Поверхность. Рентгеновские, синхротронные и нейтронные исследования, 2022, № 6, стр. 108-112
Изменение химического состава поверхностных слоев твердосплавного инструмента с покрытием системы Ti–Al–N в процессе резания
К. Н. Рамазанов a, Э. Л. Варданян a, В. Р. Мухамадеев a, И. Р. Мухамадеев a, А. А. Маслов a, *
a Уфимский государственный авиационный технический университет
450022 Уфа, Россия
* E-mail: alexey.maslov2011@gmail.com
Поступила в редакцию 04.04.2021
После доработки 19.06.2021
Принята к публикации 22.06.2021
- EDN: UORGUD
- DOI: 10.31857/S1028096022040136
Аннотация
В работе приведены результаты исследования изменения химического состава в поверхностных слоях инструмента на начальных стадиях обработки. Для этого был физически смоделирован процесс, имитирующий период приработки и начальную стадию нормального износа. Изучаемые образцы из твердого сплава марки ТТ8К6 с покрытием TiAlN отжигали при температуре 700°C, давлении 0.5 ГПа в течение 20 мин, что эквивалентно термическим и механическим нагрузкам на покрытие в процессе обработки. Методом оптической эмиссионной спектрометрии с тлеющим разрядом (GDOES) исследовано изменение химического состава в приповерхностных слоях инструмента с покрытием. Описаны изменения в содержании титана, алюминия и кислорода в поверхностных слоях, происходящие в процессе моделирования и работы. Получены качественные профили элементного состава для исследуемых образцов. Методом растровой электронной микроскопии исследована микроструктура образцов. Получены карты распределения элементов.
ВВЕДЕНИЕ
Режущий инструмент является наиболее уязвимым элементом процесса механической обработки, поэтому задача повышения его долговечности и надежности является одной из приоритетных в производстве [1–6]. Одним из эффективных методов повышения износостойкости инструмента является нанесение различными методами защитных покрытий, в частности, композиционных наноструктурированных покрытий. Такие покрытия обеспечивают ряд преимуществ, главным из которых является значительное повышение долговечности [7–10].
В работе рассматривается композиционное износостойкое покрытие на основе системы Ti–Al–N, обладающее хорошо сбалансированными характеристиками: термостойкостью, низким коэффициентом трения, высокой твердостью, оптимальным модулем Юнга, а также хорошо работающие при отсутствии смазочно-охлаждающих жидкостей [11–14].
Для повышения конкурентоспособности и эффективности разрабатываемых покрытий необходимо всестороннее исследование их изменений в ходе работы, а также механизмов их формирования. Особую роль играет механизм разрушения и износа контактных поверхностей, серьезно влияющий на качество результата обработки. Диффузионные процессы в поверхностных слоях инструмента являются относительно малоизученным фактором износа инструмента, представляющим, тем не менее, интерес, особенно, если имеется химическое сродство между обрабатываемым изделием и материалом инструмента или покрытия [15]. Снижение работоспособности режущего инструмента может происходить за счет изменения структуры его приповерхностных слоев в процессе работы вследствие взаимной диффузии в зоне контакта обрабатываемого материала и инструмента в воздушной среде.
Целью работы является исследование диффузионных изменений в приповерхностных слоях режущего инструмента с износостойким покрытием (Ti, Al)N.
МЕТОДИКА ИССЛЕДОВАНИЙ
Для экспериментальных исследований использовались быстросменные многогранные пластины из сплава ТТ8К6 (аналог сплавов DIN HF10, HF20) с нанесенным на них покрытием (Ti, Al)N. Покрытие наносилось при помощи метода катодно-дугового осаждения (Arc-PVD) с двух катодов Ti и Al в среде аргона с применением фильтрации капель при помощи сепаратора на установке ННВ 6.6-И1. Поверхность образцов предварительно очищали в ультразвуковой ванне, непосредственно перед осаждением покрытия образцы были подвергнуты ионной очистке в среде аргона.
Согласно экспериментальным данным [3], при максимальных режимах резания со скоростью 200–300 м/мин значения температуры в зоне резания достигают 750–800°С, а давление на контактные поверхности достигает 0.5 ГПа. Эти нагрузки близки к максимально допустимым для износостойких покрытий системы (Ti, Al)N [3]. Поэтому для моделирования процесса резания были использованы условия, близкие к вышеописанным: время воздействия 20 мин, что составляет приблизительно 20–30% от периода стойкости инструмента, давление прессом на контактную поверхность 0.5 ГПа и температура 700°С. Схема воздействия на образец приведена на рис. 1.
Был определен химический состав в поверхностных слоях, испытанных образцов с покрытием, исследование проводили на различной глубине (по сечению от покрытия к подложке). Исследование методом оптической атомной эмиссионной спектрометрии GDOES (Glow Discharge Optical Emission Spectrometry) проводили на приборе Profiler-2 компании Horiba Scientific (Франция) при следующем режиме: давление аргона 700 Па, мощность 12 Вт, частота разряда 13.56 МГц, диаметр анода 4 мм, использовали не импульсный режим.
Микроструктуру образцов исследовали методом растровой электронной микроскопии (РЭМ), использовали сканирующий электронный микроскоп Vega3 компании Tescan. Ускоряющее напряжение составляло 20 кВ, увеличение – ×5000 и ×20 000 крат. Изображения были получены с помощью детектора отраженных электронов (BSE, backscattered electrons).
Толщина покрытия исследовалась на приборе CSM Calotest.
РЕЗУЛЬТАТЫ И ИХ ОБСУЖДЕНИЕ
Средняя толщина покрытия, измеренная на приборе Calotest, составила hпокр = 6.124 мкм. При исследовании на спектрометре в тлеющем разряде под ионной бомбардировкой происходит травление поверхности образцов, следовательно, длительность нахождения в тлеющем разряде кореллирует с толщиной стравленного слоя. Таким образом, действие разряда напрямую коррелирует и с глубиной исследования. Вследствие особенности применяемого метода и большого содержания кислорода в поверхностных слоях образцов практически невозможно количественно описать глубину исследования. Поэтому были получены качественные профили элементного состава двух образцов в зависимости от времени травления (рис. 2). В первом образце концентрация кислорода в приповерхностном слое значительно выше, чем в исходном образце, при этом концентрация титана у подложки несколько ниже.
Рис. 2.
Качественный профиль зависимости интенсивности излучения от времени распыления, индекс 1 – элементы в исходном образце, индекс 2 – элементы в испытанном образце.
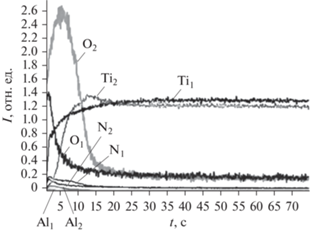
На качественных профилях распределения элементного состава представлены следующие элементы: Ti, Al, N, O. Из профиля распределения концентрации элементов следует, что у испытанного образца с покрытием и у исходного образца содержание кислорода в верхних слоях поверхности отличается незначительно. Однако через десять секунд травления концентрация кислорода в испытанном образце в шесть раз превышает таковую у исходного, что свидетельствует о диффузии кислорода в поверхностные слои. После 17 секунд концентрации кислорода в образцах становятся практически одинаковыми. Начиная с некоторой глубины диффузионной способности кислорода становится недостаточно, и его содержание в испытанном образце становится практически одинаковым с исходным образцом.
Характер профилей титана свидетельствует об уменьшении его содержания в поверхностных слоях испытанного образца. После 8 с травления происходит выравнивание с содержанием титана в исходном образце, затем имеет место некоторое превышение, после чего происходит окончательное выравнивание профилей. Это можно объяснить тем, что титан диффундирует вглубь образца в ходе испытаний.
Профили алюминия имеют зеркальный титану характер, что объясняется образованием у поверхности оксида алюминия, который уменьшает силу трения инструмента.
Профили азота свидетельствуют о диффузии азота к поверхности и к его постепенному замещению кислородом в приповерхностных слоях в ходе испытаний.
Микроструктуру образцов исследовали при помощи растрового электронного микроскопа Vega3 фирмы Tescan. На рис. 3, 4 представлены РЭМ-изображения исходного и испытанного образцов.
Рис. 3.
РЭМ-изображение микроструктуры образцов (20 кВ, увеличение ×5000): а – исходный образец, б – испытанный образец.
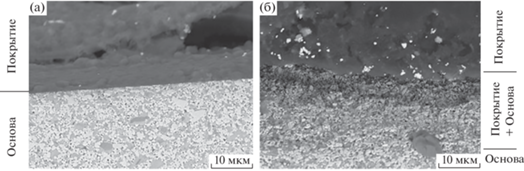
Рис. 4.
РЭМ-изображение микроструктуры образцов (20 кВ, ×20 000): а – исходный образец, б – испытанный образец.
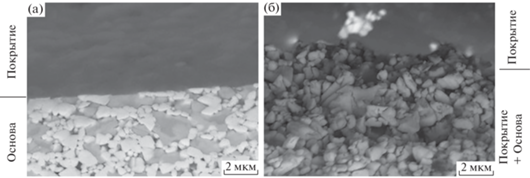
По результатам анализа микроструктуры наклонных шлифов исходных и испытанных образцов установлено, что на образцах после 20 мин испытания четкая граница раздела покрытия и подложки постепенно исчезает за счет процессов диффузии, в то время как у неиспытанного образца видна четкая граница раздела твердого сплава и покрытия.
Карта распределения элементов, полученная при помощи рентгеновского энергодисперсионного анализа (рис. 5), демонстрирует рост концентрации алюминия в испытанном образце по сравнению с исходным. Кроме того, для испытанного образца характерно увеличение переходной зоны кобальта, предположительно, это происходит вследствие взаимной диффузии кобальта как вглубь подложки, так и к поверхностным слоям покрытия.
ЗАКЛЮЧЕНИЕ
Методом оптической атомной эмиссионной спектрометрии изучено поведение различных элементов в покрытии (Ti, Al)N в процессе испытаний при помощи давления и нагрева. Установлено значительное повышение содержания кислорода в поверхностных слоях инструмента, а также постепенное их обеднение титаном и азотом, что может объясняться диффузией титана в подложку и замещением азота кислородом. Для алюминия характерна склонность к формированию оксидов, снижающих силу трения инструмента при обработке. Изучение микроструктуры показало постепенное размытие границы “покрытие–подложка” у испытанных образцов, что также можно объяснить взаимной диффузией элементов. Однако для более подробного описания этих процессов потребуются дальнейшие исследования.
Список литературы
Мигранов М.Ш. Повышение износостойкости инструментов на основе прогнозирования процессов адаптации поверхностей трения при резании металлов: Дис. ... д-ра техн. наук: 05.03.01. Москва: РУДН, 2007. 328 с.
Старков В.К. Физика и оптимизация резания материалов. Москва: Машиностроение, 2009. 640 с.
Верещака А.С. Работоспособность режущего инструмента с износостойкими покрытиями. Москва: Машиностроение, 1993. 336 с.
Hoornaert T., Hua Z. K., Zhang J. H. // Advanced tribology. 2009. P. 774. https://doi.org/:10.1007/978-3-642-03653-8_257.
Локтев Д., Ямашкин Е. // Наноиндустрия. 2007. № 4. С. 18.
Григорьев С.Н. Методы повышения стойкости режущего инструмента: учебник для студентов втузов. М.: Машиностроение, 2009. 368 с.
Углов В.В., Злоцкий С.В. Структура и свойства многокомпонентных покрытий на инструментальных материалах. Современное машиностроение: наука и образование//Материалы первой международной научно-практической конференции / Под ред. А.Н. Евграфова и А.А. Попова. СПб.: Изд-во Политехн. ун-та. 2011. № 1. С. 370.
Eleonora Santecchia, A.M.S.Hamouda, Farayi Musharavati, Erfan Zalnezhad, Marcello Cabibbo, Stefano Spigarelli // Ceramics international. 2015. V. 41. №. 9. P. 10349.
Michael Tkadletz, Nina Schalk, Rostislav Daniel, Jozef Keckes, Christoph Czettl, Christian Mittererb //Surf. Coat. Technol. 2016. V. 285. P. 31.
Mahdi Khadem, Oleksiy V. Penkov, Hee-Kyung Yang, Dae-Eun Kim // Friction. 2017. V. 5. №. 3. P. 248.
Alexey Vereschaka, Vladimir Tabakov, Sergey Grigoriev, NikolaySitnikov, Filipp Milovich, Nikolay Andreev, Catherine Sotova, Natalya Kutina // Surface and Coatings Technology. 2020. V. 385. P. 125402.
Криони Н.К., Мигранов М.Ш., Дементьева М.С., Мухамадеев В.Р. // Вестник УГАТУ. 2016. Т. 20. № 2(72). С. 29.
Chu X., Barnett S. A., Wong M. S. // Surf. Coat. Technol. 1993. V. 57. P. 13. https://doi.org/10.1016/0257-8972(93)90331-H
Hovsepian P. E., Lewis D. B., Munz W. D. // Surf. Coat. Technol. 2000. V. 133–134. P. 166. https://doi.org/10.1016/S0257-8972(00)00959-2
Vereschaka A.A., Grigoriev S.N., Sitnikov N.N., Oganyan G.V., Batako A. //Surf. Coat. Technol. 2017. V. 332. P. 198. Doi.org:10.1016/j.surfcoat.2017.10.027
Дополнительные материалы отсутствуют.
Инструменты
Поверхность. Рентгеновские, синхротронные и нейтронные исследования