Поверхность. Рентгеновские, синхротронные и нейтронные исследования, 2022, № 3, стр. 37-43
Исследование термической стабильности структуры и механических свойств композитных проводов из микролегированных алюминиевых сплавов
А. В. Нохрин a, Я. С. Шадрина a, *, В. Н. Чувильдеев a, В. И. Копылов a, b, А. А. Бобров a, Н. Н. Берендеев a, А. В. Пискунов a, А. А. Мурашов a
a Нижегородский государственный университет им. Н.И. Лобачевского
603950 Нижний Новгород, Россия
b Физико-технический институт Национальной академии наук Беларуси
220141 Минск, Беларусь
* E-mail: janashadr@gmail.com
Поступила в редакцию 12.04.2021
После доработки 22.05.2021
Принята к публикации 27.05.2021
- EDN: VDBVBX
- DOI: 10.31857/S1028096022010125
Аннотация
Исследована термическая стабильность композитной проволоки из микролегированных алюминиевых сплавов Al–Zr–(Sc,Hf). Проволока была получена путем совместного волочения алюминиевого сплава с медной оболочкой. Изучено влияние отжигов на механические свойства композитной проводниковой алюминиевой проволоки. Показано, что процесс распада твердого раствора при отжиге композитных проводов носит двухстадийный характер, обусловленный раздельным выделением частиц Al3Zr при “низких” температурах и выделением частиц Al3(Sc,Hf) при “высоких” температурах отжига. Механические испытания на растяжение показали, что отжиг при температуре 500°С в течение 30 мин приводит к снижению прочности и увеличению пластичности проволоки до 10%. После отжига в проволоке сформирована однородная мелкозернистая структура, наблюдается повышенная твердость и прочность образцов за счет выделения частиц Al3(Sc,Hf).
ВВЕДЕНИЕ
Одной из актуальных задач современной электротехники является замена медных проводов на алюминиевые при условии сохранения их термической стабильности, высокой электропроводности и прочности при повышенных температурах [1–3]. Это позволяет снизить вес бортовой сети современных транспортных средств, в первую очередь, самолетов [4] и, следовательно, повысить их дальность полета и грузоподъемность, снизить расход топлива. Особенно сложной является задача обеспечения физико-механических свойств малогабаритных композитных проводов с медной или серебряной оболочкой, поскольку длительная выдержка при повышенных температурах может приводить к интенсивной диффузии меди в поверхность алюминиевой жилы.
Целью работы является исследование термической стабильности малогабаритных композитных проводов, изготовленных из новых микролегированных алюминиевых сплавов.
Новые микролегированные алюминиевые сплавы должны в перспективе обеспечить замену промышленного высоколегированного алюминиевого сплава 01417, который в настоящее время используется отечественной промышленностью для изготовления малогабаритных композитных проводов [4], но не обеспечивает необходимого уровня термической стабильности механических свойств.
МЕТОДИКА
Объектами исследования являются микролегированные алюминиевые сплавы (табл. 1) и полученные из данных сплавов биметаллические алюминиевые провода диаметром 0.26 мм с покрытием из высокочистой меди (толщина покрытия ~0.03 мм). Образцы алюминиевых сплавов получали методом индукционного литья из высокочистого алюминия А99(997) с помощью литьевой машины INDUTHERM VTC-200 (табл. 2). Химический анализ сплавов проводился с использованием анализатора с индуктивно-связанной плазмой iCAP 6300-ICP-OES Radial View Spectrometer (Thermo Scientific, Waltham, USA). Образцы композитных проводов получали путем совместного волочения при комнатной температуре в стане цепном CGD-CE 1200 Rodent (∅ 8 → → 4 → 1.25 → 0.26 мм).
Таблица 1.
Состав исследуемых сплавов и механические свойства проводов
Обозначение | Химический состав, мас. % | Механические свойства проволоки | ||||||
---|---|---|---|---|---|---|---|---|
исх. состояние | отжиг 450°С | |||||||
Al | Zr | Sc | Hf | Hv, МПа | σв, МПа | Hv, МПа | σв, МПа | |
Сплав № 1 | 100% | – | – | – | 220 | 230 | 230 | 135–140 |
Сплав № 2 | Ост. | 0.25 | 0.10 | – | 490 | 345 | 470 | 220–235 |
Сплав № 3 | Ост. | 0.20 | 0.10 | 0.10 | 485 | 350 | 485 | 190–210 |
Сплав № 4 | Ост. | 0.25 | 0.05 | 0.05 | 460 | 370 | 465 | 195 |
Сплав № 5 | Ост. | 0.25 | – | 0.10 | 425 | 370 | 430 | 180 |
Сплав № 6 | Ост. | 0.25 | – | – | 365 | 320 | 285 | 150 |
01417 | – | – | – | – | 710* | ≥160 [4] | 613 (500°С, 4 ч)* | – |
Таблица 2.
Режимы получения сплавов
Параметры литья | Номер сплава | |||||
---|---|---|---|---|---|---|
1 | 2 | 3 | 4 | 5 | 6 | |
Изложница, мм | 22 × 22 × 160, графит | |||||
Тигель 150 см3 | SiO2 + ZrO2 | |||||
Продувка аргоном перед плавкой, циклы | 3 | |||||
Продувка аргоном во время нагрева, циклы | 3 | |||||
Перемешивание расплава | Индукционное | |||||
Мощность нагрева, кВт | 4.5 | |||||
Время до расплавления компонентов, с | 520 | 515 | 480 | 515 | 510 | 450 |
Температура выдерживания расплава, °С | 780 | 820 | 820 | 820 | 820 | 810 |
Выдержка перед разливкой, мин | 3 | 20 | 20 | 20 | 20 | 9 |
Температура разливки, °C | 760 | 760 | 760 | 760 | 760 | 750 |
Время охлаждения, с | 50 | 250 | 250 | 250 | 250 | 40 |
в т. ч. время вибрации, с | 50 | 50 | 50 | 50 | 50 | – |
Исследования микротвердости Hv проводились в центре поперечного сечения провода с использованием твердомера HVS-1000. Для испытаний на разрыв проволоки была использована универсальная разрывная машина Lloyd Instruments LR5KPlus (скорость перемещения траверсы составляла 10 мм/мин). В процессе испытаний фиксировалась диаграмма “напряжение σ–деформация ε”, по которой определяли значения предела прочности σв и относительного удлинения до разрушения δ. Фрактографическое исследование изломов образцов проводов после испытаний на растяжение проводилось при помощи растрового электронного микроскопа TESCAN VEGA II, оснащенного энергодисперсионным микроанализатором Oxford Instruments INCA 350. Металлографические исследования макроструктуры проводились с использованием микроскопа Leica IM DRM. Образцы перед исследованием подвергались механической полировке до уровня шероховатости менее 1 мкм с последующей электрохимической полировкой и травлением в спиртовом растворе 10.4% HF + 6.3% HNO3 + 83.3% C3H8O3. Для получения статистически достоверных результатов проводили испытания не менее чем для трех образцов в каждой серии.
Для исследований термической стабильности образцы проводов подвергали отжигам в воздушной печи типа СНОЛ.
ЭКСПЕРИМЕНТАЛЬНЫЕ РЕЗУЛЬТАТЫ
В исходном состоянии литые сплавы в зависимости от химического состава имеют однородную крупнозернистую структуру в центральной части слитков, по краям образцов наблюдается структура столбчатых кристаллов (рис. 1). Соотношение площади занимаемой каждой из типов структур зависит, в первую очередь, от типа и концентрации легирующих элементов.
Рис. 1.
Фотографии макроструктуры литых сплавов: а – Al–0.25Zr–0.10Sc; б – Al–0.20Zr–0.10Sc–0.10Hf; в – Al–0.25Zr–0.05Sc–0.05Hf; г – Al–0.25Zr–0.10Hf; д – Al–0.25Zr.
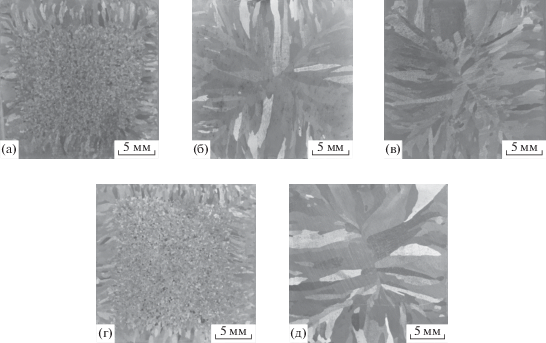
Обобщение результатов механических испытаний показывает, что в исходном состоянии биметаллические провода имеют высокую твердость и прочность. Максимальные значения предела прочности наблюдаются для сплавов № 2–4 системы Al–Zr–(Sc,Hf). Анализ диаграмм деформации показывает, что в исходном состоянии пластичность сплавов очень мала: стадия устойчивого пластического течения практически отсутствует, и сплавы хрупко разрушаются при достижении предела прочности (рис. 2).
Рис. 2.
Диаграммы растяжения образцов биметаллической проволоки при комнатной температуре в исходном состоянии и после отжига при температуре 500°С в течение 30 минут.
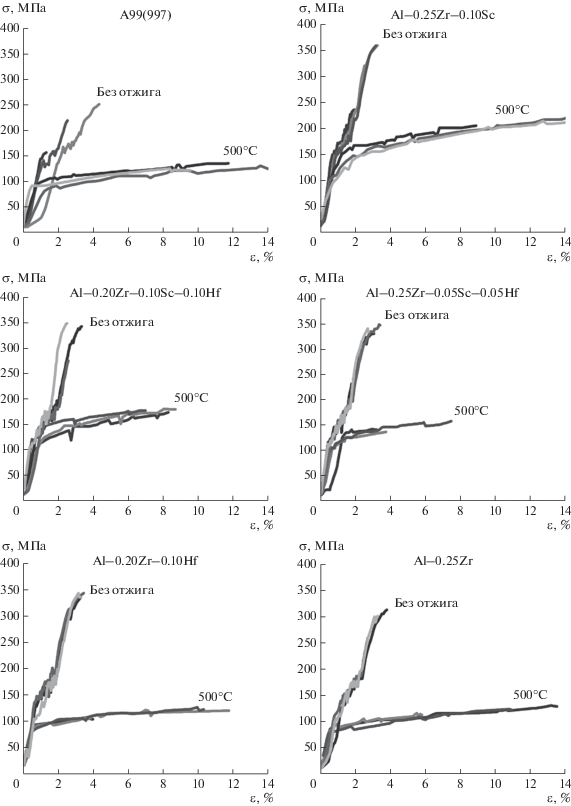
Фрактографический анализ области разрушения (рис. 3) показывает, что разрушение происходит хрупко: путем среза, который реализуется в результате сдвига по плоскости скольжения. На изломе наблюдается отслоение медной оболочки от алюминиевой проволоки, что может свидетельствовать о недостаточно высоком уровне адгезионной прочности межфазной границы “алюминий–медь”. Медная оболочка при испытании на растяжение разрушается вязко, при этом образуются микропоры.
Рис. 3.
Фрактографический анализ изломов образцов биметаллической проволоки № 2 после испытания на растяжения в исходном состоянии (а) и после отжига при температурах 250 (б) и 500°С (в).
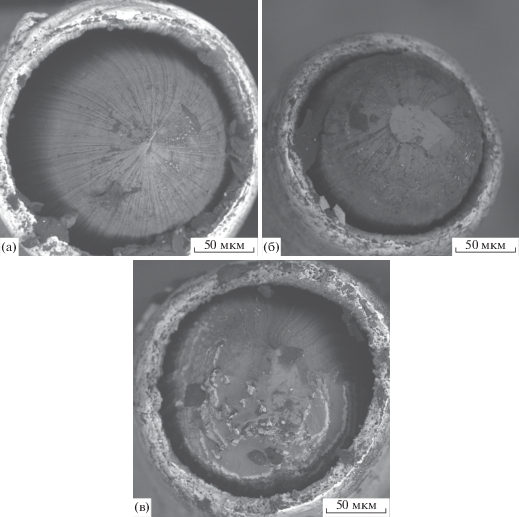
На рис. 4 показаны зависимости микротвердости от температуры при 30-минутном отжиге. Исследования показали, что зависимости Hv(T) для сплавов № 2–4 системы Al–Zr–(Sc,Hf) имеют два максимума: при температурах отжига 200 и 350°С. Зависимость микротвердости биметаллической проволоки изготовленной из сплава Al–0.25% Zr (серия № 6) имеет только один максимум, соответствующий температуре отжига 200°С.
Рис. 4.
Зависимости микротвердости (а) и предела прочности (б) от температуры отжига образцов биметаллического провода (состав сплавов, табл. 1).
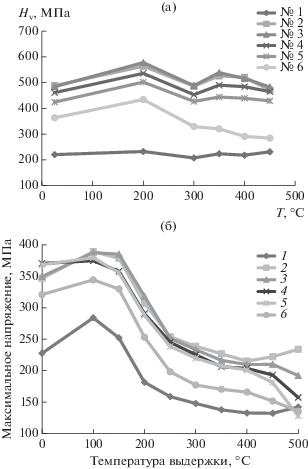
Полученный результат позволяет предположить, что в процессе отжига происходит двухстадийный распад твердого раствора: при более “низких” температурах нагрева (~200°С) в сплавах Al–Zr–(Sc,Hf) происходит выделение наночастиц Al3Zr, а при повышенных температурах (~350°С) – интенсивное выделение частиц Al3Sc (в сплаве № 2) или интерметаллидов переменного состава Al3(Sc,Hf) (сплавах № 3, 4). В пользу данного предположения также свидетельствует близость температуры второго максимума к температуре, при которой наблюдаются максимальные значения твердости при отжиге микрокристаллических проводниковых сплавов Al–0.5Mg–Sc с содержанием скандия от 0.2 до 0.5% [5].
Отметим, что выделение частиц Al3Zr при столь низких температурах отжига алюминиевой проволоки является достаточно неожиданным результатом, поскольку обычно распад твердого раствора Al–Zr в литых и рекристаллизованных алюминиевых сплавах происходит при значительно более высоких значениях температур, выдержек [6–8] или высоких степеней пересыщения (высоких концентраций циркония в сплаве) [9, 10]. Одной из причин этого, по нашему мнению, является формирование в алюминиевом сплаве сильнодеформированной ультрамелкозернистой структуры, способствующей увеличению интенсивности распада твердого раствора и снижению характерных температур протекания диффузионно-контролируемых процессов [11].
Двухстадийный характер распада твердого раствора позволяет сохранить высокие значения микротвердости и предела прочности вплоть до температур нагрева 450–500°С (рис. 4, табл. 1). Значения предела прочности и твердости разработанных микролегированных проводниковых сплавов оказываются близки к характеристикам проволок, изготовленных из проводниковых алюминиевых сплавов с заметно бóльшим суммарным содержанием скандия и циркония [12].
Механические испытания на растяжение отожженных проводов, показывают, что отжиг при температуре 500°С приводит к снижению прочности, но заметному повышению пластичности. Как видно из рис. 3, на диаграммах σ(ε) наблюдается стадия устойчивого пластического течения, а величина относительного удлинения до разрушения достигает для большинства сплавов величины более 10%. Максимальные значения твердости и предела прочности наблюдаются для сплавов № 2 и № 3, в которых при повышенных температурах наблюдается выделение частиц Al3Sc или Al3(Sc,Hf).
Повышенная пластичность образцов биметаллической проволоки свидетельствует о том, что отжиг привел к росту зерен и формированию однородной мелкозернистой структуры (рис. 5), а повышенная твердость и прочность образцов обеспечена за счет выделения частиц Al3(Sc,Hf).
Рис. 5.
Микрофотография структуры проволоки из сплава № 3 после отжига при температуре 400°С (30 мин).
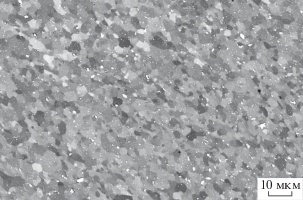
Интересно отметить, что сплавы, содержащие в своем составе одновременно скандий и гафний, обладают более низкой пластичностью в отожженном состоянии, чем сплавы Al–Zr, Al–Zr–Sc или Al–Zr–Hf (рис. 2). Это косвенно может свидетельствовать о том, что частицы переменного состава Al3(Sc,Hf) обладают повышенной энергией межфазной границы “алюминиевая матрица–частица Ll2” или более высоким модулем сдвига. Эти факторы могут препятствовать “перерезанию” выделившихся наночастиц Al3(Sc,Hf) решеточными дислокациями, что приводит к образованию петель дисклинационного типа на частицах и увеличению дальнодействующих внутренних полей напряжений [13].
Заметим также, что сплав Al–0.25% Zr–0.10% Hf имеет более низкие значения предела прочности и твердости в отожженном состоянии, что может свидетельствовать о более высокой скорости роста частиц Al3Hf по сравнению с частицами Al3Sc или Al3(Sc,Hf). Снижение механических свойств в отожженном сплаве Al–0.25% Zr–0.05% Sc–0.05% Hf обусловлено, по нашему мнению, малой объемной долей выделяющихся частиц Al3(Sc,Hf).
Фрактографический анализ изломов показывает, что отжиг не оказывает существенного влияния на характер разрушения, но приводит к увеличению зоны разрушения и уменьшению степени отслоения алюминиевого провода от медной оболочки. Это может свидетельствовать о том, что в процессе нагрева произошла взаимная диффузия меди в поверхность алюминиевого провода и алюминия в медную оболочку.
ЗАКЛЮЧЕНИЕ
Исследованы особенности изменения механических свойств при отжиге биметаллических микролегированных алюминиевых проводов малого сечения (∅0.26 мм) с покрытием из высокочистой меди. Показано, что наибольшей термической стабильностью обладают образцы, изготовленные из сплавов Al–Zr–(Sc,Hf). После отжига провода, изготовленные из сплавов Al–Zr–(Sc,Hf), обладают наиболее высокими значениями твердости и предела прочности. Установлено, что процесс распада твердого раствора при отжиге данных сплавов носит двухстадийный характер: выделение частиц Al3Zr при пониженных температурах отжига (~250°С) и выделение частиц Al3(Sc,Hf) при повышенной температуре нагрева (~350°С). Отмечено, что выделение частиц Al3Zr при столь низких температурах является неожиданным результатом, который, вероятно, обусловлен формированием в алюминиевом сплаве сильно неравновесной ультрамелкозернистой структуры при волочении. Двухстадийный характер процесса распада твердого раствора позволяет сохранить высокие значения микротвердости и предела прочности вплоть до температур нагрева 450–500°С. Установлено, что при отжиге изменяется характер излома образцов биметаллических композитных проводов, испытанных на растяжение, что обусловлено взаимной диффузией меди в поверхность провода и алюминия в медную оболочку.
Список литературы
Medvedev A., Arutyunyan A., Lomakin I., Bondarenko A., Kazykhanov V., Enikeev N., Raab G., Murashkin M. // Metals. 2018. V. 8. № 12. P. 1034.https://doi.org/10.3390/met8121034
Yang C., Masquellier N., Gandiolle C., Sauvage X. // Scripta Materialia. 2020. V. 189. P. 21.https://doi.org/10.1016/j.scriptamat.2020.07.052
Moisy F., Gueydan A., Sauvage X., Keller C., Guillet A., Nguyen N., Martinez M., Hug E. // Materials Science Forum. 2018. V. 941. P. 1914. https://doi.org/10.4028/www.scientific.net/MSF.941.1914
Матвеев Ю.А., Гаврилова В.П., Баранов В.В. // Кабели и провода. 2006. № 5. С. 22.
Чувильдеев В.Н., Шадрина Я.С., Нохрин А.В., Копылов В.И., Бобров А.А., Грязнов М.Ю., Шотин С.В., Табачкова Н.Ю., Пискунов А.В., Чегуров М.К., Мелехин Н.В. // Металлы. 2021. № 1. С. 10.
Knipling K.E., Dunand D.C., Seidman D.N. // Acta Materialia. 2008. V. 56. P. 1182.https://doi.org/10.1016/j.actamat.2007.11.011
Wen S.P., Gao K.Y., Huang H., Wang W., Nie Z.R. // J. Alloys and Compounds. 2014. V. 599. P. 65.https://doi.org/10.1016/j.jallcom.2014.02.065
Mikhaylovskaya A.V., Mochugovskiy A.G., Levchenko V.S., Tabachkova N.Yu., Mufalo W., Portnoy V.K. // Materials Characterization. 2018. V. 139. P. 30.https://doi.org/10.1016/j.matchar.2018.02.030
Belov N., Akopyan T., Korotkova N., Murashkin M., Timofeev V., Fortuna A. // Metals. 2021. V. 11. № 2. P. 236.https://doi.org/10.3390/met11020236
Belov N., Murashkin M., Korotkova N., Akopyan T., Timofeev V. // Metals. 2020. V. 10. № 6. P. 769.https://doi.org/10.3390/met10060769
Segal V.M., Beyerlein I.J., Tome C.N., Chuvil’deev V.N., Kopylov V.I. Fundamentals and Engineering of Severe Plastic Deformation. N.Y.: Nova Science Publishers, 2010. 542 p.
Чувильдеев В.Н., Нохрин А.В., Шадрина Я.С., Пискунов А.В., Копылов В.И., Берендеев Н.Н., Чепеленко В.Н. // Металлы. 2020. № 5. С. 64.
Чувильдеев В.Н., Нохрин А.В., Смирнова Е.С., Копылов В.И. // Металлы. 2013. № 5. С. 52.
Дополнительные материалы отсутствуют.
Инструменты
Поверхность. Рентгеновские, синхротронные и нейтронные исследования