Поверхность. Рентгеновские, синхротронные и нейтронные исследования, 2022, № 3, стр. 50-55
Использование механолюминесцирующих композиционных покрытий для визуализации механических напряжений и трещин в материалах
А. Ф. Банишев *
Институт проблем лазерных и информационных технологий
Российской академии наук – филиал Федерального научно-исследовательского центра
“Кристаллография и фотоника” РАН
140700 Московская область, Шатура, Россия
* E-mail: banishev@mail.ru
Поступила в редакцию 03.06.2021
После доработки 25.07.2021
Принята к публикации 30.07.2021
- EDN: IHQNSV
- DOI: 10.31857/S1028096022030049
Аннотация
Получен композиционный материал на основе прозрачного в видимой области спектра клея и порошка люминофора SrAl2O4:(Eu2+,Dy3+). Исследовали фотолюминесцентные и механолюминесцентные свойства полученного композиционного материала, а также процесс разрушения хрупких материалов при механическом воздействии (ударе). Для регистрации и визуализации распределения возникающих механических напряжений при ударе и процесса образования и роста трещин использовался полученный механолюминесцирующий композиционный материал, который наносился на поверхность исследуемого материала. Показано, что механолюминесцирующий слой чувствителен к образующимся при ударе трещинам в образце и позволяет с хорошим разрешением визуализировать распределение механических напряжений и процесс образования и роста трещин.
ВВЕДЕНИЕ
Материалы, преобразующие внешние механические воздействия в излучение света, привлекают все большее внимание исследователей [1–5]. В литературе такое излучение называют механолюминесценцией или деформационно-стимулированной люминесценцией. В последние годы синтезировано большое количество новых материалов-механолюминофоров, механолюминесцирующих в разных спектральных диапазонах [6–10]. Возрос интерес и к исследованиям механо-пьезо-люминофоров и созданию на их основе новых типов приборов и устройств механо-пьезо-фотоники [3, 11–14]. В работе [15] представлены обнадеживающие перспективы использования механо-пьезолюминофоров в полупроводниковой микро-пьезоэлектронике и пьезофотонике, в которых транспорт носителей (электронов и дырок) в p–n переходе управляется не внешним источником напряжения, а пьезопотенциалом, создаваемом механическими воздействиями. Это новые типы элементной базы для современной электроники и фотоники, работающие на новых физических принципах и не требующие внешних источников напряжения.
Механолюминофоры, в частности, могут быть успешно использованы для создания сенсорных элементов механических воздействий (механооптических конверторов) для контроля состояния материалов, подвергающихся механическим воздействиям [16–22]. В отличие от традиционных способов контроля напряжений и деформаций различных материалов и конструкций с помощью тензодатчиков, использование механолюминесцирующих композиционных материалов имеет существенные преимущества, так как слой такого материала можно наносить на большие площади исследуемой конструкции. Известно [14, 23–25], что интенсивность механолюминесценции пропорциональна величине напряжений и деформаций поверхности, поэтому по распределению интенсивности свечения механолюминесцирующего слоя можно судить о величине и распределении напряжений и деформаций исследуемой детали или конструкции. В работах [20, 26, 27] с помощью механолюминесцирущего покрытия, нанесенного на поверхность образца, исследовали образование и скорость роста трещин в керамике. Для инициирования образования и роста трещин использовался индентор. Была показана высокая информативность использования механолюминесцирующих покрытий для диагностики напряжений, а также зарождения и роста трещин в материалах при механическом воздействии. В работе [20] механолюминесцентные покрытия использовались для регистрации глубоких микротрещин, образующихся в объеме материала при циклических нагрузках и растяжении.
Целью данной работы является исследование фото- и механолюминесценции полученного композиционного материала, а также исследование процесса разрушения хрупких материалов (стекол) при механическом (ударном) воздействии.
РЕЗУЛЬТАТЫ И ИХ ОБСУЖДЕНИЕ
В данной работе получен композиционный механолюминесцирующий материал на основе прозрачного в видимой области спектра клея и порошка механолюминофора SrAl2O4:(Eu2+,Dy3+). Исследовали кинетику свечения фотолюминесценции и механолюминесценции полученного композиционного материала. Для исследования механолюминесценции наносили слой суспензии (композита) толщиной ≈150–200 мкм на поверхность металлической пластины радиусом 2 см и толщиной 100 мкм. После затвердевания суспензии проводили исследования механолюминесценции. На рис. 1 показана схема установки для исследования кинетики механолюминесценции. Возбуждение механолюминесценции проводилось путем воздействия механического ударника. Механический ударник воздействовал на свободную поверхность металлической пластины. На рис. 2a представлена кинетика механолюминесценции полученного композита, возбуждаемой в результате воздействия механического ударника. На рис. 2б представлена кинетика фотолюминесценции полученного композита, возбуждаемой в результате воздействия лазерного импульса (λ = 355 нм, τ = 8 нс). Регистрацию фотолюминесценции и механолюминесценции проводили с помощью фотоумножителя. Видно, что максимум фотолюминесценции достигается практически одновременно с максимумом лазерного импульса, в то время как максимум механолюминесценции достигается только через примерно Δt ≈ 0.3 мс после начала воздействия металлического ударника, что связано с временем деформации материала при ударе. Известно, что интенсивность механолюминесценции пропорциональна величине механических напряжений. Поэтому, зная время нарастания интенсивности механолюминесценции, которое соответствует времени торможения ударника, скорость и массу ударника можно оценить силу удара и давление, возникающее при ударе. Масса ударника составляла m ≈ 3.2 × 10–3 кг, скорость изменяли натяжением пружины в пределах от 1 до 2.5 м/с. Как следует из рис. 2, сила удара составила F = 2 Н, давление P ≈ 6 × 105 Н/см2.
Рис. 1.
Схема экспериментальной установки для исследования кинетики механолюминесценции: 1 – металлическая пластина, 2 – механолюминесцирующий композиционный слой, 3 – ударник, 4 – фотоумножитель.
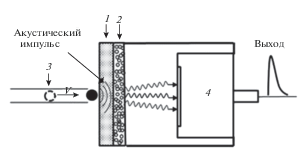
Рис. 2.
Фотолюминесценция и механолюминесценция композита на основе прозрачного в видимой области спектра клея и порошка люминофора SrAl2O4:(Eu2+,Dy3+), возбуждаемая лазерным импульсом (λ = 355 нм, τ = 8 нс) (а) и механическим ударом (б).
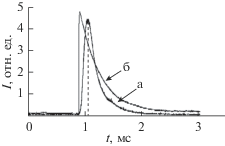
На рис. 3 показана кинетика фотолюминесценции композита при возбуждении: непрерывным лазерным излучением (λ = 405 нм, I ≈ 10 мВт) (рис. 3а), лазерным импульсом (λ = 355 нм, W ≈ ≈ 10 мДж, τ = 8 нс) (рис. 3б) и совместным воздействием непрерывного лазерного излучения и лазерного импульса (рис. 3в). На рисунке I0 – интенсивность фотолюминесценции при возбуждении непрерывным лазерным излучением. При подаче лазерного импульса на участок поверхности, которая облучается непрерывным лазерным излучением, амплитуда фотолюминесценции увеличивается, но остается значительно меньше, чем суммарная амплитуда, которая получилась бы при сложении амплитуды фотолюминесценции при импульсном воздействии и интенсивности I0. Возможной причиной этого является изменение заселенностей электронных уровней по сравнению с тем случаем, когда лазеры воздействовали по отдельности.
Рис. 3.
Фотолюминесценция SrAl2O4:(Eu2+,Dy3+), возбуждаемая непрерывным лазерным излучением (λ = 405 нм, I ≈ 10 мВт) (а), лазерным импульсом (λ = 355 нм, W ≈ 10 мДж, τ = 8 нс) (б) и совместным воздействием непрерывного лазерного излучения и лазерного импульса (в). На рисунке I0 – интенсивность фотолюминесценции при возбуждении непрерывным лазерным излучением.
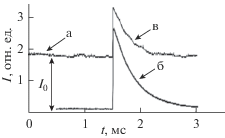
В работе исследовали процесс разрушения (образования трещин) хрупких материалов с использованием механолюминесцирующего композита для визуализации и диагностики процесса разрушения при механическом воздействии (ударе). Для визуализации напряжений и процесса образования трещин на поверхность исследуемого материала (стеклянной пластины диаметром 30 мм и толщиной 2 мм) наносили слой суспензии композиционного материала. Согласно данным растровой электронной микроскопии (РЭМ), после затвердевания суспензии на поверхности пластины формировался тонкий слой (h ≈ 350 мкм) композиционного механолюминесцирующего материала (рис. 4).
Рис. 4.
РЭМ-изображение микрочастиц люминофора SrAl2O4:(Eu2+,Dy3+) (а), РЭM-изображения скола стеклянной пластины с нанесенным на поверхности механолюминесцирующим слоем: 1 – подложка из стекла, 2 – композиционный слой, 3 – свободное пространство (вакуум) (б).
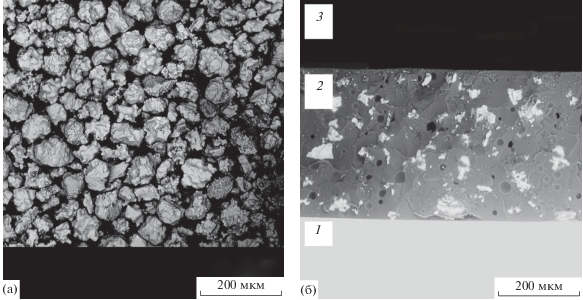
На рис. 5 показана схема экспериментальной установки для исследования процесса разрушения материалов. Механический ударник воздействовал на обратную (свободную) поверхность стеклянной пластины. Регистрация свечения механолюминесцирующего слоя, возникающего в результате удара металлического ударника массой m ≈ 32 × 10–3 кг, осуществлялась с помощью скоростной видеокамеры.
Рис. 5.
Схема экспериментальной установки для исследования процесса разрушения материалов: 1 – пластина из стекла, 2 – механолюминесцирующий слой, 3 – механический ударник, 4 – видеокамера.
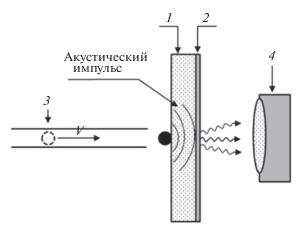
Картина распределения напряжений в пластине, возникающая в результате удара, визуализировалась распределением интенсивности свечения механолюминесцирующего слоя. При силе удара ниже порога разрушения материала свечение имело форму пятна с максимумом интенсивности в центре пятна (рис. 6a). При силе удара выше порога разрушения материала (порога образования трещин) в механолюминесцирующем слое начинают появляться светящиеся линии (рис. 6б, 6в), положение которых совпадает с положениями трещин, образовавшихся в пластине в результате удара. В местах образования трещин происходит “разделение” материала, что вызывает растягивающие напряжения в механолюминесцирующем слое и свечение вдоль образующихся трещин. Так как интенсивность свечения механолюминесцирующего слоя пропорциональна возникающим напряжениям, то по распределению интенсивности свечения можно судить о распределении напряжений в исследуемом образце и о процессе роста трещин. Следует заметить, что некоторые трещины были практически не видны невооруженным глазом и рассмотреть их можно было только с помощью лупы или под микроскопом, в то время как в механолюминесцирующем слое они достаточно надежно проявляются.
Рис. 6.
Полученные с помощью скоростной видеокамеры изображения поверхности механолюминесцирующего слоя на стеклянной пластине: a – до порога образования разрушения (скорость шарика v ≈ 1.3 м/с), б – начало образования трещин (скорость v ≈ 1.6 м/с), в – образование набора трещин (разрушение поверхности, v ≈ 2.5 м/с).
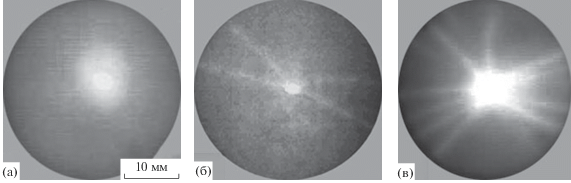
К настоящему времени не существует единого мнения относительно механизма возбуждения механолюминесценции механолюминофора SrAl2O4:(Eu2+, Dy3+) [2]. В ряде работ, например [16, 28], авторы считают, что механолюминесценция обусловлена возникновением локальных пьезоэлектрических полей в материале при воздействии механических напряжений. Пьезоэлектрические поля, в свою очередь, активируют туннельные переходы электронов с уровней ловушек в зону проводимости кристалла. Захват электронов из зоны проводимости на верхние уровни ионами Eu2+ и их последующий излучательный переход в основное состояние определяют механолюминесценцию SrAl2O4:(Eu2+,Dy3+). В работе [29] авторы обратили внимание, что только нецентросимметричная фаза SrAl2O4:(Eu2+,Dy3+) с двойниками обладает высоким выходом механолюминесценции. Авторами было высказано предположение, что пьезоэлектрические поля возникают в результате смещения двойниковых границ под действием механических напряжений. В работах [21, 22] авторы считают, что в механолюминесцирующих порошках, частицы которых имеют зернистую структуру, механолюминесценция может возникнуть также из-за активации ловушек в результате их взаимодействия с движущимися зернограничными дислокациями при деформации механолюминофора.
ЗАКЛЮЧЕНИЕ
Проведены исследования процесса разрушения хрупких материалов при воздействии механического удара. Впервые предложено использование композиционного механолюминесцирующего материала на основе полимера и мелкодисперсного порошка люминофора SrAl2O4:(Eu2+, Dy3+) для визуализации процесса разрушения при механическом (ударном) воздействии. Показано, что напряжения и трещины, возникающие в материале в процессе разрушения при ударе, достаточно полно и надежно визуализируются механолюминесцирующим слоем, нанесенным на поверхность исследуемого материала.
Список литературы
Jun-Cheng Zhang, Xusheng Wang, Gerard Marriott, Chao-Nan Xu // Progress in Materials Science. 2019. V. 103. P. 678. https://doi.org/10.1016/j.pmatsci.2019.02.001
Ang Feng, Philippe F. Smet // Materials. 2018. V. 11. P. 484. https://doi.org/10.3390/ma11040484
Xiandi Wang, Dengfeng Peng, Bolong Huang, Caofeng Pan, Zhong Lin Wang // Nano Energy. 2019. V. 55. P. 389.https://doi.org/10.1016/j.nanoen.2018.11.014
Chandra B.P., Chandra V.K., Jha P. // Physica B. 2015. V. 463. P. 62. https://doi.org/10.1016/j.physb.2015.01.030
Chunfeng Wang, Lin Dong, Dengfeng Peng, Caofeng Pan. // Adv. Intell. Syst. 2019. V. 1. P. 1900090. https://doi.org/10.1002/aisy.201900090
Haitao Lv, Zhidong Pan, Yanmin Wang // J. Luminescence. 2019. V. 209. P. 129. https://doi.org/10.1016/j.jlumin.2019.01.026
Chunfeng Wang, Dengfeng Peng, Caofeng Pan // Science Bulletin. 2020. V. 65. P. 1147. https://doi.org/10.1016/j.scib.2020.03.034
Dong Tu, Chao-Nan Xu, Sunao Kamimura, Yoichi Horibe, Hirotaka Oshiro, Lu Zhang, Yoshiharu Ishii, Koji Hyodo, Gerard Marriott, Naohiro Ueno, Xu-Guang Zheng // Adv. Mater. 2020. V. 32. P. 1908083. https://doi.org/10.1002/adma.201908083
Jha P., Chandra B.P. // Luminescence. 2014. V. 29. P. 8. https://doi.org/10.1002/bio.2647
Kamimura S., Yamada H., Xu C.N. // Appl. Phys.Lett. 2012. V. 101. № 9. P. 091113. https://doi.org/10.1063/1.4749807
Hongling Sun, Yi Zhao, Chunfeng Wang, Kangkang Zhou, Chao Yan, Guoqiang Zheng, Jiajia Huang, Kun Dai, Chuntai Liu, Changyu Shen // Nano Energy. 2020. V. 76. P. 105035. https://doi.org/10.1016/j.nanoen.2020.105035
Chunfeng Wang, Lin Dong, Dengfeng Peng, Caofeng Pan // Adv. Intell. Syst. 2019. V. 1. P. 1900090.
Yang Zhang, Guanyin Gao, Helen L.W. Chan, Jiyan Dai, Yu Wang, Jianhua Hao // Adv. Mater. 2012. 06 March. V. 24(13). P. 1729-35. https://doi.org/10.1002/adma.201104584
Hanlu Zhang, Dengfeng Peng, Wei Wang, Lin Dong, Caofeng Pan // J. Phys. Chem. C. 2015. V. 119. № 50. P. 28136. https://doi.org/10.1021/acs.jpcc.5b10302
Caofeng Pan, Lin Dong, Guang Zhu, Simiao Niu, Ruomeng Yu, Qing Yang, Ying Liu, Zhong Lin Wang // Nat. Photonics. 2013. V. 7. P. 752. https://doi.org/10.1038/nphoton.2013.191
Xiandi Wang, Hanlu Zhang, Ruomeng Yu, Lin Dong, Dengfeng Peng, Aihua Zhang, Yan Zhang, Hong Liu, Caofeng Pan, Zhong Lin Wang // Adv. Mater. 2015. 8 Apr. V. 27(14). P. 2324–31. https://doi.org/10.1002/adma.201405826
Linsheng Liu, Chao-Nan Xu, Akihito Yoshida, Dong Tu, Naohiro Ueno, Shigenobu Kainuma // Adv. Mater. Technol. 2018. 27 September. V. 4(1). P. 1800336. https://doi.org/10.1002/admt.201800336
Gun Jin Yun, Mohammad Reza Rahimi, Amir Hossein Gandomi, Gong-Cheo Lim, Jun-Seong Choi // Smart Mater. Struct. 2013. V. 22. P. 055006. https://doi.org/10.1088/0964-1726/22/5/055006
Ali Imani Azad, Mohammad Reza Rahimi, Gun Jin Yun // Smart Mater. Struct. 2016. V. 25. P. 095032. https://doi.org/10.1088/0964-1726/25/9/095032
Yuki Fujio, Chao-Nan Xu, Yoshitaro Sakata, Naohiro Ueno, Nao Terasaki // J. Alloys and Compounds. 2020. V. 832. P. 154900.
Banishev A.F., Banishev A.A. // International J. Modern Physics B. 2019. V. 33. № 30. P. 1950367. https://doi.org/10.1142/S02179792195036614
Банишев А.Ф., Банишев А.А. // Письма в ЖТФ. 2019. Т. 45. № 10. С. 3. https://doi.org/10.21883/PJTF.2019.10.47746.17737
Ratnesh Tiwari, Vikas Dubey, Chandra B.P. // Materials Physics and Mechanics. 2014. V. 19. P. 25.
Nao Terasaki, Hiroshi Yamadaa, Chao-Nan Xu // Catalysis Today. 2013. V. 201. P. 203. https://doi.org/10.1016/j.cattod.2012.04.040
Suman Timilsina, Kwang Ho Lee, Yong Nam Kwon, Ji Sik Kim // J. Am. Ceram. Soc. 2015. P. 1. https://doi.org/10.1111/jace.13566
Kim Ji Sik, Yong-Nam Kwon, Namsoo Shin, Kee-Sun Sohn // Applied Physics Letters. 2007. V. 90. P. 241916.
Kim J.S., Koh H.J., Lee W.D., Shin N., Kim J.G., Lee K.-H., Sohn K.-S. // Metals and Materials International. 2008. V. 14. № 2. P. 165. https://doi.org/10.3365/met.mat.2008.04.165
Chandra B.P., Chandra V.K., Mahobia S.K., Jha P., Tiwari R., Haldar B. // Sensors and Actuators A: Physical. 2012. V. 173. № 1. P. 9. https://doi.org/10.1016/j.sna.2011.09.043
Matsuo H., Ikeda K., Hata S., Nakashima H., Yamada H., Xu C.-N. J. // Alloys Compd. 2013. V. 577. P. 507. https://doi.org/10.1016/j.jallcom.2012.04.009
Дополнительные материалы отсутствуют.
Инструменты
Поверхность. Рентгеновские, синхротронные и нейтронные исследования