фазы Ti3SiC2 при СВС в сравнении с сажей или графитом не проводились.
Целью настоящей работы было сравнительное исследование влияния различных структурных форм углерода на формирование силикокарбида титана Ti3SiC2 методом СВС. В качестве источника углерода брали углеродные нанотрубки и фуллерит, представляющий собой молекулярный кристалл. Исследования проводили в сравнении с сажей, которая традиционно используется при получении MAX-фаз. Знание реальной структуры продуктов горения необходимо для понимания механизмов СВС, что в свою очередь важно для более эффективного применения данного метода при получении MAX-фаз [16, 17].
МЕТОДИКА ЭКСПЕРИМЕНТА
Для приготовления исходных шихтовых заготовок использовали смесь порошков титана марки ПТМ-1 (99%, 5–15 мкм), кремния марки Кр-00 (99%, фракция 76–160 мкм) и углерода, в качестве которого выбрали сажу (П803), многослойные углеродные нанотрубки (производитель УНМ “Таунит”, ТГТУ, г. Тамбов) и смесь фуллерита С60/70. Смесь С60/70 была получена в НЦ МФМ УдмФИЦ УрО РАН методом электродугового испарения графитовых стержней с последующей экстракцией фуллеренов из фуллеренсодержащей сажи кипящим толуолом в приборе “Сокслет” и дальнейшей кристаллизацией фуллерита из раствора в ротационном испарителе. По данным высокоэффективной жидкостной хроматографии состав исходной смеси С60/70: 82.18 мас. % С60, 14.08 мас. % С70, 2.81 мас. % оксидов С60О, С60О2 и С70О; 0.93 мас. % высших фуллеренов С76, С78, С82, С84. Согласно термогравиметрическому анализу содержание остаточного толуола в образце составляет 1.1 мас. % (находится в образце в виде кристаллосольвата С60–С70–С6Н5СН3).
Исходные порошки Ti, Si и С предварительно сушили при температуре 140–150°С в течение 2 ч. Шихтовые заготовки подготавливали из расчета стехиометрического состава металлокерамики Ti3SiC2. Механическое перемешивание исходных компонентов осуществляли в бочкообразном смесителе со скоростью вращения 19 об./мин в течение 2 ч. Далее смесь засыпали в тигель диаметром 48 мм и высотой 49 мм. Процесс СВС проводили в реакторе РВС-10 объемом 10 л, изготовленном в НЦ МФМ УдмФИЦ УрО РАН, в атмосфере аргона при РAr = 70–110 атм. Волну послойного горения реакционной смеси инициировали раскаленной вольфрамовой спиралью.
Рентгеновские дифрактограммы получены на дифрактометре ДРОН-6 (CuKα-излучение). Исследования фазового состава порошков проведены с помощью пакета программ MISA. Морфология образцов изучена с помощью растрового электронного микроскопа (РЭМ) Termo Fisher Scientific Quattro S, оснащенного системой энергодисперсионного микроанализа на основе спектрометра EDAX Octane Elect Plus EDS System.
РЕЗУЛЬТАТЫ И ИХ ОБСУЖДЕНИЕ
Изображения исходных порошков сажи, углеродных нанотрубок (УНТ) и фуллерита C60/70 приведены на рис. 1. Используемые углеродные материалы отличаются морфологией и дисперсностью частиц. Размер сферических частиц сажи составлял ~100–200 нм (рис. 1а). Нанотрубки характерной нитевидной формы диаметром ~30–70 нм представляли собой агломераты размером ~50–250 мкм (рис. 1б). Частицы фуллерита – плоские, размером ~60–200 мкм, рыхлые внутри, состоящие из более мелких частиц около 1–4 мкм (рис. 1в).
Рис. 1.
РЭМ-изображения исходных углеродных материалов: а – сажа; б – многослойные УНТ; в – фуллерит С60/70.
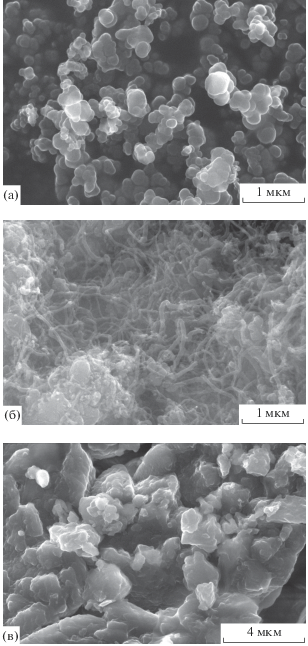
В результате СВС-реакции смесей 3Ti–Si–2C получены материалы, отличающиеся фазовым составом в зависимости от используемой формы углерода (рис. 2). На дифрактограмме образца с сажей наблюдаются интенсивные рефлексы MAX-фазы Ti3SiC2, рефлексы карбида TiC небольшой интенсивности и следы фазы TiSi2. В материалах, синтезированных с использованием УНТ и фуллерита, помимо указанных фаз также присутствует фаза Ti5Si3Cx, промежуточная при формировании MAX-фазы Ti3SiC2. В табл. 1 приведены количественные данные образующихся фаз. Согласно полученным результатам в образце с УНТ преобладает карбид TiC (40 мас. %), а в образце с фуллеритом С60/70 – Ti5Si3Cx (46 мас. %).
Рис. 2.
Дифрактограммы образцов, полученных методом СВС с использованием: 1 – сажи; 2 – углеродных нанотрубок; 3 – фуллерита С60/70.
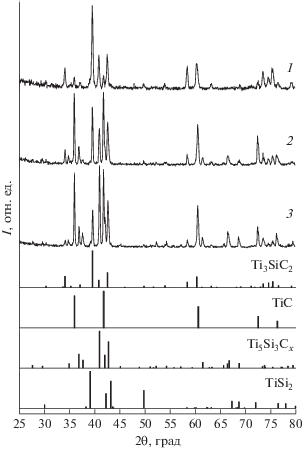
Таблица 1.
Количественное содержание фаз в материалах, полученных методом СВС с использованием различных форм углерода
Форма углерода | Ti3SiC2, мас. % | TiC, мас. % | Ti5Si3Cx, мас. % |
---|---|---|---|
Сажа | 90 | 10 | – |
УНТ | 32 | 40 | 28 |
Фуллерит | 20 | 34 | 46 |
На рис. 3 представлены изображения микроструктуры сколов полученных материалов. В образце с сажей (рис. 3а) выявлено несколько структурных составляющих. Методом микрорентгеноспектрального анализа по стехиометрическому соотношению элементов определен их фазовый состав – TiC, Ti3SiC2, TiSi2. Карбосилицид Ti3SiC2 имеет характерную для MAX-фаз слоистую структуру и представлен в двух формах – в виде пластин толщиной 0.5–1 мкм и тороидальных частиц диаметром 5–10 мкм. Карбид TiC сформирован в виде округлых зерен. Силицид TiSi2 – кристаллы, имеющие прямоугольную огранку.
Рис. 3.
Микроструктура сколов образцов (в разном масштабе), полученных методом СВС с использованием: а – сажи; б – углеродных нанотрубок; в – фуллерита С60/70.
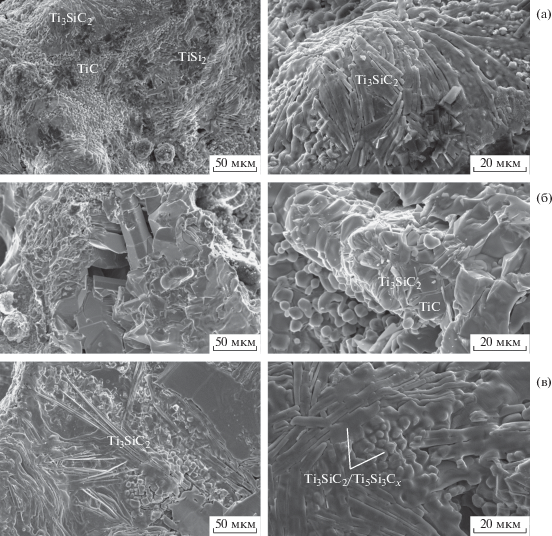
Микроструктура материалов, полученных с использованием УНТ и фуллерита, отличается более неоднородным строением (рис. 3б, 3в). В первом случае на поверхности скола выявлены округлые зерна карбида TiC со встроенными между ними пластинами Ti3SiC2 (рис. 3б). Кроме того, можно видеть крупные частицы с выраженными гранями, которые согласно энергодисперсионному анализу не являются монофазными. Во втором случае обнаружены плотные скопления и частицы округлой формы, имеющие слоистую структуру (рис. 3в). Согласно микрорентгеноспектральному анализу, указанные участки могут соответствовать как МАХ-фазе Ti3SiC2, так и промежуточной фазе Ti5Si3Cx. В отличие от образца, при получении которого использовалась сажа, указанные участки имеют сильно сглаженный, “оплавленный” вид. Наличие различных по форме зерен со слоистой структурой может быть объяснено многоступенчатым характером процесса их образования и роста. Кроме того, присутствуют локальные участки, сформированные частицами, имеющими ровные грани, соответствующие карбиду SiC (здесь не представлены). Отметим, что на рентгеновских дифрактограммах рефлексы карбида SiC не обнаружены (рис. 2). Следовательно, в образце он присутствует в незначительном количестве. Важно отметить, что в образцах, полученных с использованием УНТ и С60/70, имеются участки непрореагировавшего углерода. Таким образом, форма углерода влияет на качественный и количественный фазовый состав, а также микроструктуру синтезируемых методом СВС материалов. Установление механизмов их формирования является предметом дальнейших исследований.
ЗАКЛЮЧЕНИЕ
Методом самораспространяющегося высокотемпературного синтеза получены композиционные материалы 3Ti–Si–2C с использованием в качестве углерода сажи, УНТ и фуллерита С60/70. Показано, что в результате СВС-реакции в сравниваемых образцах формируется МАХ-фаза Ti3SiC2, количество которой зависит от формы углерода. Продуктом синтеза в случае с сажей также является карбид TiC, а в случае УНТ и фуллерита – карбид TiC и фаза Ti5Si3Cx. Кроме того, во всех образцах обнаружены следы силицида титана TiSi2. Методом РЭМ выявлены различия в структуре полученных материалов. Показано, что структура образцов с фуллеритом и нанотрубками неоднородна и содержит области, состоящие одновременно из нескольких фаз.
Список литературы
Barsoum M.W. // Prog. Solid St. Chem. 2000. V. 28. P. 201.
Андриевский Р.А. // Успехи физических наук. 2017. Т. 187. № 3. С. 296. https://doi.org/10.3367/UFNr.2016.09.037972
Rahman A., Rahaman Z. // Am. J. Modern Phys. 2015. V. 4. № 2. P. 75. https://doi.org/10.11648/j.ajmp.20150402.15
Sun Z.M. // Int. Mater. Rev. 2011. V. 56. № 3. P. 143. https://doi.org/10.1179/1743280410Y.0000000001
Yong-Ming L., Wei P., Shuqin L., Jian Ch. // Ceram. Int. 2002. V. 28. P. 227.
Li J.-F., Matsuki T., Watanabe R. // J. Am. Ceram. Soc. 2002. V. 85. № 4. P. 1004. https://doi.org/10.1111/j.1151-2916.2002.tb00210.x
Atazadeh N., Heydari M.S., Baharvandi H.R., Ehsani N. // Int. J. Refr. Met. Hard Mater. 2016. V. 61. P. 67. https://doi.org/10.1016/j.ijrmhm.2016.08.003
Istomin P.V., Istomina E.I., Nadutkin V., Grass V.É. // Refr. Ind. Ceram. 2019. V. 60. № 3. P. 264. https://doi.org/10.1007/s11148-019-00349-3
Gao N.F., Li J.T., Zhang D., Miyamoto Y. // J. Eur. Ceram. Soc. 2002. V. 22. P. 2365. https://doi.org/10.1016/S0955-2219(02)00021-3
Emmerlich J., Music D., Eklund P., Wilhelmsson O., Jansson U., Schneider J.M., Hogberg H., Hultman L. // Acta Mater. 2007. V. 55. P. 1479. https://doi.org/10.1016/j.actamat.2006.10.010
Gao N.F., Miyamoto Y., Zhang D. // Mater. Lett. 2002. V. 55. P. 61. https://doi.org/10.1016/S0167-577X(01)00620-6
Zhang Z.F., Sun Z.M., Hashimoto H., Abe T. // J. Alloys Compds. 2003. V. 352. P. 283. https://doi.org/10.1016/S0925-8388(02)01171-4
El Saeed M.A., Deorsola F.A., Rashad R.M. // Int. J. Refr. Met. Hard Mater. 2012. V. 35. P. 127. https://doi.org/10.1016/j.ijrmhm.2012.05.001
Yeh C.L., Shen Y.G. // J. Alloys Compds. 2008. V. 461. P. 654. https://doi.org/10.1016/j.jallcom.2007.07.088
Afanasyev N.I., Lepakova O.K., Kitler V.D. // J. Phys.: Conf. Ser. 2020. V. 1459. P. 012008. https://doi.org/10.1088/1742-6596/1459/1/012008
Vadchenko S.G., Sytschev A.E., Kovalev D.Yu., Shchukin A.S., Konovalikhin S.V. // Nanotechnologies in Russia. 2015. V. 10. № 1–2. P. 67. https://doi.org/10.1134/S1995078015010206
Meng F., Liang B., Wang M. // Int. J. Refr. Met. Hard Mater. 2013. V. 41. P. 152. https://doi.org/10.1016/j.ijrmhm.2013.03.005
Рогачев А.С., Мукасьян А.С. Горение для синтеза материалов: введение в структурную макрокинетику. М.: ФИЗМАТЛИТ, 2013. 400 с.
Thomas T., Bowen C.R. // Ceram. Int. 2016. V. 42. P. 4150. https://doi.org/10.1016/j.ceramint.2015.11.088
Robles Hernandez F.C., Calderon H.A. // Mater. Chem. Phys. 2012. V. 132. P. 815.
Medvedev V.V., Popov M.Y., Mavrin B.N. et al. // Appl. Phys. A. 2011. V. 105. P. 45. https://doi.org/10.1007/s00339-011-6544-4
Ahmad S.I., Hamoudi H., Abdala A., Ghouri Z.K., Youssef Kh.M. // Rev. Adv. Mater. Sci. 2020. V. 59. P. 67. https://doi.org/10.1515/rams-2020-0007
Lukina I.N., Chernogorova O.P., Drozdova E.I., Stupnikov V.A., Soldatov A.V. // IOP Conf. Ser.: Mater. Sci. Eng. 2019. V. 525. P. 012034. https://doi.org/10.1088/1757-899X/525/1/012034
Дополнительные материалы отсутствуют.
Инструменты
Поверхность. Рентгеновские, синхротронные и нейтронные исследования