Поверхность. Рентгеновские, синхротронные и нейтронные исследования, 2022, № 4, стр. 93-101
Окисление циркониевого сплава, обработанного компрессионными плазменными потоками
В. И. Шиманский a, *, В. В. Шевелёва a, В. М. Асташинский b, А. М. Кузьмицкий b
a Белорусский государственный университет
220030 Минск, Беларусь
b Институт тепло- и массообмена Национальной академии наук Беларуси
220072 Минск, Беларусь
* E-mail: shymanskiv@mail.ru
Поступила в редакцию 22.04.2021
После доработки 20.06.2021
Принята к публикации 25.06.2021
- EDN: RTSVGN
- DOI: 10.31857/S102809602204015X
Аннотация
Представлены результаты исследования влияния высокоэнергетической импульсной плазменной обработки на кинетику окисления циркония. Образцы технически чистого циркониевого сплава обрабатывали компрессионными плазменными потоками в режиме плавления приповерхностного слоя, в результате которого происходит формирование мелкодисперсной структуры и рост поверхностного слоя нитрида циркония. Последующий отжиг в воздушной атмосфере при температурах 700 и 900°С приводит к формированию моноклинной фазы диоксида циркония ZrO2 с небольшим присутствием тетрагональной (высокотемпературной) модификации. Показано, что предварительное плазменное воздействие способствует повышению доли тетрагональной фазы вследствие ее стабилизации внутренними напряжениями из-за повышенной дефектности. Предварительное плазменное воздействие также снижает скорость окисления циркония.
ВВЕДЕНИЕ
Безопасности установок для ядерной энергетики сегодня уделяют особое внимание при их проектировании, эксплуатации, а также при выборе приемлемых конструкционных материалов, к физическим свойствам которых предъявляются повышенные требования. Цирконий и сплавы на его основе являются основными материалами, используемыми для изготовления оболочек тепловыделяющих элементов (ТВЭЛов), что обусловлено, в первую очередь, его высокой коррозионной стойкостью по отношению к щелочным и кислотным растворам, малым сечением захвата тепловых нейтронов. Однако в случае аварийных ситуаций на реакторе цирконий взаимодействует с теплоносителем (в случае водно-водяного энергетического реактора – с водой), что приводит к его интенсивному окислению [1, 2] с последующим формированием поверхностного слоя диоксида циркония ZrO2. При этом наблюдается резкая деградация физико-механических свойств, которая наряду с накоплением водорода является причиной быстрого разрушения стенок ТВЭЛов и невозможности контролировать тепловыделение в активной зоне реактора. Для снижения скорости окисления оболочек ТВЭЛов используют различные методы модифицирования поверхности, в частности, нанесение защитных покрытий и легирование дополнительными элементами, которые во многих случаях существенно повышают сечение захвата тепловых нейтронов. Так, для повышения коррозионной и эрозионной стойкости циркония под действием термических, радиационных и химических нагрузок наиболее широко используют циркониевые сплавы, например, Э110, Э365 или М5 марки ZIRLO [3, 4]. Также актуальным является разработка подходов модифицирования поверхности циркония, способствующих повышению коррозионной стойкости за счет происходящих структурных изменений. В качестве одного из таких подходов можно рассматривать воздействие на поверхность материалов высокоэнергетических импульсных потоков плазмы или пучков заряженных частиц. В частности, в [5, 6] продемонстрирована возможность повышения эксплуатационных свойств циркония и его сплавов за счет ионного перемешивания в приповерхностном слое при ионном облучении многослойной металлической пленки. Показано, что многоэлементное легирование сплавов атомами Fe, Al, Mo, Y повышает адгезионную прочность слоя оксида к поверхности сплава, уменьшая нарушения несплошности.
Однако методы ионного перемешивания позволяют модифицировать структурное состояние сплава в относительно тонком приповерхностном слое, толщина которого определяется энергией и типом бомбардирующих ионов и, как правило, не превосходит сотен нанометров. В этом ключе ряд последних проведенных работ [7–9] показал перспективность использования компрессионных плазменных потоков, генерируемых квазистационарными плазменными ускорителями, которые сочетают высокую плотность энергии и большую длительность импульса стабильного существования плазменного потока, для модифицирования толстых приповерхностных слоев различных металлов и сплавов. В результате такого воздействия достигаются высокие критические температуры в приповерхностном слое, обеспечивающие его плавление и последующее скоростное охлаждение расплава, приводящее к диспергированию зеренной структуры. Более того, предварительные эксперименты на технически чистом сплаве титана показали повышение его коррозионной стойкости по отношению к высокотемпературному окислению в воздушной атмосфере [10].
В настоящей работе предложено использовать воздействие компрессионных плазменных потоков на поверхность циркония с целью модифицирования его структуры, которое обеспечивает повышение стойкости структурно-фазового состояния при взаимодействии с воздушной атмосферой при повышенных (до 900°С) температурах. Основной целью работы было установление особенностей структурно-фазовых превращений в поверхностных слоях циркония после высокоэнергетического плазменного воздействия и изотермического отжига.
МЕТОДИКА ЭКСПЕРИМЕНТА
Объектами исследования в проведенных экспериментах служили пластины технически чистого циркониевого сплава размером 10 × 10 мм и толщиной 2 мм с минимальным количеством примесей, поверхность которых предварительно обезжиривали и очищали в спиртовом растворе.
Образцы циркониевого сплава обрабатывали компрессионными плазменными потоками [11], генерация которых происходила в магнитоплазменном компрессоре компактной геометрии в атмосфере остаточного газа – азота. Давление остаточной атмосферы составляло 10 Торр (1.33 кПа). Длительность импульса плазмы – 100 мкс. С целью равномерного воздействия на всю поверхность образца проводили многократную обработку тремя импульсами, следовавшими друг за другом с интервалом 10–15 с. Энергия плазменного потока определялась энергией, запасенной в системе накопительных конденсаторов, заряженных до напряжения 4.0 кВ. Их разрядка и приводила к формированию газоразрядной плазмы между электродами в камере магнитоплазменного компрессора. Обрабатываемые образцы помещали в камеру на расстоянии 10 см от срезов электродов. Согласно ранее проведенным калориметрическим исследованиям выбранные режимы плазменного воздействия обеспечивали плотность поглощенной энергии, необходимой для плавления приповерхностного слоя.
После воздействия плазменными потоками образцы циркониевого сплава отжигали в муфельной печи при атмосферном давлении. Для отжига были выбраны две температуры – 700 и 900°С, время отжига достигало 3 ч. Точность поддержания температуры составляла ±10°С. Охлаждение образцов проходило в печи в процессе ее остывания. Выбор температур отжига был обусловлен изучением диффузионных процессов как в низкотемпературной фазе циркония (700°С), так и в высокотемпературной фазе (900°С).
Кинетику окисления циркониевых образцов изучали на основе прироста их массы, связанного с накоплением кислорода. Для измерения массы окисленных образцов использовали аналитические весы Radwag, точность которых составляла ±0.00005 г.
Фазовый состав образцов циркония после окисления на воздухе определяли методом рентгеноструктурного анализа на дифрактометре Ultima IV Rigaku в геометрии параллельных пучков (фокусировка Брэгга–Брентано) при длине волны рентгеновского излучения 0.154178 нм. Рентгеновские дифрактограммы записывали в диапазоне углов дифракции 2θ от 20° до 80° с шагом 0.05° при скорости движения детектора 2 град/мин.
Морфологию поверхности образцов изучали в растровом электронном микроскопе LEO 1455 VP, работающем в режиме регистрации как вторичных, так и отраженных электронов, при ускоряющем напряжении 20 кВ.
С целью определения кристаллографических модификаций оксида циркония дополнительно применяли метод комбинационного рассеяния света. Спектры регистрировали с помощью спектрометра на базе конфокального микроскопа Nanofinder HE при использовании лазера с длиной волны 532 нм. Мощность лазерного излучения составляла 60 мкВт.
РЕЗУЛЬТАТЫ И ИХ ОБСУЖДЕНИЕ
Воздействие компрессионными плазменными потоками с выбранными энергетическими режимами на поверхность циркония приводит к нагреву его приповерхностного слоя выше температуры плавления. Затем вследствие интенсивного теплоотвода в объем нерасплавленной части происходит скоростная кристаллизация расплава. С помощью рентгеноструктурного анализа (рис. 1) установлено сохранение поликристаллического структурного состояния модифицированного слоя после кристаллизации. Распределение интенсивностей дифракционных максимумов указывает на преобладание кристаллографической ориентации зерен [101], соответствующее равновесному состоянию гексагональной структуры низкотемпературной α-фазы циркония. Дополнительно обнаружен дифракционный максимум при угле дифракции 2θ = 39.53° и “плечо” со стороны малых углов дифракции около дифракционной линии 002 α-Zr, которые соответствуют отражениям от кристаллографических плоскостей (200) и (111) кубического нитрида циркония ZrN, формирование которого обусловлено взаимодействием остаточной атмосферы в магнитоплазменном компрессоре с нагретым слоем циркония после завершения плазменного воздействия.
В результате изотермических отжигов образцов циркония в воздушной атмосфере происходит насыщение приповерхностных слоев кислородом, которое определяется как диффузией кислорода, так и формированием новых оксидных фаз. Согласно равновесной диаграмме состояния Zr–O [12], при температуре 700°С формирование оксида циркония начинается при концентрации кислорода 28–29 ат. %, и вплоть до концентрации кислорода 66 ат. % фазовый состав окисленного слоя представляет собой совокупность твердого раствора внедрения α-Zr(O) и оксида циркония ZrO2 – x. Как известно, оксид циркония ZrO2 может существовать в трех основных структурных модификациях, отличающихся типом кристаллической структуры – моноклинная фаза (m-ZrO2), тетрагональная фаза (t-ZrO2) и кубическая фаза (c-ZrO2). Две последние фазы являются высокотемпературными и могут быть стабилизированы при комнатной температуре за счет легирующих элементов или остаточных внутренних напряжений.
На рис. 2 представлены рентгеновские дифрактограммы образцов циркония после изотермического отжига при температуре 700°С, на которых отчетливо видна совокупность дифракционных линий, соответствующих моноклинной модификации оксида циркония m-ZrO2. При угле дифракции 2θ = 30.29° обнаруживается дифракционный максимум, который может быть отнесен к тетрагональной фазе оксида циркония t-ZrO2. В случае окисления образцов циркония, предварительно обработанных компрессионными плазменными потоками (рис. 2б), в анализируемом слое также обнаруживаются моноклинная и тетрагональная фазы оксида циркония. Однако в этом случае следует отметить более высокую интенсивность дифракционной линии тетрагональной фазы, что указывает на увеличение ее объемного содержания.
Рис. 2.
Рентгеновские дифрактограммы циркония в исходном состоянии (а) и после воздействия компрессионными плазменными потоками (б), подвергнутого окислению при 700°С в течение: 1 – 30; 2 – 90; 3 – 180 мин. Штрихи в нижней части рисунка показывают стандартные положения дифракционных максимумов.
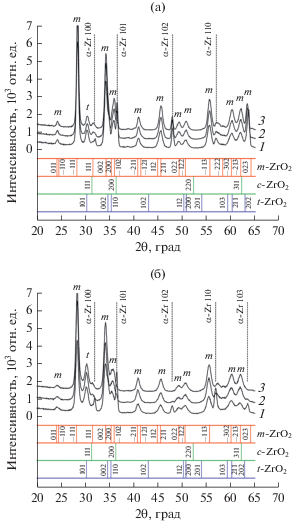
Параметры решетки оксидов циркония m-ZrO2 и t-ZrO2 практически не зависят от времени отжига в интервале от 30 до 180 мин, оставаясь меньше равновесных значений, о чем свидетельствует сдвиг соответствующих дифракционных линий. Такие значения параметров решетки, по-видимому, могут быть связаны с формированием фаз оксида в виде твердых растворов вычитания, в которых остается некоторая доля незаполненных узлов кристаллической решетки (т.е. формирование оксидных фаз происходит с недостатком по кислороду).
Следует обратить внимание на обнаруженные дифракционные линии фазы α-Zr, обусловленные отражениями рентгеновских лучей от неокисленного циркония, локализованного под сформированным слоем оксида. Интенсивность дифракционных линий α-Zr так же, как и их угловое положение, при окислении циркония без предварительной обработки компрессионными плазменными потоками практически не зависит от времени отжига. Это может являться результатом того, что толщина слоя оксида остается неизменной в исследуемом временном интервале. На рентгеновских дифрактограммах циркония, подвергнутого воздействию компрессионными плазменными потоками и последующему изотермическому отжигу, дифракционные максимумы фазы α-Zr наблюдаются лишь при минимальном времени отжига (30 мин) и не обнаруживаются при увеличении продолжительности отжига. Это может быть результатом формирования более глубокого слоя оксида в образцах циркония, обработанных компрессионными плазменными потоками.
После воздействия компрессионными плазменными потоками на цирконий в приповерхностном слое была обнаружена фаза нитрида циркония ZrN, которая исчезает уже после 30 мин отжига при температуре 700°С. По-видимому, при термическом воздействии происходит распад нитридной фазы с выделением свободного азота.
При температуре 862°C низкотемпературная α-фаза циркония с гексагональной решеткой переходит в высокотемпературную β-фазу с кубической (ОЦК) решеткой, упакованной с меньшей плотностью, что способствует повышению скорости диффузионных процессов кислорода в приповерхностном слое. Так, на рентгеновских дифрактограммах (рис. 3) обнаружены дифракционные максимумы преимущественно моноклинной фазы оксида циркония m-ZrO2, а также дифракционный максимум тетрагональной фазы t-ZrO2 слабой интенсивности. Дифракционные рефлексы фазы α-Zr весьма слабой интенсивности наблюдаются только на начальных этапах отжига, после чего полностью исчезают. Это указывает на достаточно быстрое формирование слоя оксида циркония, толщина которого превосходит глубину анализа с помощью рентгеновских лучей.
Рис. 3.
Рентгеновские дифрактограммы циркония в исходном состоянии (а) и после воздействия компрессионными плазменными потоками (б), подвергнутого окислению при 900°С в течение: 1 – 15; 2 – 60 мин.
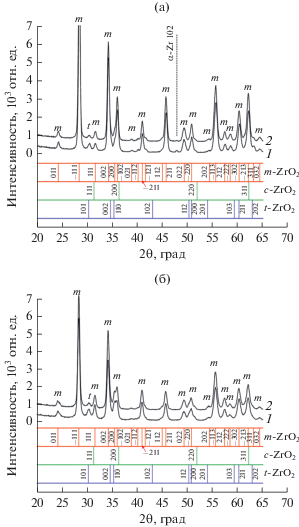
Анализ угловых положений дифракционных линий фаз оксида циркония, в первую очередь моноклинной модификации, показывает, что параметры решетки данной фазы не зависят от температуры и времени отжига, оставаясь ниже равновесного значения. По-видимому, данное обстоятельство может быть связано с характером формирования фазы оксида циркония. Так, формирование оксидной фазы происходит в широком диапазоне концентраций кислорода (29–66 ат. %), когда некоторые узлы кристаллической решетки являются вакантными, что и приводит к уменьшению параметров решетки.
Вследствие того, что из-за низкой симметрии фаз оксида на рентгеновских дифрактограммах образцов присутствует достаточно большое количество отражений, которые иногда сложно однозначно сопоставить с табличными параметрами, для независимой идентификации фазового состава был применен метод комбинационного рассеяния света, который основан на регистрации упруго рассеянного оптического излучения на колебаниях кристаллической решетки. В спектрах комбинационного рассеяния (рис. 4) обнаружены спектральные линии при волновых числах 178, 189, 222, 305, 332, 345, 382, 483, 502, 536, 558, 616, 638 см–1, которые согласно [13, 14] связаны с модами колебаний кристаллической решетки моноклинной модификации оксида циркония. Также наблюдается спектральная линия с волновым числом 476 см–1, которая отсутствует в спектре моноклинной фазы и близка к положению (473 см–1) спектральной линии тетрагональной фазы оксида циркония [15].
Рис. 4.
Спектры комбинационного рассеяния света (КР) образцов циркония после отжига в течение 180 мин при 700°С (а) и 60 мин при 900°С (б): 1 – без предварительного плазменного воздействия; 2 – после плазменного воздействия.
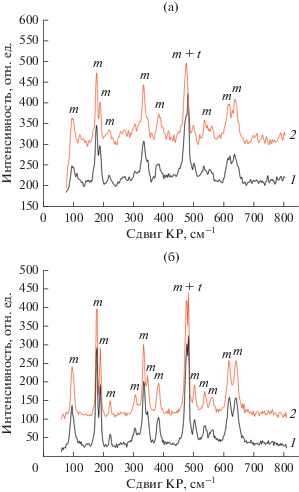
Анализ дублета в интервале волновых чисел 450–500 см–1 обнаруживает близко расположенные линии – 476 и 483 см–1, первая из которых соответствует фазе t-ZrO2, а вторая – m-ZrO2. На рис. 4а видно, что при отжиге при температуре 700°С интенсивность линии, соответствующей фазе t-ZrO2, превышает интенсивность линии фазы m-ZrO2 в случае предварительной плазменной обработки. Полученный результат в точности соответствует данным рентгеновской дифракции (рис. 2): интенсивность отражения при 2θ = = 30.29°, соответствующая фазе t-ZrO2, повышается после плазменного воздействия. Таким образом, в цирконии, подвергнутом воздействию компрессионных плазменных потоков, увеличивается доля тетрагональной модификации оксида циркония. Следует отметить, что обнаруженная закономерность формирования фаз оксида не наблюдается при отжиге при температуре 900°С.
Как известно, высокотемпературная тетрагональная фаза оксида циркония при комнатной температуре стабилизируется при его легировании атомами или оксидами переходных металлов. Наиболее часто для этих целей используют оксид иттрия Y2O3. Однако согласно [16] стабилизация фазы t-ZrO2 может происходить за счет “дефицита” кислорода в кристаллической решетке, когда образуются кислородные вакансии. Действительно, при окислении циркония, предварительно обработанного плазменными потоками, на начальных этапах происходит распад поверхностного нитрида циркония ZrN, в котором высвобождается свободный азот и повышается степень дефектности кубической кристаллической решетки. Именно в этом слое может формироваться преимущественно тетрагональная фаза, симметрия которой близка к симметрии кубической фазы нитрида циркония. При возрастании температуры отжига до 900°С увеличение количества дефектов в приповерхностном слое за счет распада нитрида ZrN нивелируется их отжигом, в результате предварительная плазменная обработка практически не сказывается на фазовом составе окисленного слоя.
Описанные выше механизмы формирования различных модификаций оксида циркония при изотермических отжигах могут объяснять различие в морфологии поверхности образцов, обнаруженное с помощью растровой электронной микроскопии (РЭМ) (рис. 5). На поверхности окисленных образцов, которые подвергались предварительному плазменному воздействию, видно формирование “рыхлой” структуры, образующейся за счет островкового механизма роста непосредственно на поверхности. Именно здесь происходит диффузионное проникновение кислорода в приповерхностный слой после распада нитридной фазы с образованием поверхностных зародышей роста.
Рис. 5.
РЭМ-изображения поверхности участков образцов циркония, отожженных при 700 (а, б) и 900°С (в, г) после воздействия компрессионными плазменными потоками (а, в) и без плазменной обработки (б, г).
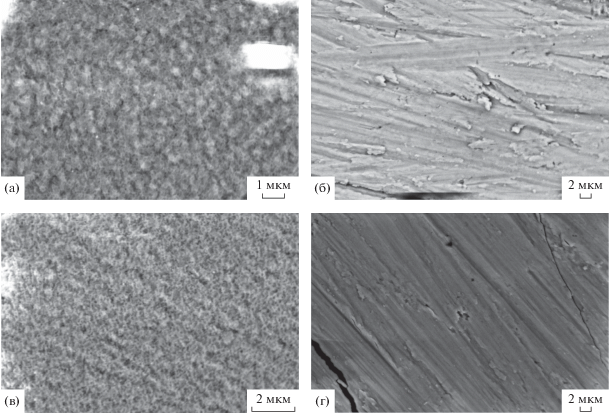
После окисления образцов циркония без предварительной плазменной обработки морфология поверхности повторяет рельеф, связанный с наличием полос шлифовки при механической подготовке пластин. По-видимому, в данном случае кислород проникает в гексагональную решетку низкотемпературной фазы циркония (700°С) или кубическую решетку высокотемпературной фазы (900°С). Зародыши роста образуются не на самой поверхности, а в виде отдельных локальных областей внутри приповерхностного слоя в результате трансформации кристаллических решеток твердых растворов α-Zr(O) или β-Zr(O) при достижении необходимой концентрации кислорода. Изменение морфологии поверхности окисленного слоя обуславливает изменение внешнего вида образцов (рис. 6). Образцы циркония, окисление которых происходило после предварительного плазменного воздействия, характеризуются однородным белым цветом, в то время как образцы без предварительного плазменного воздействия частично сохраняют темно-серый металлический блеск. Поскольку согласно структурным исследованиям фазовые составы образцов практически не различаются, единственной видимой причиной изменения их цвета является различная морфология их поверхности.
Рис. 6.
Внешний вид образцов циркония после окисления в течение 3 ч при 700°С (а) и 1 ч при 900°С (б). Верхний образец – после предварительной плазменной обработки, нижний – без плазменного воздействия.
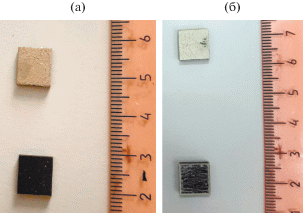
Предварительное плазменное воздействие также влияет на морфологию поверхности образцов циркония на макроуровне (рис. 7). С помощью РЭМ на окисленных поверхностях исследуемых образцов обнаруживаются микротрещины. Действительно, в результате проведения изотермического отжига после максимального времени выдерживания 1 ч при температуре 900°С на поверхности появляется совокупность параллельных друг другу трещин. Как известно, появление трещин может быть обусловлено влиянием внутренних механических напряжений, превышающих в локальных областях предел прочности материала. Это происходит вследствие внедрения в кристаллическую решетку дополнительных элементов, а также различия коэффициентов термического расширения в многофазной системе. В данном случае можно заметить, что количество трещин на единице площади существенно меньше у образца, который был предварительно подвергнут воздействию компрессионных плазменных потоков (рис. 7а). Однако согласно результатам рентгеноспектрального микроанализа, концентрация кислорода в приповерхностном слое практически не зависит от температуры отжига (табл. 1). Полученные значения концентрации кислорода соответствуют его содержанию в диоксиде циркония ZrO2. Следует также заметить, что концентрация кислорода в приповерхностном слое циркония, подвергнутого предварительному плазменному воздействию, немного выше, чем в отсутствие воздействия.
Рис. 7.
РЭМ-изображения трещин на поверхности образцов циркония после отжига при температуре 900°С: а – после воздействия компрессионными плазменными потоками; б – без плазменной обработки.
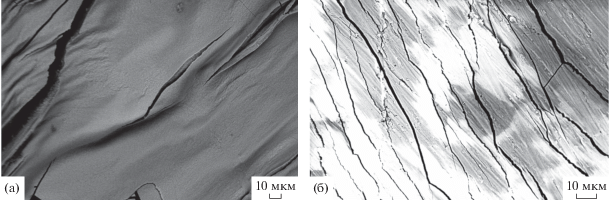
Таблица 1.
Содержание кислорода в образцах циркония после изотермического отжига
Описание образца | Температура отжига, °С | Концентрация, ат. % |
---|---|---|
Без воздействия КПП | 700 | 65 |
После воздействия КПП | 700 | 77 |
Без воздействия КПП | 900 | 68 |
После воздействия КПП | 900 | 77 |
Наиболее вероятной причиной повышенной поверхностной плотности трещин у образца циркония без предварительной плазменной обработки можно считать следующее. Воздействие компрессионных плазменных потоков с выбранными энергетическими параметрами на поверхность циркония приводит к его плавлению и последующей скоростной кристаллизации, в результате формируется мелкокристаллическая зеренная структура модифицированного слоя. При нагреве до температуры отжига, которая остается ниже температуры рекристаллизации, разница коэффициентов линейного расширения циркония и оксида циркония приводит к возникновению внутренних механических напряжений. В случае мелкокристаллической структуры модифицированного циркония происходит частичная релаксация напряжений на межзеренных границах, в результате количество трещин существенно снижается.
Высокотемпературное окисление циркония приводит к увеличению массы образца, что объясняется внедрением кислорода в приповерхностный слой за счет диффузионного твердофазного насыщения. На рис. 8 представлены зависимости прироста массы образцов после отжигов при различных температурах в зависимости от времени выдерживания. Образцы, предварительно обработанные компрессионными плазменными потоками, характеризуются меньшей скоростью увеличения массы при температуре отжига 700°С, что особенно проявляется на начальном этапе отжига (до 100–120 мин), после чего увеличение массы обоих образцов становится мало различимым. Такое поведение массы образца может быть связано с наличием на поверхности циркония, модифицированного компрессионными плазменными потоками, плотного слоя нитрида циркония ZrN, который выступает в качестве барьера для проникновения кислорода.
Рис. 8.
Зависимость прироста массы образцов циркония от времени отжига при 700 и 900°С: 1 – после воздействия компрессионными плазменными потоками; 2 – без плазменной обработки.
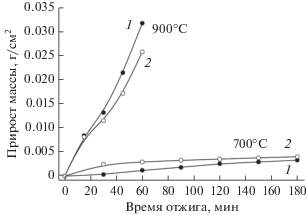
В случае отжига при температуре 900°С наблюдается, во-первых, интенсивный рост массы образца, а, во-вторых, более интенсивное окисление образцов после предварительного плазменного воздействия. Резкий прирост массы может объясняться увеличением коэффициента диффузии, связанным как с повышением температуры отжига, так и с формированием высокотемпературной фазы циркония с ОЦК-решеткой, упакованной с меньшей плотностью, чем гексагональная. На увеличение интенсивности диффузионного процесса в образцах, модифицированных плазменными потоками, сказывается повышение роли зернограничной диффузии, обусловленной формированием мелкокристаллической зеренной структуры.
Характерный вид кривых прироста массы (кинетических кривых) показывает, что в случае отжига при T = 900°С $\Delta m \sim t$, а при T = 700°C $\Delta m \sim \sqrt t $. Следовательно, в первом случае механизм окисления определяется фазовым переходом, т.е. формированием фаз оксида, а во втором случае – диффузионным насыщением приповерхностного слоя.
ЗАКЛЮЧЕНИЕ
В результате проведенных экспериментов исследовано влияние высокоэнергетического импульсного воздействия компрессионными плазменными потоками на структурно-фазовое состояние циркония и изучены особенности его окисления в воздушной атмосфере при температурах 700–900°С. Слой циркония, модифицированный воздействием компрессионных плазменных потоков, представляет собой низкотемпературную α-фазу с тонким приповерхностным слоем нитрида циркония ZrN.
Установлено, что под воздействием изотермического отжига на поверхности формируется моноклинная модификация оксида циркония ZrO2 с небольшим количеством тетрагональной фазы. При этом предварительное плазменное воздействие приводит к повышению объемной доли тетрагональной модификации вследствие ее стабилизации дефектами, образовавшимися при распаде фазы нитрида. Предварительная плазменная обработка способствует изменению механизма роста фаз оксида на поверхности, а также снижению интенсивности диффузионного насыщения кислородом, повышая тем самым термическую стабильность циркония.
Список литературы
Lee C.M., Sohn D.S. // Corrosion Sci. 2018. V. 131. P. 116.
Gosset D., Le Saux M., Simeone D., Gilbon D. // J. Nucl. Mater. 2012. V. 429. P. 19.
Горячев А.В., Косвинцев Ю.Ю., Лещенко А.Ю. // Физика и химия обработки материалов. 2009. № 2. С. 14.
Назин В.Г., Лев Л.Л., Рогалев В.А. // Поверхность. Рентген., синхротр. и нейтрон. исслед. 2014. № 11. С. 25.
Калин Б.А., Волков Н.В., Валиков Р.А., Яшин А.С. // Физика и химия обработки материалов. 2016. № 4. С. 5.
Калин Б.А., Волков Н.В., Олейников И.В., Наквасин С.Ю. // Поверхность. Рентген., синхротр. и нейтрон. исслед. 2008. № 5. С. 72.
Черенда Н.Н., Углов В.В., Гусакова С.В., Асташинский В.М., Кузьмицкий А.М. // Перспективные материалы. 2018. № 4. С. 49.
Shymanski V.I., Cherenda N.N., Uglov V.V., Astashynski V.M., Kuzmitski A.M. // Surf. Coat. Technol. 2015. V. 278. P. 183.
Cherenda N.N., Basalai A.V., Shymanski V.I., Uglov V.V., Astashynski V.M., Kuzmitski A.M., Laskovnev A.P., Remnev G.E. // Surf. Coat. Technol. 2018. V. 355. P. 148.
Шиманский В.И., Черенда Н.Н., Углов В.В., Асташинский В.М., Кузьмицкий А.М. // Поверхность. Рентген., синхротр. и нейтрон. исслед. 2018. № 7. С. 84.
Astashynski V.M., Ananin S.I., Askerko V.V. et al. // Surf. Coat. Technol. 2004. V. 180–181. P. 392.
Диаграммы состояния двойных металлических систем: Справочник. Т. 3. Кн. 1 / Ред. Лякишев Н.П. М.: Машиностроение, 2001. 872 с.
Naumenko A., Gnatiuk Iu., Smirnova N., Eremenko A. // Thin Solid Films. 2012. V. 520. P. 4541.
Huy L.D., Laffez P., Daniel Ph., Jouanneaux A., Khoi N.T., Simeone D. // Mater. Sci. Eng. B. 2003. V. 104. P. 163.
Ghosh A., Suri A.K., Pandey M., Thomas S., Rama Mohan T.R., Rao B.T. // Mater. Lett. 2006. V. 60. P. 1170.
Савченко Н.Л., Саблина Т.Ю., Кульков С.Н. // Порошковая металлургия. 1995. № 3/4. С. 61.
Дополнительные материалы отсутствуют.
Инструменты
Поверхность. Рентгеновские, синхротронные и нейтронные исследования