Поверхность. Рентгеновские, синхротронные и нейтронные исследования, 2022, № 12, стр. 70-79
Модифицирование микроструктуры ПТФЭ в сверхкритической среде
С. А. Хатипов a, *, Н. В. Садовская a, b, **, А. С. Авилов b, Р. С. Хатипов a, В. М. Бузник c
a ООО “НПП “Арфлон”
109456 Москва, Россия
b ФНИЦ “Кристаллография и фотоника” РАН
119333 Москва, Россия
c Институт общей и неорганической химии им. Н.С. Курнакова РАН
119991 Москва, Россия
* E-mail: info@npp-arflon.ru
** E-mail: nataly_sadovska@mail.ru
Поступила в редакцию 10.06.2022
После доработки 14.07.2022
Принята к публикации 14.07.2022
- EDN: ELYRBU
- DOI: 10.31857/S1028096022120159
Аннотация
Проведено исследование влияния обработки ПТФЭ в ск-СО2 и ск-ПФО выше температуры плавления кристаллической фазы на микроструктуру и характеристики фазовых переходов с использованием растровой электронной микроскопии высокого разрешения и ДСК. Показано, что в зависимости от условий кристаллизации после выдержки ПТФЭ в ск-среде возможно формирование нетипичной для этого полимера микроструктуры с радиальной ориентацией фибрилл. Обработка ПТФЭ в ск-среде ведет также к необратимому увеличению теплоты плавления и кристаллизации и, соответственно степени кристалличности в 1.5–2 раза, по сравнению с исходными значениями. Рост кристалличности объясняется изменением микроструктуры расплава ПТФЭ в ск-среде: высвобождением части сегментов макромолекул из физических узлов в процессе набухания и пластификации полимерной матрицы. Распутывание узлов, ограничивающих молекулярную подвижность, способствует увеличению количества звеньев макромолекул, участвующих в формировании кристаллических доменов, и необратимому увеличению степени кристалличности.
ВВЕДЕНИЕ
Политетрафторэтилен (ПТФЭ) широко применяется в промышленности благодаря уникальным физико-химическим свойствам [1–3]. Ограничения по применению возникают в связи с его высокой ползучестью и низкой износостойкостью [3, 4]. Указанные недостатки связаны с особенностями микроструктуры ПТФЭ. В отличие от термопластичных полимеров (например, полиэтилена), кристаллизующихся из расплава с образованием ламеллярных сферолитов, в ПТФЭ приблизительно на том же масштабе (1–10 мкм), формируются крупные ламели, обладающие низкой прочностью к сдвигу [5]. Легкость сдвиговой деформации ламелей, сопровождаемой ориентацией фибрилл (и макромолекул) вдоль направления действующей силы, является причиной хладотекучести (сверхпластичности) ПТФЭ. Введение в полимер наполнителей позволяет частично блокировать этот процесс и увеличить модуль упругости, снизить ползучесть и скорость изнашивания при трении [4, 6, 7]. Однако, очевидно, что наиболее эффективное влияние на деформационные свойства могло бы оказать изменение самой микроструктуры. Возможность подобного изменения микроструктуры ПТФЭ была подтверждена с использованием радиационного модифицирования выше температуры плавления кристаллитов [8–10]. Кристаллизация облученного расплава приводила к образованию центрально-симметричных структур на масштабе 10–50 мкм и радиальной ориентацией макромолекул в отличие от плоскопараллельной упаковки в ламелях в исходном ПТФЭ. Снижение скоростей изнашивания и ползучести ПТФЭ при таком структурном переходе достигало 3–4 порядков величины [11, 12]. Было сделано предположение о том, что ключевую роль в наблюдаемом структурном переходе играет снижение вязкости расплава в процессе воздействия ионизирующего излучения [8].
Влияние вязкости расплава полимера на структурообразование в процессе кристаллизации хорошо известно [13]. Так, при высоком давлении (4800 атм.) и, соответственно, повышенной вязкости в полиэтилене (ПЭ) формируются крупные ламели с вытянутыми полимерными цепями толщиной 1–2 мкм в отличие от сферолитов, образующихся в обычных условиях [13, 14]. ПТФЭ в исходном состоянии обладает высокой вязкостью расплава, на 9–10 порядков выше типичных значений для термопластов, что, по-видимому, так же как в ПЭ при высоком давлении, способствует образованию крупных ламелей. Поэтому для ПТФЭ представляет интерес исследование характера структурообразования в условиях пониженной вязкости расплава. В литературе такие данные отсутствуют, а их получение затруднено нерастворимостью ПТФЭ и отсутствием набухания в обычных растворителях. Ограниченную растворимость и набухание этого полимера наблюдали в высококипящих перфторрастворителях и сверхкритических средах [15–19]. Выше температуры плавления в ск-среде наблюдали гелеобразное состояние ПТФЭ [16], в котором вязкость расплава снижена значительно.
В настоящей работе проведено исследование влияния обработки ПТФЭ в сверхкритических средах углекислого газа и перфтороктана выше температуры плавления кристаллической фазы на микроструктуру, формирующуюся в процессе последующей кристаллизации, и характеристики фазовых переходов.
ЭКСПЕРИМЕНТАЛЬНАЯ ЧАСТЬ
Исследовали частицы порошка полимеризата ПТФЭ суспензионной полимеризации марки ПН (ГОСТ 10 007-80) производства Кирово-Чепецкого химического комбината, а также блочные образцы, полученные из этого порошка одноосным прессованием при давлении 30 МПа с последующим спеканием при температуре 380°С.
Образцы помещали в титановые чашечки, которые устанавливали в сосуде высокого давления объемом 500 см3. Для сброса давления сосуды были снабжены отводами с игольчатыми кранами. В качестве ск-среды использовали двуокись углерода и перфтороктан. Критическая температура и давление для ск-СО2 и полифениленоксида (ПФО) составляют соответственно 30.98°С, 7.38 МПа и 229.1°С, 1.66 МПа. Количество растворителя для каждого опыта определяли с учетом заданных значений температуры, давления и весовой доли растворителя. Давление в экспериментальном объеме при заданной температуре определяли построением изохор с использованием базы данных NIST [20].
Нагрев сосуда с образцами в растворителе осуществляли в программируемом режиме со скоростью 1°С/мин до достижения заданных температуры 365°С и давления. Затем образцы выдерживали в этих условиях в течение 12, 24, 48 и 60 ч и проводили их охлаждение и неизотермическую кристаллизацию со скоростью 1°С/мин непосредственно в ск-среде, либо при атмосферном давлении после удаления растворителя открытием игольчатого крана.
Термограммы плавления/кристаллизации получали методом дифференциальной сканирующей калориметрии (ДСК) на приборе DSC 204 F1 Phoenix фирмы NETZSCH при скорости сканирования 5°С/мин. Масса образца при измерении термограмм составляла 10 мг. Образец запрессовывали в капсулу, которую помещали в измерительную камеру. В течение всего времени сканирования капсула с образцом находилась в атмосфере гелия. Степень кристалличности определяли с использованием теплоты плавления, равной 82 Дж/г для ПТФЭ при 100% кристалличности [21].
Плотность образцов определяли методом гидростатического взвешивания. Для измерения массы образцов на воздухе и в дистиллированной воде использовали весы HJR-620CE фирмы Vibra (Япония) с дискретностью показаний 1.0 мг.
Плотность рассчитывали по формуле:
Микроструктуру образцов исследовали методом растровой электронной микроскопии (РЭМ). Использовали сканирующий электронный микроскоп высокого разрешения с автоэмиссионным катодом JSM-7500F фирмы JEOL. Изображения получали в режиме низкоэнергетических вторичных электронов при ускоряющем напряжении 5 кВ и токе зонда 10–12 А. Исследовали полученные в жидком азоте сколы при разрешении не хуже 5 нм.
РЕЗУЛЬТАТЫ И ИХ ОБСУЖДЕНИЕ
Особенностью ПТФЭ является существенное отличие температур и энтальпий первого и второго плавления частиц порошка полимеризата. Температура первого плавления составляет 344°С и снижается до 327°С при втором плавлении, энтальпия при втором плавлении снижается в 3–4 раза (табл. 1). Столь значительные различия характеристик фазовых переходов связаны с изменением микроструктуры. Частицы полимеризата обладают фибриллярной структурой, являющейся результатом холодной кристаллизации в процессе полимеризации вблизи 70°С в водной среде (рис. 1), с высокой степенью кристалличности и преимущественно выпрямленной конфигурацией полимерных цепей. Тогда как после первого плавления в процессе последующей кристаллизации формируется ламеллярная структура с более низкой степенью кристалличности и складчатой конформацией макромолекул (рис. 2).
Таблица 1.
Влияние условий обработки частиц полимеризата ПТФЭ в ск-среде на степень кристалличности χ, температуру Тm и теплоту ∆Hm плавления
Условия обработки | Тm, °С | ∆Hm, Дж/г | χ, % | η |
---|---|---|---|---|
До обработки | – | – | – | – |
Первое плавление порошка полимеризата | 343 | 79 | 96 | – |
Второе плавление порошка полимеризата | 328 | 25 | 30 | |
После обработки в ск-среде | ||||
365°С/12 МПа, ск-СО2/48 ч/охлаждение и кристаллизация при атм. давлении | 330 | 47 | 57 | 0.50 |
365°С/60 МПа, ск-СО2/24 ч/охлаждение и кристаллизация в ск-СО2 | 330 | 46 | 56 | 0.90 |
365°С/8 МПа, ск-ПФО/48 ч/охлаждение и кристаллизация в ск-ПФО | 330 | 56 | 68 | 0.70 |
Рис. 1.
Фибриллярная структура частиц порошка полимеризата ПТФЭ с выпрямленными полимерными цепями до обработки в ск-среде: пористая (а) и плотная (б) области.
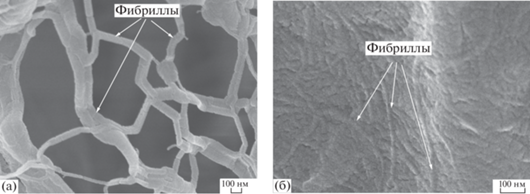
Рис. 2.
Ламеллярная структура блочного спеченного ПТФЭ со складчатыми полимерными цепями до обработки в ск-среде.
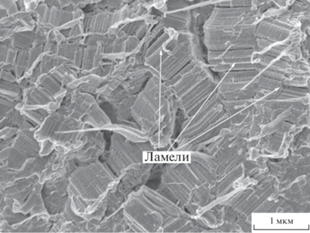
С учетом теоретических фазовых диаграмм ПТФЭ в ск-среде [15, 16] в каждом из задаваемых в настоящей работе сочетаний экспериментальных условий (давление, весовая доля растворителя, среда) температура обработки 365°С была выше температуры плавления кристаллической фазы исследуемых образцов. Соответствующая точка на фазовой диаграмме находилась выше линии ликвидуса. В этой области возможно существование двух равновесных состояний: однофазной жидкости при полном растворении образца и равновесия жидкость–жидкость (L–L). В связи с высокой кинетической заторможенностью процесса растворения ПТФЭ [16] реализация термодинамически равновесного состояния однофазной жидкости оказывается труднодостижимой. Поэтому для двухкомпонентных систем ПТФЭ/ ск-среда, исследованных в настоящей работе, наблюдалось L–L-равновесие в области существования равновесной однофазной жидкости вплоть до 60 ч выдержки раствора.
Как видно на рис. 3, обработка частиц порошка полимеризата ПТФЭ в ск-СО2 при 12 МПа и η = 0.5 приводит к образованию ламеллярной структуры типичной для исходного спеченного ПТФЭ (рис. 2). Охлаждение и кристаллизацию образца проводили при атмосферном давлении. Растворитель удаляли открытием игольчатого крана экспериментальной ячейки на воздух, что приводило к быстрому переходу растворителя из сверхкритического в газообразное состояние. Формирование ламеллярной структуры подтверждает то, что температура обработки превышала температуру плавления фибриллярных кристаллитов полимеризата ПТФЭ. Аналогичное изменение структуры происходит после первого плавления и кристаллизации порошка полимеризата ПТФЭ при атмосферном давлении на воздухе. Отсутствие осадка в виде диспергированных частиц после охлаждения раствора свидетельствует о реализации L–L-равновесия в течение всего времени обработки (48 ч).
Рис. 3.
Ламеллярная структура со складчатыми полимерными цепями после обработки порошка полимеризата ПТФЭ в ск-СО2. Условия обработки: 365°С, 12 МПа, 48 ч, η = 0.5, охлаждение и кристаллизация при атмосферном давлении.
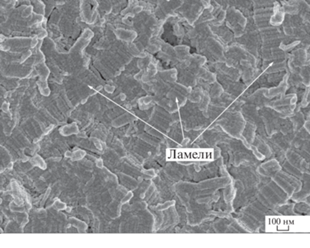
На рис. 4 представлены РЭМ-изображения частиц порошка полимеризата, обработанных в ск-СО2 при давлении 60 МПа и η = 0.9 с последующим охлаждением и кристаллизацией в ск-среде. Кристаллизация в ск-среде приводит к образованию двух типов областей с плотной ламеллярной (рис. 4а) и ячеистой (сотовой) микроструктурой (рис. 4б). Температура кристаллизации ПТФЭ и давление в ячейке в процессе кристаллизации заведомо превышают соответствующие значения в критической точке СО2. Поэтому процесс кристаллизации в ск-СО2 соответствует переходу от L–L- к L–S-равновесию, при котором СО2 остается в сверхкритическом жидком состоянии, а ПТФЭ переходит из жидкоподобного (гелеобразного) состояния в твердое. При этом в областях, подверженных наибольшей степени набухания, формируются тонкие полимерные “стенки” твердой фазы, разделенные жидкой фазой растворителя (рис. 4б). При выходе растворителя из объема образца, что происходит при снижении температуры и давления в ячейке ниже критических значений и переходе растворителя в газообразное состояние, в полимерной матрице остаются пустоты. В областях, обедненных растворителем, образуются непористые ламеллярные структуры (рис. 4а). Отсутствие мелкодисперсного осадка, как и в предыдущем случае, подтверждает существование в процессе всего времени обработки L–L-равновесия.
Рис. 4.
Микроструктура плотной (а) и пористой (б) областей полимеризата ПТФЭ после обработки в ск-СО2. Условия обработки: 365°С, 60 МПа, 24 ч, η = 0.9, охлаждение и кристаллизация в ск-СО2.
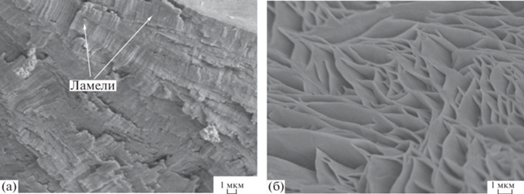
Обработка частиц полимеризата ПТФЭ в ск-ПФО (8 МПа, η = 0.7) с последующим охлаждением и кристаллизацией в ск-среде приводит к образованию более однородной и в среднем более плотной структуры, по сравнению с ск-СО2. Микроструктура характеризуется образованием двух типов структур: центрально-симметричной с радиальной ориентацией фибрилл и ламеллярной с плоскопараллельной упаковкой макромолекул (рис. 5а). Размер пор на 2–3 порядка меньше, чем в ск-СО2, и составляет 10–100 нм (рис. 4б, 5б). В процессе кристаллизации расплава полимеризата ПТФЭ в ск-ПФО, в отличие от ск-СО2, образуется не типичная микроструктура, включающая области с радиальной ориентацией фибрилл. Наблюдаемое отличие связано, по-видимому, с более эффективной пластификацией расплава ПТФЭ в ск-ПФО, по сравнению с ск-СО2, ввиду лучшей растворимости во фторированном растворителе.
Рис. 5.
Микроструктура полимеризата ПТФЭ после обработки в ск-ПФО. Условия обработки: 365°С, 8 МПа, 48 ч, η = 0.7, охлаждение и кристаллизация в ск-ПФО: а – ×35 000, б – ×75 000.
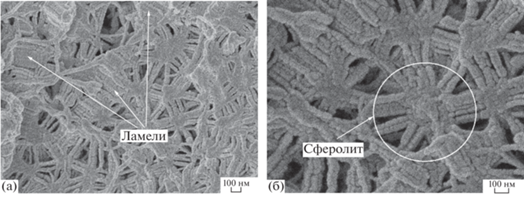
Как показано на рис. 1, частицы полимеризата ПТФЭ в исходном состоянии обладают фибриллярной структурой и очень высокой пористостью (около 30% [22]). Растворитель проникает в частицы полимеризата практически беспрепятственно. Несмотря на это, перехода из L–L-равновесия в однофазную жидкость ни в ск-СО2, ни в ск-ПФО не наблюдается в течение заданных 48 ч обработки. Можно предположить, что столь значительная кинетическая заторможенность процесса растворения объясняется сохранением достаточно плотной фибриллярной упаковки макромолекул, ограничивающей их контакт с молекулами растворителя, выше линии ликвидуса. Если это так, то возникновение центрально-симметричных фибриллярных микроструктур связано с реориентацией фибрилл, сохраняющихся в расплаве, в процессе кристаллизации благодаря пониженной вязкости в ск-среде. В обычных условиях при высокой вязкости на уровне 1011 Пуаз, свойственной расплаву ПТФЭ, такая реориентация оказывается невозможной и фибриллы кристаллизуются исключительно с образованием ламелей с плоскопараллельной ориентацией макромолекул. Аналогичный вывод сделан в работах [8, 9] для интерпретации формирования центрально-симметричных микроструктур в процессе кристаллизации облученного расплава ПТФЭ.
Кристаллическая структура полимеризата ПТФЭ формируется в процессе полимеризации при температуре около 70°С, т.е. вдали от температуры кристаллизации (317°С) и, соответственно вытянутая конфигурация полимерных цепей и образование фибрилл являются результатом одновременно протекающих процессов роста цепи (полимеризации) и “холодной” кристаллизации, в отличие от других полимеров, в которых наблюдают формирование фибрилл в процессе кристаллизации в условиях сдвиговой деформации [13]. В дальнейшем на всех стадиях переработки порошка (компактирования и спекания) макромолекулы остаются связанными в составе фибриллы. Этому способствует большое расстояние между их концами (практически на всю длину цепей до 10 мкм), перепутывание цепей в аморфных прослойках фибриллы, отсутствие достаточного свободного объема для реализации термодинамически равновесного состояния (сворачивания в клубок). Именно эта первоначально приданная в процессе полимеризации и сохраняющаяся выше температуры плавления фибриллярная структура может являться причиной чрезвычайно высокой вязкости расплава ПТФЭ, проявлений жидкокристаллических свойств и отсутствия каучукоподобного поведения, что ранее объясняли сохранением частично ориентированного состояния цепей за счет их высокой жесткости [23, 24]. В процессе кристаллизации ПТФЭ в ск-среде какие-либо механические воздействия, приводящие к фибриллизации за счет сдвиговой деформации, отсутствуют, поэтому возникновение фибриллярных структур можно объяснить только существованием самих фибрилл в расплаве.
Спеченный блочный ПТФЭ не обладает высокой пористостью, подобно частицам полимеризата, однако его набухание и пластификация в ск-растворителях выше температуры плавления протекает достаточно эффективно. Перехода в однофазную жидкость также как для частиц полимеризата не наблюдается. В случае кристаллизации спеченного блочного ПТФЭ в ск-среде формируется объемная пористая структура, что ведет к заметному снижению плотности (табл. 2). Микроструктура при этом характеризуется образованием не только ламелей, но и центрально-симметричных пористых структур с радиальной ориентацией фибрилл (6а, 6б), так же как для частиц полимеризата. При кристаллизации тех же образцов при атмосферном давлении после удаления ск-растворителя плотность остается на уровне исходного спеченного ПТФЭ (табл. 2), а микроструктура характеризуется образованием исключительно ламелей (рис. 6в, 6г). Закономерных отличий в структуре, плотности или кристалличности после обработки спеченного ПТФЭ в ск-СО2 и ск-ПФО не наблюдается.
Таблица 2.
Влияние условий обработки спеченного блочного ПТФЭ в ск-среде на степень кристалличности χ, плотность ρ, температуру Тm и теплоту ∆Hm плавления
Условия обработки | ρ, г/см3 | Тm, °С | ∆Hm, Дж/г | χ, % | η |
---|---|---|---|---|---|
До обработки | 2.15 | 328 | 25 | 30 | – |
После обработки | |||||
365°С/12 МПа, ск-СО2/48 ч/охлаждение и кристаллизация при атм. давлении | 2.14 | 330 | 53 | 65 | 0.50 |
365°С/24 МПа, ск-СО2/48 ч/охлаждение и кристаллизация при атм. давлении | 2.15 | 329 | 47 | 57 | 0.70 |
365°С/60 МПа, ск-СО2/24 ч/охлаждение и кристаллизация при атм. давлении | 2.14 | 329 | 44 | 54 | 0.90 |
365°С/60 МПа, ск-СО2/24 ч/охлаждение и кристаллизация в ск-СО2 | 1.84 | 329 | 50 | 61 | 0.90 |
365°С/90 МПа, ск-СО2/24 ч/охлаждение и кристаллизация в ск-СО2 | 1.70 | 328 | 41 | 50 | 0.90 |
365°С/2.8 МПа, ск-ПФО/12 ч/охлаждение и кристаллизация в ск-ПФО | 1.90 | 330 | 48 | 58 | 0.50 |
365°С/8 МПа, ск-ПФО/48 ч/охлаждение и кристаллизация в ск-ПФО | 1.80 | 330 | 53 | 65 | 0.70 |
365°С/10 МПа, ск-ПФО/24 ч/охлаждение и кристаллизация при атм. давлении | 2.10 | 331 | 50 | 61 | 0.90 |
Рис. 6.
Микроструктура спеченного блочного ПТФЭ после обработки в ск-СО2 (а, в) и ск-ПФО (б, г). Условия обработки: а – 365°С, 60 МПа, 24 ч, η = 0.9, охлаждение и кристаллизация в ск-СО2; б – 365°С, 10 МПа, 24 ч, η = 0.9, охлаждение и кристаллизация в ск-ПФО; в – 365°С, 60 МПа, 24 ч, η = 0.9, охлаждение и кристаллизация при атмосферном давлении; г – 365°С, 8 МПа, 48 час, η = 0.7, охлаждение и кристаллизация при атмосферном давлении.
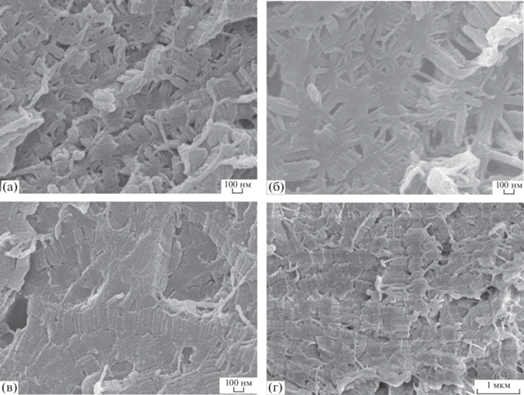
Важно отметить, что обработка частиц полимеризата ПТФЭ в ск-среде в заданных условиях приводит к значительному увеличению теплоты плавления ∆Hm, по сравнению с типичными значениями после обычного спекания на воздухе при атмосферном давлении (табл. 1). Наблюдаемый рост ∆Hm соответствует увеличению степени кристалличности χ приблизительно в два раза (табл. 1). Температура плавления при этом практически не изменяется.
Аналогичные изменения наблюдаются для спеченного блочного ПТФЭ. Обработка в ск-среде приводит к увеличению степени кристалличности в 1.5–2 раза (табл. 2). На термограммах плавления и кристаллизации этому соответствует заметное увеличение интенсивности соответствующих пиков (рис. 7а, 7б).
Рис. 7.
Термограммы плавления (а) и кристаллизации (б) для спеченного блочного ПТФЭ до (1) и после (2–5) обработки в ск-среде. Условия обработки: 2 – 365°С, 60 МПа, ск-СО2, 24 ч, охлаждение и кристаллизация в ск-СО2; 3 – 365°С, 24 МПа, ск-СО2, 48 ч, охлаждение и кристаллизация при атмосферном давлении; 4 − 365°С, 12 МПа, ск-СО2, 48 ч, охлаждение и кристаллизация при атм. давлении; 5 − 365°С, 10 МПа, ск-ПФО, 24 ч, охлаждение и кристаллизация при атмосферном давлении.
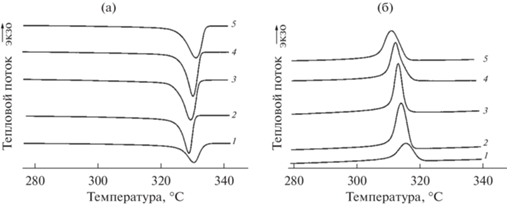
Принципиальной особенностью наблюдаемых изменений степени кристалличности является их необратимость. При повторном плавлении образцов наблюдаются те же повышенные значения ∆Hm и χ. Обратимые изменения ∆Hm и χ для полимеров явление обычное и могут быть достигнуты различными способами, например отжигом вблизи температуры плавления или закалкой (быстрым охлаждением расплава). Однако повторное плавление полимера после таких обработок приводит к восстановлению первоначальных значений.
Необратимые изменения ∆Hm и χ должны быть связаны с необратимыми изменениями микроструктуры полимера. Так, согласно эмпирическому соотношению Суве [25], изменение молекулярной массы ПТФЭ ведет к необратимому изменению теплоты кристаллизации:
(1)
${{M}_{{\text{n}}}} = 2.1 \times {{10}^{{10}}}{{\left( {\Delta {{H}_{{\text{c}}}}} \right)}^{{ - 5.16}}}.$В табл. 3 приведены значения температуры и теплоты кристаллизации для образцов ПТФЭ, обработанных в ск-среде в различных условиях, и значения Mn, рассчитанные по уравнению (1). Видно, что наблюдаемому увеличению энтальпии кристаллизации соответствует уменьшение молекулярной массы приблизительно на порядок величины (табл. 3). Столь значительное снижение Mn характерно для ПТФЭ при высокоэнергетическом радиационном воздействии [26] и объясняется процессами электронного возбуждения с последующим разрывом С–С-связей по радикальному механизму [27]. Однако возникновение напряженных состояний цепи, приводящих к разрыву С–С-связей в процессе набухания в ск-среде выше температуры плавления кристаллитов в пластифицированном состоянии, представляется крайне маловероятным. С другой стороны вклад термически активируемого разрыва С–С-связей также можно считать пренебрежимо малым, поскольку температура обработки (365°С) была даже ниже температуры, при которой проводят стандартное спекание ПТФЭ (380°С), а продолжительность обработки 12–60 ч превышала типичные времена спекания. Сами растворители ск-СО2 и ск-ПФО не являются химически активными и не могут инициировать реакции разрыва макромолекул.
Таблица 3.
Влияние условий обработки частиц полимеризата и спеченного блочного ПТФЭ в ск-среде на температуру Тс и теплоту ∆Hc кристаллизации
Условия обработки | Тс, °С | ∆Hc, Дж/г | Мn, 104 |
---|---|---|---|
До обработки при атм. давлении | 317 | 25 | 209 |
После обработки частиц полимеризата ПТФЭ | |||
365°С/12 МПа, ск-СО2/48 ч/охлаждение и кристаллизация при атм. давлении | 313 | 37 | 27 |
365°С/60 МПа, ск-СО2/24 ч/охлаждение и кристаллизация в ск-СО2 | 314 | 37 | 27 |
365°С/8 МПа, ск-ПФО/48 ч/охлаждение и кристаллизация в ск-ПФО | 316 | 34 | 43 |
После обработки спеченного блочного ПТФЭ | |||
365°С/12 МПа, ск-СО2/48 ч/охлаждение и кристаллизация при атм. давлении | 312 | 40 | 19 |
365°С/24 МПа, ск-СО2/48 ч/охлаждение и кристаллизация при атм. давлении | 313 | 40 | 19 |
365°С/60 МПа, ск-СО2/24 ч/охлаждение и кристаллизация при атм. давлении | 314 | 39 | 21 |
365°С/60 МПа, ск-СО2/24 v/охлаждение и кристаллизация в ск-СО2 | 314 | 42 | 14 |
365°С/90 МПа, ск-СО2/24 ч/охлаждение и кристаллизация в ск-СО2 | 316 | 40 | 19 |
365°С/2.8 МПа, ск-ПФО/12 ч/охлаждение и кристаллизация в ск-ПФО | 315 | 39 | 21 |
365°С/8 МПа, ск-ПФО/48 ч/охлаждение и кристаллизация в ск-ПФО | 316 | 38 | 24 |
365°С/10 МПа, ск-ПФО/24 ч/охлаждение и кристаллизация при атм. давлении | 311 | 37 | 27 |
Для объяснения полученных результатов необходимо предположить, что расплав ПТФЭ не является обычной аморфной неупорядоченной средой, подобно другим термопластичным полимерам, а обладает микроструктурой, необратимое изменение которой в ск-среде ведет к нетипичной кристалличности. Такие изменения возможны при сохранении фибриллярной упаковки макромолекул в расплаве. В структуре фибрилл наряду с участками с частично-упорядоченными сегментами, формирующими кристаллиты с выпрямленными цепями в процессе кристаллизации, существуют прослойки с неупорядоченными проходными цепями [8, 10], которые в силу кинетических (и стерических) ограничений не способны претерпевать дальнейшее разупорядочение выше температуры плавления или дальнейшее упорядочение в процессе кристаллизации. Пластификация расплава в ск-среде может способствовать распутыванию физических (и механических) “узлов” в таких прослойках и тем самым обеспечивать возможность их последующей кристаллизации с увеличением общей степени кристалличности.
Подобное изменение микроструктуры расплава будет необратимым, поскольку протекает самопроизвольно при пониженной вязкости в условиях пластификации и, соответственно, с понижением свободной энергии. Заметное снижение температуры кристаллизации ПТФЭ после обработки в ск-среде (табл. 3) косвенно подтверждает предлагаемый механизм. Высвобождение сегментов макромолекул из сетки зацеплений увеличивает в среднем молекулярную подвижность и энтропию расплава. Тогда согласно соотношению: Tc = ∆Hc/∆Sc рост энтропии приводит к уменьшению Tc.
Следует отметить, что сам по себе рост степени кристалличности не оказывает значительного влияния на механические свойства термопластичных полимеров, например модуль упругости, предел текучести или прочность при разрыве. Тогда как изменение морфологии (формы и размера кристаллических доменов, или их ориентации в микроструктуре сферолитов) может влиять кардинальным образом. Так, переход от плоскопараллельной упаковки кристаллических фибрилл к радиальной после радиационной обработки расплава ПТФЭ увеличивает износостойкость и снижает величину деформации при постоянной нагрузке на целые порядки [11, 12].
Как показано выше, аналогичная перестройка микроструктуры ПТФЭ может наблюдаться в ск-среде выше температуры плавления кристаллитов. Этот результат открывает перспективу разработки “зеленой” технологии модифицирования ПТФЭ с целью значительного улучшения его механических и трибологических свойств.
ЗАКЛЮЧЕНИЕ
Обработка частиц полимеризата и спеченного блочного ПТФЭ в ск-среде выше температуры плавления кристаллической фазы может приводить к существенному изменению микроструктуры и характеристик фазовых переходов. В зависимости от условий кристаллизации после выдержки ПТФЭ в ск-среде возможно формирование микроструктуры с радиальной и/или плоско-параллельной ориентацией фибрилл, а также ячеистой сотовой структуры. При атмосферном давлении в условиях высокой вязкости образуются в основном частично-кристаллические блоки (ламели). В пластифицированном состоянии сохраняющиеся в расплаве фибриллы формируют структуры с радиальной ориентацией. Модифицирование микроструктуры ПТФЭ носит объемный характер.
Независимо от условий кристаллизации после обработки в ск-среде теплота плавления и кристаллизации и, соответственно степень кристалличности необратимо увеличиваются в 1.5–2 раза, по сравнению со значениями для исходного ПТФЭ до обработки. Рост кристалличности связан с необратимым изменением микроструктуры расплава ПТФЭ в ск-среде: высвобождением части сегментов макромолекул из физических узлов в процессе набухания и пластификации полимерной матрицы. Распутывание узлов, ограничивающих молекулярную подвижность, способствует увеличению количества звеньев макромолекул, участвующих в формировании кристаллических доменов, и необратимому увеличению степени кристалличности. Полученные результаты открывают перспективу разработки “зеленой” технологии получения ПТФЭ с улучшенными механическими и трибологическими свойствами.
Список литературы
Бузник В.М. Фторполимерные материалы. Томск: Изд-во НТЛ, 2017. 600 с.
Острер С.Г. Фторполимеры в химической промышленности. Пермь: П., 2019. 400 с.
Ebnesajjad S. Fluoroplastics. V. 1. The Definitive User’s Guide and Data Book. Oxford. United Kingdom: William Andrew Publishing, 2015. 718 p.
Истомин НП., Семенов А.П. Антифрикционные свойства композиционных материалов на основе фторполимеров. М.: Наука, 1984. 147 с.
Speerschneider C.J., Li C.H. // J. Appl. Phys. 1963. V. 34. № 10. P. 3004.
Blanchet T.A. Wear of Polytetrafluoroethylene and PTFE Composites // Polymer Tribology / Ed. Sinha S.K., Briscoe B.J. London, United Kingdom: Imperial Colledge Press, 2009. P. 347.
Bahadur S., Tabor D. // Wear. 1984. V. 98. № 1–3. P. 1.
Бузник В.М. // Фторполимерные материалы. Томск: Изд-во НТЛ, 2017. С. 340.
Khatipov S.A., Serov S.A., Sadovskaya N.V., Konova E.M. // Rad. Phys. Chem. 2012. V. 81. № 3. P. 256.
Хатипов С.А., Садовская Н.В., Обвинцев А.Ю., Касаткин А.Н. // Поверхность. Рентген., синхротр, и нейтрон. исслед. 2015. № 11. С. 72. https://doi.org/10.7868/S0207352815100121
Хатипов С.А., Серов С.А., Садовская Н.В. // Вопросы материаловедения. 2012. № 4(72). С. 191.
Хатипов С.А., Конова Е.М., Артамонов Н.А. // Росссийский химический журн. 2008. Т. LII. № 5. С. 64.
Вундерлих Б. Физика макромолекул. Кристаллическая структура, морфология, дефекты. М.: Мир, 1976. 623 с.
Prime R.B., Wunderlich B. // J. Polimer Sci. A2. 1969. V. 7. P. 1969.
Tuminello W.H., Dee G.T. // Macromolecules. 1994. V. 27. № 3. P. 2061.
Tuminello W.H., Dee G.T. McHugh M.A. // Macromolecules. 1995. V. 28. № 5. P. 1506.
Vopilov Yu.E., Nikitin L.N., Yurkov G.Yu., Kharitonova E.P., Khokhlov A.R., Bouznik V.M. // J. Supercritical Fluids. 2012. V. 62. P. 204.
Chu B., Wu C., Buck W. // Macromolecules. 1989. V. 22. № 2. P. 831.
Smith P., Gardner K.H. // Macromolecules. 1985. V. 18. № 6. P. 1222.
NIST Chemistry Web Book. https://webbook.nist.gov/ cgi/fluid
Lau S.F., Suzuki H., Wunderlich B. // J. Polym. Sci.: Polym. Phys. 1984. T. 22. № 3. C. 379.
Паншин Ю.A., Малкевич С.Г., Дунаевская Ц.С. Фторопласты. Ленинград: Изд-во Химия, 1978. 232 с
Фторполимеры / под ред. Уолла Л.А.: пер. с англ. / Под ред. Кнунянца И.Л., Пономаренко В.А. М.: Мир, 1975. 448 с.
Bunn C.W., Cobbold A.J., Palmer R.P. // J. Polym. Sci. 1958. V. 28. № 117. P. 365.
Suwa T., Takeshita M., Machi S. // J. Appl. Polym. Sci. 1973. V. 17. № 11. P. 3253.
Fuchs B., Lappan U., Lunkwitz K., Scheler U. // Macromolecules. 2002. V. 35. № 24. P. 9079.
Милинчук В.К., Клиншпонт Э.Р., Пшежецкий С.Я. Макрорадикалы. М.: Химия, 1980. 264 с.
Дополнительные материалы отсутствуют.
Инструменты
Поверхность. Рентгеновские, синхротронные и нейтронные исследования